製造効果を早期にシミュレートすると、堅牢な設計につながります
設計とエンジニアリングでは、単純化のメカニズムとして想定が行われることが多く、その単純化で十分な場合もあります。しかし、多くの場合、非線形効果を説明するための十分な時間やツールがないことが原因です。
多くのコンポーネントでは、製造プロセスが製品のパフォーマンスに大きな影響を与えますが、多くの場合、最も一般的に見過ごされている影響の一部です。どのような製造上の影響を考慮する必要があり、どの影響を無視することができますか?これらに対する答えは必ずしもよく理解されているわけではありません。多くの場合、エンジニアリングの標準的な方法は、設計者に設計を作成させ、それをアナリストに渡してから、アナリストに設計を作成して分析させることです。多くの場合、このアプローチはかなり面倒であり、その結果、理想よりも時間がかかります。 CADからCAEへの接続と時間が理想的ではないため、モデルを実際に構築、分析、理解するよりも、データの転送と初期分析の実行に多くの時間を費やすことは珍しくありません。
3DEXPERIENCEプラットフォーム–設計ツールと弾性波ツールを統合する:
3D DASSAULTSYSTÈMESによるEXPERIENCEプラットフォームは、CATIAのワールドクラスの設計機能と、SIMULIAの線形および非線形の弾性波ツールセットを組み合わせたものです。このような強力な機能により、業界で一般的なものよりもCADとCAE間のシームレスな接続が可能になります。また、ガイド付きプロセスと標準化されたテンプレートが可能になり、最初の回答がより迅速になります。したがって、最初の簡略化された計算と仮定が専門の構造解析エンジニアによって行われる代わりに、これらの最初のパスの回答をCADと初期のエンジニアリングツールセットに埋め込んで、構造の主要業績評価指標に関する最初のモデルと最初の最初の推測の両方に到達することができます。 。これにより、アナリストに渡される前に、CAD内で最初のパスの線形構造回答を実行および分析できます。
構造解析エンジニアは、モデルをさらに改良し、提供された「ファーストパス」モデルに適切な効果を追加することで、「ブレードを研ぐ」ことができます。これらの製造上の考慮事項の一部は、単に「拡張された」線形の仮定である可能性がありますが、必要に応じて、接触、材料の非線形性、さらには応力硬化効果を含めることができます。これから説明するように、この改良は非常に重要であり、他の方法では見落とされる可能性のある障害を容易に明らかにすることができます。非線形性の「古典的な」例としては、材料の非線形性があります。鋼の塑性、ゴムの非線形挙動、さまざまな材料やコンポーネントの亀裂や破損です。これらはよく理解されていますが、他の2つの形式の非線形性は見過ごされがちです。接触の影響と「非線形ジオメトリ」の影響です。これら3つの形式の非線形性はすべて製造プロセスの結果である可能性があり、すべてが 3D で容易にモデル化、分析、および後処理されます。 EXPERIENCEプラットフォーム。
これらの製造効果を示す2つの例を評価しました。特に、システムに対する製造効果の影響を検討する際に、それぞれがどのように役割を果たすことができるかに焦点を当てています。
- 下部コントロールアームの圧入接続:
接触は一般にエンジニアによってよく理解されています。2つ以上のコンポーネントが互いに「衝突」し、それらの間で力が伝達され、応力やひずみが発生します。多くの場合考慮されないが、その意味において非常に重要になる可能性がある接触の例は、「圧入」の例です。圧入では、わずかに大きい外側セクションの1つのコンポーネントが、小さいセクションの別のコンポーネントに「強制」されるため、この名前が付けられています。圧入は、競合する要件のバランスを取る必要があります。部品間の干渉が少なすぎると、簡単に引き抜かれ、部品の分離によってシステムの整合性が損なわれる可能性があります。ただし、干渉が大きすぎると、高い応力とひずみが発生し、一方または両方の部品が破損します。
3D 内のシミュレーションモジュール EXPERIENCEプラットフォームを使用すると、(単純化されたアプローチではなく)そのような圧入をキャプチャできるだけでなく、圧入自体に起因する結果として生じる応力と、それらの圧入応力を調査するために、干渉の変動を考慮することもできます。 「標準」ローディングに含まれています。圧入効果を考慮しないと、壊滅的な結果を招く可能性があります。
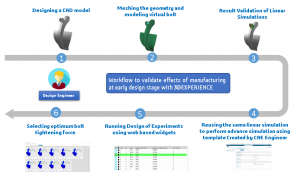
上記の例に示されているように、シミュレーション中に圧入の影響を考慮しないと、下部のコントロールアーム(圧入の一般的な例)が予期せず失敗する可能性があります。左側の結果は誤解を招くものであり、メーカーの保証の問題を引き起こす可能性があります。このような予期しない障害やリコールも、OEMの評判に影響を与える可能性があります。
多くの場合、業界では、コンポーネントの詳細な分析中に圧入効果が考慮されます。設計の初期段階で過剰な圧入を検出して修正すると、プロジェクト全体の時間とコストを節約できます。
以下に、 3D をまとめました。 これを達成するためのエクスペリエンスワークフロー:
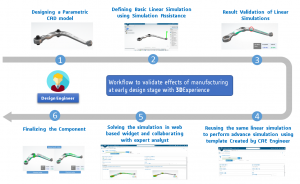
- パラメトリックCADモデリング:
3D のパラメータベースの設計 EXPERIENCEプラットフォームは、さまざまな構成の設計をテストする可能性を活用します。下の画像に示すように、下部コントロールアームとブッシングの間の干渉は、設計パラメータによって定義および変更できます。
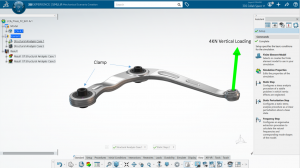
- 統合されたモデリングとシミュレーション:
CADモデリングとシミュレーション用の統合プラットフォームにより、設計者は設計されたコンポーネントをシミュレーションエンジニアに渡す前に簡単に分析できます。 3D でのシミュレーション支援 EXPERIENCEプラットフォームは、専門家でないアナリストでも、モデルを専門家のアナリストに渡す前に、基本的な線形および非線形シミュレーションを実行するようにガイドできます。この場合、4KNの垂直荷重と2.5KNの横方向(X方向)荷重の2つの別々のシミュレーションケースが定義されています。設計エンジニアレベルでの非線形効果を無視するために、ブッシングは下部コントロールアームに接続され、ブッシュの内筒はクランプされています。
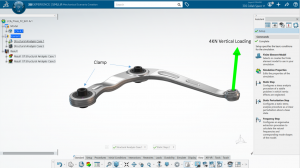
- 高度な非線形シミュレーションを実行するための線形シミュレーションの再利用:
詳細で正確な調査のために、設計エンジニアは、シミュレーションに圧入の影響を含めるために、ブッシングと下部コントロールアームの間の接続パラメーターを変更できます。 CADとFEMの関連性により、線形シミュレーション内で新しいシミュレーション機能を定義したり、既存の機能を変更したりすることが容易になります。機能マネージャーは、定義されたシミュレーション機能の統合ビューを提供し、最小限のマウスクリックで非常に簡単に変更できるようにします。
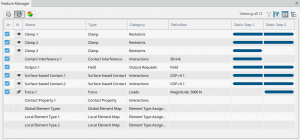
- 自動化とコラボレーション:
専門のアナリストは、明確に定義された特定のワークフローのシミュレーションテンプレートを定義し、設計エンジニアが製造効果を考慮しながら詳細な分析を実行できるようにすることができます。これらの事前定義されたシミュレーションを実行するためのWebベースのウィジェットは、設計者とシミュレーションエンジニアの間の効果的なコラボレーションを促進し、設計を共同レビューして完成させることができます。
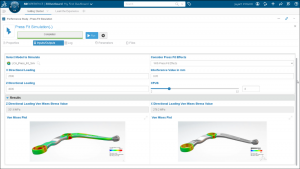
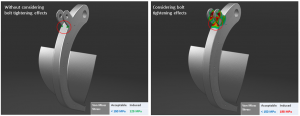
したがって、 3D の包括的なツール EXPERIENCEプラットフォームにより、設計の初期段階で圧入干渉を最適化し、不要な故障やリコールを回避できます。
- クレビスジョイントのボルトモデリング:
製造効果の2番目の例は、クレビスジョイントの例です。クレビスジョイントは、ピンまたはボルトが通過するU字型のリンケージ(「フォークエンド」と呼ばれることもあります)で構成される単純なカップリングです。このピンは通常、リンケージまたはロッドに取り付けられ、リンケージがピンを中心に回転しながら、他のすべての方向でフォークエンドに「固定」されます。
クレビスジョイントは無数の製品で使用されており、自動車や重機のサスペンション、産業機械用途、航空宇宙リンケージ、およびその他のさまざまなユースケースで非常に一般的です。それらは非常に小さく、安価な家庭用品のジョイントとして単純な小さな「ピン」を使用できますが、産業機器や大型機械の場合、人を上回るほど大きく、「ピン」のように非常に大きなボルトが必要になることがよくあります。大規模な機械用途では、ボルト自体にしっかりとトルクをかける必要があるため、フォークの端をロッドに単に「接続」するだけでは不十分なことがよくあります。これにより、「動作負荷」が考慮される前に、部品に製造ストレスが加わる可能性があります。これらのボルトで固定された荷重は、フォークの端を「曲げる」傾向があり、大きな予応力が発生する可能性があります。これらの製造応力を無視すると、動作荷重の安全率が不正確になり、非保守的なピーク荷重応力が発生し、疲労寿命が過大に予測される可能性があります。
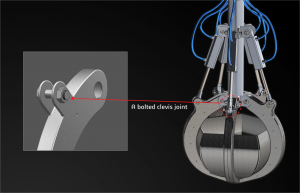
このジョーグリッパーでは、ボルトで固定されたクレビスジョイントを使用して、リンクをジョーコンポーネントに接続します。このようなアセンブリの場合、切断を回避するために、大きなボルト(関連する高いボルトの見せかけを伴う)を使用する必要があります。ボルトの負荷により、クレビスジョイントフォークが一緒に「引っ張られ」、アセンブリの応力が発生します。頑丈な機器は過剰に設計されていることが多いため、このような高価な機器のダウンタイムのリスクを冒すよりも、ある程度の質量を追加することをお勧めします。ただし、安全率が高い場合でも、これらの製造効果が運用負荷とどのように組み合わされるかを考慮することが重要です。
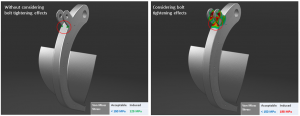
図9に示すシミュレーション結果の場合、操作負荷自体により、フォークにかなり適度な応力が発生し、目標応力よりもほぼ20%低くなります。ただし、運用上のストレスに加えて製造によるストレスを考慮すると、実際の結果は目標よりも30%高くなります。このようなストレスは、歩留まりをはるかに下回りますが、それでも最終的にコンポーネントの疲労を引き起こし、フィールド障害や運用上のダウンタイムを引き起こす可能性があります。したがって、これらの問題を回避するには、最適なボルト締め付け力を選択することが非常に重要です。 3D EXPERINCEプラットフォームは、次のワークフローに要約されているように、これらの種類のシミュレーションを実行するための設計に適したツールを提供します。
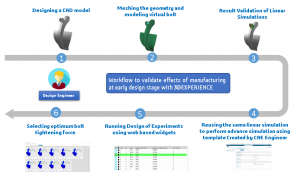
- 仮想ボルトのモデリング:
締め付けの効果を研究するためにボルトCADジオメトリを定義すると、設計エンジニアにとって不必要な複雑さ(接触による非線形性など)が含まれる可能性があります。したがって、 3D の仮想ボルト定義ツール EXPERINCEは、ボルト表現をFEエンティティとして定義し、プリロードで締め付け効果を調査できるようにするための簡略化されたアプローチを提供します。設計者は、パーツのエッジを選択するか、ボルト検出を使用してクレビスジョイントの位置に仮想ボルトを定義するだけです。
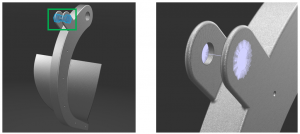
- 線形シミュレーションの定義:
圧入の例と同様に、シミュレーション支援は、設計エンジニアがシミュレーションをセットアップするようにガイドできます。面、エッジ、頂点などのCADフィーチャーを選択することで、設計エンジニアは荷重と境界条件を簡単に定義できます。この場合、ジョーは底面でクランプされ、10KNの荷重がクレビスジョイントに適用されます。
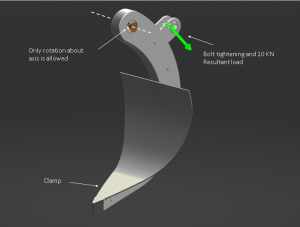
- DOEと最適化のカスタムテンプレート:
エキスパートアナリストは、設計エンジニアがクレビスジョイントに対するボルト締め付け力のさまざまな値の影響を調査するためのWebベースのシミュレーションテンプレートを定義できます。実験計画は、専門家のアナリストをループに巻き込むことなく、設計の初期段階で形成できます。この場合、500Nの差で1KNから5KNまで変化するボルトの予荷重の影響が、プロセスコンポーザーDOEテンプレートを使用して調査されます。
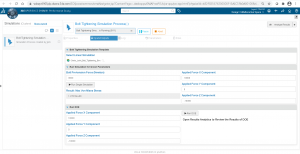
- 結果分析でのWebベースの結果検証:
プロセスが完了すると、設計エンジニアはエキスパートアナリストと協力して、結果分析と呼ばれるWebベースのウィジェットで結果を視覚化できます。荷重やボルト締め力などの入力パラメータを変更するだけで、設計者は同様の用途を持つさまざまなモデルにテンプレートを再利用できます。下の画像に示すように、設計エンジニアは、2KNを超えるボルト力が許容限界(150 MPa)を超える応力を超える可能性があると結論付けることができます。
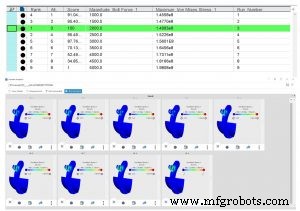
したがって、専門のCAEエンジニアはより高度なシミュレーションに集中でき、設計エンジニアは設計の初期段階で製造効果を処理し、全体的なプロセス時間とコストを節約します。
結論:
設計の早い段階で製造効果を考慮すれば、設計における真の「安全率」をより正確に理解することができます。 3D のデザイナーフレンドリーなツール EXPERIENCEプラットフォームは、製品のパフォーマンスをより一貫して予測するのに役立ち、その結果、顧客の保証コスト、リコールコスト、および運用コストを削減できます。
次のサイトにアクセスして、すべての輸送およびモビリティソリューションをご覧ください:
https://www.3ds.com/products-services/simulia/solutions/transportation-mobility/
産業機器