熱可塑性複合材料:前進する態勢
熱可塑性複合材料(TPC)は航空宇宙分野では目新しいものではありませんが、過去2年間で、民間航空機での熱可塑性プラスチックの使用が転換点に達しています。 TPCは、クリップやブラケットなどの小さな部品や小さな内装部品にしばらく使用されてきましたが、熱可塑性プラスチックは徐々に大きな航空機構造に組み込まれ、将来の民間航空機でより大きな役割を果たす準備ができているようです。
2018年3月、世界最大の炭素繊維メーカーである東レ(東京、日本)は、TenCate Advanced Composites(米国カリフォルニア州モーガンヒル、オランダ、ナイフェルダル)を9億3,000万ユーロで買収しました(TenCateはその後、社名を東レアドバンストコンポジット)。この動きは、民間航空機開発の次の波に備えて、東レの熱可塑性プラスチック機能を強化するための取り組みのようでした。その発表の直後に、Hexcel(米国コネチカット州スタンフォード)とArkema Inc.(米国ペンシルベニア州キングオブプロシア)は、炭素繊維製造におけるHexcelのスキルとArkemaのポリエーテルケトンケトンを組み合わせて、航空宇宙向けの熱可塑性複合ソリューションを開発する戦略的提携を発表しました。 (PEKK)樹脂の専門知識。そして、1年の間に、熱可塑性プラスチックのパズルの他のいくつかのピースが適切に配置されたように見えました。
2018年4月、Premium Aerotec GmbH(ドイツ、アウグスブルク)は、熱可塑性マトリックスに炭素繊維を使用して開発および製造したAirbus(フランス、トゥールーズ)A320圧力隔壁のデモンストレーターを発表しました。 8つの溶接セグメントで構成されるデモンストレーターは、熱可塑性プラスチックの溶接性が航空機の大型コンポーネントを可能にする可能性をどのように持っているかを示しています。 (プレミアムエアロテックのA320圧力隔壁デモンストレーターの詳細をご覧ください。)
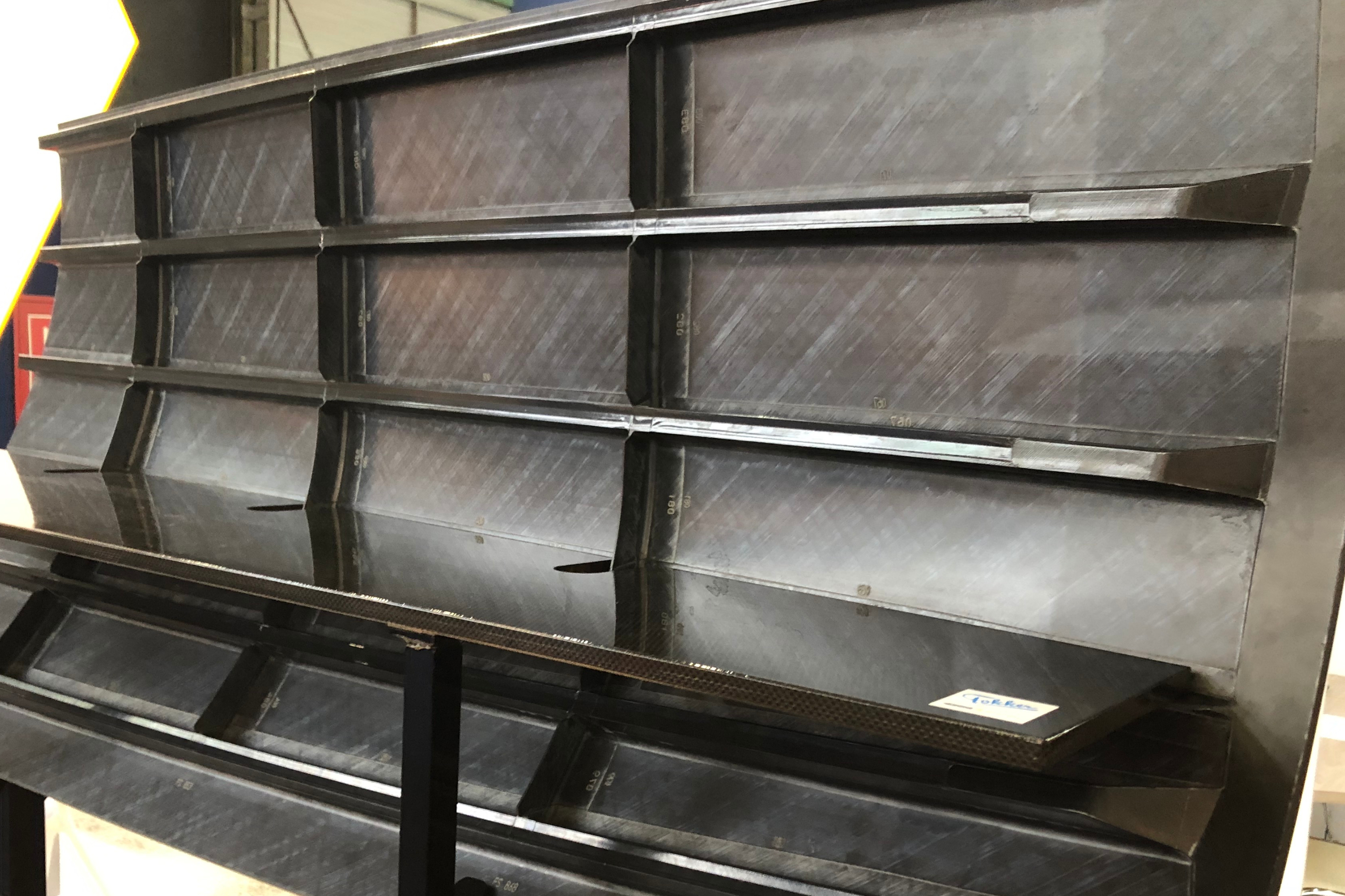
2018年8月、ソルベイ(米国ジョージア州アルファレッタ)、プレミアムエアロテックおよびフォルシアクリーンモビリティ(米国オハイオ州コロンバス)は、材料の開発と航空宇宙および自動車市場向けの熱可塑性複合材料の大量生産を可能にすることを目的としたプロセス技術。このコンソーシアムは、材料から機械、自動車や航空宇宙への応用に至るまで、熱可塑性複合材料のプロセスチェーン全体に沿って企業を統合しています。 (IRG CosiMoコンソーシアムの詳細についてはこちらをご覧ください)。
ソルベイは、2017年6月からGKN Fokker(Hoogeveen、Netherlands)と提携して、技術を進歩させ、大型航空宇宙構造物にTPCをさらに採用しています。同社は、2017年9月にPEKKポリマーの生産を開始し、2018年に認定UD熱可塑性テープの容量を2倍にしました。 2019年、ソルベイは、次世代材料の開発を目的として、米国のアルファレッタにある専用のTPC研究所に委託しました。ソルベイは、2019年後半に新しいUDテープラインの認定を開始する予定です。
帝人株式会社(東京、日本)は、2019年1月に、そのTENAX炭素繊維および炭素繊維/熱可塑性一方向プリプレグテープ(TENAX TPUD)が、中級先進国として使用するためにBoeing(シカゴ、イリノイ州、米国)によって認定されたと発表しました。一次構造部品用の複合材料(ニュース記事全文はこちらをご覧ください)。
これらおよび同様の技術と材料が進歩するにつれて、航空宇宙産業が今後数年および数十年でどのように見え始めるかについての絵が徐々に焦点を合わせられます。 TPCの役割は、その全体像の中でますます大きな部分になりつつあります。
製造業者は、熱可塑性プラスチックの製造上の利点と高速処理時間を活用し、TPCを使用して胴体パネルやリブなどのより大きな構造の製造を開始することに関心を持っています。さらに、熱可塑性プラスチックは高い破壊靭性を誇っています。良好な機械的特性;リサイクル性;炎、煙、毒性(FST)が低く、室温で保存できます。また、OEMや航空宇宙分野のサプライヤーが熱可塑性プラスチックに精通するにつれて、それらはより複雑な部品、溶接アセンブリ、および一次構造に使用されています。
Toray Advanced Composites(旧TenCate)のマネージングディレクターであるSteve Mead氏は、次のように述べています。そのギャップ。」
TPCの処理可能性
TPCが航空機プログラムでその地位を確立している理由の大部分は、その処理能力です。熱可塑性樹脂はすでに完全に重合されているため、硬化が必要な熱硬化性樹脂よりも生産速度が速くなります。
「今日の熱硬化性部品の製造にかかる時間を見て、熱可塑性複合部品の製造にかかる時間と比較すると、[熱可塑性]は約10倍高速です」と社長のMikeFavaloro氏は述べています。複合材業界のコンサルタント会社であるCompositeTechsLLC(米国マサチューセッツ州エイムズベリー)のCEO。
熱硬化性AFPと比較した熱可塑性自動繊維配置(AFP)の大きな利点は、特に硬化サイクルがないことを考えると、処理時間が短縮されるため、生産速度が速くなることです。現場でのラミネーションと脱オートクレーブ(OOA)の統合後のコスト削減が見られます。さらに、オートクレーブを方程式から外すと、より大きな構造を開発できます。
ATC Manufacturing(Post Falls、Idaho、U.S。)の事業開発ディレクターであるDavid Leachは、熱可塑性樹脂の単価が熱硬化性樹脂のコストを上回っていることを認めていますが、TPC材料の価格は下がると主張しています。さらに、処理効率は今日のコストを削減する機会を提供すると彼は言います。複合材料業界の一般的なコンセンサスは、現在、OOA熱可塑性プロセスは、熱硬化性樹脂と比較して30%以上のコスト削減を提供するというものです。
「熱可塑性プラスチックは、飛行機が生産された後でもプログラムに取り入れられつつあります」とリーチ氏は指摘します。 「これは、熱可塑性プラスチックのコストメリットの証です。」
高性能マトリックスポリマーの可能性は、現在市場で入手可能なものを超えています。 SolvayのUltra-PolymersMaterialsの責任者であるDougBrademeyerは、同社は社内とパートナーの両方と協力して、さまざまな製造プロセスに合わせてカスタマイズされたテーラードポリマーを開発していると述べています。
「私たちはこれらのカスタマイズされたPAEKソリューションに興奮しており、顧客のニーズに基づいて、これらを世界規模の資産で迅速に商品化することができます」とBrademeyer氏は述べています。
低融点PAEK
航空機のOEMとサプライヤは、より高い生産率とより短いサイクルタイムを求めてスクランブリングを行っているため、加工性が重要です。ポリエーテルエーテルケトン(PEEK)は、最大のデータベースを持ち、最も広く認定されているため、長い間熱可塑性ポリマーとして支持されてきました。しかし、ファバロロによれば、低融点のポリアリールエーテルケトン(LM PAEK)は、特にATLのような自動処理方法に対していくつかの利点を提供します。
「PEEKはスタンプ成形と連続成形で処理できますが、LM PAEKは低温で処理され、作業粘度が低いため自動処理が向上し、結晶化度が低いため残留成形応力が低減されます」と彼は言います。 「最終的な目標は、ATLマシンを使用して[テープ]を敷設し、それを使用することです。適切な結晶度、良好なウィンドウ、および良好な敷設速度が必要です。」
LM PAEKには、350〜385ºCの広いプロセスウィンドウがあります。参考までに、ポリフェニレンサルファイド(PPS)の処理温度は330〜350°Cの範囲ですが、ポリエーテルケトンケトン(PEKK)とPEEKの処理温度はそれぞれ380°Cと400°Cです。
Toray AdvancedCompositesの最高技術責任者であるScottUngerは、次のように述べています。 Toray Advanced Compositesは、Victrex(Lancashire、UK)と共同で、LMPAEKを使用した一方向テープであるCetexTC1225を製造しました。
「TC1225の開発の目的は、PPSに使用される温度に近い温度で簡単に処理でき、エンドユーザーにとって有利なコストポジションを持ち、PEEKの機械的および流体抵抗特性を備えた製品を作成することでした」とUnger氏は言います。 「TC1225LMPAEKを使用することで、これらすべての目標を達成できたと感じています。」
Cetex TC1225は現在、National Center for Advanced Materials Performance(NCAMP、ウィチタ、カンザス州、米国)による認定を受けています。さらに、東レは、素材の作業には2つの主要なエアフレーマーベースの資格と、エアタクシーや都市のエアモビリティなどの新興市場に基づくいくつかの資格プログラムがあると述べています。
LM PAEKを使用したテープは、レイダウン速度が向上していると報告されています。 VictrexのAerospaceSBUのディレクターであるTimHerrは、「現場AFPとオートクレーブ外統合AFPの両方で達成できるレイダウン率は前例のないものです」と述べています。彼は、オーブンで統合されたパネルで毎分60メートルを達成できることを示しています。伝えられるところによると、現場での統合により、毎分20メートルが可能です。
品質に関して、Ungerは、低融点PAEKは、繊維配置後のオーブン統合を経た繊維配置ラミネートと同じように、その場での繊維配置を使用して同じラミネート品質を得ることができると主張しています。
複合ボンディング
TPCの溶接性は、航空機の開発に使用される材料の大きな利点です。融着/溶接は、熱硬化性複合部品の接合に使用される方法である、機械的固定および接着剤の使用に代わる方法を提供します。
ソルベイの製品開発ディレクターであるスティーブンハインツは、次のように述べています。「接合と溶接は、組み立ての将来において主要な役割を果たし、コストを削減し、航空構造の信頼性を向上させる可能性があります。 GKN Fokkerのような企業が、溶接のデモンストレーションを主導しています。」
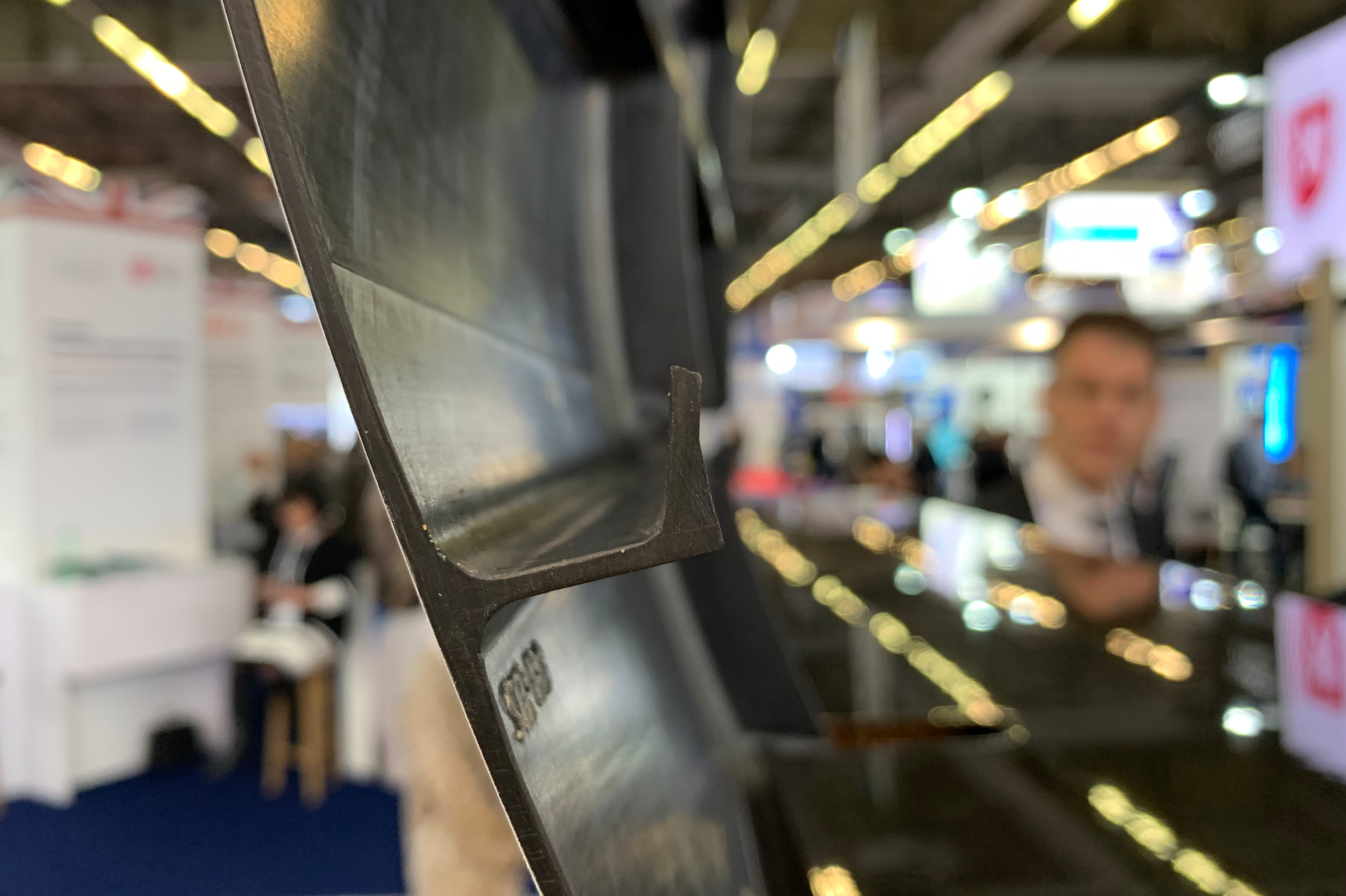
GKN Fokker(Hoogeveen、オランダ)は、1990年代に熱可塑性プラスチックの抵抗溶接の実験を開始し、しばらくの間TPC溶接の開発に取り組んできました。同社は、熱可塑性溶接プロセスを使用して、最先端の内部リブとスキンを接合しています。 JEC World 2019で、同社はソルベイのAPC(PEKK-FC)UDテープを使用して製造されたエリアルールの熱可塑性複合胴体パネルを展示しました。このパネルは、GKNFokkerとGulfstreamAerospace(米国ジョージア州サバンナ)の共同研究開発プロジェクトの結果です。伝えられるところによると、この部品は、単純な「突合せ接合」オルソグリッド補強と完全に溶接されたフレームにより、最も低コストの複合パネルです。
「熱可塑性プラスチックを使用すると、グリッドを皮膚に「突き合わせ」ることでオルソグリッドを大幅に簡素化できます」と、GKNFokkerの熱可塑性複合材料技術開発責任者であるArntOffringa氏は説明します。 「グリッドは現在、スキンラミネートと一緒に統合されて、低コストで一体的に補強されたシェルを形成する、単純で平らなプリフォームで構成されています。フレームはグリッドに溶接されています。これらの溶接はせん断荷重がかかるため、すべてのボルトを省略できます。」
溶接された熱可塑性構造物はしばらくの間エアキャフトで使用されてきましたが、この技術は現在、一次構造物での使用に適しているようです。 Mike Favaloroは、航空宇宙製造業者とOEMがTPC、特にプロセス制御に自信を持っていると信じています。 「10年の展望で、私たちはそれがはるかに多く採用されるのを見始めるでしょう」と彼は言います。
溶接技術の詳細については、GingerGardinerの記事「熱可塑性複合材料の溶接」をご覧ください。
ツールレス化
熱可塑性プラスチックの使用を加速できる可能性のあるもう1つの革新は、工具を使わない複合材料の製造です。この概念は、その名前が示すように、従来の金型や工具の必要性を排除し、それらをロボット工学に置き換えます。
航空宇宙メーカーのGeneralAtomics Aeronautical Systems Inc.(GA-ASI、米国カリフォルニア州サンディエゴ)は、熱可塑性複合構造を製造するためのこのようなプロセスを開発しています。 Composite Automation LLC(ケープコーラル、フロリダ州、米国)は、Mikrosam(プリレプ、マケドニア)機器を使用して、GA-ASIと協力して自動化を開発しました。このプロセスでは、2台の6軸ロボットが連携して熱可塑性テープを配置します。 1台のロボットは、熱可塑性材料のその場での圧密を実行するためのレーザー加熱を提供する標準的な一方向テープ配置システムで構成されています。 2番目のロボットはサポートを提供し、自動テープ層(ATL)の反対側で動作して、ATLがテープを配置するための可動工具面を提供します。 (詳細については、「General Atomics Aeronauticalがツールレス熱可塑性プラスチック複合材料を開発するプロセス」を参照してください。)
リサイクル性
TPCのもう1つの利点は、リサイクル性です。熱可塑性ポリマーは再溶解および再成形できるため、いくつかの企業は材料を再利用する方法としてTPCに注目しています。
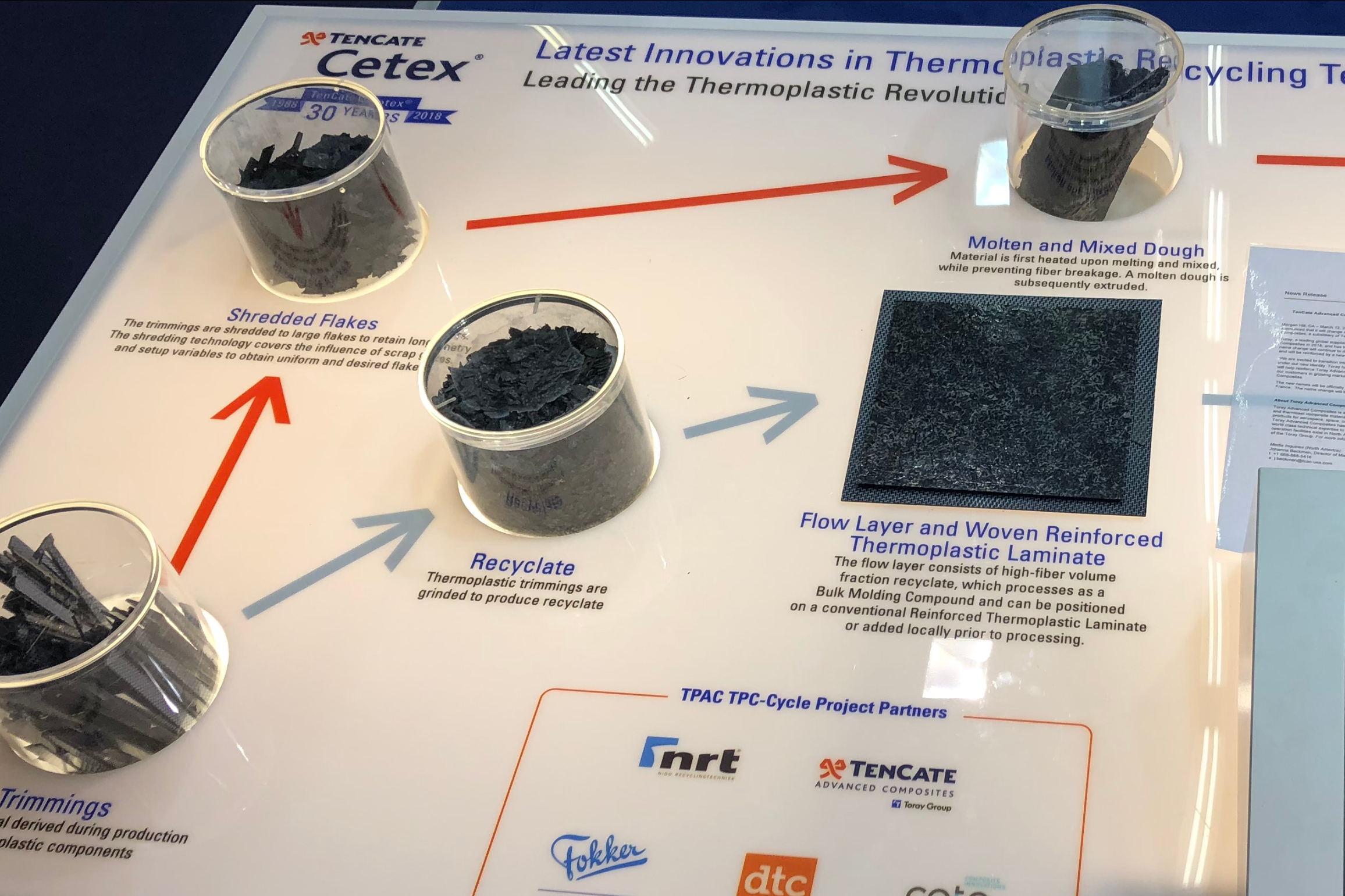
熱可塑性複合材料アプリケーションセンター(TPAC、エンスヘーデ、オランダ)と熱可塑性複合材料研究センター(TPRC、エンスヘーデ、オランダ)によって運営されているそのようなリサイクルイニシアチブの1つは、収集から細断までのTPC処理からの生産スクラップの再利用に焦点を当てています。アプリケーションまで再処理します。 TPC-Cycleプロジェクトは、元の熱可塑性材料の機械的特性を可能な限り保持する材料を製造しながら、ハイエンドで大量の市場向けに手頃な価格で環境に優しいリサイクルルートの開発に取り組んでいます。このプロジェクトは、短いサイクルタイムとネットシェイプの製造を誇り、複雑なシェイプの製造を可能にすると言われています。
コラボレーションには、GKN Fokker、Toray Advanced Composites、Cato Composite Innovations(オランダ、レーデン)、Dutch Thermoplastic Components(オランダ、アルメレ)、Nido RecyclingTechniek(ナイフェルダル)など、バリューチェーンのいくつかの産業パートナーが含まれます。 、オランダ)。
適切な仕事のための適切な資料
それで、これらの材料についての興奮の喧騒の中で、生じる問題は、TPCが到着したかどうかです。 Tier1およびTier2の航空宇宙サプライヤーは熱可塑性プラスチックに投資しています。中小規模のサプライヤーからの関心と投資が増えています。 IRG CosiMoのようなコンソーシアムは、大量生産を実現するためのプロセス技術を進歩させるために、航空宇宙市場と自動車市場の両方に注目しています。
「それはTrifectaです」とMead氏は言います。「OEMが投資し、機械の人々が投資し、適切な材料が開発されました。レシピのすべてのコンポーネントが一緒になっています。」
より広い範囲で、次世代航空機での材料の使用に関して、これはすべて何を意味しますか?結局のところ、将来の航空機のスポットをめぐって競合する多くの材料があり、革新は減速していません。熱硬化性複合材料は進化し続けています。アルミニウムとチタンは引き続き役割を果たします。
「エアフレーマーは熱可塑性プラスチックを使用して認定基準を策定するため、今では選択肢があります」とUnger氏は言います。 「そして、その選択は、問題のコンポーネントまたは構造の生産率とコスト要件を満たす特定のアプリケーションに適した材料を選択することに基づいています。今後の商用航空を見ると、エアフレーマーが行っているのは、適切な仕事に適切な材料を使用していることだと思います。材料が最小のコストで最も適切な構造を可能にし、プログラムの構築率の要件を満たしている場合、それは飛行機に乗り込むでしょう。」
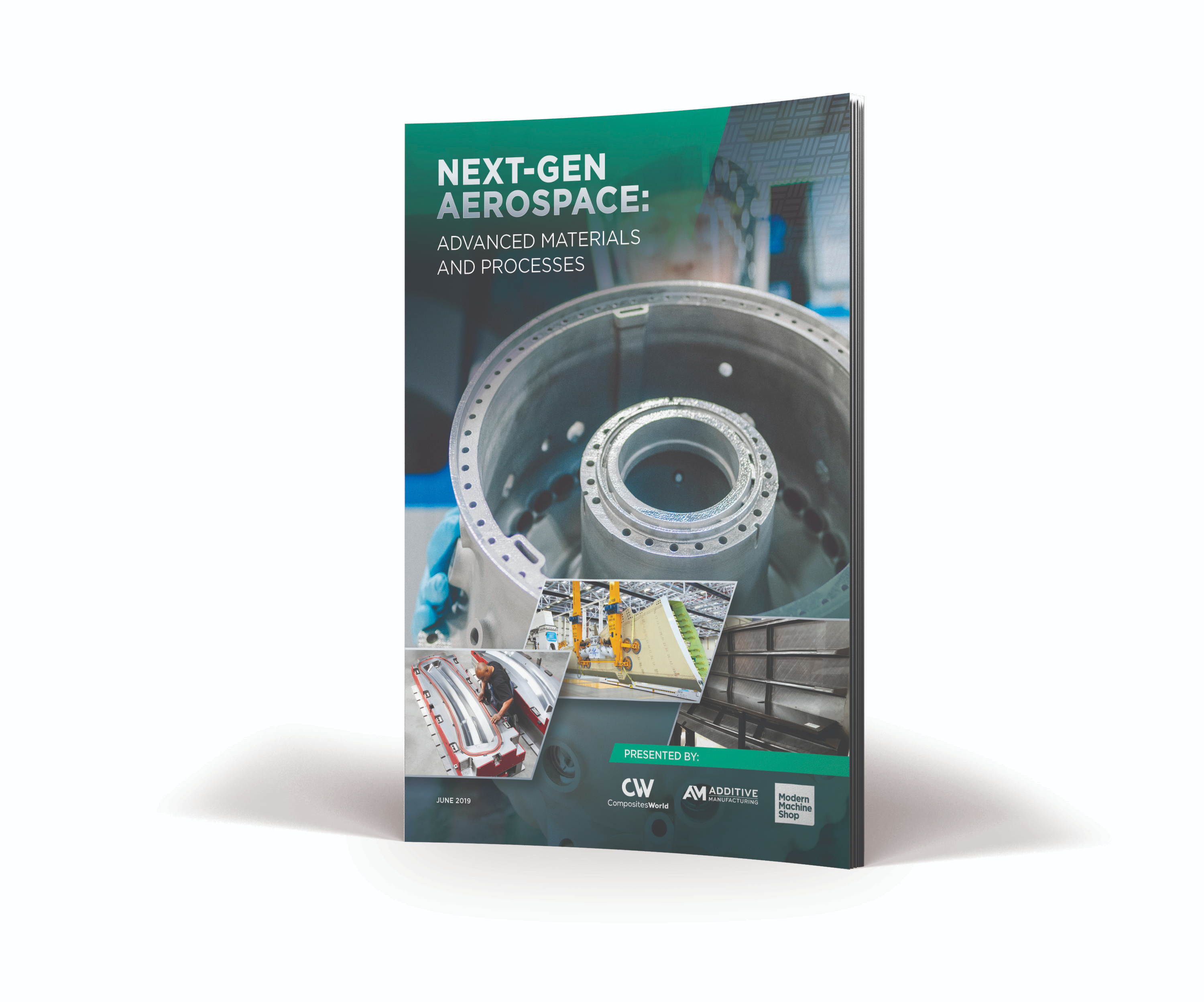
次世代の航空宇宙製造
商用航空業界は今後20年間で倍増すると予測されており、旅客機と貨物機の需要を満たすには、新しい技術と前例のない製造率が必要になります。
CompositesWorld、Modern Machine Shop のストーリーのコレクションで、次世代航空機を形作る材料とプロセスの詳細をご覧ください。 およびアディティブマニュファクチャリング 、無料で読んだりダウンロードしたりすることができます 。ここで入手してください。
樹脂
- コベストロは熱可塑性複合材料への投資を強化
- Oribi Compositesの熱可塑性複合材料:CWトレンド、エピソード4
- 熱可塑性複合材料の熱成形のトラブルシューティング
- 熱可塑性複合材料:構造用バンパーブラケット
- Toray Advanced Compositesは、熱可塑性複合材料の機能を拡張します
- Teledyne CML Compositesは、熱可塑性プラスチック加工機能に投資しています
- ACMAが熱可塑性複合材料会議2020プログラムをリリース
- 自動車用複合材料の最初の熱可塑性ドア
- 熱可塑性複合材料:風光明媚なビュー
- CAMX 2018プレビュー:TenCate Advanced Composites
- 熱可塑性複合材料の溶接