オートクレーブ外のVBOリアスパー、熱可塑性リブがWing ofTomorrowをターゲット
エアバス(フランス、トゥールーズ)は、同社のWing of Tomorrow(WOT)プログラム用の脱オートクレーブ(OOA)構造の開発について、エアロコンポジット製造業者と協力する幅広い取り組みの真っ只中にあります。これらの構造物は2021年にエアバスに納入され、デモンストレーターウィングに組み立てられ、次世代の単通路航空機での使用の可能性についてテストおよび評価されます。そのようなプログラムがいつ発表されるかは不明であり、多くの憶測が飛び交っていますが、エアバスまたはボーイング、あるいはその両方の場合でも、航空複合サプライチェーン全体が次世代の航空機製造の一部であると位置付けています。
CW は、Spirit AeroSystems(ウィチタ、カンザス州、米国)によって製造された下翼の皮膚、およびGKN Aerospace(Hoogeveen、オランダ)によって製造された熱可塑性リブについての記事ですでにこのWOT活動の一部について報告しています。 WOTの取り組みに参加しているのは、航空機メーカーであり航空構造プロバイダーであるDaher(パリ、フランス)で、このプログラム用にOOAリアスパーと5つの熱可塑性リブを開発、製造、提供しています。
「DaherはこのWOTプログラムに参加できることを誇りに思います。この開発は、熱可塑性技術と熱硬化性統合機能構造の世界的リーダーの1つであり、航空機メーカーの強力なパートナーであり、複雑な部品のTier1であるというDaherの立場を裏付けています」とDaherの研究開発担当副社長であるDominiqueBaillyは述べています。
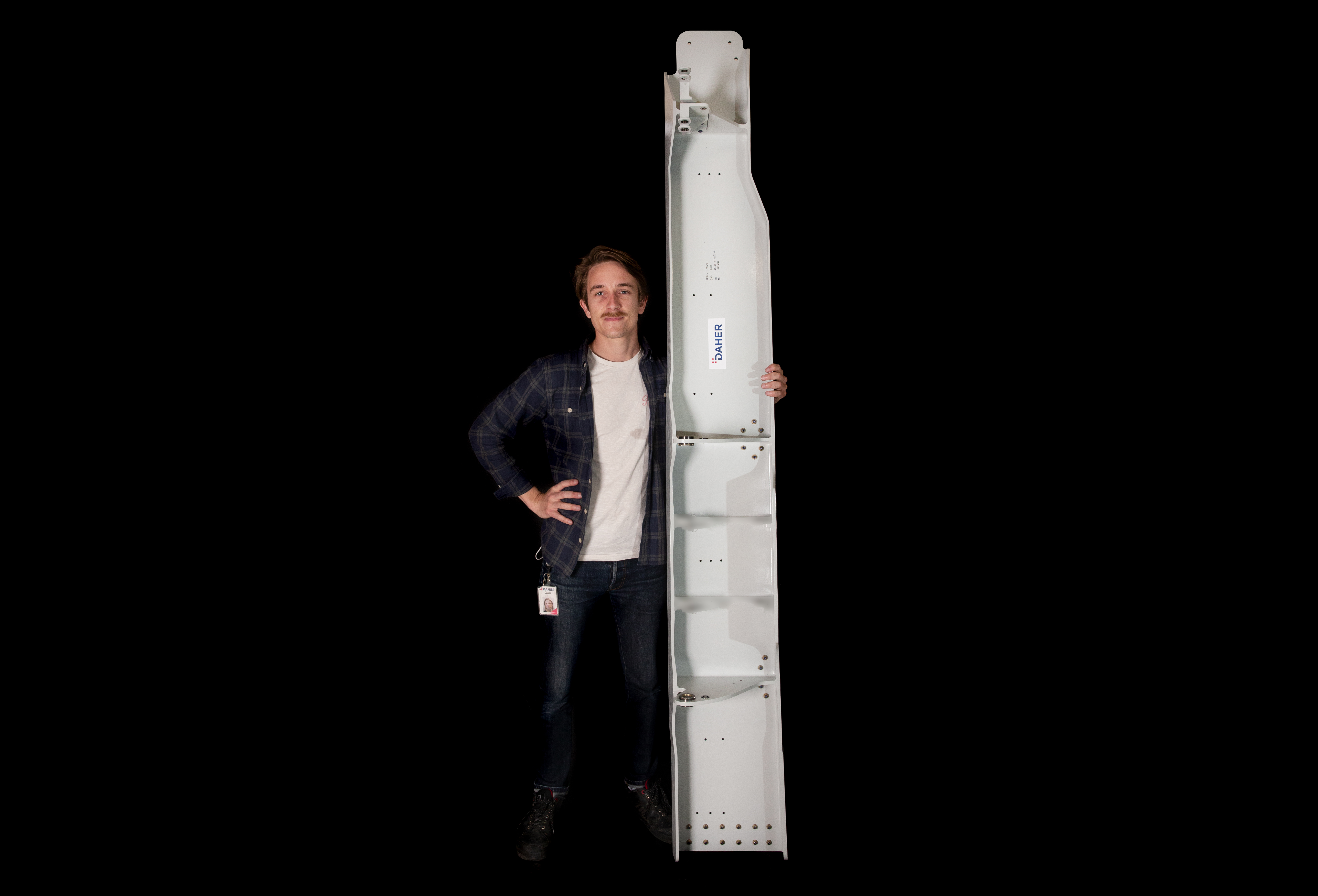
高性能スパー
WOTデモンストレーターは、他の民間航空機の翼と同様に、いくつかのスパー構造を持っています。 WOT用に開発されたリアスパーDaherはタンクの外側にあり、着陸装置のすぐ上にある胴体に隣接する2つのスパーの2番目に近いものです。長さ2メートル、厚さ10ミリメートルを超え、強度と剛性の重要な要件を満たす必要があります。「フィーチャに数トンを適用し、スパン方向のせん断と牽引に数十トンを適用します」と、バイリーは胴体と着陸装置システムへ。
さらに、スパーに取り組んだDaherのチーフエンジニアであるAlexandreCondéは、エアバスは、航空機の重量を減らし、60〜100隻の航空機の生産率に費用対効果の高い方法で対応できる高度に自動化された製造プロセスの開発を探していました。月額。 Daherは、ベースラインの複合桁設計に元々あった15個の金属部品と留め具を置き換えることができる設計を提案しました。 「アイデアは、費用効果が高く、重量を節約するためにほとんどの機能を統合することでした」とコンデは言います。
結果として生じたスパー構造は、ダッソー(パリ、フランス)ビジネスジェット用に2018年にDaherによって開発されたOOAバキュームバッグオンリー(VBO)サーモセットスパーの副産物です。バイリー氏によると、ダッソーのスパーは、ヘクセル(米国コネチカット州スタンフォード)のM56エポキシ樹脂ベースのプリプレグ、硬化したOOAVBOを使用して製造されたとのことです。その後、DaherがAirbus WOTプログラムに関与するようになると、同社はDassaultスパーの設計、プロセス、および正当化を適応させ、新しいAirbus WOT構造に適用することを決定し、HexcelM56350°F硬化OOAエポキシを選択しました。 HexcelAS4カーボンファイバーファブリックとIM7UDカーボンファイバー。
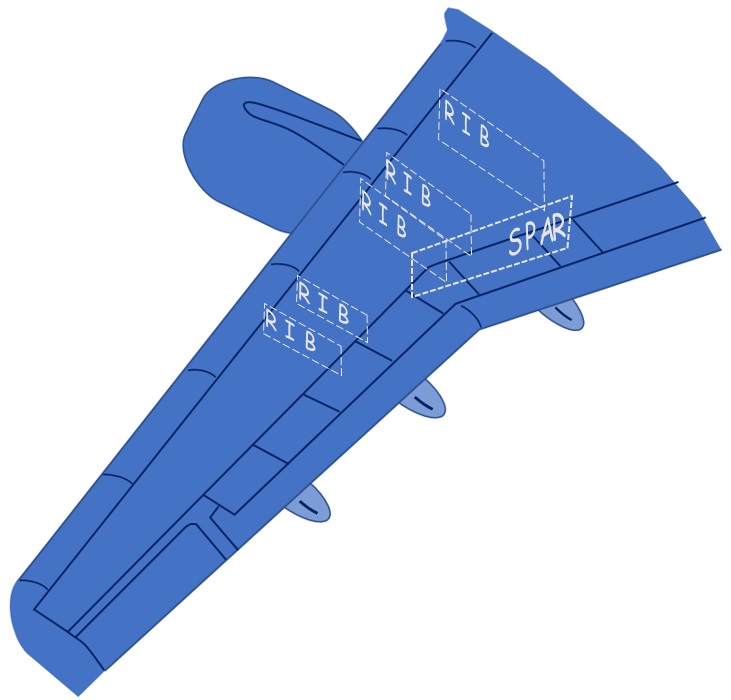
スパーの製造に使用される製造プロセスは、Coriolis Composites(Queven、フランス)システムを使用した自動ファイバー配置(AFP)であり、オス型に材料を塗布します。硬化はオーブン内の真空バッグの下で行われます。コンデによると、得られた部品の気孔率は0.1%です。
コンデは、プリプレグが過去30年間で航空宇宙製造の定番となったのと同じ理由で、液体樹脂成形よりもプリプレグが選択されたと述べています。と質量。 「この新世代のOOA樹脂を真空のみで使用すると、硬化後の複合材料の厚さの繊維含有量に完全な堅牢性が得られます」とコンデ氏は言います。 「また、樹脂を繊維の外側に押し出さないため、部品の重量は非常に安定しています。」
Daherは、2020年後半に、最初のWOTデモンストレーターに統合するために、WOTコンポーネント(英国のブリストルにあるエアバスに1つのスパー)を提供した最初のパートナーであると述べています。同社はさらに2つを提供する過程にあります。このデモンストレーションフェーズに加えて、Daherはスパー製造の工業化についても考えており、次世代シングルアイルのフルレート生産のための運用、設備、設備、および人員の要件を推定およびシミュレートする製造システム設計(MSD)分析に取り組んでいます。航空機。
複数のリブ、複数のサイズ
リブを開発するためのDaherでの取り組み WOTプログラムは、より複雑で要求が厳しいものになっています。同社は、翼の内部にさまざまなサイズと寸法の5つのリブを設計しました。他のリブは、GKNAerospaceによって設計された熱可塑性複合リブを含むアルミニウムと複合設計の組み合わせです。
ダッソーとの以前のプロジェクトで、Daherは熱可塑性複合材料から比較的小さなリブを設計および製造する能力を実証しました、とBaillyは説明します。 WOTにより、同社はより大きな(長さ約2メートル)、より高負荷のリブの開発に向けてスキルを拡張する機会を得ました。
さらに、WOTの目標ごとに、Daherは2023年末までに6の技術準備レベル(TRL)を目標としています。 2つのプログラム[WOTとDassaultAviation]で、翼のリブ部分全体をカバーできることを実証します。これがアイデアです」とベイリー氏は言います。
「このプログラムを利用して、部品を製造するさまざまな方法を調べ、機械的動作を比較し、製造への影響も調べました。並行して、スプリングバックやスタンピング効果などのコンポーネントの動作を予測するためのシミュレーションに取り組んでいます。目的は、開発中の試行を削減することであり、したがって、非反復コストを削減することです」とコンデは言います。
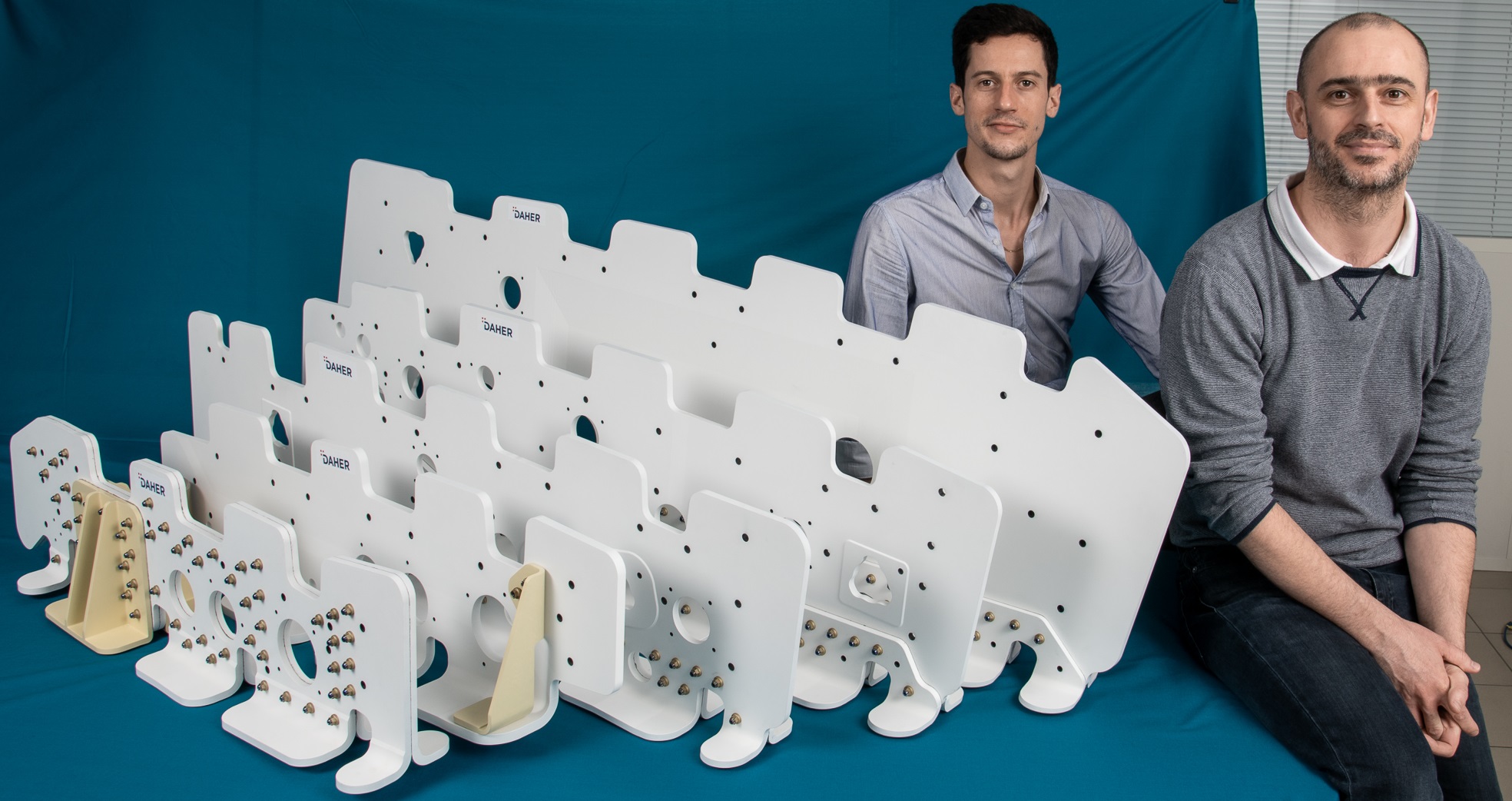
スパーと同様に、開発はクーポン、要素、詳細レベルで始まり、最終的なフルサイズの部品が製造される前にサブスケール部品が製造されました。コンデは、肋骨の特徴についてDaherが開発した特定のテストを含め、各レベルでテストを実施しました。
Daherは、5つのリブすべてに、最終的に、Victrex(Cleveleys、Lancashire、UK)が製造した樹脂を使用して、Toray Advanced Composites(Morgan Hill、CA、US)が提供する一方向(UD)炭素繊維/低溶融ポリアリールエーテルケトン(PAEK)テープを使用することを決定しました。 )。リブを製造するために、AFPを使用してフラットブランクを作成し、続いてオーブンで固めます。場合によっては、スタンプを形成する前に材料を事前に固めます。必要に応じて、追加のフランジまたはその他のコンポーネントがスタンプ成形部品に機械的に固定されます。
各リブは、翼に沿った位置、サイズ仕様、および負荷要件(1トンから50トン)に従って設計されているため、それぞれがいくつかの点で固有です。最大のリブは、長さ2メートルx幅1メートルです。とにかく、それぞれは平らなウェブから始まります。これは「L」字型にスタンプ成形され、翼の外板に接続するパーツの下部に沿ってフランジを作成します。安定性を高めるために、リブのいくつかは、機械的に背中合わせに固定された2つの「L」字型コンポーネントで構成され、双方向フランジを備えた「T」字型を形成しました。
特殊な機能には、リブに取り付けられたフラップトラックに接続するためのブラケット(熱硬化性複合材料から製造)、および部品の重量を減らすための一連の穴またはプライドロップが特定のリブに含まれていました。
「設計を行っている間、複雑さとコストを管理する必要がありました」とBailly氏は言います。 「それは常に私たちの頭の中にあり、シンプルでありながら費用対効果の高いことをすることでした。」コンデ氏は、生産率の観点からもシンプルさが重要であると述べています。 「複雑すぎると、顧客が望む非常に高いレートで、顧客の観点から競争力がなくなります。」
設計に複雑さをもたらした1つの課題は、各リブの相対的な厚さでした。最大のリブの場合、最大12ミリメートルです。厚い生地は、スタンプを形成するときにしわが寄ったり、正しく形成されなかったりする傾向があり、厚い部分は、完成した形状に機械加工するのが難しい場合があります。
機械加工では、Daherは部品の厚さの問題を軽減し、温度を管理するために、部品のニーズに応じてウォータージェット切断と機械加工を組み合わせて使用しました。さらに、厚さ12 mmのリブで、チームはコンポーネントの中央にプライドロップウィンドウを設計して、パーツ全体の重量を減らしました。 Condéは、これらの潜在的な問題を解決することに加えて、プライドロップウィンドウによってDaherが「部品のさまざまな種類の製造機能を試して、部品の動作についての理解を深める」こともできたと述べています。
スタンプ成形プロセスは、さらに大きな課題であることが証明されました。 「しわのリスクを軽減するために、新しいスタンピングの方法を想像する必要がありました」とバイリーは言います。 Daherは最終的に、問題を解決するための独自の方法を開発しました。
次のステップ
Daherは、WOTを超えて、熱可塑性リブを製造するための代替製造方法を評価している一方で、将来的には高速製造のための完全な製造ラインを開発する計画を立てています。
たとえば、WOTのデモンストレーターはファスナーを使用していますが、Baillyは、2019年に熱可塑性複合材料と誘導溶接のスペシャリストであるKVE Composites(オランダ、ハーグ)を買収したことにより、Daherは将来的に溶接コンポーネントの機能を備えていると述べています。 「私たちは、UDの厚い部品の溶接でより高いTRLレベルに到達するために、別の別のプロジェクトに取り組んでいます[次世代の単通路航空機で使用するため]」と彼は言います。
Daherは、将来的に熱可塑性リブを生産するための完全な生産ラインの開発にも取り組んでいます。 「私たちは本当にコンセプトを改善し、すべてのタスクに必要なマシンの数を減らし、プロセスコストを削減しています」とBailly氏は言い、大量の航空機生産目標を達成することを目標としています。
樹脂