顕微鏡を使用した層の厚さの測定
工業用測定顕微鏡などの光学機器を製造する日本のカメラ大手ニコンの計測部門は、NIS-Elementsイメージングプラットフォームに新しい層厚ソフトウェアモジュールを追加して、断面の層の深さと表面の検査、分析、レポートを合理化しました。フィーチャー幅。このオプションは、さまざまな機能を半自動化することで品質管理を高速化するだけでなく、特徴認識、結果の解釈、数値計算における人為的ミスのリスクを軽減することで信頼性を向上させます。このソフトウェアのアプリケーションは、製造や材料の研究から医学や鉱物学に至るまで、業界や科学全体で見つけることができます。

厚さを正確に測定することの重要性を代表する例は、大量生産で一般的です。自動車業界では、車体の塗装が少なすぎると保証請求に費用がかかる可能性があり、多すぎると年間数百万ドルが無駄になる可能性があります。同じ原則が食品業界でも、生鮮食品の貯蔵寿命を延ばすための酸素不透過性を提供するためにプラスチック包装に適用される比較的高価なEVOHバリアに適用されます。同様に、銅の過剰使用を避けるために、プリント回路基板上の導電性トラックの幅を正確に制御する必要があります。
層の厚さの測定が重要なその他のアプリケーションには、鋼やその他の金属の脱炭分析、溶射または化学蒸着分析、接着または表面摩耗のチェックなどがあります。
Nikon MetrologyのNIS-Elementsは、直立または倒立光学顕微鏡、場合によっては走査型電子顕微鏡からのデジタル画像を検査できる統合ソフトウェアイメージングプラットフォームであり、重要な機能を高精度で分析できます。画像はライブにすることも、高解像度カメラを使用してデジタルで保存することもできます。
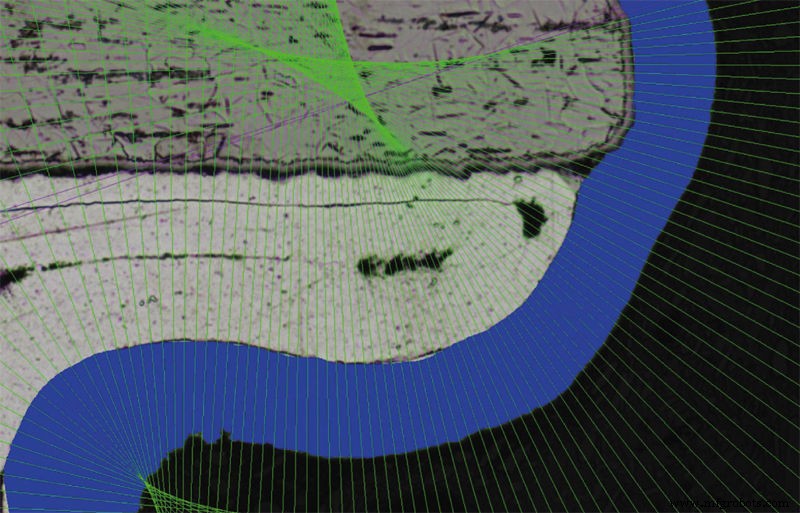
ただし、何よりも重要なのは、最初に画像をキャプチャするために使用される光学系の品質です。これはニコンのコアコンピタンスであり、特にサードパーティのサプライヤーに依存するのではなく、独自のガラスを製造している唯一の顕微鏡メーカーです。
半自動評価の4つのモード
以前はNIS-Elementsソフトウェア内で、画像内のレイヤーの測定は完全に手動のプロセスである必要があり、その機能はそのままです。これには、オペレーターがレイヤーの境界を定義し、サンプル全体で等間隔のポイントを選択し、それらの場所で厚さを測定し、値を記録し、平均の厚さを計算することが含まれます。

層の厚さソフトウェアは、これらの手動ツールを便利なモジュールに統合して、半自動ワークフローのオプションを提供します。コントラストなどの画像特性に基づく処理技術を利用して、多くの測定機能を自動化します。これは、外科用メスを使用して、またはおそらく鋸またはワイヤーEDMによって断面化された不透明な標本からのエピスコピック(反射)光によって生成された画像を分析するのに理想的です。ミクロトームからの非常に薄い半透明の材料スライスを介した透視(透過)照明によって生成された画像の分析にも同様に適用できます。

ソフトウェアには、線形、円形、アモルファスの層(またはトラック)の測定を支援するさまざまなモードがあり、4番目のモードはCalotestをサポートします。これは、検査中の表面に対して回転する研磨ボールによって露出された円形層を分析することによってコーティングの厚さを測定します。
使用方法
NIS-Elementsでデジタル画像がキャプチャされた後、電動ノーズピースを備えた顕微鏡の場合は自動的に、または手動でキャリブレーションされます。画像がライブの場合、ドロップダウンリストで関連する顕微鏡対物レンズをクリックしてキャリブレーションされます。上部のメニューバーで[レイヤーの測定]を選択すると、4つの操作モードが表示されます。

[線形]オプションが選択されている場合、直線化ツールを使用してレイヤーを水平方向に整列させることができます。間隔の数はオペレーターが変更できますが、測定が自動的に行われる5つの等間隔の垂直ベクトルが生成されます。または、測定が連続している場合もあります。アプリケーションの「バイナリエディタ」領域で、「自動検出」ツールを使用すると、オペレータはレイヤを選択してその境界を定義できます。しきい値コマンドを適用して、ピクセルの強度または色でレイヤーを区別するのに役立てることができます。
オペレーターは、サンプル内の含有物の存在を無視し、層を上から下に測定することを選択できます。これは、ほとんどのアプリケーションに最適な選択です。他のオプションでは、境界と最初の穴またはギャップの間の距離、または穴またはギャップの間の最大距離を測定できます。分析は、画像の左側から右側へ、そして上から下へと進みます。
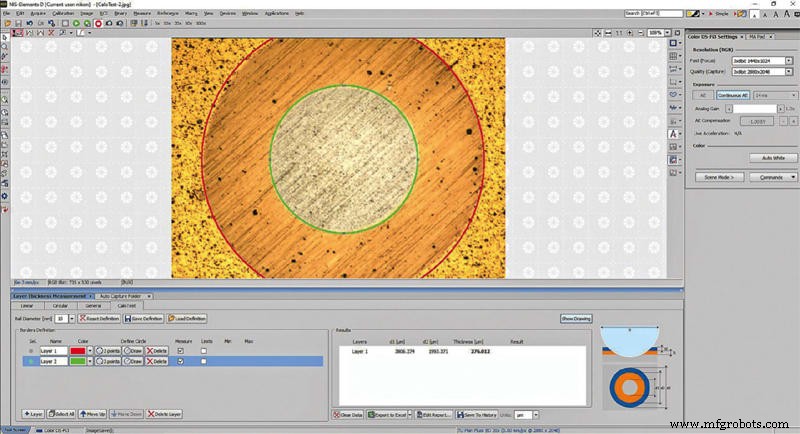
多くの場合、測定を行う前に、ソフトウェアが垂直に描かれた2本の線の間だけを見るように制限を適用する必要があります。これにより、レイヤーの代表的でない領域を除外できます。同様に、「描画」コマンドでさまざまなバイナリツールを選択し、異常を埋めることで、レイヤー境界の上または下の重要な投影などの懸念事項を画像から削除し、結果として線を滑らかにすることができます。
選択したROI(対象領域)で測定された総層長、最小、最大、平均の厚さ、および標準偏差を示すミリメートルまたはミクロン単位の結果はすべて自動的に計算され、値は画像の下に表示されます。測定された長さに平均幅を掛けると、面積の値が得られます。このプロセスは、連続するレイヤーに対して繰り返されます。各レイヤーは、オペレーターによって名前が付けられ、画像およびレイヤー測定フィールドに緑、青などの色が自動的に割り当てられます。ユーザーは、必要に応じてすべてのデフォルトのレイヤーカラーを再割り当てできます。
デジタル画像に円形のレイヤーが含まれている場合、垂直方向のベクトルは、斜めの角度でレイヤーを測定するため、適切ではありません。 [円形]オプションを選択すると、オペレーターはフィーチャの周囲に簡単に円弧を描き、レイヤーを統合して色付けすることができます。すべてのポイントでレイヤーに垂直な角度増分で事前設定された数の放射状ベクトル線が、測定が行われる場所を定義する画面に自動的に表示されます。
画像がアモルファスで不規則な形状の層を示している場合は、「一般」オプションを使用できます。 「ポリラインの定義」を選択すると、レイヤーの周囲にパスを描画できます。その後、パスが統合されて色付けされ、パスに垂直なベクトルが円形レイヤーの場合と同様に自動的に適用され、同様に測定が行われます。
測定に関する情報は、色付きのレイヤーとすべてのデータを示すPDF形式のレイヤー厚さレポートとして自動的にエクスポートされる場合があります。または、レポートをExcelにエクスポートすることもできます。標準のデフォルトテンプレートまたは顧客が定義したカスタムテンプレートのいずれかに結果を入力できます。
結論

NikonのLayerThicknessソフトウェアモジュールを使用すると、オペレーターがすべての測定を手作業で行う場合よりも、試料に関する包括的な情報をより迅速に取得できます。アプリケーションによると、ワークフローの改善により、収集および分析された特定の量のデータに対して、検査の生産性が最大5倍向上する可能性があります。測定値は、同じサンプルまたはサンプルのバッチに関連付けられた画像のグループ全体で簡単かつ迅速に平均化できます。さらに、プロセスは、機器を使用するさまざまなオペレーターの数に関係なく、より正確で再現性があり、人間の解釈を減らすことで、品質管理を損なう可能性のあるエラーのリスクが軽減されます。
この記事は、Nikon Metrology、Inc.(Brighton、MI)の南北アメリカのアシスタントマーケティングマネージャーであるMeghanE.Meinertによって書かれました。詳細については、Meinertさんにお問い合わせください。このメールアドレスはスパムボットから保護されています。表示するにはJavaScriptを有効にする必要があります。または、こちらにアクセスしてください 。
センサー