熱可塑性複合材料の溶接における新たな地平
このブログには、2018年9月の特集「熱可塑性複合材料の溶接」が付属しています。これは、誘導溶接の開発のタイムラインと将来の民間航空機の認定の詳細、修理、自動車の開発、熱可塑性樹脂(TS)の開発など、印刷物に収まらなかった画像と詳細をまとめたものです。 -TP)溶接。
溶接熱可塑性複合材(TPC)アセンブリが航空宇宙および自動車の軽量構造の両方で重要である理由を繰り返すために、エアバスA320後部圧力隔壁の以下の2つの画像を比較してください。上の画像は、アルミニウム製の現在のバージョンです。リベットの数が多いことに注意してください。次に、ベルリンで開催された2018ILA航空ショーでPremiumAerotecが発表した溶接TPCデモンストレーターと比較してください。リベットがないことに注意してください。複合材料の場合、これにより、留め具の重量、時間、コストだけでなく、穴の配置と穴あけ、さらにそれらの穴のクリーニングと検査の時間とコストも削減されます。また、耐荷重性繊維の切断を相殺するために必要なラミネートパッドアップのない、はるかに軽量な構造を意味します。
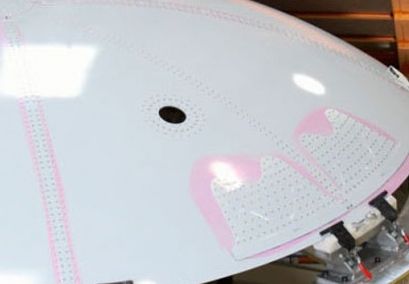
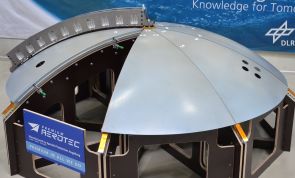
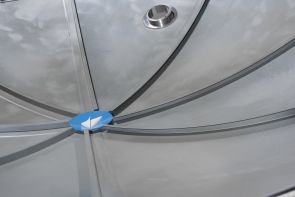
溶接された熱可塑性複合材A320後部圧力隔壁(下)は、現在のアルミニウム構造(上)に対してリベットのないソリューションを提供します。
出典:RUAG(上)と Premium Aerotec (下)、DLR Center for Lightweight Production Technology(アウグスブルク、ドイツ)
「もう1つの利点は、溶接構造の検査が接着剤で接合されたアセンブリよりも簡単なことです」と、熱可塑性複合材料の研究開発およびTPC材料サプライヤーTenCate-TorayGroupの製品開発ディレクターであるHansLuinge博士は述べています。 「C-スキャンはうまく機能し、ラミネートに多孔性がないかどうかを示します。これは、溶接が良好であることを意味します。接着剤で接着された構造の場合、キス結合や検出が難しい汚染物質が発生する可能性があります。」 TenCate-Torayは溶接技術自体を開発していませんが、さまざまな業界や顧客のプロジェクトをサポートしています。 「私たちは必要に応じて材料を最適化します。そして、TAPASのような取り組みへの長年の参加と、KVE Composites、TPRC、ティアサプライヤー、OEMのようなパートナーとの長年の参加に基づいて、開発を正しい方向に導く手助けをしようとしています。」
誘導溶接の開発
KVE Compositesは、2001年からTPCの誘導溶接を開発しました。初期のアプリケーションでは、ガルフストリームG650およびダッソーファルコン5Xビジネスジェット機用のエレベーターやラダーなど、カーボンファイバーファブリック/ PPSラミネートが使用されていました。
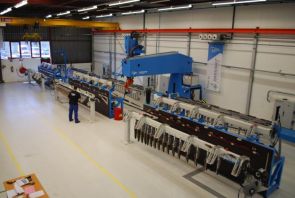
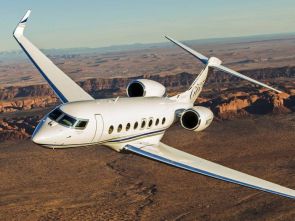
KVEコンポジットが役立ちましたガルフストリームG650(右)とダッソーファルコン5X航空機用に、GKNフォッカーによる誘導溶接式エレベーターとラダー(左)の製造を開発します。
出典:KVE Composites、GKN Fokker(左)およびGulfstream(右)。
その他の誘導溶接TPCアプリケーションには、AVIACOMPS.A.S。製の燃料タンクアクセスドアが含まれます。 (フランス、ルナゲ、現在はソゲクレアグループの一部)エアバスA220翼(以前はボンバルディアCシリーズ)用。 (Aviacompは、2017年のパリ航空ショーで展示されたSTELIAの溶接TPC胴体用のストリンガーも製造しました。)
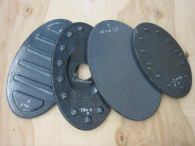
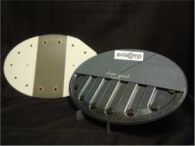
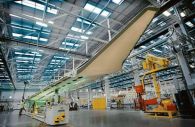
Aviacompは誘導を使用しますエアバスA220ナローボディ航空機用のTPC燃料タンクアクセスドアの製造においてKVEコンポジットによって開発された溶接技術。
出典:SogeclairGroupの一部であるAviacomp。
アクセスドアのこの一般的なカテゴリは、KVE Compositesが完了した設計および製造の調査で示されているように、TPC溶接がコストを節約する機会です。さらに小型の航空機でも、これらのアクセスパネルを最大60個持つことができ、すべて異なる形状であり、通常、機械加工されたハニカムコアを備えた複合サンドイッチ構造を使用して製造されます。 「溶接された熱可塑性プラスチックアセンブリを使用すると、航空機用のさまざまなアクセスパネルをすべて、わずか10万ドルの工具費で作成できます。これは、劇的な節約になります」とKVECompositesのマネージングディレクターであるHarmvanEngelen氏は述べています。 「コアを機械加工する必要はありません。フラットシートとプレス加工された補強材などの「レゴのような」コンポーネントを溶接してさまざまな形状を形成するだけです。また、私たちの工具は溶接ジグに似ているため、現在使用しているものに比べて比較的低コストです。航空機のすべてのアクセスパネルは、単一の溶接セルで作成できます。」
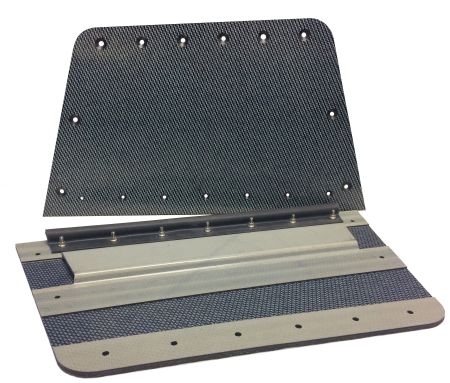
航空機のオーバーハングパネル用の溶接熱可塑性アセンブリ 自動成形および溶接セルを使用して作成 そして工具費を$ 100,000節約します。出典:KVEコンポジット。
KVE Compositesは、以下のタイムラインに示すように、TPC溶接技術の開発を続けています。 2019年の下部に示されている生産セルは、GKNFokkerによって開発された超音波溶接エンドエフェクターを使用してBoikon(Leek、オランダ)によって生産されたFalko ATL(自動テープ敷設)マシンです。 「このロボットセルは、現在使用されているピックアンドプレース方式と比較して、次のレベルの大量TPC部品生産のためのより効率的なプロセスおよび制御システムを可能にします」とR&D MaartenLabordusのKVEコンポジット責任者は説明します。 「たとえば、リージョナルジェット制御面(約60mm x 3m)のスキンとリブのラミネートを完全に自動でレイアップし、オートクレーブ外の圧密と成形の手順を適用して、組み立てを完了することができます。隣接する溶接セル。」 Falko ATLマシンは、超音波溶接用にGKNFokkerによってすでに開発された閉ループ制御も示しています。 「機械は、材料の種類、厚さ、形状ごとに必要に応じてエネルギーレベルを制御できますが、完成したTPC部品の成形中に、フラットプリフォームの完全な溶融圧密が必要になります」とGKNのAerostructures R&Tの責任者であるArntOffringaは説明します。フォッカー。
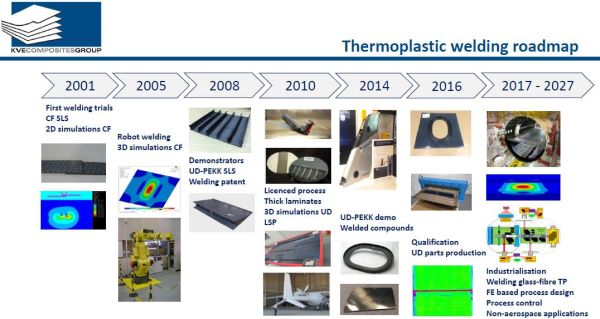
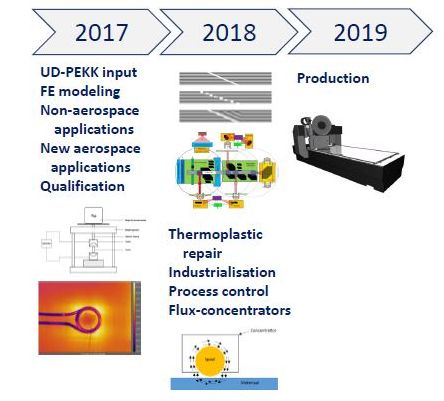
資格
2017年の主要な開発イニシアチブとして上に示した、資格 TPC航空構造の誘導溶接プロセスの開発は継続的な優先事項です。 4回目の でのKVEコンポジットの今後のプレゼンテーションの要約によると Int。会議熱可塑性複合材料に関する展示会(ITHEC、2018年10月30〜31日、ドイツ、ブレーメン)、過去数年間で、熱可塑性複合材料(TPC)溶接は、PPSやPEIなどのポリマーからPEEKなどのハイエンドポリマーへとシフトしています。 、PEKK、そして現在はLow Melt PAEK(LM PAEK、私のブログ「PEEK vs. PEKK vs. PAEK ...」で詳細を読む)、およびより高負荷の構造用の自動的に配置されたUDテープとより厚いラミネートに向けて。これに応えて、KVE Compositesは、FEAベースのシミュレーションモデルだけでなく、ツールと機器の改善と標準化を目指してきました。
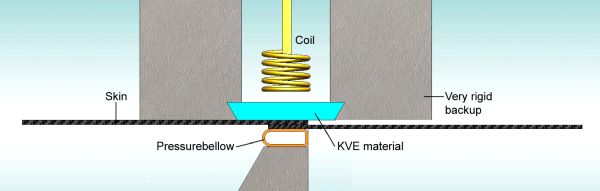
新素材による誘導溶接の認定のための標準化されたセットアップ。
出典:KVEコンポジット
これらの新しい複合ラミネートを使用した誘導溶接プロセスの成熟と認定を支援するために、KVE Compositesは、シングルラップせん断とLおよびTプルオフテストクーポンを溶接するための標準化されたセットアップを開発しました。この設定には次のものが含まれます:
- 溶接中にラミネートに圧力を加えることで荷重を受けるための剛性フレーム。
- 標準パネルの再現性のある溶接を可能にするためにフレームの下に配置できる下部ツールブロック。
- 下部ツールブロックの膨張式マンドレル(上の図の圧力ベローズ)は、一方向にのみ膨張して、溶接されるラミネートを特殊なヒートシンク(上の図の「KVE材料」)に対して圧縮し、溶接時に熱を閉じ込めることができますインターフェース。
下部のツールブロックを交換することにより、さまざまな標準クーポンを溶接して超音波検査した後、小さいクーポンを切断して機械的にテストすることができます。この標準化されたセットアップは、次のユーザーによってすでにインストールされています:
- 熱可塑性研究センター(TPRC、エンスヘーデ、オランダ)
- サウスカロライナ大学(米国サウスカロライナ州コロンバス)のマクネアセンター
- オランダ航空宇宙センター(NLR、マルクネスセ、オランダ)。
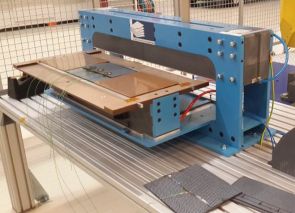

標準化された誘導溶接KVEでのセットアップ(左)と、溶接ラインでの温度を記録するための熱電対を備えた溶接UDカーボンファイバー/ PEKKサンプル(右)。
出典:KVEコンポジット。
修復
もう1つの重要な開発分野は、TPC航空構造を修復する方法です。 「私たちはまず、認定され飛行しているCFファブリック/ PPS構造に焦点を合わせています」とLabordus氏は言います。 「プロセスは基本的に熱硬化性複合材の修理に使用されるものと同じです。損傷した材料を取り除き、テーパースカーフでその領域を準備してから、プリプレグ修理パッチで接着します。 Labordus氏によると、問題の1つは、室温での熱可塑性プリプレグが板状で付着しないことです。「そのため、形状を一致させるのは困難です」。しかし、彼は、エアバス、ルフトハンザなどによって開発されているロボット修理システムが解決策を提供すると信じています。
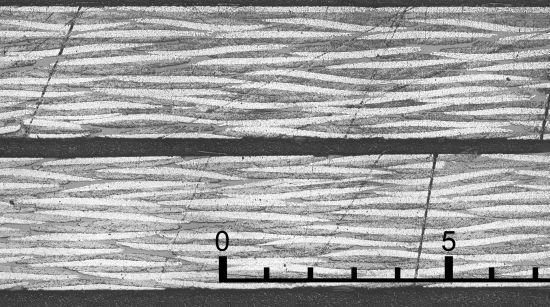
溶接構造熱可塑性複合材料の修理の継続的な開発の一環として、KVEコンポジットは、均一な厚さと90%の未使用材料特性を備えたCFファブリック/ PPSラミネートの誘導溶接2D線形テーパージョイントを実現しました。
出典:KVEコンポジット。
このようなシステムは、計測を使用してロボットで機械加工されたテーパースカーフを正確に測定し、それに合わせてロボットでテーパー加工された既製のパッチを接着します。 「熱可塑性パッチを元の構造に溶接するために誘導溶接を使用したいのです」とLabordusは言いますが、まだ解決すべき問題があります。 「パーツとパッチの形状によっては、渦電流がどこにも形成されないため、冷たさや過熱の領域が発生する可能性があります。 KVE Compositesはこれに取り組み、均一な厚さと完全な溶接を備えたCFファブリック/ PPSラミネートで2Dリニアテーパージョイントを実現することができました。 「私たちは未使用の材料特性の10%以内でした」とLabordusは言います。
次のステップは、それぞれがスカーフエッジのある2つの長方形パーツを誘導溶接し、次にテーパーパッチをテーパースカーフのある円形/楕円形の穴に溶接することです。これは基本的に熱硬化性複合材の修理に使用される方法です。 「それがうまくいけば、PEEKとPEKKで作られたUDラミネートに移行します」とLabordusは言います。彼は、誘導コイルを使用して現場で修理を行うシステムはまだ実証されていないと述べていますが、「ラボではそれを行うことができます」。もう1つの問題は、修復パッチとテーパー面が十分に密着するように圧力をかける方法です。 「現在、ラボツールで使用されている圧力は5バールです。真空バッグからの圧力だけで十分かどうかはわかりませんが、UD素材が平らな場合は、真空バッグから1バールで十分な場合があります。」
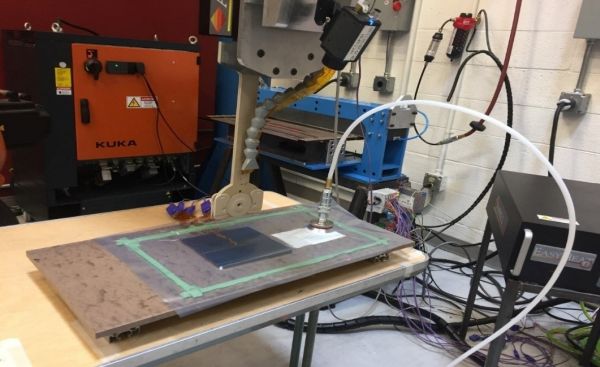
真空バッグの下での誘導溶接-将来の現場での熱可塑性複合材料の修理を可能にする可能性がある-は、サウスカロライナ大学マクネアセンターのMichel vanToorenと彼のチームによって開発されています。出典:Michel vanTooren。
KVE Compositesでのこの作業は、サウスカロライナ大学(米国サウスカロライナ州コロンビア)のマクネアセンターの一部であるSmartState Center for Multifunctional Materials andStructuresのディレクターであるMichelvanToorenによって拡張されています。 「私たちは熱可塑性複合材料を真空バッグの下で誘導溶接しています。これは、今日のホットボンダーとヒートブランケットを使用した現場での複合材料の修理方法と非常によく似ています」と彼は説明します。 「真空バッグは、2つの部品を圧縮するための柔らかい工具のように動作します。誘導電流を流して、溶融修復を実現します。プロセスの境界とパラメータを定義する必要があります。ある意味では、熱硬化性樹脂の修理よりも簡単です。これは、世界の反対側や20年のサービスの後でも、必要に応じていつでも修理を再調整できるためです。その結果、接着剤ではなく粘着性のある部品が得られるため、接着に関するすべての問題と、熱硬化性樹脂の修理で良好な接着性があるかどうかを知る方法がわかります。」彼もまた、現在開発されている自動ロボット修理技術により、「修理の誘導溶接は比較的簡単になるだろう」と信じています。
熱硬化性樹脂から熱可塑性樹脂への溶接
Van Toorenは、熱硬化性と熱可塑性の複合材料を接合するための誘導溶接も開発しています。 「熱硬化性複合材料に熱可塑性樹脂を導入しますが、溶接したい場所にのみ導入します」と彼は説明します。 「私たちはナノ粒子にグラフトし、わずかな交差重合を行います。その結果、熱硬化性複合材料に熱可塑性樹脂が埋め込まれ、化学的に溶融します。その後、熱可塑性樹脂の島に溶接できます。」繰り返しになりますが、ビジョンは、ドリル穴や従来の接着剤による接着に関連する問題を回避する、複合材料の接合と組み立ての代替方法です。
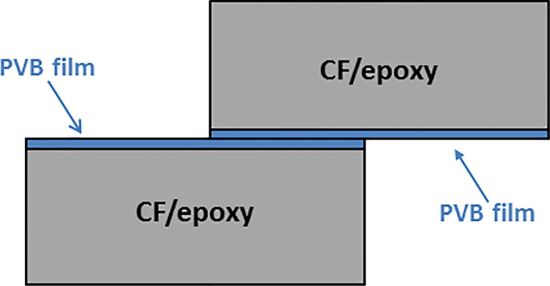
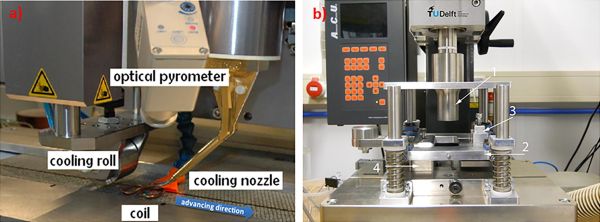
溶接前のPVB熱可塑性カップリング層を介したTSC-TSCジョイントの概略図(上)。誘導溶接(左)と超音波溶接(右)のセットアップ(下)。
出典:「CF /エポキシベースの複合材料のハイブリッド溶接」。
熱硬化性複合材料(TSC)ラミネートのTPCラミネートへの溶接(またはTS-TP溶接)は、複数の研究機関によって追求されています。デルフト工科大学のIreneFernandez Villegasは、TPCの連続超音波溶接の開発のリーダーとして印刷記事で言及されており、「炭素繊維強化エポキシベースの複合材料のハイブリッド溶接」というタイトルの2017年の論文をFrancescaLionettoと共同執筆しました。サレント大学(Lecce、イタリア)、CETMA CompositesのSilvioPappadà(Brandisi、イタリア)など。基本は次のとおりです。
- Polyvynilbutyral(PVB)は、半結晶性で低コストの熱可塑性ポリマーで、溶融温度が150〜170°Cで、優れた結合力と皮膜形成能力、および多くの表面への接着性が特徴です。
- PVB(Mowital、Kurakay提供)をカップリング層として使用し、14層炭素繊維布/エポキシTSCラミネート(繊維体積含有量58%、繊維体積含有量180のHexcel 3501-6プリプレグ)に添加して共硬化させました。 °C硬化)。
- PVBカップリング層とCF /エポキシ複合材料の間のマクロ機械的インターロックは、同時硬化中にPVB樹脂をTSCの最初の層(通常は厚さ10〜数百ミクロン)に部分的に浸透させることによって達成されました。エポキシモノマーのPVB熱可塑性フィルムへの拡散。
- 誘導溶接および超音波溶接プロセスにより、十分に強力な溶接継手が得られ、PVBカップリング層を介して溶接されたCF /エポキシからCF /エポキシへの接合は、約25 MPaの重ねせん断強度を示し、これは通常の範囲内です。 CF /エポキシ接着接合ジョイントの強度値。
自動車
熱可塑性溶接印刷物に含まれるほとんどすべての企業は、自動車および航空宇宙用途を検討しています。 「溶接は、複合材料をアルミニウムと比較して競争力のあるものにするのに役立ちます」とGKNFokkerのOffringaは言います。 「自動車はまた、溶接の迅速な代替手段として溶接を検討しています。複合材料の高速処理について、いくつかの自動車会社と話をしました。」彼は、炭素繊維複合車体はほとんど熱硬化性であり、指定された厚さの接着剤で接着されていると指摘しています。 「熱可塑性プラスチックを使用してこれらの部品を作成できれば 複合材を使用し、アセンブリを溶接することでコンポーネント間のギャップをなくすと、より剛性の高いボディ構造を作成できるため、重量、コスト、パフォーマンスにメリットがあります。」
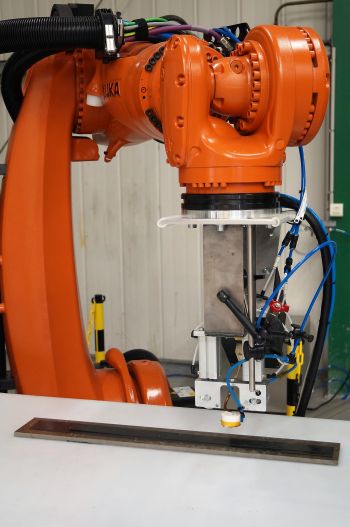
複合整合性の動的誘導溶接プロセスのセットアップ。
出典:CompositeIntegrity。
CompositeIntegrityの事業開発マネージャーであるJérômeRaynalも可能性を見出しています。彼の会社はSTELIAAerospaceと協力して、2017年のパリ航空ショーで発表されたTPデモンストレーターでCF / PEKKUDテープストリンガーと胴体スキンを結合するために使用される動的誘導溶接プロセスを開発しました。 「私たちは、ポリアミド[PA、ナイロン]とポリプロピレン[PP]の両方の複合材料を使用して、自動車用の抵抗溶接を開発しました」とRaynal氏は言います。 「これにはさまざまなテクノロジーがあります。たとえば、ある部分に金属線を埋め込んで、別の部分に接触させて電流を注入することができます。溶接インターフェースに炭素繊維抵抗パッチを配置して、必要な溶接熱を生成することもできます。」ある開発では、CF / PAで作られた2つのコンポーネントが、同じポリマーとガラス繊維フリースで作られた特別に設計された抵抗パッチを使用して溶接され、隣接するラミネートを電気的に絶縁し、溶接線にエネルギーを集中させました。自動車部品で非常に典型的な金属インサートはどうですか? 「金属インサートを備えた部品は抵抗溶接では問題ありません。誘導溶接では、特別に設計されたコイルを使用するか、他の方法で電磁界と電流を変更します」とRaynalは答えます。 「これは開発する必要がありますが、航空機構造の自動生産についてすでに示したものと似ています。」
さらなる開発とその他のプロジェクト
オープニング画像に関する注意事項。これは、超音波溶接を使用してDLR軽量生産技術センター(DLR ZLP、アウグスブルク、ドイツ)によって開発された自動プロセスのCADレンダリングを示しています。 KUKA Quantec KR210産業用ロボットに向かい、8つのTPCセクションをA320タイプの航空機用の後部圧力隔壁(RPB)に結合します。添付のTPC溶接に関する印刷記事では、DLRZLPによる抵抗溶接の開発について説明しました。 ベルリンで開催された2018ILA航空ショーで展示されたプレミアムエアロテックのA320RPBデモンストレーターで使用された方法。 DLRZLPの組立および接合技術のグループマネージャーであるLarsLarsen氏は、次のように述べています。「「溶接ブリッジ」を使用した抵抗溶接プロセスと並行して、ロボット作動の超音波溶接ヘッドも開発しました。関連する溶接プロセスパラメータを決定するための予備テストを完了しました。今後数か月以内に、その超音波溶接エンドエフェクタのロボットへの統合を改善します。私たちの目標は、航空機の胴体ストリンガーと熱可塑性複合材料を使用して作られた後部圧力隔壁の両方を溶接するための単一の工業プロセスを開発することです。」
今回取り上げることができなかった他のプロジェクトには、EireCompositesと、YbridioおよびInnovaプロジェクトへの参加が含まれ、溶接の可能性を追求してコストを削減し、自動化を促進します。同社は、CF / PEEK、CF / PEKK、およびGF / PP複合材料の誘導溶接および抵抗溶接機能と、ボンバルディアCシリーズ(現在のエアバスA220)翼の熱可塑性溶接が評価されたことを報告しています。
現在ユニテックエアロスペースの一部であるトッドエアロスペースは、ロールスロイスが後援する全国航空宇宙技術開発プログラム(NATEP)に参加し、金属埋め込みインプラントを使用しない抵抗溶接技術の開発を検討しました。 TenCate-TorayとNationalComposites Center(ブリストル、英国)もパートナーでした。
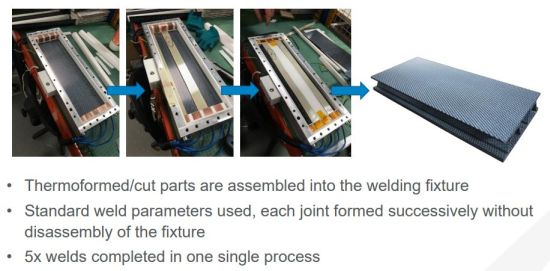
このプロセスデモンストレーターは、帽子で補強されたTPC構造を製造する方法を検討しました。出典:ユニテック航空宇宙(セクション6、39ページから開始)
近い将来、Laser Zentrum Hannover(LZH)の開発を熱可塑性複合材料のレーザー溶接でカバーする予定ですので、ご期待ください。
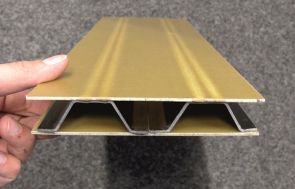
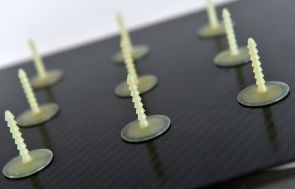
出典:LZH Laser Zentrum Hannover eV
樹脂
- コベストロは熱可塑性複合材料への投資を強化
- Oribi Compositesの熱可塑性複合材料:CWトレンド、エピソード4
- RECONTRASプロジェクトは、マイクロ波とレーザー溶接を使用してリサイクル可能な複合材料を取得することを検証します
- Salewasの新しいハイキングブーツは熱可塑性複合材を特徴としています
- 熱可塑性複合材料の熱成形のトラブルシューティング
- 熱可塑性複合材料:構造用バンパーブラケット
- Toray Advanced Compositesは、熱可塑性複合材料の機能を拡張します
- Teledyne CML Compositesは、熱可塑性プラスチック加工機能に投資しています
- IRGCosiMo熱可塑性複合材料コンソーシアムが新しい施設を発表
- 熱可塑性複合材料:風光明媚なビュー
- 熱可塑性複合材料の溶接