カスタムツーリング、ワークホールディングがローターを形作るのに役立ちます
かん合のためのより正確な機械加工プロセスを開発することによりヘリカル ローター、このホイップル スーパーチャージャーのスーパーチャージャー モデルは、より効率的に空気をエンジンに送り込み、より高い馬力を得ることができます。カスタム ワークホールディングとフォーム ツールにより、同社は B 軸ターンミルで 1 回のセットアップでスーパーチャージャー ローターを正確にフライス加工できます。
Fresno's Whipple Superchargers は、1987 年に元レース クルー チーフで自動車所有者の Art Whipple によって設立され、自動車やマリン レーサー、およびエンジンのパフォーマンスを向上させようとしている他の人向けの 2 軸スクリュー スーパーチャージャーを製造しています。これらのタイプの「パワーアダー」(ターボチャージャーと亜酸化窒素はその他)は、エンジンが自力で引き出せる以上の追加の空気をエンジンに導入します。より多くの空気は、より多くの燃料を追加できることを意味し、本質的にエンジンの排気量と馬力出力を増加させます。
ここで重要なのは、スーパーチャージャー ケーシング内の 2 つのヘリカル ローターの正確な非接触噛み合わせです。ホイップル デザインでは、オス ローターには 3 つのヘリカル ローブがあり、メス ローターには 4 つのヘリカル ローブがあります、とスーパーチャージャー デザイナーのギャレット ブライトは説明します。これらは互いに反対方向に回転し、非常に接近しています。それぞれのローブが空気入口ポートを通過すると、空気はローターとケーシングの間に閉じ込められます。ローターの回転により、空気が占めるスペースが徐々に減少し、圧縮されます。圧縮は、ローブの内側の空間が出口ポートに露出するまで続きます。出口ポートを通して、大気圧よりも高い空気がエンジンの上にある吸気マニホールドに排出されます。
スーパーチャージャーの効率は、相手ローターとケーシングの間のシール効果に依存します。以前、ホイップルは、外部の会社によって製造および供給されたローターのみを使用していました。一部のスーパーチャージャーモデルには、これらの供給されたローターをまだ使用しています。しかし、同社はその後、社内で独自のローターの設計と機械加工を開始しました。同社が開発した機械加工プロセスは、サプライヤーが提供するものよりも円筒形で正確なローターを製造し、その結果、スーパーチャージャーの設計はそれらよりも 5% 効率的になりました。付属のローターを使用してください。
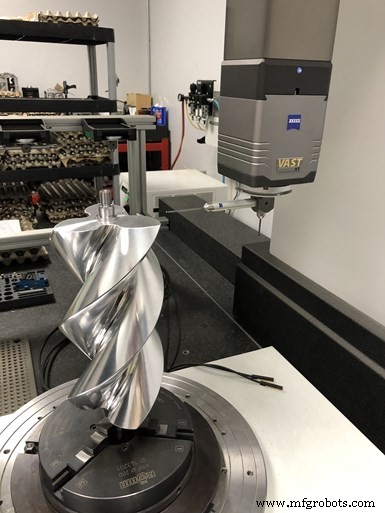
この CMM で行われた測定により、Whipple は判断できました供給されたローターと社内の機械のローターの精度。その目標は、対になるローター間に 125 ミクロンのクリアランスを達成することです。これは、内部のマルチタスク加工機能で達成できるようになりました。
Bright 氏は、Whipple が Zeiss Accura 座標測定機 (CMM) で取得したサプライヤーのローターの測定結果を見て、独自のローターを機械加工することに駆り立てられたと説明しています。この CMM は、ロータリー テーブル、Zeiss の Vast スキャニング テクノロジー、Calypso 測定ソフトウェアの Gear Pro オプションを備えています。ブライト氏によると、このソフトウェアは、オスとメスのローターのらせんプロファイルに特定の制御点を割り当てて、それらの点での 2 つの間のクリアランスを決定できるため、嵌合ローターの測定に特に効果的です。彼は、約 125 ミクロンのクリアランスを達成することを目標として、各ローターのプロファイルを ±63 ミクロンにする必要があると判断しました。 Whipple はローター ベンダーからそれを得ていませんでした。
機械加工の社内導入
同社の成形工具を使用した社内のローター加工プロセスは、サプライヤーのものと似ていますが、剛性を高めるためにワーク保持の変更が加えられています。
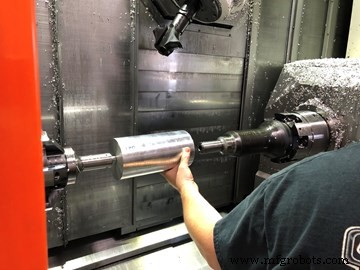
オペレーターが 6061 アルミニウム ローター ブランクをターンミル、機械のメイン スピンドル、サブスピンドル クランプをシャフトの突き出たスチール シャフト ジャーナルに取り付けます。
この用途のために数年前に購入したマシンは、B 軸フライス ヘッドを備えた Mazak Integrex e-420H-S II ターン ミルです。実際、このターンミルは旋削を行いません。
円筒状の 6061 アルミニウム ローター ブランクは、最初に別の機械で縦方向に中央にドリルで穴を開け、スチール シャフトを圧入できるようにします。オペレーターがブランクを Integrex にロードすると、機械のメイン スピンドルとサブスピンドルがシャフトの突き出たジャーナルをクランプします。次に、マシンの B 軸を大幅に傾けて、その角度で目的のローター フルート プロファイルに一致するカスタム フォーム ツールを方向付けます。最後に、スピニング フォーム ツールを Z 軸に沿って動かしながら、ローターをゆっくりと回転させて、複数のパスで各フルートを作成します。
当初、Whipple は延長された長さのプルバック スタイルの ER コレットを使用して、シャフト ジャーナルを固定していました。ブランクをサブスピンドルから離して配置し、B 軸スピンドルが成形工具を収容するために必要なだけサブスピンドルのチャック上で傾斜するのに十分なクリアランスを確保するために、延長された長さが必要でした。しかし、これらのコレットのプルバック機能により、ローター ブランクのロードに時間がかかり、困難でした。コレットの締め付け (引き戻しの結果) は、メイン スピンドルに過度の負荷をかけました。びびりや表面仕上げ不良の原因となります。その結果、作業者は負荷の大部分が取り除かれるまでクランプとクランプの繰り返しを繰り返しましたが、これには通常 10 分かかりました。さらに、Whipple はコレットを何度も締めたり緩めたりして摩耗したため、頻繁に交換していました。
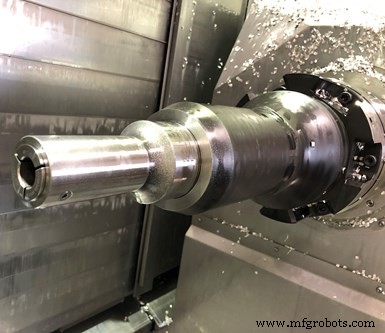
以前に使用されていた ER コレットとは異なり、デッド-長さのコレットはワークピースを引っ張ったり、排除しなければならない主軸に負荷をかけたりしません。これにより、セットアップが 10 分から 2 分に短縮されました。
このプロジェクトで Whipple と協力した Mazak のアプリケーション エンジニアである Kellen Bush のアドバイスを受けて、同社は Hainbuch に連絡を取り、代替のワーク保持アプローチを考案しました。 Hainbuch のセールス マネージャーである Tom Chambers 氏は、同社のカスタム ワーク保持ソリューションは、機械の B 軸を必要な角度まで干渉することなく傾けることができるようにするために必要な拡張リーチを提供するだけでなく、交換を簡素化しながらより高い剛性も提供すると説明しています。これは主に、プルバック タイプの代わりにデッドレングス コレットが使用されているため可能です。 Chambers 氏は、デッドレングスのコレットは「空間でクランプする」と述べています。これは、コレットがクランプされているときにローターブランクが動かないことを意味します。その結果、ダイヤルアウトしなければならない追加の負荷が主軸にかかることはありません。切り替えにかかる時間はわずか 2 分です。
Whipple がローターを機械加工するために使用する京セラ Unimerco フォーム ツール (Whipple のローター サプライヤーも同様) は、実際には金属の切断には一般的に使用されていません。京セラ ユニメルコのセールス マネージャーである Anders Varga 氏は、このタイプのツールは通常、木材、複合材、その他の繊維材料の切断に使用されると述べています。これは主に、金属ワークピースと長いインサート刃先との間の接触面積が大きい結果として工具にかかる圧力の大きさによるものです。これらのツールがこのローター加工アプリケーションで使用できるということは、Capto スピンドル インターフェースとそのカスタム ワーク保持を備えた機械の剛性を物語っています。
ローターのヘリカル フルート プロファイル (Bright が改良したプロファイル) に一致するフォーム ツールを使用すると、フルートを彫るために複数のエンド ミルを使用した場合に必要になる可能性がある研磨が不要になります。ローターは、ローブが可能な限り大きくなるように機械加工されていますが、その後の独自のコーティングを可能にするためにわずかに小さめです。 Whipple では通常、オスとメスの両方のローター用に 2 つの荒削りツールと 3 つの仕上げツールを手元に置いています。このツールは、コーティングされていないマイクログレイン カーバイド インサートを使用しています。荒削りツールのインサートは、ネジでツール本体に取り付けられています。仕上げツールがろう付けされます。
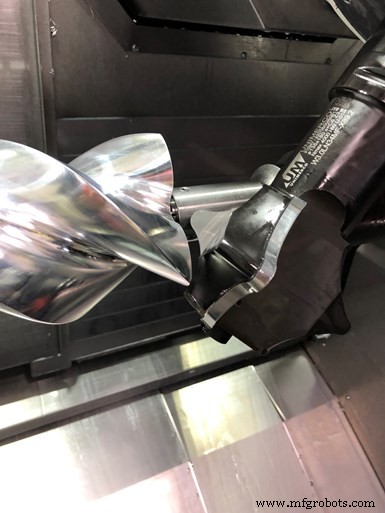
フォーム ツールを使用することで、Whipple にはエンドミルを使用してローター フルートを作成する場合と同様に、二次仕上げを行います。
現在、この機械加工プロセスは、嵌合するローター間のブライトの 125 ミクロンのクリアランス目標を達成するだけでなく、ローターの端から端までの円筒度がより一貫しています。彼によると、元のワーク保持アプローチでは、ローターの一方の端と他方の端の円筒度の差は 10 ミクロンにもなる可能性があります。それは1ミクロンに縮小されました。ローターのサイクル時間も少し速くなります。オスローターのサイクル時間は 14 分、メスローターは 20 分です。しかし、ホイップルにとって、これは肉汁です。その主な目標は、より高いローター加工精度と迅速な切り替えを実現することでした。
産業機器
- Mecademic Roboticsは、その小さなロボットで巨大な市場に拡大します
- EnergidソフトウェアをGemini水中ロボットに統合するためのSchillingRobotics
- ラピッドツーリングサービスとその効果的なアプリケーション
- 3Dプリントされた工具がプロトタイピングの未来をどのように形作ることができるか
- スイス型機械用工具
- タフなものを回す
- 無駄のない接続を行う
- ライブツーリングを始めることを考えていますか?知っておくべきことは次のとおりです
- カスタム金属加工の5つの主な利点
- ケブラーとは何ですか?ショートガイド
- TE Connectivityは、デジタルトランスフォーメーションの過程で製造の自動化を実践します