3Dフィラメントワインディングにより、車両の着座コンセプトが可能になります
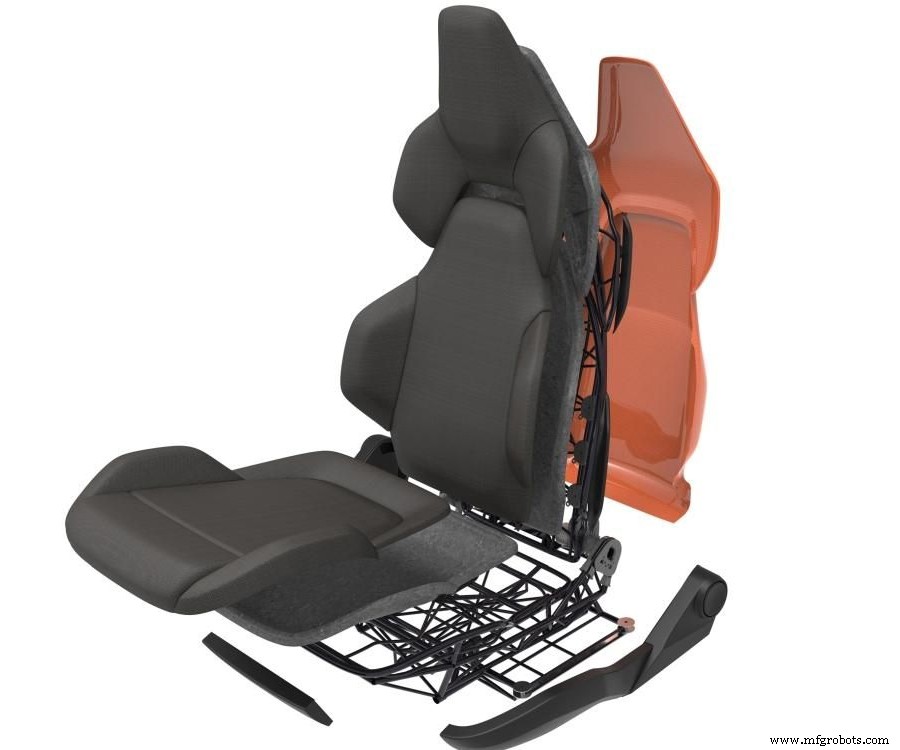
持続可能性と環境への責任は、自動車産業における技術トレンドのますます一般的な推進力になりつつあります。低エネルギーおよび低排出ガス車は国際的な自動車セクターの優先事項になり、電気自動車や都市空中移動(UAM)などの代替輸送技術へのトレンドが勢いを増しています。 OEMは、これらの将来の移動手段を可能にするものとして、新しい材料とプロセスを探していますが、自動車セクターの変化は遅いことがよくあります。新しい材料とプロセスが完全に採用されるためには、それらは適格であるだけでなく、費用効果が高く、大量生産を可能にする必要があります。
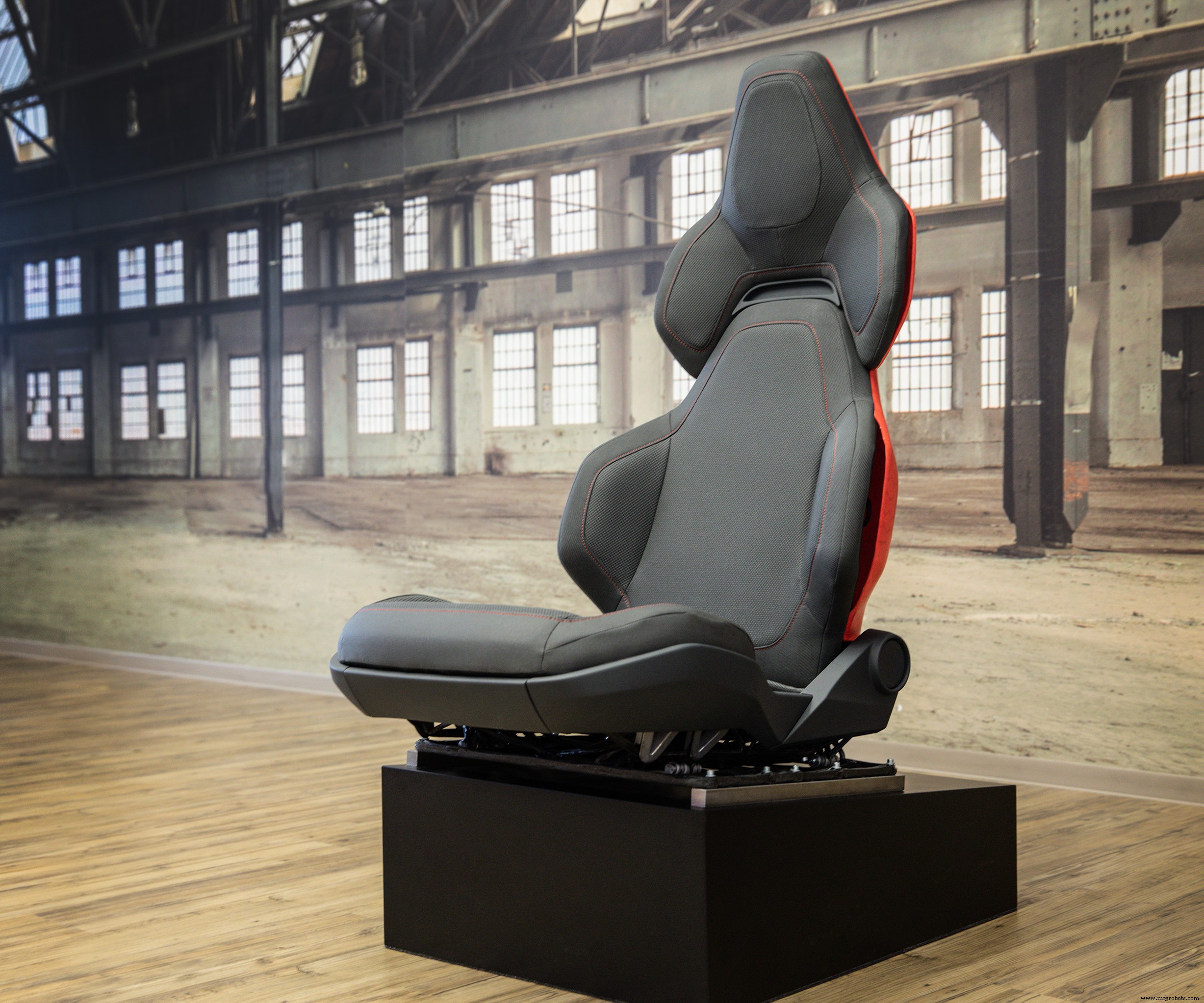
超軽量シート。 Ultra Leichtbausitz(ULBS)の座席コンセプトは、テクノロジーの組み合わせを使用した複数の企業間のコラボレーションを通じて開発されました。ソース| csi entwicklungstechnik
最近、自動車セクター、およびハイパーカーやエアタクシーなどの新興市場に可能性を秘めた革新的なプロジェクトにより、新しい材料、プロセス、テクノロジー、および企業間の緊密なコラボレーションにより、次世代の輸送手段がどのように実現されるかが実証されました。このプロジェクトの目標は、最先端の発電技術を使用してカーシートを完全に再考し、適切な場所で必要なだけ適切な材料を使用してこれを行うことでした。および 迅速に結果を出すため。結果として得られた超軽量の金属複合ハイブリッド車のシートプロトタイプは、シミュレーション主導の設計アプローチ、機敏なプロジェクト管理方法、関係する企業間の緊密な協力とシステム統合を通じて、設計から製造までわずか7か月で開発されました。
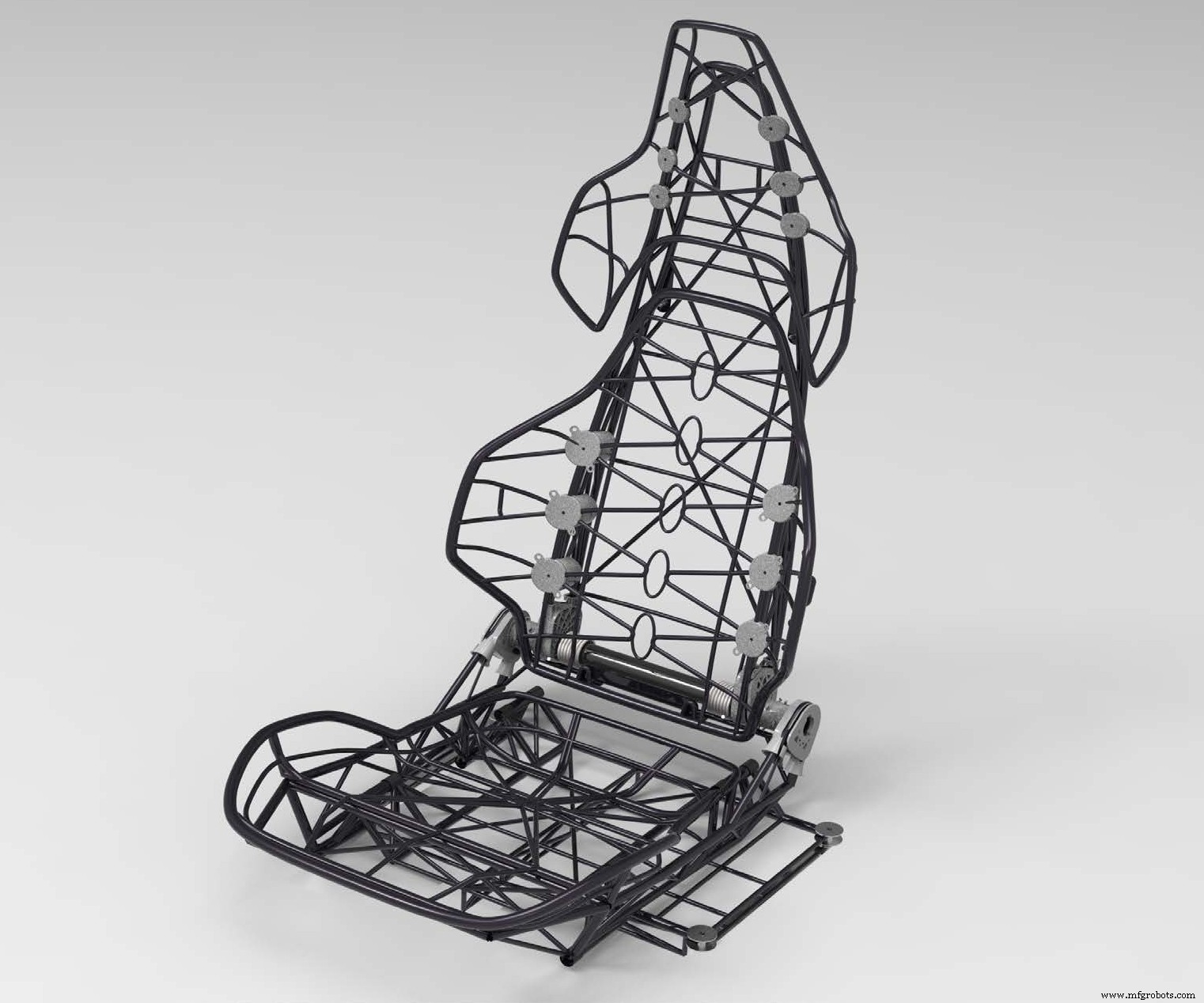
より良い座席の構築
Ultraleichtbausitz(ULBS)の超軽量シート実現可能性調査は、テクノロジーの組み合わせを使用した複数の企業間のコラボレーションを通じて開発されました。プロジェクトのビジョンは、グループの言葉で言えば、「重量の最適化の点で市場で傑出した超軽量の座席コンセプトを作成すること」でした。開始企業csientwicklungstechnik GmbH(csi、Neckarsulm、Germany)、Alba Tooling&Engineering(Forstau、Austria)、Automotive Management Consulting(AMC、Penzberg、Germany)は、Covestro(Leverkusen、Germany)、LBK Fertigungと共同で、プロトタイプの座席コンセプトを開発しました。 (フリートベルク、ドイツ)、ロバートホフマン(リヒテンフェルス、ドイツ)、3D | CORE(ヘルフォルト、ドイツ)。
共同プロジェクトの結果、重量が10 kg強のシートのプロトタイプが作成されました。これには、クッション、構造フレーム、機能インサート、および車両に取り付けることができるシートコンソールが含まれています。シートは、市場に出回っている同等の軽量シートよりも20%軽量で、その多くはアフターマーケットシートです。 CSIで軽量設計を担当するULBSプロジェクトリーダーのStefanHerrmannによると、現在、12kg未満の重量の競合するシートは市場にありません。
「しかし、アフターマーケットの座席には重量の定義に座席コンソールが含まれていないことが多いため、直接比較することはできません」とHerrmann氏は言います。同様の重量。既存のシートは、多くの場合、軽量ではあるがそれほど快適ではないバケットシート、またははるかに重量の大きい従来のスーパースポーツシートです。」
ULBSはいくつかの革新的な技術を特徴としており、その中で3Dのプロセス技術xFKに基づくファイバーロービングスケルトン構造が最も重要な役割を果たしています。 (3Dおよびその他のフィラメントワインディングテクノロジーでのxFKの詳細については、「フィラメントワインディング、再発明」を参照してください。)エンドレスファイバーロービングデポジションの受賞歴のあるテクノロジーの基本的な重要性は、シミュレーション駆動および材料の設計の自由度にあります。荷重方向に正確に最適化された繊維配置と、繊維材料のシンプルでコスト効率の高い無駄のないアプリケーション。このフレームワーク構造の荷重伝達には、3Dプリントされた部品が使用されています。背もたれの備品など、負荷が最も高い領域では、シートは高強度と高弾性率のステンレス鋼で作られた3Dプリント構造を使用しています。負荷の少ないエリアでは、アルミニウムの3Dプリントが使用されます。
csi entwicklungstechnikは、車体白(BIW)構造、および炭素繊維強化ポリマー(CFRP)や添加剤製造などの事業分野を備えた自動車の内外装を専門とするエンジニアリング会社であり、 AMCによって開始されたアイデア。 csiは、プロジェクトのスタイリング、サーフェシング、コンセプト、シミュレーション、設計エンジニアリング、およびプロジェクト管理を提供しました。
Herrmann氏は次のように説明しています。「csiは、デジタルプロセスチェーンのドメインでの作業パッケージ(スタイリング、エンジニアリングデザイン、サーフェシングデザイン、CAEシミュレーション、トポロジシミュレーション、検証シミュレーション、プロジェクトの仮想確認)を担当しました。」
彼は、ULBSプロジェクトを注目に値するのは、革新的な材料と製造方法の使用だけでなく、パートナー間の緊密なコラボレーションを使用した短い7か月の時間枠内での新しいコンポーネント設計を含む複雑な部品の開発であると強調します。
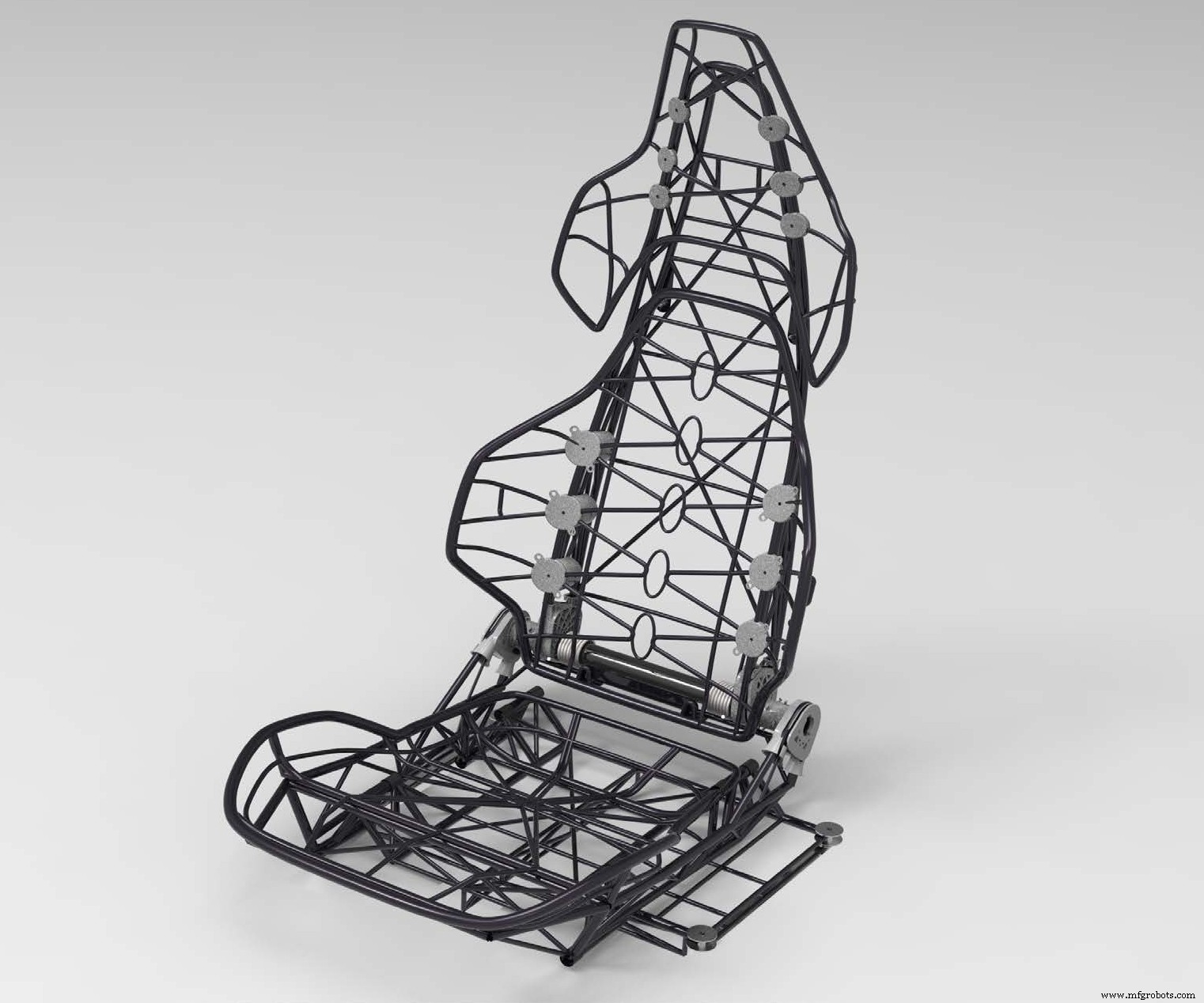
フィラメントワインドシートフレーム。 ULBSプロジェクトの軽量化の多くは、AMCの3DファイバーワインディングプロセステクノロジーxFKによるものです。ソース| csi entwicklungstechnik
フレームを巻く
ULBSプロジェクトの軽量化の多くは、AMCの3DでのxFK、巻線コンポーネント用の柔軟性が高く、構成可能で、費用効果が高く、持続可能な繊維複合技術によるものです。
3DのxFKは、さまざまな業界や市場セグメントのさまざまな製品やアプリケーションですでに使用されています。 SGL Group Wiesbaden、Germany)は、国際複合材ショーJEC World 2018で、この技術によって製造された自動車および自転車の部品をいくつか展示しました。展示された部品の1つ、AMCが開発したカーボンファイバー自転車チェーンリングは、重量を最大70%削減すると言われていますアルミニウムバージョンと比較して。
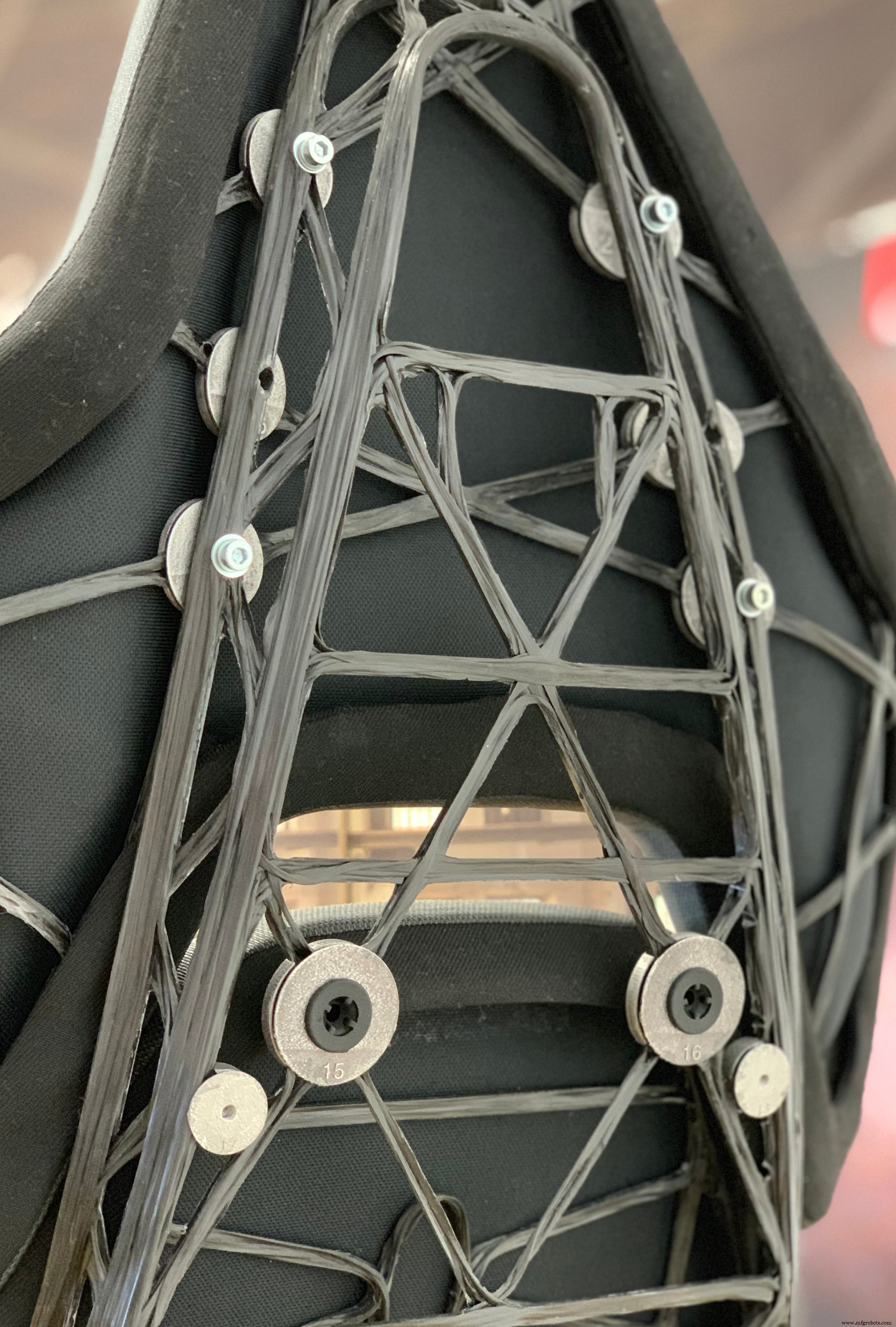
巻線ブッシング。 熱硬化性樹脂を含浸させたファイバーロービングを位置決め固定具に巻き付け、各部品の負荷と目的の機能に合わせてファイバーを配置できるようにします。ソース| csi entwicklungstechnik
3DプロセスのxFKは、熱硬化性樹脂を含浸させた連続繊維を使用して、耐荷重構造を無駄なく巻き上げます。エポキシ樹脂で飽和させたファイバーロービングをポジショニングフィクスチャまたは巻線ブッシングに巻き付け、各部品の負荷と目的の機能に合わせてファイバーを特別に配置できるようにします。
「3DでのxFKの主な利点の1つは、構造物への荷重伝達と荷重導入に関する弱点がなくなることです」とHerrmann氏は言います。彼は、弱点は構造の連続体ではなく、荷重が構造に導入される領域、特に隣接するコンポーネントが構造に接続されている領域にあることが多いと説明しています。 xFK in 3Dテクノロジーにより、接続間での荷重伝達が可能になり、必要なコンポーネント機能と荷重ケースに応じてファイバーを位置合わせし、3次元で製造することができます。
フィラメントワインディングプロセスには、追加の利点もあります。このプロセスは、材料の無駄を最小限に抑えるのに役立ちます。無駄になるファイバーロービングの1%未満です。
csiは、xFKを3Dの強みとして認識し、AMCのテクノロジー責任者であるClaus GeorgBayreuther博士のコンサルタントの下で構築されるULBSシートフレームを設計しました。
「csiエンジニア、AMCコンサルタント、Albaのツールの専門家と協力して、3DプロセスでxFKを使用して製造されるシートフレームのこのコンセプトと構造を開発しました」と、テクノロジーコンサルタントで3DテクノロジーのxFKのイニシエーターであるPeterFassbaenderは述べています。
アルバはCFRPシートフレーム用の工具を製造し、エンジニアリングサポートを提供しました。また、シートフレームは炭素繊維で巻かれていますが、天然繊維や玄武岩繊維も適しています。
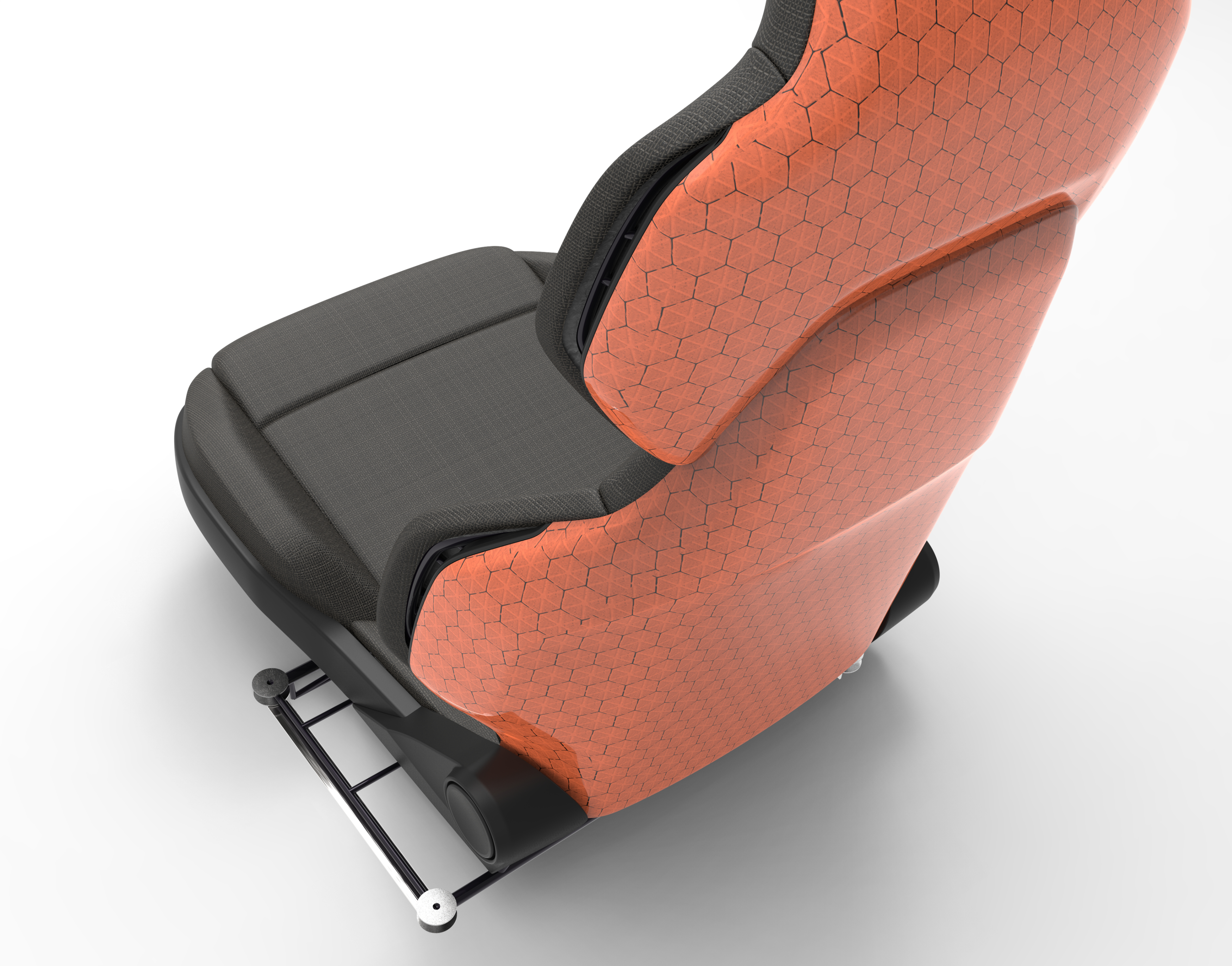
新しいテクノロジー。 ULBSプロトタイプは、層内補強コア(IRC)材料で作られたバックパネルシェルと、熱可塑性ポリウレタン(TPU)で作られた3Dプリントされたシート背もたれクッションを含む新しいテクノロジーの組み合わせを使用しています。ソース| csi entwicklungstechnik
ハイブリッド材料構造
フレームに加えて、ULBSプロトタイプには他のいくつかの新しいイノベーションが含まれています。工具を供給したAlbaは、シートのフォームボディの工具、エンジニアリング、製造も供給し、シートの組み立てを実行しました。ファイバーフリースマットがシートのCFRPフレームを覆い、その後3DプリントされたPURフォームカバーで覆われます。シートクッションエリアは伝統的なフォームで作られています。
シートバックレストのバックパネルシェル構造に、層内補強コア(IRC)素材である3D | COREを採用することで、さらなる軽量化を実現しました。この材料は、層内補強コア(IRC)材料であり、押し出しポリスチレン(XPS)とポリエチレンテレフタレート(PET)フォームコアボディが統合されたハニカムパターンで構成された構造サンドイッチコアです。複合部品の製造中、ハニカム構造は樹脂で満たされているため、層内強度が高くなります。 3D | Coreは、ガラス繊維の2つの層の間に組み立てられてプリフォームを作成します。プリフォームには、真空アシスト樹脂トランスファー成形(VA-RTM)を使用して熱可塑性エポキシ樹脂が注入されます。
コベストロは、ファイバーフリースマットのバインダーとしてDispercoll接着剤を供給し、3Dプリントされた背もたれクッションも提供しました。 Herrmannによると、Dispercollの機械的特性は優れた耐摩耗性を提供します。これは、クッションとフレームの間の表面接触によってフリースが時間の経過とともに摩耗する可能性があるため重要です。
「シングルファイバーロービングを使用している場合、それをテキスタイルに入れると、ハードCFRPパーツとフリースマットの間で微動が発生します。シートフレームのコンポーネントがテキスタイルをこすって破壊する可能性があります」とHerrmann氏は説明します。
従来のシートは通常、クッションを支える表面積が大きく、この問題はありません。ただし、3DのxFKでは、フレーム構造のために接触表面積が小さくなります。
「3D構造のxFKがフリース生地を押すときは、特定の耐久性のあるバインダーが必要です。これは、Dispercollがこのコンテキストで提供するものです」とHerrmann氏は付け加えます。
コベストロは、世界初の3Dプリントクッションと言われるものも提供しました。シートの背もたれには通常、工具を多用するフォームが使用されますが、TPU(熱可塑性ポリウレタン)で作られた3Dプリントのシートの背もたれクッションを使用すると、ULBSシートの美観に関する柔軟性と適応性がさらに向上します。機能統合オプションと快適さ。
未来の席
ULBSプロジェクトはいくつかの目標を達成します。結果として得られるコンセプトは、まだ市場に出回っていませんが、ハイパーカー、エアタクシー、超軽量車両、マイクロモビリティ、ヘリコプター、マルチコプターなどの多くのニッチ市場にサービスを提供する可能性があります と航空。確かに生産用カーシートよりも高価ですが、ULBSは廃棄物を最小限に抑え、それによって材料費を削減するいくつかの技術を実証しています。他の炭素繊維技術と比較すると、3DのxFKは非常に少量の廃棄物を生成します。実際、プロジェクト全体は、最小限のリソースと必要最小限の資料のみを使用することを目的としています。 ULBSは、フレーム構造、クッション、テキスタイルに天然繊維などの再生可能で持続可能な資源を使用する可能性も提供します。
しかし、さらに重要なことは、このプロジェクトは、企業が短く機敏な調整手順を通じて協力することにより、市場投入までの時間を最小限に抑える方法を示しています。また、デザイン思考を使用して、機能要件に焦点を当て、将来のアプリケーションと持続可能性の目標を先取りすることで、製品をアイデアからハードウェアプロトタイプにうまく移行させる良い例です。
ファイバ