CNC プラスチック加工のニッチを切り開く
プラスチックの機械加工は、工具、ワークの保持と切りくず (および粉塵) の管理。 (写真提供:K&E Plastics)
ニッチな CNC マシン ショップであることには利点がありますが、特有の課題もあります。バーモント州ベニントンの K&E Plastics はその好例です。
契約工場の名前が示すように、エンジニアリング プラスチック (熱可塑性樹脂と熱硬化性樹脂の両方) の加工のみに焦点を当てており、1966 年に Peter Broderson が K&E を設立して以来、そうしてきました。彼の息子である Eric は現在、会社の社長です。
研磨ガラスを充填した G7 や G10 などの熱硬化性樹脂を含む、プラスチックの加工を専門とするショップはあまり多くないため、アルミニウム、スチール、その他の従来の金属を加工するショップに比べて競争が激化しています。しかし、機器や工具のベンダーがプラスチックに精通していないため、K&E は、これらの材料を効果的に加工するための戦略を考え出すために、独自のデバイスに任せられることがありました.
2013 年に K&E を訪れ、ショップに関する最初の記事を書いたときに、これらの課題のいくつかを知りました。集塵の必要性。プラスチックの固定の難しさ。ガラス入り熱硬化性樹脂の加工に伴うツーリングの問題。リストは続く…
この話のために K&E を物理的に再訪することはできませんでしたが、再接続して、ショップがプラスチック加工の能力と効率を高めるために追加した新しい技術とプロセスについて聞くことができて感謝しています.これには、ツーリングとワーク保持の見方を変えること、および以前は従来のくし刃旋盤で実行されていたポリエーテルエーテルケトン (PEEK) などの熱可塑性プラスチックで作られた複雑な部品のより厳しい公差とより迅速な生産を実現するために、最初のスイス型旋盤を追加することが含まれます。この機械により、ショップは以前は外注していた作業を社内に戻すこともできました。
新しい機会、新しいアプローチ
当初、K&E は材料の優れた電気絶縁特性を考慮して、電気用途専用のプラスチック部品に焦点を当てていました (下のサイドバーを参照)。 Broderson が 27 年前に父親から事業を引き継いだとき、彼は医療および航空宇宙産業における非電気的アプリケーションを追求することによって会社を多様化しようとしました。今日では、電気自動車、燃料電池、エネルギー貯蔵などの新しいエネルギー技術の機会も追求しています。このショップは、ISO 9001:2015 の認証を受けており、国際武器取引規則 (ITAR) に登録されており、共同認証プログラム (JCP) の一部として認証されているため、秘密の防御作業を勝ち取ることができます。また、歴史的に十分に活用されていないビジネス ゾーン (HUBZone) プログラムの認定も取得しており、都市部および農村部のコミュニティの中小企業が連邦政府調達の機会に優先的にアクセスできるよう支援しています。
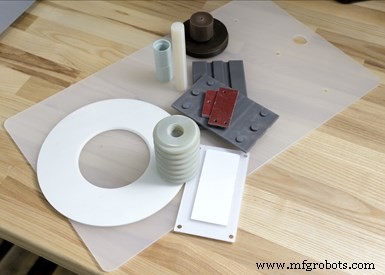
K&E マシンはプラスチックのみ (熱可塑性樹脂と熱硬化性樹脂を含む) ) 電気、航空宇宙、医療などの産業向け。また、燃料電池、電気自動車、エネルギー貯蔵などの新しいエネルギー用途にもチャンスがあると考えています。
工場の 30,000 平方フィートの施設には、さまざまな CNC ルーター、VMC、および旋盤 (全部で 28 台) が含まれています。これらの大部分は Haas Automation モデルです。 2018年に購入したスイス式旋盤はツガミのS205型(詳細は後述)。材料によっては、クーラントを使用して部品を機械加工したり、冷気ガンを使用して乾燥させたりして、切削操作を冷却し、切りくずを壊すのに役立ちます.
クーラントは、充填されていない熱可塑性樹脂に使用されることがあります。油性クーラントは、プラスチックを劣化させることが多いため使用できません。代わりに、K&E は Master Fluid Solutions の Trim Microsol 585XT などの水性冷却剤を使用しています。これは、潤滑性の高い半合成のマイクロエマルジョン クーラントであり、前世代の半合成クーラントよりもサンプの寿命を延ばし、泡の制御を向上させると言われています。
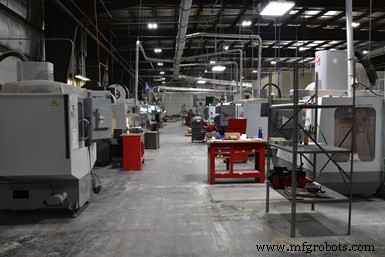
K&E のお店はダクトがあるのが特徴です2 つの中央集塵システムのうちの 1 つに、プラスチックを乾燥させる機械を接続します。
ただし、多くの熱硬化性樹脂は乾式で機械加工されます。これらの材料は、多くの場合、機械加工時に粉塵を発生させるガラスまたはその他の研磨材料で満たされています。クリーンな作業環境を維持し、工作機械の寿命を延ばすためには、効果的な集塵が不可欠です。実際、集塵に使用されるダクトは、ショップに独特の外観を与えるものです.
ダクトは、プラスチック部品を機械加工して乾燥させる各機器のワークゾーンに送られます。この工場は最近、2 番目の 18,000 cfm の集塵システムを追加しました。これにより、機械部品の乾燥にさらに 12 台のマシニング センターを追加することができます。
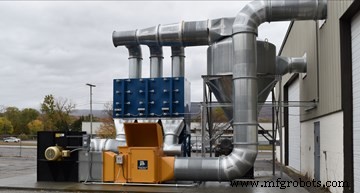
ショップは最近、2 番目の 18,000-cfm を設置しました集塵システムにより、プラスチックを乾式加工するためのマシニング センターを 12 台追加できます。
熱は、プラスチックを加工する際の大きな問題です。ツールの実行速度が速すぎると、材料の燃焼が発生する可能性があります。さらに、切りくずを効果的に排出しないと、機械加工された材料がワークピースに再溶接される可能性があります。ツールのフルート形状は、切りくずを工作物から排出したり遠ざけたりする上で重要な役割を果たし、冷気ジェットも同様です。ただし、G7 や G10 などの熱硬化性ラミネートも、樹脂の結合強度と部品の加工方法によっては、剥離しやすくなります。
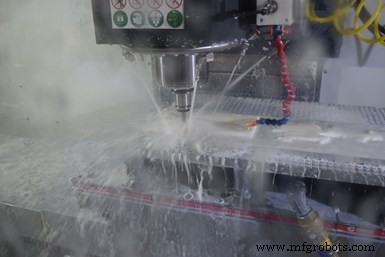
熱可塑性樹脂は、通常、水ベースのクーラントを使用して加工されます.石油ベースのクーラントは、プラスチック材料を劣化させる可能性があります。
このショップは最近、Datron Dynamics の切削工具を使い始めました。一例として、直径 6 mm の研磨された 1 枚刃の超硬エンドミルがあります。同社によると、多段階の研削プロセスにより、バリのない機械加工のためのシャープで研磨されたエッジが得られ、部品を手作業で仕上げる必要が減少または排除されます。
もう 1 つは、Harvey Tool の複合材用アモルファス ダイヤモンド コーティングを施した超硬エンド ミルです。これらは、G10 や FR4 などの繊維または充填濃度の高い複合材料の粗加工および半仕上げ加工に適していると言われています。これは、繊維を効率的に剪断し、切りくず除去を改善するために切りくずを短くするチップブレーカーを備えた最適化された形状によるものです。
さらに、K&E は現在、高品質の表面仕上げで正確で深い穴を繰り返し加工する必要がある場合に、Sterling のガン ドリルを使用しています。
この工場では、マシニング センター用に Rego-Fix の PowRgrip ツール保持システムの標準化も開始しています。その理由は、従来のツールホルダー システムでは 0.002 インチもの振れが発生し、公差が非常に厳しいパーツ フィーチャでは許容されなかったからです。 「現在、振れは 10 分の 4 に達しています」と Broderson 氏は言います。
このショップは、油圧プレスがホルダーからコレットを挿入または取り外します。各コレットには浅いセルフロック テーパーがあり、9 トンの力でツールホルダーに押し込まれます。 Broderson 氏によると、これらのホルダーは従来のモデルに比べて振れと剛性が優れています。
このシステムは、高精度のコレット スタイルのツールホルダーと、コレットをホルダーに挿入したり、ホルダーから取り外したりするために使用される卓上油圧プレスで構成されています。コレットには浅い自動ロック式テーパーがあり、9 トンの力でツールホルダーに押し込まれます。また、押し込んだときにツールホルダーに接触する四角い肩が付いています。このポジティブストップ設計により、組み込みのバックアップスクリューを使用してツールの長さを正確に設定できます。これらのツールホルダーは、高いクランプ力と振動減衰、長さと直径の比率 3:1 で ≤ 3 ミクロンのインジケーターの全振れ (TIR) を特長としています。 Rego-Fix によると、このツール保持システムは焼きばめシステムよりも迅速で安全なツール交換を可能にします。新しいツールの組み立てには 10 秒もかからないと言われています。 「当店には現在、これらのツールホルダーが約 800 個ありますが、さらに追加し続けています」と Broderson 氏は言います。
ワーク保持のために、一部のマシンは真空チャックを使用して切り替えを高速化し、ツールがパーツの 5 つの側面にアクセスできるようにします。同様に、K&E は、ひよこ万力をトッピングした一般的な基礎プレートの使用を開始しました。 Broderson 氏によると、Chick バイスは位置決めの再現性が高く、プレートが共通の場所に取り付けられるため、工場で単にバイスをマシン テーブルにボルトで固定する場合と比べて、セットアップ中のプロービングは必要ありません。店はまた、仕事が繰り返されるときに使用する万力の顎を保存して保管します.
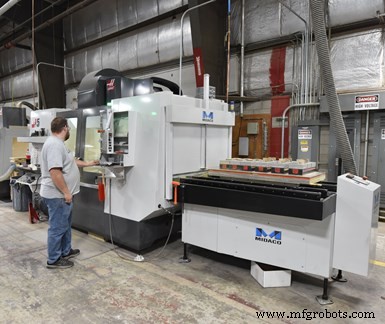
この VMC のスピンドル稼働時間を増やすには、K&Eパレット交換システムを追加したため、マシンで別のジョブを完了している間にジョブをオフラインでセットアップできます。他の 2 つの VMC についても同じことが行われています。
3 台の VMC のスピンドルのアップタイムを最大化するために、K&E はそれぞれに Midaco パレット チェンジャーを追加しました。これにより、新しい材料が機械の外のパレットに固定されている間、各機械はジョブを実行し続けることができます。ジョブが完了すると、そのパレットがシャトル アウトし、次のジョブが固定された新しいパレットがシャトルインします。
Swiss-Type を追加する理由
Broderson 氏によると、数年前に S205 を追加する前に、K&E は特定の仕事のためにねじ機械工場に仕事を委託していました。時間が経つにつれて、そのアウトソーシング作業の量は増加し続けました。さらに、いくつかのくし刃旋盤で実行された許容範囲の狭いジョブのスクラップ率または不合格率が、必要以上に高くなることがありました。ショップは、特徴的なガイド ブッシング設計と多機能機能を備えたスイス型が必要な精度を提供し、ショップがその作業を社内で維持できるようにすることを決定しました.
ツガミ S205 には、直径 20 mm の棒材容量と Edge Technologies Minuteman 320 SE バーフィーダーが搭載されており、ツガミ/REM の販売代理店であるロバート E. モリス カンパニーを通じて購入されました。同社のアカウント マネージャーであるジョン リカルディ氏によると、この機械には 1,000 psi のクーラント供給システム (主に切りくず処理用)、ミスト収集ユニット、切りくずコンベヤ、サブスピンドルから長い部品を受け取るための特別なシュート、コンバーチブル/チャッカー変換が含まれていました。
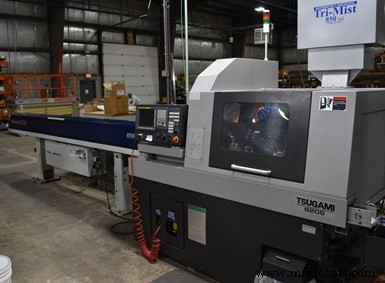
長さ 10 フィートのバーフィーダーバーは、長さ 4 フィートのバーを実行するくし型旋盤のバーフィーダーよりも長い時間、ショップの最初のスイス型を無人で実行することを可能にします.
おそらく、このマシンの最大のセールス ポイントは、油性クーラントのようにプラスチック ワークを劣化させないように、水性クーラントで動作するように設計されていることです。リカルディ氏によると、ツーリング アタッチメントとスピンドルの正圧は、クーラントがベアリングに入り、潤滑油を洗い流すのを防ぎます。さらに、バーフィーダーチャンネルセットにも水性潤滑剤が使用されています。
スイス型は、公差が非常に厳しい部品に使用されます。 Broderson 氏は、従来の旋盤でプラスチック部品を加工すると、工具の圧力によってテーパーが形成される可能性があると述べています。スイスタイプの特徴的なガイドブッシングは、この問題を解消するためにカットでサポートを提供します。さらに、この機械は非常によく繰り返すと彼は言います。プロセスがダイヤルインされると、カット、測定、およびプロセスの繰り返しはもうありません。さらに、バーフィーダーには、長さ 12 フィートのバーを走らせる能力があります。 K&E では通常、長さ 10 フィートの棒材を使用しているため、4 フィートの棒材供給装置を備えた従来の旋盤と比較して、長時間の無人加工が可能です。 PEEK などの材料の場合、通常はバーストックを +0.002 インチ / -0 インチに研磨します。
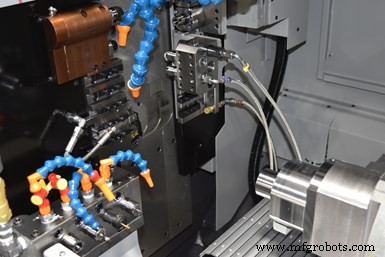
スイス式旋盤。水性クーラントを使用することで、以前は従来のくし刃型 CNC 旋盤で行っていた熱可塑性部品の公差が厳しくなり、生産性が向上したと言われています。この機械により、ショップは以前は外注していた作業を社内に戻すこともできました。
とはいえ、ショップはガイド ブッシングを取り外して、機械を従来のチャッカー旋盤として操作し、標準的な旋盤と同じ加工アプローチでジョブを実行できます。
Broderson 氏によると、最大の学習曲線の 1 つは、機械加工される部品の寸法を変更せずに切りくずを除去して部品に水を流すために、大量のクーラント ポンプに使用する圧力を決定することでした。圧力が高すぎると、クーラントの流れによってプラスチック部品の寸法が変化する可能性があります。また、マシンのスピンドルが急速に加速するため、棒材のねじれも発生しました。その修正は、よりゆっくりと加速することでした。もう 1 つの課題は、部品のどの機能を機械加工できるか、またそれらをいつシーケンス処理する必要があるかを知ることでした。
重要な問題
Broderson 氏によると、彼のショップが最近直面している全体的な課題の 1 つは、プラスチック材料のばらつきです。彼は米国のサプライヤーから購入するように努めていますが、中には海外で生産された素材を販売しているサプライヤーもあります。 「注文するときは、非常に具体的にする必要があります」と彼は言います。
1 つの例では、工場はジョブ用に FR4 材料を注文し、その材料のバッチの機械加工プロセスを調整しました。その後、ジョブが戻ってきたときに別のバッチを注文しました。ただし、その 2 番目のバッチは電気エンクロージャの同じ NEMA 分類を満たしていましたが、樹脂とガラスのフィラーの違いが十分にあり、以前の FR4 バッチで使用された切断データとツールは新しいバッチと互換性がありませんでした。 「このような素材で 2 人を保持するのは十分に困難ですが、バッチ間の差異によりさらに困難になります。」
熱硬化性樹脂、熱可塑性樹脂の基礎
K&E は、エンジニアリング プラスチックを扱って 54 年の経験があります。ショップによると、熱硬化性樹脂は高い耐熱性と電気絶縁性を必要とする用途に適しています。熱硬化性樹脂の架橋ポリマーは不可逆的な結合を形成し、熱が再適用された場合に製品が溶融するリスクを排除します。また、金属よりも軽量でありながら、優れた耐摩耗性と寸法安定性を提供します。
熱可塑性ペレットは加熱すると軟化し、さらに加熱すると液化するため、化学結合が起こらないため、硬化プロセスは完全に可逆的です。これにより、材料の物理的特性に悪影響を与えることなく、熱可塑性樹脂を再成形してリサイクルすることができます。熱可塑性プラスチックには、耐薬品性、耐衝撃性、電気絶縁性、低吸湿性、低摩擦係数、嵌合部品の摩耗の低減、製品操作中の潤滑の排除などの利点があります。
産業機器