大きな複合カバーは多くの水を保護します
コロンビアのボゴタでの水の貯蔵と供給は、他の大都市圏と同様に複雑です。課題は供給の1つではありません。約900万人の都市が毎年32インチ(824ミリメートル)の雨を受け取り、さらにボゴタ川が都市を流れています。課題は、その水を捕獲し、処理してから保管し、住民や企業が必要に応じて飲用に利用できるようにすることです。これを行うために、Empresa de Acueductos y Alcantarillados(Company of Aqueducts and Sewers、EAAB、Bogotá)は、処理水を貯蔵し、顧客への供給を確保するために、長年にわたって市内に一連の59のタンクを建設してきました。
これらのタンクのいくつかは実際のタンクであり、外部の要素から水を保護するために完全に密閉されています。他のもの、それらの多くは古いもので、一連の取り外し可能なカバーで要素から保護された巨大なコンクリートの盆地です。カサブランカと呼ばれ、ボゴタ南部のシウダッドボリバル地区にあるそのようなタンクの1つは、約300万人の人口にサービスを提供しています。 EAABネットワークで最大の貯水タンクであり、コロンビアで最大の貯水タンクであるカサブランカは、長さ144メートル(472フィート)x幅110メートル(361フィート)x奥行き9メートルで、143,000立方メートル( 3,800万ガロン)の水。タンクは、中央を走るコンクリートの仕切りによって二分されているため、水は2つの等しいセクションに保管されます。
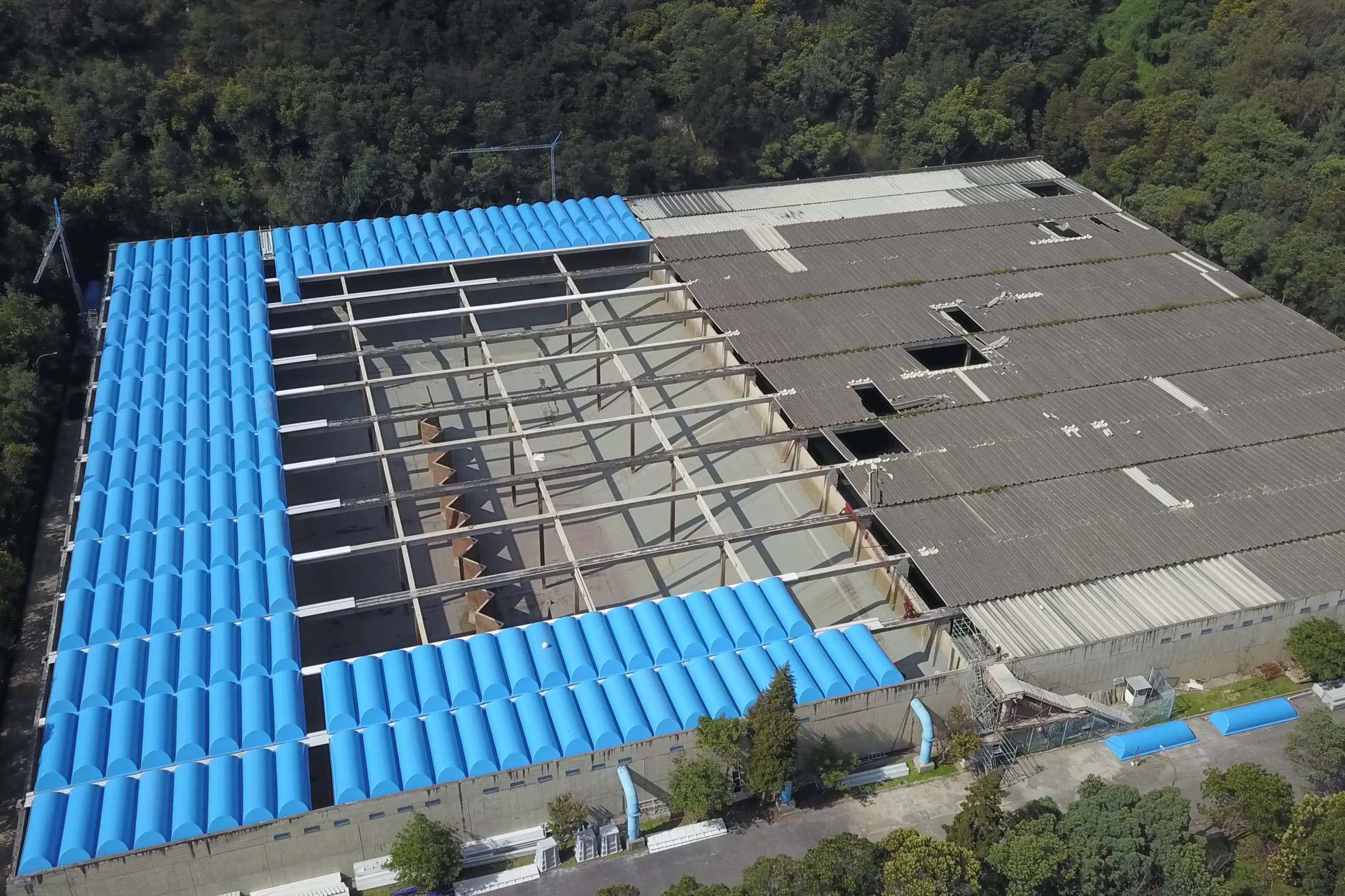
66歳のカサブランカを維持することは簡単な作業ではありません。 2009年に、タンクのコンクリートの床にひびが入ったために、毎時360,000リットル(95,000ガロン)の水が漏れていることが発見されました。 。ポリ尿素コーティングを施したコンクリートの修理により、漏れがゼロになりました。しかし、カサブランカはまだコンクリートの上に問題を抱えていました。タンク内の水は、コンクリートとアスベストの混合物で構成された一連のカバーによって保護されていました。これは、水質と人間の健康に重大な脅威をもたらしました。古いカバーも故障しやすく、メンテナンスに費用がかかりました。 EAABは、古いカバーをより安全で、より軽く、より耐久性のある代替品に交換する必要がありました。
大きなカバー、そしてそれらの多く
EAABは、カバーの複合ソリューションを追求することを決定しましたが、プロジェクトの規模によってすぐに挑戦されました。カサブランカは、カバーが載っている梁のネットワークを支える一連のコンクリート柱が交差しています。これらの梁の間隔は約7.2メートル(23.6フィート)であるため、新しいカバーは自立型であり、既存のインフラストラクチャを利用するにはそのスパンをカバーする必要があります。 EAABは、このようなカバーを軽量樹脂トランスファー成形(LRTM)で製造することを提案しました。チャレンジ?このアプリケーションに必要なこのサイズの複合構造は、コロンビアでLRTMを介して製造されたことはありませんでした。多くの製作者は単にプロジェクトを引き受けることができませんでした。
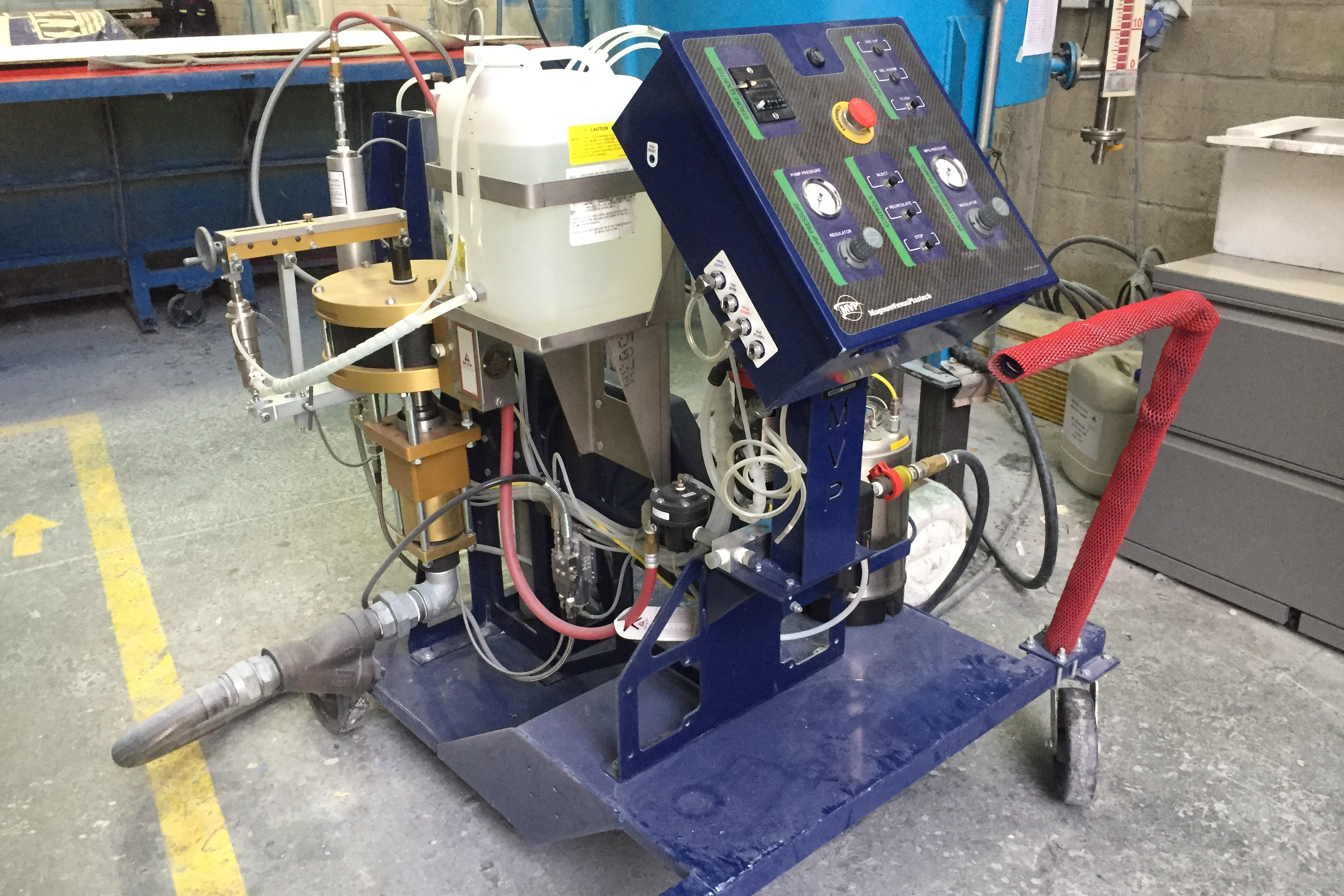
例外は、メデジンのすぐ南にあるコロンビアのアンティオキアのラエストレージャにある複合材製造業者であるInnovative EngineeringSolutionsまたはSolingでした。 Solingは、コロンビアとその周辺でいくつかの複合材料製造会社を所有および運営しているJaviarMorenoによって2014年に設立されました。 SolingのエンジニアリングコーディネーターであるRodrigoVergaraは、カバーのサイズは多くの製造業者にとって初心者ではなかったと言います。 「部品のサイズが大きいため、コロンビアでは誰もこれを経験していませんでした」と彼は述べています。 「これは、コロンビアで製造された最大の複合部品です。」しかし、モレノにとって、カバーのサイズは興味深い挑戦でした。 「私たちの所有者[モレノ]にとって、それは夢の実現でした」とヴェルガラは言います。 「不可能」は彼が理解できない言葉です。彼は、「これをやります!」と言いました。私は「OK!」と言いました。
Solingは、Casablancaプロジェクトの具体的なソリューションを提案しました。一連の 840 ドーム型の長方形の複合構造で、それぞれ長さ7.6メートル、幅2.4メートル(24.9 x 7.9フィート)です。半円形のドームデザインが選択されたのは、「機械的抵抗が最も大きい幾何学的形状が円周であるためです」とVergara氏は言います。これが、カバーが自立していることを保証する主な要因でした。一方、製造現場から260マイル離れた設置場所まで輸送する最も簡単な方法を見つける必要がありました。」
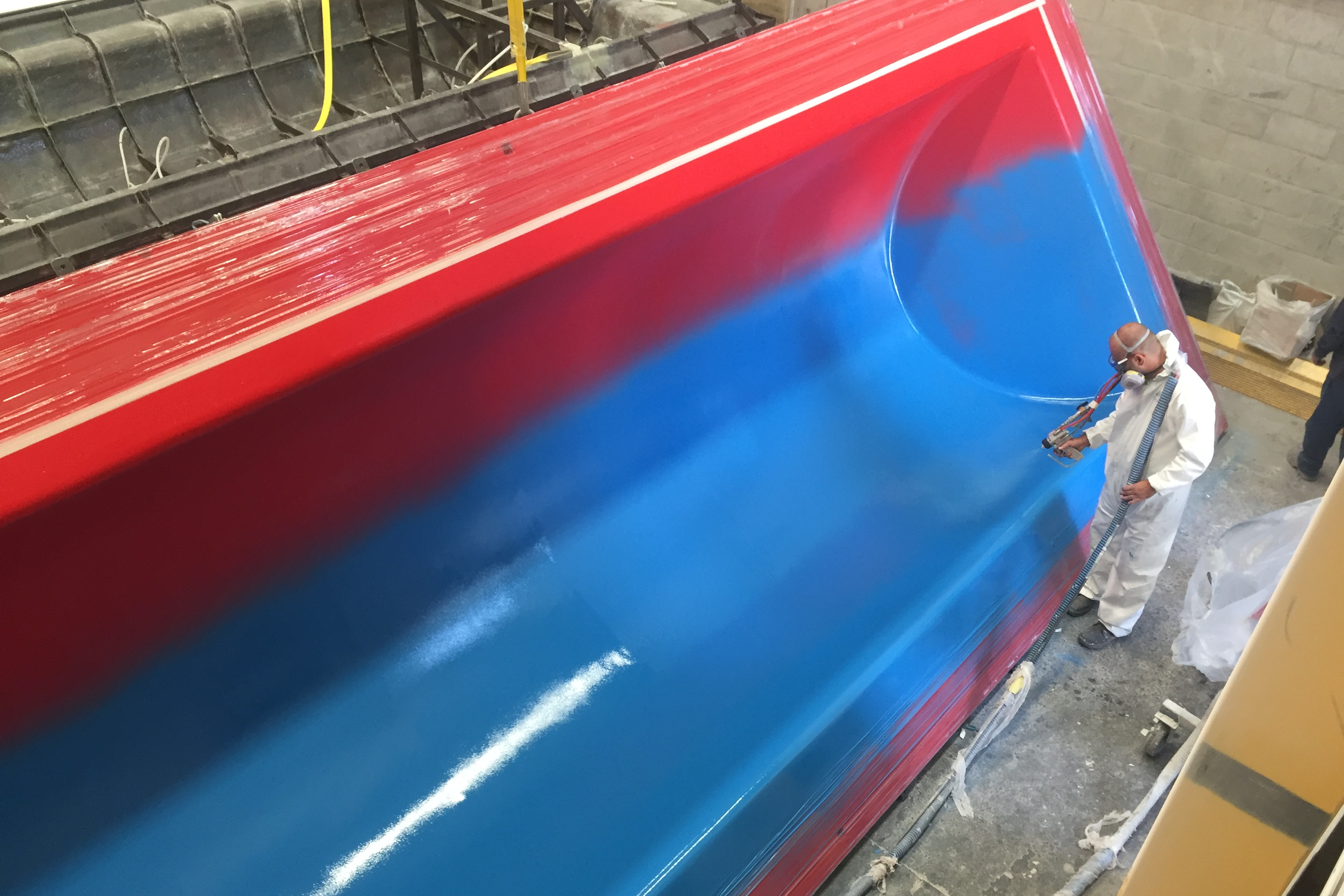
カバーは、EAAB仕様に従って、外面に青いゲルコート、内面に白いゲルコートを備えたLRTMを介して製造されます。ガラス繊維織物とポリエステル樹脂で構成される、表面積が28.5平方メートル(207平方フィート)のカバーの重量は320キログラム(705ポンド)で、そのうち208キログラムが樹脂になります。デザインを手に入れ、カバーを提供するというコミットメントを持って、VergaraとSolingは仕事に取り掛かりました。
完璧なカバーを作成する
もちろん、ソリングは助けなしにカサブランカプロジェクトを引き受けませんでした。同社と協力していたのは、販売業者、材料供給業者、設備供給業者を含む供給ネットワークでした。ディストリビューターであるMineproSAS(コロンビア、メデジン)は、技術サポートを提供し、LRTMプロセス用のポンプと補助装置を供給した装置サプライヤーMagnum Venus Products(MVP、米国テネシー州ノックスビル)と協力しました。材料のサプライヤーは、ポリエステル樹脂マトリックス、ゲルコート、技術サポートを提供したAndercol(Medellín)と、E-ガラス繊維織物を提供したJushi(中国、桐郷市)です。
当然のことながら、製造は工具から始まります。問題は、プロジェクトに必要な金型の数でした。これを決定するために、Vergaraは、Solingは、EAABの納品要件を満たすために、最初に製造のペースを確立する必要があったと言います。これは、次に、作業現場の要件の影響を受けました。新しいカバーの取り付け中に給水が汚染される可能性を回避するために、EAABは、カバーが配送されて所定の位置に下げられていたカサブランカの半分を空にすることに同意しました。カサブランカの貯水容量を半分に減らすことは課題となるため、EAABは可能な限り迅速に配送と設置を行う必要がありました。
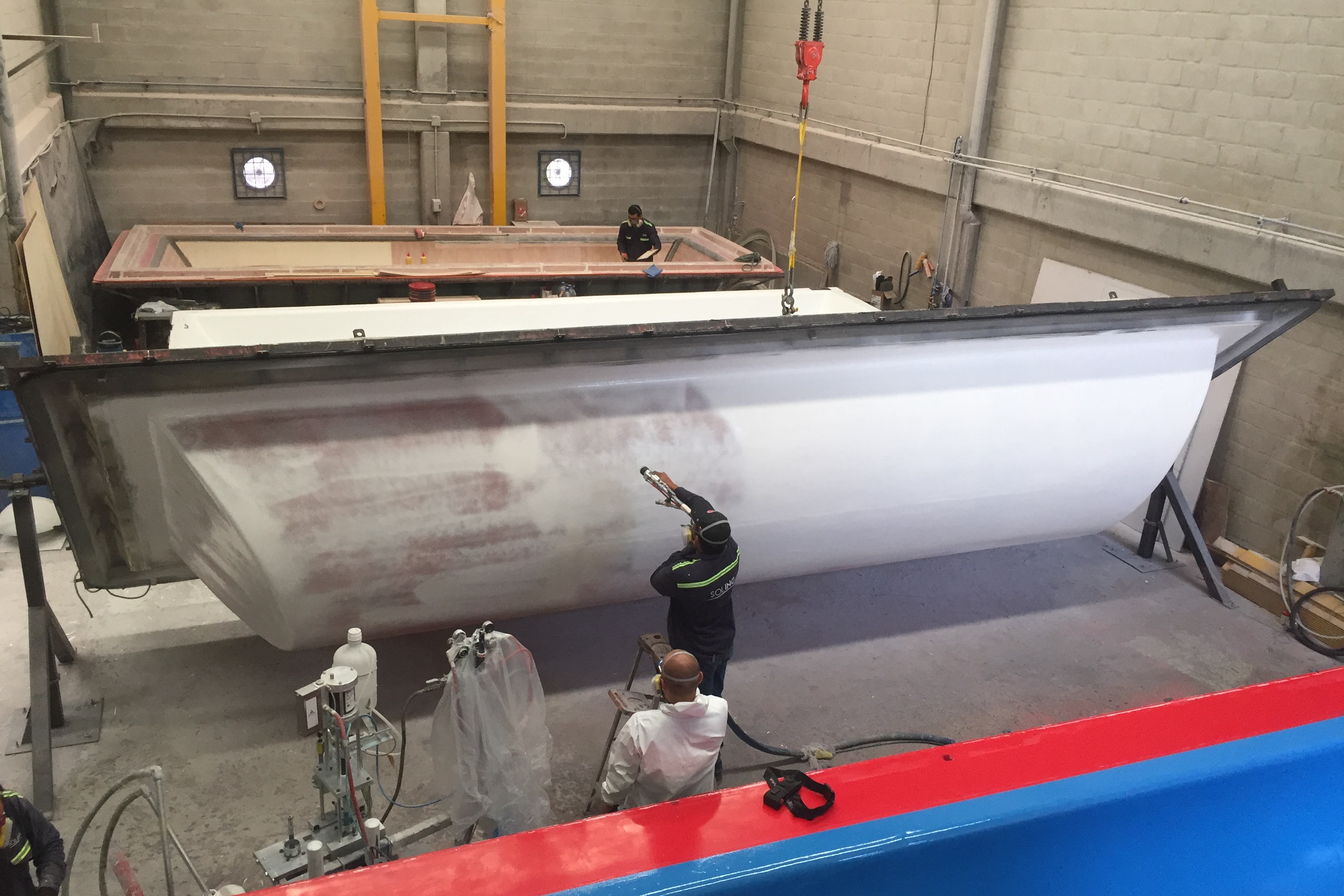
Solingは、EAABと協力して、1日6回のカバーを提供する制作スケジュールに決着したVergaraについて説明します。 1日3回の8時間シフトを実行する施設では、2つの金型が必要であり、それぞれがシフトごとに1つのカバーを製造できます。金型は社内で製造され、鋼製の支持構造に裏打ちされたガラス繊維複合材のオス/メスのデザインで構成されていたと彼は言います。
型が作られると、ソリングは具体的にはドームの製造方法を確立する作業を開始しました。 Vergaraは、MineproおよびMVPと協力して、各金型に2つの樹脂射出ポートと1つの真空ポートを供給することが決定されたと述べています。樹脂射出には、MVPは、各カバーに必要な大量の樹脂を供給することができるPatriot Innovator大量樹脂トランスファー成形(RTM)ポンプユニットの使用を推奨しました。 MVPは、Turbo Autosprueバルブ、ユニバーサルカプラー、シール、モールドアクセサリも提供しました。
カバーの製造を開始するために、金型のメスの半分に白いゲルコートをスプレーし、金型のオスの半分に青いゲルコートをスプレーしたとVergaraは言います。前述のように、両方のゲルコートはAndercolによって供給されました。次に、Jushiが提供したE-ガラスマットとファブリックを、型のメスの半分に手で敷き詰めました。これに続いて、クレーンを介して、金型のオスの半分をメスの半分に下げ、2つの半分を一緒にクランプしました。真空引き後、樹脂注入を開始しました。ヴェルガラ氏によると、各カバーの注入は約40分で完了し、その後室温で硬化しました。各カバーを型から外した後、最終的な寸法にトリミングし、雨水を軽減するための供給チャネルをカバーフランジの表面に切り込みました。
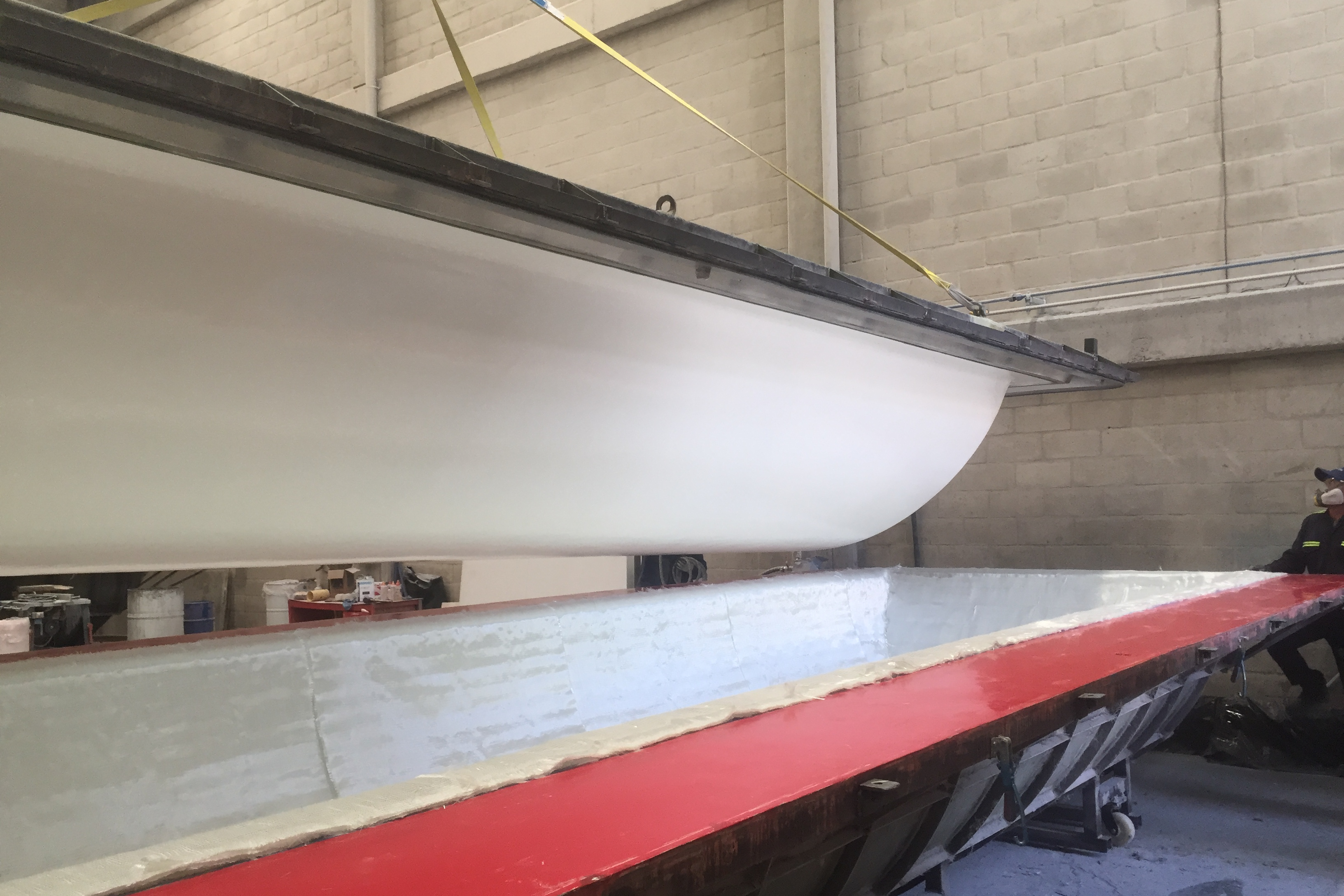
Vergara氏は、カバーのサイズが非常に大きいことと、厳密な重量と寸法の要件が組み合わさって、製造に最大の課題をもたらしたと述べています。注入口の位置を決定し、注入のタイミングを管理するには、多くの試行錯誤と技術専門家との協議が必要でした。しかし、最終的には、Vergara氏は、Solingは、再現性と信頼性が高いことが証明された製造プロセスに落ち着いたと述べています。
「最大の課題は、既存の構造物の耐荷重を超えることができなかったため、設置する要素の重量でした」とVergara氏は言います。 「これには、すべての部品が形状と重量の両方で同じ特性を持っている必要がありました。これらの条件を保証する唯一の方法は、再現性を保証するプロセスを使用することでした。」
完成したカバーは、メデジン近くのソリングの施設からボゴタのカサブランカ作業現場まで418 km(260マイル)で輸送され、クレーンで設置され、支持構造物に降ろされ、カバーが置かれる梁の上に立っている作業員によって配置されました。カバーは支持構造に機械的に固定されていませんが、Vergaraは、「非常に深刻な事態が発生した」場合を除いて、カバーを移動または取り外すようには設計されていないと述べています。
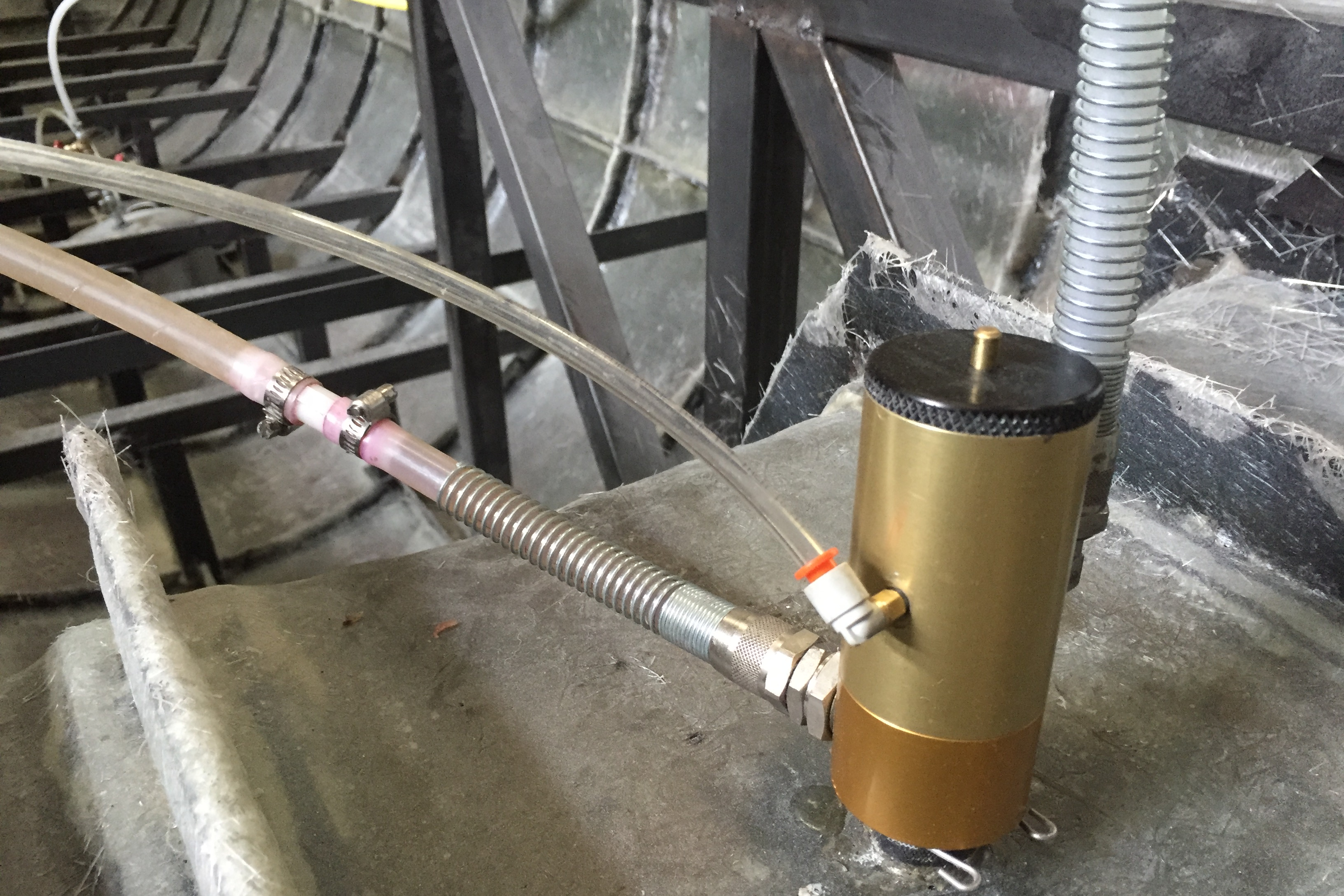
Solingは、2019年の初めにカバーの設計作業を開始し、2020年に最初のカバーの製造を開始しました。コロナウイルスのパンデミックと時折の機械的問題により、製造が停止および開始しましたが、Vergaraは、Solingが7年間で840のカバーすべての生産を完了したと述べています。 8か月で、2020年後半に終了します。新しいカバーは、交換したものよりも大幅に長持ちし、メンテナンスがはるかに少なくて済むと予想されます。
カサブランカプロジェクトは、高品質、高性能、大型の複合構造の製造業者としてのソリングの能力を実証し、他の機会への扉を開いたとヴェルガラは言います。 「このプロジェクトは、この製造方法ではこの規模の部品を製造できないというパラダイムを打ち破らなければならないという課題でしたが、それでも私たちはそれを行いました」と彼は言います。 「ソリングの将来については、何かが非常に明確です。私たちが実行できないプロジェクトはありません。」
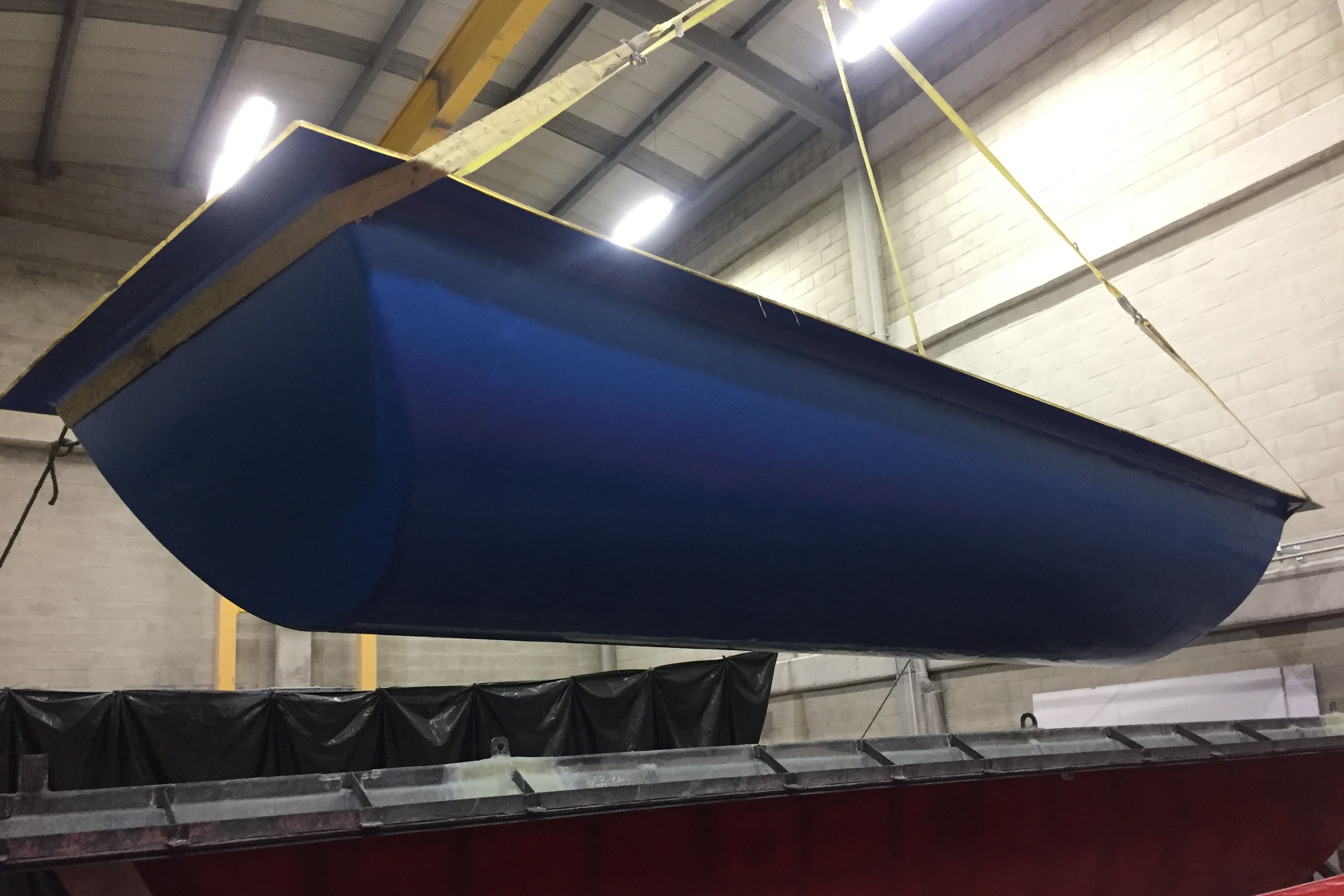
樹脂