熱可塑性一次航空構造はさらに一歩前進します
靭性、比較的高い面外強度、持続可能性/リサイクル性などの熱可塑性複合材料の有利な機能は、航空機の設計を引き付けています。 何十年にもわたって熱可塑性複合材料の一次構造の概念にエンジニア。しかし、航空機の製造 エンジニアは、CADシミュレーションから生産現場に進むための費用効果の高い方法を見つけることに自信がありませんでした。しかし、彼らは思いとどまることはありません。必要な製造技術を開発するための努力は世界中で続いており、おそらくオランダほど粘り強くはありません。
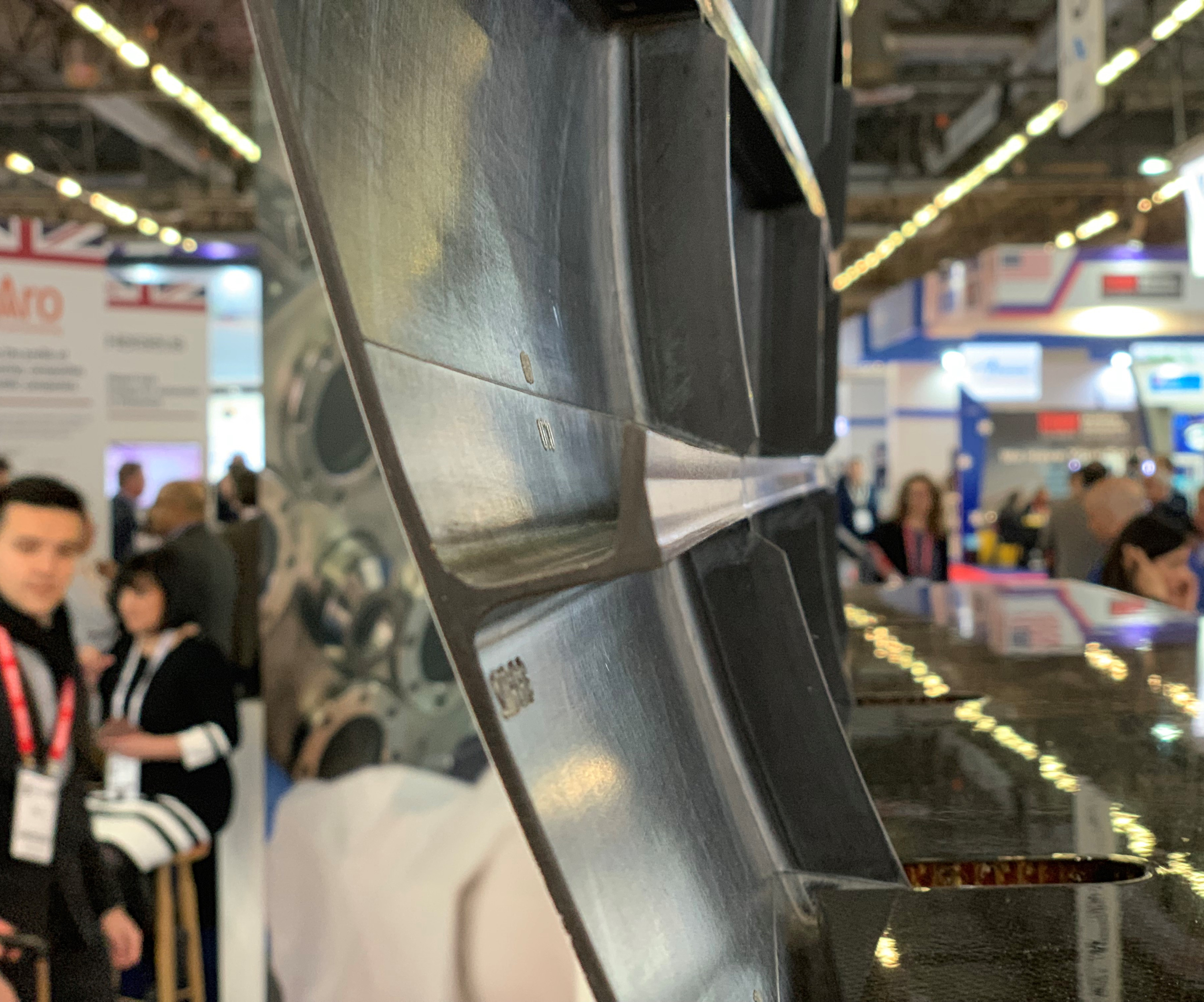
統合Lストリンガー。 Gulfstream用に設計および製造されたGKNFokkerカーボンファイバー/ PEKK胴体には、ツールのリリースを可能にするために、わずかに鈍角の湾曲した縦方向のLストリンガーが組み込まれています。 CW 写真|ジェフ・スローン
2009年に、9つのオランダの産業会社と研究機関がエアバス(フランス、トゥールーズ)とともに、熱可塑性の手頃な一次航空機構造(TAPAS)コンソーシアムを結成しました。イニシアチブは2014年に12のパートナーに拡大し、TAPAS2として継続されました。 GKN Fokker(Hoogeveen、Netherlands)は、TAPAS2でAirbusが開発したアプリケーションを対象に、熱可塑性複合胴体設計の費用効果の高い生産を可能にする「バットジョイントオルソグリッドテクノロジー」と呼ばれるものを使用して胴体デモンストレーターを最近開発しました。
ガルフストリームエアロスペース(米国ジョージア州サバンナ)がGKNフォッカーと提携してTAPAS2胴体技術を進歩させ、おそらく材料と完全な胴体へのプロセス。新しく開発された胴体パネル(今年初めにJEC Worldで展示された)の背後にあるストーリーは、設計および製造方法の進歩の1つであり、さらに、より完全に統合された設計-製造エンジニアリングアプローチです。
「従来は、GKNFokkerのチーフエンジニアであるAndriesBuitenhuis氏は、次のように説明しています。彼らは、他の分野とは関係なく、プライレイアップテーブルから作業します。」新しいアプローチは、統合されたデジタル化された設計製造ソフトウェアプラットフォーム(TAPASを通じて開発)であり、さまざまな分野のエンジニアがすべて同じデジタルモデルを検討し、より複雑な部品設計を概念化することができます。 「これにより、前例のない最適化の可能性のまったく新しい世界が開かれます」とBuitenhuis氏は続けます。 「複雑な形状では、繊維の方向がいたるところにある可能性があります。型にはまらないラミネートを作成し、設計の許容範囲、製造のギャップとオーバーラップ、半径などを新たに検討することができます。また、構造の強度をローカルで最適化できます。」これらの拡張された設計オプションは、自動ファイバー配置(AFP)マシンのファイバーステアリング機能をより完全に採用し、以下で説明する他の製造機能を進歩させます。
この統合されたデジタルシステムによってもたらされる設計の自由は、ビジネスジェットパネルの設計と製造に不可欠であることが証明されています。 TAPAS2胴体の設計では、炭素繊維/ポリエーテルケトンケトン(PEKK)パネル(ソルベイのAPC PEKK-FCで作成)は、溶接されたファスナーのないフレームとスキンの接合部を備えています。これは、設計の費用対効果に不可欠です。 GKNFokkerの熱可塑性複合材料技術の責任者であるArntOffringaは、「アルミニウム製の胴体シェルと同等のコストを達成できると予測しています。これは、アルミニウム製のシェルがリベットで留められているためです」と説明しています。機械的な留め具をなくすことで、従来の複合ソリューションと比較して、航空機の一次構造のコストを20%削減し、重量を10%削減することが期待されます。もちろん、コストと重量の節約の多くは、ファスナー自体の排除と、ファスナーを取り付けるための人件費によるものです。また、ファスナーを収容するために複合コンポーネントの穴をなくすことも非常に重要です。穴は、補強を追加する必要があるため、重量を追加する必要があります。
GKN Fokkerは、2017年12月にTAPAS2の下で、加圧胴体のエアバスで技術準備レベル(TRL)3(概念実証)に達し、アルミニウム胴体パネルと同等のコストを示しました。その過程で、GKNFokkerチームはこの熱可塑性製品のビジョンを拡大しました。民間航空会社からビジネスジェットアプリケーションまでの胴体技術。
ガルフストリームの関心
熱可塑性複合部品に関するガルフストリームでのGKNFokkerの成功した仕事の歴史は、ビジネスジェットメーカーとのパートナーシップを論理的な次のステップにしました。 「ガルフストリームが熱可塑性複合部品を何年も飛行していることは広く知られています」と、ガルフストリームのAdvanced Structures and Materials Initiative(ASMI)のマネージャーであるMarkChapmanは述べています。彼は、胴体パネルプロジェクトは、「私たちが行ってきたことから、より単純な部品から始まり、主要な構造部品に向かって自然に進んでいる」と付け加えています。 GKN Fokkerは、Gulfstreamと提携して、テールエレベータやラダー、G650のフロアパネルなど、多数の熱可塑性複合二次部品の開発を行ってきました。
2015年、OffringaとBuitenhuisはTAPAS2プロジェクトの開発をガルフストリームに提示し、Chapmanと彼のチームはTAPAS2の結果のメリットを獲得する可能性を認識しました。 「潜在的な軽量化のメリット、耐衝撃性と靭性の向上、パフォーマンスの向上が見られました」とチャップマン氏は振り返ります。ファスナーのないデザインも魅力的です。 「溶接技術により、機械的に固定されたアセンブリよりも効率的に胴体を組み立てることができます」とチャップマン氏は言います。
GKN Fokkerとのパートナーシップは、金属構造では経済的に実現できない可能性のある、より複雑な胴体形状のガルフストリームの研究開発をサポートしています。 「これまでのところ、ストレッチフォームの金属しかできません」とチャップマン氏は述べています。 「複雑な形状に必要なスプライスと支持構造はあまり効率的ではありません。」 Offringaは、「このような複雑な形状は、従来の技術では製造が困難です」と同意しています。
設計と製造の結合
ファスナーのない生産可能な設計を実現するために、GKN Fokkerのアプローチは、機体の接合部が受ける2つの主要な力、つまり客室の圧力と工具の落下などの衝撃に耐えることに重点を置いています。キャビンの圧力により胴体に半径方向の力がかかり、フレームとスキンの接合部に高い負荷がかかります。従来の設計では、胴体フレームには、縦ストリンガーが通過する「マウス穴」が含まれています。キャビン圧力の力の下で、これらのマウスの穴は、高い剥離力を受ける不連続部として機能します。これは、金属と比較して複合材料の面外強度が低いことを考えると、ファスナーのない設計の主な懸念事項です。フレームは衝撃を受けても曲がらないため、衝撃によってフレームとスキンのジョイントに高い荷重が発生します。
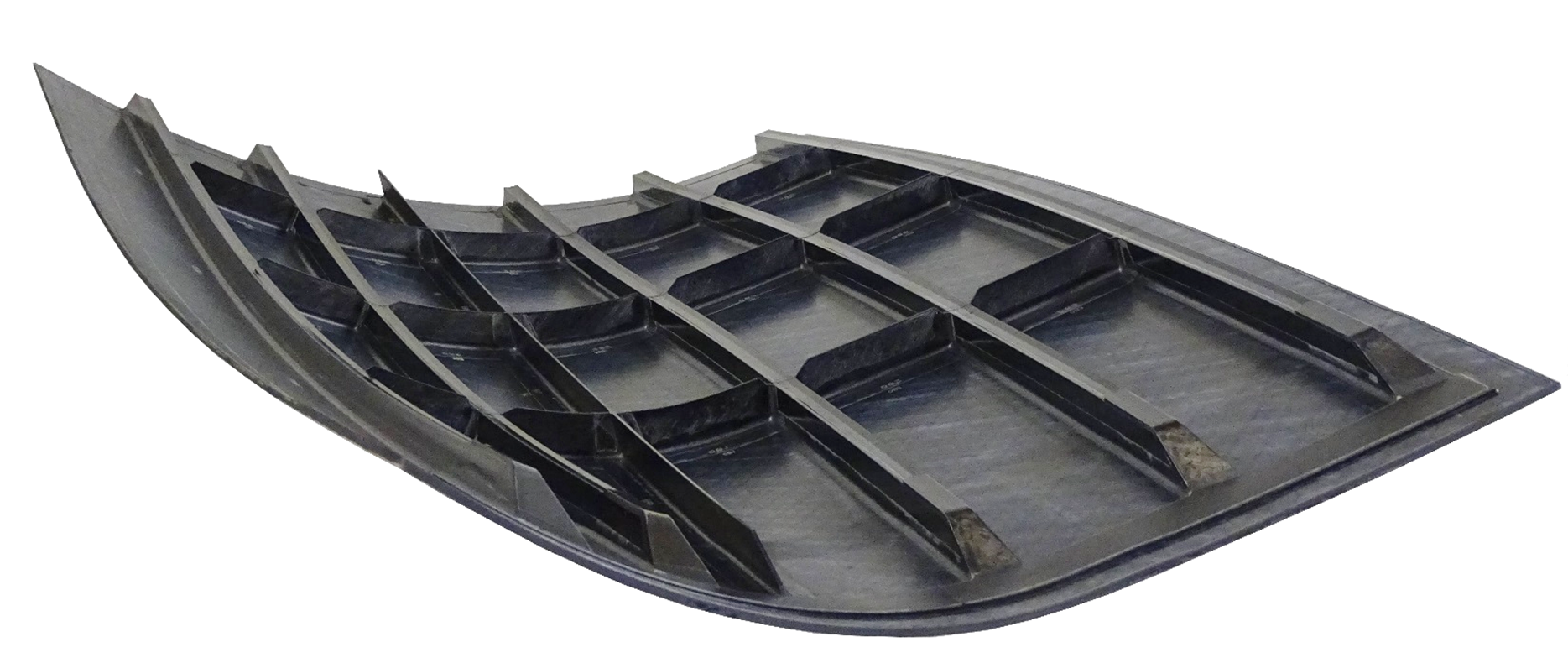
二重曲率。 熱可塑性複合材の胴体パネルは、ガルフストリームビジネスジェット後部胴体の複雑な形状に対応し、スキンのファイバーステアAFPレイアップとオルソグリッドの同時統合を備えています。後でフレームに溶接される円周方向のブレードストリンガーに注意してください。ソース| GKNフォッカー
GKN Fokker / Gulfstreamチームは、金属または従来の複合材料の設計-製造アプローチのいずれかを使用して、複雑な湾曲によって生じる課題に対処することは不可能であることを認識していました。特に、Buitenhuis氏は、「複雑な胴体の設計は、ファイバーステアリングなしでは不可能です」と指摘しています。 AFPマシンのこの機能により、設計者はシェルの複雑な形状に基づいて繊維配向をローカルで最適化し、標準の0/45/90繊維配向オプションから逸脱することができます。 「形状と重量の最適化のためのファイバーステアリングは、このプロジェクトの最も重要な進歩の1つです」とChapman氏は信じています。
GKN Fokkerは、同社が迅速な熱可塑性テープのレイアップ用に開発した超音波AFPマシンで、胴体パネルの外板を作成しました。テープは一方向であるため、ファブリックテープと比較してラミネートのパフォーマンスも向上します。
キャビンの圧力や衝撃力、その他の性能要求によって生じる高荷重をうまく処理するために、TAPASとTAPAS2で開発され、現在Gulfstreamパネルで採用されている新しいコンセプトは、「直交補強された突合せ継手」と呼ばれるものです。溶接されたフレームのあるスキン。」この説明を展開すると、3つの主要な設計機能と、それらを実装するために必要な製造開発が明らかになります。(1)オルソグリッド、(2)突合せ継手、および(3)溶接技術です。
オルソグリッド
パネルの強度要件は、完全に相互接続された直交グリッド補強によって部分的に満たされます。このオルソグリッドは、マウスの穴に関連するピーク荷重を排除し、剥離力が拡大されるポイントの設計を取り除きます。オーソグリッドは、連続した縦方向のストリンガーと、2つの異なるコンポーネントで構成されるフレームで構成されています。不連続であるが接続された円周方向のブレードストリンガーと、これらの上に溶接されたフレームです。
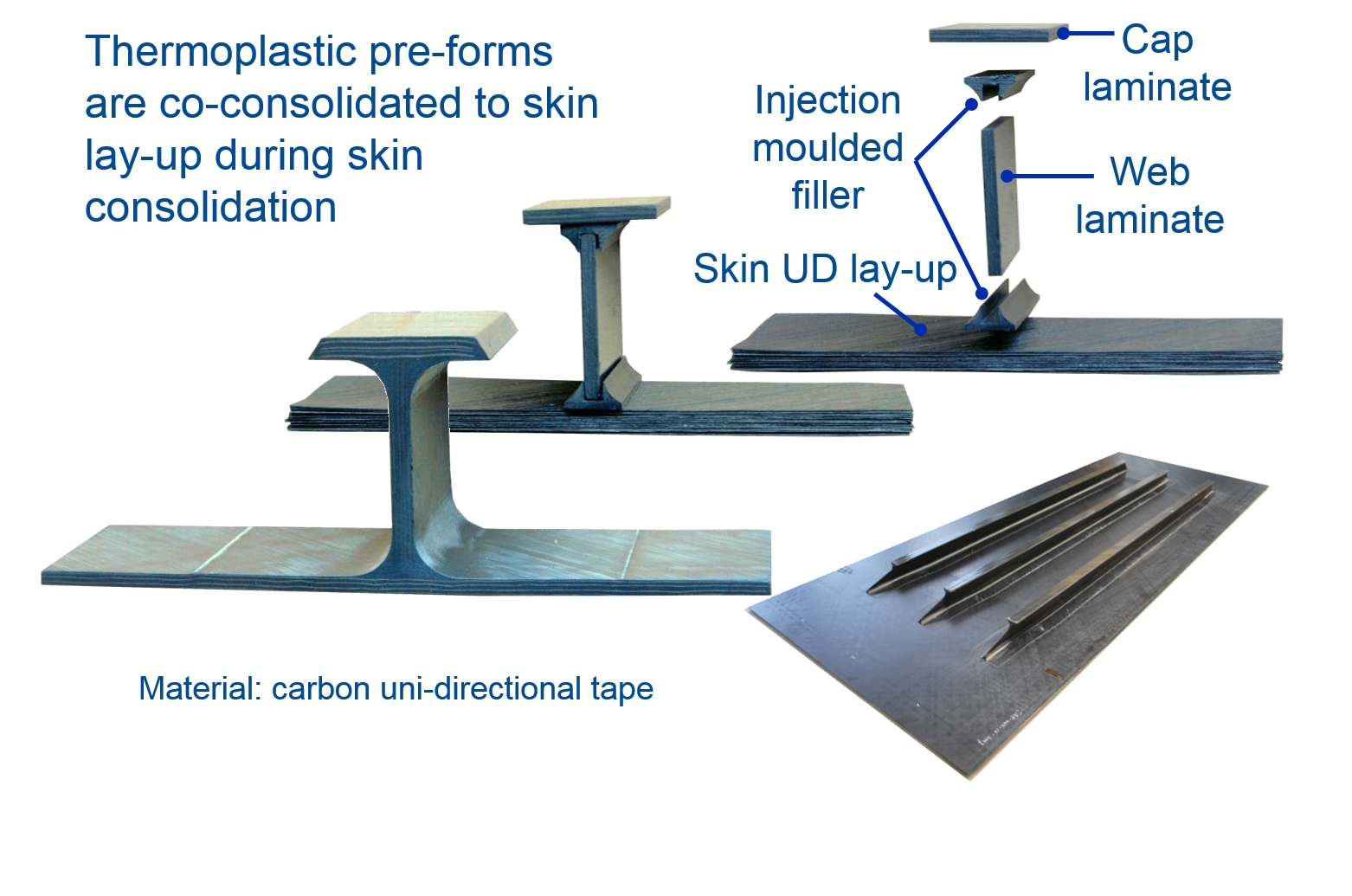
費用効果の高い突合せ継手。 GKN Fokkerは、ストリンガーウェブとキャップ(ここではTストリンガー、Gulfstreamパネルに組み込まれている)に費用効果の高い短繊維射出成形要素と連続繊維フラットラミネートを使用して、オルソグリッドとオルソグリッドとスキンの接合を可能にする突合せ継手を革新し、特許を取得しました同じ技術のLストリンガー)。ソース| GKNフォッカー
したがって、これは、長年のオルソグリッド開発の間に進化した胴体補強材設計の新世代を表しています。当初、GKN Fokkerは、縦方向と円周方向の両方の部材のキャップが連続していて、コーナーで重なっているTストリンガーを使用していました。ただし、フレームとの接合には、円周キャップの取り外しが必要でした。したがって、TストリンガーはLストリンガーになり、フレームはフレームが溶接された円周方向のブレードストリンガーになりました。
縦方向と円周方向の両方で使用される湾曲したストリンガーは、ツールのリリースをはるかに困難にするため、別の変更が必要です。したがって、Lストリンガーは、キャップとウェブの角度が90度を超えるように設計されているため、ツールピースは常にストリンガーグリッドから横にスライドできます。
バットジョイント
GKN Fokkerは、オルソグリッドの設計だけでなく、グリッドの新しい製造アプローチや、グリッドとスキンの結合メカニズムも開発しました。 「グリッドの製造には法外な費用がかかる可能性がありますが、当社のグリッドはフラットラミネートと単純な射出成形の「フィラー」で構成されています。」
より具体的には、GKN Fokkerは、特許取得済みの突合せ継手技術をGulfstreamパネル(以前のTAPASパネルにも)に適用しました。 TまたはLストリンガーコンポーネントのウェブとキャップ、およびブレードストリンガーコンポーネントは、フラットカーボンファイバー/ PEKKラミネートからウォータージェットカットされたプリフォームから製造されます。接合要素(スキンからウェブおよびウェブからキャップ)は、短繊維カーボン/ PEKK材料から作られた射出成形されたパイ型フィラーです。樹脂と炭素繊維のタイプはどちらもグリッド部材のものと一致します。
スキンとオルソグリッドは、インバーインナーモールドライン(IML)ツールで統合されています。ツールは、オルソグリッドコンポーネントとツールブロックがロードされる溝を備えています。次に、AFPで形成されたスキンをIMLに配置し、アセンブリ全体を袋に入れてオートクレーブで固めます。
溶接
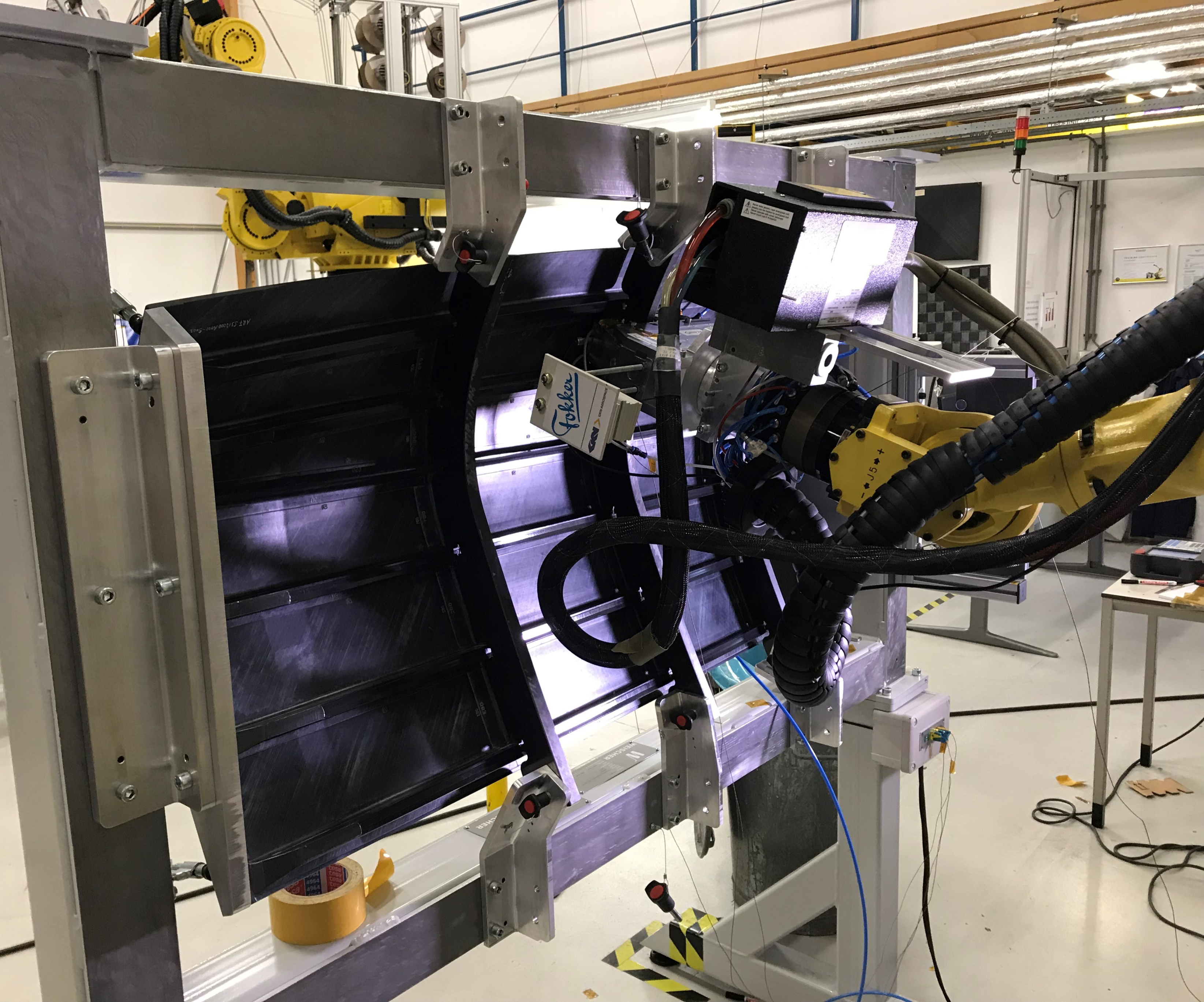
自動溶接。 GKN Fokkerは、熱可塑性複合材の胴体パネルの経済的な実現可能性に貢献し、ロボット溶接技術を開発して採用しました。ソース| GKNフォッカー
オーソグリッドと突合せ継手の設計の組み合わせにより、溶接によるオルソグリッドとフレームのファスナーなしの接合が可能になります。誘導、伝導、超音波溶接技術など、いくつかの溶接技術がTAPAS2フェーズ中にTAPASチームメンバーによって開発されました。ガルフストリームパネルは、フレームウェブを円周方向のブレードストリンガーに接合するために伝導溶接を採用しました。このタスクは、ロボットに取り付けられた溶接ヘッドを使用して実行されます。これは、費用効果の高い製造可能性に貢献するもう1つの開発です。
いくつかのステップ
GKN Fokkerは2017年にガルフストリームとのコラボレーションを開始し、胴体パネルの設計コンセプトを作成しました。 2018年と2019年には、いくつかの湾曲したパネルの設計と製造が行われ、今年のJECワールドで画期的な最初のパネルデモンストレーターが展示されました。
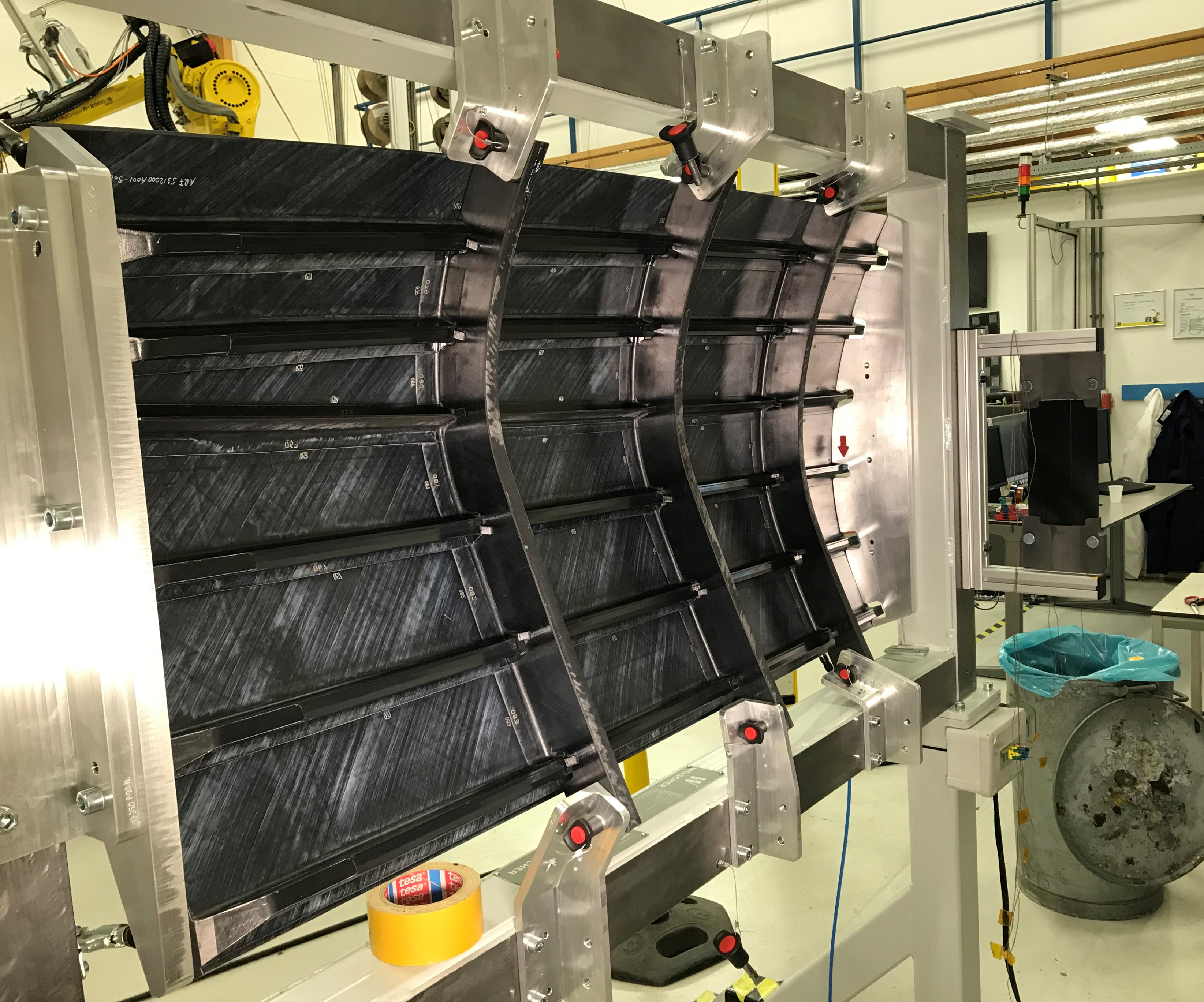
完成したコンポーネント。 フレーム要素が円周方向のブレードストリンガーに溶接されているため、ガルフストリーム胴体パネルは、熱可塑性複合材の胴体の製造に向けて取り組んでいるため、テスト、評価、および継続的な開発の準備ができています。ソース| GKNフォッカー
GKN Fokkerはパネルの構築を続けており、今年後半にTRL4(コンポーネント検証)を達成する予定です。 「私たちは現在、完全な成熟への道を話し合っています」とOffringaは報告します。パネルの設計は特定のプラットフォームを対象としていないことを指摘し、Chapmanは、パネルのテストがガルフストリームの材料特性と性能の理解を深めるのに役立つと報告しています。ジェットの性能、製造コスト、使用コスト、耐久性など、熱可塑性複合材料の一次構造の幅広いビジネスケースについて、チャップマン氏は次のように述べています。今のところ、私たちの焦点は、これらの複雑な形状を費用効果の高いものにすることにあります。」
樹脂