11金属鋳造法
炉の火から宝物を引き出すための用語とプロセスを学ぶ
金属鋳造とは何ですか?
金属鋳造は、溶けた金属を空の形の空間に注ぐことによってオブジェクトを作成するプロセスです。次に、金属は冷却されて硬化し、この成形された型によって与えられた形になります。鋳造は、多くの場合、固体金属片から部品を機械加工する場合と比較して、部品を製造するためのより安価な方法です。選択できる多くの金属鋳造方法があります。どのタイプの鋳造が最も効率的かは、使用する金属、ランのサイズ、および鋳造の複雑さによって異なります。
生産を開始する前に、ファウンドリフロアからいくつかの用語と方法を知っておくと役に立ちます。
- キャスティングの用語にジャンプ
- 金属鋳造の種類にジャンプ
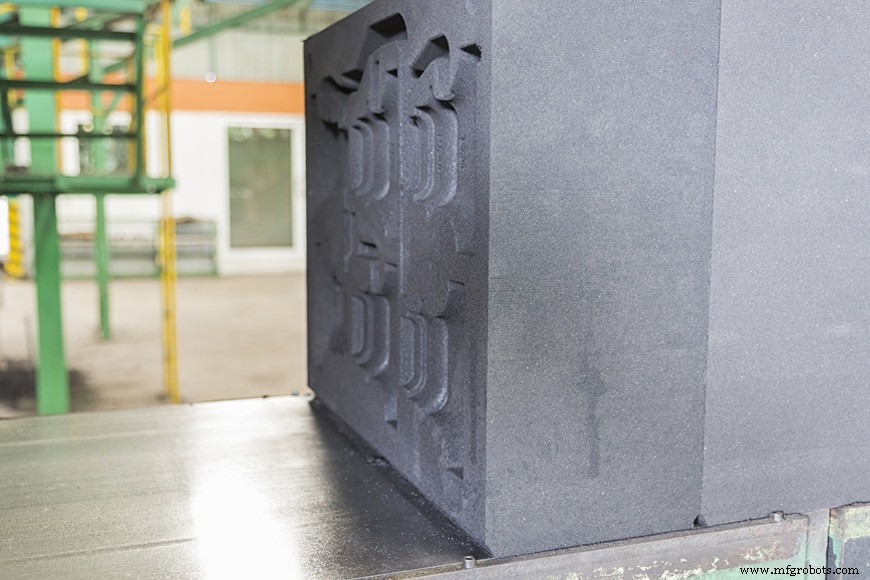
用語のキャスト
鋳造金型
カビ は、液体金属を受け取り、その空洞の形状で冷却されたオブジェクトを生成する材料の空洞です。型は単純にすることができます。金属のインゴットを作成するために使用されるフォームは、パンのようなもので、金属を単に中に注ぎ、放冷します。ほとんどの型はより複雑な形状用であり、パターンに基づいています。スプリットモールドに刻印されたパターン。パターンの半分は型の片側に刻印され、半分は反対側に刻印され、次に型が満たされる前に半分が一緒にクランプされます。型を2つに分割することにより、パターンを引き出してから充填することができます。これらの型は、水平分割で作成できます
コピーしてドラッグ
水平成形では、金型の上半分はコープと呼ばれます。 、下半分はドラッグと呼ばれます 。
スイングとラム
垂直成形では、金型の前半分はスイングと呼ばれます。 、後半はラムと呼ばれます 。
成形コア
金型に内部スペースまたは穴があると想定される場合は、コア よく作られます。これらのコアは内部空間のような形をしています。コアは通常、鋳造物を越えて伸び、コアプリントを介して所定の位置に保持されることにより、所定の位置に保持されます。 、2つのバンク間のブリッジのようにコアを中断します。コアの周りの空きスペースは金属で満たされ、コアは最終鋳造から削除され、かつてあった場所に穴が残ります。コアが非常に長い場合は、ビーズ状の物でサポートされている可能性があります それを支えるために。これらは通常、材料で溢れ、最終鋳造の一部となる空間に配置されるため、最終鋳造と同じ金属でできています。
寸法公差
鋳造方法を選択する際の重要な要素の1つは、寸法公差です。 。寸法公差は、最終製品のサイズで許容できる変動です。金属は冷却時に収縮し、鋳造の種類はその程度に影響します。製品が正確である必要がある場合、クライアントはニアネットキャスティングを生成するキャスティング方法を望むかもしれません 。これは、金型から振とうしたときに、製品が適切なサイズに非常に近いことを意味します。
表面仕上げ
もう1つの考慮事項は、表面仕上げです。 。鋳物の表面はどのくらい粒状、でこぼこ、または粗くなりますか?鋳鉄製の鍋に許容できるものは、結婚指輪には許容できません。非常に滑らかな金属表面は通常、機械加工で作成されますが、これは追加コストです。光沢のある滑らかな結果が望ましい場合は、より細かい仕上げの鋳造方法を選択すると、機械加工コストを削減できます。
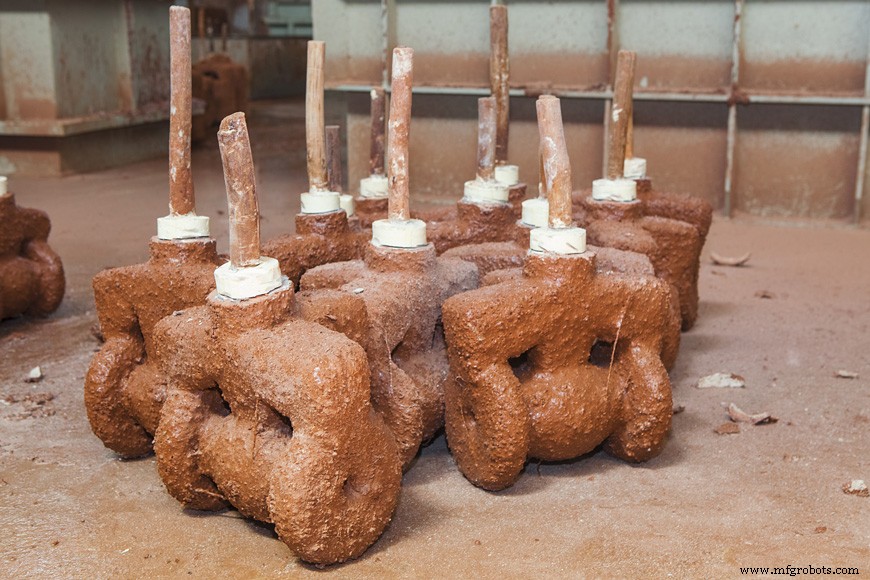
金属鋳造方法
金属鋳造には、再利用可能な金型を使用するプロセスと消耗品を使用するプロセスの2つの主要なカテゴリがあります。
- 再利用可能な金型:
-
- 恒久的な型
- 半永久的な型
- スラッシュキャスティング
- 遠心鋳造
- 圧力鋳造
- ダイカスト
-
- 消耗品:
-
- 砂型鋳造
- シェルモールド
- インベストメント鋳造(ロストワックス)
- フルモールドまたはフォーム
-
再利用可能な金型または恒久的な金型は多くのアイテムを作成しますが、消耗品の金型は鋳造プロセスによって破壊されます。素人の観点からは、再利用可能な金型は大規模な生産工程でより費用効果が高い必要があるように思われるかもしれませんが、常にそうであるとは限りません。ほとんどの鉄鋼のオブジェクトは、消耗品の鋳造プロセスで作られています。
低温成形品(樹脂、チョコレート、ワックスなど)は、ほとんどの場合、再利用可能な金型を使用します。冶金学の違いは、高温が関係していることです。これらは金型に大きな負担をかけます。したがって、亜鉛、アルミニウム、マグネシウム、スズ、銅などの融点の低い合金が、再利用可能な成形プロセスで成功することが多いのは当然のことです。
ただし、状況によっては、鉄金属でさえ再利用可能な型に流し込まれます。設計の複雑さ、金属の選択、寸法公差と表面仕上げの要件はすべて、再利用可能な金型が適切かどうかに影響します。
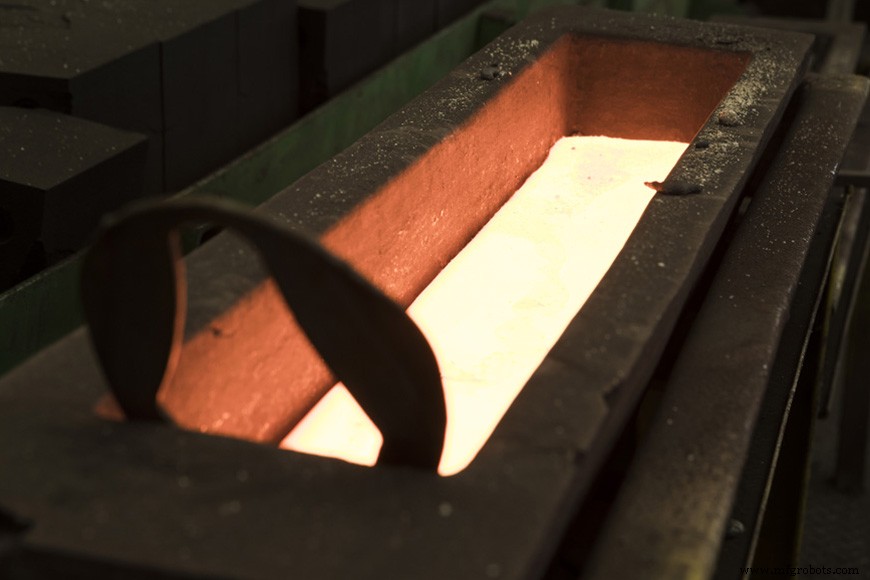
再利用可能なカビ
永久金型
恒久的な金型は通常、金属でできています。金属は、充填されている金属よりも融点が高くなっています。流体金属は、いかなる種類の外圧もなしに注がれます。パーマネントコアは、完成した鋳造物から再利用するために引き出すことができるように、単純でなければなりません。
これらの型は、鋳鉄や低温合金で使用されることがあります。組立ラインではなくターンテーブルが、最も一般的な産業ワークフローです。金型のコーティング、コアの配置、金型の閉鎖、注入、金型の開放、鋳造物の排出などの個々の操作は、各金型が次のステーションを通過するときに実行されます。
金型は、最初の鋳造物が注がれる前に予熱され、温度差によって割れないようになっています。
この方法で得られる鋳物は、ダイカストなどの他の再利用可能な方法の場合ほど壁を薄くすることはできません。ただし、鋳物は「厳密な公差」で製造されているため、最終的な鋳物のサイズをより正確に予測できます。この方法で作られた鋳物は、緻密できめが細かいです。それらはより滑らかな表面仕上げを持ち、いくつかのタイプの欠陥を回避します。
この成形形態は、鉄で使用するのに十分な耐久性がありますが、黄銅には好ましくないスタイルです。黄色の真ちゅうは亜鉛を多く含み、金型や金型を汚します。
半永久的なモールド鋳造の唯一の変更点は、鋳造プロセスで使用されるコアが消耗品の砂コアである可能性があることです。サンドコアは、最終的な鋳造からそのまま抽出する必要がないため、より複雑なコア形状が可能です。鋳物の開口部を残してコアを取り除くと、振動するテーブルでコアを「振り落とす」ことができ、砂時計を通して砂のように排出されます。永久鋳型鋳造の耐性、密度、および外観の利点は、金型に対して鋳造されたセクションにのみ存在します。
このカラフルな名前の鋳造スタイルは、金型の内側を少量の金属でコーティングするだけで、コアを必要とせずに中空の鋳造物を作成し、金属の「スキン」を作成します。金属または他の材料がどれだけ速く硬化するかに応じて、スラッシュ鋳造にアプローチするさまざまな方法があります。 1つの方法では、創設者は少量の液体を型に注ぎ、回転させて内部を金属で覆うことができます。別の方法では、ファウンダーは金型を完全に充填し、指定された冷却時間後に余分な材料を注ぎ出すことができます。亜鉛、アルミニウム、ピューターは、一般的にスラッシュキャストされる金属です。
真の遠心鋳造では、液体金属が供給されている間、水冷金型がその中心軸を中心に高速で回転します。遠心力により、液体金属が金型の表面に沿って均一な層で引っ張られます。この方法が機能するためには、最終的な鋳造物がスピン軸の周りに均一な形状を持っている必要があります。したがって、この形式の鋳造は、チューブやリングのように、ほぼ円筒形または円形の金型に最適です。
この方法でキャストされたオブジェクトは、通常、欠陥率が非常に低くなります。不純物は最終的に鋳造物のボアまたは内面の近くになり、機械加工で取り除くことができます。圧力下で使用されるほとんどのパイプまたはフィッティングは、シームレス構造の強度のために遠心鋳造されます。
宝石のようないくつかの小さな金属鋳物は、中心点の周りで型全体を振り回す遠心分離機を使用して作られ、るつぼが回転するときに金属を引き抜きます。これらの鋳物は真の遠心鋳造ではなく、圧力鋳造の一形態です。
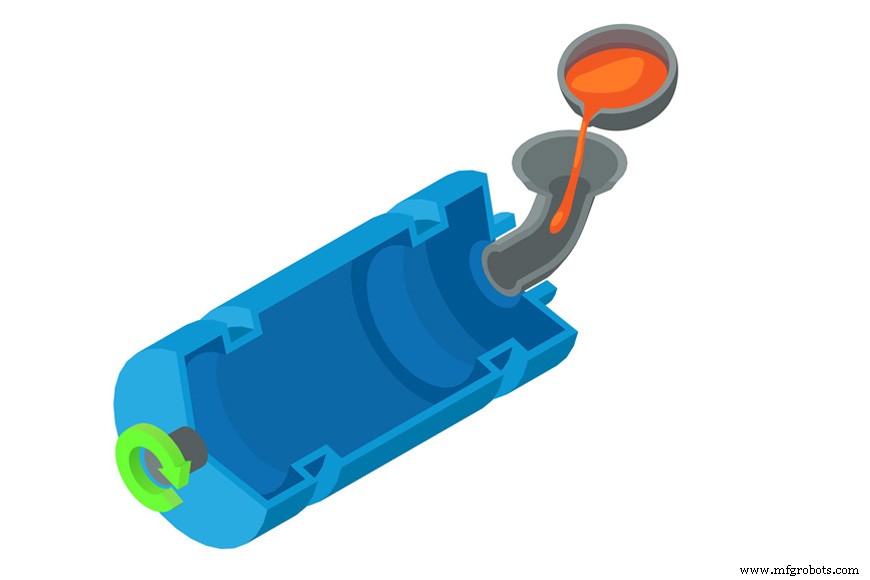
圧力鋳造法では、重力以外の力を使用して、永久金型への金属の流れを制御します。圧力鋳造では、空気またはガス、真空、機械的、または遠心力がすべて使用されます。これらの方法により、鋳造所は金型が充填される速度を正確に制御できます。重力は常に同じ力で機能しますが、人工の力は変化する可能性があります。
金型が減圧されると、真空鋳造によって金属が金型に引き込まれ、生成された真空によって液体金属が下のリザーバーから引き上げられます。金属が冷える間、真空は維持されなければならないので、この方法は主に薄壁の鋳造に使用されます。優れた表面仕上げを提供します。低圧鋳造は、金型内に真空を作り出すのではなく、液体金属が置かれている炉を加圧することによってこのプロセスを逆転させます。金属はライザーを介して金型キャビティに押し込まれます。
すべてのダイカストマシン(下記)も、何らかの形の圧力を使用して鋳造物を作成します。
ダイカストマシンは、溶融金属を保持する盆地、2つのプレート上の金型またはダイ、および材料を引き込み、圧力をかけてダイに押し込む注入システムで構成されています。
ダイカストのプロセスは、オープンモールドから始まります。ノズルは金型に潤滑剤をスプレーして、部品がくっつくのを防ぎます。次に、金型の2つの半分を閉じ、閉じた金型に圧力ノッスルを使用して射出します。新しい鋳造品は、ダイが開く前に冷却する時間が与えられます。エジェクターピンが新しい鋳造物をダイから押し出し、プロセスが再開されます。
ダイカストでの金属射出には2つの形態があります。コールドチャンバーダイカストは注射器のように機能します。各ダイを鋳造する前に、射出チャンバーに溶融金属を充填する必要があります。次に、ピストンがインジェクターの内容物をダイに押し込みます。ホットチャンバーまたはグースネックダイカストは、インジェクターシステムのチャンバーを溶融金属に浸すことによって機能します。システムの形状は、インジェクターがそれ自体を補充することを意味します。ホットチャンバーダイカストは、ピストンまたは空気圧のいずれかを使用して、この材料を金型に押し込みます。
グースネックシステムは、溶けた金属の槽にあるため、腐食しやすくなります。このため、通常、融点の低いアルミニウムまたはアルミニウム-亜鉛合金で使用されます。ピストンまたはコールドチャンバーインジェクションダイキャスターは、インジェクターが継続的に熱にさらされないため、真ちゅうと青銅を溶かすのに必要な高温に使用できます。
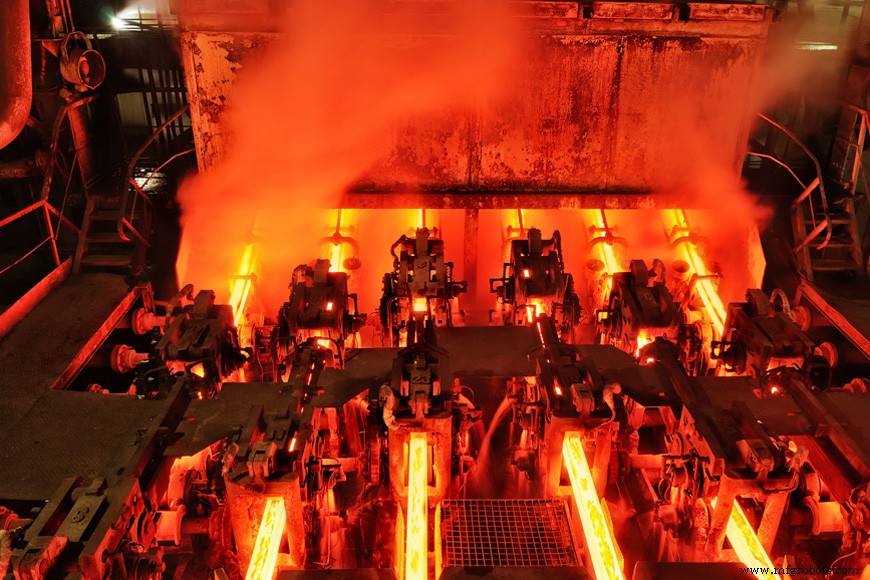
連続鋳造
完全に機械加工された、圧延された、またはその他の方法で加工されたと私たちが考える金属部品でさえ、しばしば鋳造所の床から始まりました。連続鋳造は、パーマネントフォームから押し出すことにより、単純な金属形状のさまざまなサイズのブルーム、ビレット、およびスラブを作成します。この鋳造プロセスにより、加工鋼の原料が作成されます。
連続鋳造プロセスは、工場の床より高い位置から始まります。溶融金属は、鋳造速度を制御する漏斗に供給されます。じょうごはその下の型を満たします。これは単純な形で、通常は長さが20〜80インチで、その幅が正方形、円、または長方形のように形作られています。金型壁は、鋳物が通過するときに鋳造物の外部が凍結するように冷却されます。金属が形を離れるとき、それは固化しますが、それでもしなやかです。これにより、連続鋳造機で曲げることができ、完成品が水平に出てきます。一連のホイールがスラブをコンベヤーベルトに導き、冷却スプレーが表面を固化します。水平面のガスジェットは、連続した金属片を扱いやすい長さに切断するため、持ち上げて積み重ねることができます。
鉄金属の鋳造に関しては、消耗型の方法が明らかに勝者です。高温に耐える必要がないため、費用対効果が高くなります。
砂型鋳造は、金属鋳造に使用される最も一般的な方法です。それは少なくとも3000年前の製造工程です。粘土鋳造の最初の証拠は、殷王朝(紀元前1600年から1046年頃)の間に中国から出てきました。
このプロセスが今でも非常に人気があるのも不思議ではありません。砂は安く、豊富で、しなやかで、熱を奪うことができます。
砂から作られたコアは簡単に取り除くことができます:それらは振動するテーブルで振り払うことができます。金属を金型キャビティに向けるために使用されるランナーとゲートは、経験豊富な成形業者が手作業で切断するか、パターンの一部として作成されます。
砂型鋳造品の表面仕上げは粗く、寸法公差は正確ではないことが多いため、砂型鋳造は装飾フェンスから鋳鉄鍋、自動車のエンジン部品まで、大きくて頑丈な部品を製造するのに最適です。
このシリーズの前回の記事で砂型鋳造の詳細をご覧ください。
シェルモールドは、砂型鋳造の一種であり、より厳密な寸法公差を提供します。砂型鋳造と非常によく似ていますが、砂だけが樹脂と混合されています。砂と樹脂の混合物が溶銑成形パターンの各半分に注がれます。この混合物は溶けて冷えて殻になります。型の「殻」は一緒にされ、通常は砂でいっぱいのフラスコによって支えられています。樹脂が内面をさらにサポートするため、これらのシェルは非常に正確な型を形成します。
多くの場合、シェルモールドは従来の砂型鋳造用のコアを製造するために使用されます。樹脂は、鋳物となるボイドの上に配置された場合でも、砂のコアに形状を維持するための強度を与えます。これらのシェルコアは中空で、スラッシュ鋳造のようなプロセスで溶銑型で作成されます。コアモールドの2つの半分をクランプして加熱し、樹脂でコーティングされた砂を充填します。シェルの壁がコアのサイズを支えるのに十分な厚さになるまで型を焼き、次に余分な未硬化の樹脂砂を注ぎ戻します。型の2つの半分が分割されると、頑丈なコアが現れ、砂型鋳造型に配置する準備が整い、鋳造物にスペースができます。
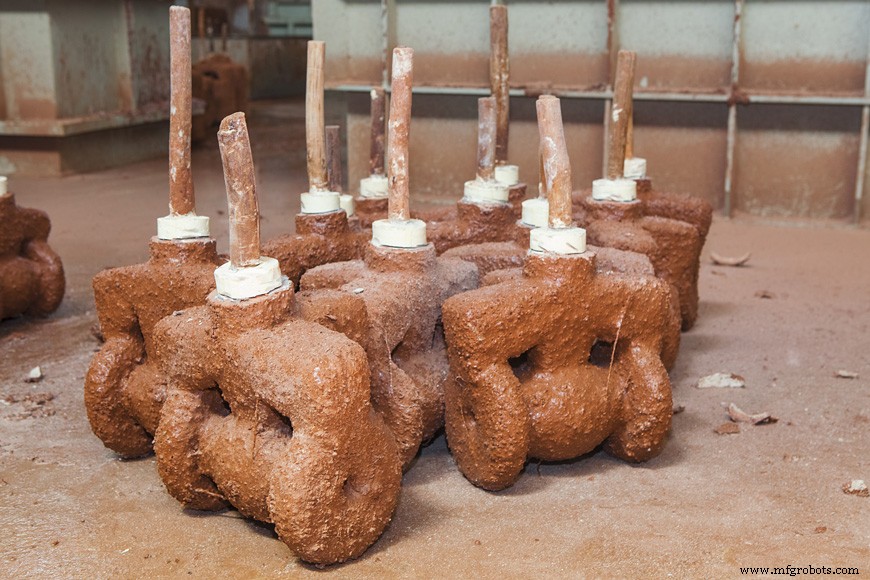
-
インベストメント鋳造(ロストワックス鋳造)
砂型鋳造は、これまでで最も使用されている金属鋳造の形態ですが、砂型鋳造には、一部のプロジェクトには不適切な側面が1つあります。砂型鋳造パターンは、それらが作成する型から取り除く必要があります。これは、複雑なパターン構造を意味する可能性があります。ドラフト要件、パーティングラインの配置、ゲート、ライザー、およびコアでは、パターンメーカーが鋳造プロセスの各段階でパターンのニーズを慎重に検討する必要があります。
ロストワックス、投資、または精密鋳造プロセスは、砂型鋳造の代替手段であり、ほとんどのグレードの金属、さらには高融点鉄合金でも機能しますが、砂型鋳造におけるパターン作成のこれらの課題のいくつかを回避します。
インベストメント鋳造の設計者は、ワックスまたはプラスチックのパターンが鋳造される正確な金属ダイを作成します。これらのパターンは、これもこの材料で作られたスプルー上に組み立てられます。鋳造作業員は、トーチを使用して、各パターンをスプルーに取り付けるのに十分なほどスプルーを溶かします。
次に、このアセンブリを使用して、金型として使用されるシェルを作成します。それは、細粒で耐火性の高い骨材と、主にケイ酸エチルで構成される独自の接着剤のスラリーにスプレー、ブラッシング、または浸漬されます。次に、この混合物を硬化させます。パターンの周りに骨材の殻ができるまで、パターンを粗いスラリーで繰り返しコーティングします。金型はコーティングが固まるまで放置され、その後オーブンで逆さにして加熱され、ワックスがなくなり、回収されて再利用されます。ワックスを取り除いた後、型を予熱した炉で焼きます。その後、型は緩い砂で支えられ、従来の方法で注がれます。
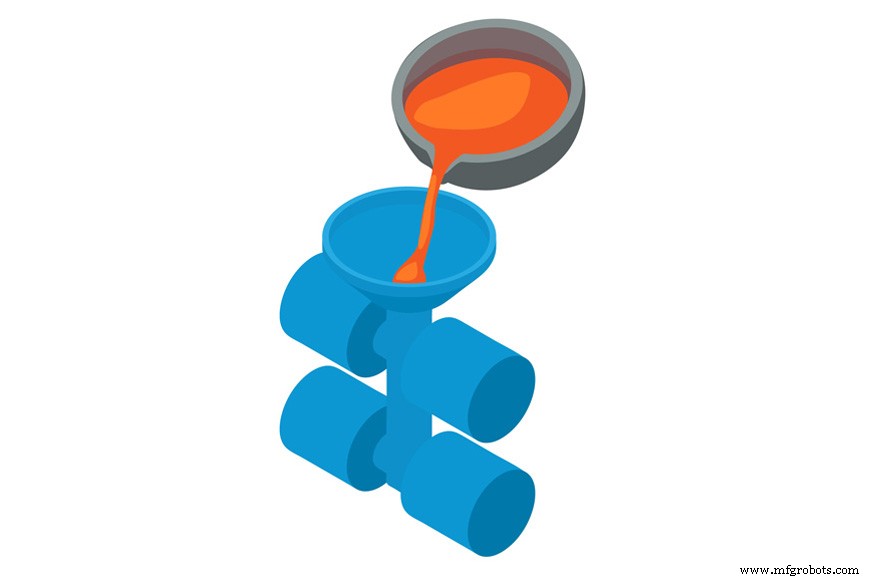
鋳物が冷えると、インベストメント鋳物の周りのシェルが壊れ、振動テーブルを使用して振り落とされます。
インベストメント鋳造は、優れた表面仕上げと高い寸法精度を提供します。砂型鋳造のようなパーティングラインはありません。
フルモールドまたはフォーム鋳造プロセスは、砂とインベストメント鋳造プロセスの組み合わせです。発泡スチロールのパターンを使用しています。確かに、発泡パターンは、ゲーティングおよびランナーシステムで完全にすることができ、ドラフト許容値の排除を組み込むことができます。充填前にパターンが削除されることもありますが、一部のフォームでは、パターンを金型内の所定の位置に残して、溶銑を注入するとすぐに気化することができます。
このプロセスは、1つまたは数個の鋳造工程に理想的ですが、ファウンドリがフォームパターンを大量生産して生産量を生み出すこともあります。破壊可能なフォームパターンを作成するための設備には余分な費用がかかりますが、パターンが非常に複雑な場合は、多くの場合、鋳造プロセス全体の経済性が有利になる可能性があります。
鋳造プロセスの比較
製造業者との協議は、プロジェクトをキャストするための最も費用効果の高い方法を見つけるのに役立ちます。一般に、鉄の金属は消耗品の型を使用して鋳造されますが、非鉄の金属はより広い範囲の可能性がありますが、この単純な規則にも例外があります。
プロジェクトのニーズを明確に理解してプロセスに入ると、キャストに最適なプロセスを選択するのに役立ちます。デザインは正確なサイズである必要がありますか?壁はどれくらい薄くする必要がありますか?最終的に鋳造物はどのようなサイズと重量になりますか?表面仕上げはどうですか?これらすべての質問に対する答えを事前に知っておくと、知識のある設計者が製品を理解して鋳造プロセスをガイドし、仕事をするための最良で最も安価なプロセスを見つけるのに役立ちます。
前の投稿:プロトタイピング金属鋳造プロセス次の投稿:砂型鋳造
金属