AFMチップベースのナノミリングプロセス下でのポリジメチルシロキサンナノ流体チップの製造
要約
現在の研究分野では、ポリジメチルシロキサン(PDMS)ベースのナノ流体デバイスは、医療、化学、および生物学のアプリケーションで広く使用されています。本論文では、PDMSチップ上にナノチャネル(制御可能なサイズ)を作製するための新しいナノミリング技術(AFMシステムと圧電アクチュエータからなる)を提案し、圧電アクチュエータに入力される駆動電圧と周波数によってナノチャネルサイズを制御しました。 。さらに、マイクロチャネル型とナノチャネル型はそれぞれUVリソグラフィーとAFMチップベースのナノミリングによって製造され、最後に、マイクロ/ナノチャネルを備えたPDMSスラブが転写プロセスによって得られました。ナノチャネルサイズに対するPDMS重量比の影響も調査されました。マイクロチャネルとナノチャネルのスラブの結合プロセスは、光学単眼顕微鏡と精密ステージで構成される自家製のアライメントシステムで実施されました。さらに、KCl溶液(1 mMの濃度)の電気的特性に対するナノチャネルサイズの影響を分析しました。したがって、サブ100 nmの深さの複数のナノチャネルを備えたPDMSナノ流体デバイスは、提案された方法によって効率的かつ経済的に製造できると結論付けることができます。
背景
マイクロ/ナノ流体システムは、化学、医療、生物学の分野で大きな可能性を秘めているため、DNA分析[1,2,3,4]、細胞分離[5]、タンパク質研究[6,7,8]、食品安全[9]、および環境モニタリング[10]。ナノファブリケーション技術の急速な発展に伴い、1次元サイズが100nm未満のナノ流体デバイスの需要が継続的に増加しています[11]。ナノ流体チップは、ウイルス検出[12]、ナノ粒子操作[13]、およびイオン拡散の研究[14]にも効果的に使用できます。ただし、ナノ流体チップの検出効率と感度は、ナノチャネルの特徴の寸法と分布に依存します。ナノ流体ベースのラベルフリー検出には、ナノチャネルの特徴寸法を正確に制御することが不可欠です。制御可能なフィーチャの寸法と分布を備えたナノチャネルを製造する方法は、ナノ流体分野でのアプリケーションにとって依然として課題です。
これまで、ナノ流体チップの製造に利用できるいくつかの方法があります。反応性イオンエッチング[15]、従来のフォトリソグラフィー[16]、高エネルギービーム処理[17]、干渉リソグラフィー[18]、ナノインプリント[19]、およびホットエンボス技術[20、21]は、ナノ流体デバイス;ただし、これらの方法はすべて、独自の制限があります。反応性イオンエッチングと従来のフォトリソグラフィーは、マイクロ/ナノ流体チャネル製造の主流の方法です。ただし、製造されたチャネルの横方向の寸法は入射光の波長に依存するため、製造されたチャネルの幅は、ナノスケールではなくマイクロメートルスケールで見られることがよくあります[22]。その上、製造されたマイクロ/ナノ構造が異なる特徴を持っている場合、フォトマスクを変更することは不便です。集束イオンビームリソグラフィー(FIB)と電子ビームリソグラフィー(EBL)はどちらも高エネルギービーム処理法であり、サブ100nmのナノチャネルを備えた高精度のナノ流体チップを簡単に製造できます。しかし、製造設備への投資は非常に高く、厳しい環境要件が必要です[23]。干渉リソグラフィー(IL)は、広い領域にわたって単純な周期的構造を製造するのに適しています。ただし、単一のナノチャネルを加工することは適切ではありません[24、25]。ナノインプリントの処理分解能はテンプレートの特性に依存します。このアプローチの重要な問題は、高精度のナノ構造でテンプレートを製造する方法です[26]。さらに、マイクロ/ナノスケールデバイスの製造には、犠牲成形とクリークベースの方法も採用されています[27、28]。ただし、これらのアプローチでは、ナノチャネルサイズを正確に制御することは非常に困難です。したがって、ナノ流体デバイスの製造には、高い加工精度、使いやすさ、広い処理範囲、および低い環境要件の特性を備えた、より実現可能な製造アプローチが求められます。
近年、加工精度が高いため、ナノミリング、精密研削、超精密旋削などの超精密加工法がマイクロ/ナノ構造の製造に広く使用されています[29、30、31、32]。さらに、1986年に原子間力顕微鏡(AFM)が発明されて以来、AFMチップベースのナノファブリケーションはナノ構造を調製するための強力な方法です[33]。従来のチップベースのナノスクラッチには、加工幅の制限や製造効率の低さなど、いくつかの制限があります。このアプローチによって製造されたナノチャネルの幅は、AFMチップの形状に依存します。これは、アクセスできない制御可能な幅のナノチャネルを意味します。さらに、従来のチップベースのナノスクラッチプロセスの製造効率は、特に、得られたナノ構造の深さと幅を拡大するために機械加工プロセスでフィードを使用する場合、比較的低い。制御可能な加工サイズや高い製造効率などの重要な利点により、チップベースのナノミリングはナノチャネルの製造に広く採用されています。御膳他[34、35]ナノミリングプロセスにより、ポリメチルメタクリレート(PMMA)上にナノ構造を作製しました。張ら。 [36,37,38]は、AFMを使用して3次元ナノ構造を作成し、さまざまな加工パラメータの影響を研究しました。 Park etal。 [39]ナノマシニングプロセスのメカニズムを調査し、切削抵抗の強度が大幅に低下することを発見しました。しかし、提案されたシステムでは、機械加工設備が比較的複雑であることがわかり、材料除去プロセスは詳細に調査されていませんでした。駆動周波数と電圧を含む加工パラメータと得られたナノチャネルの特徴寸法との関係は研究されていません。さらに、彼らの研究は、製造されたナノチャネルの応用に焦点を合わせていませんでした。したがって、このAFMチップベースのナノミリングアプローチの適用範囲を調査するには、さらに多くの作業が必要です。ポリカーボネート(PC)は、その優れた機械加工性により、ナノファブリケーションに一般的に使用されています[40]。それにもかかわらず、ナノ流体チップを製造するために選択されることはめったにありません。対照的に、ポリジメチルシロキサン(PDMS)は、マイクロ流体およびナノ流体チップの処理に広く使用されています。マタら[41]は、引張応力に対するPDMS重量比の影響を研究しました。 Park etal。 [42]はPDMSの剛性を改善するための新しい方法を開発しました。ラベルフリーテスト分野でのナノ流体チップの用途は、主にナノチャネルの電気伝導率に依存するため[43]、測定結果はナノチャネルの寸法サイズに影響されることがよくあります[44]。
したがって、従来のチップベースのスクラッチプロセスの欠点を克服するために、この研究では、ナノミリングアプローチを使用してナノチャネルの製造プロセスを実施します。さらに、先端の摩耗を軽減し、製造コストを削減するために、実験サンプルとしてPCシートを選択しました。さらに、PCシート上のナノチャネルサイズは、圧電アクチュエータに入力される駆動電圧と周波数によって制御されました。ナノチャネルサイズに対するPDMS重量比の影響も調査されました。さらに、ナノチャネルの電気伝導率に対するさまざまな寸法サイズの影響を検証するために、現在の測定テストはKCl溶液を使用して実行されました。
メソッド
ナノミリングシステムのセットアップ
提案されたAFMチップベースのナノミリングシステムは、市販のAFM(Dimension Icon、Bruker Company、ドイツ)と圧電アクチュエータ(P-122.01、PI Company、ドイツ)で構成されていました(図1a)。圧電アクチュエータのx方向とy方向の移動範囲は1μmに制限されていました。さらに、圧電アクチュエータは、信号増幅器(PZD350A; TREK、Inc.、USA)の増幅下で、適切な電圧(市販の信号発生器デバイス(AFG1022; Tektronix、Inc.、USA)から生成)の正弦波信号によって駆動されました。自家製ホルダー(エポキシ樹脂製)に固定ネジでPCシートを固定しました。ナノマシニング操作は、厚さ100 nmの長方形のピラミッド型ダイヤモンドコーティングチップ(DT-NCLR、Nanosensors、スイス)を使用して実行されました。チップのカンチレバー(通常のばね定数68 N / m)はシリコンでできており(図1b)、シリコンチップ(半径10 nm)(TESPA、Bruker Company、ドイツ)を使用して溝を測定しました。機械加工。
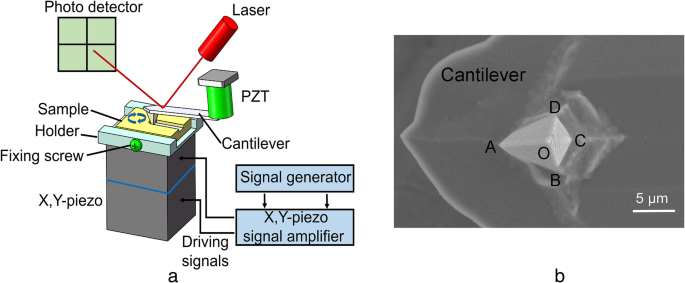
a ナノミリングシステムの概略図。 b ダイヤモンドコーティングされたAFMチップのSEM顕微鏡写真
ナノチャネルおよびマイクロチャネルモールドの製造
PDMSチップ上でのナノチャネルの製造ルートを図2に示します。AFMシステムと圧電アクチュエータを使用して、PCシート上に(制御可能なサイズの)ナノチャネル型を製造しました。 15mm×12mm×1mmサイズのPCシート(分子量35,000)はGoodfellowから購入しました。 PCシートの表面粗さ(Ra)の平均と標準偏差は、それぞれ0.6nmと0.2nmと測定されました(これらの値は、AFMタッピングモードでサンプルの50μm×50μmの領域をスキャンすることによって得られました)。円運動を生成するために、圧電アクチュエータは、x方向とy方向に90°の位相差を持つ正弦波信号によって駆動されました。機械加工されたナノチャネルの幅は、生成された円運動の振幅に依存していました。圧電アクチュエータに入力する駆動電圧の範囲は、30Vから150Vまで30V間隔で設定し、さらに100Hzと1500Hzの2つの潜水周波数を選択しました。エッジフォワード方向に沿った機械加工中に、材料はパイルアップ形成で排出され、ナノチャネルの両側に均一に分布していることがよくあります[45]。これは、ボンディングプロセス中のナノ流体チップの漏れを防ぐのに役立ちます。そのため、本研究ではエッジフォワード加工方向を選択しました。長さ80μmのナノチャネルは、AFMシステムのNanomanモジュールを使用して製造されました。すべての機械加工プロセスは、送り値の影響を受けます。したがって、この影響を排除するために、送り速度は駆動周波数に応じて変化させる必要があります。本研究では、送り値を10 nmに設定し、100Hzと1500Hzの周波数の送り速度をそれぞれ1μm/ sと15μm/ sと計算しました。チップの通常の負荷は、位置敏感光検出器(PSD)から生成される出力電圧に依存していました。したがって、私たちの研究で使用されたさまざまな通常の負荷は、相対電圧(設定値)を設定することによって達成されました。以前の研究[46]によると、機械加工の通常荷重は式(1)によって計算されました。 (1)得られた力-距離曲線の傾きから感度を測定した[47]。
$$ {F} _ {\ mathrm {N}} ={V} _ {\ mathrm {setpoint}} \ timessensitive \ times {K} _ {\ mathrm {N}} $$(1)<図> <画像>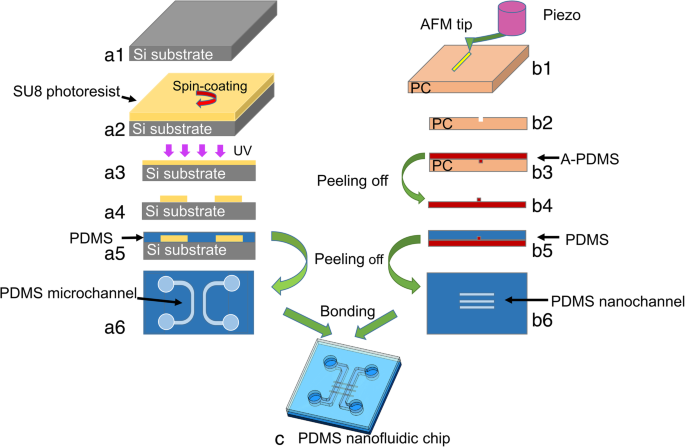
ナノ流体チップ製造のフローチャート:(a1)–(a6)PDMSチップ上でのマイクロチャネル製造の作業ステップ。 (a1)リソグラフィ基板に使用されるシリコンシート。 (a2)Si基板へのSU8フォトレジストのスピンコーティング。 (a3)SU8層のUV光への曝露。 (a4)得られた凸状の微細構造; (a5)マイクロチャネルモールド上のPDMSコーティング。 (a6)マイクロチャネルを備えた最終的なPDMSチップ。 (b1)–(b2)PDMSチップ上でのナノチャネル製造の作業ステップ。 (b1)PCシートのAFMチップスクラッチ。 (b2)引っかいた後に得られたナノチャネル型。 (b3)ナノチャネルモールド上のA-PDMSコーティング。 (b4)凸状ナノ構造のA-PDMSチップ。 (b5)A-PDMSモールド上の通常のPDMSコーティング。 (b6)ナノチャネルを備えた最終的なPDMSチップ。 (c)結合後のPDMSナノ流体チップ
したがって、ナノミリングプロセスの通常の負荷は17μNと25μNに設定されました。さらに、比較のために、PCシート上のナノチャネルモールドも振動なしで製造されました。この方法はシングルスクラッチと呼ばれます。シングルスクラッチプロセスの通常の負荷は、25μN、33μN、42μN、50μN、および58μNに設定されました。ナノチャネルモールド断面の概略図を図2(b2)に示します。
マイクロチャネル型は、UVリソグラフィープロセスによって準備されました。図2(a1–a4)のフローチャートは、リソグラフィープロセスの操作の詳細を示しています。フォトレジスト(SU-82015; MicroChem、USA)は、Si基板上に500 rpsで30秒間、4000rpsで120秒間スピンコーティングされました。一対の「U」字型マイクロチャネルがマイクロチャネルチップを形成し(図2(a6))、これをナノチャネルでブリッジして最終的なナノ流体チップを形成しました。マイクロチャネルの幅は30μm、リザーバーの直径は1mmでした。さらに、2つの「U」字型マイクロチャネル間の距離は50μmでした(追加ファイル1:図S1およびS2)。
マイクロチャネルとナノチャネルの転写印刷
凸型マイクロチャネル型(図2(a4))と凹型ナノチャネル型(図2(b2))をPDMS(Sylgard 184、Dow Corining、USA)で転写し、最終的なナノ流体チップを作成しました。図2(b3)–(b6)は、ナノチャネルモールドトランスファーの技術プロセスを示しています。これは、最初のトランスファーと2番目のトランスファーの2つのステップで構成されています。ナノチャネルサイズに対するモノマーと硬化剤の重量比の影響を調査するために、3つの異なるPDMS重量比(A-PDMS)を第1および第2の転写プロセスの両方で使用しました。最初の転写印刷プロセスのPDMS重量比は、9:1、7:1、および5:1に設定されましたが、2番目の転写の値は10:1、9:1、および8:1に設定されました。図2(a5)および(a6)は、ワンステップ移送アプローチを使用したマイクロチャネル金型の移送プロセスを示しています。 10:1のPDMS重量比は、凸状マイクロチャネルの転送に使用されました。すべての転写印刷プロセス中に、2成分PDMSエラストマーを最初に均一に攪拌し、次にケースに注いで型を準備しました。次に、ケースを真空デシケーターに30分間保持し、2〜3回脱気して、閉じ込められた気泡をすべて除去しました。準備した型を80°Cの加熱オーブンで4時間保持し、最後にPDMSレプリカを型から静かに剥がしました。
チップボンディング
準備されたナノ流体チップは、酸素プラズマ処理(Zepto、Diener electronic、Germany)によって、1.5mbarのチャンバー圧力と81Wのチャンバー電力の下で32秒間結合されました(図2(c))。マイクロチャネルとナノチャネルの表面はスコッチテープで洗浄され、PDMSマイクロチャネルチップ上の4つのリザーバーは接着前に打ち抜かれました。プラズマ処理後のチップをきれいに保つために脱イオン水を使用し、ホルダー、単眼顕微鏡、および一次元精密ステージ(TSDT-401S; SIGMAKOKI、日本)で構成される自家製のアライメントシステムを使用してチップを整列させました。 )(図3a)。自家製のアライメントシステムの詳細は、ESIに記載されています。次に、密閉されたマイクロ/ナノチャネルチップを得るために、チップを95°Cの温度で20分間結合しました(図3b)。
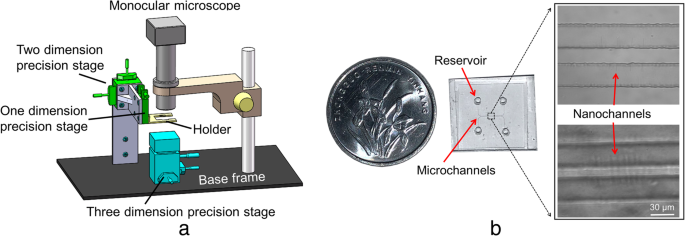
a 自家製アライメントシステムと b の概略図 ナノ流体チップ
結果と考察
圧電アクチュエータの回転軌道
二次元圧電アクチュエータは、AFMチップベースのナノミリングシステムで回転運動を行うための重要なコンポーネントです。したがって、ある範囲の駆動電圧および周波数の下でのその動きを特徴づけるために、予備的な引っかき試験が実施された。スキャン範囲が0nmの接触モデルでは、AFMチップは、特定の通常の負荷の下で最初にPCシートの表面に近づき、静止状態に保たれました。二次元圧電アクチュエータの回転は、事前に設定された周波数と電圧によって制御されました。スクラッチ処理が完了した後、AFMチップをPCシートの表面から持ち上げました。したがって、圧電アクチュエータの運動振幅は、駆動電圧および周波数の関数として得られた。駆動電圧は30〜150 Vの範囲で30 Vの間隔で設定され、駆動周波数は100Hzと1500Hzに設定されました。 2つの駆動周波数で測定された振幅と駆動電圧の関係は、追加ファイル1:図S3に表示されます。駆動電圧の上昇に伴い加工振幅の値が大きくなり、1500Hzでの加工振幅の値が100Hzよりも大きかったことがわかります。提案した方法で作製したナノチャネルの幅は350nmから690nmの範囲であることがわかった。
PCシート上でのナノチャネルモールドの製造
シングルスクラッチおよびナノミリングでのナノチャネルサイズと加工パラメータの関係を、それぞれ図4aおよびbに示します。機械加工されたナノチャネルの幅と深さは、 W で表されます。 0 および D 0 、それぞれ(図5a)。
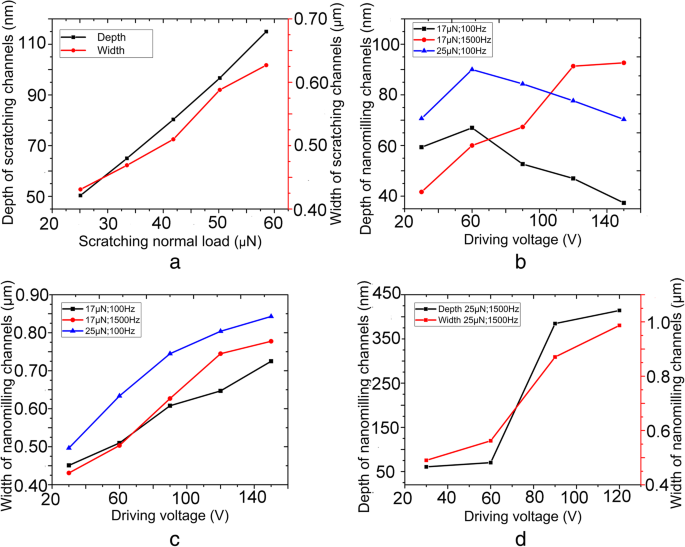
加工されたナノチャネルサイズと加工パラメータの関係: a 通常の負荷でのシングルスクラッチの範囲は25μNから58μN、 b 深さ、および c 17μN、25μNの通常の負荷と100 Hz、150 Hz、 d の駆動周波数で製造された場合の機械加工されたチャネルの幅 25μNの通常の負荷と1500Hzの駆動周波数で製造された場合の機械加工されたチャネルの深さと幅
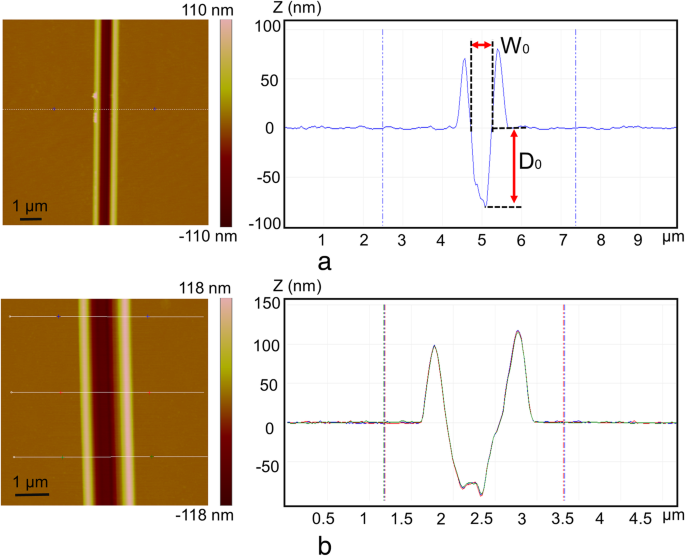
さまざまな加工パラメータで加工されたナノチャネルの典型的なAFM画像: a 42μNの通常の負荷の下での引っかき傷。 b 25μNの通常の負荷、100 Hzの周波数、および60Vの駆動電圧の下でのナノミリング
図4aから、製造されたナノチャネルの幅と深さが通常の負荷の増加とともに増加したことが観察できます。 42μNの通常の負荷の下での引っかき傷の典型的なAFM画像を図5aに示します。材料がナノチャネルから排出されてパイルアップを形成し、それがナノチャネルの両側に均一に分布していることが注目に値します。 AFMチップの形状は、機械加工プロセス中にエッジ「OA」によって形成された表面に対して対称であるためです(図1b)。したがって、材料は、エッジフォワードスクラッチ中にチップの前端によって均一に排出されました。図4b、c、およびdは、機械加工されたナノチャネルサイズと駆動電圧の関係を示しています。図4bから明らかなように、ナノチャネルの深さは最初に増加し、その後、17μNと25μNの通常の負荷で100Hzの周波数で減少し始めました。私たちの研究で使用されたPCシートは、高ひずみレベルでの指数関数的なひずみ硬化の組み合わせで弾性-粘塑性挙動を示すアモルファスポリマーでした[48、49]。加工中の通常の荷重は、式(1)によって計算されました。 (2)ここで、\(\ overrightarrow {n} \)と\(\ overrightarrow {t} \)は、それぞれ法線の単位と動線ベクトルに接する単位です。 p およびτ それぞれ局所的な法線圧力とせん断応力を意味し、\(\ overrightarrow {z} \)は垂直方向の単位です[50]。
$$ {F} _ {\ mathrm {N}} =p \ cdot \ int \ overrightarrow {n} \ cdot \ overrightarrow {z} ds- \ tau \ cdot \ int \ overrightarrow {t} \ cdot \ overrightarrow {zds } $$(2)本研究では、製造されたナノチャネルの寸法サイズがナノスケールで見出されたため、局所的な法線圧力とせん断応力の値は一定であると仮定されました。さらに、式。 (2)式の簡略化された形式に変換されました。 (3)、ここで S n および S h それぞれ、AFMチップとサンプル間のインターフェースの水平方向と垂直方向の投影です。
$$ {F} _ {\ mathrm {N}} =p \ cdot {S} _n- \ tau \ cdot {S} _h $$(3)S 間の関係 n および S h 式で表されます。 (4)、ここでα およびβ それぞれ、先端表面と垂直面および水平面の間に含まれる角度です。
$$ {S} _ {\ mathrm {n}} =\ frac {S _ {\ mathrm {h}}} {\ cos \ alpha} \ cdot \ cos \ beta $$(4)通常の負荷は、式(1)によって計算されました。 (5)。
$$ {F} _ {\ mathrm {N}} =\ left(p \ cdot \ frac {\ cos \ beta} {\ cos \ alpha}-\ tau \ right)\ cdot {S} _h $$(5 )。それは式から明らかです。 (1)通常の荷重の値は機械加工プロセス全体を通して一定でした。 Briscoeらによると。 [51]、平均ひずみ速度の値は式(51)によって計算されました。 (6)、ここで V および w それぞれ、チップ速度とノーカットチップの厚さを示します。未切断の切りくずの厚さの最大値は〜10nmであることがわかりました。
$$ {} _ {\ varepsilon} ^ {\ bullet} =\ frac {\ mathrm {d} \ varepsilon} {\ mathrm {d} t} \ approx \ frac {V} {w} $$(6)また、先端速度の値は式(1)から得られました。 (7)、ここで f は入力信号周波数です。
$$ V =\ pi \ cdot {W} _o \ cdot f $$(7)100Hzでの平均ひずみ速度の値は1.42×10 4 の範囲で見つかりました。 s -1 〜2.27×10 4 s -1 。局所常圧の値( p )ひずみ速度が1.42×10 4 の範囲になると、ひずみ速度の増加とともに上昇し始めました。 s -1 〜2.27×10 4 s -1 [52]。 τの値 p よりもはるかに小さかった 、通常の負荷が主に p に依存していることを意味します 。したがって、通常の負荷の値を維持するために(F N )加工プロセス全体で一定であるため、駆動電圧が高くなると加工深さの値は小さくなります。ただし、製造されたナノチャネルの最終的な寸法サイズは、サンプル材料の回収率の影響を受けました。サンプルの回復は、142〜227μm / sの範囲で加工速度の増加とともに減少しました[53]。したがって、30 Vでより高い弾性回復が発生したことを示しています。その結果、30Vで製造されたナノチャネルの深さ(〜142μm / s)は60 V(〜161μm / s)よりも浅かった。追加ファイル1:図S4(a)と図5bは、それぞれ17μNと25μNの通常の負荷の下で100Hzで加工されたナノチャネルの典型的なAFM画像です。ナノチャネルの右側のパイルアップが左側よりも大きいことは明らかです。ナノミリングプロセス中のサンプルの回転運動は反時計回りであり、主刃先の切断角度は回転に伴って変化します。未切断の切りくずの厚さは、ナノミリングプロセスのサイクルの開始時と終了時に切りくずを形成するには薄すぎます。ナノミリングプロセスのサイクルの途中での未切断のチップの厚さは比較的大きいです。ただし、迎え角が小さいと、パイルアップが形成されます。したがって、より多くの材料がチャネルの右側に押し出され、パイルアップは非対称になります。 非対称パイルアップの形成の詳細は、以前の研究[54]に記載されています。
図4bおよびdから、17μNおよび25μNの通常の負荷の下で、1500Hzでの駆動電圧の増加に伴ってナノチャネルの深さが増加し始めたことが観察できます。図4dは、25μNの通常の負荷の下で、ナノチャネルの深さが60 V(〜2.64 mm / s)から90 V(〜4.10 mm / s)に急激に増加したことを示しています。ゲンらによると。 [55]、材料の除去状態は切削速度に大きく影響されます。材料は、2.64 mm / sの速度で機械加工中にパイルアップ形式でナノチャネルから排出されましたが、材料の除去状態は、4.10 mm / sでパイルアップからチップに変更されました(追加ファイル1:図S4(b)) 。したがって、90 V(〜4.10 mm / s)での加工深さの増加は、材料除去状態の変化に起因する可能性があります。製造されたナノチャネルの幅は、駆動電圧の増加とともに増加し始めた。図6は、ナノミリング中のAFMチップの軌道の概略図を示しています。破線の楕円、黒い実線の楕円、青い矢印は、それぞれ、完成した加工プロセス、進行中の加工プロセス、およびAFMチップの移動方向を表しています。幅( W 2 図6(b)の加工チャンネルの)はそれ( W )よりも大きかった 1 )図6(a)。 AS 1 およびAS 2 (赤い実線)は、AFMチップの断面とサンプル材料の間の接触長さを表します。 AS 1 の値 AS 2 よりも大きいことがわかりました 加工幅「 L 1 」は「 L 」と同じでした 2。 」
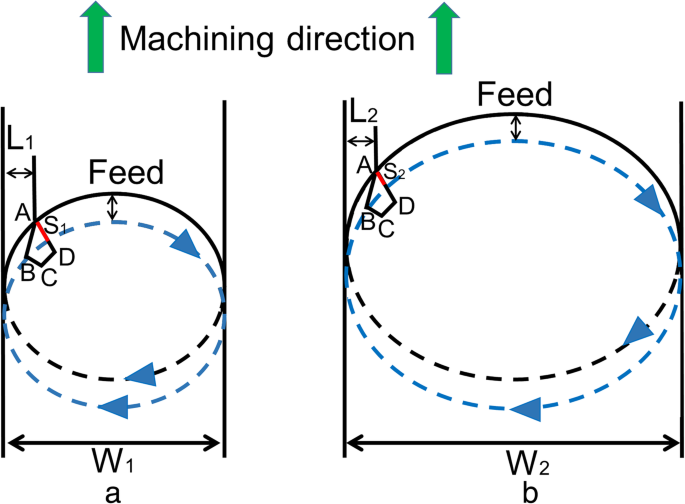
ナノミリングプロセス中のAFMチップ軌道の概略図:ナノチャネルの機械加工幅( a )はナノチャネルよりも小さい( b )、破線の楕円、黒い実線の楕円、青い矢印は、それぞれ、完成した加工プロセス、進行中の加工プロセス、およびAFMチップの移動方向を表しています。
S h の値 式で。 (5)は式(5)によって得られました。 (8)ここで、DとASはそれぞれ、機械加工されたチャネルの深さと、AFMチップの断面とサンプル材料の間の接触長さです。
$$ {S} _h =\ frac {1} {2} \ cdot \ left | D \ left | \ cdot \ right | \; AS \ right | $$(8)したがって、式。 (5)はさらに式(5)の形に書き直されました。 (9)。
$$ {F} _ {\ mathrm {N}} =\ frac {1} {2} \ cdot \ left(p \ cdot \ frac {\ cos \ beta} {\ cos \ alpha}-\ tau \ right) \ cdot \ left | D \ left | \ cdot \ right | AS \ right | $$(9)αの値 およびβ 機械加工プロセス全体を通して一定に保たれました。 1500Hzでのひずみ速度の値は2.03×10 5 の範囲で見つかりました。 〜3.66×10 5 s -1 ;したがって、局所的な常圧( p )1500Hzで限界値に達しました。さらに、加工速度は、30〜150 V(〜2.03〜3.66 mm / s)での加工中のサンプルの回収率に影響を与えませんでした[53]。したがって、ナノチャネルの最終的な寸法サイズは、機械加工の寸法によってのみ決定されました。 AS 2 の値 (図6(b))はAS 1 よりも小さいことがわかりました。 (図6(a))より大きな機械加工幅の場合、および式(1)に従って。 (9)、ASの値が小さいほど、Dの値は大きくなります。したがって、加工深さの値は、駆動電圧の増加とともに増加しました。 25μNの通常の負荷、120 Vの駆動電圧、1500Hzの周波数で製造されたナノチャネルの典型的なAFM画像は、追加ファイル1:図S4(b)に示されています。チップとパイルアップの両方の形成で材料が除去され、排出された材料がナノチャネルの片側にのみ蓄積したことが注目されます。さらに、放出された材料は、25μNの通常の負荷の下で150Vでの機械加工中にナノチャネルの底にチップ形成で蓄積しました。したがって、150Vの電圧と1500Hzの周波数(25μNの通常の負荷の下で)での機械加工中に製造されたナノチャネルのサイズデータは、図4dでは空でした。
図4cから、駆動電圧の増加に伴ってナノチャネル幅が増加し始めたことが明らかです。さらに、通常の負荷と駆動電圧の値を一定に保つと、1500Hzの周波数で製造されたナノチャネルの幅は100Hzの幅よりも広くなりました。また、1500Hzで作製したナノチャネルの加工深さは100Hzよりも深く、より深いナノチャネルの加工では先端の断面サイズが大きくなることがわかりました。したがって、より深く加工すると、ナノチャネルはより広く製造されました。
ナノチャネルモールドの最初の転送
25μN、33μN、41μN、50μN、および58μNの通常の負荷の下でシングルスクラッチ法によって機械加工されたナノチャネルは、最初の転送プロセスに適用されました。さらに、30〜150 Vの駆動電圧範囲(30 Vの間隔)で100Hzの周波数でナノミリングによって製造されたナノチャネルモールドも、転送プロセスで使用されました。シングルスクラッチ法で加工されたナノチャネル(深さ80nm、幅510nm)を「ナノチャネルI」と呼び、ナノミリングで作製したナノチャネル(深さ50nm、幅610nm、深さ90nm、幅630nm)を「ナノチャネル」と呼びました。それぞれ「II」と「ナノチャネルIII」。最初の転送プロセスでは、3つの異なるPDMS重量比(5:1、7:1、および9:1)が使用されました。
図7aおよびbは、25μNの通常の負荷と100Hzの周波数での壁サイズに対するさまざまなPDMS重量比の影響を示しています。黒い破線は、転送前の元のナノチャネルサイズを表しています。ナノチャネルIIIから最初の転写中に5:1の重量比で得られた壁の典型的なAFM画像と対応する断面を図7cとdに示し、この壁を「壁III」と呼びました。 17μNの通常の負荷と100Hzの周波数での単一の引っかきプロセスの下での壁サイズに対する異なるPDMS重量比の影響がESIに示されました(追加ファイル1:ESIの図S5、S6、S7、およびS8を参照)詳細については)。 「ナノチャネルI」および「ナノチャネルII」から得られた壁は、それぞれ「壁I」および「壁II」と呼ばれた。異なるPDMS重量比でのすべての壁の高さがほぼ同じであったことは明らかです。壁の幅は元のナノチャネルの幅よりも大きく、5:1の重量比での幅が最大であることがわかりました。 PCシートの熱膨張により、最終的な壁のサイズと元のナノチャネルのサイズの間にわずかな偏差が見られました。 PDMSの重量比が5:1から7:1に減少するにつれてPDMSの弾性が増加することも観察されました[41、42]。したがって、5:1の重量比で得られた壁はより剛性が高く、その弾性回復は小さかった。したがって、5:1の重量比で得られた壁の幅が最大でした。
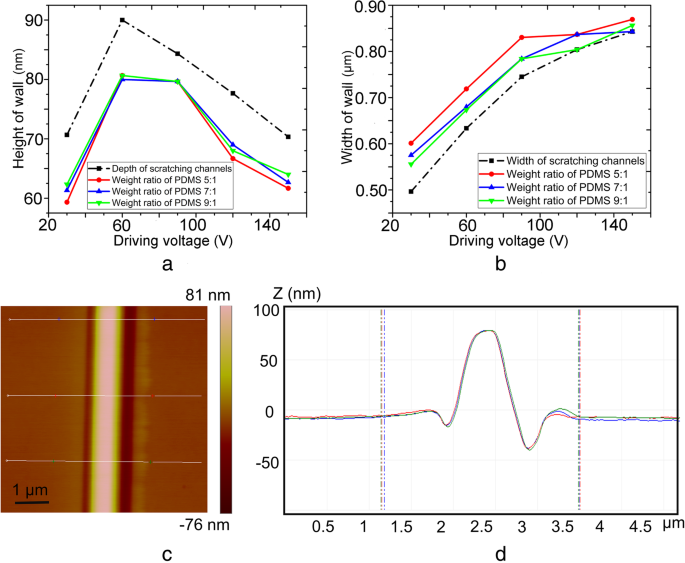
a 間の関係 壁の高さ、 b チャネルモールドが25μNの通常の負荷と100Hzの周波数で製造された最初の転送プロセス中の壁の幅と転送パラメータ(PDMSのさまざまな重量比)、および c 典型的なAFM画像と d 5:1の重量比でナノチャネルIIIから得られた壁の対応する断面
ナノチャネルモールドの2回目の転送
ナノチャネルを備えた最終的なPDMSスラブは、最初の移送プロセスで5:1の重量比で得られた壁に基づいて、2番目の移送プロセス中に得られました。 3つの異なるPDMS重量比(10:1、9:1、および8:1)が、2番目の転送プロセス中に使用されました。図8aおよびbは、25μNの通常の負荷と100Hzの周波数で得られたナノチャネルサイズと、2回目の転送中の転送パラメータとの関係を示しています。図8aから明らかなように、ナノチャネルの深さは元の加工サイズよりも大きく、さらに、10:1での深さは他の2つの比率よりも大きいことがわかりました。また、壁の幅も元のサイズより大きく、10:1の幅が最も大きいことがわかりました(図8b)。図8cおよびdは、典型的なAFM画像と、2回目の転写中に10:1の重量比で壁IIIから得られたナノチャネル(深さ120nmおよび幅690nm)の対応する断面を示しています。これは「ナノチャネルC」と呼ばれます。 。」 25μNの通常の負荷と100Hzの周波数での単一の引っかきプロセスの下で得られたナノチャネルサイズと2番目の転送プロセス中の転送パラメータとの関係がESIに示されました(追加ファイル1:図S9、S10、S11を参照)詳細についてはESIのS12)、「壁I」と「壁II」から得られたナノチャネルは、それぞれ「ナノチャネルA」と「ナノチャネルB」と呼ばれていました。
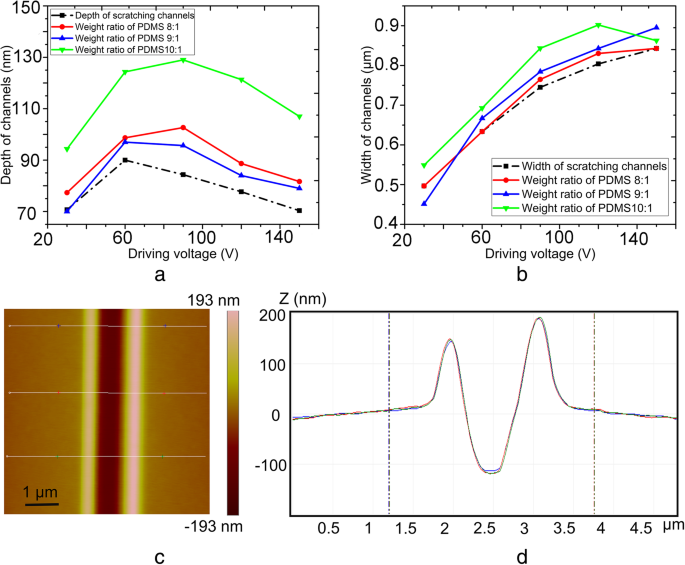
a 間の関係 ナノチャネルの高さ、 b ナノチャネル幅、および2回目の転送中の転送パラメータ(PDMSのさまざまな重量比)。チャネルモールドは、25μNの通常の負荷と100Hzの周波数、および c で製造されました。 典型的なAFM画像と d 2回目の転送中に10:1の重量比で壁IIIから得られたナノチャネルの対応する断面
壁IIおよびIIIから得られたナノチャネルの深さは、元の加工サイズよりも大きかったのに対し、壁Iから得られた深さは、初期の加工サイズよりも小さかった。さらに、幅の変化は深さの変化と同じでした。壁Iのアスペクト比は壁IIおよびIIIのアスペクト比よりも大きかったため、各壁は異なる熱膨張値を示しました。したがって、2回目の転送中の幅と深さの変化する傾向は、同じPDMS重量比ではありますが異なっていました。 9:1と8:1での壁IIとIIIの深さと幅の値は、10:1と比較して元の加工サイズに近いことがわかりました。 9:1および8:1でのPDMSの弾性回復は10:1よりも5:1に近いため、これは9:1、8:1、および5:1でのPDMSの回復傾向がほぼ同じであることを示しています。
>電流測定におけるナノチャネルデバイスの応用
ナノチャネルデバイスは、単一ナノ粒子操作、動電学的輸送現象、DNA分析、および酵素反応検出の分野でよく使用されます。ナノ流体チップの主な動作原理は、電流の変動に依存します。したがって、ナノチャネルデバイスの導電率を測定することが重要です。ナノチャネルの電気コンダクタンスは、式(1)で見積もることができます。 (10)[56]。
$$ G ={10} ^ 3N \; {} _ Ae \ frac {wh} {l} \ sum {\ mu} _i {c} _i + 2 {\ mu} _e \ frac {w} {l} {\ delta} _n $$(10)ここでμ i はイオンの移動度です i 、 c i はイオンの濃度です i 、δ n はナノチャネル内の有効表面電荷であり、N A および e w に加えて、アボガドロ定数と電子電荷を意味します 、 h および l それぞれ、ナノチャネルの幅、高さ、長さです。ナノチャネルの電気コンダクタンスは、ナノチャネルの特徴の寸法と溶液濃度の影響を受けることは明らかです。電気二重層(EDL)は、DELの厚さとナノチャネルの高さの比率が大きくなると、ナノチャネルで重要な役割を果たします。 EDLの拡散層の厚さは、デバイ長(λ)の3〜5倍です。 D )、これは式で表すことができます。 (11)[57]。
$$ {\ lambda} _D =\ sqrt {\ frac {\ varepsilon_0 {\ varepsilon} _r {k} _bT} {2 {n} _ {i \ infty} {(ze)} ^ 2}} $$(11 )。ここで n i ∞ 溶液中のイオン密度εを示します o は真空の誘電率、ε r は電解液の誘電率 z は緩衝液の原子価です( z = z + − z − =1(KClの場合)、およびk b および T はそれぞれボルツマン定数と温度です。本研究では、転写プロセスの完了後に3つの異なるナノ流体チップが得られました。ナノチャネルA、B、およびCで構成されるナノ流体チップは、それぞれナノ流体チップA、B、およびCと呼ばれていました。各ナノ流体チップには、4つのナノチャネルが含まれていました。ナノ流体チップA、B、およびCの幅と深さは、それぞれ60nmと500nm、80nmと680nm、120nmと690nmと測定されました。すべてのチップのナノチャネルの有効長は50μmと計算されました。図8に示すように、パイルアップはナノチャネルA、B、およびCの側面に分布します。パイルアップはナノチャネルに充填され、ナノ流体チップの準備に失敗する可能性があります。そこで、作製したナノチャネルデバイスの信頼性を検証するために、電気伝導率測定試験を実施しました。濃度1mMのKClを本研究の電解液とし、電流値を電位計(Model 6430、Keithley、USA)で測定しました。マイクロチャネルとナノチャネルの電流測定の概略スケッチは、それぞれ図9aとbの挿入図として示されています。実験は、DC電力(Ag電極によって適用される)の下で、2Vの増分で3秒間実行されました。図9aは、測定された I を示しています。 - V 3つの異なるナノ流体チップのマイクロチャネルの曲線、および電流と電圧の間の線形関係が観察されました。さらに、マイクロチャネルでのEDLの影響はごくわずかであり、異なるナノ流体デバイスでのマイクロチャネルの寸法サイズは同じであったため、異なるチップでの電流の値はほぼ同じでした。図9bから明らかなように、異なるナノ流体デバイスの電流値は、異なるナノチャネルサイズのために異なっていました。 1 mM濃度のKCl溶液の場合、λの値 D は約10nmであったため、EDLの拡散層の厚さは30〜50nmであることがわかりました[57]。その結果、EDLはナノ流体チップAの深さ(60 nm)に沿って重なりました。ただし、ナノ流体チップC(深さ120 nm)ではオーバーラップは観察されませんでした。ただし、ナノ流体チップB(深さ80 nm)でEDLがオーバーラップしているかどうかを判断することは困難でした。実効表面電荷(δ n )表面の電荷密度は材料特性であるため、すべてのナノチャネルで同一です[58、59]。ナノチャネル内のイオン濃度はEDLフィールドに依存し、EDLフィールドが強いほど、ナノチャネル内のイオン濃度が高くなります[44]。本研究では、ナノ流体チップAのEDLフィールドは、ナノチャネルの高さに対するDELの厚さの比率が最も高いため、最も強くなります。これは、ナノ流体チップAのナノチャネルのイオン濃度が最も高いことを意味します。式によると。 (10)、ナノ流体チップAのナノチャネルは、イオン濃度が高いため、導電性が高くなります。したがって、ナノ流体チップAの電流値が最大であったのに対し、ナノ流体チップCの電流値は最小でした。さらに、より大きな幅のサイズでは、EDLはナノチャネルの幅方向に沿って重なりませんでした。ナノ流体チップBでは、印加電界の値が25 V未満の場合、電流と印加電圧の間に線形関係が見られました。しかし、印加電圧の値が増加すると制限領域が現れ、最終的に電界がさらに増加すると再びライナーになり、この現象はオーム制限-過制限電流特性に属します[60、61]。電流測定の結果、提案手法で作製したナノ流体デバイスが有効であり、ナノチャネルA、B、Cのパイルアップがナノ流体デバイスの性能にほとんど影響を与えないことが明らかになりました。
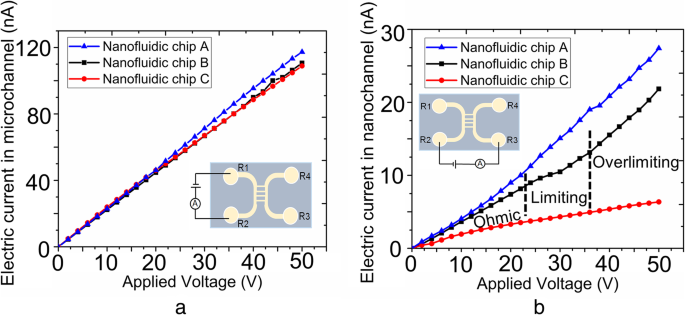
作製したナノチャネルデバイスに基づく電流測定結果は、ナノ流体チップA、B、Cのナノチャネルの断面サイズ(深さ×幅)がそれぞれ60×500 nm、80×680 nm、120×690nmです。 a マイクロチャネルの電流。 b ナノチャネルの電流。挿入図は、測定値の概略スケッチを示しています
結論
本研究では、制御可能なサイズ(サブ100 nmの深さ)のナノチャネルをAFMチップベースのナノミリングによって製造し、機械加工されたナノチャネルを初めて適用してナノ流体デバイスを作成しました。マルチチャネルナノ流体デバイスは、(1)AFMチップと圧電アクチュエータによるナノチャネルの製造、(2)リソグラフィによるマイクロチャネルの製造、(3)マイクロチャネルとナノチャネルの転送、および(iv)ボンディングの4つのステップで準備されました。さらに、アクチュエータに入力される駆動電圧と周波数を変更することにより、ナノチャネルのサイズを制御しました。最初の転写で得られた壁の高さは元の加工サイズよりも小さかったのに対し、幅は元の加工サイズよりも大きかった。実験結果は、2番目の転送プロセス中に、ナノチャネルサイズがPDMSの重量比に影響を与えることを明らかにしました。最後に、PDMSマイクロチャネルチップ上にPDMSナノチャネルチップを結合することにより、3つの異なるナノチャネルサイズのマイクロナノ流体チップが得られました。また、作製したナノ流体チップについて電流測定実験を行ったところ、電流値がナノチャネルサイズの影響を受けることがわかった。したがって、サブ100 nmの深さの複数のナノチャネルを備えたPDMSナノ流体デバイスは、提案された方法によって効率的かつ経済的に製造することができます。
他の製造アプローチと比較して、研究で提案されたナノ流体デバイスの製造方法は、使いやすく、低コストです。その上、制御可能な寸法サイズのナノチャネルを簡単に得ることができます。しかし、市販のAFMシステムは、空間的な制限のため、大規模で高精度のステージを装備することはできません。したがって、ナノチャネルの最大製造長は80μmに制限されます。また、加工速度が速いため、長期間の加工後のチップ摩耗は無視できません。今後の作業で検討する必要があります。
略語
- AFM:
-
原子間力顕微鏡
- DC:
-
直流
- EDL:
-
電気二重層
- KCL:
-
塩化カリウム
- PC:
-
ポリカーボネート
- PDMS:
-
ポリジメチルシロキサン
- PSD:
-
位置に敏感な光検出器
ナノマテリアル