複合材料のコストパラダイムに革命を起こす、パート2:成形
DARPAのTailorableFeedstock and Forming(TFF)プログラム内のRAPMサブプログラムは、現在/過去の生産からの分析データと、これらの曲線を生成するための複数の部品に対する独自の成形試験からの経験的データをまとめました。目標は、複合部品とプロセスのトレードスペースをよりよく理解することです。
すべての画像の出典:ボーイング社、DARPA
調整可能な原料と成形(TFF)プログラムは、国防高等研究計画局(DARPA、アーリントン、バージニア州、米国)によって2015年に開始され、防衛用の小型で複雑な形状の複合部品の迅速、低コスト、俊敏な製造を可能にしました。航空機。この48か月のプログラムは、複合材料の軽量化と、機械加工されたアルミニウムと比較した場合の腐食や亀裂に対する耐性を活用するために、複合材料のコスト競争力を高めることを目的としています。このシリーズのパート1では、 CW TFFのビジョンと、成形用の調整可能なユニバーサル原料(TuFF)サブプログラムを検討しました。このサブプログラムは、高い機械的特性と金属のような成形性を備えた短繊維シート材料を開発しました。
この記事では、原料からTFFの2番目のサブプログラムであるボーイング社(米国イリノイ州シカゴ)が主導するRApid高性能製造(RAPM、「ラップエム」と発音)を使用した成形に焦点を移します。このプログラムは2016年7月に開始され、SAMPE 2019で6つの論文と2つのプレゼンテーションを含む多数の出版物でその結果を発表しました。ボーイングのテクニカルフェローであり、主任研究者であるGailHahnとTomTsotsisが説明するように、RAPMの目標は「コストパラダイムに革命を起こすことです。小さな複合部品であり、防衛用途で広く使用できます。」
「私たちは、自動車の効率で航空宇宙性能を達成するというこのビジョンから始めました」とハーンは言います。このプログラムは、Solvay Composite Materials(米国ジョージア州アルファレッタ)、SGL Composites(オーストリア、Ried and Ort im Innkreis)などの自動車用複合材料および部品メーカーと協力しましたが、航空宇宙特性の達成は必ずしも簡単ではありませんでした。 「低温で急速硬化するエポキシは自動車用途ですぐに利用できますが、航空宇宙の要件を満たすにはほど遠いです」とTsotsis氏は言います。 RAPMは、航空宇宙グレードの樹脂注入部品を対象とした、新しい急速硬化型の2液型エポキシを使用しました。ただし、当初、SGLの成形システムは130°Cを超えることができなかったため、ツールで30分の時間という目標を達成できませんでした。
「私たちの目標は、高速ワークセルを使用してシステムレベルのコストを削減し、機械加工されたアルミニウムとコスト競争力を持たせるために、ツールで最大30分の時間を達成することでした」とTsotsis氏は言います。 「ボーイングの範囲内で、防衛アプリケーションで見たすべてのものを満足させることができました」とハーン氏は付け加えます。 「熱可塑性プラスチックで2〜6分かかるのに、なぜここに設定するのですか?熱可塑性プラスチックは、対応する工具の制約を伴うさらに高温の処理を必要とするため、私たちの目標は、サプライチェーンに多くのオプションを提供することです。」
プログラムが進むにつれ、航空宇宙材料やメーカー、さらにはソルベイのXEP-2750などの実験システムにも開放されました。 「当初は、2007年から2012年にかけてDARPAプログラム「非オートクレーブ製造技術」でCYCOM 5320-1を使用した場合と同様に、このシステムを完全に評価できると考えていました」とハーン氏は言います。同程度の評価は不可能でしたが、XEP-2750は現在ソルベイによってCYCOM EP-2750として商品化されています(オンラインサイドバー「RAPMでの圧縮成形用の新しいプリプレグ」を参照)。 」)そして、多くのRAPMパートトライアルと学んだ教訓から恩恵を受けました。
「私が欲しいのは、貿易調査でアルミニウムに勝つことができる小さな複合部品のいくつかのプロセスです」と、複合材業界とTFFプログラムコンサルタントのジェフヘンドリックスはRAPMの目標について述べています。それで、RAPMは成功しましたか? CW 時間とコストを削減する方法を追求しながら、複数の材料とプロセスを通じて12を超える航空宇宙部品の構成を比較しながら、数百の部品を製造するプログラムの取り組みを探ります。
プログラムフレームワーク
主要な業界パートナーと協力して、RAPMは3つの主要なトラックで部品を試しました:
- レジン注入 HITCOカーボンコンポジット(米国カリフォルニア州ガーデナ)およびSGLコンポジットを使用
- 熱硬化性プリプレグ Solvay Composite Materials(Heanor、U.K。and Anaheim、CA、U.S。)、Fiber Dynamics(Wichita、Kan。、U.S。)およびReinhold Industries(Santa Fe Springs、CA、U.S。)
- 熱可塑性成形 ATC Manufacturing Inc.(米国アイダホ州ポストフォールズ)およびTxV Aero(米国ロードアイランド州ブリストル)との提携
成形試験は2つのフェーズで完了しました。最初の「製造開発」フェーズ(図1)と、それに続く「チャレンジと移行」(C&T)パーツ(図2)からチャレンジまでです。 初期の開発と移行 機械加工されたアルミニウムに勝つ可能性のある候補者。
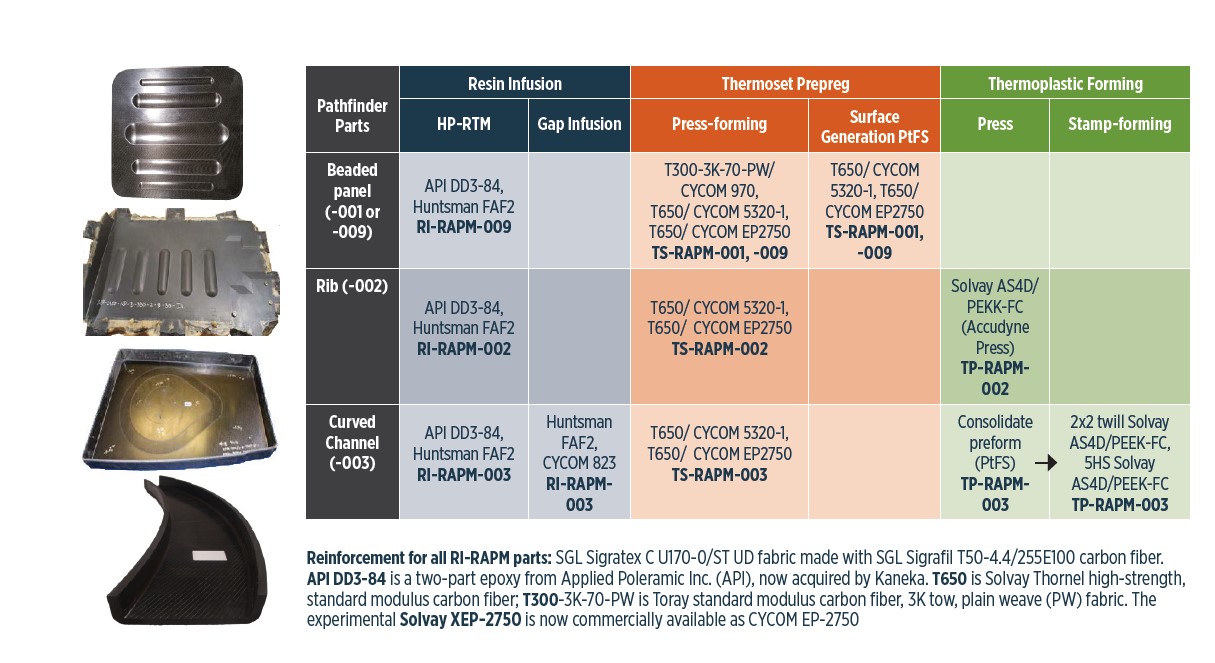
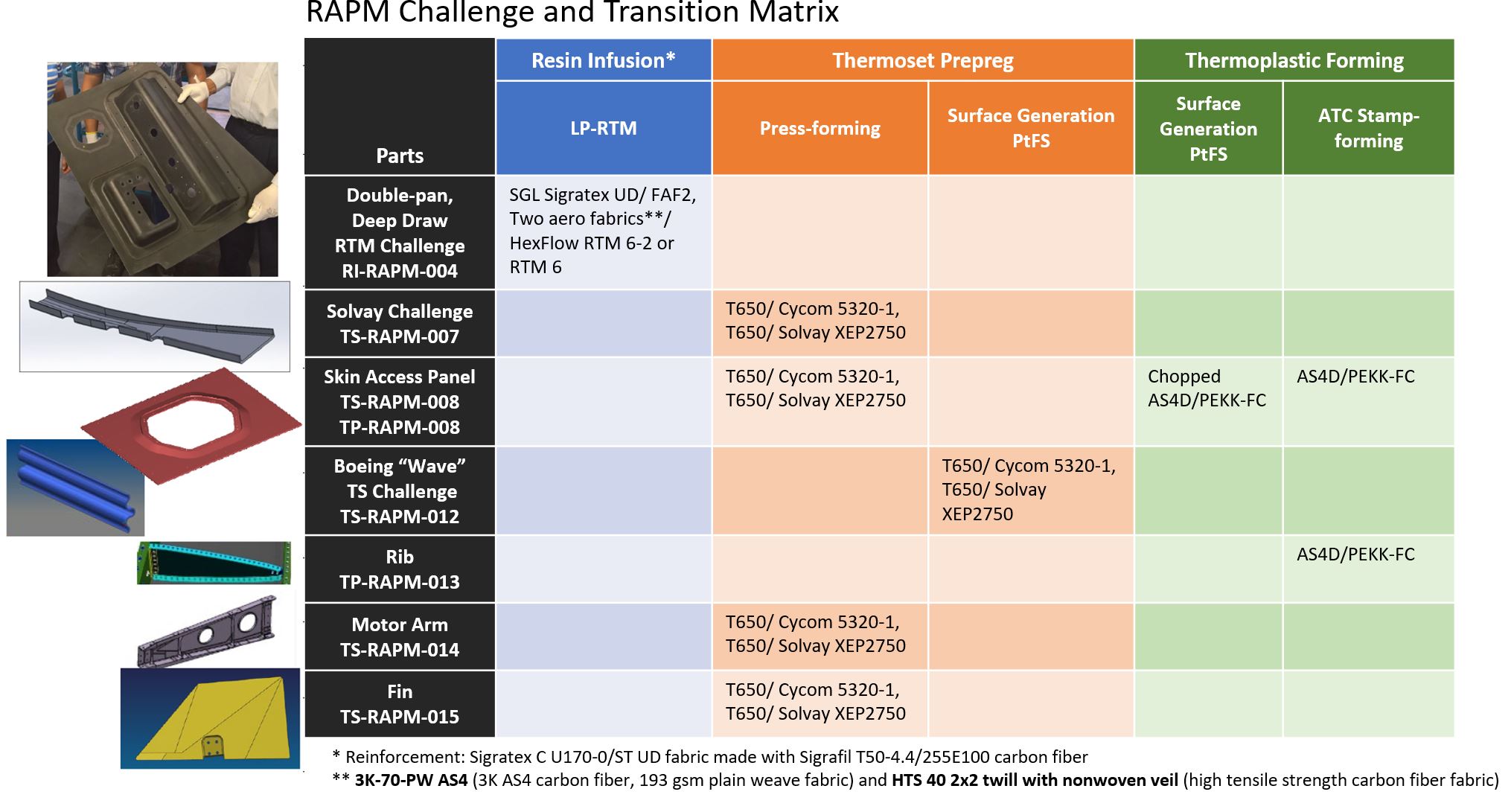
製造開発 試験では、3つの主要な部品構成を使用しました。ビードパネル(2つのタイプがありました)、パッドアップ付きのリブ(プライビルドアップ)、および湾曲したCチャネルです。製造上の課題を引き起こす可能性のある航空宇宙部品に共通するこれらの組み込まれた機能:ビードパネルには、複数の面外機能に加えて、パッドアップ、パッドダウン、および垂直エッジがありました。リブパネルには、複数の90度のエッジと、エッジの1つにジョグルがあるパッドアップがありました。また、Cチャネルの内側と外側の半径が異なり、フランジの曲率が異なり、ウェブのプライが大幅に低下しました。
目標は、3つのトラックそれぞれの設計と製造のガイドラインを作成することでした。 「これらの最初の試行を行うのはセクシーに見えませんでした」とハーンは回想します。 「しかし、それらは、不要な繊維の歪みのない部品を生成する許容可能な半径と部品の形状、および適用される張力、温度、圧力、工具の時間などのパラメータの最適な組み合わせを決定するのに役立ちました。」
3つのRAPM材料およびプロセストラックすべてに、Surface Generation(Rutland、UK)Production to Functional Specification(PtFS)ピクセル化加熱制御およびツールシステムを使用した試験が含まれていました(オンラインサイドバー「 PtFSを使用したRAPM開発」を参照) 」)、米国ミズーリ州セントルイスのボーイングR&Tにあります。「これは、柔軟な料金環境で3種類すべての材料/プロセスに対応できるワークセルを探していたために起こりました」とハーン氏は言います。 「さまざまな温度制御アプローチとコストを調査することができました。」ボーイングPtFSセルの最高温度は440°C、型締力は150トン、有効部品量は750 x 750 x100ミリメートルです。
当初のビジョンはTuFF短繊維シート材料を使用することでしたが、これらは最初から入手できなかったため、RAPMは代理材料を使用しました。これは、複合材料業界にとって実際に有益です。これは、サロゲートが、このプロジェクト以外で使用および開発されているもの(自動車用有機シートおよび航空宇宙認定プリプレグ、実験用エポキシ、半結晶性熱可塑性プラスチック、およびチョップドプリプレグ化合物)をより反映する材料にまたがっているためです。したがって、結果と調査結果は、防衛関連のメーカーだけでなく、すべてのタイプの複合材メーカーに関連しています。
トラック1:レジン注入/ RTM製造
このトラックでの製造開発試験は、自動車タイプの材料とプロセスから始まりました。部品は、高圧樹脂トランスファー成形(HP-RTM、300 bar)およびC T50標準弾性率、50K炭素繊維非圧着布(ドイツ、ヴァッカースドルフのSGLカーボン)を使用して、3つの部品構成でSGLコンポジットによって作成されました:RI-RAPM-009 、RI-RAPM-002、RI-RAPM-003(図1)。これらは、高品質の完成部品に必要なプリフォームパラメータを特定するために使用されました。ギャップ注入(圧縮RTM、またはC-RTM)も、ボーイングセントルイスがPtFSシステムを使用してRI-RAPM-003に対して試行されました。
計算フローモデリングを使用して、これらの部品を注入する方法をよりよく理解し、プロセスの動作を分析して材料とプロセスパラメータを最適化し、射出シナリオを評価しました。
繊維の歪みを最小限に抑えるために、さまざまなタイプのプリフォーム形状に張力を適用する方法とタイミングについて、ツーリングアプローチを評価しました。これらの設計変更は、変更されたCチャネルの形状に対して検証され、その後、コンピューター断層撮影(CT)分析が行われました。学んだ教訓は、その後のC&Tフェーズに適用され、コストを削減するために低圧RTM(LP-RTM)に移行しました。
これらのパスファインダー部品の試験では、深絞り半径のいくつかで層間剥離が見つかりました。 Tsotsisは、これらはツール内の樹脂の不十分な初期硬化(SGLの蒸気加熱システムがツール内の温度を130°Cに制限したため)と、部品の取り外し中の熱的/機械的な面外応力の組み合わせによって引き起こされたと考えています。 「樹脂の強度がまだ十分に発達していないため、これらの異常は、ツールを完全に硬化させることで解消できた可能性があります」と彼は示唆しています。 「SGLはツールとの両方の時間を満たすことができませんでした オイル加熱(蒸気のみではなく)がツールに追加されるまでの航空宇宙特性により、130°C以上での硬化が可能になります」とハーン氏は述べています。これは、製造開発の試行後に追加されました。
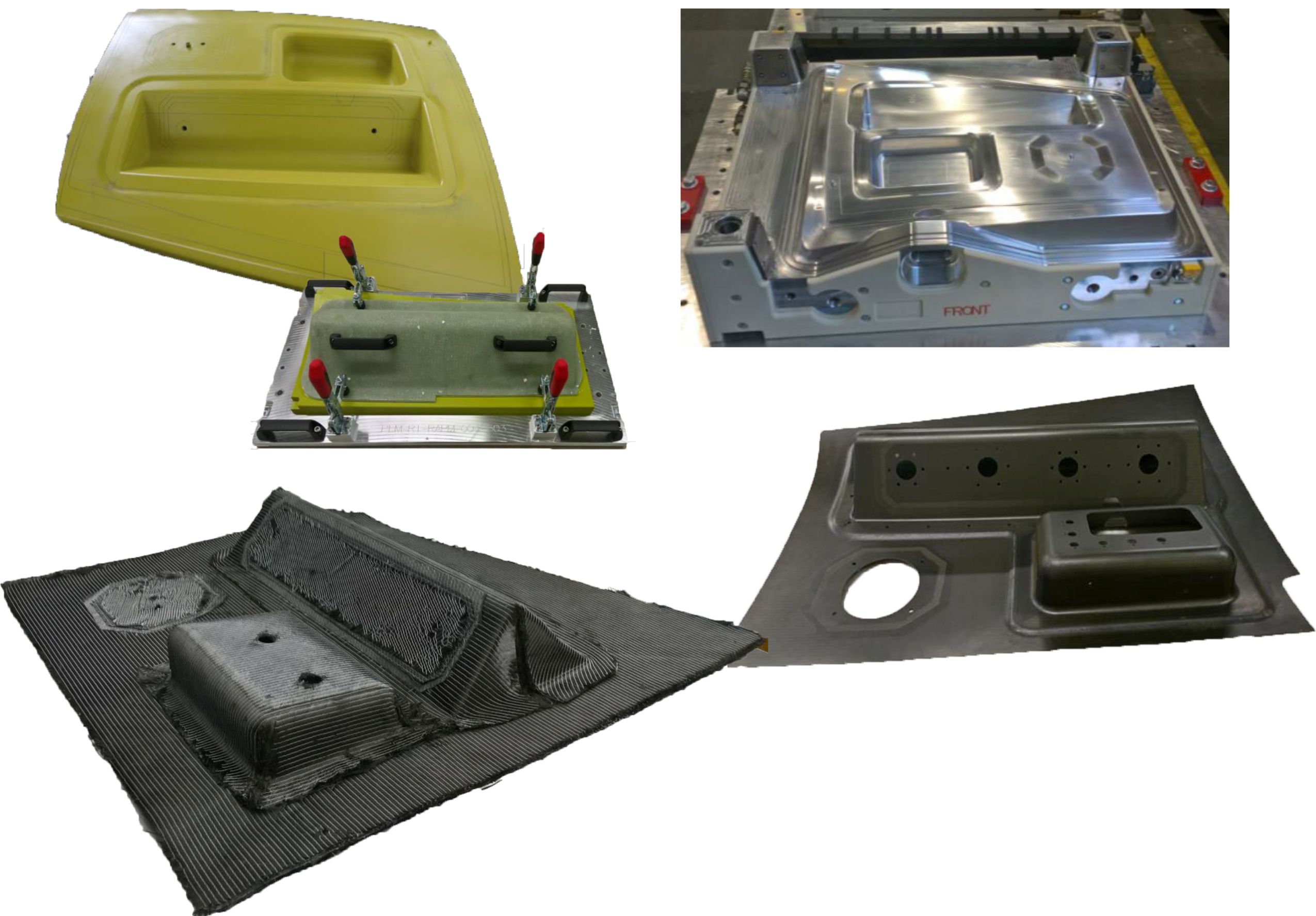
深絞りチャレンジパート
次に、製造開発試験の結果を使用して、チャレンジおよび移行試験を開発しました。 RI-RAPM-004深絞りチャレンジパーツ(図3)のモデリングも完了しました。このパーツは、5センチメートルの長方形領域と10センチメートルの長方形からV字型に遷移する領域の2つの深絞りを特徴としています。生産パンアセンブリに触発されたその複雑な形状により、不均一な樹脂流路が確保されました。 Huntsman(バーゼル、スイス)は、PAM RTMソフトウェア(ESI Group、パリ、フランス)を使用して、FAF2 2液型エポキシ(Huntsman、The Woodlands、テキサス州、米国)とSGL Carbon NCF150を使用したLP-RTMプロセスのフローモデリングを実行しました。 -1平方メートルあたりのグラム数は2軸で、190グラム/平方メートルの単方向(UD)補強材です。
RI-RAPM-004は、皮膚用に1つのプリフォーム、深絞りセクションごとに1つ、および2つのビルドアップ領域で構成されています(図3)。これらのプリフォーム要素には、設計されたパネルの厚さに合わせてさまざまなレイアップが使用されました(「 RAPMの複雑な形状の部品の製造」を参照)。 」)。
「低圧プリフォーミングとLP-RTMにより、(鋼と比較して)費用効果の高いツールを使用できました。手動クランプを備えたプリフォームツールは、ポリウレタンベースのRaku-Tool材料(RAMPF Tooling Solutions、Grafenberg、ドイツ);硬化ツールは5083アルミニウムで作られました。
最初のRI-RAPM-004試験では、出口付近の流れに予期しない異常があり、表面の層が浮き上がり、繊維の歪みが発生していることが示されました。インレットとアウトレットを逆にすると、問題が解決しました。 130°Cの工具で注入して最初に硬化させた後、部品を180°Cで60分間後硬化させた後、ネット形状に機械加工しました。自動超音波システム(AUSS)Cスキャン用に10個の高品質部品がボーイングに納入されました。
完成したチャレンジパーツは、完全な統合、優れたファイバーアライメント、および高品質を示しました。部品は、197°Cのガラス転移温度と49.5%の繊維体積分率(FVF)を示し、使用されたNCFに典型的でした。部品のレイアップ部品数は、現在のプリプレグプロセスと比較して3分の2以上削減され、タッチ作業は推定90%削減されました。 RAPMはまた、開発したツールとプロセスの適応性をテストするために、航空宇宙認定の樹脂とファブリック、および非破壊検査(NDT)の製造要件に合格した製造部品を使用して課題を作成しました。
トラック2:TSプリプレグ形成

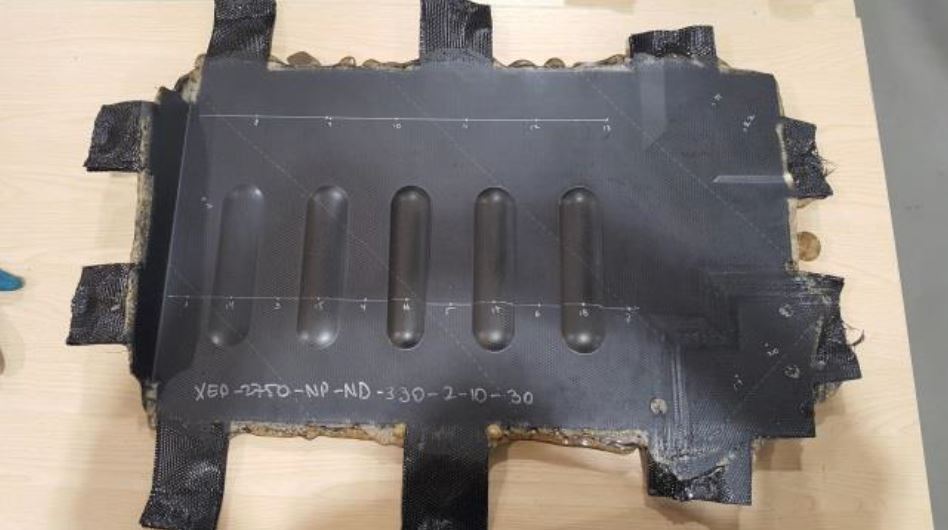
3つの製造開発熱硬化性(TS)プリプレグ部品が、英国のヒーナーにあるソルベイのアプリケーションセンターで、スプリングフレームスタンピングおよび/またはダブルダイアフラムフォーミング(DDF)を使用して製造されました。 3つの部品はすべて、CYCOM 5320-1、CYCOM 970、およびCYCOMEP-2750航空宇宙システムを含むソルベイ樹脂に基づくエポキシプリプレグを使用して製造されました。 「CYCOM5320-1は、脱オートクレーブ(OOA)部品の頼みの綱ですが、オートクレーブの認定システムとしても使用されています」とハーン氏は言います。 「CYCOM970は溶剤対ホットメルトプリプレグオプションです。[CYCOM] EP-2750は、プロセスの物理学と動力学に最適化されており、最良の部品を製造できることを示したため、プレス成形用のシステムです。」
スプリングフレームスタンピングとDDFは、熱硬化性プリプレグを切断、照合、および2Dプリフォームに統合する等温圧縮成形プロセスです。次に、プリフォームは予熱され、適合した金属工具にシャトルされ、従来の油圧プラテン印刷機で成形されます。プリフォームは、スプリングフレーム(図4)によって張力をかけられた状態に保たれます。これにより、成形中に材料の圧縮ゾーンによって引き起こされるしわが減少します。あるいは、DDFはプリフォームを2つのダイアフラムの間に挟み、金型のクリーニングとリリースの必要性を排除します。プリフォームはダイヤフラムの1つにテープで固定されており、直接ではありませんが、基本的に張力がかかった状態で保持されます またはスプリングフレームのように調整可能。 RAPMでは、ばねのタイプ、位置、および張力は、ばねフレームと同様に、シミュレーションを使用して各部品に対して最適化されました。たとえば、ビーズパネルTS-RAPM-009は、上下に作動して、プレスの閉鎖と並行してチャージの形成を調整できるフレームを使用していました。
RAPMは、15〜30分の初期硬化後に寸法的に安定した部品を取り外し、その後、バッチ後硬化してレート能力を高めることにより、部品のオンツール時間を最小限に抑えました。セルの使用を最大化するために、単一のツールセット(たとえば、翼の長さに沿って3つの異なるフランジ角度を持つCチャネル)を使用してパーツファミリも調査されました。 RAPMTSアプローチを導くその他の目標は次のとおりです。
- 手作業を最小限に抑えるための自動照合とフォーミング
- 177°C硬化の航空宇宙機械性能
- ツールセットあたり1,000個を超える部品が可能な鋼製工具。
チャレンジパートを「波打つ」ための開発
熱硬化性プリプレグ製造開発部品が形成され、十分な部品品質に達するまで、一度に1つの変数にインデックスが付けられました。レオロジー曲線の正しいポイントで材料を圧密して内部静水圧を生成し、樹脂のブリードを最小限に抑え、硬化が進みすぎないようにして、亀裂を回避することを目的として、プレスの閉鎖速度、閉鎖位置、閉鎖圧力などの変数を評価しました。誘導。成形パラメータを設定したら、プロセスの再現性を検証するために3〜5個の部品を作成し、品質をテストしました。ビーズパネルは、高い圧密圧力(20.7バール)のために<0.5%の気孔率を示しました。再現性のある高品質のリブも製造されました。
次に、学んだ教訓を波形の「波」チャレンジパーツTS-RAPM-012に適用して、曲率が狭い(12.7ミリメートル)形状の厚い(公称厚さ6.3ミリメートル)UDラミネートの圧縮成形を実演しました。要件を満たすために、パーツは中間弾性率(IM7; Hexcel; Stamford、Conn。、U.S。)カーボンファイバーUDテープの準等方性レイアップを使用しました。スタイル108グラスファイバーファブリックとSolvayTHORNEL T650標準モジュラスカーボンファイバーの8ハーネスサテンファブリックの外層は、UDファイバーを保護し、金属部品に結合する側のガルバニック腐食を防ぎます。 Solvay CYCOM 5320-1エポキシ樹脂を使用すると、177°Cで2時間の自立型後硬化により、より短い長さ(≤30分)の等温硬化サイクルが可能になりました。
ウェーブチャレンジパーツは、ボーイングのPtFSワークセルと、真空シールと樹脂シールが統合されたP20鋼の金型面を使用して成形されました。ツールキャビティは、材料の樹脂含有量の変動を考慮して、公称ラミネート厚さよりも薄く、高品質の部品の内部静水圧を維持しました。
冷間成形(熱を使用しない事前成形プライ)、熱間デバルク予備圧密、およびプリフォームの予熱を含む3つのプロセスパラメータがテストされました。冷間成形は時間がかかり、役に立たなかったとして却下されました。予備固結のために、ラミネートをガラス繊維ブリーザーで織ったプレートに真空バッグに入れ、116℃のオーブンで40分間完全真空下で減量した。自動赤外線予熱は工業生産の標準ですが、これらの試験では、予熱はプリフォームをホットモールド(179°C)に入れ、3分間触れずに可能な限り閉じることで構成されていました。次に、成形品を圧縮成形しました。
完了した9つのトライアル8(#0-8)は、主に事前統合に起因する最高品質のパーツを生成しました。そこから採取したサンプルは、厚さ(他の部品の問題)とラミネート品質を満たし、繊維量は59〜63%、ボイド含有量は0〜0.6%でした。
トラック3:膀胱形成されたTPリブとCチャネル
RAPMは、製造開発試験からTP-RAPM-002リブを選択して、原材料から完成した複雑な部品までのシングルステップ圧縮成形を実証し、TP-RAPM-003湾曲チャネルを2ステップアプローチとして選択しました。ボーイングセントルイスは、Accudyne Systems(Del。、U.S。)プレスを使用して-002リブを成形し、PtFS装置を使用して-003Cチャネル用のブランクを統合しました。 2番目のステップでは、ATCManufacturingがCチャネルブランクをパーツにスタンプしました。
-002リブの場合、RAPMはソルベイが提供する12インチ幅のUDテープを使用しました。12KAS4Dカーボンファイバー(Hexcel、米国コネチカット州スタンフォード)で強化されたポリエーテルケトンケトン(PEKK)です。 Cramer Fabrics Inc.(Dover、N.H.、U.S。)の-003 Cチャネル使用済みファブリック:2x2ツイルの3K AS4(Hexcel)サイズなしカーボンファイバー、ポリエーテルエーテルケトン(PEEK)で粉体塗装。繊維の面積重量は250グラム/平方メートルです。樹脂含有量は42%です。
熱可塑性(TP)形成の問題
TP複合材料は、熱硬化性樹脂よりも高い温度で処理されます(たとえば、PEEKの場合は390°C、PEKKの場合は375°C)。これには多くの問題があります。これらの高いプロセス温度を処理できる工具材料は限られています。さらに、部品の処理と取り外しの間の大きな温度差により、均一な工具温度を維持することが困難になります。改善策は、熱を吸収したり、ランプを上下に遅くしたりすることです。これにより、サイクル時間が長くなります。
高温はまた、熱膨張係数(CTE)の課題を提示します。工具材料のCTEは、多くの場合TPラミネートのCTEとは異なります。これにより、TPラミネートが工具から収縮し、加えられる圧力が低下し、完全な圧密が妨げられる可能性があります。また、TPラミネートCTEは炭素繊維に沿って一定ですが、繊維に垂直な双直線曲線です。これにより、TPラミネートが加熱および冷却されるため、面内と面外で収縮が異なります。これは、工具設計でも対処する必要があります。
TPラミネートは、液体から固体への変化に伴って樹脂の体積が減少するため、工具から収縮することもあります。重要な樹脂マトリックスの結晶化が発生するのは、この冷却段階であり、完成品の高品質な特性を確保するには、温度の均一性とラミネート圧力を正確に制御する必要があります。
もう1つの問題は、成形中に溶融TP液を収容するためにツールを完全に密閉する必要があることです。 「375°Cから390°Cでツールをシールすることは困難です。この温度を処理できる適合ガスケットが非常に少ないためです 300〜500psi以上のTP成形圧力」とハーンは言います。 「シーリング機能を提供するために、金属ガスケットまたは対応する金属工具のいずれかに限定されています。エラストマー工具は非常に有益ですが、現在のエラストマーはすべてTP成形温度で分解します。」
ボーイングセントルイスでは、垂直作動のみの油圧プレスでの圧密中に、リブの垂直要素に水平方向の圧力を加えるための新しい工具が必要でした。その解決策は薄いアルミニウムブラダーでした(同様のシステムを使用してTP-RAPM-003を形成しました(図5))。高温で不活性アルゴンガスで加圧されると、ブラダーが膨張し、圧密中にすべての部品表面に均一な圧力がかかります。
上部と下部のツールは、UDカーボンファイバー/ PEKKラミネートの面内CTEと一致する410ステンレス鋼で作られました。プレスサイクル中に、アルミニウムブラダーを備えた上部ツールが下降し、レイアップを下部ツールのメスキャビティにゆっくりと押し込みました。このワンステッププロセスで未固結のテーププリフォームの大部分に対応するために、ブラダーは最終部品の厚さから30%小さめになりました。このツールは、電気加熱カートリッジを備えた従来のプレスに取り付けられ、リブのフランジとウェブのツール表面温度を制御するために、12の独立して制御されるゾーン(およびプレスプラテンの6つのメインゾーン)に配線されました。
これらの成形試験により、合格のNDI結果をもたらす複合部品が製造されました。ただし、ブラダーツールの設計では、レイアップをパーツのタイトな内側半径に形成することを改善し、均一な表面の厚さを維持するために、さらに開発する必要があります。
PEEKファブリックブランクの統合
TP-RAPM-003湾曲Cチャネルの場合、使用された粉体塗装PEEK2x2ツイル生地は比較的高いバルクファクターを持っていました。ボーイングセントルイスは、最初に、パーツの長さに沿って32から24プライに落ちたレイアップを、テーパー断面のフラットブランクに統合し、次にブランクをATC Manufacturingに送信し、最後のパーツに垂直をスタンプしました。フランジ。
リブと同様に、ボーイングは成形ブラダーと鋼製の上下工具を使用しました。ブラダーは、アルミニウムよりも破裂に強いAZ31マグネシウムに変更されました。 Cチャネルツールは、Surface Generation PtFSフォーミングセル内で動作するように設計されており、リブにカートリッジヒーターを使用する従来のプレスと比較して、より迅速な加熱と冷却を可能にします。
Cチャネルツールアプローチは、複数のパーツの柔軟性を高めるために開発されました。レイアップを下部のツールに配置し、材料のガラス転移温度(T g )に加熱しました。 )溶けずに柔軟性を維持します。圧力シールガスケットを含む体積減少フレームを下部ツールの上部に配置し、パーツレイアップよりもわずかに大きいキャビティを残しました(図5)。熱と水圧がトップツールからブラダーを通ってレイアップに加えられました。成形温度に達したら、アルゴンガスをブラダーに適用し、ブラダーをフレームキャビティに押し下げて、テーパーブランクに圧力を加えました。次に、ブラダー圧力を維持しながら、材料の溶融段階を通じてツールの温度を上げました。これにより、溶融段階にあるときに材料が下部ツールを横切って流れるのを防ぎました。
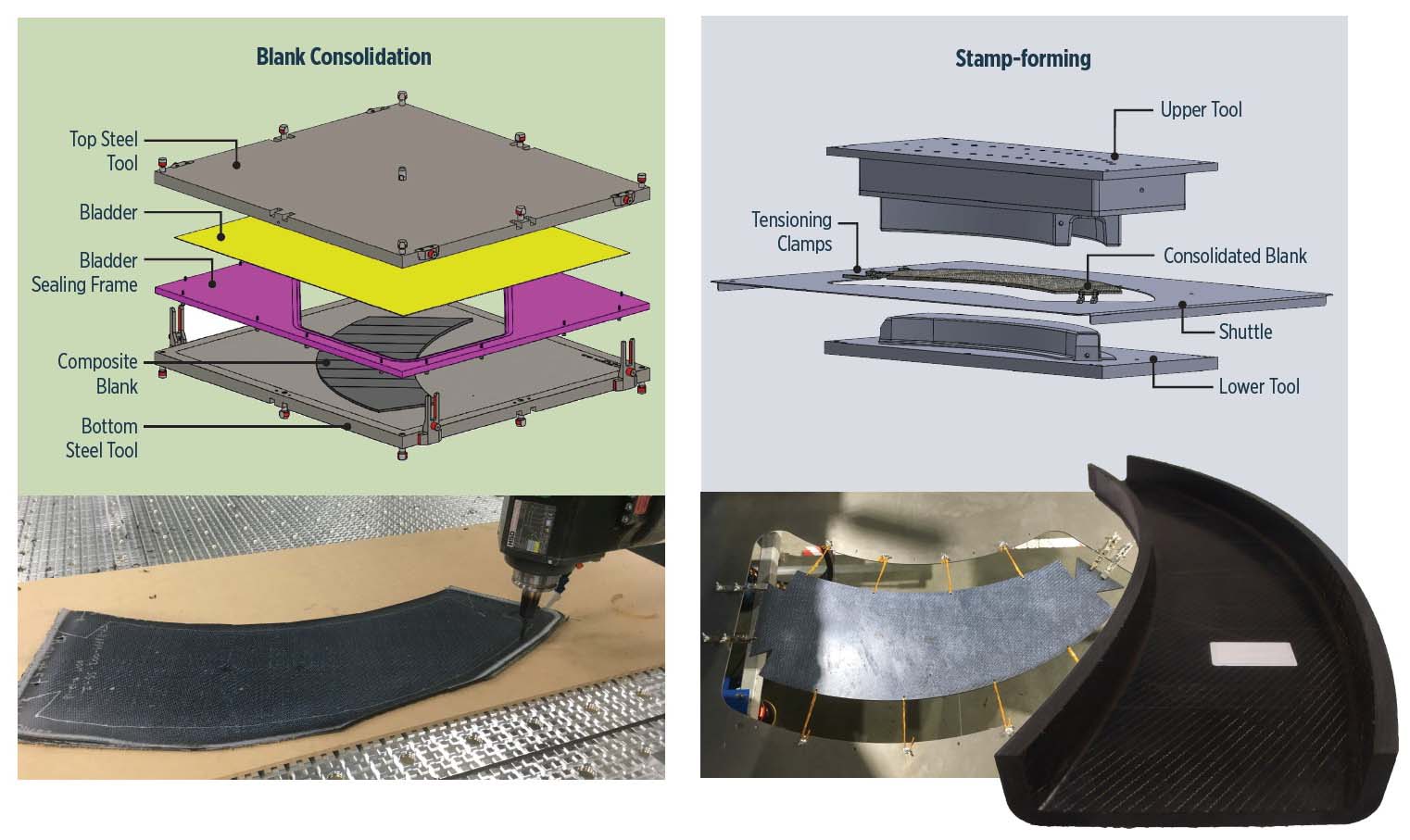
予備成形サイクル時間は、ブラダーとTPチャージがプロセス温度に達するまで55分、PEEK結晶化温度以下に冷却するために30分で構成されていました。圧力は1.4から9.7バールの範囲で、バルブ付きの高圧タンクから手動で維持されました。最近、プレスクレーブが組み込まれました。 システムをPtFSセルに組み込むと、プレス金型キャビティ内の真空と圧力(±3psi)のオートクレーブのような制御が将来自動化されます。
TPスタンプ形成
-003 Cチャネル用の統合ブランクは、スタンプ形成のためにATC Manufacturingに送られました。そこでは、ブランクが溶融温度を超えて十分に加熱され、ポリマーの流れが確保されます。次に、それを急速に閉じるプレスに移して、部品を迅速に形成および冷却した。プレスの成形工具は一定の温度に保たれ、ランプアップとクールダウンを排除することでサイクルタイムを短縮できます。ツールの温度は、溶融温度とT g の間でなければなりません。 必要なレベルの熱可塑性マトリックスの結晶化度を短時間で開発し、変形することなく部品を確実に取り外すことができます。熱電対が埋め込まれた一連のブランクを使用して、Cチャネルをスタンプ形成するための完全な熱サイクルを検証しました。
Aniformソフトウェア(オランダ、エンスヘーデ)を使用した成形シミュレーションでは、ドレープ性の高いPEEKファブリックブランクが、圧縮領域、つまり内側(半径が小さい)フランジにシワのリスクがあることが示されました。したがって、シャトルプレートとクリップを含む張力システム(図5)は、一致する金属ツールが閉じてブランクを形成するときに、ブランクを張力で保持しました。それにもかかわらず、圧縮されたフランジ面は、繊維が内側の半径で内側に押されたときに座屈を示しました。 「3つのRAPMトラックはすべて、この部分を作るのに苦労しました」とハーンは主張します。 「その形状は極端であり、実際の部品を示すものではありませんが、成形性で達成できることを推進するように設計されています。」
製造開発試験は、TP-RAPM-008スキンアクセスパネルの複数のバージョン、フランジにジョグルを備えたTP-RAPM-013リブ、およびTP-RAPMの3つの異なる形状を使用したブラダー研究を含むチャレンジおよびトランジションパーツにつながりました。 -017パネル(図2)。ボーイングセントルイスは、ATCが製造したTP-RAPM-013リブを除いて、これらすべてを製造しました。 「この部品はUDテープで作られていましたが、これは通常、布地よりも成形が困難ですが、これらの部品を非常にうまく成形することができました」とATCManufacturingのR&DディレクターであるTrevorMcCrae氏は述べています。全体として、TP成形試験では、スタンプ成形により、従来の圧縮成形では不可能な複雑な形状が生成される可能性があることが示されました。
アルミニウムと比較してコストを削減する方法を学ぶ
RAPMは、3つのトラックすべてで新しい成形機能を実証し、圧縮成形中の滑りを防ぐためのパッドアップの配置方法から、品質を最大化し、金型コストを最小化するための部品形状のガイドラインに至るまで、多くの教訓を蓄積しました。 「面外の特徴、半径と厚さの比率、および幾何学的詳細間の距離の影響を理解することは、小さな部品に移動するときに重要になります」とハーン氏は述べています。 「半径、曲線、フランジ角度などの機能を標準化することで、コスト要因を軽減できます。たとえば、標準のAUSSシューを有効にすることで、工具コスト、開発中の成形試行回数、NDI(非破壊検査)中の複数のスキャンの必要性を削減できます。パーツのファミリー。」
RAPMが強調したもう1つのコスト要因は、TSプリプレグ圧縮成形中の時間のかかる事前統合ステップでした。 「低バルクで樹脂含有量の高いプリプレグは、プロセスウィンドウを広げ、高品質の部品の再現性を高めます」とハーン氏は説明します。 「ソルベイは、圧密成形中に金型キャビティ内の静水圧を保証する方法として、圧縮成形前に低含浸プリプレグに適用できる特許出願中の「トランスフォーマーフィルム」を開発しました。」
RAPMは2020年秋まで正式に終了せず、その後に追加の公開された結果が続きますが、実際の防衛プログラムに基づく選択された部品のこれまでの調査結果は、複合材が 機械加工されたアルミニウムと競合します(図6)。選択した樹脂注入およびTP部品は、経常コストを削減します。たとえば、非経常インフラストラクチャが整っていると仮定して、ファミリごとの総部品に対して計算された材料、機械時間などですが、TS-RAPM-012ウェーブアセンブリは実際には7%増加 対機械加工されたアルミニウム。ただし、目的の重量は達成されます 節約、および ヘンドリックスが義務付けているマージンの範囲内にあるプレミアムで、次のように述べています。アルミニウムの10パーセント以内の費用がかかる必要があります。」しかし、彼は認めています。「形状をうまく形成するために必要な工具や開発など、理解するための時間とコストの問題はまだ発生していません。」
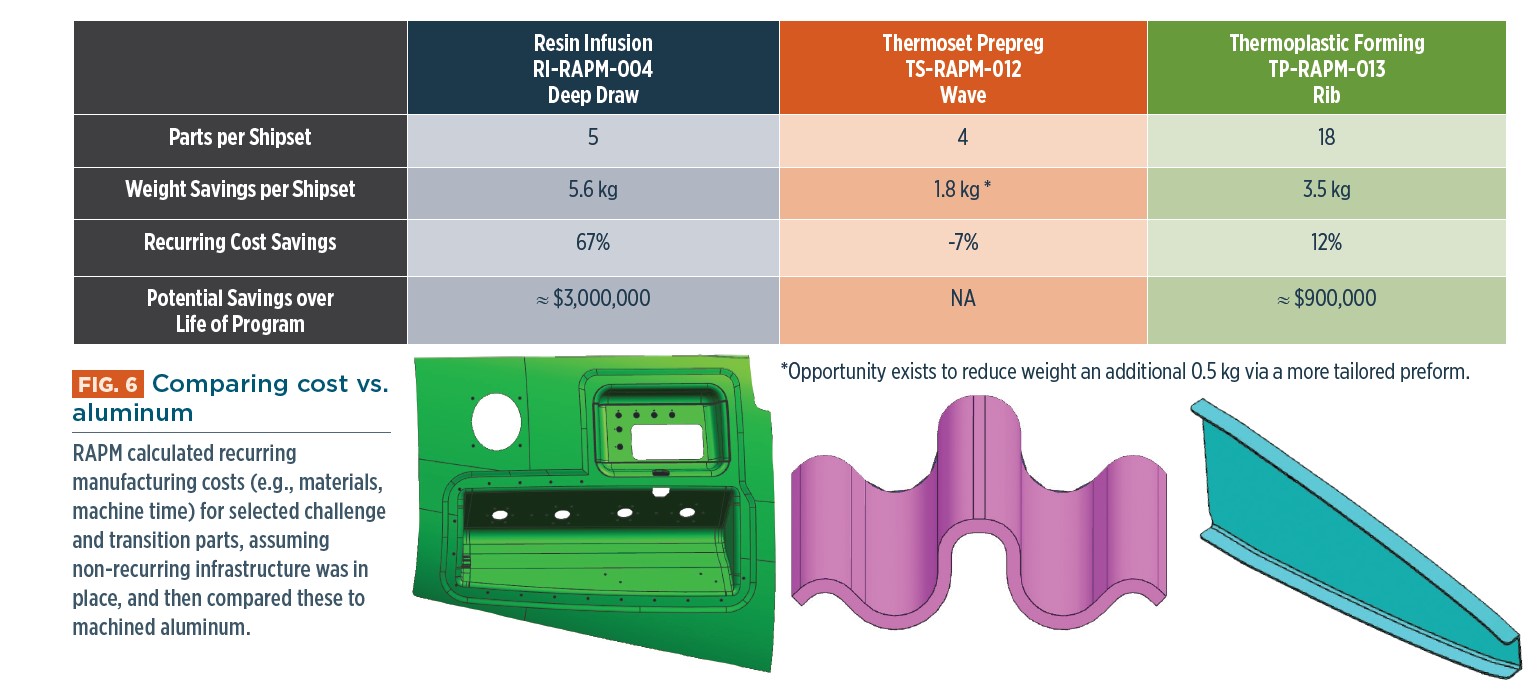
拡張オプション
樹脂注入は大きな部品に勝ちますが、ハーンは言います、TSとTPのスタンピングは小さな部品にはかなりよく見えます。 「金属部品が非常に複雑で、多くの機械加工が必要な場合を除いて、樹脂注入の初期工具費を克服するのは困難です」と彼女は説明します。
「熱可塑性プラスチックは大量生産には適していますが、特定のプログラムの下請け業者が熱可塑性プラスチックを製造するように設定されていない可能性があります。ただし、少量の交換部品の場合でも、熱硬化性スタンピングは非常に優れたオプションである可能性があります。防衛用途は非常に広範囲にわたるため、貿易に関する議論では複数の資料とプロセスを用意することが重要です。」ハーン氏は、RAPMが新しい材料を開拓し、実証済みの航空宇宙材料が自動車タイプのプロセスで機能する可能性があると述べています。 「新しいメーカーも導入しました。」
ヘンドリックスは、RAPMの航空宇宙および自動車製造の交換が有益であったことに同意します。さらに、彼は、繊維の歪みやその他の欠陥なしに複雑な形状を形成するソルベイとSGLの能力に感銘を受けました。 「審美的な自動車部品を作るのに必要なことには、実際に利点があります」と彼は認めます。 「しわや表面仕上げが悪いことはありません。彼らは完璧でなければなりません。しかし、RAPMパーツを形成するには、それでも複数の試行と重要な開発が必要でした。防衛プログラムが少量を扱っている場合、この非反復エンジニアリングに投資するかどうかはわかりません。経済学はケースバイケースで行われますが、ツールと開発は私たちが取り組む必要のある問題のままです。」ハーンは、「私たちは学んだ教訓を公開し、拡張されたオプションでより多くの情報に基づいた貿易研究を可能にし、業界の議論のための合理的に開かれた基盤を確立しています」と付け加えます。 CW 今年後半にRAPMが終了したら、このディスカッションを更新して継続します。
樹脂