マグネシウム合金への無電解Ni-P-Al2O3複合コーティングの堆積プロセスと特性
要約
マグネシウム(Mg)合金上の無電解ニッケル-リン(Ni-P)コーティングの耐食性と耐摩耗性を向上させるため。 Ni-P-Al 2 O 3 コーティングは、複合めっき浴からのMg合金上に生成されました。最適なAl 2 O 3 濃度は、めっき浴とコーティングの特性によって決定されました。 Ni-P-Al 2 の形態成長の進化 O 3 走査型電子顕微鏡(SEM)を使用して、異なる時間の複合コーティングを観察しました。結果は、nano-Al 2 O 3 粒子はMgとNi 2+ の置換反応を遅くする可能性があります 堆積プロセスの初期段階ではありますが、Ni-P自己触媒還元プロセスの速度にはほとんど影響しません。コーティングの防食および微小硬度試験により、Ni-P-Al 2 O 3 複合コーティングは、Ni-P-Al 2 のより適切な結晶面間隔と粒子サイズにより、Ni-Pコーティングと比較して優れた性能を示します。 O 3 コーティング。熱衝撃試験は、Al 2 O 3 粒子はコーティングの接着に影響を与えません。さらに、複合めっき浴の耐用年数は4.2金属ターンオーバーであり、マグネシウム合金の分野での潜在的な用途があることを示唆しています。
背景
マグネシウム(Mg)合金は、密度が低く、比強度が高く、被削性に優れているため、多くの注目と科学的研究が行われています[1、2]。したがって、Mg合金は通常、航空宇宙、電子機器、自動車の分野で利用されています[3、4]。しかし、Mg合金の用途は、耐食性と耐摩耗性の望ましくない欠陥のために制限されています[5、6]。このように、マイクロアーク酸化膜、化成処理コーティング、溶射、物理蒸着、電気めっき、無電解めっきなどの表面防食および減摩法が、Mg合金用に開発されました[7、8、9、 10,11,12,13]。
無電解ニッケル-リン(Ni-P)めっきは、低コスト、効率、耐食性、耐摩耗性に優れた包括的な利点があるため、Mg合金の最も効果的な表面技術の1つです[14、15]。したがって、無電解Ni-Pコーティングは、Mg合金の防食分野で重要な役割を果たします。 Ni-Pコーティングの性能をさらに向上させるために、ナノ粒子、たとえばSiC、ZrO 2 、TiO 2 、SiO 2 、およびAl 2 O 3 等は通常無電解めっき浴に加えられ、Ni-Pナノ粒子複合コーティングを調製します[16、17、18、19、20]。以前の研究[20,21,22,23]によると、Ni-Pコーティングの性能はナノ粒子によって効果的に改善されます。 Ni-Pナノ粒子複合コーティングはNi-Pコーティングと比較して比較的高い性能を持っていますが、注意しなければならない3つの問題があります。第一に、ナノ粒子は凝集しやすく、無電解めっき浴で活性中心を形成します。これにより、めっき液の安定性が低下します。第二に、複合めっき浴のプロセスパラメータは通常、コーティング中のナノ粒子の含有量と分布を決定し、コーティングの特性を改善するための重要な要素でもあります。第三に、Ni-Pとのナノ粒子の共堆積のプロセスは、コーティング特性に対する別の影響要因です。したがって、これらの要因は注目に値します。 Nano-Al 2 O 3 粒子は安価な研磨剤であり、硬度が高く、化学的安定性が良好です[24、25]。無電解ニッケルめっき浴によく分散させることができます。したがって、Ni-P-Al 2 O 3 複合コーティングは通常、鋼または銅の基板を保護するための防食および耐摩耗コーティングとして使用されます。ただし、無電解Ni-P-Al 2 に焦点を当てた報告はごくわずかです。 O 3 マグネシウム合金基板へのめっき[20、22、26]。さらに、Ni-P-Al 2 の成長過程の研究 O 3 Mg合金へのコーティングと複合めっき浴の安定性はかなりまれです。したがって、複合浴の性能とNi-P-Al 2 の共蒸着プロセスに関する詳細 O 3 勉強する必要があります。
本研究では、Mg合金基板上のNi-Pコーティングの特性をさらに向上させるために、めっき浴の主な塩と錯化剤として、それぞれ硫酸ニッケルと乳酸システムを採用しました。一方、nano-Al 2 O 3 無電解Ni-Pめっき浴に粉末を加えた。 AZ91D Mg合金に適した無電解複合めっき浴を得るために、この浴のプロセスパラメータを堆積速度とコーティング特性によって評価しました。さらに、定期的なサイクルテストを実施して、最適なプロセス条件でのめっき浴の耐用年数と安定性を評価しました。 nano-Al 2 の効果を研究するには O 3 コーティングの成長過程における粒子、Ni-Pコーティングの堆積挙動および相構造が議論された。さらに、耐食性、微小硬度、コーティングの接着性などの特性を、形態と構造に基づいて分析しました。結果は、Ni-P-Al 2 の特性が O 3 複合コーティングはNi-Pコーティングよりも好ましく、無電解複合めっき浴は耐用年数において良好な安定性を示しました。したがって、この研究での私たちの結果は、Mg合金に無電解Ni-Pナノ粒子複合コーティングを適用するための有用な参考資料です。
メソッド
複合コーティングの準備
この作業では、2cm×1cm×0.5cmのサイズのAZ91DダイカストMg合金を実験材料として使用しました。これには、化学組成がwt%で含まれています:8.5 Al、0.34 Zn、0.1 Si、0.03 Cu、0.002 Ni 、0.005 Fe、および0.02その他、Mgのバランスを取ります。 AZ91D基板は、なしで連続的に研磨されました。 500および1000SiC紙、脱イオン水ですすぎ、65°Cで5分間アルカリ性溶液に浸した後、クロム酸溶液(CrO 3 200 g / L)60秒間。その後、Mg合金基板を濃度380mL / Lのフッ化水素酸溶液に浸し、活性化処理を約10分行いました。 Mg基板は、各ステップで脱イオン水で洗浄された。マグネシウム合金用の無電解ニッケルめっきの基本的な浴組成と操作条件を次のように示しました。35g/ L NiSO 4 ⋅6H 2 O、35 g / L乳酸、30 g / L Na 2 H 2 PO 2 ⋅H 2 O、10 g / L NH 4 HF 2 、3 mg / L安定剤、pH 4.5〜7.0、温度70〜90°C。無電解めっき浴は、サーモスタット制御の水浴に置かれたガラスビーカーに保持された。デジタルディスプレイ電気攪拌機を使用して攪拌力を提供した。 nano-Al 2 の平均粒子サイズ O 3 粒子は約50nmです。ナノAl 2 O 3 無電解めっきの前に、粒子は超音波条件下で浴中に適切に分散されました。
めっき浴の堆積速度と安定性のテスト
nano-Al 2 の効果を研究するには O 3 無電解ニッケルめっき浴の堆積速度に粒子が存在する場合、堆積速度は式(1)で表されます。 (1)。
$$ v =\ frac {\ Delta w \ times {10} ^ 4} {\ rho St} $$(1)ここで v 、ρ 、 S 、 t 、および△ w 堆積速度(μm/ h)、Ni-Pコーティングの密度(〜7.9g / cm 3 )、Mg基板の表面積(cm 2 )、堆積時間(h)、およびコーティング重量(g)、それぞれ。さらに、nano-Al 2 の含有量 O 3 コーティング中の粒子は、電子天秤(AR2140、Ohaus)を使用した計量法によって推定されました。無電解めっき浴の安定性を評価するために、定期サイクル試験(または金属ターンオーバー、MTO)を使用して、浴の耐用年数と安定性を評価しました。ここで、1 MTOは、Niの堆積重量がNi 2+ の初期濃度に等しいと定義しています。 お風呂で。 1 Lのめっき浴を例にとると、浴から約7.8 gのNiが得られます\(\ left({C} _ {{\ mathrm {Ni}} ^ {2 +}} =7.8 \ kern0.5em \ mathrm {g} / \ mathrm {L} \ right)\)1MTOと見なします。さらに、新しい混合溶液(\({\ mathrm {Ni}} ^ {2 +}:{\ mathrm {H}} _ 2 {\ mathrm {PO}} _ 2 ^ {2-} =1:3 \)浴の堆積速度が遅いときに、モル比で)をめっき浴に加えた。めっき浴が分解するまで安定性試験を終了した。したがって、MTOの式は次のように表すことができます。 (2)。
$$ \ mathrm {MTO} =M / m $$(2)M および m Niの累積堆積重量とNi 2+ の濃度を表します それぞれメッキ浴で。
材料の特性評価
コーティングの表面形態は、走査型電子顕微鏡(SEM、日立S−4800)を使用することによって観察された。コーティングの構造は、CuK αを備えたX線回折計(XRD、D / Max-2200、日本)によって研究されました。 放射線(γ =0.154nm)。
電気化学的測定
電気化学分析装置(CHI800、Chenhua、中国)で動電位分極試験を実施しました。電気化学的実験は、作用電極(サンプル、1 cm 2 )で構成される従来の3電極構成を使用して、3.5 wt%のNaCl水溶液で実施しました。 )、対極(白金)、および参照電極(飽和カロメル電極)。動電位掃引実験中、開回路電位( E )を安定させるために、サンプルを最初に電解液に30分間浸漬しました。 0 )。ターフェルプロットは、記録されたデータと腐食電流密度( i )から変換されました。 corr )は、陽極および陰極のターフェル線の直線部分を外挿することによって決定されました。実験の掃引速度は5mV / sで、25°Cで実行されました。さまざまな複合コーティングを施したマグネシウム合金の微小硬度を、100gの荷重と15秒の耐久時間でビッカー圧子を備えたHXD-1000微小硬度試験機を使用して評価しました。コーティングの密着性を評価するために熱衝撃試験を実施した[23]。それは次のように説明されました:空気雰囲気中で、Ni-PコーティングまたはNi-P-Al 2 を備えたMg基板 O 3 コーティングを高温ボックス抵抗炉に入れ、20°Cmin -1 の加熱速度で250±10°Cに加熱しました。 その後、冷水で急冷しました。このプロセスを20回繰り返しました。
結果と考察
図1は、nano-Al 2 の濃度の影響を示しています。 O 3 粒子、攪拌速度、堆積速度のpHと温度、およびAl 2 O 3 複合コーティングの含有量。図1aに見られるように、堆積速度はAl 2 の増加とともにわずかに減少します。 O 3 粒子濃度は0〜15 g / Lです。一方、Al 2 O 3 複合コーティングの含有量は、Al 2 の濃度が高くなるにつれて徐々に増加します。 O 3 粒子は0〜10 g / Lに増加します。ただし、Al 2 の濃度が高くなると、代わりに減少します。 O 3 粒子が10g / Lを超えています。この変化は、高濃度での粒子の凝集によるものであり、Ni-PとAl 2 の共堆積挙動を弱めます。 O 3 。図1bにおいて、攪拌速度を300〜400rpmに設定した場合の堆積速度とAl 2 O 3 複合コーティングの含有量は、それぞれ18μm/ hと3.6%です。結果は、Al 2 の分散性が O 3 めっき浴中の粒子は、この範囲の攪拌速度で最適です。酸性複合めっき浴に関しては、堆積速度とAl 2 に対するpH値の影響 O 3 コーティングの含有量を図1cに示します。 pH値が6.0〜6.5の範囲内にある場合、最大堆積速度は最大18.5μm/ hですが、Al 2 O 3 コーティングの含有量は、pH値とともにほぼ増加します。図1dは、堆積速度とAl 2 の両方を示しています。 O 3 イオンと粒子の活性が向上し、複合浴の反応速度も高温で加速されるため、複合コーティングの含有量は温度とともに増加します。しかし、高温(> 85°C)ではめっき浴の安定性とコーティングの多孔性が悪化します[13、22]。上記の分析結果に基づいて、複合浴の予備プロセスパラメータと動作条件がマグネシウム合金、つまり35 g / L NiSO 4 に対して決定されます。 ⋅6H 2 O、35 g / L乳酸、30 g / L Na 2 H 2 PO 2 ⋅H 2 O、10 g / L NH 4 HF 2 、10 g / L nano-Al 2 O 3 粒子、3 mg / L安定剤、pH =6.0〜6.5、 T =85°C、350rpmでの攪拌速度。
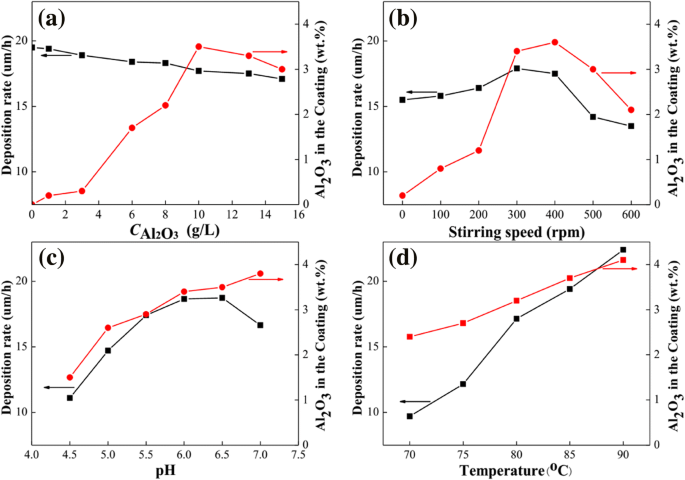
堆積速度とAl 2 に対するプロセスパラメータの影響 O 3 コーティングの内容
Ni-P-Al 2 の堆積プロセスを調査するには O 3 コーティング、堆積反応時間に伴うマグネシウム合金の表面形態画像の変化を図2に示します。比較分析のために、図2a–cはNi-Pコーティングの堆積プロセスを表し、図2d–fはcoを示します。 -Ni-P-Al 2 の堆積プロセス O 3 (3.6 wt%)複合コーティング。図2aは、Mg基板をめっき浴に0.5分間浸漬したときの形態画像であり、多数の立方体構造の粒子がその表面に分布しています。これらの立方体粒子はMgF 2 として確認されます 、これは主にHF活性化プロセスで形成され、文献の報告と一致しています[23、27]。ただし、図2dの画像の形態は図2aとは明らかに異なります。主な違いは、MgF 2 図2dの粒子は図2aの粒子よりも少ないです。さらに、多くのナノAl 2 O 3 Mg基板の表面に粒子が観察されます。形態の変化はAl 2 に起因します O 3 高温および攪拌プロセスでマグネシウム合金の表面に継続的に衝突する粒子。図2bに示すように、無電解Ni-Pめっき時間が最大5分になると、Ni粒子が徐々に成長し、マグネシウム合金の表面全体を覆います。しかし、無電解複合めっき(図2eを参照)の場合、より大きなNi粒子とナノAl 2 O 3 マグネシウム合金の表面に粒子が観察され、Ni-P-Al 2 O 3 コーティングは5分以内にMg基板を完全に覆いません。これは、Ni-P-Al 2 の成長率を示しています。 O 3 複合浴のコーティングは、Al 2 のない浴のNi-Pコーティングよりも低くなっています。 O 3 粒子。これは、複合めっき浴の堆積速度が遅い原因を裏付ける証拠です。無電解めっき時間を30分間行った場合、Ni-PコーティングとNi-P-Al 2 の形態 O 3 コーティングはそれぞれ図2c、fに示されています。 Ni-Pコーティングの場合、表面は平均サイズ3μmの緻密で結節状の構造を示します。しかし、図2fでは、Ni-P-Al 2 の平均結節サイズ O 3 複合コーティングは、Ni-Pコーティングよりも明らかに小さいです。さらに、nano-Al 2 O 3 Ni-Pコーティングに埋め込まれた粒子。重要なのは、Al 2 の表面分布の観点からです。 O 3 粒子、Al 2 の分布 O 3 図2fの粒子は、図2cの粒子よりも大幅に少なくなっています。この結果は、Ni-Pの堆積が支配的であるのに対し、Al 2 の堆積が支配的であることを示しています。 O 3 粒子は、5分の堆積反応時間後に従属します。同様の推論は、Al 2 の相対的な含有量からも取得できます。 O 3 コーティング中の粒子(図1)。言い換えれば、Al 2 の効果 O 3 堆積プロセス上の粒子は、主に無電解ニッケルめっきの初期段階に存在します。
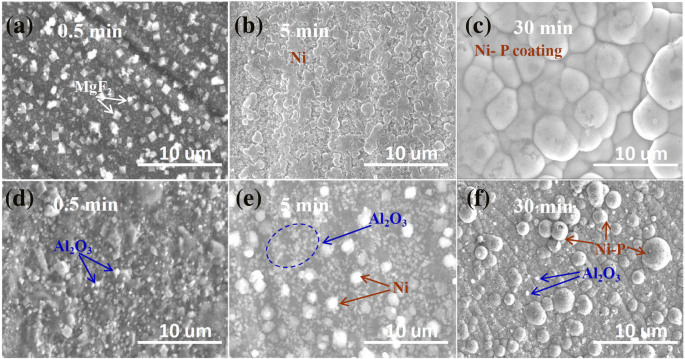
Ni-Pコーティングの表面形態(上、 a - c )およびNi-P-Al 2 O 3 複合コーティング(下、 d - f )異なる堆積時間で
nano-Al 2 の効果を調査するには O 3 Ni-Pコーティングの構造上の粒子、AZ91D Mg合金のXRDパターン、Ni-Pコーティング、およびNi-P-Al 2 O 3 複合コーティングを図3で分析します。図3に示すように、マグネシウム合金の結晶面の回折角は主に30°〜70°の範囲に集中します。たとえば、α (10 \(\ overline {1} \)0)32.2°、α (0002)34.2°、β (10 \(\ overline {1} \)1)36.8°など。Ni-PコーティングでコーティングされたMg合金の場合、Ni-Pコーティングの回折パターンは、44.7°で広がるピークと高強度の回折を示します。ニッケルの面心立方(fcc)相の(111)結晶面に起因する可能性があります(表1)[28]。さらに、そのような広いピークの存在は、混合アモルファス結晶構造を有するNi-Pコーティングの形成を示している。 Ni-P-Al 2 をめっきした後 O 3 (3.6 wt%)複合コーティング、25.6°、43.5°、および73.2°に3つの新しい回折ピークが明らかに見られます。これらのピークは、Al 2 の特徴的な回折ピークに起因します。 O 3 PDFカード番号と比較して。 88-0826。したがって、Ni-P-Al 2 O 3 複合コーティングはMg合金の表面に堆積されます。さらに、Ni-P-Al 2 では、Niの(111)結晶面の回折ピークが45.2°にシフトします(表1を参照)。 O 3 複合コーティング、ナノAl 2 を示唆 O 3 粒子は、Niの(111)結晶面間隔に一定の影響を及ぼします。ブラッグの法則によれば、nλ =2 d sin θ ( n =1、2、3、...、λ= 0.154 nm、 d およびθ それぞれ面間間隔と回折角を表します)、Niの(111)結晶面間隔はAl 2 によって約3%減少します。 O 3 粒子。さらに、Ni-Pコーティング中のNiの(111)回折ピークとNi-P-Al 2 O 3 複合コーティングは、それぞれガウス関数によって適合されました。結果は、Ni-P-Al 2 のこの回折ピークの半値全幅(FWHM)を示しています。 O 3 複合コーティングは、Ni-Pコーティングよりも幅が広くなっています(表1)。シェラーの式によると、 D =Kγ / B cos θ ( D 、 K 、 B Ni-P-Al 2 の結晶粒である結晶粒、シェラー定数、およびFWHMをそれぞれ表します。 O 3 複合コーティングはAl 2 によって約8%削減されます O 3 Ni-Pコーティングと比較した粒子。これは、nano-Al 2 O 3 粒子はNi結晶粒のサイズを微細化します。これは、上記のSEMの観察結果と一致しています。
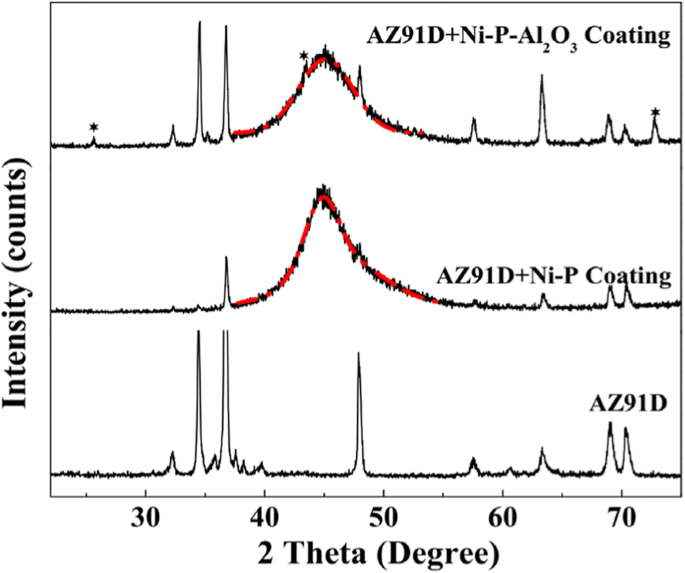
AZ91D基板、Ni-Pコーティング、およびNi-P-Al 2 のXRDパターン O 3 (3.6 wt%)複合コーティング
図4と表2は、AZ91D Mg合金基板、Ni-Pコーティング、およびNi-P-Al 2 の分極曲線と防食パラメータを示しています。 O 3 それぞれ、室温での3.5 wt%NaCl水溶液中の複合コーティング。分極曲線の陰極反応は水素の発生に対応しますが、陽極分極曲線は耐食性の最も重要な特徴的な反応プロセスです[29]。 AZ91D Mg合金基板の場合、印加電位が陽極領域に増加すると、活性化制御された陽極プロセスが観察されます。さらに、それは電解質溶液に真剣に溶解し、その腐食電位( E corr )は-1.47 Vで読み取られます。ただし、 E の場合 corr Ni-Pコーティングでは、Mg合金基板(-1.47 V)と比較して-0.51 Vへの有意な正のシフトと腐食電流密度( i corr )明らかに1.4×10 -4 から減少します A / cm 2 基板の3.1×10 -6 A / cm 2 Ni-Pコーティングの(表2を参照)。 Ni-P-Al 2 について O 3 (1.7〜4.2 wt%)複合コーティング、ここでは、Al 2 O 3 コーティングの含有量は、計量法によって得られます。表2に示すように、すべての E corr 複合コーティングの正のシフトと i corr 複合コーティングの割合はNi-Pコーティングと比較して減少しており、Ni-P-Al 2 O 3 コーティングは耐食性においてより高い性能を持っています。ここで、3.6 wt%のAl 2 を含むNi-Pコーティング O 3 最高の E を示します corr (− 0.35 V)および最低の i corr (4.5×10 −7 A / cm 2 )。ただし、 E corr および i corr Ni-P-Al 2 の O 3 (4.2 wt%)は-0.41Vおよび1.0×10 -6 に変更されます A / cm 2 、 それぞれ。 Al 2 の可能性があります O 3 粒子はNi-Pコーティングの多孔性を高め、複合コーティングの性能を低下させます。したがって、Al 2 O 3 複合コーティングの含有量は、複合コーティングの耐食性に重要な影響を及ぼします。また、結晶面の間隔やコーティングの粒径などの構造にも関係しています(図3)。
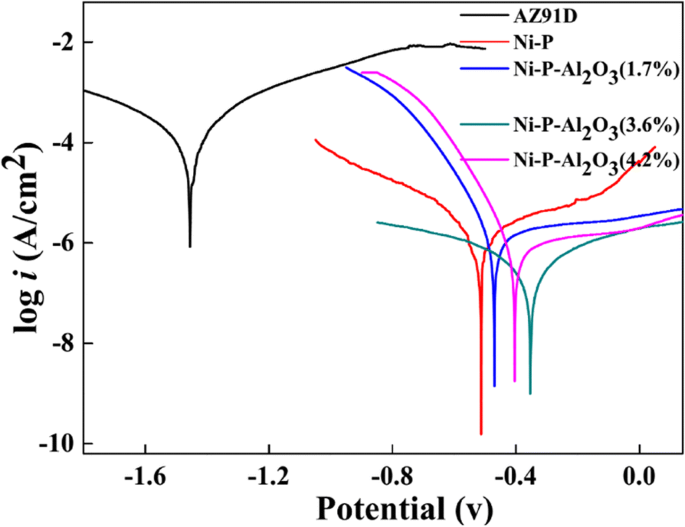
AZ91D基板、Ni-Pコーティング、およびNi-P-Al 2 の分極曲線 O 3 複合コーティング
コーティングの微小硬度をテストするために、すべてのコーティングの平均厚さを18μmと決定しました。これは、堆積速度と堆積時間によって推定されました。 Mg合金基板と異なるAl 2 のコーティングの微小硬度試験の結果 O 3 内容を図5に示します。図5に示すように、裸のAZ91DMg合金の微小硬度はわずか約120HVですが、Ni-PコーティングでコーティングされたMg合金基板の微小硬度は最大です。 520HV。基板より約400HV高く、Ni-Pコーティングが基板コーティングの硬度を効果的に向上させることができることを示しています。その結果、Mg合金基板の耐摩耗性はNi-Pコーティングによって強化されます。さらに、Ni-P-Al 2 O 3 複合コーティングは、Al 2 の含有量が高い場合、微小硬度のかなりの増加傾向を示します。 O 3 コーティング中は0から3.6wt%に増加します。したがって、Ni-P-Al 2 O 3 (3.6%)複合コーティングは、638HVで最高の硬度値を示します。その理由はnano-Al 2 に由来します O 3 Ni-P合金の相構造(図3を参照)を最適化し、コーティングの微小硬度を高める粒子。ただし、Al 2 の内容 O 3 複合コーティングでは4.2wt%に達し、コーティングの微小硬度は代わりに576HVに低下します。これは、ナノ粒子の含有量が多いと、Ni-P結晶構造に影響を及ぼし、複合コーティングの性能が低下する可能性があることを意味します。
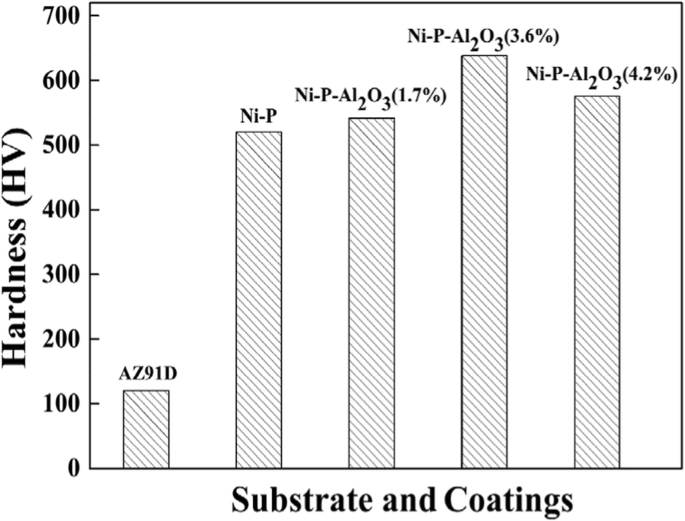
AZ91D基板、Ni-Pコーティング、およびNi-P-Al 2 の硬度 O 3 複合コーティング
コーティングとMg合金基板との間の接着は、実験セクションに従って熱衝撃試験によって実施された。 20サイクルのテストにより、Ni-PコーティングとNi-P-Al 2 O 3 複合コーティングはMg合金基板によく接着しました。試験プロセス中に亀裂、膨れ、剥離などの欠陥は観察されなかった。これは、Ni-PまたはNi-P-Al 2 O 3 コーティングは、熱衝撃プロセスに対して、Mg合金基板との良好な接着性を示しました。さらに、コーティングとMg合金基板の間の断面形態画像もSEMを使用して観察されました。図6に見られるように、熱衝撃試験により、コーティングと基板の間に明らかな欠陥がないことがさらに明らかになります。重要なことに、熱衝撃試験と断面観察は、ナノAl 2 O 3 粒子は複合コーティングの接着に影響を与えません。
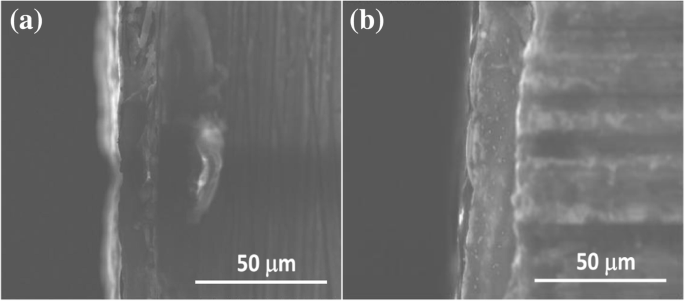
Ni-Pコーティングの断面形態画像( a )およびNi-P-Al 2 O 3 (3.6 wt%)複合コーティング( b )
本研究では、nano-Al 2 を使用した場合と使用しない場合の1Lめっき浴 O 3 粒子(10g / L)をそれぞれ調製した。ここで、めっき浴中の初期ニッケル源含有量は7.8 gと計算され、浴の耐荷重は0.5 dm 2 に設定されました。 / L。定期サイクル試験のルール(実験セクションを参照)に従って、最初に無電解Ni-Pめっき浴のMTOを評価し、約48.2gのNi-P合金が得られました。ここでは、EDS分析を使用してNi-Pコーティングで90%のニッケル含有量が特定されました(図7を参照)。したがって、コーティング中のニッケルの含有量は43.4gと計算できます。つまり、Al 2 を含まないめっき浴のMTO O 3 式を使用すると、粒子は5.6になります。 (2)。無電解Ni-P-Al 2 O 3 複合めっき浴、合計38.8 g Ni-P-Al 2 O 3 コーティングは複合浴から堆積された。同様に、86.45%Ni、9.84%P、1.96%Al、および1.75%OがEDS分析によって決定されました(図7)。したがって、複合コーティング中のニッケルの含有量は33.5 gと計算でき、複合浴のMTOは4.2です。定期サイクル試験の結果から、複合めっき浴の使用サイクルは無電解Ni-Pめっき浴の使用サイクルより1.4MTO少なくなっています。これは、nano-Al 2 O 3 粒子は無電解めっき浴の耐用年数を短縮します。それにもかかわらず、Ni-P-Al 2 O 3 複合めっきは、マグネシウム合金の分野でまだ潜在的な用途があります。
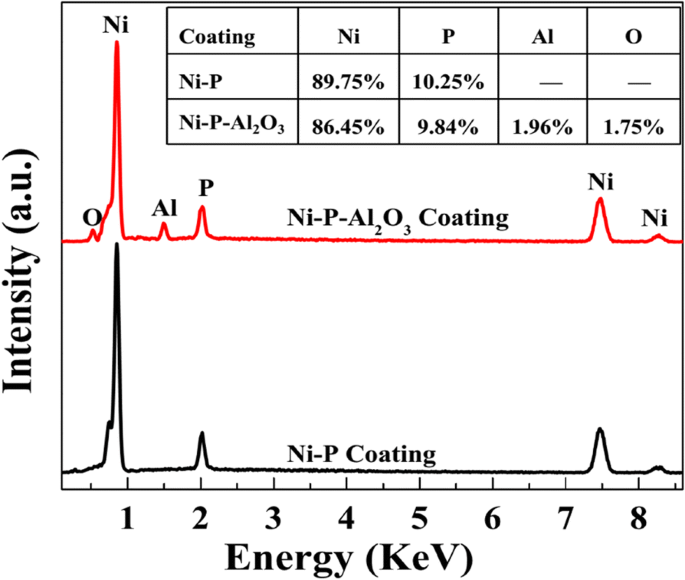
Ni-PコーティングとNi-P-Al 2 のEDSスペクトル O 3 複合コーティング
結論
要約すると、Ni-P-Al 2 を共蒸着するための無電解複合めっき浴と動作条件を取得しました。 O 3 マグネシウム合金のコーティング、つまり35 g / L NiSO 4 ⋅6H 2 O、35 g / L乳酸、30 g / L Na 2 H 2 PO 2 ⋅H 2 O、10 g / L NH 4 HF 2 、10 g / L nano-Al 2 O 3 粒子、3 mg / L安定剤、pH =6.0〜6.5、 T =85°C、350rpmでの攪拌速度。複合コーティングの形態特性評価と相構造分析により、nano-Al 2 O 3 粒子は、コーティングの成長プロセスと相構造(結晶面の間隔と粒子サイズ)に重要な影響を及ぼしました。 3.6 wt%Al 2 O 3 含有量は、Ni-Pコーティングの微小硬度と耐食性を効果的に改善しました。さらに、接着試験では、Ni-PコーティングとNi-P-Al 2 の間にほとんど違いがないことが示されました。 O 3 コーティング。耐用年数試験により、無電解複合めっき浴のMTOは約4であることが確認されました。つまり、無電解Ni-P-Al 2 O 3 複合めっきは、マグネシウム合金の用途を拡大するための重要な技術です。
略語
- E 0 :
-
開回路電位
- i corr :
-
腐食電流密度
- Mg:
-
マグネシウム
- MTO:
-
金属の売上高
- Ni-P:
-
ニッケルリン
- SEM:
-
走査型電子顕微鏡
- XRD:
-
X線回折
ナノマテリアル