DLR Institute of Structures and Designは、熱可塑性複合材の胴体構造の成熟度を高めます
「LuFoV-3TB-Rumpf」プロジェクトの一環として、熱可塑性プリプレグラミネートと抵抗溶接のオートクレーブフリーの統合がさらに開発され、将来の航空機フューズラグのテクノロジーブリックとして検証されています。この作業は、シュトゥットガルトのドイツ航空宇宙センター(DLR)、構造設計研究所(Institute BT)によって実施されており、エアバスや他の研究機関を含む航空宇宙産業のパートナーと協力しています。

DLR Institute BTは、スキン、ストリンガー、フレーム、クリートで構成される、完全に統合された胴体交差点を実証しました。デモンストレーターは、脱オートクレーブ(OOA)で統合された湾曲したスキンと、統合されたストリンガー、および抵抗溶接によるフレームとクリートの統合に基づいています。溶接部は機械的試験によって特徴付けられており、溶接線は光学顕微鏡を使用してさらに調べられました。
TB-Rumpf成熟OOA統合および溶接
連続繊維強化高温熱可塑性プラスチック(ポリアリールエーテルケトンやPAEKなど)で作られた大面積部品の圧密の最新技術は、オートクレーブ圧密です。ただし、最適化されたプロセス設定と調整されたプロセス制御により、温度と真空圧のみを使用して完全な統合を実現できます。自己加熱型またはオーブンを使用すると、オートクレーブが不要になり、コスト面でのメリットが得られます。 TB-Rumpfプロジェクトは、VCT(Vacuum Consolidation Technique)と呼ばれるプロセスを成熟させ、可能な最大ラミネート厚さを含むプロセス限界を決定することを目的としています。
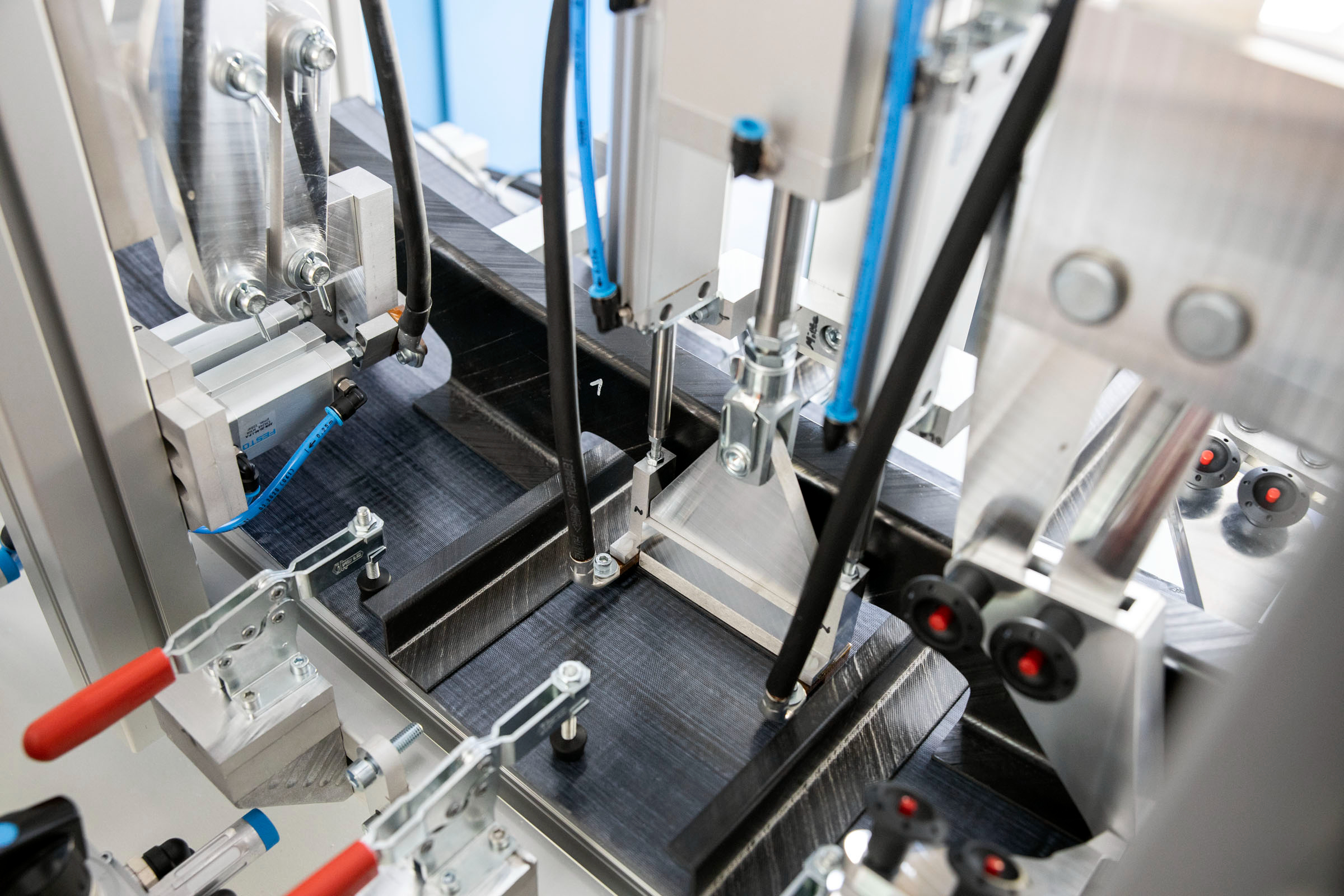
高度な熱可塑性複合材料の将来の用途のためのもう1つの重要な技術は、組み立てのための溶接です。 DLRとエアバスは、高強度構造を実現できるため、抵抗溶接を主要な技術として認識しています。 TB-Rumpfプロジェクトでは、抵抗溶接プロセスと必要な溶接要素が最適化されています。得られたデモンストレーターは、ジョイントと溶接された複合ラミネートの機械的性能を検証するために構造的にテストされます。
真空圧密技術(VCT)の調査
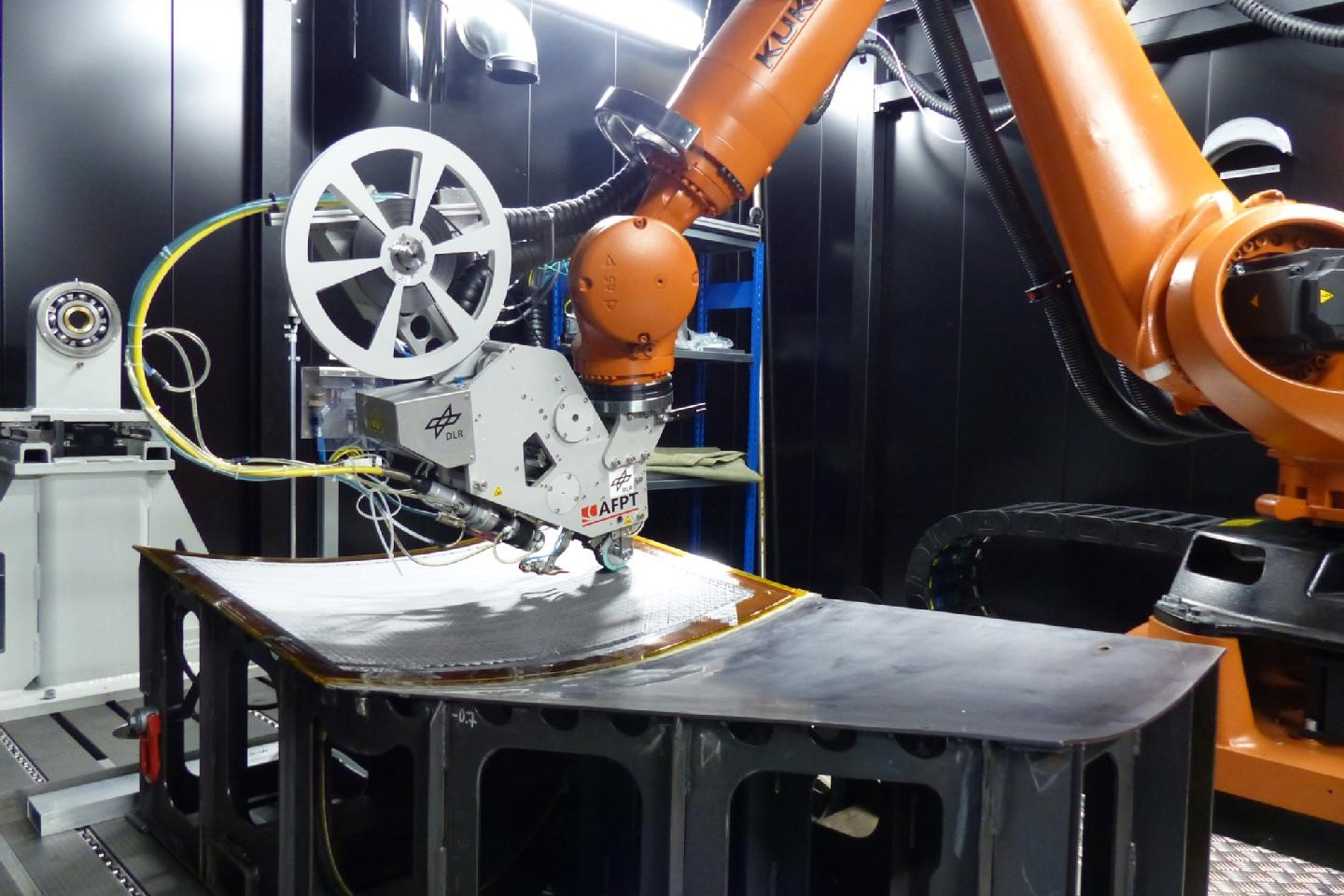
DLR InstituteBTのプロジェクトリーダーであるMatthiasHornは、TB-Rumpfデモンストレーターが一方向炭素繊維強化低溶融ポリアリールエーテルケトン(LM-PAEK)を使用していると説明しています。この熱可塑性複合テープは、テープを加熱するためのAFPT(Doerth、Germany)エンドエフェクターと6キロワットのレーザーを備えたKUKA(Augsburg、Germany)ロボットを使用して実現された自動ファイバー配置(AFP)を使用して処理されます。
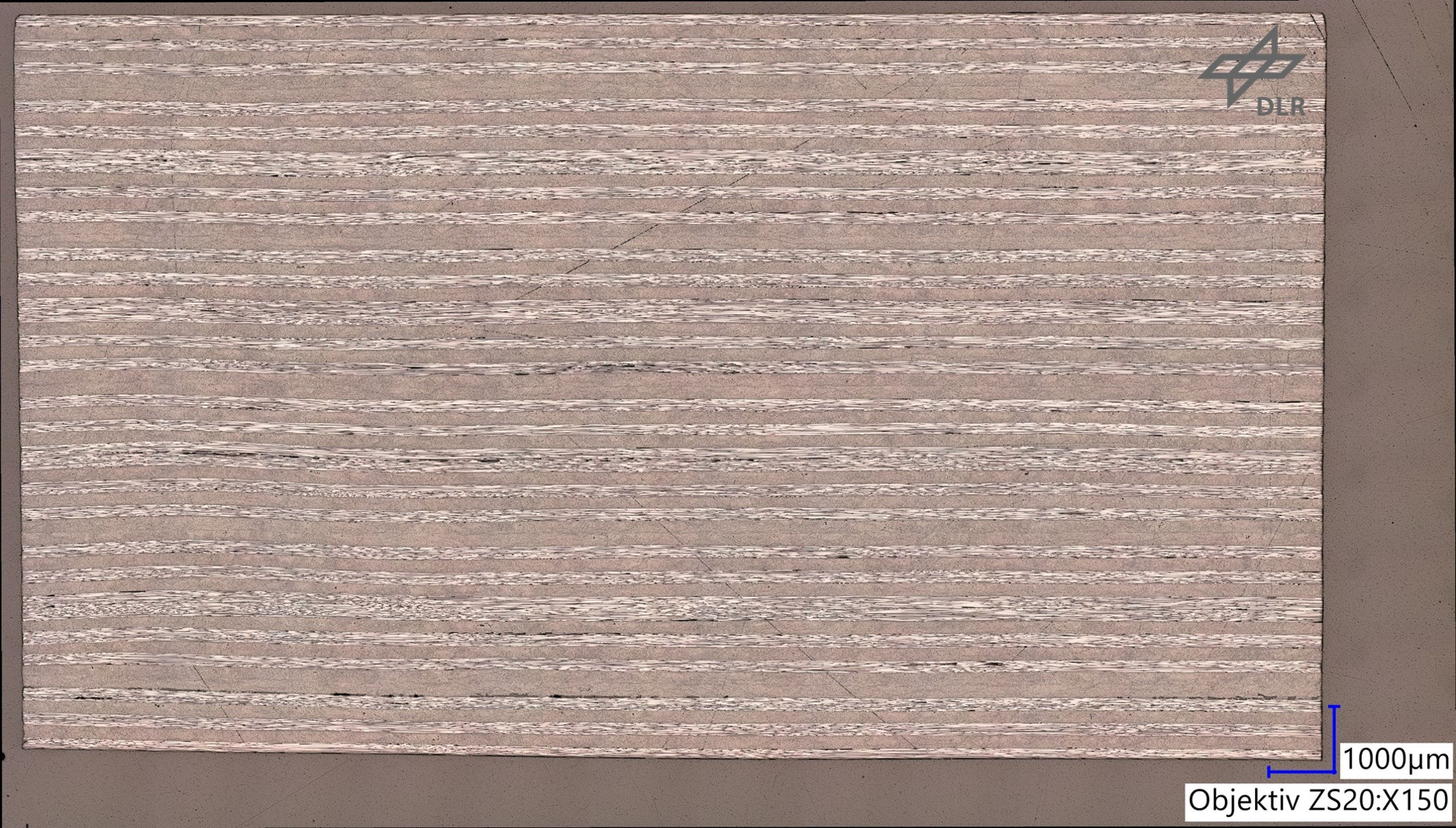
VCTを使用したOOA統合: 「目標は、厚いラミネートに対するこのプロセスの実現可能性を検証することでした」と、InstituteBTの研究者でTB-Rumpfの統合リーダーであるGeorgDollは述べています。 「私たちは、顕微鏡写真の断面と超音波検査によって検証された、細孔やその他の欠陥のない、最大11ミリメートルの厚さのラミネートで良好な結果を示しました。この成功の鍵は、最適化されたVCTセットアップ、調整された加熱サイクル、および均質で一貫したプリプレグ品質です。」
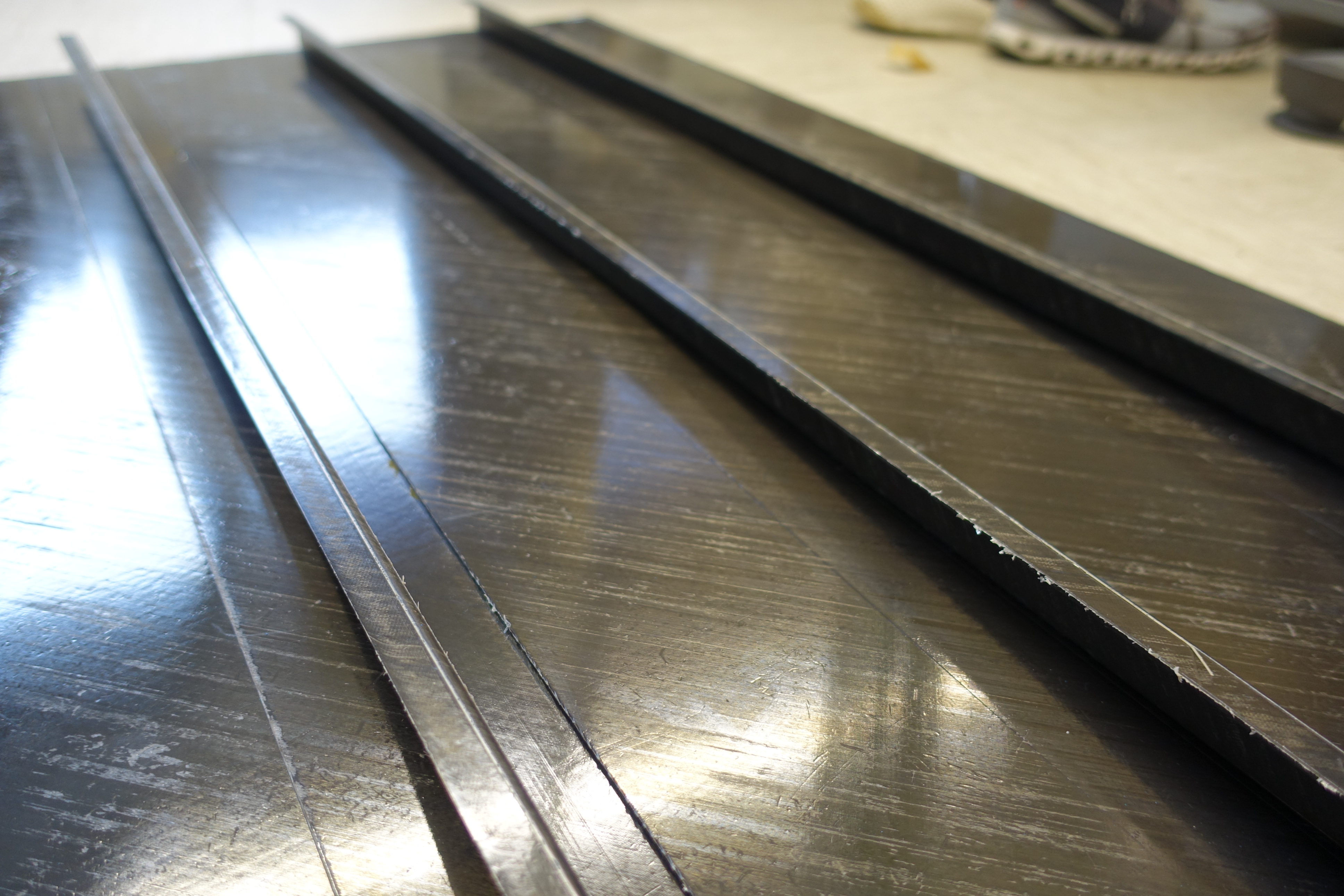
補強材要素のOOA共同統合: TB-Rumpfプロジェクトは、オートクレーブなしの胴体スキンパネルの製造にVCTを使用することに加えて、単一のVCTプロセスサイクル中にストリンガー補強材要素をスキンに直接統合するための共同統合の開発にも成功しました。
曲線および二重曲線形状のAFPレイアップ: VCTを補完するプロセスとしてのレーザーベースのAFPは、約800 x 1200ミリメートルの二重湾曲ラミネートを製造することにより、プロセスと材料の制限(最大テープステアリングなど)を含めて調査されました。これらの製造試験の結果を使用して、OOA統合と、二次操作なしでAFP中に達成される現場統合を進めることができます。
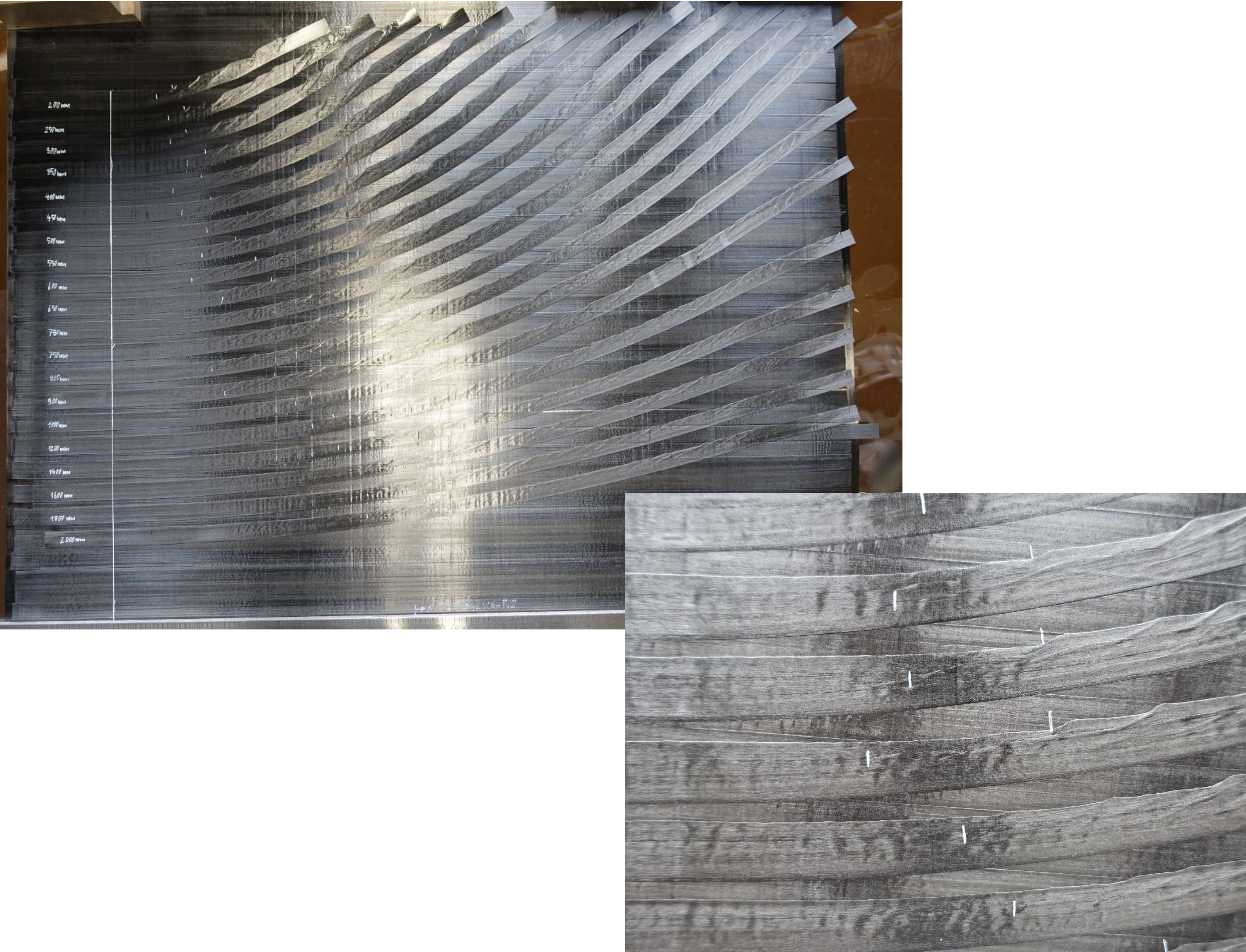
抵抗溶接
「構造胴体要素を統合し、将来の熱可塑性胴体コンセプトの生産を実現可能にするために、プロセスの堅牢性の向上と強度値の最適化に関して抵抗溶接を調査しました」と、溶接の研究所BT研究者でTB-RumpfリードのSimonBauerは述べています。 「焦点は、発熱体としての炭素繊維に基づく最適化された溶接要素のセットアップと、加熱サイクル、温度、圧力、電流、電圧などの最適な溶接パラメータと組み合わせた電気伝導の改善にありました。」クリートをフレームとストリンガーの両方に取り付けるために抵抗溶接が使用されました。フレームを皮膚に取り付けるためにも使用されました。
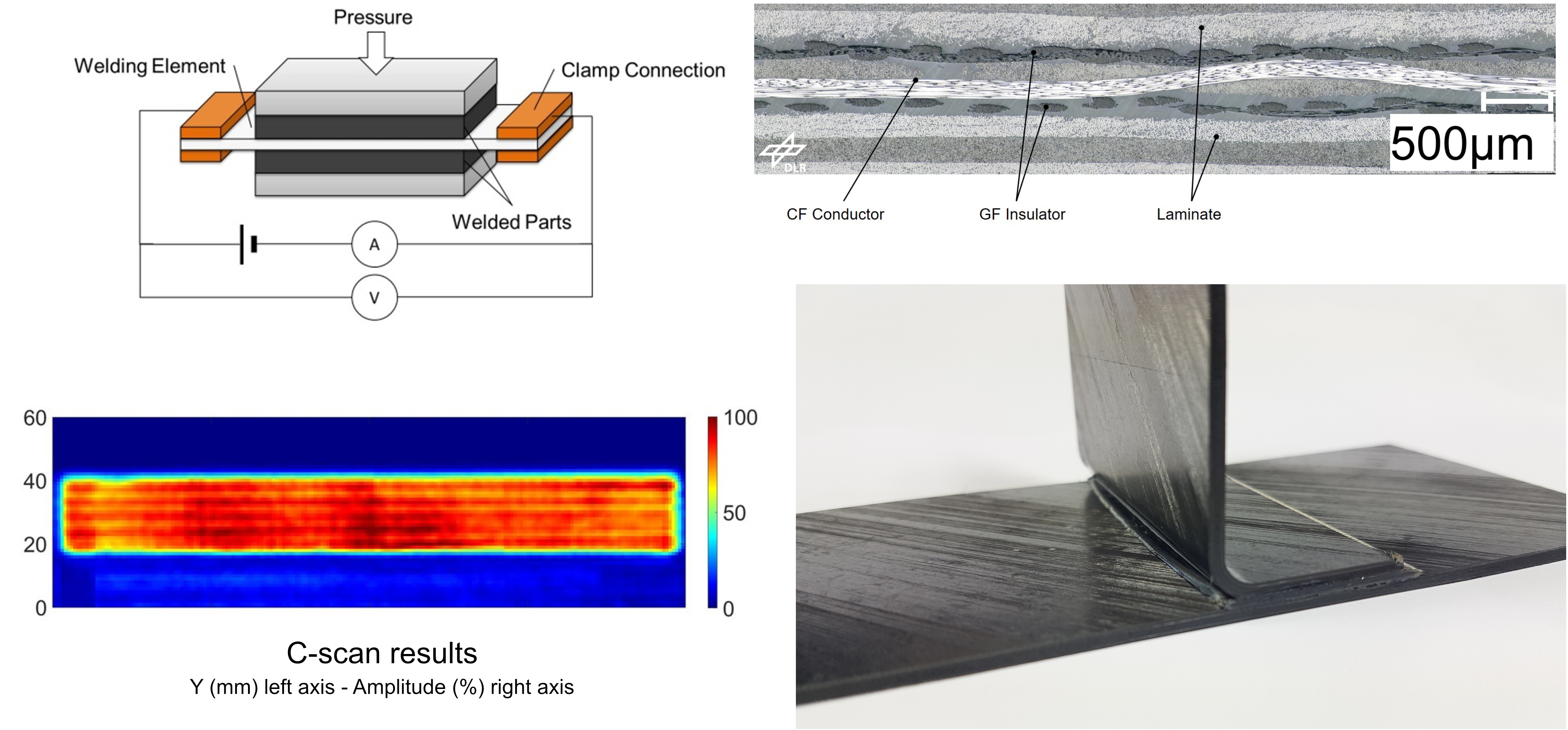
今後の胴体設計のためのテクノロジーブリック
「実証された技術の成熟度により、オートクレーブ外の圧密と抵抗溶接の両方が将来の胴体設計に重要な役割を果たす可能性があります」と、対応するエアバスプロジェクトの責任者であるポールイェルン博士は強調します。
技術をさらに産業用途に近づけるために、さらに挑戦的な側面が近い将来調査されるでしょう。真空統合の場合、サイズのスケーリングと二重に湾曲した輪郭への転送に焦点が当てられます。抵抗溶接の公差の側面と自動化の側面について説明します。
ここに示す結果は、ドイツ連邦経済エネルギー省が資金提供した連邦航空研究プログラムV-3の枠組みの中で、TB-Rumpf研究プロジェクト(FKZ:20W1721D)内で達成されました。
詳細については、dlr.de / btにアクセスしてください。
樹脂
- ポンプおよびバルブコンポーネントにおける熱可塑性プラスチックの設計上の利点
- ソルベイが熱可塑性複合材料の容量を拡大
- RECONTRASプロジェクトは、マイクロ波とレーザー溶接を使用してリサイクル可能な複合材料を取得することを検証します
- 熱可塑性テープは、複合エアロストラクチャーの可能性を示し続けています
- 使いやすいキットにより、複合構造の内野修理が可能になります
- 革新的な堆積技術を使用した複合アイソグリッド構造の開発
- 設計の革新により、複合医療テーブルの効率が向上します
- 明日のリブの翼:ワンショット、熱可塑性、OOA統合
- 熱可塑性複合構造が、セーフティクリティカルなブレーキペダルの金属に取って代わります
- コンソーシアムは、炭素繊維熱可塑性複合構造のソリューションを対象としています
- 熱可塑性複合材料の溶接