生産用のリサイクル熱可塑性複合材料
リサイクル性は、熱可塑性複合材料(TPC)を使用することで長い間期待されてきた利点です。しかし、まだ大規模に商業的に使用されていません。材料サプライヤーのTenCateAdvancedCompositesとThermoPlasticComposites Research Center(TPRC)は、2016年にTier1メーカーのGKNFokkerと提携して、このようなプロセスを実証しました。チームは、スクラップTenCate Cetex TC1100繊維/ポリフェニレンサルファイド(CF / PPS)GKNFokkerによるGulfstreamG650エレベーターおよびラダーの製造からの材料。生産廃棄物は細かく刻まれ、TPRCによって設計されたプロセスと金型を使用して圧縮成形されました。アクセスドアパネルは、成形された補強リブ、厚さのバリエーション、ボス付きの成形された穴を備えていました。 (ボスは、ファスナーを穴に導く突出した機能です)。ガルフストリームG650ラダーの前縁にアクセスドアパネルが使用されたため、再生材料を使用することで、閉ループ製造プロセスを形成しながら、より優れた成形機能を備えた軽量部品が可能になりました。このプロジェクトは、2016年にJECイノベーションアワードを受賞しました。
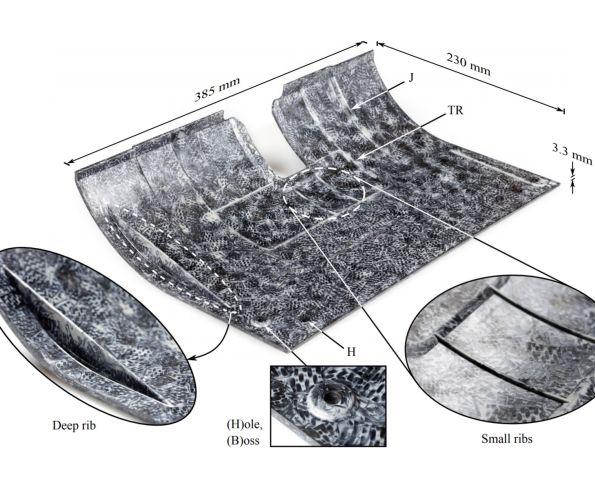
アクセスドアパネル2016年に実証されたのは、Cetex CF / PPSのスクラップ材料でできており、補強リブとボス付きの成形穴が特徴です。ソース| TPRC。
その研究以来、新しい組織である熱可塑性複合材料アプリケーションセンター(TPAC)が設立されました。 「TPRCは10年前に設立され、主に航空宇宙産業の基本的なTPC研究に取り組んでいます」と、TPACの軽量構造の研究者であるThomas deBruijnは説明します。 「TPACはおよそ 2つ形成されました 数年前、より応用された働き方があります。 Saxion大学およびSMEともリンクしています。より費用効果の高いプロセスを開発することにより、コストを削減することに重点を置いています。これら2つのグループが一体となって、TPCテクノロジーのスマート産業であるデジタルイノベーションハブであるTPCNLを形成しています。」
TPACとTenCateの継続的な研究開発の関与は、このタイプの閉ループ製造が可能であるだけでなく、経済的にも有益であることを示しています。当初はCF / PPS材料に焦点が当てられており、研究は業界パートナーと協力して、このTPCリサイクルで強化された部品生産の実装を支援しています。
ただし、実際に開発されるプロセスは異なります。 TenCateは、連続繊維部品に成形された幾何学的特徴と機能を追加するためのフロー層として使用されるより短い繊維材料に焦点を合わせています。一方、TPRCとTPACは、より長い繊維長を維持することを目指しており、従来の短繊維コンパウンドよりも高い機械的特性を備えた部品に圧縮成形できる生地のような材料を作成しています。
TenCate —フローレイヤーで強化されたオルガノシートパーツ
「3年前、私たちは研究開発予算の多くをリサイクルに投資し始めました」と、熱可塑性プラスチックのTenCate製品マネージャーであるFrank tenNapelは述べています。 「これは単に「グリーンラベル」を取得するためだけのものではありません。私たちは、リサイクルされた材料をあなたの部品に組み込むことは、非常に現実的な経済的および建設上の利益をもたらすと確信しています。他の方法では達成できなかったレベルのジオメトリをパーツに適用できます。再生材のフローレイヤーを適用することで、成形品全体に剛性のあるリブとさまざまな厚さの成形を行うことができます。また、穴の周りのボスは、ファスナーによって引き起こされる荷重を分散させます。これらすべてにより、未使用の材料を使用する場合と比較して、連続性の低い繊維材料を使用して、より薄く、より軽く、より費用効果の高い部品を使用できます。」彼は、これらの成形機能を連続繊維材料で実現するのは難しいと述べています。「しかし、連続繊維と局所的なオーバーモールドの両方を組み合わせることで、設計の自由度が高まります。」
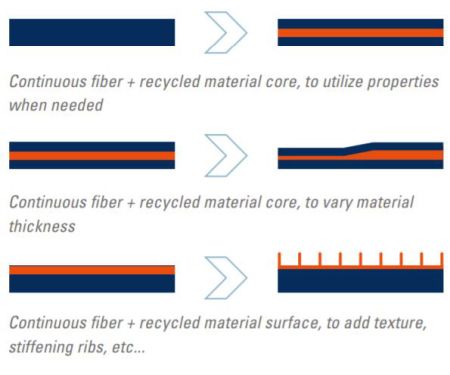

このブラケットタイプのデモンストレーターは、同じパーツの両面を示し、従来の織られた有機シート層とリサイクルされたTPCフロー層を強調しています。後者は、インサート用の補強リブとボスを備えています。ソース| TenCate
TPC-サイクルプロジェクト
この4年間のプロジェクトは、2015年9月に開始され、熱可塑性複合材(TPC)サプライチェーン全体のパートナーが参加しています。
- TenCate Advanced Composites(東レグループ)–材料
- GKN Fokker Aerostructures –航空宇宙構造物およびアセンブリのTier1設計および製造
- Dutch Thermoplastic Components(DTC)–航空宇宙用リブ、ストリンガー、ブラケット、クリップ、ボックスのSME設計および製造
- Cato Composites –航空、自動車、防衛、スポーツ、消費者市場向けの部品のSME製造および設計
- Nido RecyclingTechniek(NRT)–リサイクルする材料/部品を細断してサイズを縮小する技術
TPC-Cycleは、TPACとSaxion University of Applied Sciences、特にその軽量構造研究グループによって促進され、オランダ科学研究機構(NWO)の一部であるRegieorgaanSIAによって資金提供されています。
Thomas de Bruijnは、TPC-Cycleプロジェクトマネージャーであり、Saxion / TPACの軽量構造の研究者です。彼は、TPC-Cycleプロジェクトを開始するための多くの推進力があったと説明します。 「クリップやブラケットのように、特にスタンプ成形のために、連続繊維TPCの使用が増加することがわかりました。この増加に伴い、産業廃棄物の量はかなりの量になります。そのため、環境と経済の両方で、また規制を満たすためにも、リサイクルが必要でした。たとえば、ヨーロッパの終末期の法律では、自動車に使用されている材料の95%をリサイクルすることが義務付けられています。」彼は、エアバスもリサイクルと寿命末期の目標を設定し、それらをサプライヤーに伝えていると述べています。 「サプライチェーンは、これらの目標を達成できると言うだけでなく、デモンストレーターによるその能力を証明する必要があります」とdeBruijn氏は付け加えます。
「TPCは、サイクルタイムが短く、軽量でスマートな構造を提供するため、航空宇宙以外の食品箱、家具、産業用コンポーネントなどのアプリケーションでも成長しています」とdeBruijn氏は述べています。
彼は続けます。「私たちは、ダウンサイクリングである粉砕だけでなく、商業的に実行可能なリサイクルプロセスチェーンを証明したかったのです。高性能が欲しかった。そのため、0.5〜1.0インチの繊維長を維持するために、低せん断混合アプローチを選択しました。剛性のために、あなたはほんの数ミリの長さを必要とします。しかし、強度と耐衝撃性のためには、0.5インチ以上の長さが必要です。」繊維の長さを維持することに加えて、もう1つの重要な課題は、材料の混合と最終的なリサイクル製品の均一性を高めることでした。
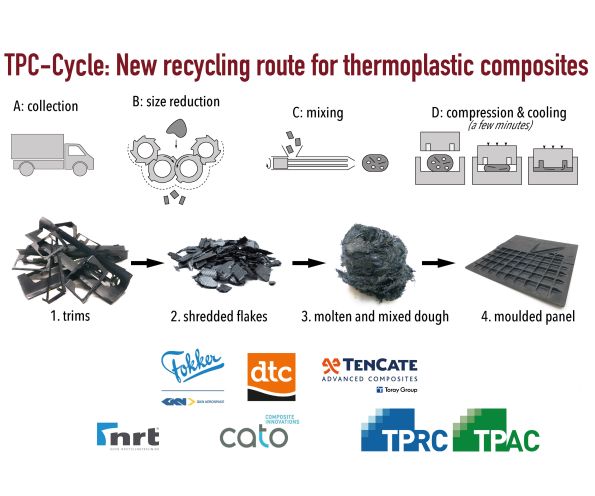
「目標は、廃棄物を収集し、0.5〜1.0インチのフレークに細断して均質な生地に変換し、それを押し出して圧縮成形プレスに直接移すことです」とTPRCの研究者および博士号は説明します。学生ギヨームヴィンセント。 「生地の処理は、フレークとバージンポリマー顆粒を低せん断ミキサーに供給し、繊維の重量分率を25〜40%に減らすことで行われます。」彼は、このプロセスは、自動車で一般的な長繊維熱可塑性プラスチック(D-LFT)の直接配合と非常に似ていると述べています。 「しかし、D-LFTプロセスは数百万ドルの投資を必要とするため、大量生産でのみ使用されます。小型のマシンを使用してアプローチを変更しましたが、同様の結果が得られます。 D-LFTプロセスと比較してボリュームは少ないです。」
Vincentは、完全なリサイクルバリューチェーンを含めることで成果が得られる例について次のように説明しています。「NRTは、Unthaなどの大型シュレッダーマシンのメーカーとのつながりを支援してくれました。」これは、シリアルパーツ生産のプロセスをスケーリングする上で重要な部分です。
開発中の最初のプロセスチェーンはCF / PPS用です。 Vincent氏によると、TPC-Cycleは、リサイクルされた材料の繊維長と繊維分布を特徴付けるシミュレーションモデルと分析方法を構築しました。 「これらの材料特性が成形品の特性にどのように移行するかも理解しています」と彼は観察します。これは、実際、彼の博士号の焦点です。 2019年末までに公開される論文。
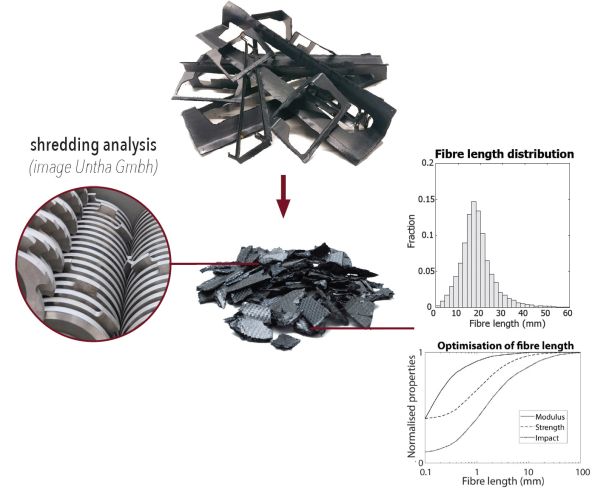
TPC- Cycledプロジェクトは、費用効果の高い細断処理や繊維の長さと分布の特性評価など、熱可塑性複合材料をリサイクルするための完全なプロセスチェーンを開発しました。ソース| TPRC / TPAC。
このリサイクル生地は、バルク成形コンパウンド(BMC)と呼ばれることもあります。歴史的に、BMCは、短いガラス繊維(<25mm)、熱硬化性樹脂ペースト、および複合部品に圧縮成形されたフィラーの生地のような混合物でした。シート成形コンパウンド(SMC)と比較して、繊維の体積が少なく、流動性が高いため、機械的特性もわずかに低くなります。 TenCateは熱硬化性樹脂と熱可塑性樹脂を販売しています BMCは何年もの間、後者は刻んだ一方向プリプレグテープを型に広げてプレスするプロセスです。 「私たちの製品は実際にはまったく異なります」とVincentは主張します。 「従来の熱可塑性BMCでは、一般に混合がなく、長い加熱と固化のサイクルが必要です。混合すると、より均質な製品が得られ、部品の応力集中が少なくなるため、特性が高くなることがわかりました。従来の熱可塑性BMCを使用すると、両端にマトリックスが豊富な領域があり、複合ラミネートに応力集中が発生する、より厚いフレークが得られます。」
低せん断混合プロセスは、フレークを層に解きほぐし、次に層を束に分離し、束を緩い繊維に分離します。また、ポリマーを混合して繊維含有量を減らし、流動性を向上させて、材料をより簡単に形状に加工できるようにします。
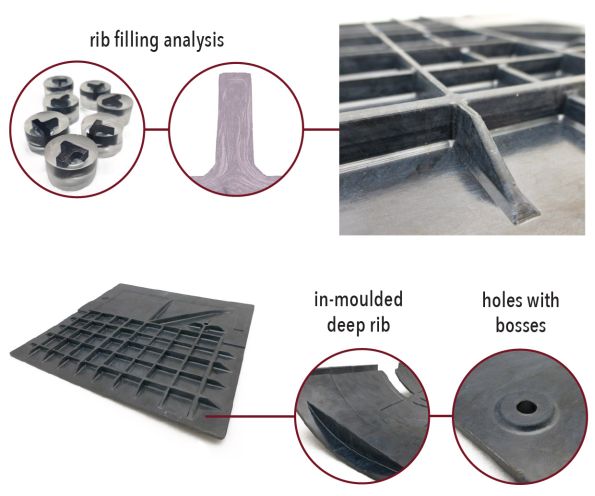
「生地を押し出し、ロボットで開いた等温[加熱]圧縮金型に入れます」とdeBruijn氏は説明します。 「混合後、生地の繊維はランダムに配向します。しかし、プレス中に、材料の流れが繊維の向きを変えます。この配向は、射出成形された短い繊維を使用した混合物と比較して少なくなりますが、部品ごとに類似しています。これは私たちの継続的な研究のトピックの1つです。」
コスト
これまでに開発されたTPC-Cycleプロセスチェーンは、経済的に有益であるように思われます。 「2019年後半までに部品コストをどれだけ削減できるかについてお答えしたいと思います」とdeBruijn氏は言います。 「しかし、市場が必要であり、リサイクルされた材料を販売しなければならないため、これは複雑です。」彼は多くの経済的要因があると述べています。たとえば、今日のほとんどのメーカーは、単に生産廃棄物を捨てています。埋め立て地に処分するための現地費用は1トンあたり80ユーロ(90ドル)です。 「しかし、捨てられるこの材料には価値があります」とdeBruijnは言います。 「また、廃棄物を収集し、細断し、混合してから、新しい部品に圧縮成形するためのコストを考慮する必要があります。ただし、これは等温金型のためにサイクルタイムが短いニアネットシェイププロセスでもあります。」言い換えれば、二次仕上げと機械加工を大幅に削減または排除する必要があります。 De Bruinは、TPC-Cycleは現在、コスト分析とライフサイクル分析の完了を検討していると述べています。
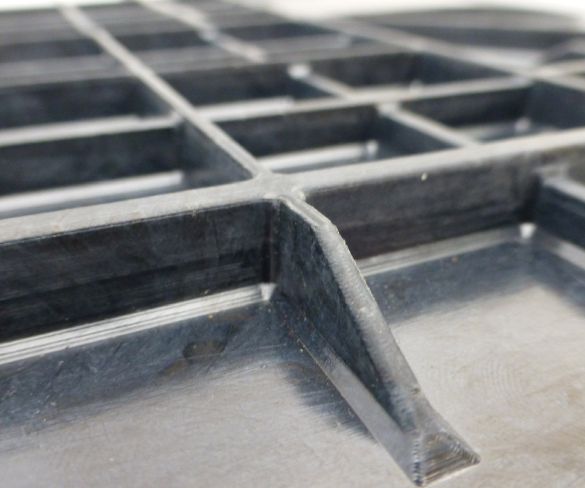
ソース| TPRC / TPAC
クリーンスカイリセット
TenCateとTPC-Cycleプロジェクトで完了した作業の重要性を繰り返す3番目のプロジェクトは、2016年1月から2017年12月まで実行され、スペインのバルセロナにあるLeitat TechnologicalInstituteによって調整されたRESETプロジェクトです。 RESETはCleanSky(2008-2016)で開始され、Clean Sky 2(2017-2021)で完了したようです。
CleanSkyおよびCleanSky 2プログラムは、革新的な航空機デモンストレーションプログラムの最上位層(下の画像の車両IADPを参照)と革新的な技術デモンストレーターの下位層(下の画像の大規模システムITDを参照)に編成されています。 RESETは、機体ITD、特に機体のワークパッケージ(WP)A-3.4エコデザインの一部として完了しました。
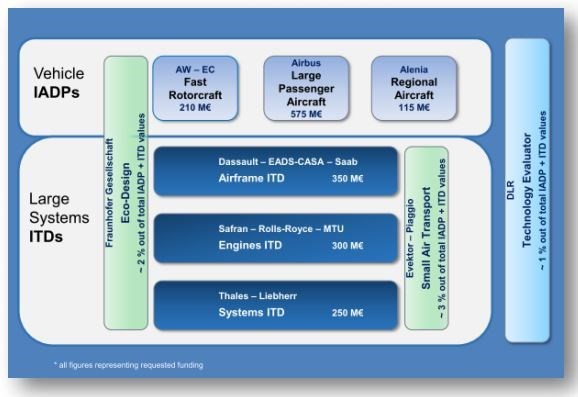
出典:クリーンSky2ジョイントテクニカル 提案
For 詳細については、をご覧ください。 「熱可塑性複合材料のデモンストレーター—将来の機体のEUロードマップ」
CleanSkyプロジェクトオフィサーのElenaPedoneによると、LeitatのRESETチームは、以前に使用された航空機の複合材料をリサイクルし、それを使用して新しい部品を製造するプロセスを開発しました。彼らは、これらのリサイクル部品を市販の部品と比較し、同様の機械的特性を持っていることを発見しました。 「このプロジェクトで開発された技術は、今後数年間で航空部門で現実的に商業化され、他の経済部門にも波及する可能性があります」とPedone氏は述べています。
RESETプロジェクトでは、PEEKおよびPPS熱可塑性マトリックス材料の影響と炭素繊維強化材の化学的性質を調査する作業が完了しました。繊維の長さや織布と不織布などの補強材の形状を調べました。繊維含有量(ポリマーと繊維の比率)の影響も調べました。
2番目の作業パッケージでは、主な目的は、押出成形と結果として得られる成形複合材料に基づくリサイクルCF / PPSの調整と特性評価でした。熱可塑性ブラケットと熱可塑性クリートの2つの部品は射出成形で作成され、もう2つは熱成形で作成されたとLeitatのプロジェクトClaudiaAguilarの科学コーディネーターは説明しています。次に、これらの部品をテストしました。 「材料の機械的特性は、市販の材料と同等であることがわかりました」とAguilar氏は言います。
RESETプロジェクトは、航空機の生産からTPC廃棄物を取り出し、それを航空機の新しい部品を生産するための原材料として使用できるリサイクルプロセスを実証したと主張しています。 「リサイクルされた材料の最大70%が、新しい複合材料ファミリーの製造に使用されました」とAguilar氏は言います。彼女は次のように付け加えています。「RESETのリサイクルプロセスにより、ヨーロッパの航空は環境フットプリントを制限し、新しい航空機部品の製造コストを削減できます。したがって、このプロジェクトは航空業界をより競争力のある環境に優しいものにします。」
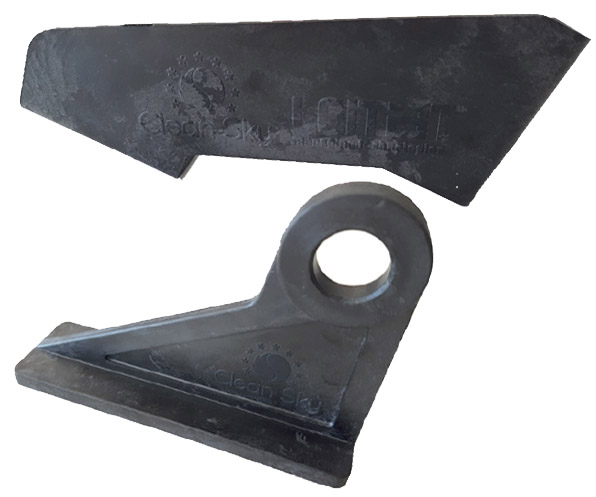
Clean Sky RESETプロジェクトで実証された、リサイクルされたCF / PPS素材で作られたブラケット(左)とクリート(右)。ソース|レイタット技術研究所
TPCの未来はデザインから始まります
TenCateとTPRC / TPACによる主張は、現在実証されているこれらのリサイクルプロセスは、環境に優しいだけでなく、経済的にも魅力的であるというものです。では、どのような投資が必要なのでしょうか。 「それは生産量に依存します」とTenCateのTenNapelは言います。 「必要なシュレッダーは大型でも高価でもありません。プロセスはかなり簡単なところまで開発されています。」マトリックスタイプはリサイクル性に影響しますか? 「いいえ」とTenNapel氏は言います。「しかし、経済的実行可能性の観点から、炭素繊維とPPSは、ガラス繊維とポリプロピレンよりも価値が高いため、PEEKまたはPEKKの方が実行可能です。」
「これが業界で取り上げられるのであれば、それはデザインから始めるべきだと思います」と彼は続けます。 「現在の最大のハードルは、エンジニアの考え方です。実際に外に出て、リサイクルされた材料でデザインする(またはこれらを部分的に新製品にデザインする)ことは、彼らにとってかなり新しいことです。」
Ten Napelは、TenCateが部品を商業的に設計も製造もしていないことを認めています。「しかし、私たちは設計者が新しい部品や構造を開発する際にこのように考えるように促そうとしています。」彼は、航空機の内装、アクセスパネル、アクセスドアを、リサイクルされた材料を再利用するための手に負えない果物として挙げています。 「私たちが業界として自分たちのスクラップや廃棄物を再利用することに慣れることができれば、次のステップに進み、寿命の切れた部品に対処する方法を検討し始めることができます。」
Ten Napel氏によると、熱可塑性複合材料のリサイクルに関するマントラ(単に研削と再成形)は確実に採用できますが、経済的にあまり意味がないことがよくあります。 「私たちは、より優れたプロセスと、より費用効果の高い部品と全体的なプログラムを実際に作成できるプロセスを実証しました。熱可塑性複合材料で何が完全に可能であるかについて業界に刺激を与えるために、TPRCおよびTPACとともにこの知識を広めることを選択しました。」熱可塑性複合材料を大規模に採用する場合、生産の本質的な部分としてのリサイクルはもはや選択肢ではなく、必要です。
樹脂
- リサイクル:リサイクルされたポリカーボネートを使用した連続繊維強化熱可塑性複合材料
- 医療用途向けに「微調整」された熱可塑性生体材料
- KarlMayerが熱可塑性UDテープの生産ラインを立ち上げ
- StyLight熱可塑性複合材料の生産拠点を構築するINEOSStyrolution
- Hexionは、航空宇宙複合材料の製造に2成分エポキシソリューションを導入しました
- 自動車用複合材料の最初の熱可塑性ドア
- ランクセスは、連続繊維強化熱可塑性複合材料の生産能力を拡大します
- CAMX 2018プレビュー:TenCate Advanced Composites
- 熱可塑性複合材料の溶接
- TenCateは、ブラジルでの熱可塑性複合コンソーシアムの組み立てを祝います
- 熱可塑性複合材料コンソーシアムは、自動車および航空宇宙向けの大量生産を目指しています