高速フライス盤の戦略
小さなフライス盤を使った高速フライス盤と製造業での適切な使用については、ナットやボルトと同じくらい多くの意見があります。高速フライス盤の利点は、切削負荷と切りくず率を低くして、より良い表面仕上げを実現できることです。高速、高公差、高生産の機械加工の世界では、完璧な部品を作成するために多くのポイントが組み合わされています。 DATRONでは、適切なDATRONマシン構成、最適化された速度と送りを備えた材料保持および切削工具の戦略を推進して、この戦略を定義します。
高速フライス盤で成功するための5つの必需品:
- 振動のない高速/周波数スピンドル
- 剛性と振動のないX、Y、Z軸
- 剛性、完全なサポート、振動のないワークホールド。
- 振動のない工具
- 適切な送りと速度を使用して最適化されたプログラム
このディスカッションは、4番目の項目であるツールに関するものです。
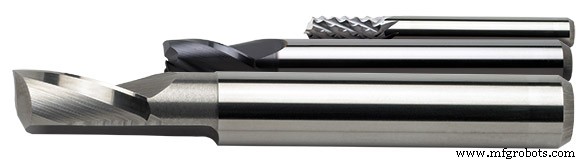
そのため、あなたの店は高速フライス盤に投資し、実行するプログラムが提示されました。 1つのテストピース、複数のテストピース、または数百の本番稼働である可能性があります。フライス盤が機能するかどうかは疑問の余地がありません。そのプロセスは購入前に確認されています。したがって、作業の保持と工具は、この作品の成功を左右します。
議論のために、上記の他の4つのポイント(振動のない速度/周波数スピンドル、振動のないX YおよびZ軸、剛性のあるフルサポートの振動のないワーク保持、最適化されたプログラム)が満たされていると仮定するので、高速フライス工具戦略について説明しましょう 。
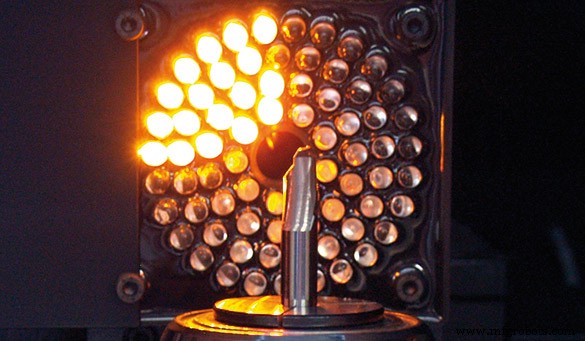
高速度鋼または超硬?高速フライス盤では、振動がキラーであり、それ以上にキラーであることに誰もが同意できます。生産、コストの境界を満たし、最高の仕上がりを実現するための高速および送りでの操作は、最も剛性が高く振動のない工具を決定します。高速度鋼の工具による屈曲と高速速度での振動の可能性があります。したがって、リジッドツーリングの必要性はカーバイドに傾いています…高品質で頑丈なマイクログレインカーバイドツーリング。
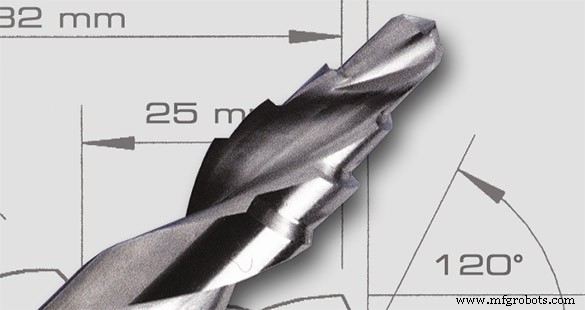
高速超硬工具、特にDATRON工具の幾何学的設計により、高速および送り速度で最も熟練したクリーンな材料の切削が可能になります。これにより、重い荒削りパスが可能になり、カールすることなく完全な形状のチップが作成され、スピンドルの完全な切削エネルギーが材料の除去に費やされます。
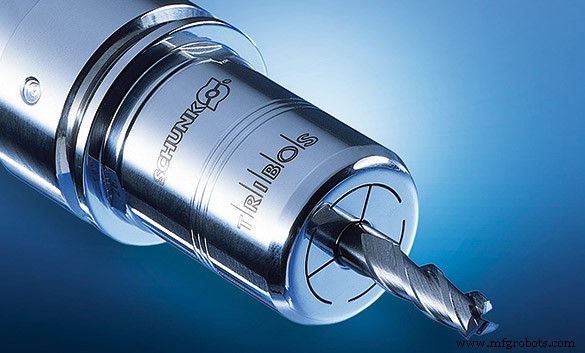
高速フライス工具の保持
次に、ツールを適切に保持します。工具の振動は通常、高速フライス盤用に作られていない工具、不適切にバランスの取れた工具、または不適切にチャックされた工具の結果です。ダイレクトシャンクスピンドルまたはHSKスピンドル用のバランスツールホルダーの両方を使用して、振動のない切断を実現できます。ツールを適切にロードする場合(真ちゅう製のストップリングまたはHSKツールホルダーを備えたダイレクトシャンクツール)、上部の間に20%または4〜6 mmのスペースが必要です。または、フルートからストップリングまたはHSKツールホルダーにフェードアウトします。これにより、フライス盤で切りくずを工具から自由に離すことができます。ただし、ダイレクトクランプコレットまたはHSKツールホルダーを充填するシャフトは約80%のみである必要があります。ツールの上部がコレットまたはHSKツールホルダーの上部に接触しないようにする必要があります。これにより、スピンドルが損傷する可能性があります。
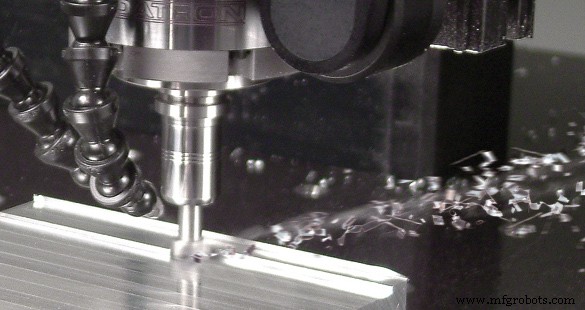
高速フライス工具(プラスチップ除去)の送りと速度
さて、楽しい部分が来ます。最高の速度と送り速度はどれくらいですか?そして、あなたはあなたのプログラムのためにどんなタイプのチップ除去を持っているべきですか?
一般的に述べられているように、高速ミルを使用したフライス盤戦略は、従来のコモディティ(非高速)フライス盤と同じ道をたどることはありません。より小さな工具をより速く、よりきれいに、そして高い送り速度で使用する能力は、標準的な商品の機械加工慣行よりも短いサイクル時間で複数のパスを可能にします。仕上げが高いため、コモディティマシンのフライス盤で通常必要となる2番目と3番目のステップのプロセスを追加する必要がありません。
これを念頭に置いて、戦略には、最も一般的なフライス盤の慣行を満たすツールの選択が含まれます。また、選択した工具の送りと速度を「ダイヤルイン」して、各工具とフライス盤の操作に最適な速度と送り速度を探すこともできます。これは、タップテスト、振動テスト、オクターブ(ハーモニックピッチ)テスト、または昔ながらのトレイルとテストの方法など、さまざまな方法で実行できます。最終的な目標は、最良の結果を得るために最良の送り速度と速度を見つけることです。成功したDATRONオペレーターの大多数は、TrialandTestメソッドを使用します。
公表されている速度(rpm)と送り(切削移動)は良い出発点ですが、せいぜい出発点にすぎません。機械、スピンドル、材料、工具を考慮する必要がありますか?戦略を最大化するためのいくつかの要因の組み合わせであることを忘れないでください:高速/周波数スピンドル、X Y軸とZ軸の剛性と公差、剛性のあるワーク保持。工具の種類(幾何学的設計、直径、フルート、長さ、工具保持)とパスの深さはすべて、送りと速度に影響します。
高速フライス盤にもいくつかの異常があります。高速フライス盤では、びびりと振動がキラーであり、通常、速度や送り速度を下げるようにオペレーターに指示します。ただし、高速フライス盤のコミュニティでは、ダイヤルアップして速度を上げると送り速度が向上し、チップの負荷が大きくなると実際に問題が解決することがよくあります。
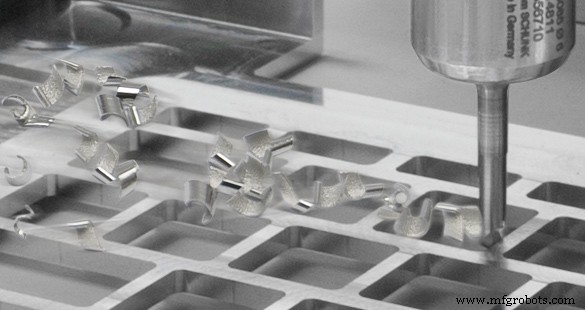
チップ負荷の確認
切りくず負荷は、機械加工プロセスで生成される切りくずの実際の厚さです。これは、カッターの送り速度(材料内を移動する)と速度速度(回転速度、RPM)の組み合わせを反映しています。切りくず負荷が高すぎると、切削圧力の上昇により、不十分なエッジ仕上げや部品の動きが発生します。スピンドルと工具に高い応力がかかり(破損の危険性があります)、確かに工具の摩耗が大きくなります…最終的には寿命を短くすることは耐用年数です。良好な切りくず負荷の必要性は、工具損失の主な原因である熱を減らすのに役立ちます。熱は、工具の切削作用、刃先と材料の摩擦から発生します。チップを適切に排出すると、切削動作から発生する熱が放出され、工具への損傷の可能性が減少します。
切りくず負荷は1000分の1インチ(つまり0.010)で測定され、CNCマシンのスピンドル速度と送り速度の影響を受けます。フルートの数、フルートの長さ、シャンクの直径、切り込みの深さも、切りくずの負荷に影響します。工具の刃先の数によって、切りくず負荷の分割方法が決まります。シングルエッジツールは回転中のすべてのチップ負荷を提供し、ダブルエッジツールは負荷を2つのエッジに分割します。
チップ負荷を決定するための式:
チップ負荷=送り速度/(rpmx#刃先)
チップ負荷の操作:
チップの負荷を増やすには:
- 送り速度を上げる
- RPMを下げる
- フルートの使用量を減らす
チップの負荷を減らすには:
- 送り速度を下げる
- RPMを上げる
- フルートをもっと使う
参考までに、DATRONエンドミルのチップ範囲は次のようになります。
直径1mm=.01mm(.000394)
直径20mm=.15mm(.7874)
これは、シャンクの直径とフルートの長さに大きく依存します。フライス盤の深さの要件には、常に最短のフルート長さを使用してください。ツールの追加コストを回避するために生産を遅くすることが正当化されることはめったにありません。
チップの負荷能力は、メーカーの幾何学的設計にも影響されます。したがって、ツールの製造元の仕様に精通している必要があります。
最後に、実際のアプリケーションで最高の速度とフィードをダイヤルします。見て、聞いてください。材料の仕上げと、操作中にスピンドルがツールで作るピッチは、正しい方向または間違った方向に進んでいるかどうかを示す良い指標になります。実稼働環境でツールを指定する前にツールをテストしておくと、アプリケーションの「最先端」が得られます。ツールの振動がいつ(どの速度で)導入されるかを知ることで、壊滅的な結果をもたらすことなく、ツールの動作をこれに近づけることができます。これにより、工具、機械、スピンドル、およびプログラムを最大限に活用して、最良の部品をフライス加工して仕上げることができます。
CNCマシン