一般的な射出成形ツールの表面処理と適切なものの選択方法
射出成形プロセスは非常に複雑です。プラスチック製品を製造するために、いくつかの異なる部品が連携して機能します。しかし、目立つのは金型そのもので、溶融プラスチックを注入して、プラスチック製品の固定された望ましい形状を形成します。金型は明らかに射出成形の最も重要な機能部品の1つですが、最も高価な部品の1つでもあります。カビの損傷は重大な経済的義務を表しています。幸いなことに、これは回避できる義務です。どのように?適切なカビ処理による。ここでは、射出成形ツールの表面処理の概要を説明します。
射出成形金型の処理が重要な理由
おそらく、この質問に対する最も簡単な答えは、コストを節約することです。これは、金型のコストを考えると理にかなっています。 1つの金型には数十万ドルの費用がかかる可能性があり、それはそれを購入するための費用にすぎません。このコストは回避でき、回避する必要があります。射出成形ツールの表面処理は、これを実現する1つの方法です。
型はまったく弱くはなく、通常は焼入れ鋼でできています。ただし、溶融樹脂を高温高圧で射出するプロセスは、最終的には射出成形金型に負担をかけます。現在使用されている熱可塑性材料の多くは研磨性もあり、多くの射出サイクルの後に金型表面に摩耗と摩擦を引き起こします。継続使用後の腐食や疲労のリスクもあります。
最終的な結果は通常、成形工具の損傷ですが、腐食、摩擦、摩耗、および摩耗の影響を受ける金型によって生成される作業の品質は、通常、必要とされるよりも低くなります。金型の流れは、適切な金型処理なしでも影響を受ける可能性があります。これらすべてが顧客を追い払う可能性があり、金型を交換した後でも、顧客を取り戻すことは通常困難です。これは、射出成形業者が金型処理とさまざまな金型仕上げツールについて教育を受けなければならない理由をさらに強調しています。
プラスチック射出成形工具の表面処理の種類
はい、鋼は固いです。しかし、高温高圧の溶融樹脂に長時間さらされた後、射出成形金型を摩耗から保護するのは十分に難しいのでしょうか。いいえ、そうではありません。さまざまな表面処理により、非常に必要とされている追加の保護を提供できます。以下でそれらのいくつかを簡単に調べます。
メッキ
メッキは、カビの摩耗、裂け目、摩耗に対する最も一般的な解決策の1つです。めっきには、電解と無電解の2つの主要な形態があります。 2つの違いは、電流が存在するかどうかに起因します。電解めっきには電流が必要ですが、無電解めっきには電流は必要ありません。
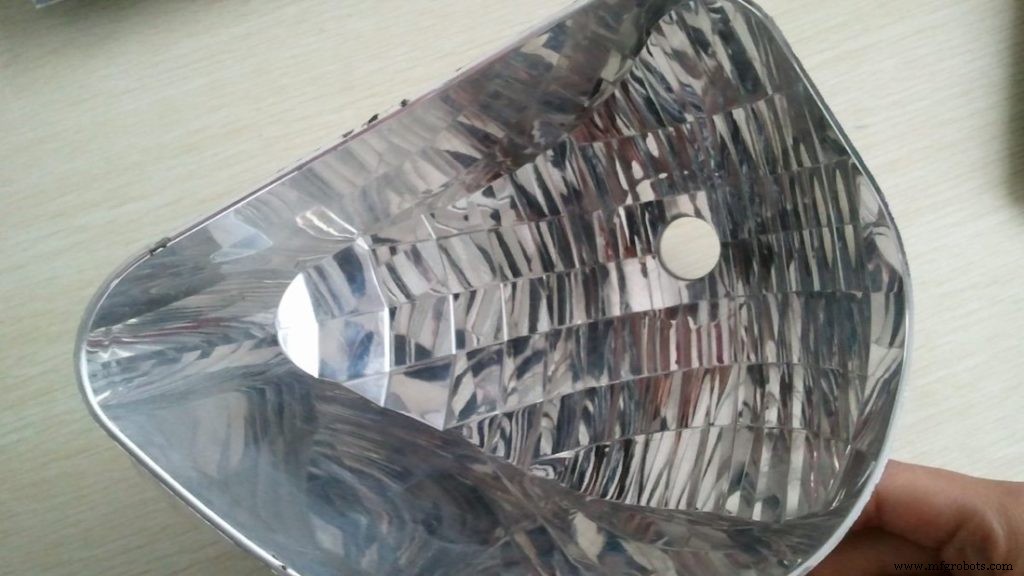
クロムメッキと無電解ニッケルメッキは、金型のメッキの最も一般的な2つの形式です。クロムめっきでは、金型にクロムの薄層を電気めっきします。クロームメッキの製品はクロームです。ニッケルメッキとは異なり、クロムメッキでは、金型キャビティに入るコンフォーマルアノードを使用する必要があります。これは、特に詳細な金型の場合、クロムメッキに時間がかかり、暗黙のうちにコストがかかる可能性があることを意味します。ここでのもう1つの欠点は、クロムメッキが長すぎると、特に詳細な金型で均一なメッキができなくなる可能性があることです。金型の表面の質感はクロムの方が硬く、錆びにくいです。クロムメッキは通常滑らかで非常に機能的です。
無電解ニッケルメッキは、すべての射出成形金型表面処理の中で最も用途の広いものの1つです。無電解めっきは、電流ではなく化学反応に依存しています。腐食、潤滑の懸念、摩耗、さらには化学的攻撃に対する保護を提供します。この形式のめっきは陽極を必要としません。これは、クロムめっきよりも均一なめっきを意味します。黒ニッケルは、最も識別可能な無電解ニッケルメッキの1つです。
クロムであろうとニッケルであろうと、メッキが保証するものの1つは耐久性です。メッキによる金型処理により、製品の品質を損なうことなく、金型がより多くの射出サイクルにわたって持続することが保証されます。
窒化
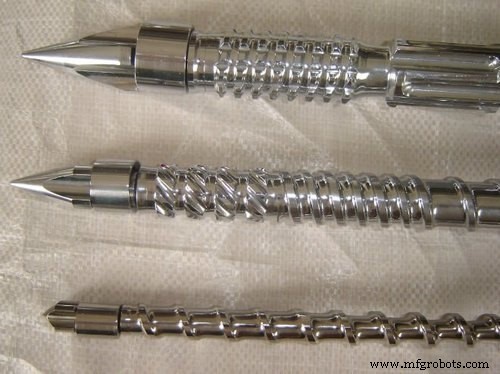
窒化は熱化学的拡散プロセスです。浸炭に加えて、この形式のカビ処理は最も一般的な熱処理方法です。このプロセスにより、金型表面の相構造を変化させることなく、低温で金型表面に窒素原子を拡散させることができます。相変化がないということは、金型の鋼の歪みが最小限であることを意味します。
窒化には、イオン窒化、パック窒化、塩浴窒化、ガス窒化などさまざまな形態があり、成形面の質感と性能を向上させることを目的としています。
このプロセスでは、金型部品は925〜985Fの活性窒素にさらされます。鋼の歪みを最小限に抑えるために、窒化プロセスには適切な温度制御が不可欠です。さらに、窒化処理を使用して処理される射出成形金型コンポーネントは、通常、最終加工の前に応力が緩和され、サイズの変化が無視できるようになります。
時間の経過とともに、窒化プロセスは開発され、従来のガス窒化技術から、コンピューターを使用して窒化パラメーターを制御するより制御された窒化に改善されてきました。
窒化はハードモールドケースの開発につながりますが、柔らかく保つ必要のある部品は窒化プロセスでマスクすることができます。ハードモールドケースは、摩耗や摩耗に強いようになります。
浸炭
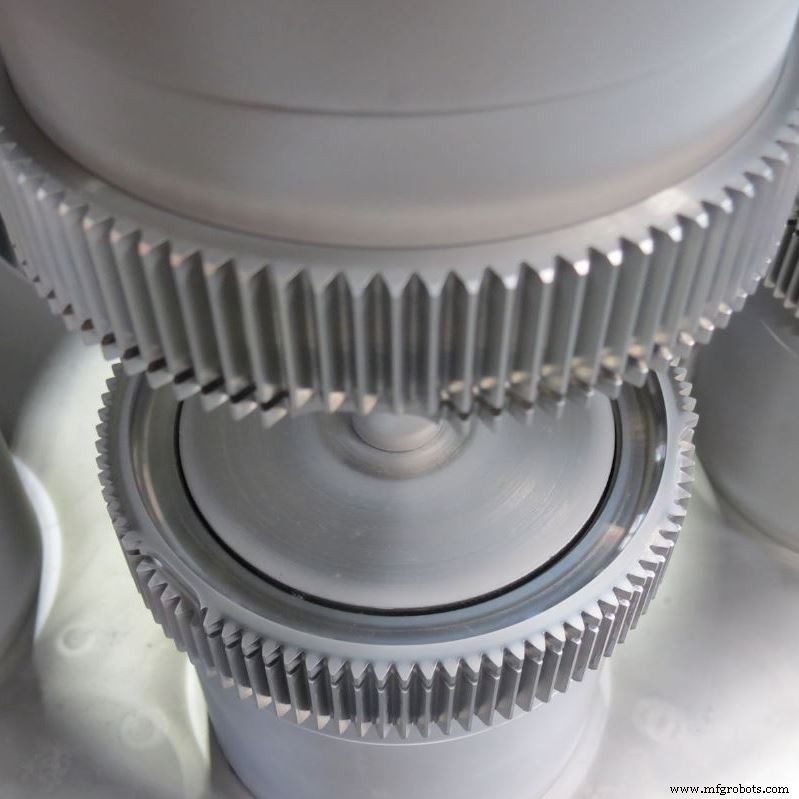
熱を必要とする別のカビ処理方法は浸炭です。このプロセスは窒化に似ています。主な違いは、窒化処理中の窒素原子ではなく、処理中の射出成形金型コンポーネントの表面への炭素原子の拡散です。
浸炭はしばしば耐摩耗性で丈夫なカビにつながります。このプロセスでは、ピット炉で射出成形金型コンポーネントを加熱します。次に、浸炭ガスを導入して金型表面に拡散させます。
窒化と同様に、ガス浸炭、真空浸炭、パルスプラズマ浸炭、高温浸炭など、さまざまな形態の浸炭プロセスがあります。
浸炭は、大型の歯車やベアリングなど、より重くて負荷の高い金型部品の窒化よりも優れた射出成形ツールの表面処理です。窒化とは異なり、浸炭には後熱処理が必要です。これは、で著しく高温の浸炭が発生するためです。
PVDコーティング
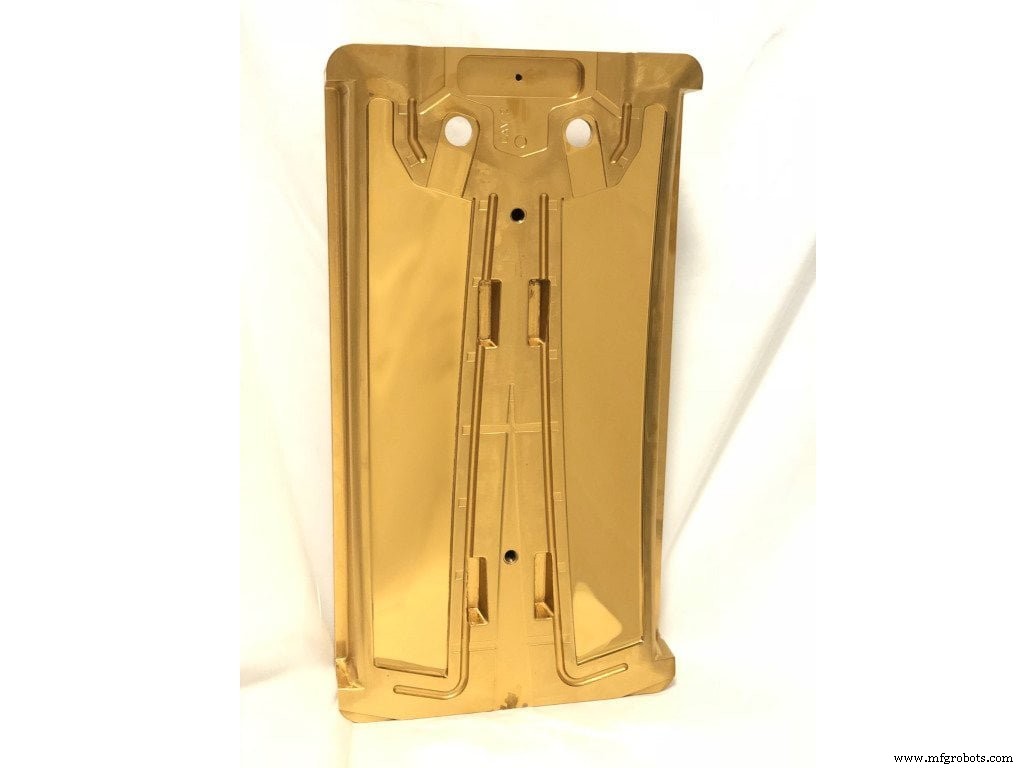
PVDは、PhysicalVaporDepositionの頭字語です。薄膜コーティングとしても知られるこのタイプのモールド処理は、ソースと呼ばれる固体材料を真空中で蒸発させ、モールドコンポーネントの表面に堆積させるプロセスです。ソースは通常、セラミックまたは金属のロッドです。
最も一般的なPVDコーティングプロセスは、蒸着とスパッタリングです。蒸発では、プロセスは陰極アークまたは電子ビーム源を利用します。一方、スパッタリングには、磁気増強源の使用が含まれます。
このプロセスの背後にある原理は、金型コンポーネントにエネルギーのある正に帯電したイオンが衝突することによる高密度の金型表面の形成です。原料はプラズマにスパッタされ、金型表面と強力な結合を形成し、薄い接着層を形成します。
爆撃中に酸素や窒素などの反応性ガスを真空チャンバーに導入することにより、複合コーティング組成物を作成することも可能です。
PVDコーティングは、金型の強度を向上させるのに役立ちます。形成された層も非常に薄いため、コートは金型コンポーネントの最終的な寸法にほとんど影響を与えません。 PVD射出成形ツールの表面処理は、今日の業界で最も受け入れられているものの1つです。ただし、その使用は、このプロセスに伴う非常に高い温度に耐えることができる材料にのみ使用されます。このプロセスは、隠れたパーツがたくさんある非常に詳細な金型にも理想的ではありません。
PVDコーティングは、全体的なパフォーマンスの向上と美観の向上のどちらに重点が置かれているかに基づいて、機能的または装飾的にすることができます。窒化チタン(TiN)は機能的なPVDコーティングの例であり、Zrベースのフィルムは装飾的なPVDコーティングの例です。
CVDコーティング
CVDはChemicalVaporDepositionの頭字語です。このコーティングの背後にある原理はPVDと似ていますが、主な違いは、化学反応を使用して、CVDコーティングで金型をコーティングする薄膜を生成することです。
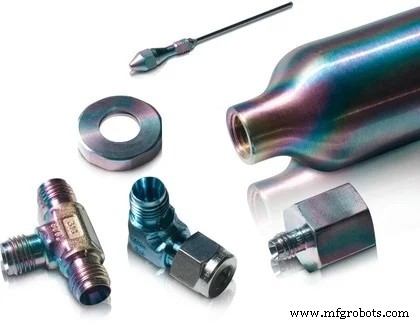
CVDコーティングプロセスは通常、CVDリアクターで実行されます。 PVDコーティングの問題の1つは、それが実行される高温です。さて、CVDコーティングはさらに高い温度(約1925F)で実行されます。ご想像のとおり、これにより、この金型処理は高温に耐えられるコンポーネントに限定されます。
このコーティングプロセスで形成される薄膜は、気相と反応器内の高温の金型表面との間の反応によるものです。
PVDと同様に、CVDコーティングは、耐摩耗性と耐摩耗性を備えた頑丈なモールドを保証します。形成されるフィルムも非常に薄く、通常はナノメートルの範囲であるため、金型の最終的な寸法が大幅に変更されることはありません。
CVDコーティングは、さまざまな金型部品、特に多くの滑りを伴う部品に役立ちます。ただし、このプロセスはガスに依存する性質があるため、一部の領域をマスキングすることは困難または不可能な場合もあります。
これらのプロセスの多くは、迅速なツーリング中に適切に考慮されることは注目に値します。そして、RapidDirectで最高のラピッドツーリングサービスを見つけることができます。
カビ処理に関する考慮事項
さまざまな金型仕上げ工具を適用する前に考慮すべきいくつかの要因があります。こちらがその一部です。
- 金型処理プロセスを受ける金型コンポーネントまたは部品のタイプを十分に検討する必要があります。金型仕上げ工具を選択するだけではいけません。むしろ、プロセスが異なれば金型表面への熱影響も異なるため、金型コンポーネントの耐熱性を考慮してください。また、最終的な寸法変更で余裕がある余裕が出てくるはずです。一部の金型コンポーネントは非常に薄いフィルムを必要としますが、他の金型コンポーネントは比較的厚いコーティングを施すことができます。
- カビ処理の価格は、考慮すべきもう1つの重要な要素です。最良のプロセスは通常より多くの費用がかかりますが、特に射出成形金型が散発的に使用される場合は特に、より安価なオプションを選択する方が経済的である場合があります。
- プロセスと金型の互換性も確認する必要があります。たとえば、一部のプロセスではマスキングが可能です。他の人はしません。したがって、一部の金型コンポーネントのマスキングが金型処理に不可欠である場合は、マスキングを可能にするプロセスを選択する必要があります。同じ原理がコーティングの均一性にも当てはまります。
RapidDirect射出成形サービス
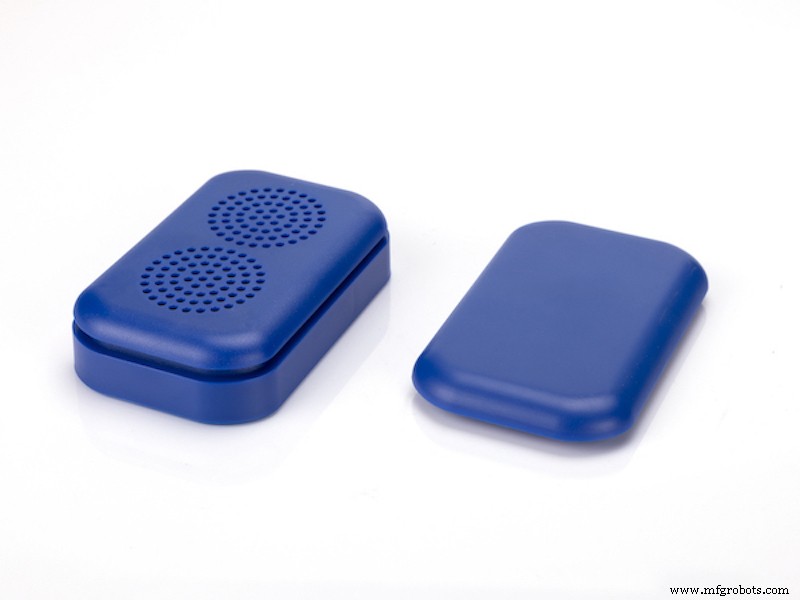
RapidDirectには、射出成形金型の設計と金型処理に関する豊富な経験があります。私たちの専門家チームが利用可能であり、射出成形金型のすべての問題を解決する準備ができています。もっとあります。最高品質の成形サービスを提供し、適切な表面処理を心配する必要がなく、金型部品の可能性と寿命を最大限に延ばします。
複合材料
- 適切なレベリングフィートを選択する方法
- 適切な引き出しスライドを選択する方法
- 3種類のフィットと適切なものの選び方
- 射出成形技術の意義
- コンパクターとは何ですか?適切なコンパクターを選択するにはどうすればよいですか?
- クレーンの購入:適切なクレーンの選び方
- 適切な CNC ターニング センターを選択してジョブを迅速かつ正確に完了する方法
- 適切なプラズマ カッターを選択して作業を正しく (かつ迅速に) 行う方法
- CNC に適したカッターとプログラミングの選択方法
- 一般的な射出成形用語の説明:マルチキャビティ、ファミリ、インサートなど
- CNC マシン ショップはどのように機能し、適切なマシンをどのように選択しますか?