あなたの機械から学ぶ:もしいくつかの機械部品が決して故障しないとしたら?
機械部品が良すぎると思ったことはありますか?これが当てはまる可能性は十分にあります。この新しいビジネスモデルを活用し、現場の機械から学び、大幅な節約を実現します。
データ主導の意思決定を聞いたことがあると思います。 AIに基づく機械学習、ニューラルネットワーク、自己学習マシンなどは、競争に追いつきたい企業にとっては避けられません。しかし、あなたの考えを聞いています。機械学習はトリッキーであり、多大な投資がなければ私の自動化プラットフォームではサポートされません。それに加えて、一部の機械や設備は、とにかくそのようなアプローチを実際に利用することができません。
マシンから学ぶはどうですか 新しい収入源を生み出すには?
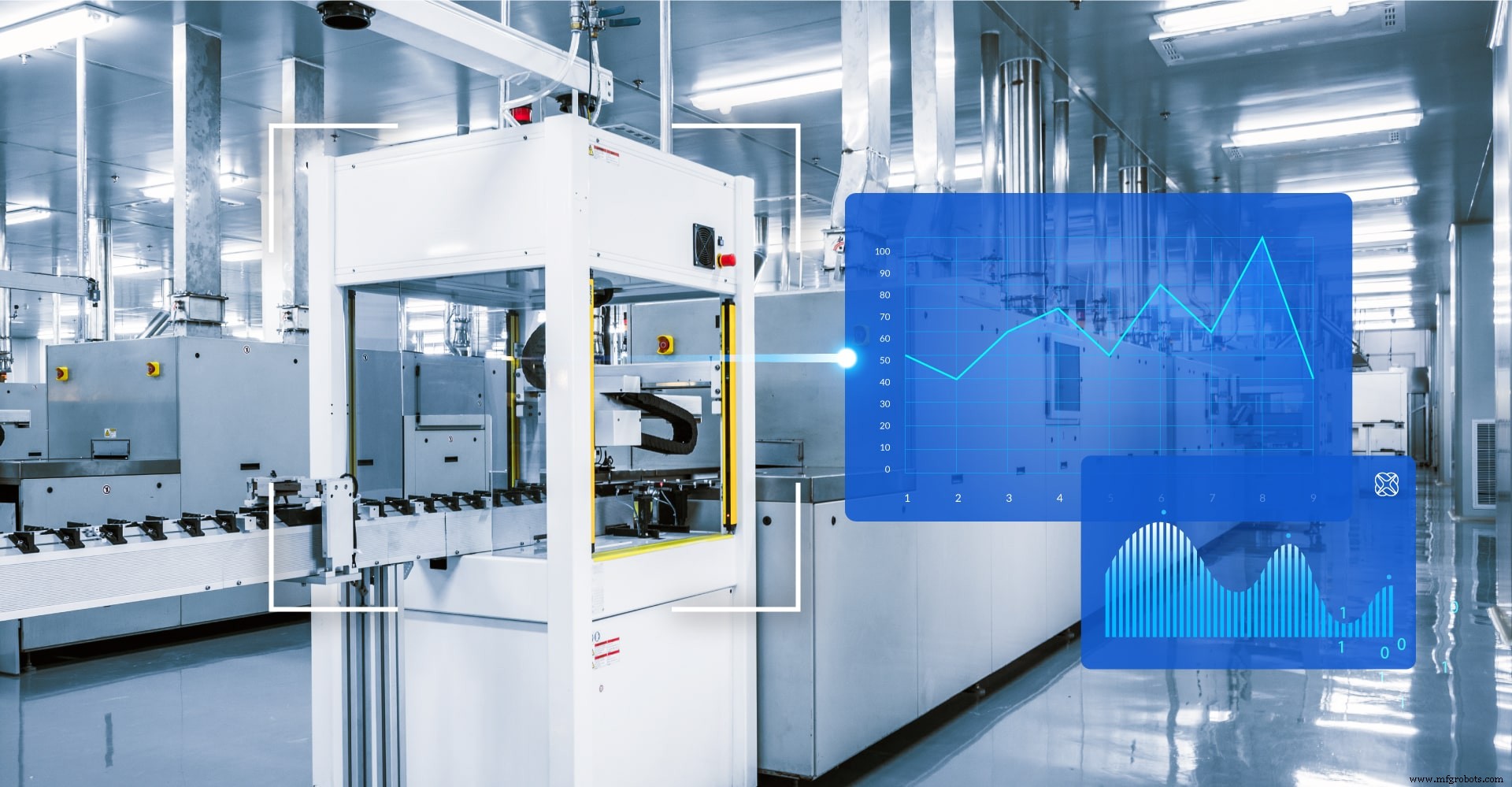
機械からの学習と機械学習
前述のように、AIとニューラルネットワークに基づく自己最適化アルゴリズムは、すべてのマシンビルダーにまだ適しているわけではありません。小規模な機械製造業者にとっては現実ではなく、多くの場合、せいぜい将来の計画です。ほとんどの機械製造業者(および顧客)にとって、焦点は、高いOEEを備えたスムーズで高速な機械の作成にあります。さらに、最適化された機器やマシンでPLCソフトウェアに触れることは、ほとんどの場合、「実行中のシステムに触れない」というモットーであるため、ほとんどの場合、失敗と見なされます。 。
ただし、すべてのマシンビルダーにとって現実的なステップは、マシンから学ぶことです。新しいマシンは新しい車のようなもので、最初は故障していて、最適化する必要があります。現場の機械から学ぶことで、最終的に部品の故障を防ぎ、他の興味深い洞察を発見することができます。ほとんどの機械製造業者は非常に効果的な品質保証システムを備えており、根本原因分析に基づいて、機器の故障と弱点を見つけて修正します。
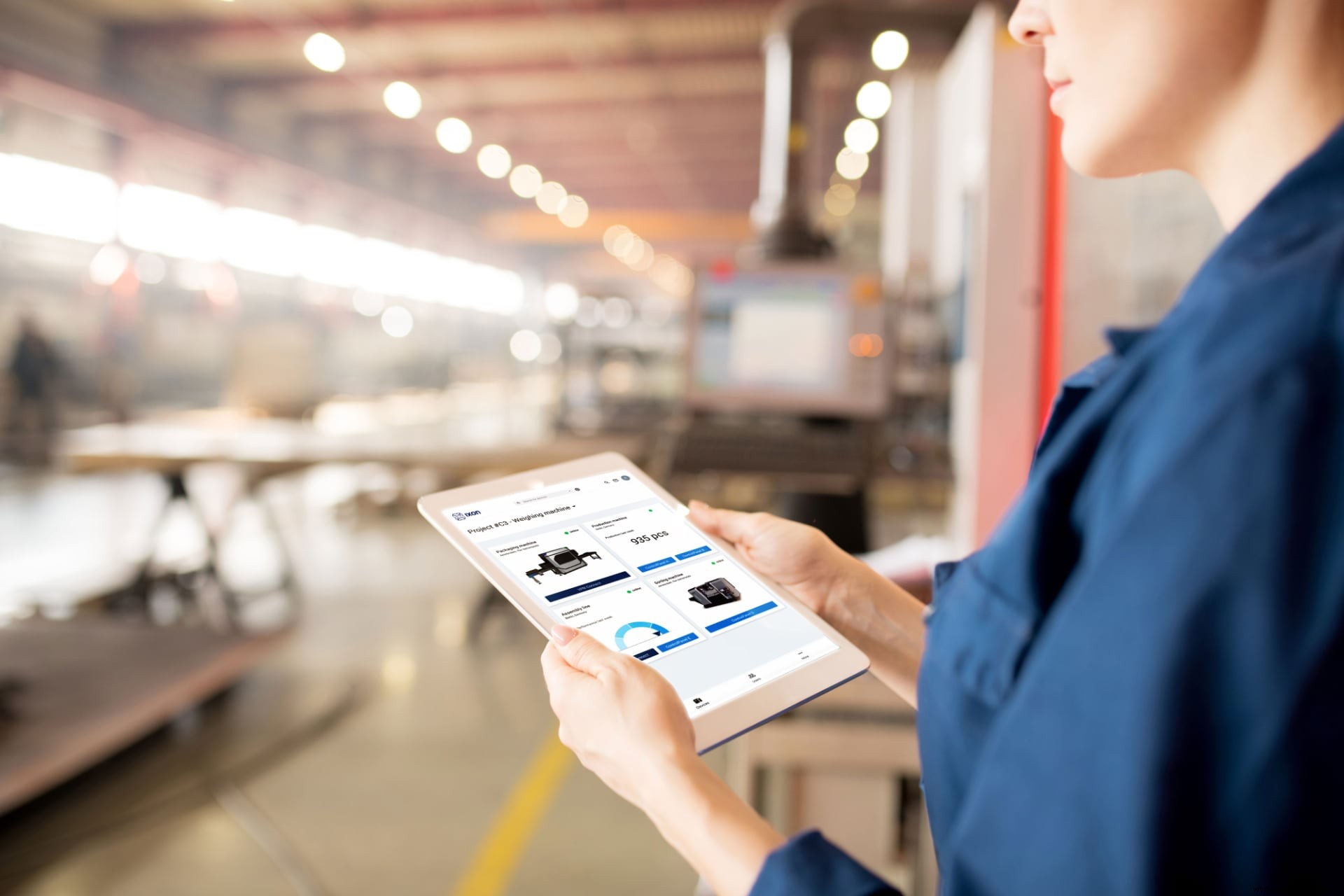
既存のマシンから学ぶことで何がもたらされるか
機械製造業者は、故障と是正措置に基づいて、寿命を通じて機械の品質を向上させるためのシステムを導入しています。これらは研究開発部門にも渡されるため、将来の機器での同様の障害を回避できます。しかし、マシンのデータを収集して分析し、複数のマシン間でベンチマークを行い、一部の部品が故障しないことを発見した場合はどうでしょうか。 または、予想される設計基準を大幅に下回っていますか?
現場での故障を回避しようとするため、設計基準と安全マージンが高すぎることがよくあります。ただし、「うまく機能する場合は修正しないでください」というモットーに忠実に、マシンデータを調べずにこのフィードバックを受け取ることはありません。
この洞察により、「良すぎる」機械部品をダウングレードして、再設計の設計基準または安全マージンを低くすることができます。これは大幅な節約につながる可能性があります 品質低下のリスクを冒すことなく。適応せず、競合他社が適応した場合はどうなりますか?間違いなく、すべての機械メーカーにとって検討する価値のあるビジネスモデルです。
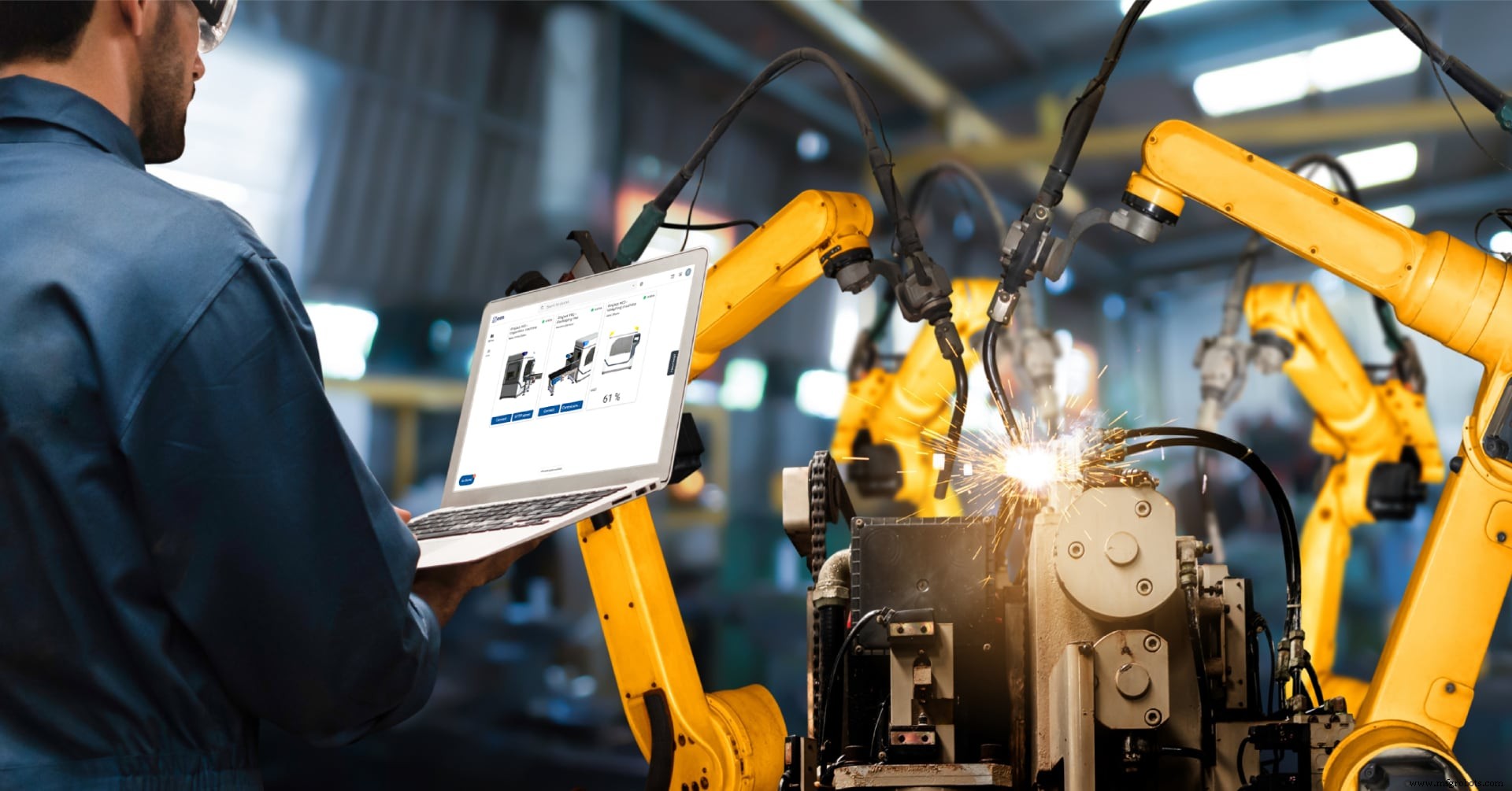
ユースケース:コンベヤーベルトの再設計
コンベヤーベルトを設計するとき、負荷や摩擦などに基づいて正しく動作するには、4 Nm @ 200 RPMを提供できるドライブパッケージが必要であると計算しました。安全マージンを20%に設定し、サイズを決定するためのコンポーネントを設計します。 Nm @ 200RPM。これらが実行されているので、特定のコンポーネントやプロセスから長期間にわたってデータの収集を開始できます。
世界中のすべてのマシンを調べ、PLCを監視し、クラウドに収集されたデータを使用して高度な分析を行います。負荷が実際にはすべてのマシンで3.8Nm RMSであり、4Nmを超えることはないことがわかったと想像してください。次に、それに応じてドライブパッケージの要件を下げ、コストを節約し、得られた知識を使用して安全マージンを再検討することができます。 あなたのコンベア設計のために。
特定の部品を節約できるかどうかを発見する準備はできていますか?
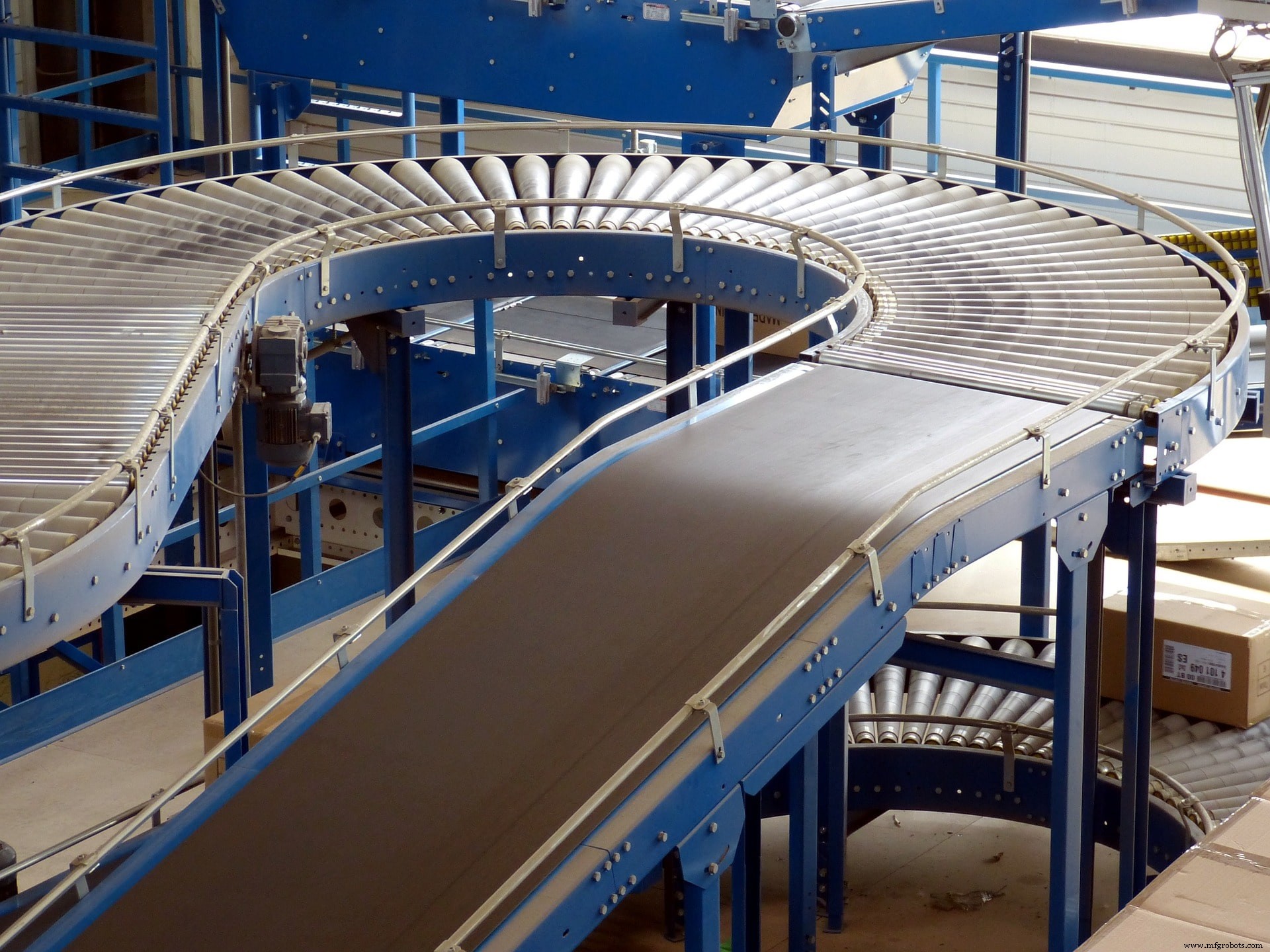
独自の「機械学習」戦略を構築する方法
非常に限られた投資と迅速なROIで、実用的かつ効果的な方法で現場の機械の履歴データから学び、この新しいビジネスチャンスに基づいて独自の戦略を構築します。次のリストからインスピレーションを得ることができます:
1)開始点-現在の機器のパフォーマンス-必要なデータ
最初のフェーズは、マシンパークからの現在のパーツプラクティスを分析することです。定期的に交換する部品とそうでない部品を特定します。与えられた値と問題の部品の状態との間に明確な統計的関係があるデータがキャプチャされているかどうかを確認します。
標準のPLC変数と部品の間に明確な相関関係があるデータもあれば、追加の変数を定義して収集する必要があるデータや、追加のセンサーを使用する必要があるデータもあります。エッジゲートウェイを介して、PLCデータを現場のマシンからクラウドに一括送信できます。
2)プロトタイピング-テスト
次のステップは、安全マージンの最小値と最大値を見つけることです。機械部品の性能を分析し、どの部品を改善する必要があり、どの部品をダウングレードできるかを判断します。
仮説を強化または反論するために、問題の部品に対して社内テストを実行します。これらの洞察を次のマシンの設計に使用してください。
3)ビジネスモデルの展開
安全マージンを下げる方法を定義し、これを次の再設計で実装して大幅な節約を実現します。

「良すぎる」機械部品のコストを節約
機械設計のコストを節約しませんか?現場の機械から学び、安全マージンが高すぎる部品を再設計することで、より多くの利益と競争上の優位性を得ることができます。 。
マシンから学習を開始する方法についてアドバイスが必要な場合は、義務を負うことなく、業界の専門家に相談してください。
[[無料の専門家による相談]]
モノのインターネットテクノロジー