熱可塑性複合材料の熱成形のトラブルシューティング
注:この記事の情報と画像熱可塑性複合材料研究センター(TPRC)が教える「熱可塑性複合材料の高度な成形」コースから取得しました。
熱可塑性複合材料(TPC)は、航空宇宙およびその他の軽量アプリケーションでのより速い生産速度の要求で最初に有利になりました。ほんの数分で部品を製造することで、熱成形(スタンピングとも呼ばれます)が最も一般的な熱可塑性複合材料プロセスとなり、最初にフライング部品を大量生産しました(「熱可塑性複合材料ホットベッドの内部」および「熱可塑性複合材料のクリップ時間…」を参照)。
このプロセスは、ブランク(必要な層の向きを持つ事前に固められた熱可塑性複合ラミネート)から始まり、次のステップで構成されます(図1)。ブランクの準備(切断と固定)、ブランク加熱、金型への移動、ブランクの位置決め、成形、冷却、部品の離型、およびトリミング/仕上げ。熱成形プロセスは単純な概念ですが、再現性のある高品質の複合部品を実現するために対処する必要のある複雑さと課題が含まれます。
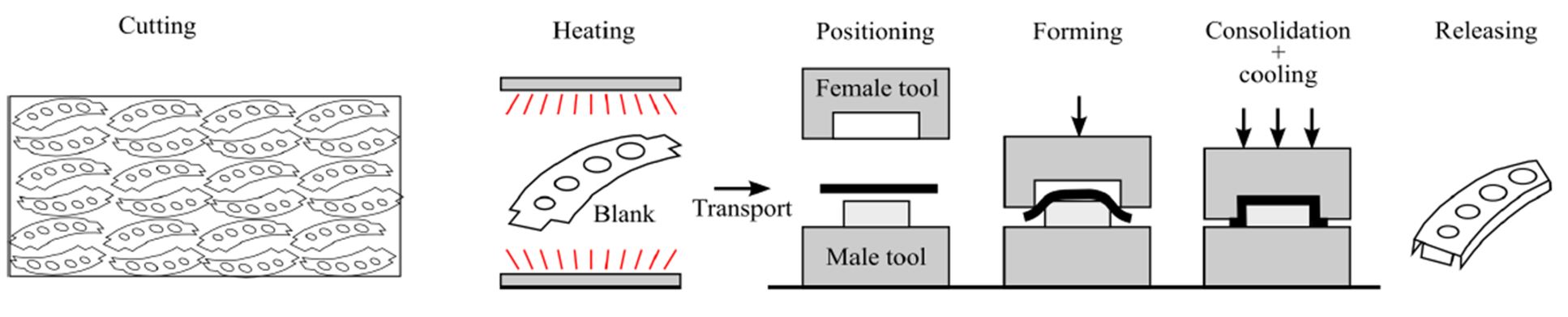
しわの回避
十分な予熱と高速転送。 ブランクの成形中、温度は溶融温度(T m )を超えたままにする必要があります。 )せん断変形を可能にするTPCマトリックスの。予熱段階から金型への移行中に、温度が大幅に低下する可能性があることを考慮に入れてください。3秒で40〜50°Cに達する可能性があります。したがって、予熱は、ポリマーがT m を超えたままになるように十分に高くする必要があります。 —またはガラス転移温度(T g )アモルファスポリマーの場合—転写後および成形中。コールドブランクは適切に変形せず、しわが発生します。ただし、ポリマーの劣化を防ぐために、ブランクを過熱しないように注意してください。
生地織りのスタイルとレイアップ。 ハーネスサテン(HS)生地は、面内せん断変形が容易であるため、ドレープ性が高く、しわを防ぐのに役立ちます。織物のドレープ性は、最高から最低まで、次のとおりです。8HS> 5HS> 2 x2ツイル>平織り。 5HSファブリックは、ドレープ性と機械的性能のバランスが取れているため、多くの場合、出発点として適しています。一方向(UD)補強材を使用して作成されたブランクは、面内せん断に抵抗する繊維間の摩擦が大きいため、HSファブリックよりもしわが寄る傾向があります。面内せん断を可能にすることは、特に二重に湾曲した表面でのUDブランクの形成を成功させるための鍵です。
[0、90、±45] s などのプライの向き 準等方性レイアップに見られるものは、しわを強化するせん断変形を抑制することができます。または、クロスプライ([0、90]など)のレイアップは、他のプライによってせん断が制限されないため、しわを防ぐのに役立ちます。
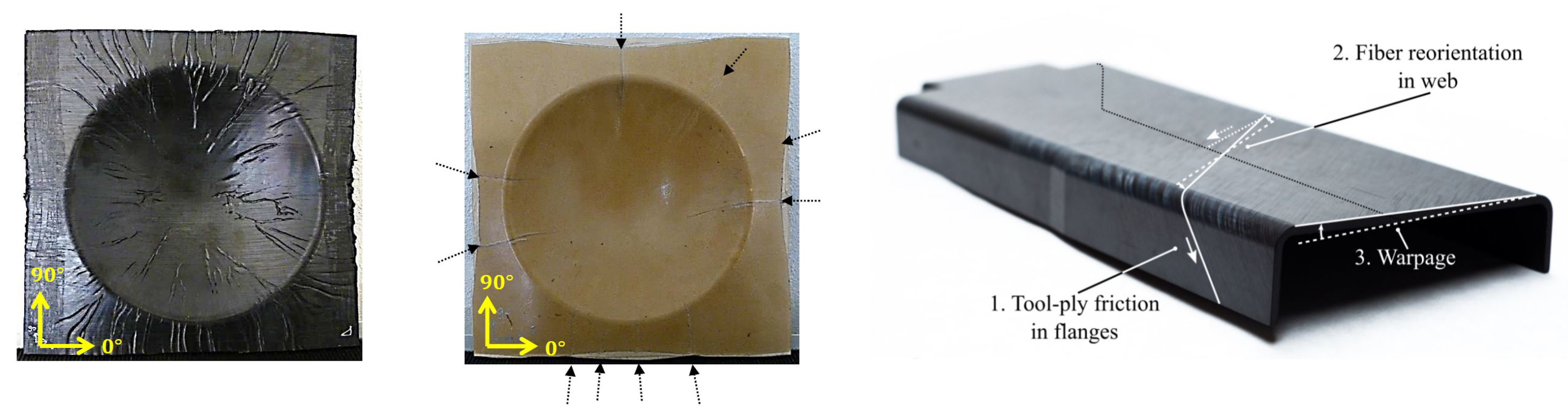
図。 2.しわや反りを避ける
半球部分には、UDブランクを使用した大小のシワが多数見られます(左) 、8HSブランクを使用すると大きなしわのみが表示されます(右) 。この複合スパーの反りは、フランジのツールプライ摩擦による繊維の再配向に起因していました。写真提供者:D.J。による「熱可塑性複合材料の成形限界」 Wolthuizen、et。 al。 (左 )およびTjitse K. Slangeによる「自動レイアップおよびスタンプフォーミングによるテーラード熱可塑性複合材料の迅速な製造」(右 。
空白の準備と固定。 グリッパーとテンショナーを使用して、面外に曲がりやすい領域でブランクを張力状態に保つことができます。最適化された構成を見つけるには時間がかかり、複数の反復が必要になる場合がありますが、プロセスシミュレーションソフトウェアを使用すると役立ちます。ブランクに適切な張力をかけることで、ブランクのたるみを防ぎます。これにより、転写および成形中に問題が発生する可能性があります。このような問題には、ブランクが金型に触れるのが早すぎることが含まれます。これにより、ドレープが発生する前に金型に材料が多すぎて、座屈やしわが発生する可能性があります。ブランクがたるんでヒーターに触れることもあり、ブランクに損傷を与えたり、プロセスを停止したりする可能性があります。
ブランクの最終的な形状を最適化し、ネットに近い形状にカットすることで、しわを防ぎ、スクラップを減らすことができます。カットやダーツは、繊維の応力を減らして成形を改善することにより、面外曲げを防ぐのにも役立ちます。
金型設計の課題を克服する
熱成形および同様の成形プロセスでは、金型自体に課題が生じる可能性があります。適切な金型設計は、金型コスト、加熱、部品の欠陥、離型の問題を回避するのに役立ちます。
金型工具材料。 熱成形ツールに適切な材料を選択するには、必要な金型温度(T 金型)に影響を与えるため、最終部品に使用される材料を検討してください。 )。たとえば、経験則に従って T モールド =(T m + T g )/ 2 、強化PPS(ポリフェニレンサルファイドT m )で作られた部品 =280°C)にはT モールドが必要です 約180°Cの。 (非晶性および半結晶性の熱可塑性ポリマーにはT g があります 、ただし、半結晶性ポリマーにもT m があります。 。)したがって、成形品を成形するために、加熱されたプレスまたは加熱された工具のプラテンから十分な熱を伝導するために金型が必要です。部品を効率的に冷却するには、伝導も必要です。ただし、T g がはるかに低い強化PMMA(ポリメチルメタクリレート)を使用して製造された部品の場合 (〜100°C)、室温の木製またはエポキシ工具で十分な場合があります。
その他の考慮事項には、現在の開発フェーズと利用可能な予算だけでなく、ツールから製造される部品の数も含まれます。加工中、金型は摩擦、高温、高圧にさらされます。木材とエポキシは金属に比べて耐熱性と耐荷重性が低いため、これらの材料で作られた金型は寿命が短く、少量生産に適していますが、大量生産には金属工具が好まれます。
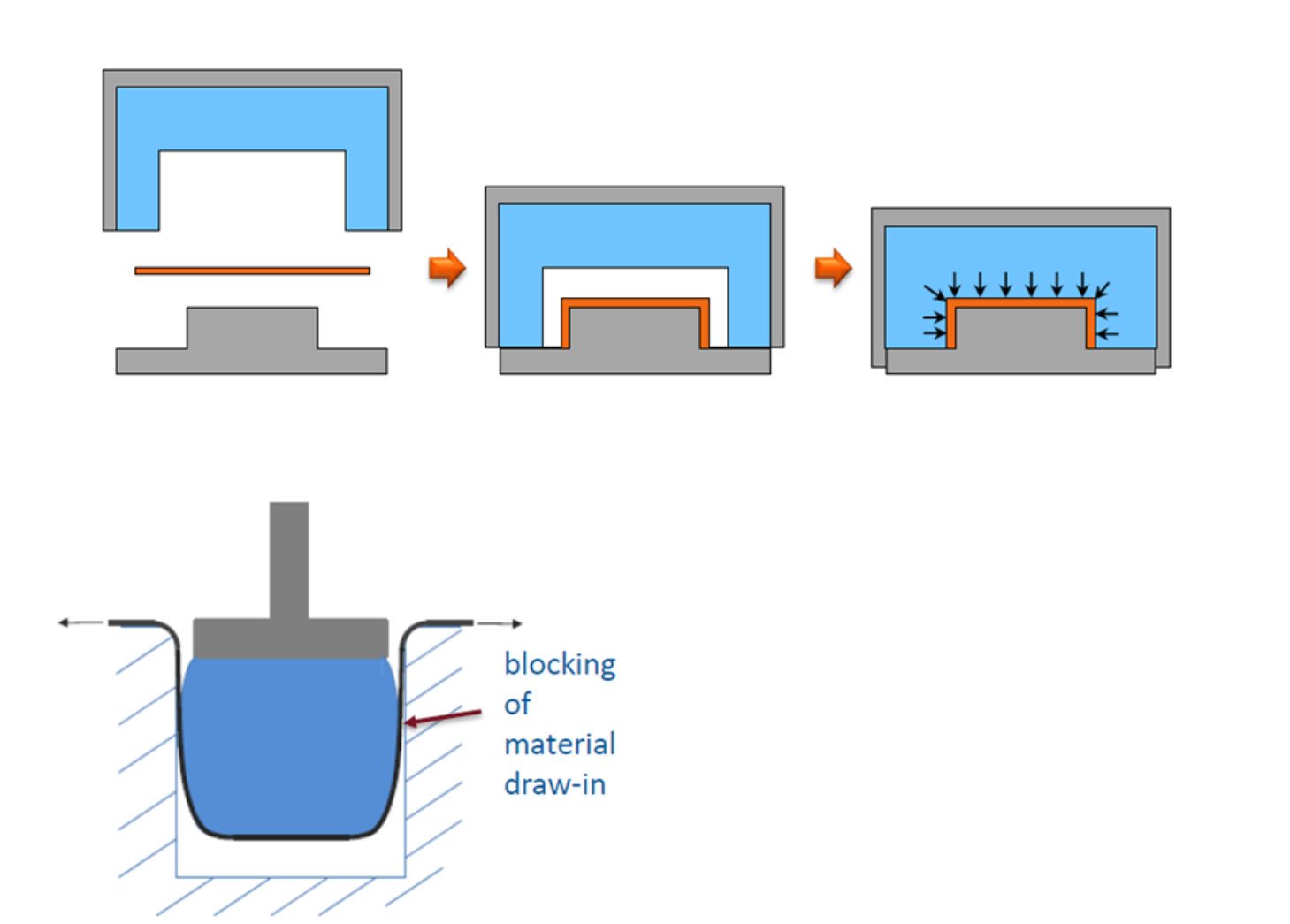
ツーリングで考慮すべきもう1つの材料システムは金属ゴムです、一致するセットの半分が金属で、もう一方がゴムです。これにより、生産の柔軟性が高まり、公差の大きい部品に使用できます。金属ゴムツールは均一な静水圧も提供します。これは、フランジ領域や、複数のUDプライで作られたテーラードブランクに典型的な厚さの変化があるブランクで有益です。
静水圧のこの固有の適用は、同じ部品が複数の異なる厚さで製造される場合にも利点であり、厚さごとに別々の金型のコストを排除します。金属ゴム工具を設計するときは、次の欠点と課題も考慮することが重要です。
- ツールの金属面は、ゴムよりも滑らかな仕上がりになります。
- 金属ゴム工具は、全金属工具に比べて熱膨張係数(CTE)が1桁高くなります。
- 金属に比べて熱伝導率が低いため、冷却に少し時間がかかり、温度制御応答の遅れが大きくなります。
- 摩耗と経年劣化が増えると、オールメタルツールに比べて耐用年数が短くなります。
成形と離型。 適切な金型設計により、十分な圧力と最適なドレープが確保され、欠陥の防止と安全な部品の取り外しが容易になります。成形と離型に関しては多くの問題がありますが、最も重要なもののいくつかは次のとおりです。
- 圧力。 熱成形中、低圧は圧密不良、機械的特性の低下、および公差外の部品寸法につながる可能性があります。一致する金属-金属ツールの場合は、エンドストップを削除して、エンドストップが作成するギャップによってラミネートへの継続的な圧力が妨げられないようにします。
- マテリアルの描画を許可する 。プレス中の金型のゴム側の膨張(バレルと呼ばれる)を回避するために、プレス中の材料の動きを妨げる可能性があります(引き込み)、成形ツールのメス側にゴムを配置します(図3を参照)。 。
- パーツの削除 。 L字型の部品の場合、希望のL角度をVに傾けて金型を設計します。これにより、工具との摩擦が減り、部品を簡単に取り外すことができます。箱型の部品の場合、各辺に1〜2度のドラフト角度を使用します。より深い部分には、より高い角度が必要になる場合があります。
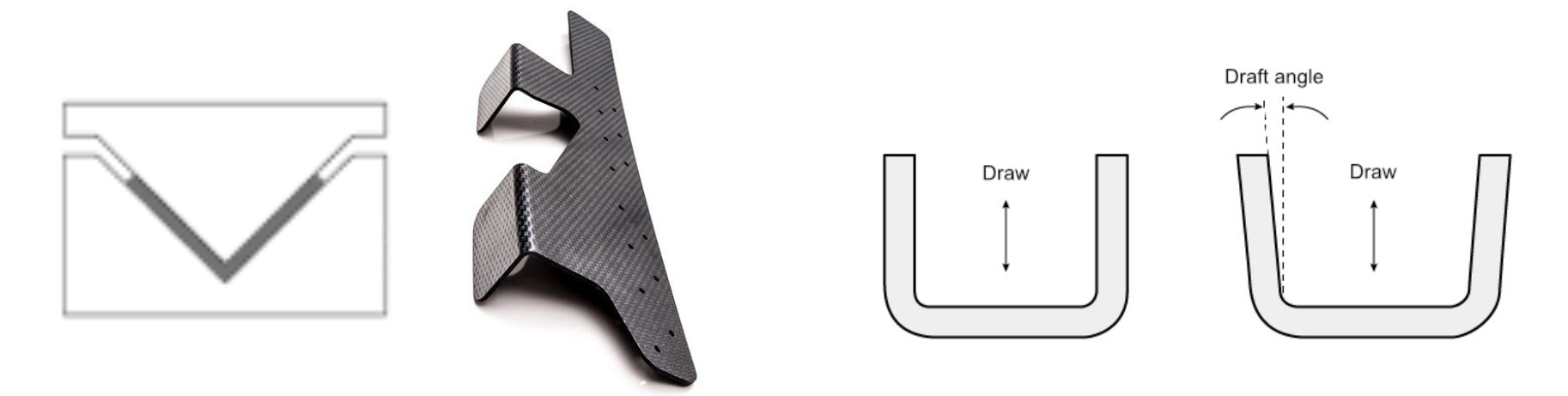
反りとスプリングイン
反りとスプリングインは、成形後に発生する異方性材料特性と不均一な樹脂冷却によって引き起こされる形状の歪みであり、許容範囲外の部品寸法につながる可能性があります。組み立てに問題が発生し、部品が廃棄される原因になります。反りは、成形品内の成形応力が高い領域が成形応力が低い領域と交差するときに発生します。その応力の不均衡は、高応力領域が低応力領域を歪ませ、ラミネートの曲がりやねじれを引き起こすことによって緩和されます。
スプリングインは、成形された応力によって壁セクションが設計どおりの角度よりも小さい角度で内側に歪むときに、湾曲したパネルまたはコーナーセクションのあるパーツで発生します。これは、異方性特性のために繊維強化複合材料でよく発生します。部品の形状も要因です。面内(繊維方向のCTEが低い)と厚さ方向(マトリックスのCTEが高い)の収縮差により、角度が1〜3度減少する可能性があります。
形状の歪みに対処するには、コストと時間がかかる可能性があります。部品開発を迅速化するには、シミュレーションおよび設計ツールを使用することを強くお勧めします。反りに直面した場合は、次の考えられる原因と修正を探してください。
- プロセスパラメータ 。金型温度は、結晶化および粘弾性効果に関連する厚さ方向の特性に影響を与え、反りに影響を与える可能性があります。金型温度を下げると、スプリングインを減らすことができますが、内部応力が増加し、解放されるとスプリングインが発生する可能性があります。この不確実性は注意深く調べる必要があります。高圧と成形速度はまた、スプリングインを減らし、逆の問題であるスプリングバックを促進する可能性があります。滞留時間を長くすると、マトリックスが完全に固化し、余熱がなくなり、部品を取り外した後の収縮が減少し、スプリングインが減少します。
- モールドデザイン 。金型の壁の角度を変更することで、スプリングインの補正を行うことができます。また、前述のように、金型はより均一な冷却を促進し、特に厚い部品での反りのリスクを減らすのに役立ちます。
- レイアップ。 対称レイアップは、反りを軽減するために一般的に使用されますが、熱成形中に繊維の再配向が発生し、非対称と反りが発生する可能性があります。非対称性のもう1つの兆候は、半径形成中の樹脂の移動です(コーナーを含む)。これにより、繊維の再分布と繊維の体積分率の局所的な変化が発生し、異方性と反りが促進されます。繊維が応力に反応し、それが反りに影響を与えるため、レイアップとレイアップシーケンスが異なれば動作も異なります。シミュレーションおよび予測ツールは、この複雑な材料の挙動に対処するのに役立ちます。
熱成形/スタンピングプロセスには複数のパラメータと複雑な材料の挙動が含まれますが、開発を成功させるための基本的な原則とアクションがあります。熱成形TPC部品、特にUDテーラードブランクの実装が増えるにつれ、革新的なソリューションと改善された設計/シミュレーションツールによって新しい課題に取り組んでいます。
樹脂
- コベストロは熱可塑性複合材料への投資を強化
- リサイクル:リサイクルされたポリカーボネートを使用した連続繊維強化熱可塑性複合材料
- Oribi Compositesの熱可塑性複合材料:CWトレンド、エピソード4
- 熱可塑性複合材料:構造用バンパーブラケット
- Toray Advanced Compositesは、熱可塑性複合材料の機能を拡張します
- Teledyne CML Compositesは、熱可塑性プラスチック加工機能に投資しています
- ACMAが熱可塑性複合材料会議2020プログラムをリリース
- 自動車用複合材料の最初の熱可塑性ドア
- 熱可塑性複合材料:風光明媚なビュー
- CAMX 2018プレビュー:TenCate Advanced Composites
- 熱可塑性複合材料の溶接