FRACAS:機器の故障を友達にする方法
失敗はしばしばメンテナンスの汚い言葉です。機器が故障すると、あなたの部門はかみ砕かれます。また、ダウンタイムメトリックで測定されると、あらゆる機器が究極の罪を犯します。
それは非生産的です。さらに悪いことに、それは不公平です。アセットの古さ、デザイン、ユーザーエラーなど、制御できないものがいくつかあります。そして、失敗は実際には貴重なリソースになる可能性があります。
「改善には失敗が必要です」と、Fiixのソリューションエンジニアであり、元産業およびメンテナンスエンジニアであるThibautDrevet氏は述べています。 「障害は、保守しているシステム、それらがどのように動作し、どのように保守できるかを理解するのに役立ちます。」
この記事では、FRACASを使用して障害の力を活用し、それを使用してビジネスの生産量を増やす方法について説明します。
FRACASとは何ですか?
FRACASは、障害の報告、分析、および修正アクションシステムの略です。これは、次の3つの主要コンポーネントを使用して機器の障害を制御および排除するための閉ループレポートシステムです。
- 障害の報告(資産の障害の特定)
- 障害分析(障害からの学習)
- 障害の修正(障害を修正し、再発を防ぐための手順を実行します)
FRACASは、機器のパフォーマンスの履歴を考慮に入れて、一般的な障害を見つけ、将来の故障を処理するための最良の方法を決定します。また、設計からスケジューリングまで、信頼性の維持戦略についても通知します。
FRACASループを使用してFRACASを作成する方法
FRACASループは、障害の報告、分析、および修正に役立つ一連のプロセスです。これらのプロセスは常に繰り返されるため、障害を継続的に見つけ、学習し、修正することができます。
FRACASループには5つの主要なアクティビティがあります:
- 障害モードと影響分析
- 障害コードの作成
- 作業指示分析
- 根本原因分析
- 戦略の調整
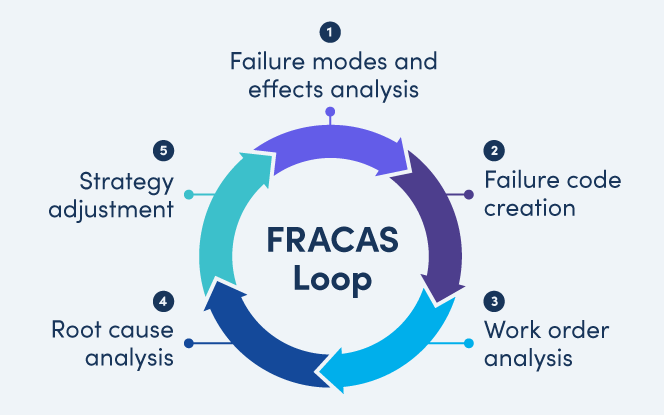
故障モードと影響分析
<図>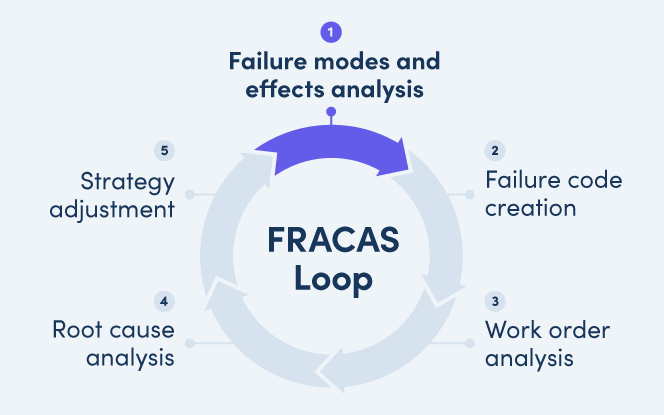
故障モードおよび影響分析(FMEA)は、最悪の事態が発生した場合の計画です。これは、機器が故障する可能性のあるすべての方法、各故障の影響、およびそれに対する対処法のリストです。
FMEAは、10の主要な要素で構成されています。
- アセットコンポーネント
- 潜在的な障害モード
- 潜在的な障害の影響
- 失敗の重大度
- 考えられる原因
- 予想される障害の頻度
- 障害を検出して防止するための現在のプロセス
- 障害の検出可能性
- 失敗の総リスク
- 推奨されるアクション
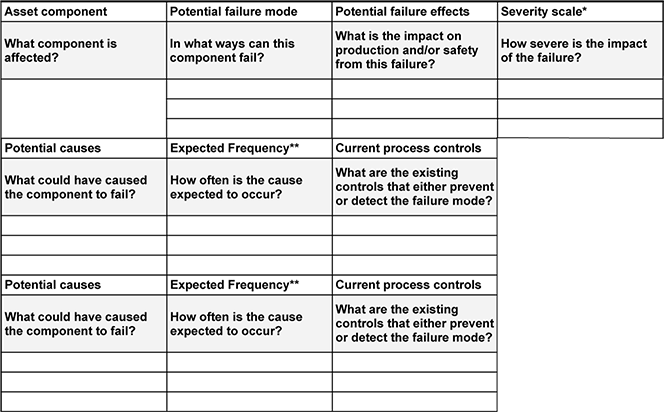
ここから独自のFMEAテンプレートをダウンロードします
FMEAは、障害のベースラインです。すべてのシナリオがレイアウトされているため、資産の重要度、影響、頻度、および必要なリソースに基づいてアクションに優先順位を付けることができます。それは生きた文書でもあります。施設での障害とそれを排除する方法について詳しく知ると、FMEAは変更を反映するように変更されます。そのため、FRACASループは常にこのステップに戻ります。
障害コードの作成
<図>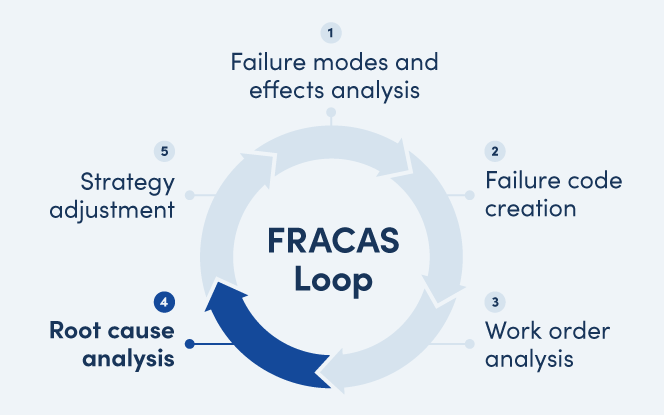
障害コードは、機器の問題を、部品、欠陥、および原因を特定する非常に短い説明に変換します。たとえば、可変速移送コンベヤの障害コードは、ベアリング、摩耗、潤滑不足などです。
しばらく前に障害コードの完全な要約を行いましたが、ここにいくつかの簡単なベストプラクティスがあります:
- 各部分に異なる命名規則があることを確認してください。 2つの類似したコンポーネントが混同されると、さらに大きな問題が発生する可能性があります。
- 欠陥をカテゴリに分類して、物事をシンプルかつ明確に保ちます(つまり、摩耗、過熱などの状態に基づいて)。
- CMMSでプリロードされたコードを使用している場合は、最も一般的なコードのみを使用してください。通常、10を超えるものは多すぎて、技術者は適切なコードを見つけるのに時間を費やすのではなく、「その他」のオプションを選択することになります。
- FMEAを使用して、主要な障害コードの初期リストを作成します。このリストを技術者に確認してください。
障害コードを追跡すると、時間の経過に伴う障害の傾向を確認するのに役立ちます。これにより、最も頻繁に発生し、会社に最も損失をもたらすものを特定できるため、優先順位を付けてそれらを一掃する計画を立てることができます。
作業指示分析
<図>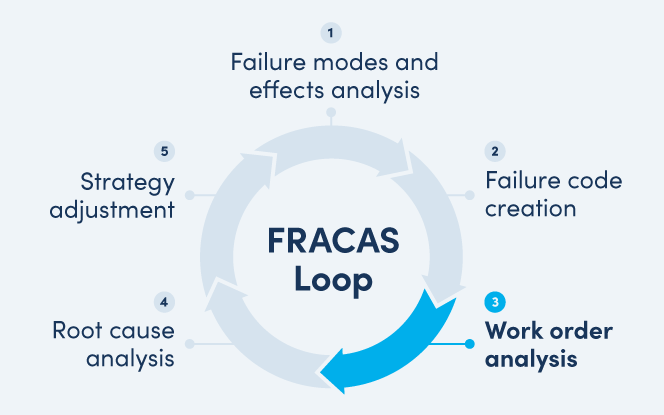
1つの失敗は迷惑です。同じ種類の障害が多数発生する傾向にあるため、チームに莫大な費用がかかり、スケジュールが中断され、生産の悪い面に陥ります。作業指示分析は、これらの傾向を見つけて解決するのに役立つFRACASループのステップです。
作業指示書の障害データを分析する最も簡単な方法の1つは、完了ノートで障害コードとその頻度を確認することです。たとえば、6か月間に合計12回の障害が発生した同じ機器が4つあるとします。これらのマシンは金儲けであり、修正に長い時間がかかるため、故障率はページから飛び出します。
これらの障害を見ると、最も一般的な障害コード(12個のインスタンスのうち10個)がミスアライメントによる発作を引き起こしていることがわかります。これで、どの問題に焦点を当てるべきかがわかりました。また、応答を測定するためのベースラインもあります。この障害のインスタンスがさらに6か月で2つまたは3つに減少した場合、何をしたとしても機能しています。
作業指示書の障害データを使用する方法は他にもたくさんあります。以下でそれらのいくつかについて説明しますが、作業指示データの検索と使用に関するこの短いガイドも確認できます。
根本原因分析
<図>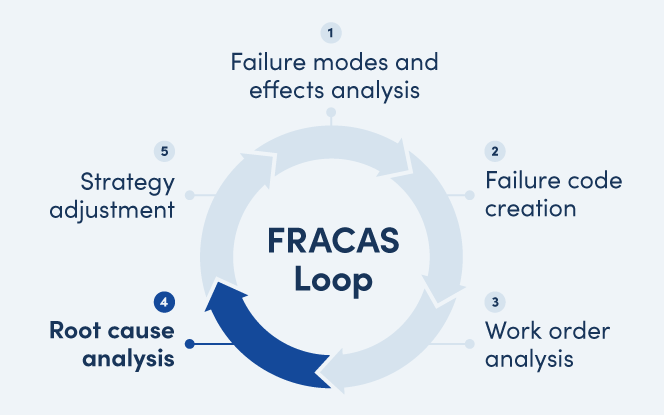
根本原因分析はトラブルシューティングツールではありません。これは、トラブルシューティングから価値を引き出すためのツールです。あなたとあなたのチームは、RCAなしでずれたベアリングを修正することができます。ただし、修正する必要があるのは2回以上です。つまり、時間、予算、部品を複数回使用することを意味します。
FRACASは、お金をポケットに戻し、スケジュールに時間を戻すという長期的な改善を行っている場合にのみ価値があります。それがRCAの目的です。
根本原因分析を行うための戦略を取り上げ、ダウンロード可能な根本原因分析テンプレート全体を作成したため、この記事ではRCAを実施するためのより細かいポイントについては説明しません。ただし、前のセクションのベアリングの位置がずれている場合に、RCAをFRACASに統合する方法の一例を次に示します。
- ベアリングの位置がずれているのはなぜですか?シャフトの位置がずれているため。
- シャフトの位置がずれているのはなぜですか?機械が不適切に組み立てられたため。
- 機械が正しく組み立てられなかったのはなぜですか?技術者が急いで組み立てたからです。
- 技術者が急いで組み立てたのはなぜですか?仕事に適切な時間が与えられなかったからです。
- 仕事に十分な時間が割り当てられなかったのはなぜですか?生産前の定期メンテナンスの時間枠が小さすぎたためです。
RCAを実行するときに覚えておくべき最も重要なことは、結論に飛びついて調査を短くしないことです、とThibautは言います。
「単純な原因は資産が故障した理由であると簡単に推測できます」とThibaut氏は言います。 「だからこそ、RCAに貢献するには多様な人々が必要であり、さまざまな視点やアイデアを持ち、これらの仮定を回避する必要があります。」
戦略調整
<図>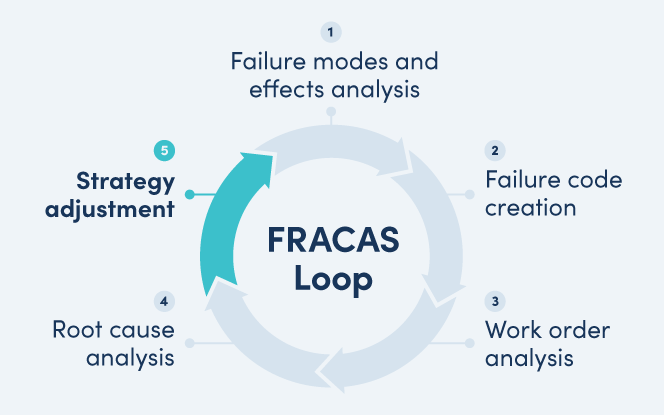
FRACASループで収集したすべての洞察は、それらに基づいて行動しなければ、それほど多くはありません。行動を起こすことは、必ずしも大きな変化についてではありません。作業指示書に潤滑を適用するためのより具体的な指示を追加するのと同じくらい小さい場合があります。ただし、チームのトレーニングを受けていない専門的なタスクを行うために請負業者を雇うなど、大きな調整が必要になる場合があります。
それぞれの対応は異なりますが、長期的に失敗を修正して防止するのに役立ついくつかの一般的な戦略があります。
- プロセスに技術者を含める:技術者は、思いもよらなかったソリューションを提供する場合があります。変更を加える理由と、それがどのようにメリットをもたらすかを正確に伝えます。これにより、バイインが増加します。そして、変更の結果を彼らに示してください。変更されたプロセスにより、営業時間外のコールインが40%減少した場合は、そのことを知らせてください。それは彼らの仕事への感謝を示し、将来の変化への賛同を向上させます。
- 結果を監視する:戦略が機能していない場合は、戦略を早期に把握し、適切になるまで調整を続けることができます。ドミノ効果に注意してください。変更は、操作の1つの領域には適しているかもしれませんが、別の領域からは取り除いてください。最後に、成功事例を追跡して、必要なときにマネージャーから賛同と予算を獲得します。
- 小さく始めてゆっくりと拡大する:大きな変更が必要な場合は、一度にすべてを行わないでください。全体的な変化の1つに焦点を当てます。たとえば、(生産を犠牲にして)機器のメンテナンス時間を数時間延長しようとしている場合は、1台のマシンから始めます。計画の実施が容易になるだけでなく、人々が変更に適応する時間を与えることができます。
ループを閉じる
戦略を調整した後、FRACASループが最初からやり直します。失敗を見つけて修正し続けることができるように、戦略を完全に一周させるいくつかの方法があります:
- FMEAを更新して、発見した新しい障害と、行った変更の影響を反映します。障害の発生頻度が低いか、FRACASの作業に基づいて特定の障害を処理するための新しい手順がある可能性があります。
- 障害コードを監査します。発見した新しい一般的な障害コードを追加し、頻度が低くなったコードをすべて削除します。使用しているコードが、関連性があり、明確で、有用であることを確認してください。
- 行った変更の影響を追跡するためのレポートを作成します。対処した領域で障害が発生する頻度は低くなっていますか?これは、コストやスケジュールなどにとってどのような意味がありますか?
FRACASの適切なデータを取得する方法
データは、FRACASのすべてのステップをガイドします。また、他の優れたガイドと同様に、データは信頼できるものである必要がありますが、常にそうであるとは限りません。あなたの数字は決して防弾ではないかもしれませんが、いくつかの重要な行動で情報の質を向上させることができます。
メンテナンスの価値を理解する文化を作りましょう
ほとんどのデータエラーは、技術者が急いでいるときに発生します、とThibautは言います。彼らは次の仕事に急ぐ前に仕事を完了する時間がほとんど与えられていません。技術者は、このような状況で生産の怒りに直面するのではなく、記憶があまり良くない1日の終わりにデータ入力を任せます。または、完全にスキップします。
工場の全員がメンテナンスの価値を理解している健全な文化は、これに対抗するのに役立ちます。
「メンテナンスは生産の敵ではないことを誰もが理解する必要があります」とThibaut氏は言います。
「メンテナンスが必要で有益であることを誰もが理解すると、技術者は時間をかけてデータを適切に記録できます。」
明確で記入しやすい作業指示書を作成する
悪いデータを人為的ミスのせいにするのは簡単です。しかし、ヒューマンエラーには常により深い原因があります。最も一般的なものの1つは、不明確で圧倒的な作業指示です。
たとえば、写真、図、または適切な命名規則がないと、コンポーネントを誤認しやすくなります。これにより、その資産および同様の資産の将来の障害分析とレポートが破棄される可能性があります。また、失敗を報告してフォローアップするための明確なプロセスがないと、通常、アクションはまったく実行されません。
効果的なFRACASをサポートする世界クラスの作業指示書を作成するための優れたスターターパックは次のとおりです。
- 基本をマスターする:メンテナンス作業指示書
- 目標を達成するのに役立つ作業指示書を設計するための簡単なガイド
- メンテナンス作業指示書テンプレート
- 機器のメンテナンスログテンプレート
- 予防保守チェックリスト
自動化と統合
優れた作業指示書を作成しても、人的エラーを完全に排除することはできません。誰でも間違いはある。しかし、テクノロジーはそれらを少なくします。機器に状態監視ソフトウェアをインストールすると、手動のデータ入力が自動測定に置き換わります。
手動でログに記録すると、壊れた資産のメーターの読み取り値を間違えるのは簡単です。たぶん、マシンにたどり着くのに5分かかりました。その5分間で、メーターの読み取り値が変化しました。今、あなたは失敗を間違った測定に関連付けています。
メーターの読み取り値をリアルタイムで記録するソフトウェアを使用すると、このリスクを取り除くことができます。障害発生時の正確な読み取り値を示しているため、正しいと確信できます。このシステムをメンテナンスソフトウェアと統合することにより、このすべての情報を1か所で収集して分析できます。メーターの読み取り値に基づいてメンテナンスをすぐにトリガーできるという追加の特典もあります。
データを頻繁に監査する
データをチェックし、データが正確であることを確認するために、毎月時間を取っておきます。これは、すべての作業指示書と番号を調べて確認することを意味するものではありません。スポットチェックを実施し、危険信号を探し、技術者に相談して、鉛筆のむち打ちが懸念される場所を特定します。指さしは避けてください。鉛筆のむち打ちは、多くの場合、技術者の性格やスキルレベルよりも外部の障害物に関するものです。いくつかの良い質問が含まれます:
- 不要と思われる検査や作業はありますか?このタスクを削除するか、頻度を減らすか、重要な理由を説明してください。
- ログに記録するデータと、それが重要である理由を明確にしていますか?何をどのように測定するか(つまり、数時間ではなく数分で測定する)について、全員が同じページにいるようにします。
- データは簡単に記録できますか?そうでない場合、なぜですか?紙の上では理にかなっているが、実際には機能しないプロセスを明らかにします(つまり、定量化が難しい障害コードや測定値の長いリスト)。
FRACASの使用方法:結果を出すのに役立つ5つのメンテナンスレポート
失敗を見つけて修正するのは素晴らしいことです。あなたの会社がより多くのものを生産し、より多くのお金を稼ぐことを妨げている失敗を見つけて修正することはさらに良いことです。そのためには、この種の資産の障害を検出するレポートが必要です。開始する5つは次のとおりです。
- 起動後の失敗
生産を開始する前に生産を停止する障害は、運用を大幅に遅らせます。このレポートは、これらの有害な障害を特定し、防止するのに役立ちます。 - 障害コードによるメンテナンスコスト
クローズド作業指示書のすべての障害コードの人件費と部品のコストを集計して、コストが高いものを特定し、優先順位を付けます。 - 障害コードによるメンテナンス時間
同じ障害を何度も修正することに時間を費やすと、他の場所でのダウンタイムを防ぐ可能性のあるタスクに時間を費やすことができなくなります。 - スケジュールされたメンテナンスとスケジュールされていないメンテナンスで見つかった障害
このレポートは、コストのかかる事後対応型メンテナンスの原因となる繰り返し発生する障害に優先順位を付けるのに役立ちます。 - シフトまたはサイトによる障害
このレポートは、プロセスまたはトレーニングに存在する大きな問題を特定するのに役立ちます。これらの問題に対処すると、大きな利益につながる可能性があります。シフトまたはサイトの故障率が低い場合は、彼らがどのように異なっているかを調べて、すべてのシフトまたはサイトにそれを複製することができます。
FRACASの使用方法:実際のビジネスの例と使用例
FRACASは、常にコンピュータ上の別のファイルになるリスクがあります。それはあなたとあなたのチームの働き方を変えるからです。それは簡単ではありません。 FRACASが解決する問題を理解することは、これらの増大する痛みを和らげるのに役立ちます。 FRACASが、メンテナンスチームの最大の苦痛のいくつかをターゲットにするのにどのように役立つかについての実際の例を次に示します。
- FRACASを通じて、古い部品を修理や交換に使用すると、機器が最も頻繁に故障することがわかりました。また、これらの障害が全体的なメンテナンスと生産の損失にどれほどのコストをかけているかを確認できます。これらの失敗を排除するために、より高い在庫予算を取得するためのケースを作成できます。
- 以前はめったに故障しなかった資産がより頻繁に故障し、その理由がわかりません。 FRACAS分析により、障害が1つのコンポーネントで発生しており、3か月前に開始されたことが明らかになりました。そのとき、ラインはメンテナンスが認識していなかったさまざまな製品仕様を使用し始め、それがマシンのセットアップに影響を及ぼしました。複数のサイトでのダウンタイムを削減する回線変更を通信するための新しいプロセスを開発します。
- 障害コードを確認すると、3つの一般的なタイプの障害が特定されます。今四半期に取り組むリソースは1つだけです。 FMEA、コストレポート、および根本原因分析に飛び込んで、最大の影響を与える障害を見つけます。この成功の後、あなたはあなたが見つけた他の失敗を修正するためにもっと技術者を雇うための予算を確保します。
結論
FRACASの構築には、データ、時間、コミットメントの3つの要素が必要です。根本的な原因を見つけて対処するには、失敗に関する多くのデータが必要です。このデータを取得するには時間が必要です。また、正確なデータを収集してその教訓を適用するには、長期的な取り組みが必要です。これらの要素を習得するには時間がかかるため、小さなことから始めて、勝利を追跡し、すぐに結果が表示されない場合でも諦めないでください。この取り組みは、長期的な投資収益率に見合う価値があります。
機器のメンテナンスと修理