メンテナンス分析を改善するための10のめちゃくちゃ便利なメトリック
メンテナンス分析は、過去10年ほどで大きく変化しました。新しいツールとテクノロジーにより、データを収集して解釈する能力が向上しました。これにより、10年前には不可能だった情報に基づいた意思決定を行うことができました。
しかし、メンテナンス分析の理解が変わったとしても、なぜ40年または50年前と同じ少数の指標に依存しているのでしょうか。
設備総合効率(OEE)や平均修理時間(MTTR)などの指標は、業界で注目されている測定値のほぼすべてのリストを支配しています。しかし、専門家は彼らが欠陥があることに同意します。これらの従来の指標は偏見や不正確さを伴う傾向があるだけでなく、多くの場合、目的がありません。また、データに目的がない場合、データを使用して、追加の技術者を雇うか、タスクの頻度を増やすかなどの重要な決定を下すことはできません。
そのため、他のリストには表示されない10の有用な指標と、それらを使用してメンテナンスプログラムを改善するためのヒントをまとめました。
より良いメンテナンス分析のための10のメンテナンス指標
#1 –本番環境のサポートに費やした時間
それは何ですか?:保守チームが生産に焦点を合わせた活動に費やす合計時間。通常、毎週、毎月、または四半期ごとに測定されます。
どのようにそれを使用できますか?:誰もがたまに大きな注文を完了するために売り込む必要があります。しかし、たまに毎日になると、メンテナンスに支障をきたします。このメトリックは、不健全なバックログが発生する前にそれをキャッチし、それを防ぐためにリソースを再割り当てするのに役立ちます。また、チームの人員を増やしたり、トレーニング予算を増やしたりして、生産スタッフがマイナーなメンテナンスタスクを学習できるようにすることもできます。
<図>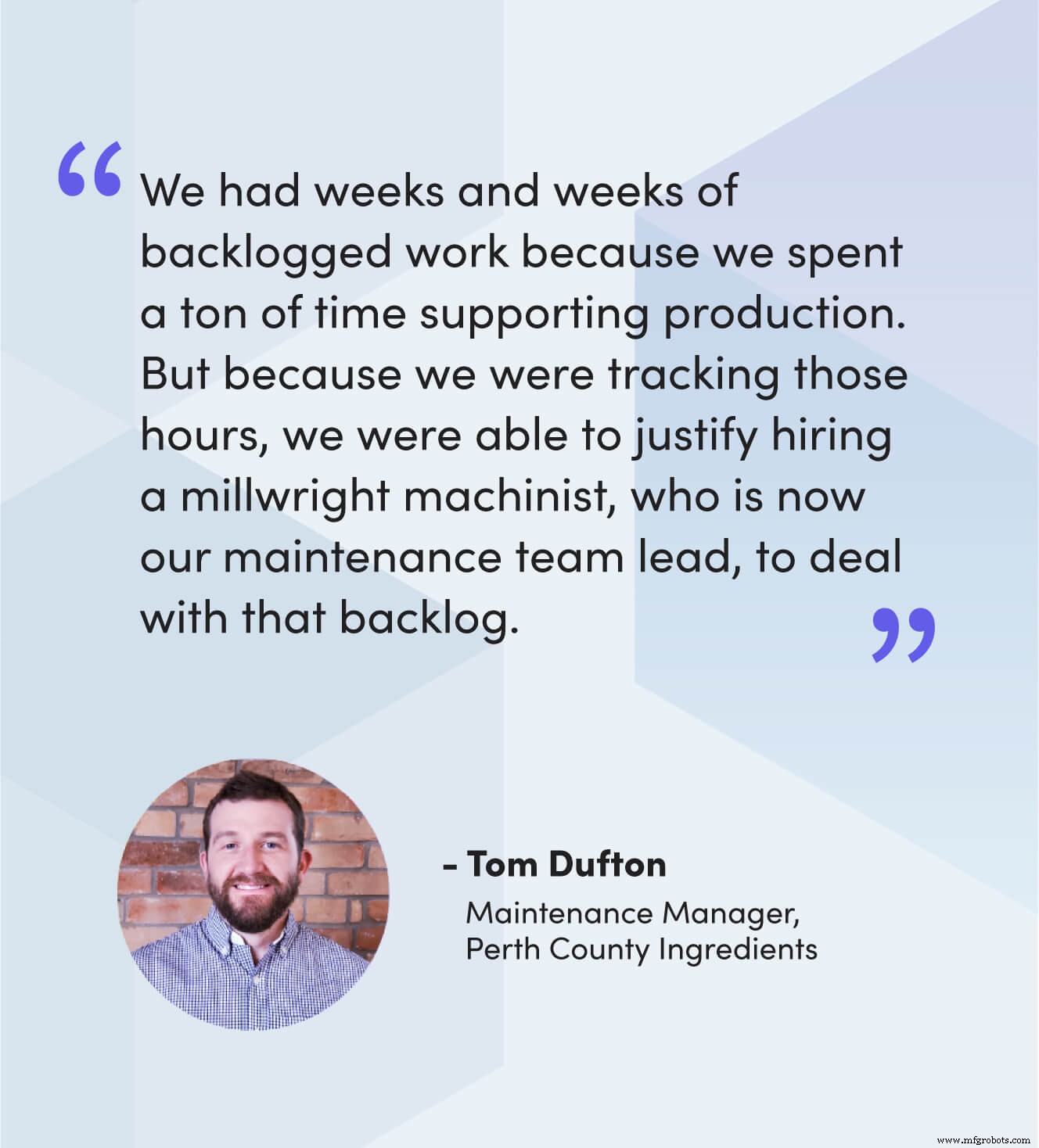
#2 –検査後に作成されたフォローアップ作業
それは何ですか?:定期検査から作成された修正作業指示の数。通常、月次、四半期、または年次で測定されます。
どのように使用できますか?:このメトリックを保守分析に使用するには、さまざまな方法があります。マシン、シフト、またはサイトで並べ替えて、資産またはチームのパフォーマンスに関する洞察を得ることができます。しかし、最も便利なのはタスクによるものです。
定期的な予防保守にフォローアップ修理が含まれる場合、これは良い兆候です。これは、スケジュールが正確であり、より大きな問題を防止していることを意味します。これにより、一般的な修復にフラグを立て、プロセスを構築して、それらをより効率的にすることができます。たとえば、すばやくアクセスできるようにパーツキットを作成できます。
不合格率が低い場合は、予防保守の間隔を長くすることができます。これにより、リスクを増大させることなく、タスクに費やす時間と費用を削減できます。
#3 –フォローアップメンテナンスのコストと全体的な障害の予想コスト
それは何ですか?:修正保守のコスト(つまり、人件費と部品)と、保守が行われなかった場合の資産の失敗のコスト(つまり、生産、人件費、部品の損失)の比較。
どのように使用できますか?:このタイプの保守分析を使用して、保守戦略を計画します。たとえば、定期的な検査で失敗よりもコストがかかる場合は、予防的な資産よりも失敗までのアプローチを採用する可能性があります。
この指標を使用して、タスクとバックログに優先順位を付け、予算を割り当てる方法を把握することもできます。
<図>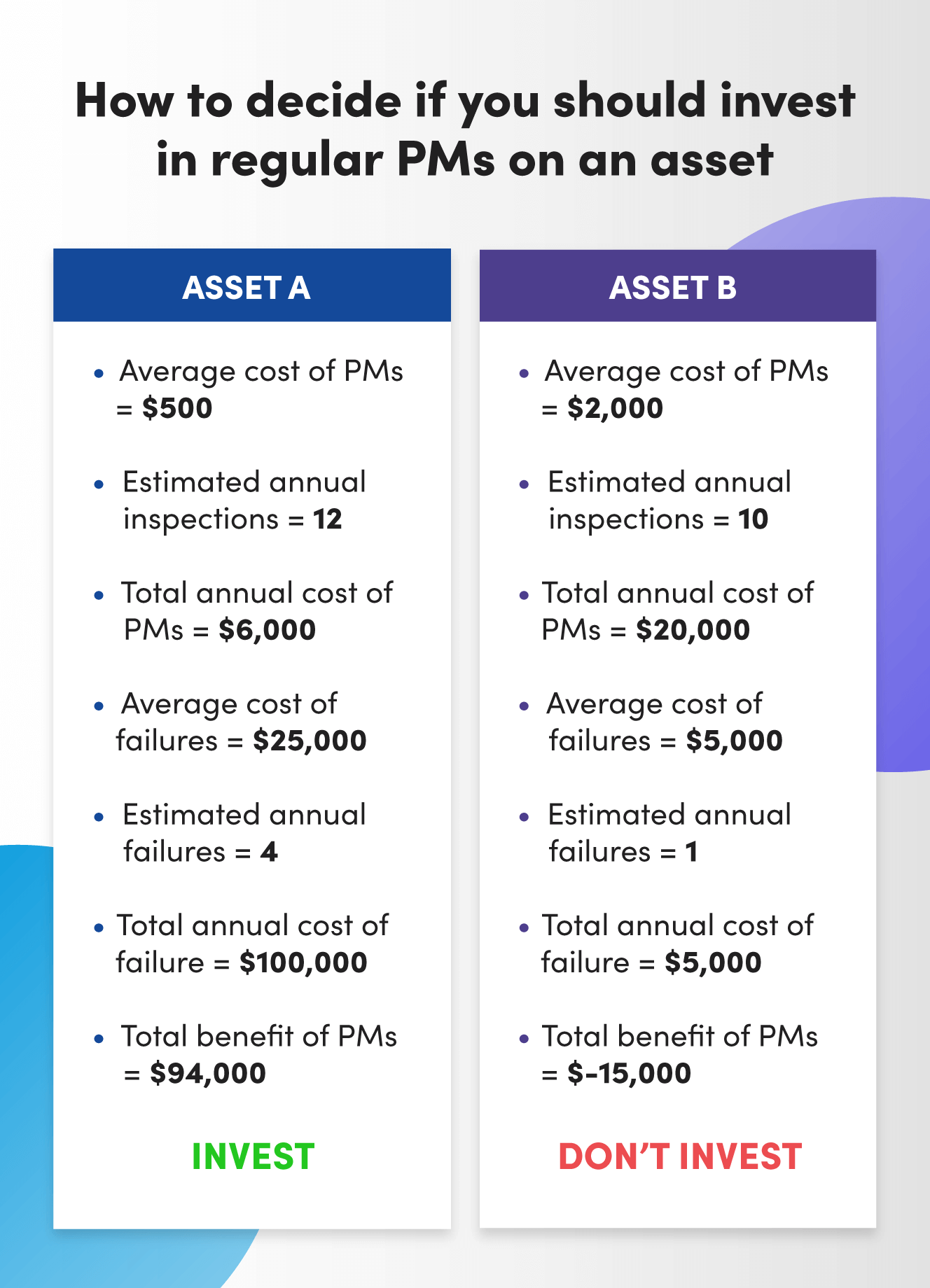
#4 –メンテナンスタイプ別のコスト
それは何ですか?:メンテナンスの種類(予防、緊急、フォローアップなど)ごとのメンテナンス(つまり、人件費と部品)の総コスト。通常、月次、四半期、および/または年次で測定されます。
どのように使用できますか?:コストが高くなるのは、通常、プロセスが壊れているためです。このビューでは、作業が必要なプロセスを見つけて、効率を上げることができます。
たとえば、作業指示が不明確で、修理時間と人件費の増加につながっていますか?指示を明確にしてみてください。
緊急修理のために外部の請負業者を連れてきていますか?チームのトレーニングにさらに投資するか、スペシャリストを雇うことができます。
#5 –メンテナンス後のクリーンなスタートアップ
内容:メンテナンス完了後、生産ラインが停止や無駄なく稼働する回数。これは、月次、四半期、および年次で測定されます。
どのように使用できますか?:この指標をメンテナンス分析に含めて、チームの作業と生産量の増加の間に直接的な線を引きます。
クリーンなスタートアップが少ない場合は、プロセスの問題を見つける別の機会が得られます。たとえば、生産ラインの仕様が古くなっている場合があります。これにより、技術者はコンポーネントを誤って再構築し、ラインを失速させることになります。仕様の更新は簡単な調整であり、出力が高くなる可能性があります。
#6 –バックログのサイズ
それは何ですか?:延滞およびスケジュールされたメンテナンスタスクの合計時間数。この指標を毎週および毎月追跡します。
どのように使用できますか?:このメトリックは、チームに切望されている救済を得るという点で、天の恵みになる可能性があります。利用可能な労働時間と総バックログ時間の間のギャップを定量化します。バックログの量が、チームが実行できる量をはるかに上回っていることに気付くかもしれません。これを使用して、余分な残業、別の技術者の雇用、またはより多くの請負業者の招聘に費やす予算を増やすことができます。
#7 –ダウンタイム別の上位10の資産
それは何ですか?:これはあなたのヘビーヒッターリストです—最も頻繁に故障するか、修理に最も時間がかかる機器です。これらの資産を毎週、毎月、四半期ごとに監視します。
どのように使用できますか?:このメトリックは、最大の問題を可視化します。あなたはそれで眉を上げるかもしれません、しかし非常に目に見える問題は最も速く解決されます。この種の保守分析は、問題解決の取り組みに優先順位を付け、迅速に意思決定を行い、その影響を測定するのに役立ちます。
たとえば、資産Aがダウンタイムリストの一番上にあることがわかっている場合は、理由を特定することから始めることができます。その資産の修理に時間がかかるからですか?仕事が遅れていますか?その機器は何度も故障しますか?
これらの質問への回答は、将来の障害を防ぐ方法のアイデアを提供します。壊れ続ける古い部品を取り除くかもしれません。または、追加の技術者を仕事に配置します。または、ベアリングに使用する潤滑剤の量を明確にします。他のすべてが失敗した場合、このタイプのメンテナンス分析を実施することは、新しい機器への資本支出を正当化するのに役立ちます。
#8 –計画されたメンテナンスの割合(過去90日間)
それは何ですか?:過去90日間の他のすべてのタイプのメンテナンスに対する計画されたメンテナンスの比率。
どのように使用できますか?:これは進歩の尺度です。事後対応型から計画的なメンテナンスへの移行は一夜にして起こりません。時間枠により、アクションと結果を明確に関連付けることができます。起こったこととそれが最終目標に与える影響との間に線を引くことができます。
たとえば、パーセンテージが低下した場合、過去90日間に何が起こったのかを調べてその低下を引き起こすことができます。それは大規模な、予期しない故障である可能性があります。または繁忙期の生産サポートの増加。割合を増やしたい場合は、より適切な作業要求プロセスを作成して、問題を早期に発見してみてください。または、予期しないダウンタイムが発生する可能性が最も高い資産の検査間隔を短縮します。
計画されたメンテナンスの割合とその改善方法の詳細
#9 –レンチ時間(過去90日間)
それは何ですか?:技術者が仕事を完了するのにかかる合計時間の一部として機器の作業に費やす時間。これは通常、仕事ごとに、または週次、月次、四半期ごとの平均として測定されます。
どのように使用できますか?:レンチ時間はメンテナンス分析の一般的なツールですが、間違った方法で使用されることがよくあります。技術者は通常(そして不当に)レンチ時間の短さのせいになります。技術者がトラブルを避けるために数字をファッジするので、それはレンチ時間のインフレにつながります。
レンチ時間の短縮は通常、技術者の能力ではなく、壊れたプロセスに起因します。これにより、バックログが大きくなり、メンテナンスがより迅速になり、人件費が回避できます。
メンテナンス分析でレンチ時間を使用するには、スコアが最も低いジョブから開始します。技術者と段階的にこれらのジョブを確認してください。協力して、不明確または不完全なプロセスが遅延の原因となる場所を見つけます。タスクを細かく分割すると、ボトルネックを簡単に見つけることができます。その結果、チームの時間とお金の価値が高まります。
<図>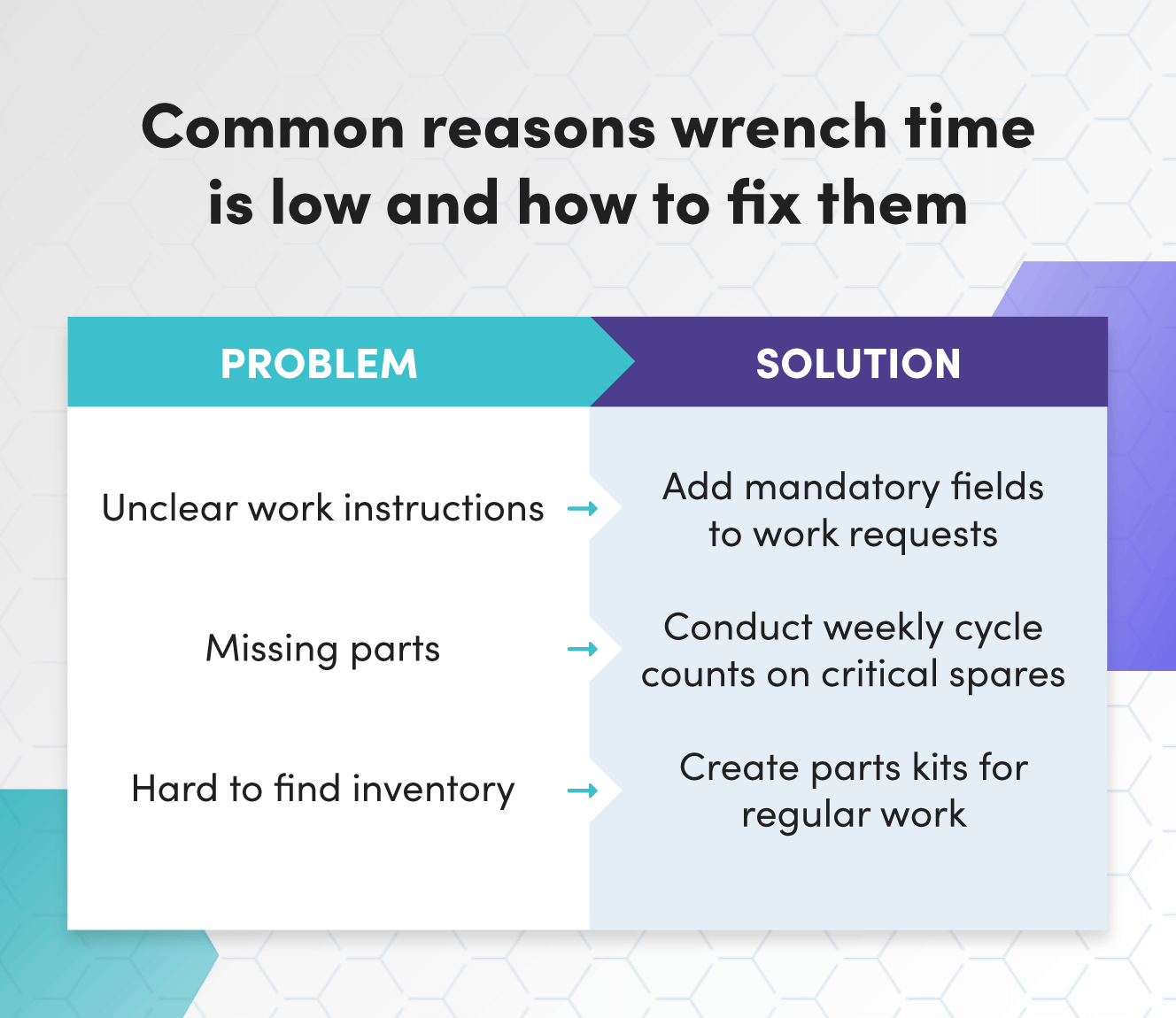
#10 –健康と安全に関する作業指示が完了しました
それは何ですか?:健康と安全またはコンプライアンスの目的で完了した作業指示の数。これは通常、毎月、四半期ごと、および毎年追跡されます。
どのように使用できますか?:一部の指標は定量的です。その他は定性的です。これは後者です。また、メンテナンスチームのパフォーマンスと、それがビジネスに与える影響を測定するために不可欠です。安全な職場は事故を低く抑え、生産性と士気を高めます。監査に合格し、コンプライアンスを維持することは、スタッフの安全と罰金の回避に不可欠です。
これらの指標を組み合わせることで達成できる3つの大きな目標
上記のすべてのメトリックは、それ自体が強力です。しかし、これらを組み合わせると、メンテナンス分析が強化され、3つの一般的な目標を達成するのに役立ちます。
より多くの予算とメンテナンスのためのより多くの時間を得る
組み合わせる指標:
- メンテナンスタイプ別のコスト
- メンテナンス後のスタートアップをクリーンアップする
- ダウンタイム別の上位10の資産
メンテナンスのためにより多くのお金と時間を得るということは、予算を分割する人、そして生産を主導する人に勝つことを意味します。彼らを参加させる最も簡単な方法は、あなたの計画を彼らの目標に合わせることです。上記の3つの指標は、そこに到達するのに役立ちます。
まず、予防保守の費用対効果を強調します。定期的な予防保守は費用がかかるように思われるかもしれません。しかし、緊急メンテナンスの1つのインスタンスだけで、最大250,000ドルの費用がかかる可能性があります。メンテナンスの種類ごとにコストを追跡している場合は、事後対応型メンテナンスで会社がどれだけの損失を被っているか、予防的メンテナンスに投資することでどれだけ節約できるかを強調できます。
次に、制作チームを揺さぶる時が来ました。メンテナンス後にクリーンなスタートアップを使用して、生産に彼らの最善の利益を念頭に置いていることを示します。メンテナンスに適しているものが生産に適していることが多いことを強調しています。
計画がなければ、誰もあなたにもっと多くのリソースを与えるつもりはありません。悪意のある人物のリストは、余分な時間とお金を最大限に活用するための青写真です。問題を定量化し、どこに注力するかを明確にします。
次の大きな(そして高価な)メンテナンスプロジェクトを売り込むためのテンプレートを入手してください
メンテナンスチームに変化を受け入れてもらう
組み合わせる指標:
- 計画されたメンテナンスの割合(90日)
- レンチ時間(過去90日間)
- 検査後に作成されたフォローアップ作業
変更は最悪です。そして、それはあなたのチームが新しいシステムやプロセスに乗り込むのを難しくします。否定論者の心を変える最良の方法は、あなたの計画が彼らの最大の苦痛をどのように取り除くかを彼らに示すことです。上記の指標を追跡することは、これを行う1つの方法です。
これらのデータポイントは、変更前の運用方法(つまり、多くの事後対応型のメンテナンスと当て推量に対するフラストレーション)と、新しいシステムまたはプロセスの実装以降に達成したことを比較する機会を提供します。見返りを直接確認することで、CMMSを設定する場合でも、機械のオペレーターが日常のメンテナンスを行えるようにする場合でも、批評家を変えてプロジェクトを拡大することが容易になります。
他のほとんどの企業を嫉妬させる予防保守プログラムを構築する
組み合わせる指標:
- メンテナンスタイプ別のコスト
- 検査後に作成されたフォローアップ作業
- フォローアップメンテナンスのコストと全体的な障害の予想コスト
最高の予防保守プログラムには、ほとんどのPMがありません。代わりに、彼らは最も効率的なPMを持っています。つまり、適切なタイミングで適切な作業を行うことを意味します。これらの指標は、このバランスを達成するのに役立ちます。
メンテナンスの種類ごとにコストを測定すると、予防タスクにリソースを割り当て、PMの効率を測定するのに役立ちます。コスト削減戦略が機能しているかどうかを追跡し、それらが将来の事後対応コストにつながっていないことを確認できます。
フォローアップ作業を監視することは、PM頻度を最適化する1つの方法です。検査が修正作業につながらない場合は、検査間隔を長くすることができます。つまり、より少ない労働時間と部品を使用し、そのお金と時間を他の場所で使うことができます。同様に、修正メンテナンスのコストと全体的な障害を比較することで、価値のないプロアクティブなタスクにお金をかけないようにすることができます。
<図>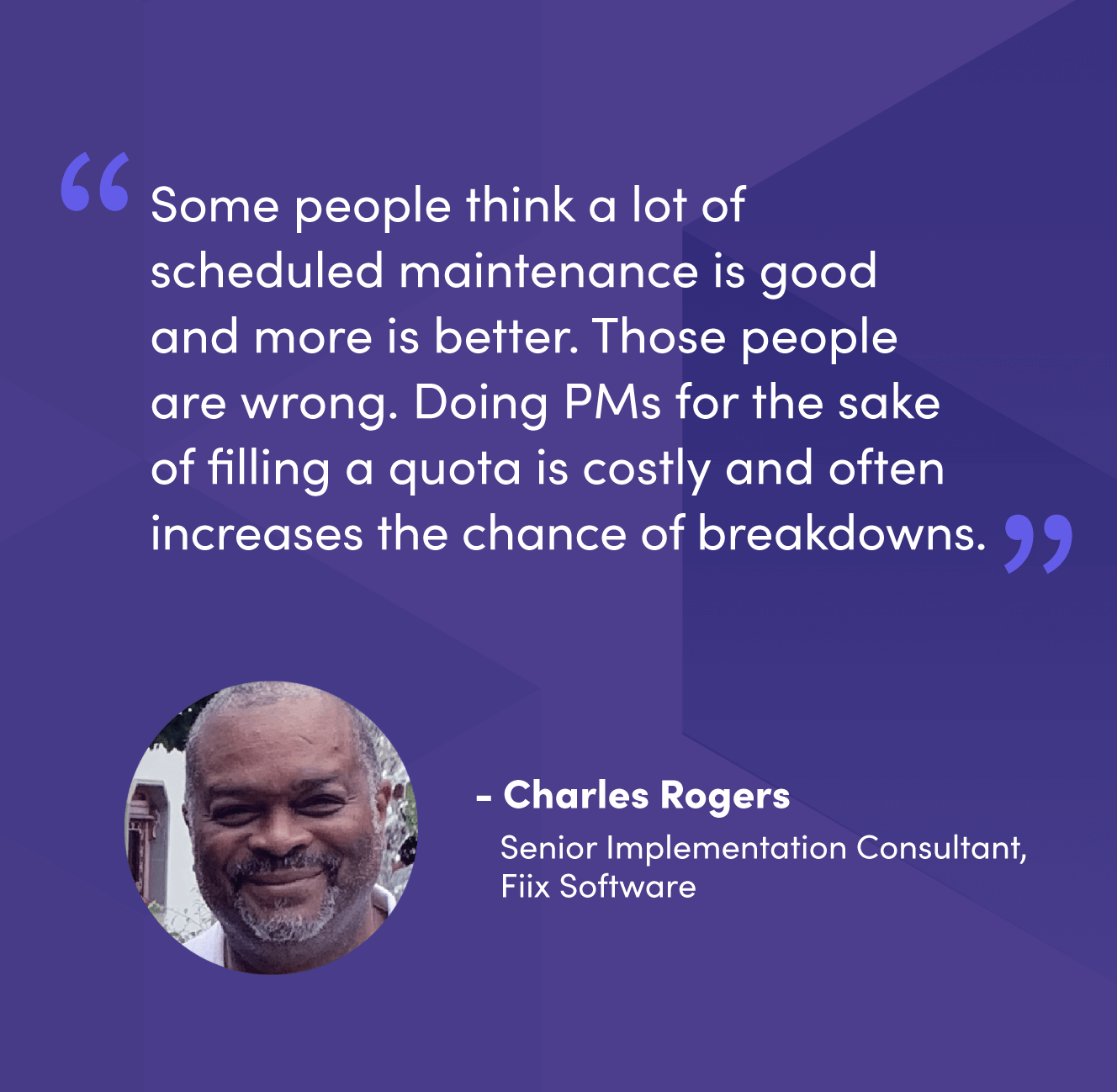
最高のメンテナンス分析は常に進化しています
最高のメンテナンス指標には目的があります。それらは収集され、一貫して使用されます。彼らは決定を導き、あなたのメンテナンスプログラムを毎日実行する方法についてあなたに知らせます。これは、メンテナンス分析を成功させるためのバックボーンです。
反対に、すべての保守分析は進行中の作業です。定期的に指標を見直して、目標とメンテナンスチームの働き方に関連していることを確認してください。上記の指標のいくつかは今はうまくいくかもしれませんが、他の指標は6か月でより効果的になるかもしれません。または多分5年。
最後に、最良の保守分析には、他の部門が役立つと考えるデータが組み込まれています。上記の指標を結び付けて他のビジネスユニットの課題を解決できれば、世界クラスのメンテナンスプログラムを作成する準備が整います。
機器のメンテナンスと修理