溶媒と相対湿度を調整することによるエレクトロスピニングPVDFナノファイバーの二次表面形態の制御
要約
この作業は、単一/二成分溶媒システムと相対湿度を使用して、二次表面形態(多孔質表面、粗い表面、溝付き表面、内部多孔性など)を持つポリフッ化ビニリデン(PVDF)ナノファイバーを直接生成するためのシンプルで信頼性の高い方法を示します。ポリマー、溶媒、水蒸気の間の分子相互作用を体系的に調査することにより、これらの形態の形成に関与するメカニズムを明らかにしました。我々の結果は、二次表面形態の形成には、適切なレベルの相対湿度で、ポリマーの非溶媒である水蒸気の存在が必要であることを証明した。二次表面形態の形成は、溶媒(ACE、DMF、およびそれらの混合物)の蒸発速度、および非溶媒(水)と溶媒の相互拡散と浸透に依存していました。 )。 N 2 の結果 物理吸着-脱着等温線は、マクロ多孔質繊維(> 300 nm)が23.31±4.30 m 2 の最も高い比表面積を示すことを示しました。 / gおよび0.0695±0.007cm 3 の細孔容積 / g、シリコーンオイル、モーターオイル、オリーブオイルでそれぞれ50.58±5.47 g / g、37.74±4.33 g / g、23.96±2.68 g / gの高い吸油能力を実現します。この作業は、エレクトロスピニングによる内部多孔性を備えたマクロ多孔性、粗い、溝付きナノファイバーのさまざまな構造を形成するためのガイドラインとして役立つ可能性があると考えています。
背景
エレクトロスピニングは、ポリマージェットを繊維に放出および伸長するための静電力を伴う繊維形成方法です。このプロセスは現在、直径が数ナノメートルから数マイクロメートルの範囲の繊維を製造しています[1]。ビーズ繊維[2]、多孔質繊維[3]、溝付き繊維[4]、マルチチャネル繊維[5]、リボン繊維[6]、サイドバイサイド繊維[7]、中空繊維[8]を含むエレクトロスピニング繊維のさまざまな形態]、階層型繊維[9]、米粒状ナノコンポジット[10]、バタフライウィング繊維[11]、コアシース繊維[12]、および圧着繊維[13]は、エレクトロスピニングパラメーターを制御することによって形成できます[14]。
エレクトロスピニングされたナノファイバーは、高い比表面積、柔軟性、機能性の容易さ、さまざまな形態と構造、優れた指向性強度、高い多孔性などの優れた特性を示しており、エネルギーハーベスティングなどのさまざまな用途に適した材料形態になっています[15]。センサー[16]、ろ過[17,18,19]、生物医学的応用[20]、セルフクリーニング表面[21,22,23]など。研究により、二次形態(例えば、多孔質表面、溝付き)を調整することにより、エレクトロスピニングされた繊維の表面、粗い表面、および内部多孔性)、それらの特性および挙動は、大幅に強化または変更される可能性があります。たとえば、多孔質繊維は、繊維内細孔の導入による比表面積の増加により、触媒作用、ろ過、生物医学研究などのさまざまな用途で広く使用されています[24]。摩擦面積の増加により、掃気エネルギー装置の電気出力を改善するために粗い繊維が使用されてきた[25]。溝付き繊維は、組織工学および超疎水性表面の分野で大きな可能性を示しています[26]。さらに、比表面積と多孔性を高めると、吸収[27、28]、触媒作用[29、30]などのパフォーマンスが向上します。
以前に、2つの入力チャネルからの液体混合と他の出力チャネルからの混合物の同期エレクトロスピニングを可能にする3つのチャネルを含むマイクロ流体ノズルを使用して、調整可能なマクロ細孔構造と分布を持つポリスチレン繊維の製造を報告しました[3]。 。さらに、高沸点溶媒と低沸点溶媒からなる混合溶媒系を用いたエレクトロスピニングによる溝構造の酢酸酪酸セルロースとポリスチレン繊維の製造を報告しました[4、31]。
この研究では、特別な収集方法や紡糸後処理を必要とせずに、エレクトロスピニングを使用して、マクロ多孔質、粗い、溝のある表面構造と内部細孔を備えたポリフッ化ビニリデン(PVDF)ナノファイバーの製造を示します。ここでは、PVDFはさまざまな溶媒に溶解できるため、モデルとして選択されました。
私たちの知る限り、これまでのところ、相対湿度を制御することにより、内部多孔性を備えたマクロ多孔性(> 300 nm)、粗い、溝のあるエレクトロスピニングPVDFナノファイバーの形成を操作する研究は体系的に調査されていません。ここでは、単一および二成分溶媒システムの両方を使用して、相対湿度の4つのレベル(5%、25%、45%、および65%)でのPVDF溶液のエレクトロスピニングを報告しました。この作業の主な目的は、さまざまなレベルの相対湿度を使用して、固体および多孔質の内部構造を持つマクロ多孔質、粗い、および溝付き繊維の製造の実現可能性を調査し、それらの形成メカニズムを発見することです。エレクトロスピニングされたPVDF繊維の二次表面形態に対する相対湿度の影響を体系的に調査することにより、相対湿度がPVDF繊維の表面および内部形態を決定する上で重要な役割を果たすと結論付けました。この研究は、エレクトロスピニングによるナノファイバーの二次表面構造の調製に役立つガイドラインを提供することができます。
メソッド
化学薬品および材料
PVDFペレット(Mw =275,000)はSigma-Aldrich、Inc。から購入しました。アセトン(ACE)およびN、N-ジメチルホルムアミド(DMF)は、中国の上海にあるShanghai Chemical Reagents Co.、Ltd。から購入しました。すべての材料はさらに精製することなく使用されました。
二次表面形態を備えたPVDF繊維のエレクトロスピニング
マクロポーラスで粗い溝のある繊維を得るために、18%ACE( w / v )PVDFソリューション、35%DMF( w / v )PVDFソリューション、および25%(ACE / DMF)( w / v )溶媒比(4:1、2:1、1:1、1:2、および1:4)のPVDF溶液をそれぞれ調製し、各溶液をプラスチックシリンジにロードしました。この作業では、溶媒比は体積比であり、溶液濃度は重量/体積( w )でした。 / v )(g / ml)。 21ゲージのシリンジ針を紡糸口金として使用し、高電圧供給業者(Tianjin Dongwen Co.、Ltd。、中国)に接続されたシリンジポンプ(KDS 100、KD Scientific Inc.、米国)に固定しました。接地されたドラムコレクター(長さ40 cm、直径20 cm)を紡糸口金から18 cm離して配置し、回転速度を2 rpmに設定して、ランダムに配向した繊維を得ました。すべての実験は、さまざまなレベルの相対湿度(5%、25%、45%、および65%)の下で20°Cで実行されました。温度は実験室の中央空調システムによって調整され、相対湿度は環境湿度によって制御されました。環境湿度は、加湿器/除湿器を使用して狭いウィンドウ(±2%)でさらに設定できます。すべてのサンプルは、それぞれ1.5 ml / hと18kVの供給速度と印加電圧で準備されました。以前のすべてのパラメーターは、異なる形態と同様の直径を持つ繊維を取得するように調整されました。
三元状態図
曇点曲線は、65%の相対湿度で滴定法によって決定されました。 PVDF溶液は、ACEおよびDMFを使用する単一溶媒システム、およびACE / DMFを1:1の溶媒比で使用する二成分溶媒システムにポリマーを溶解することによって調製された。得られた均質な溶液を、非溶媒として脱イオン水で滴定した。恒久的な濁りの開始時に、溶液の組成と使用された非溶媒の量が記録され、二元状態図を表すために使用された三元状態図にプロットされました[32、33]。
特性評価
エレクトロスピニングされたPVDFナノファイバーの表面形態と断面は、金コーティング後、電界放出型走査電子顕微鏡(FE-SEM)(S-4800、日立製作所、東京、日本)でチェックされました。繊維の断面は、それらを液体窒素に入れ、手動で破壊することによって準備されました。繊維径は、画像解析ソフトウェア(Adobe Acrobat X Pro 10.1.2.45)を使用してSEM画像に従って測定しました。 N 2 物理吸着-脱着等温線(JW-BK132F、北京科学技術株式会社、中国)を測定して、比表面積、細孔分布、および総細孔容積を決定しました。
吸油
吸油量は、25℃で以下の方法で測定しました。次に、1:1の比率の水と油の混合物15 mLを準備し、ビーカーに入れました。さらに、0.3 gの吸着剤をビーカーに追加して1時間油を吸収し、次に湿った吸着剤をスクリーンメッシュに移動し、約40分間排水して、吸着剤に油滴が残らないようにしました。吸油能力は、次の式に従って計算されました。
$$ Q \ kern0.5em =\ kern0.5em \ frac {m_0- {m} _1} {m_1} $$ここで Q は吸油能力(g / g)、 m 0 は、吸油が約40分(g)、 m 排出された後の湿式吸着剤の総質量です。 1 は吸収前の吸着剤の質量(g)です。
結果と考察
エレクトロスピニングされたPVDF繊維の二次形態に対する相対湿度の影響を調べるために、18%( w / v )ACEを使用したPVDFソリューション、35%( w / v )DMFを含むPVDFソリューション、および25%( w / v )ACE / DMF比が異なるPVDF溶液をエレクトロスピニングしました。
ACEからエレクトロスピニングされた繊維
さまざまなレベルの相対湿度でPVDF / ACE溶液から得られた繊維が展示され、比較されています(図1および2)。滑らかな繊維は、相対湿度5%でPVDF / ACE溶液を使用して形成されましたが(図1aおよび追加ファイル1:図S1A)、マクロ多孔質繊維は、相対湿度25%、45%、および65%で生成されました。 (図1b–dおよび追加ファイル1:図S1B-D)。表面細孔の形成は、熱誘起相分離(TIPS)に起因する必要があります[24]。
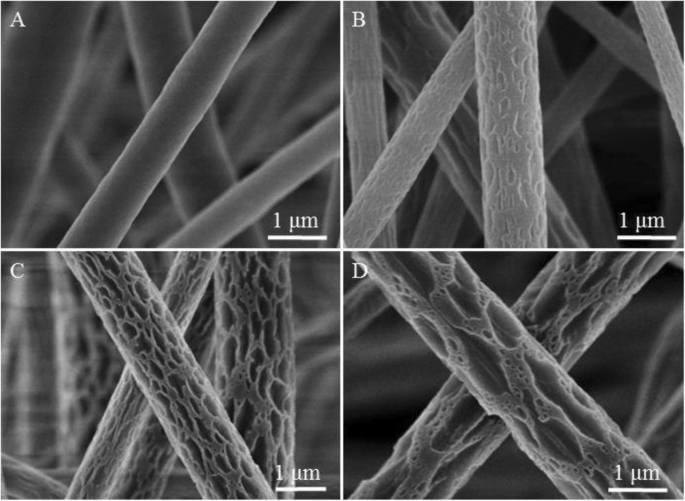
18%( w )のエレクトロスピニングによって作製されたサンプルの代表的なSEM画像 / v )さまざまなレベルの相対湿度でのACEのPVDFソリューション。 a 5%、 b 25%、 c 45%、および d 65%
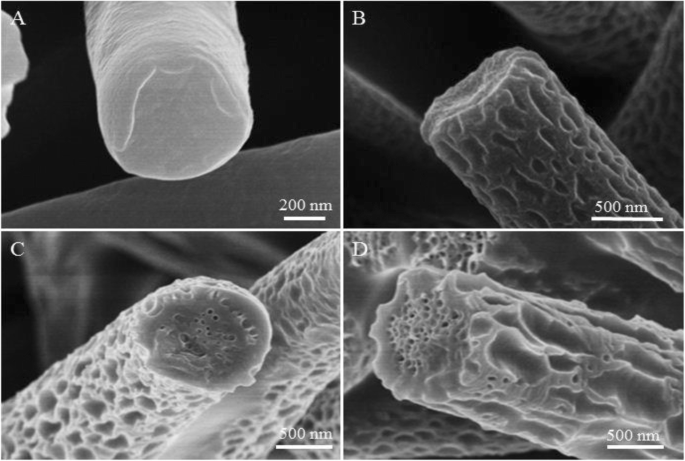
15%( w )のエレクトロスピニングによって作製されたサンプルの断面SEM画像 / v )さまざまなレベルの相対湿度でのACEのPVDFソリューション。 a 5%、 b 25%、 c 45%、および d 65%
PVDF / ACE溶液から形成されたPVDFマクロ多孔質繊維の形成メカニズムを確認するために、調査した相対湿度のさまざまなレベルで形成された繊維の断面を確認しました。相対湿度5%と25%で形成された繊維は内部が固体であり(図2a、b)、内部に細孔のある繊維は相対湿度45%と65%で形成された(図2c、 d)。したがって、相分離がないため、相対湿度5%で表面が滑らかで内部が固体である繊維が形成されたと結論付けることができます。一方、TIPSにより、内部が固体のマクロポーラス繊維が形成されました。一方、内部細孔を備えたマクロポーラス繊維は、TIPSと蒸気誘起相分離(VIPS)の両方が共存するため、45%と65%の相対湿度で形成されました。つまり、揮発性の高い溶媒が蒸発すると、大量の熱を吸収して繊維の表面を冷却し、繊維表面に水滴を凝縮させて引き付けます。相対湿度が高くなると、水滴の蒸発速度が低下し、液滴間の合体によりマクロ液滴が形成され、そのメカニズムは核形成成長(NG)として知られています[34]。凝縮したマクロ水滴が乾燥した後、それらは繊維の表面にマクロ細孔を形成した。一方、繊維を貫通した水滴の一部は、最終的に乾燥して内部の細孔を形成しました。相対湿度が高い場合のマクロ多孔質繊維の形成メカニズムを図3aに示します。相対湿度が高いと、繊維表面に凝縮した水滴の蒸発速度が低下し、NGによりこれらの水滴が合体する時間が長くなります。したがって、繊維の表面のマクロ細孔のサイズは、相対湿度25%で約50 nm、相対湿度45%で約100 nm、相対湿度65%で約400nmに増加しました。 。さまざまなレベルの相対湿度でPVDF / ACEソリューションから得られたすべての表面と内部形態を表1にまとめています。重要なことに、相対湿度を5%から65%に上げると、繊維の直径が約0.77から約1.81μmに増加します(追加ファイル1:図S2A)。
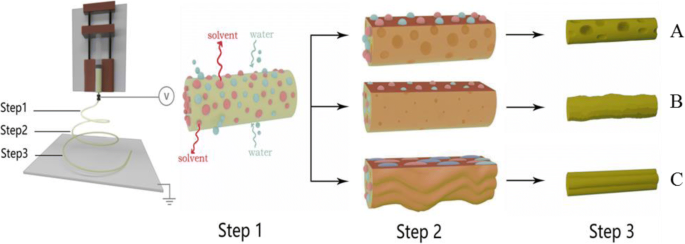
高い相対湿度でのエレクトロスピニング中の溶液ジェットのプロセス図。ステップ1:溶媒の蒸発と水の凝縮、ステップ2:水滴の浸透と細孔の生成、ステップ3:繊維の伸長と固化。 a マクロ多孔質繊維、 b 粗い繊維、および c 溝付きファイバー
DMFからエレクトロスピニングされた繊維
ここでは、35%( w / v )PVDF溶液は、さまざまなレベルの相対湿度(5%、25%、45%、および65%)でエレクトロスピニングされました。
滑らかな繊維は相対湿度5%でPVDF / DMF溶液を使用して生成され(図4aおよび追加ファイル1:図S3A)、粗い繊維は相対湿度25%、45%、および65%で形成されました(図4aおよび追加ファイル1:図S3A)。 。4b–dおよび追加ファイル1:図S3B-D)座屈の不安定性[35]および電気力による伸び[26]による。調査した以前の相対湿度で形成された繊維の断面によると、内部に固体の繊維は5%の相対湿度でのみ得られ(図5a)、内部に細孔のある繊維は相対湿度5%で形成されたことがわかりました。 25%、45%、および65%(図5b–d)。この場合、相分離がないために滑らかな表面と固体の内部で形成された繊維と、VIPSのために粗い表面と内部の細孔で得られた繊維と言えます[24]。言い換えれば、DMFと水蒸気の企業拡散と浸透は、内部に細孔を持つ繊維を形成する上で重要な役割を果たしました。 20°Cの温度では、水の蒸気圧(2.34 kPa)がDMFの蒸気圧(0.36 kPa)よりも高いため、水蒸気が空気との境界面の近くの領域を飽和させたと考えるのが妥当です。そして、最初にジェット、次に非溶媒としての作用により、液体ジェットの表面にPVDFのシースを沈殿させます。固化したPVDF層は、DMFを内部に閉じ込め、その蒸発速度を緩めるのに役立ちました。これにより、水蒸気が表面に急速に凝縮または蓄積して大きな液滴を形成するのを防ぐことができた可能性があります。水蒸気はシースを透過し、常にPVDF-DMF相に入り、急速な相分離をもたらしました。図3dは、相対湿度が高い場合の粗い繊維の形成メカニズムを示しています。さまざまなレベルの相対湿度でPVDF / DMF溶液から得られたすべての表面と内部形態を表1にまとめています。興味深いことに、相対湿度が5%から65%に増加すると、繊維の直径が〜0.8から〜1.79μmに増加します。 (追加ファイル1:図S2B)。
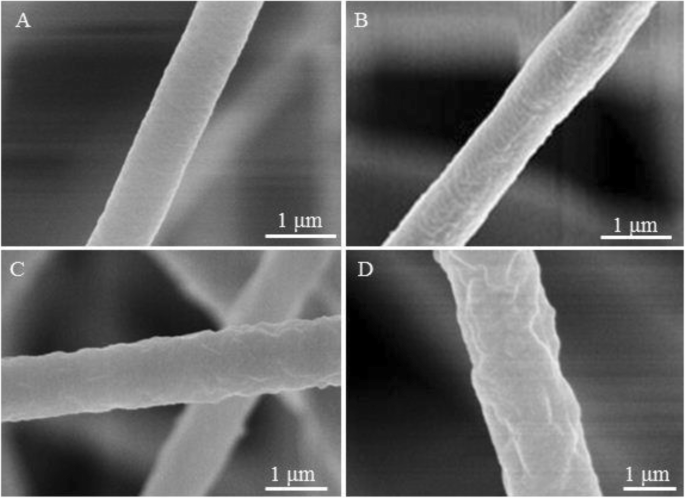
35%( w )のエレクトロスピニングによって作製されたサンプルの代表的なSEM画像 / v )さまざまなレベルの相対湿度でのDMFからのPVDFソリューション。 a 5%、 b 25%、 c 45%、および d 65%
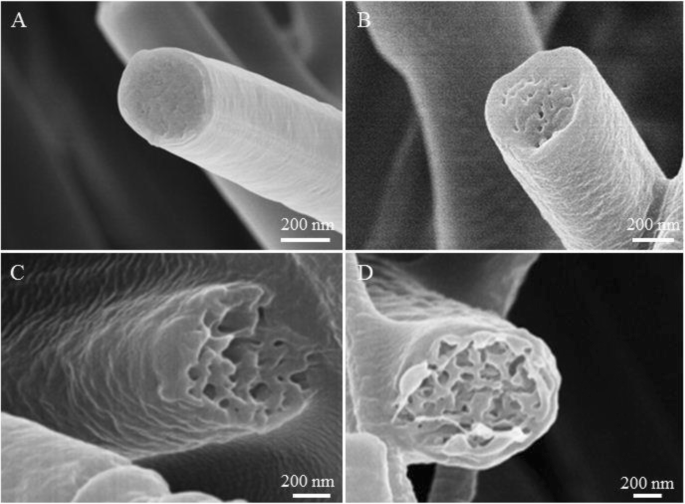
35%( w )のエレクトロスピニングによって作製されたサンプルの断面SEM画像 / v )さまざまなレベルの相対湿度でのDMFからのPVDFソリューション。 a 5%、 b 25%、 c 45%、および d 65%
ACE / DMF混合液からエレクトロスピニングされた繊維
この場合、25%( w / v )異なるACE / DMF比(4:1、2:1、1:1、1:2、および1:4)のPVDF溶液を、さまざまなレベルの相対湿度でエレクトロスピニングしました。 25%( w / v )(溶媒比4:1のACE / DMF)、相対湿度5%で滑らかな繊維が形成され(図6aおよび追加ファイル1:図S4A)、相対湿度でピラーの浅い縦方向の溝付き繊維が生成されました。 25%(図6bおよび追加ファイル1:図S4B)であり、ピラー縦溝付きファイバーは、相対湿度45%および65%で生成されました(図6c、dおよび追加ファイル1:図S4C、D)。 25%( w / v )(溶媒比2:1のACE / DMF)、相対湿度5%で滑らかな繊維が形成され(図6eおよび追加ファイル1:図S4E)、相対湿度25%で粗い繊維が製造されました。 (図6fおよび追加ファイル1:図S4F)、45%の相対湿度で浅い縦方向のピラー溝付きファイバーが得られ(図6gおよび追加ファイル1:図S4G)、ピラー縦方向の溝付きファイバーが相対湿度で生成されました。湿度65%(図6hおよび追加ファイル1:図S4H)。 25%( w / v )(溶媒比1:1のACE / DMF)相対湿度5%で、滑らかな繊維が観察され(図6iおよび追加ファイル1:図S4I)、相対湿度25%で粗い繊維が生成されました。および45%(図6j、kおよび追加ファイル1:図S4J、K)、およびピラーの小さな溝付きファイバーが65%の相対湿度で生成されました(図6lおよび追加ファイル1:図S4L)。 25%( w / v )(溶媒比1:2および1:4のACE / DMF)、相対湿度≤25%の場合、滑らかな繊維が見られました(図6m、n、q、rおよび追加ファイル1:図S4M、N 、Q、R)、一方、粗い繊維は45%と65%の相対湿度で生成されました(図6o、p、s、tおよび追加ファイル1:図S4O、P、S、T)。
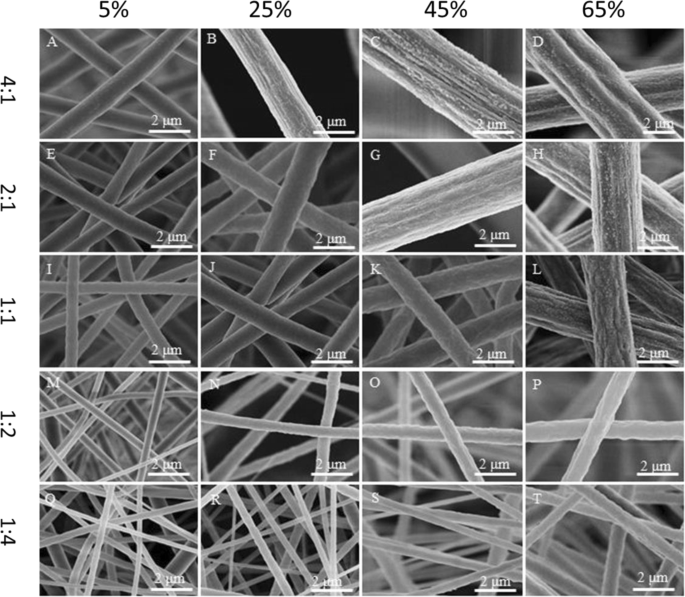
25%( w )のエレクトロスピニングによって作製されたサンプルの代表的なSEM画像 / v )さまざまなレベルの相対湿度(5%、25%、45%、および65%)および溶媒比でのACE / DMFからのPVDFソリューション。 a – d 4:1、 e – h 2:1、 i – l 1:1、 m – p 1:2、および q – t 1:4
ACE / DMFから形成されたPVDF溝付き繊維の形成メカニズムをより正確に把握するために、調査したすべての溶媒比とさまざまなレベルの相対湿度で形成された繊維の断面を確認しました。相対湿度5%で、形成されたすべての繊維の内部がしっかりしていることに気づきました。ここで、滑らかな表面と固体の内部を備えた繊維の形成では相分離は起こらなかったと結論付けます(図7a、e、i、m、q)。 25%、45%、および65%の相対湿度では、生成されたすべての繊維に内部細孔がありました。内部に細孔を有する溝付き繊維は、しわに基づく伸長メカニズムによって製造された[36]。この場合、揮発性の高いACE(蒸気圧、24 kPa)の急速な蒸発と相分離により、エレクトロスピニングの初期段階でガラス状のスキンが形成され、その後、形成によりジェットのしわのある表面が形成されました。内部の細孔の、そしてその後溝のある繊維に引き伸ばされます(図7b–d、g、h、l)。図3cは、高相対湿度での溝付き繊維の形成メカニズムを説明しています。溝付き繊維の表面でのナノピラーの形成は、ACEの急速な蒸発に直面したガラス状の皮膚によって繊維に閉じ込められたACEの事実による可能性がありますが、いくつかの弱点がまだ存在し、その結果、ナノピラー。
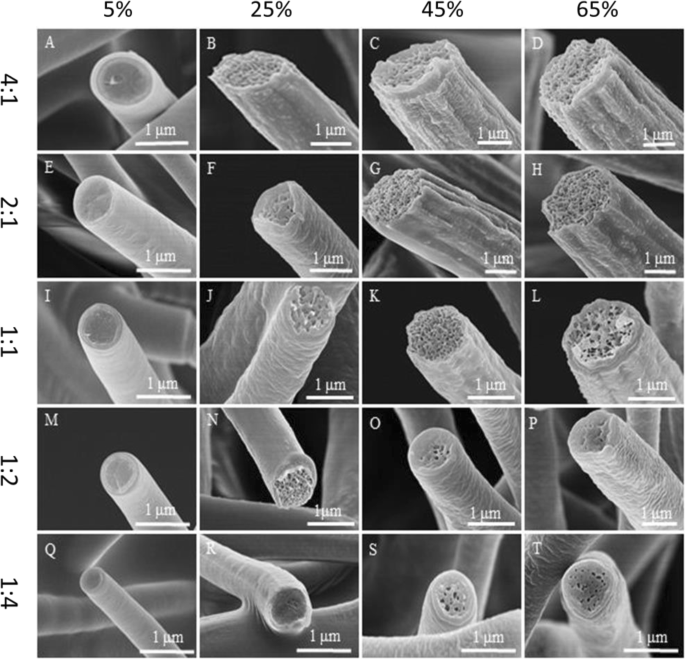
25%( w )のエレクトロスピニングによって作製されたサンプルの断面SEM画像 / v )さまざまなレベルの相対湿度(5%、25%、45%、および65%)および溶媒比でのACE / DMFからのPVDFソリューション。 a – d 4:1、 e – h 2:1、 i – l 1:1、 m – p 1:2、および q – t 1:4
VIPSにより、表面が粗く、内部に細孔がある繊維が形成されました(図7f、j、k、o、p、s、t)。 VIPSにより、表面が滑らかで内部に細孔がある繊維も形成されました(図7n、r)[24、37]。相対湿度を上げると、溝の幅と深さが増したことは特筆に値します。さまざまなレベルの相対湿度でACE / DMF混合溶液から得られたすべての表面と内部形態を表1にまとめます。相対湿度を5%から65%に上げると、繊維の直径が約1から約3.75μmに増加することがわかりました。 、〜0.85〜〜2.9μm、〜0.6〜〜2μm、〜0.35〜〜1μm、および〜0.26〜〜0.7μm(次の4:1、2:1、1:1、1:2の溶媒比) 、および1:4(追加ファイル1:図S2C-G)。
PVDFファイバーの二次表面構造を形成する上で高い相対湿度が重要であるため、相対湿度65%での状態図を作成することにより、エレクトロスピニング溶液の相挙動を示しました(図8)。この図は、バイノーダル曲線によって2つのゾーンに分割されています。ソリューションジェットは、紡糸口金(ゾーンI)から押し出されると、雲ひとつなく均質になります。 ACEの高い揮発速度、DMFの低い揮発速度、およびその後の溶液ジェットへの水の浸透により、ジェット内の成分(PVDF、溶媒、および水)の比率は、経路に従うように動的に変更されます。矢印で示されています。溶液ジェットは、二峰性曲線を横切った後、ゾーンIIに入り始め、そこで熱力学的不安定性のために曇って多相に分離します[37、38]。揮発性の高い溶媒(ACE)は、より急な矢印で表されます。これは、相分離の発生が速いことに対応します。
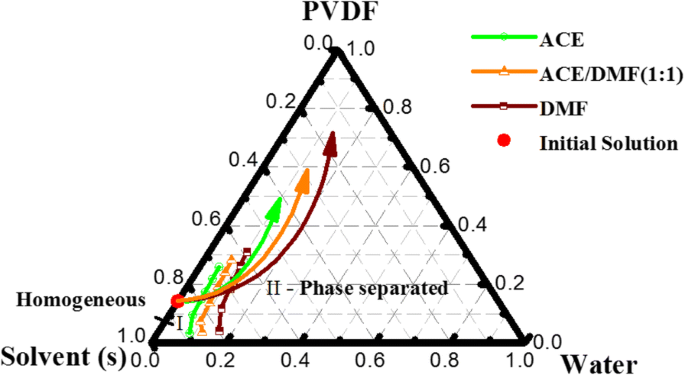
相対湿度65%でのPVDF、溶媒、および水の状態図。赤い点は初期の解決策を示しています
繊維の表面積と細孔構造を定量化するために、同様の直径を持つマクロ多孔質繊維(図1d)、粗い繊維(図4d)、および溝付き繊維(図6l)の窒素吸着等温線を測定しました。比較のために選ばれました。マクロ多孔質、溝付き、粗い繊維の比表面積は23.31±4.30 m 2 でした / g、10.26±2.19 m 2 / g、および4.81±0.58 m 2 / g、細孔容積は0.0695±0.007 cm 3 / g、0.0182±0.003 cm 3 / g、および0.0135±0.002 cm 3 それぞれ/ g(図9a)。これらの結果は、20.06 cm 3 のマクロ多孔質、溝付き、粗い繊維の最大窒素吸着と調和しています。 / g、12.29 cm 3 / g、7.49 cm 3 それぞれ/ g(図9b)。さらに、メソ細孔(2〜50 nm)がマクロ多孔質、溝付き、粗い繊維に存在するのに対し(図9c)、マクロ細孔(> 100 nm)はマクロ多孔質繊維にのみ出現し、その結果、高い比表面積と細孔容積(図9d)。
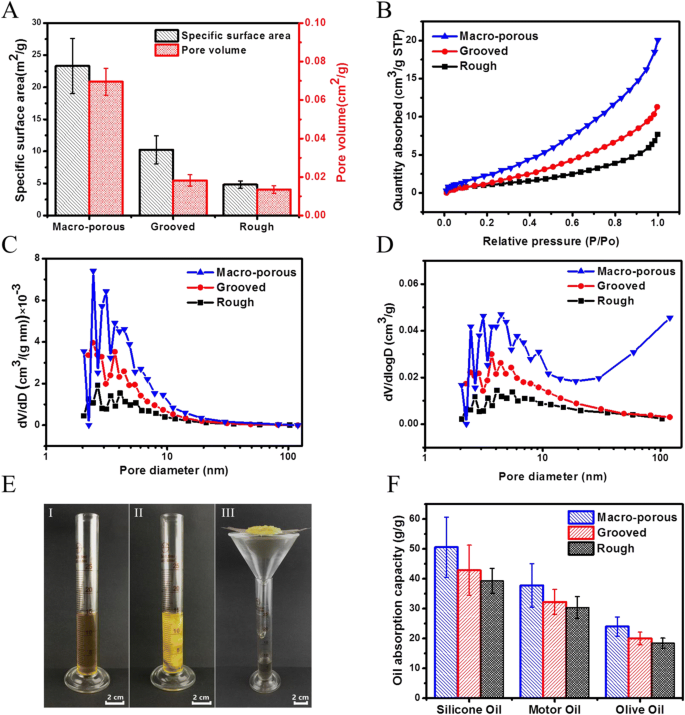
マクロ多孔質、溝付き、および粗い繊維の特性評価。 a 比表面積と細孔容積。 b 窒素吸着等温線。 c dV / dD-細孔径曲線。 d dV / dlogD-細孔径曲線。 e 吸油の写真。 (I)吸着剤を含まない15 mLの水と油の混合物(1:1)、(II)吸収中、(III)排水中。 f 吸油能力
PVDFは疎水性ですが疎油性ではないため、PVDF吸着剤は、水をはじきながら油を吸収することができます。次に、油を吸収するためのマクロ多孔質、溝付き、粗い繊維の適用を示しました(図9e)。さまざまなサンプルをチェックするために、3つの典型的なオイル(シリコンオイル、モーターオイル、オリーブオイル)が選択されました。
これらのオイルの典型的な特性を表2に示します。予想どおり、3種類のオイル吸収材料の中で、マクロポーラスファイバーは50.58±5.47 g / g、37.74±4.33 g / gという最高のオイル吸収能力を示しました。シリコンオイル、モーターオイル、オリーブオイルの場合はそれぞれ23.96±2.68 g / gです(図9f)。特に、マクロポーラス繊維は、シリコンオイル、モーターオイル、オリーブオイルの溝付きファイバーのそれぞれ1.18、1.17、1.19倍の吸油能力を示しました。さらに、マクロポーラス繊維は、シリコンオイル、モーターオイル、オリーブオイルの粗繊維のそれぞれ1.29、1.24、1.26倍の吸油能力を示しました。これらの結果は、マクロ多孔質繊維が最大の表面積を有し、一方、粗い繊維がすべてのサンプルの中で最小の表面積を有するという事実に起因するはずである。調査した3種類のオイルの中で、テストしたすべてのサンプルは、おそらくシリコンオイルの粘度が高いために、シリコンオイルに対して最高の吸収能力を示しました。
<図> 図>結論
内部細孔を備えたマクロポーラス、ラフ、およびグルーブドPVDFナノファイバーを形成するための適切で信頼性の高い方法を示しました。 PVDF繊維の形成に関与するメカニズムを理解するために、さまざまなレベルの相対湿度(5%、25%、45%、および65)で3つの溶媒システム(つまり、ACE、DMF、およびACE-DMF混合物)をテストしました。 %)。従来の溶剤を使用することにより、相対湿度5%で相分離が起こらず、内部が固体の滑らかな繊維が形成されることを発見しました。相対湿度25%で内部が固体である繊維の表面にマクロ細孔が形成されるのは、ACEの蒸気圧と核形成メカニズムが高いためにTIPSに起因するはずであり、マクロ細孔が形成されるのは45%と65%の相対湿度で内部の細孔を持つ繊維表面は、TIPSとVIPSの両方のメカニズムの共存に起因するはずです。さらに、DMFの低蒸気圧が、VIPSによる内部に細孔のある粗い繊維の製造に中心的な役割を果たしていることを発見しました。しわに基づく伸長メカニズムは、多孔質の内部構造を備えた溝付き繊維を製造する上で重要な役割を果たしました。マクロポーラスファイバー(> 300 nm)は、シリコンオイル、モーターオイル、オリーブオイルで、50.58±5.47 g / g、37.74±4.33 g / g、23.96±2.68 g / gの最高の吸油性能を示しました。それぞれ。重要なことに、内部多孔性を備えたマクロポーラス、ラフ、およびグルーブドPVDFファイバーの形成に関与するメカニズムの理解は、溶媒と相対湿度を調整することにより、エレクトロスピニングファイバーの製造の重要な基準として役立ちます。
略語
- ACE:
-
アセトン
- DMF:
-
N、Nジメチルホルムアミド
- PVDF:
-
ポリフッ化ビニリデン
- ヒント:
-
熱誘起相分離
- VIPS:
-
蒸気による相分離
ナノマテリアル
- ドラッグデリバリーを強化するためのナノファイバーとフィラメント
- 炭素繊維の生産と炭素繊維の部品:基本は何ですか?
- スタックカップカーボンナノファイバーの原子および電子構造を明らかにする
- 原子層堆積と水熱成長によって製造された抗菌性ポリアミド6-ZnO階層型ナノファイバー
- TIPS-ペンタセンベースの有機電界効果トランジスタの移動度と形態に及ぼすその場アニーリング処理の影響
- フェニルトリメトキシシランで修飾されたアルミナナノ粒子をベースにしたAl2O3:SiOCナノコンポジットの形成と発光特性
- 界面層の設計によるZnO膜の表面形態と特性の調整
- 表面の湿潤性と湿度を制御することによる絶縁基板へのエレクトロスピニング
- メタマテリアルにおける表面プラズモンポラリトンと磁気双極子共鳴の結合効果
- チタニアナノチューブの熱伝導率に及ぼす形態と結晶構造の影響
- 社内での平面研削と円筒研削の利点をご覧ください