航空宇宙における熱可塑性複合材料の加速
連続繊維強化熱可塑性複合材料(TPC)は、持続可能な航空機の将来を可能にする技術として挙げられており、穴や留め具なしで経済的な溶接アセンブリに接合できる軽量で高靭性の部品の生産率を向上させます。
>
CW 2018年にTPCテープ、現場での圧密および溶接に関する一連の記事を公開し、2019年に自動車用途のTPCおよび航空宇宙向けのTPC開発に関する2つのウェビナーを発表しました。 私ののほとんど これまでの記事やプレゼンテーションでは、ヨーロッパのTPC部品メーカーと機器サプライヤー、および米国のトレレボリの自動ダイナミクス部門を参照しています。また、米国を拠点とするTri-MackPlasticsのツアーも行いました。しかし、残念ながら、私はここ米国にある別のTPC部品メーカーを見落としていました。このメーカーは、15年間、技術と生産の限界を静かに推し進めてきました。ワシントン州スポケーンのすぐ外にあるアイダホ州ポストフォールズにあるATCManufacturingは、年間100万個の部品を生産しており、すべて連続繊維強化熱可塑性プラスチックであり、すべて航空宇宙産業向けです。 ATCは、3D部品の迅速な成形に関する独自の専門知識を開発しており、ボーイング社(米国イリノイ州シカゴ)および国防高等研究計画局とのRApid高性能成形(RAPM)研究プログラムの主要パートナーでもあります。 (DARPA、アーリントン、バージニア州、米国)米国国防総省(DoD)。
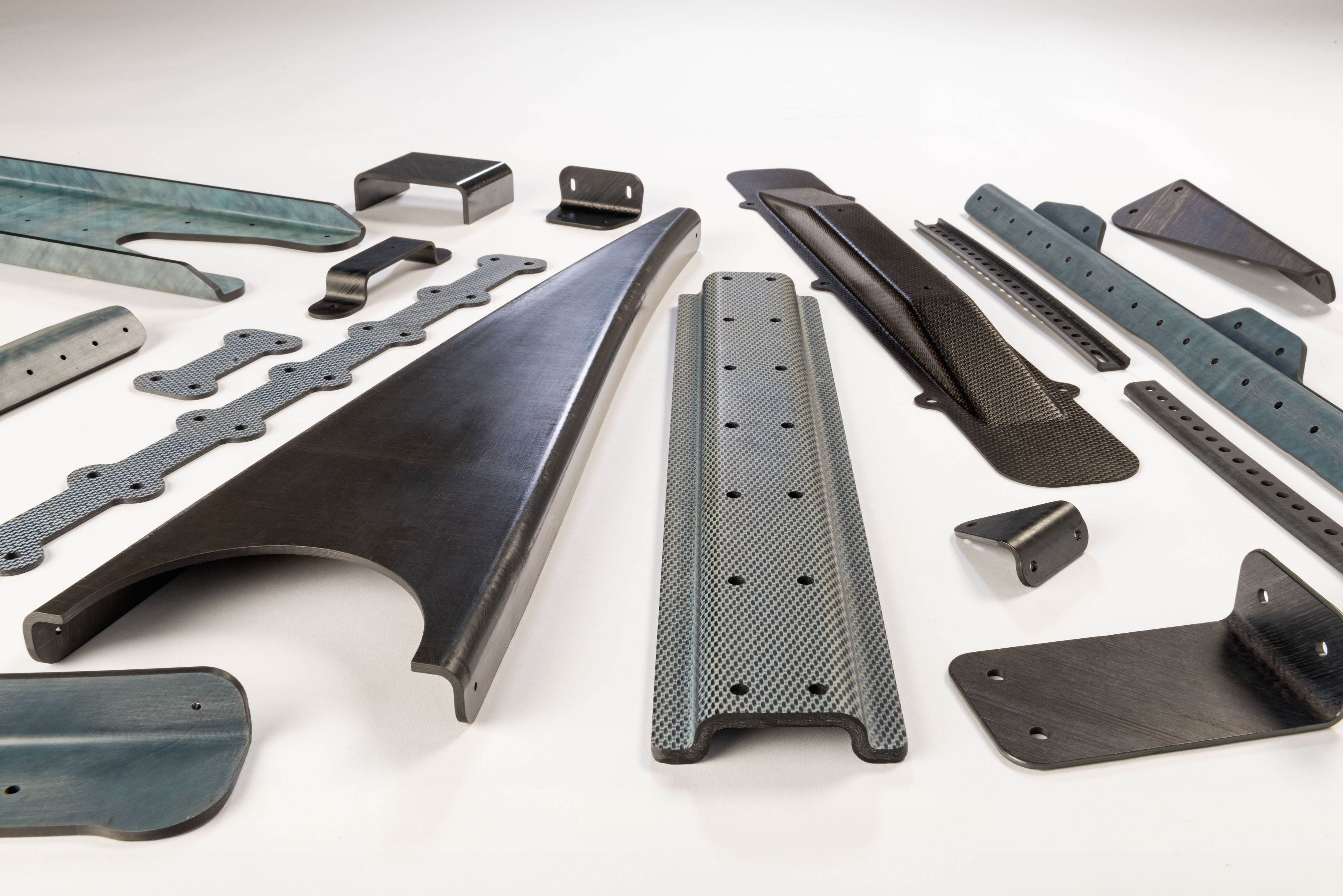
ATC Manufacturingは、リブ、クリップ、ブラケット、補強材など、航空宇宙用途向けに年間100万個の熱可塑性複合部品を製造しています。ソース| ATCマニュファクチャリング
ATCとは誰ですか?
ATC Manufacturingは、ボーイングの元エンジニアであり、同社の共同議長であるDanJorgensonによって2004年に設立されました。 「私たちは常に技術とエンジニアリングに重点を置いてきました」と、ATCManufacturingの事業開発ディレクターであるDavidLeachは述べています。同社はまた、ボーイングとの長い歴史があり、過去5年連続でシルバーレベルのサプライヤーとして認められ、2016年と2017年にボーイングサプライヤーオブザイヤーにノミネートされました。ブラケットと小さな刻印部品」とリーチは言います。 「しかし、近年、私たちはより複雑なアセンブリに発展し、さらに厚くて大きな部品(長さ60インチまで)や一次構造用の部品になりました。」後者には、構造的な翼端コンポーネント、さまざまな断面で調整されたレイアップを備えた長い梁、胴体および尾翼構造が含まれます。
同社には150人の従業員と20人以上のエンジニアがいます。その製造は、2015年に専用に構築され、拡張の余地がある最適化されたワークフロー用に設計された、単一の67,000平方フィートの施設に集中しています。 (注:52,500平方フィートのスペースは、将来の成長のためにすでに事前に計画されています。)「すべてが1つの屋根の下にあります」と、リーチ氏は述べています。これには、30〜150トンの容量の9つのスタンプ成形プレスと、最大60インチ×30インチのプラテン領域が含まれます。 「2019年末までに完全に稼働する200トンのプレスを追加で設置します」と彼は付け加えます。 ATCには、最大12フィートの長さの部品を処理できる10個のCNCマシニングステーションと、最大30フィートの長さの部品のウォータージェット切断があります。
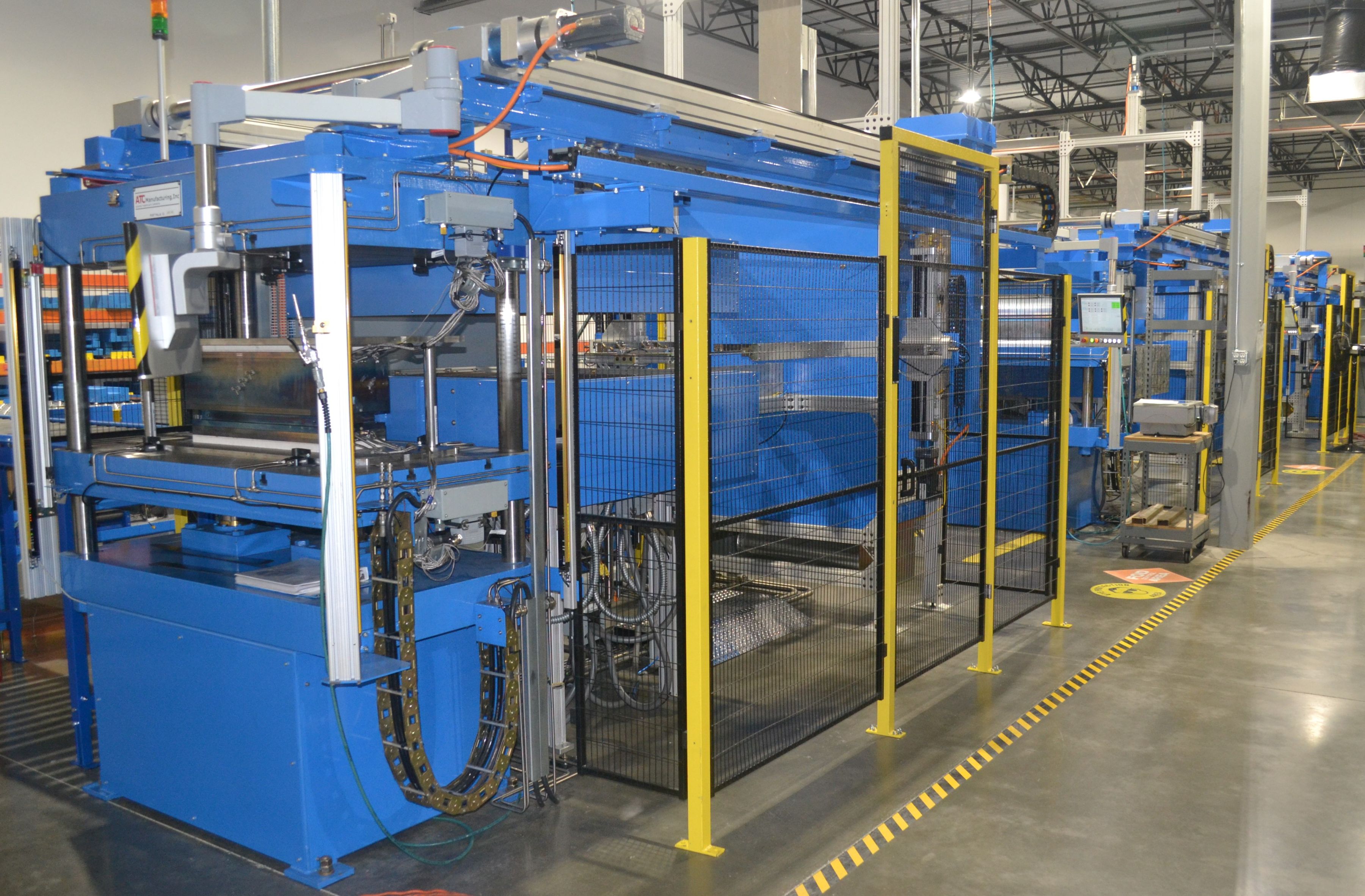
ATC Manufacturingは、ここに示す80トンのプレスを含む9つのスタンプ成形プレスを運用しており、容量は最大150トン、プラテン面積は最大60 x30インチです。
ソース| ATCマニュファクチャリング
非破壊検査(NDI)も、施設の運用とワークフローの設計に統合されています。これには、パルスエコーを提供する5つのC-スキャンタンクシステムや、最大30フィートの長さの部品の伝送テストが含まれます。その他の社内の専門知識には、すべての表面処理と塗装が含まれます。 「私たちは熱可塑性複合材料用の非常に効率的な表面処理を開発しました。これは塗装や接着が難しい場合があります」とリーチ氏は述べ、ATCはTPC部品のプラズマ処理にも取り組んできました。同社は年間20万個の部品を塗装し、年間70,000個の部品をエッジシールしています。
「DARPAのRAPMプログラムなどの研究にも多額の投資を行っており、ThermoPlastic Composites Research Center(TPRC、オランダ、エンスヘーデ)のメンバーです」と彼は続けます。 ATCは、オランダのトゥエンテ大学で10月8日に開催される「FutureofThermoplasticComposites」というタイトルのTPRCの10周年記念会議に参加しています。 「ATC副会長のコービン・チェンバレンがパネルセッションに参加し、会議に関連して開催された展示会で製造した航空宇宙構造部品のデモンストレーションも行います」とリーチ氏は言います。
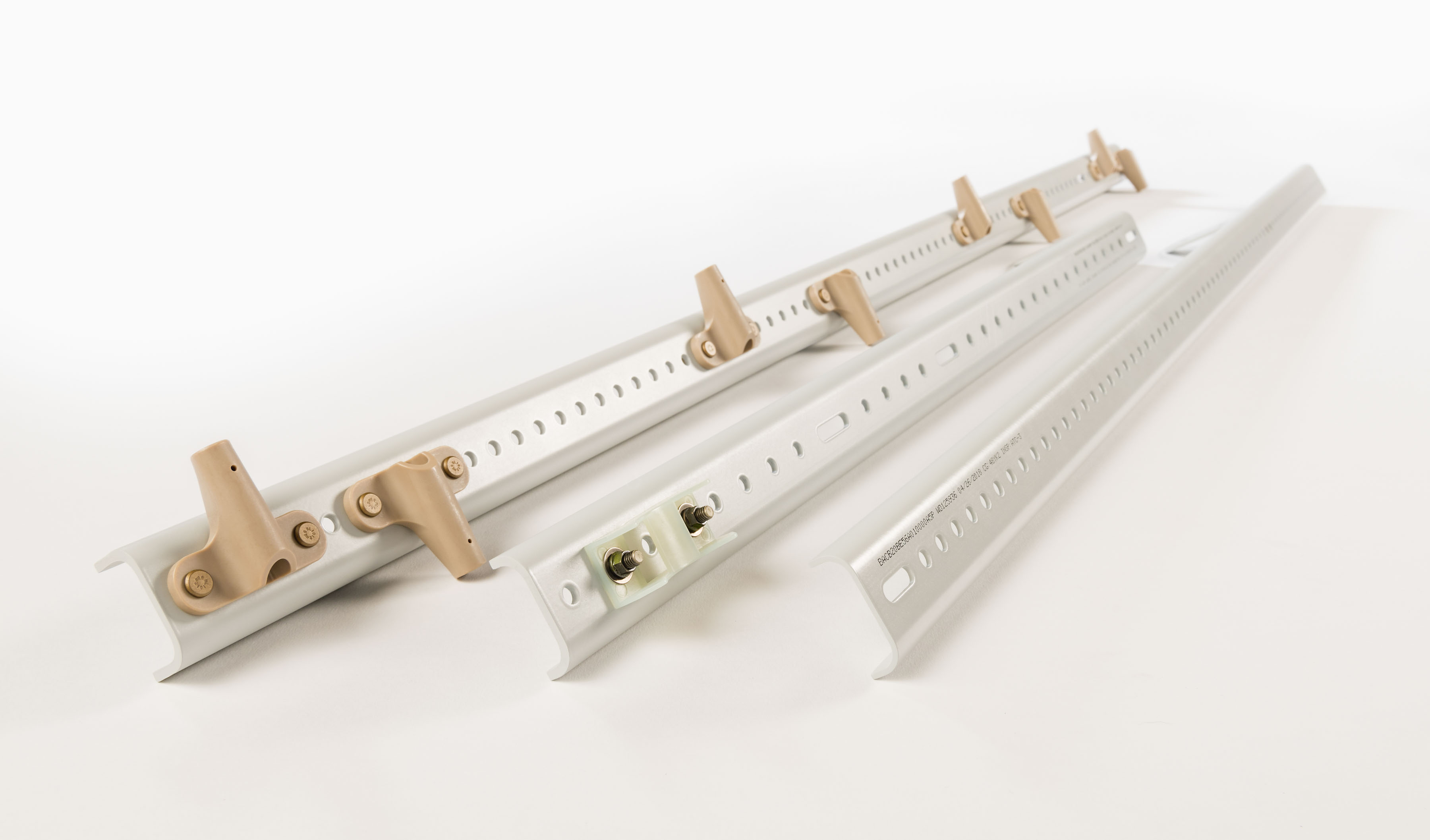
継手が取り付けられた塗装済み熱可塑性複合チャネル。ソース| ATCマニュファクチャリング
ファブリックからUDテープ、フォーミング、高速サイクルタイム
ATCによるTPCブラケットとクリップの製造は、布地の補強から始まりましたが、現在は一方向(UD)テープの使用に移行しています。 「その後、UDテープを使用して3Dパーツを形成する方法についてすでに優れた経験を積んでいるため、より大きな構造パーツに進化しました」とLeach氏は説明します。 「これらの部品は、厚さが1〜2ミリメートルから6.5ミリメートルの範囲であり、他の構造と結合する必要があります。接合面の厳しい寸法公差、たとえば±0.010インチ(0.25ミリメートル)のプロファイル公差と±0.5度の角度公差を満たす必要があります。」
その後、同社は長いTPCプロファイルの開発を開始しました。 「私たちは連続圧縮成形(CCM)を使用して独自のフラットラミネートストックを作成しています」とリーチ氏は言います。 「フラットラミネート用の2台のCCMマシンと、TPCプリプレグを連続した3Dプロファイルに形成し、最大75フィートの長さのチャネルを生成する1台のマシンがあります。」
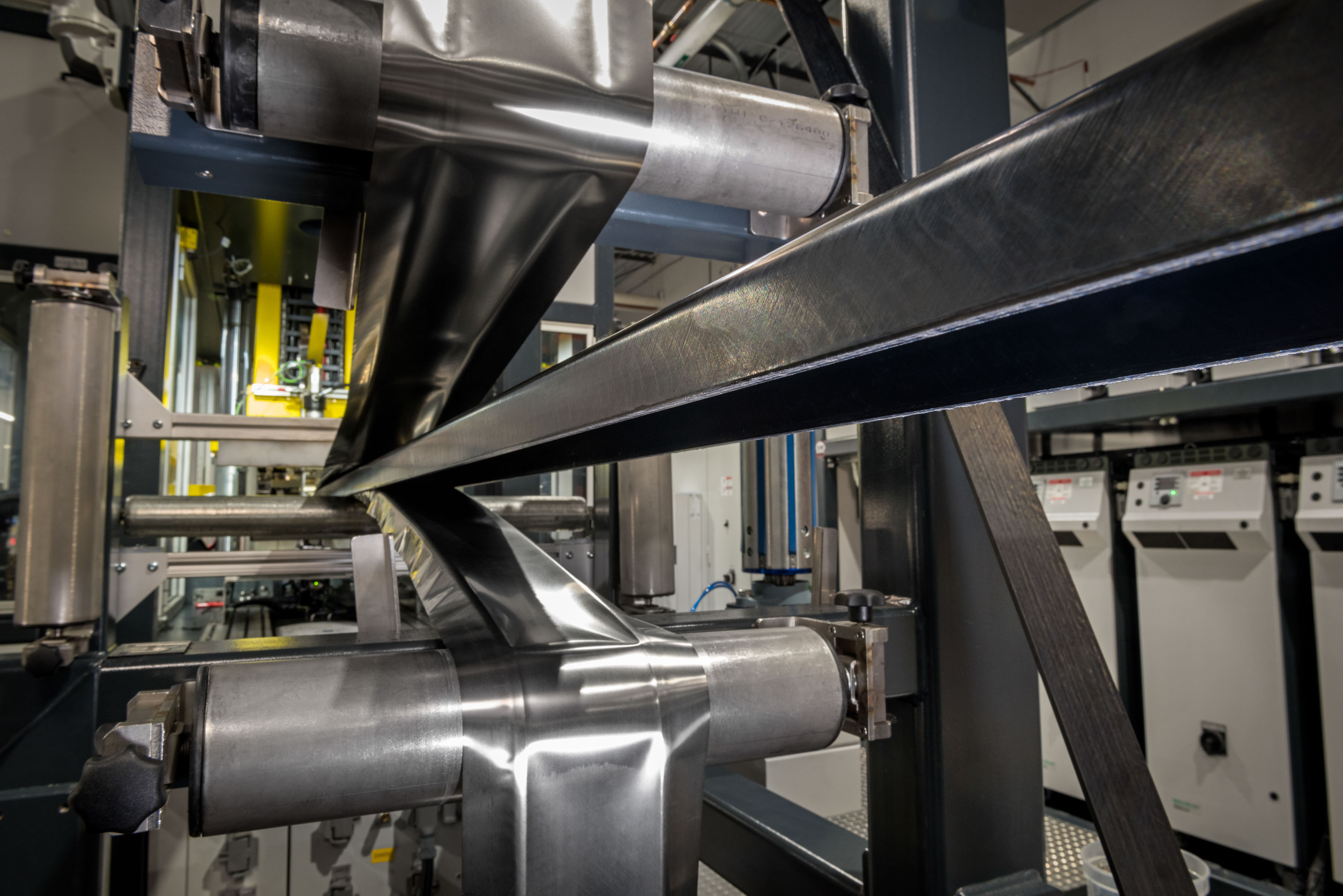
連続圧縮成形(CCM)を使用して形成される熱可塑性複合プロファイル。ソース| ATCマニュファクチャリング
3Dプロファイルと形状を形成する際の課題について尋ねられたとき、ATCManufacturingのR&DエンジニアリングディレクターであるTrevor McCreaは、ファブリックについて次のように説明しています。 UDには、さまざまなダイナミクスがあります。たとえば、半径に対して90度の角度で薄くしたり厚くしたりする必要がありますが、構造部品にそれを含めることはできません。これらの問題は、より複雑な形状で悪化します。また、フォーミングのプロセスをどのように管理するかについても、より多くの課題があります。」
プロセスを管理しますか? 「私たちにとって、これは熱硬化性樹脂での成形とは大きく異なります。成形に2秒しかかからないからです」とMcCrea氏は言います。 「オートクレーブサイクルで多くの罪をカバーすることができます」と彼は付け加えます。 「しかし、私たちはその余裕のない非常に高速な成形およびスタンピングプロセスを使用しています。結晶化度も管理する必要があります。」これは、高負荷の航空機構造が、ポリエーテルエーテルケトン(PEEK)、ポリエーテルケトンケトン(PEKK)、低融点ポリアリールエーテルケトン(LM PAEK)などの半結晶性熱可塑性マトリックスポリマーを使用しているためです。彼らが冷えるにつれて。 「等温結晶化することができます。これは平板にはそれほど難しくありませんが、3D形状でははるかに困難になります」とMcCrea氏は言います。 「材料は形成するのに十分に加熱する必要があります[これらの材料の溶融温度は300〜400°Cであることに注意してください]が、形状、公差、結晶化度、表面仕上げを管理しながらツールの熱サイクルを回避するために、熱間離型するのに十分な速さで冷却します。」
TPC部品が近年成長した理由の1つは、非常に速いサイクルタイムを提供できることです。 「軍用機のデモンストレーター用に5分のサイクルタイムでリブを作成しました。平均サイクルタイムは約10分です」とLeach氏は述べています。 「航空機OEMが現在求めている高い生産率を実現できます。」その非常に速い平均サイクルタイムは、実際には絶えず変化する部品の組み合わせをもたらします。 「私たちは何ヶ月も続けて部品を1つだけ生産したいと思っていますが、私たちのレート能力は航空機製造のそれを上回っています」とMcCreaは言います。 「それで、私たちは常にさまざまな部分を循環しています。」 ATCの製造のほとんどは、1日1シフト、週5日です。 「生産量の増加に対応するための十分な能力があります」とリーチ氏は述べています。
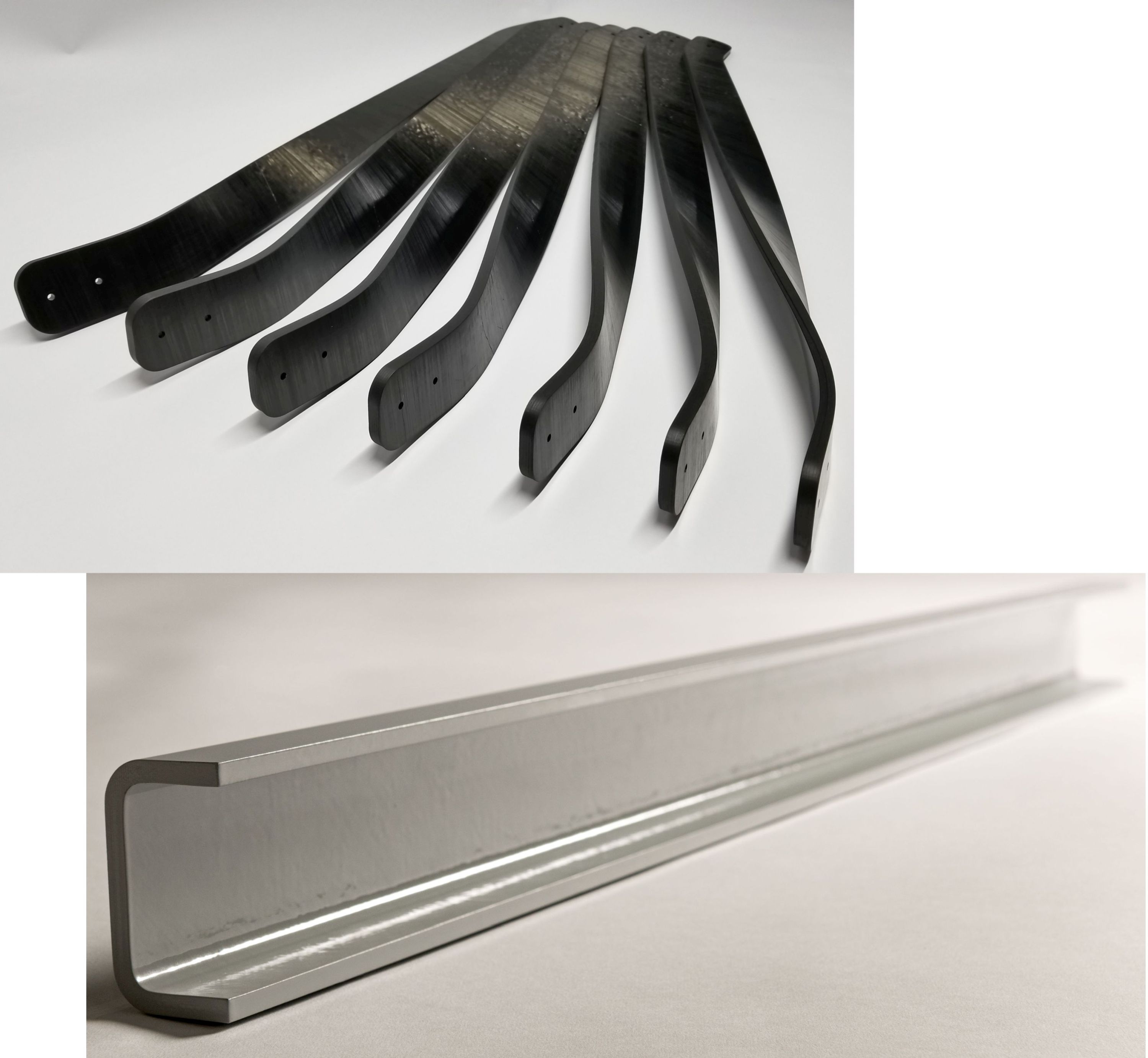
熱可塑性複合材料の構造用ストラップと塗装済みプロファイル。ソース| ATCマニュファクチャリング
将来のビジョン
ATCは、10年以上のTPC制作経験を通じて、大きな価値を提供します。 「私たちは、お客様が製造用の部品を設計するのを頻繁に支援します」とリーチ氏は言います。 「私たちはしばしば、熱硬化性複合材から部品を変換しています。たとえば、元の厚さを維持するために製造された胴体の一次構造フィッティングです。しかし、もともとTPC用に設計されていれば、はるかに軽い部品になる可能性があります。」どうして? 「これらの半結晶性TPマトリックス材料はより高性能であるためです」と彼は説明します。 「熱硬化性マトリックスの場合のように、マイクロクラックや損傷許容性を設計する必要はありません。また、ホット/ウェットノックダウンもはるかに少なくなります。実際、PEEK、PEEK、またはPAEKにはウェットノックダウンはまったくありません。また、Tg(通常は約150°C)に近づかない限り、ホットノックダウンはありません。たとえば、サンプルをRTから120°Cに移行するときに強度を評価する、損傷許容性の標準的なオープンホール圧縮(OHC)テストでは、ノックダウンはほとんどありません。」
「より薄い部品を設計することができ、複合材料の現在の第1世代の設計にある多くのアルミニウムとチタン(ボーイング787やエアバスA350ワイドボディ機など)を排除することもできます」とMcCrea氏は付け加えます。 「私たちはこれらの材料の成形を継続的に進めており、それによって新しいアプリケーションが開かれ続けます。」
リーチは、これが将来の航空機の用途に大きな影響を与えると考えています。 「私たちは実際に部品を検討していますが、要求される特性と生産率のために、熱硬化性樹脂を使用して生産することはできません。」
詳細については、ATC Manufacturingは、9月25日水曜日午後4時の熱可塑性材料およびアプリケーションセッションで、CAMX 2019で、著者のCorbin Chamberlain、David Leach、TrevorMcCreaによる技術論文「CostEffectiveThermoplastic CompositesinAerostructures」を発表します。 210C室で。
また、SAMPE 2019(5月4〜7日、米国ノースカロライナ州シャーロット)でのクローズドセッションで、ボーイングとの共同論文「構造用熱可塑性複合部品の高速高性能成形」を発表しました。私のブログを参照してください:https://www.compositesworld.com/news/darpa-presents-tff-program-for-rapid-low-cost-composites-to-replace-metals-in-small-parts-for-defense-アプリケーション
樹脂
- 3Dプリントが航空宇宙をどのように変えたか
- コベストロは熱可塑性複合材料への投資を強化
- Collins Aerospaceは、熱可塑性部品の製造業者であるDutch ThermoplasticComponentsを買収しました
- Oribi Compositesの熱可塑性複合材料:CWトレンド、エピソード4
- 熱可塑性複合材料の熱成形のトラブルシューティング
- 熱可塑性複合材料:構造用バンパーブラケット
- Toray Advanced Compositesは、熱可塑性複合材料の機能を拡張します
- ACMAが熱可塑性複合材料会議2020プログラムをリリース
- 熱可塑性複合材料:風光明媚なビュー
- 熱可塑性複合材料の溶接
- 熱可塑性複合材料コンソーシアムは、自動車および航空宇宙向けの大量生産を目指しています