リチウムイオン電池のSi電極に及ぼすタングステンナノ層コーティングの影響
要約
タングステン(W)は、その電気化学的特性を強化するために、物理的気化堆積法(PVD)を介してナノスケールでシリコン(Si)アノードにコーティングされました。電極の特性は、走査型電子顕微鏡(SEM)、透過型電子顕微鏡(TEM)、エネルギー分散型X線分析、および電子プローブX線微量分析によって特定されました。電気化学的特性分析では、Wコーティングおよびコーティングされていない電極セルの最初の充電容量は2558 mAh g − 1 でした。 および1912mAh g − 1 、 それぞれ。 50サイクル目までに、容量比はそれぞれ61.1%と25.5%でした。サイクリング中のWコーティングされたSiアノードの形態変化は、SEMおよびTEMを使用して観察され、電気化学的特性はインピーダンス分析によって調べられました。原子W層コーティングからPVDまでの導電性と機械的特性により、電極はサイクル性を改善し、体積破壊から構造を維持しました。
背景
シリコン(Si)は、その高い比容量(4200 mAh g − 1 )により、アノードとして使用できる最も魅力的なエネルギー源要素の1つです。 )、これはグラファイトの10倍です[1]。ただし、Siは充電および放電プロセス中に問題のある体積膨張を経験し、膨張により格子体積が300%変化します[2、3、4、5]。これにより、電極に亀裂や崩壊が生じ、活物質の損失、電気的接触の減少、そして最終的には電気的特性の低下につながります。さらに、Siの低い電気伝導率は、電極材料としての使用の障壁になります。
したがって、Si電極の電気化学的特性を改善する方法は非常に関心が高く、炭素(C)複合組成、多次元構造、および金属を含む電極を使用するなど、Si電極に関連する問題を解決するために広範な研究が行われています。 -合金フォーム[6,7,8,9,10,11,12]。特に、耐衝撃性に使用される活物質法については、多くの研究が、対象をさまざまな材料でコーティングするためのアプローチを追求してきました[13、14、15、16]。膨張効果を抑えるために、カーボン、金属合金、さらには導電性高分子などの導電性材料が採用されており、緩衝効果だけでなく、電荷輸送の向上も実現しています。ただし、これらの研究方法は、詳細な製造手順のため、商用アプリケーションでの使用に関して制限があります。
物理蒸着(PVD)は、原子層堆積のプロセスを通じて、ナノメートルから可視スケールで基板上に均一なコーティングを生成します[17、18、19、20]。この用途の広い技術は、あらゆる種類の無機材料、さらには一部の有機材料の堆積を可能にするために、さまざまな分野に適用できます。さらに、この方法は、不均一な核形成と成長によって形成されたタイトな層を備えた化学蒸着よりも抵抗が少ないため[21]、耐摩耗性や硬度などの機械的特性が大幅に向上します。
この研究では、PVD法を使用してSi電極をタングステン(W)でコーティングし、バッファ層を提供してその導電率を高めました。純粋な形のすべての金属の中で、Wは最高の引張強度と優れた硬度を持っています[22、23]。さらに、Hornik etal。 [24]は、セラミック基板へのマグネトロンスパッタリングによるW PVDの効果を研究し、Wコーティングが低硬度または耐摩耗性の基板に適切に機能できることを示しました。電極表面にWナノ層を塗布することにより、Si電極の電気化学的特性と形態をさまざまな分析技術を使用して調べました。このWナノレイヤーのアプリケーションは、改善された電気化学的特性と持続的な構造上の安全性を示しました。
実験的
電極の製造
Si電極は、40 wt%Siナノ粉末(≤100nm)、導電性材料として40 wt%Denka Black、バインダーとしてカルボキシメチルセルロースを使用した鋳造法を使用して製造されました。これらの物質を脱イオン水に溶解してスラリーを形成した。次に、スラリーを銅箔(50μm)にコーティングし、70°Cで1時間乾燥させました。 Si電極のWコーティングは、Dongwoo Surface Tech Co.、Ltd。でPVD法(図1)を使用して実施しました。プラズマ発生器として100°CでArガスを使用し、W蒸着を5分間実施しました。堆積したW電極表面は、走査型電子顕微鏡(SEM)、透過型電子顕微鏡(TEM)、電子プローブX線微量分析(EPMA)、およびエネルギー分散型X線分光法(EDX)によって検査されました。
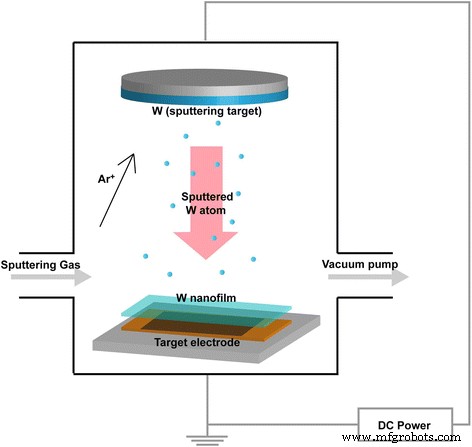
Wコーティングの物理蒸着の概略図
テストセル手順
テストセルは、乾燥室でCR2032タイプのコインセルを使用して組み立てられました。 Siアノード電極は14Φのサイズに打ち抜かれ、対電極はリチウム箔から16Φのサイズに打ち抜かれました。 14Φサイズの電極に対応するWナノレイヤーの測定重量は、約0.0001gです。使用した電解液は1M LiPF 6 等量のエチレンカーボネート、ジメチルカーボネート、およびエチレンメチルカーボネートを含む混合物(大韓民国、ソウルブレイン)。すべてのセルは乾燥室で製造されました。組み立てられたセルは、40°Cで24時間エージングされました。
定電流電気化学試験は、WBCS 3000機器(WonATech Inc.、大韓民国)を使用して実行されました。充電と放電のプロセスは、0〜1.5 Vで実行され、各プロセスに特定の電流レートが使用されました。サイクル後、W被覆および非被覆Si電極の表面観察を行った。さらに、インピーダンステストは10 − 2 の周波数で実行されました。 〜10 5 コーティング効果を比較するための5mVのAC振幅(SOLATRON SI1280B)のHz。
結果と考察
図2は、未処理のコーティングされていない(a)およびWコーティングされた(b)Si電極のSEM画像を示しています。電極は100nm未満のサイズのSiナノ粉末で構成されていたため、粉末は元のサイズを維持しました。ただし、コーティングされた電極へのWの物理蒸着により、各粒子はW層で覆われているように見え、粒子の全体的なサイズは約100〜120nmに増加しました。 SEM画像の赤いボックス内の要素のEDX分析(図2b)により、Wの存在が明らかになりました(図2d)。さらに、EPMAは、堆積したWが均一に分布していることを確認しました(図3)。
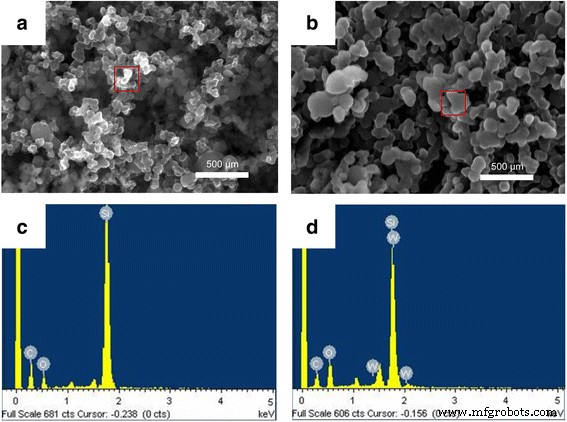
未処理のコーティングされていない a の走査型電子顕微鏡画像とエネルギー分散型X線プロファイル および c コーティングされた b および d Si電極表面
W層の厚さを調べるために、深さプロファイリングを使用したTEM分析を実施しました。図4は、Siナノ粒子(黒)上に堆積されたW層(白)の深さが約40nmであることを確認しています。 W層は、Si粉末と他の電極材料の間のギャップも覆っていました。上記の試験から、PVD法でコーティングされたW層がナノメートルスケールで良好に形成されたことが明らかです。
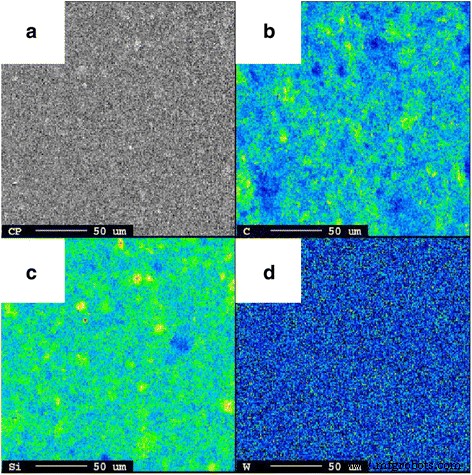
a b の走査型電子顕微鏡画像および電子プローブX線微量分析測定結果 C、 c Si、および d W
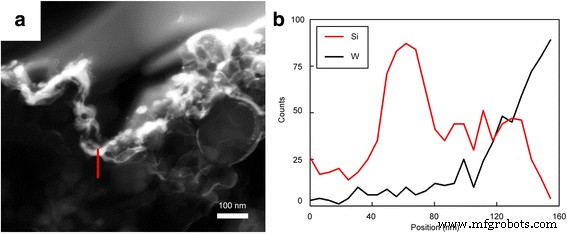
a 透過型電子顕微鏡画像と b WコーティングされたSi電極の深さプロファイリング
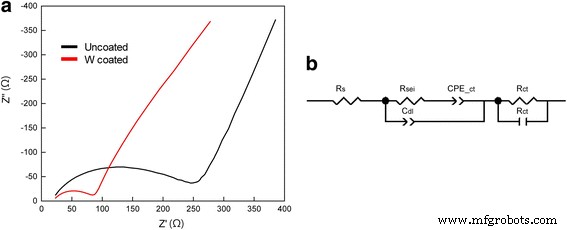
a サイクル前のコーティングされていないSi電極とWコーティングされたSi電極のEIS分析および b 同等のプロット
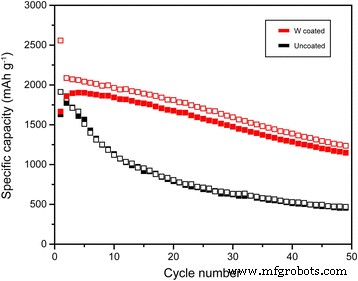
0.1 CのレートでのコーティングされていないSi電極とWコーティングされたSi電極の充電/放電容量プロファイル、および50サイクルにわたる0〜1.5Vのカットオフ電圧範囲
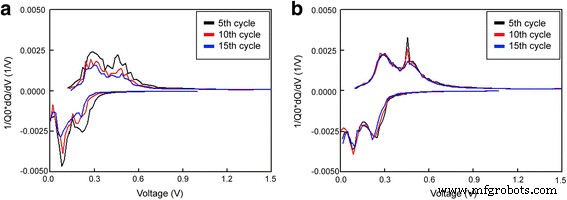
a のdQ / dV曲線 コーティングされていない b 5、10、および15サイクルで0〜1.5 V(vs。Li / Li +)のカットオフ電圧範囲で0.1CのレートでWコーティングされたSi電極
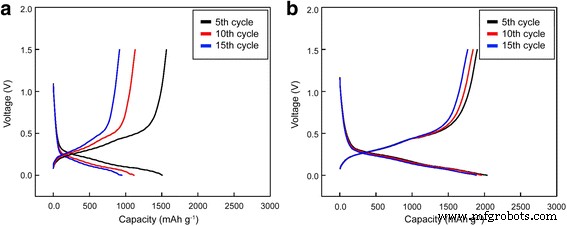
a の電圧プロファイル コーティングされていない b 5、10、および15サイクルで0〜1.5 V(vs。Li / Li +)のカットオフ電圧範囲で0.1CのレートでWコーティングされたSi電極
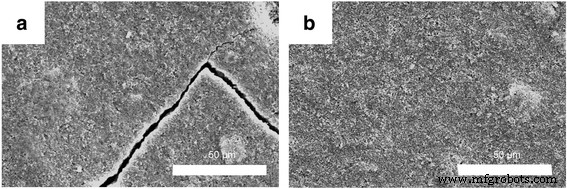
a の走査型電子顕微鏡画像 コーティングされていない b 10サイクル後のWコーティングされたSi電極
さらなる分析のために、電気化学的インピーダンス分光法(EIS)テストを実施しました。図5は、(a)コーティングされていないSi電極とWコーティングされたSi電極、および(b)等価回路のインピーダンス結果を示しています。この図は、ランドルス回路構造に基づく等価回路を示しています。表1は、インピーダンスフィッティングの結果を示しています。等価回路では、 R s 電極と電解質のオーム抵抗の合計を示し、 R ct および C dl それぞれ、電荷移動抵抗と二重層静電容量を表します。定相素子(CPE)は R に接続されています ct シリーズ[25、26]。 R sei および C sei 、電極表面の抵抗と静電容量に関連する[27]は、並列になっています。
<図> 図>図5と表1に示すように、初期状態を比較することにより、 R の値 s および R ct Wコーティングにより減少しましたが、 R sei 表面抵抗の増加により増加しました。この結果は、W層が均一にコーティングされているため、導電性が向上し、容量の増加と安定したサイクル性能に貢献している可能性があることを示しています。ただし、 R の増加 sei イオン拡散インピーダンスも観察され、W層がイオン透過性阻害剤として機能できることを意味します。
図6に、50サイクルにわたる0.1 Cの速度での裸セルとWコーティングセルの比容量をプロットします。最初のサイクルでは、WコーティングおよびコーティングされていないSi電極セルの充電容量は2588および1912mAhでした。 g − 1 、 それぞれ。これは、Wの高い導電率によって説明される可能性があります。これにより、Si電極はより多くのLiイオンを受け取り、より速い電荷移動を刺激します。 10、20、および50サイクルでのWコーティングされたSi電極の放電容量は、1843、1676、および1137 mAh g − 1 でした。 、それぞれ、同じサイクルの保持率は、それぞれ99.1、90.1、および61.1%でした。コーティングされていないSi電極の値は、1132、790、および452 mAh g − 1 でした。 それぞれ63.9、44.6、25.5%。コーティングされたセルは明らかに改善された能力を示した。この結果は、緩衝層を形成し、導電性を高めるWコーティングに起因します。コーティングされていないSi電極は構造破壊にさらされ、WコーティングされたSi電極はWナノレイヤーによって保護され、全体的な亀裂の形成を防ぎ、電極表面の保護につながりました。ただし、Wコーティングは、すべてのサイクルで不可逆的な容量損失を引き起こしました。 Liイオンは、EISテストで説明したようにイオン伝導性材料ではない不活性なW層を通過する必要があるため、放電中のイオン輸送が遅くなり、不可逆性が生じる可能性があります。
図7は、WコーティングされたSi電極とコーティングされていないSi電極の両方について、5、10、および15サイクルのdQ / dV曲線を示しています。反応のピークは同じ電圧領域にあります。これは、充電と放電のプロセスが同等の反応で発生したことを意味します[28、29]。これは、WコーティングがSi電極の形態に影響を与えず、表面層のみを覆い、活物質として機能しなかったことを示しています。サイクル数が増加すると、コーティングされていないSi電極の反応電圧領域がシフトし、分極が増加しましたが、WコーティングされたSi電極の反応電圧領域は比較的一定のままでした。これは、Wコーティングが化学的安定性の維持に役立つことを意味します。この結果は、図8の電圧プロファイルにも反映されています。これは、Wコーティングされた電極が持続的な反応電圧でその容量を維持していることを示しています。
WコーティングされたSi電極とコーティングされていないSi電極の両方が、10サイクル後にSEMによって観察されました(図9)。 100 nm未満のナノ粉末サイズを使用した場合、Si電極自体に亀裂は観察されませんでした[30]。しかし、電極全体の膨張により、サイクル中にスプリットが発生しました。それにもかかわらず、WコーティングされたSi電極はひび割れがなく、PVDによる原子堆積とWの強力な機械的強度が効果的に膨張を維持したことを示しています[19、20]。
結論
電極の電気化学的性能を改善するために、PVD手順を使用してWをSi電極上にコーティングしました。コーティング層は約40nmの厚さで、均一に堆積されました。 Wコーティングされた電極の容量保持は、サイクル性能の向上を示し、50サイクルを通じて61.1%で維持されましたが、コーティングされていない電極の保持はわずか25.5%でした。サイクリング後に2つの異なる電極の表面を調査したところ、観察結果から、Wがバッファー層として機能していることがわかりました。さらに、Wコーティング層は電極の抵抗率を下げ、セルの導電率を高めました。 PVDを介したこの簡単なナノレイヤーアプリケーションが、Siベースの電極の将来の設計のリファレンスとして役立つことを願っています。
略語
- CPE:
-
定相要素
- EDX:
-
エネルギー分散型X線分光法
- EIS:
-
電気化学インピーダンス分光法
- EPMA:
-
電子プローブX線マイクロアナリシス
- PVD:
-
物理的気化堆積
- SEM:
-
走査型電子顕微鏡
- TEM:
-
透過型電子顕微鏡
ナノマテリアル