静電アセンブリ法によって製造されたAl2O3ベースのナノカーボン複合材料の制御された微細構造と機械的特性
要約
この作品は、相互接続された炭素層状Al 2 の微細構造制御された形成について報告します O 3 カーボンナノ粒子(CNP)-アルミナ(Al 2 O 3 )複合粒子。 Al 2 O 3 この研究で使用された微粒子は、ナノサイズのAl 2 の造粒によって得られました。 O 3 平均直径150nmのナノ粒子。次に、CNP-Al 2 O 3 複合材料は、粒状のAl 2 を使用した静電アセンブリ法を使用して製造されました。 O 3 およびCNP。グラニュー糖Al 2 の表面のCNPの装飾 O 3 一次粒子サイズと被覆率の関数として、一定量のCNPを使用して調査しました。特に、Al 2 の界面にある相互接続された炭素粒子の層 O 3 粒界に似たものが得られました。 Al 2 で異なる粒子サイズとCNPカバレッジで得られたサンプルの機械的特性 O 3 複合セラミック材料の微細構造設計を通じて機械的特性を制御する可能性を示した粒子も調査されました。
はじめに
アルミナ(Al 2 O 3 )高硬度、優れた耐摩耗性、高い化学的安定性などの優れた特性を備えています。一方、アルミナの欠点は、破壊靭性が低く、高温での強度が低く、耐熱衝撃性が低いことです[1]。これは、マイクロおよびナノスケールでのアルミナベースのナノコンポジット開発における集中的な研究を促しました。セラミックマトリックス中にナノサイズの粒子が十分に分散した機能性セラミック複合材料は、破壊強度、破壊靭性、疲労、耐摩耗性などの機械的特性だけでなく、電気的、磁気的、熱的、光学的特性も改善すると報告されています[2 、3,4,5,6,7]。セラミックの機械的特性を改善および制御するために、微細構造の多孔性[8、9]、添加剤フィラーの組み込み[10]、および熱処理プロファイル[11、12]が使用され、報告されています。これは、Al 2 の微細構造を制御することによって O 3 、Al 2 の望ましい機械的特性 O 3 セラミックを得ることができた。ただし、報告されたほとんどの作業では、Al 2 の単純な方法を使用しただけです。 O 3 Al 2 の微細構造と設計を適切に制御するには不十分な、焼結前の粉末の混合 O 3 セラミックは、その機械的特性の制御性が低くなります。従来の混合方法によるナノコンポジットの形成において、添加剤粒子の凝集のために、指定された一次粒子上にナノサイズの添加剤粒子の均質な装飾を得ることが依然として大きな課題である。凝集によって引き起こされる不均一な分布は、セラミック複合材料の特性だけでなく、微細構造設計にも悪影響を及ぼします。したがって、この研究では、静電吸着法を使用したボトムアップアセンブリによる新しい方法を使用して、制御された望ましい特性をAl 2 > O 3 光学的、電気的、機械的特性などのセラミック。 Al 2 の可能な添加剤の1つとして O 3 セラミック複合材料、繊維(カーボンナノチューブ(CNT)、ナノファイバー)や板状(グラフェン)などのさまざまな形状のナノサイズの炭素材料、および粒子が開発されています。これにより、最近報告されている材料製造の添加剤としての炭素ベースの材料の適用が可能になります。
炭素ベースのアルミナ複合材料の開発において、Kumari等。カーボンナノチューブ(CNT)-アルミナ複合材料の熱伝導率が、CNT添加の重量パーセントと焼結温度を変更することにより、純粋なアルミナと比較して60%から318%に向上したことを報告しました[4]。それに加えて、発電、輸送、製造などの用途向けの炭素ベースの複合材料の並外れたトライボロジー特性により、多くの研究者が炭素ベースの複合材料の開発に関心を向けています[13、14]。表面が炭素で強化されたセラミックは、耐摩耗性が向上し、摩擦係数が低下することが報告されています。アルミナとジルコニアにカーボンナノファイバー(CNF)を使用した機械的強度の向上については物議を醸す報告がありますが、ほとんどの著者は機械的特性の改善を報告しています。アルミナのクリープ特性に関する最近のCNTの研究では、CNTの添加量に応じて、粒界すべりの障害または粒界の促進によりクリープ強度が強められたり弱められたりする可能性があると報告されているため、反対の結論が導き出されました。それぞれ拡散またはスライド[15]。一方、Crepo etal。酸化グラフェン強化アルミナ複合材料は、CNF強化アルミナよりも優れた耐クリープ性を示すことが報告されています[16]。また、グラファイトの優れた潤滑特性により、炭素ベースの材料は固体潤滑剤の用途に適しています。乾式摩擦の間に、炭素ベースの複合材料は、炭素の剥離と、影響を受けた接触領域でのセラミック破片とのその取り込みから潤滑膜を生成すると報告されています[13]。しかし、報告された研究のほとんどは、懸濁液の超音波混合または従来の機械的粉砕のいずれかによる唯一の混合の使用を含み、微細構造制御炭素の形成につながるセラミック上の炭素材料の制御された装飾に関する研究は実証されていません。ベースのセラミック。したがって、この研究では、CNP-Al 2 O 3 複合材料は、静電吸着アセンブリを使用して製造されました。これにより、複合材料のアセンブリと設計がより制御しやすくなります。 Al 2 O 3 この作業で使用される微粒子は、ナノサイズのAl 2 の対照造粒を使用して得られました。 O 3 粒子。次に、粒状のAl 2 O 3 得られた微粒子は、カーボンCNP-Al 2 の形成に使用されました。 O 3 複合。研究は、カーボンナノスフェアの量を0.3、0.6、および1.0 vol%(体積パーセント)から変化させ、使用されるアルミナ粒子の平均サイズを変化させることによって体系的に実施されました。次に、カーボンベースの複合材料サンプルの機械的特性を特性評価し、3点曲げおよび押し込み試験を使用してモノリシックアルミナサンプルと比較しました。得られた微細構造と機械的特性の間の相互相関についても議論され、解明されています。
メソッド
平均直径150nmのアルミナナノ粒子を大明科学工業株式会社から購入し、粒状のAl 2 を得るための前駆体として使用しました。 O 3 微粒子。造粒は、Al 2 の混合物の噴霧乾燥を使用して実施された。 O 3 アクリルバインダーを含む微粒子。 Al 2 O 3 次に、微粒子をふるいにかけて、37、62、および98μmの3つの異なる平均直径を得て、これらを一次粒子として使用しました。平均直径260nmのCNPは東海カーボン社から購入し、添加剤ナノ粒子として使用しました。 CNPは疎水性であり、水媒体に分散できないため、最初にSDC(デオキシコール酸ナトリウム)溶液に分散させ、次に親水化処理を行って次のコーティングを行いました。 40ミリリットルの0.1wt%SDC溶液を1 gのCNPに添加し、30分間の超音波処理によって分散させました。次に、溶液を遠心分離し、ミキサーで水を攪拌することによって実施されたイオン交換水を使用して3回洗浄した。その後、ポリカチオンとポリアニオンを用いて表面電荷の変化を行った。ポリカチオンおよびポリアニオンとして、ポリジアリルジメチルアンモニウムクロリド(PDDA)(平均分子量100,000〜200,000、Sigma-Aldrich)およびポリアニオンとしてのスチレンスルホン酸ポリナトリウム(PSS)(平均分子量70,000、Sigma-Aldrich)をそれぞれ使用しました。その後、安定した正の表面電荷を誘導するために、SDCでコーティングされたCNPをPDDA、PSS、およびPDDAに交互に浸漬しました。吸着プロセス後、残りの懸濁液を乾燥させてから回収した。最初の調査では、Al 2 O 3 直径62μmの粒子を使用し、Al 2 でのCNPカバレッジ制御の実現可能性 O 3 粒子が実行されました。追加されたCNPの体積分率は、0.3、0.6、および1.0 vol%でした。 Al 2 の効果の調査において O 3 サイズ、Al 2 の間にCNP添加の固定0.6vol%が設定されました O 3 複合材料の形成には、平均直径が37、62、および98μmの異なる粒子を使用しました。 CNP-Al 2 O 3 複合粒子は、最初に直径12mmのダイを使用して一軸プレスされました。加えた圧力は300MPaで、保持時間は5分でした。その後、得られたペレットをh-BN粉末を入れた黒鉛ダイに挿入し、ホットプレス焼結(Diavac Inc. Ltd.)を行った。真空雰囲気(8×10 -3)でホットプレス焼結を行った。 Pa)1350°C(加熱速度10°C / min)で2時間、圧力30MPa。 CNP-Al 2 の形態 O 3 得られた複合材料および焼結微細構造を、S-4800電界放出走査型電子顕微鏡(FE-SEM、日立S-4800)を使用して観察した。ゼータ電位は、大塚電子株式会社(ELSZ-1)およびマイクロテックニッション株式会社(ZEECOM)を使用して測定しました。機械的特性の決定については、得られたサンプルの弾性率を3点曲げ試験を使用して測定しました。 。サンプルは最初にストリップ状のテストシートにカットされ、表面グラインダーを使用して寸法が微調整されました。準備した試験片の寸法は3×4×40mmでした。その後、0.5mmのアルミナと9μmのグレードのダイヤモンドペーストを使用して研磨を行いました。インストロン式コンパクトテスターを用いて3点曲げ試験を行った。まず、ストレス(σ )式を使用して計算されました。 1ここで、 l 、 b 、および h は各試験片のスパン距離と寸法であり、 P 負荷を表します。次に、応力とひずみの関係をプロットし、最小二乗法の傾きから弾性率を計算しました。クロスヘッド速度は0.02mm / min、スパンは30mmでテストされました。
$$ \ sigma =\ frac {3 lP} {2 bh} $$(1)複合材料サンプルの硬度特性は、圧痕を使用してさらに評価されました。使用したロックウェル圧子はダイヤモンド( E )で構成されていました i =1050 GPa、υ =0.20)公称曲率半径 R =200は、頂角が120°の円錐形の先端に埋め込まれています。圧子はインストロン型テスター(サンワインスツルメンツ)にセットし、クロスヘッド速度0.05mm / sで一定深さ(20μm)まで打ち込みました。インデント時に得られた荷重はロードセル(TCLZ-100KA、東京学校)で測定し、インデント深さは非接触静電変位計(VE-222、小野測器)で測定しました。
結果と考察
図1は、Al 2 の表面電荷ゼータ電位を示しています。 O 3 したがって、PDDSとPSSのコーティングを交互に行った後の粒子とCNP。アルミナとCNPは、3層のコーティング後、それぞれ+55と-55mVのゼータ電位を示したことが観察できました。 CNPとAl 2 の両方に3層コーティングした後に達成されたゼータ電位 O 3 微粒子は安定していた。 CNP-Al 2 の表面形態 O 3 図2のSEM画像にCNP添加量が0.3、0.6、1.0 vol%異なる複合材料を示します。高倍率のSEM画像から、Alの表面に吸着されたCNPの量を明確に観察できます。 2 O 3 粒子は、CNP添加の体積パーセントが高くなるにつれて増加しました。 CNPがAl 2 全体に均一に分布していることに注意することが重要です。 O 3 均一で均一な分布を得るためのEA法の利点を表す凝集の兆候のない表面。観察されたCNPの粒子サイズは約260nmです。 CNPの添加を0.6vol%に固定し、Al 2 のサイズを変更する O 3 37、62、および98μmの微粒子、Al 2 の表面でのCNPの分布 O 3 粒子を図3のSEM画像に示します。SEM画像の観察から、粒子サイズの直径が大きくなるにつれて、表面に吸着されるCNPの量がそれに応じて増加することが観察されました。より大きなAl 2 O 3 粒子は、小さいAl 2 と比較して、全体の表面積が小さくなっています。 O 3 粒子の場合、CNPの吸着に利用できる総表面積も、小さいAl 2 と比較して小さくなります。 O 3 粒子。したがって、0.6 vol%の一定のCNPの添加により、より多くの量のCNPがより大きなAl 2 のより低い全体表面積に吸着されました。 O 3 粒子。その結果、Al 2 に吸着されたCNPの量 O 3 表面はAl 2 の直径サイズとともに増加することが観察されます O 3 98μmAl 2 の表面へのCNP吸着の高密度をもたらした粒子 O 3 粒子。一方、粒子サイズが小さくなると、Al 2 へのCNP吸着に利用できる全体的な表面積が小さくなります。 O 3 増加し、したがって、懸濁液中のCNPの量が不十分なため(固定0.6 vol%)、CNPのまばらな分布が観察されます。 CNP-Al 2 を使用して得られた焼結微細構造 O 3 図4に示すように、界面での複合および高倍率。図4aのSEM画像から、得られた微細構造は、得られたCNP-Al 2 の形状を反映していることがわかります。 O 3 複合。粒界がつながって粒界に沿ってネットワークを形成していることは注目に値します。粒界に沿って形成されたCNPネットワークの観察から、Al 2 の表面でのCNP分布の均一性 O 3 粒子を決定することができます。この結果は、複合前駆体を設計することにより、微細構造が制御された複合材料を得ることが可能であることを示しています。図4bの高倍率SEM画像から、Al 2 の界面の間に炭素層が存在します。 O 3 粒界が観察できます。これは、Al 2 間のCNPの焼結を示しています。 O 3 ホットプレス焼結中の粒子は、粒界に沿って炭素層の均一なコーティングの形成をもたらした。 Al 2 に注意することも重要です O 3 得られたマトリックスは緻密でよく焼結されており、図4bに示すように細孔は観察されません。これは、密に詰まった粒状のAl 2 の形成によるものです。 O 3 ナノ粒子(150 nm)は、この作業の新しい技術を実証する優れた焼結性を可能にします。 CNP-Al 2 の弾性率 O 3 Al 2 の関数としてプロットされた3点曲げ試験を使用して得られた複合材料 O 3 粒子サイズと表面被覆率を図5に示します。図5aから、Al 2 を使用して製造されたサンプルの示されている弾性率を示します。 O 3 粒子のみが約390GPaであり、多結晶Al 2 で報告された結果と一致しています。 O 3 これは300から400GPaの間です[6、12]。この弾性率の値の達成は、粒状のAl 2 を使用して良好な微細構造と圧縮が達成されたSEM観察と一致します。 O 3 ナノ粒子。芦塚らの研究では。アルミナセラミックの機械的特性に対する多孔性の影響については、多孔性のないセラミックの弾性率(0%)は、約380GPaでわずかに低くなっています[17]。 CNP-Al 2 の弾性率について O 3 複合材料の場合、CNPの体積分率を高くするか、Al 2 を増やすと、特性が直線的に減少するため、特性を制御できることがわかります。 O 3 粒子サイズ。同様の傾向は、Shin et al。の研究でも観察され、還元された酸化グラフェンと単層CNT-アルミナ複合材料の弾性率は、添加剤の含有量を増やすことによって減少しました[6]。両方の要因として(CNPの量とAl 2 の粒子サイズ O 3 )比表面積に大きく影響し、Al 2 へのCNPの吸着を促進します。 O 3 粒子表面、これはAl 2 の焼結を阻害します O 3 カーボン層のスリップ効果の可能性により、弾性モジュールが低くなりました[6]。この発見は、Gopalanらによって報告されたものと一致しています。ここで、複合材料に使用されたCNTは粒成長を遅らせましたが、粒界の滑りには影響を与えず、超塑性が発生しました[15]。この発見は、Al 2 の弾性率を変更および制御する可能性を示しています。 O 3 CNP-Al 2 の形成に使用される前駆体複合材料の設計を介して微細構造形成を制御することによるセラミック O 3 。図5bでは、Al 2 のCNP被覆率の関数として得られた弾性率のプロット O 3 示されています。 CNP被覆率と弾性率強度の間に線形相関が観察され、上記の結果をさらに裏付けています。したがって、これらの結果から、CNP-Al 2 の機械的特性が実証されます。 O 3 複合セラミックは、CNPの添加量または一次Al 2 の粒子サイズを変更することにより、CNP被覆率を介して制御できます。 O 3 。 CNP-Al 2 の微小硬度の測定 O 3 複合サンプル、純粋なAl 2 間の比較 O 3 およびCNP-Al 2 O 3 異なるAl 2 を使用して1.0vol%のCNPを添加して製造されたサンプル O 3 37、62、および98μmの粒子サイズが実施されました。得られた圧痕の結果を図6に示します。得られた結果は、純粋なアルミナサンプルが最高の硬度値を示し、CNP-Al 2 の硬度が最も高いことを示しています。 O 3 より大きなAl 2 で還元された複合サンプル O 3 粒子サイズ。これは、Al 2 の全体的な表面積が小さいためです。 O 3 粒子サイズが大きくなり、表面に吸着されるCNPの量が増える場合。続いて、Al 2 上のCNPの量が多くなります。 O 3 界面は、Al 2 間の効果的な焼結を阻害するため、硬度が低下しました。 O 3 Al 2 の粒界に沿った連続接続炭素層の界面またはすべり O 3。 したがって、Al 2 の表面にCNPの分布を制御することが重要です。 O 3 CNP-Al 2 の所望の機械的特性につながる所望の微細構造の形成を誘導するために O 3 コンポジット。
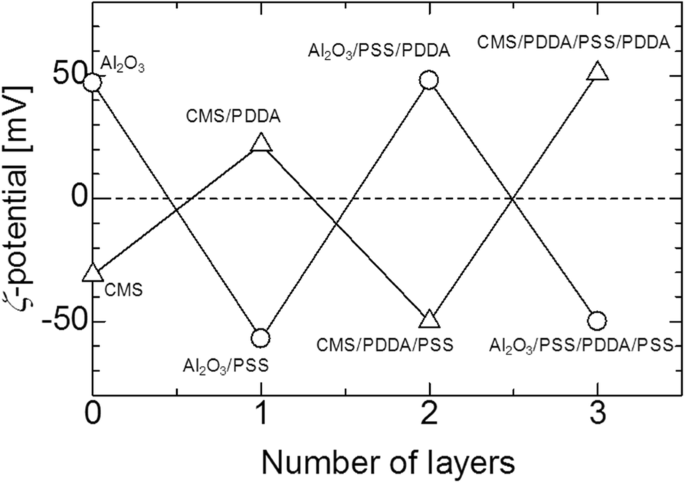
表面電荷制御されたAl 2 のゼータ電位 O 3 およびカーボンナノ粒子
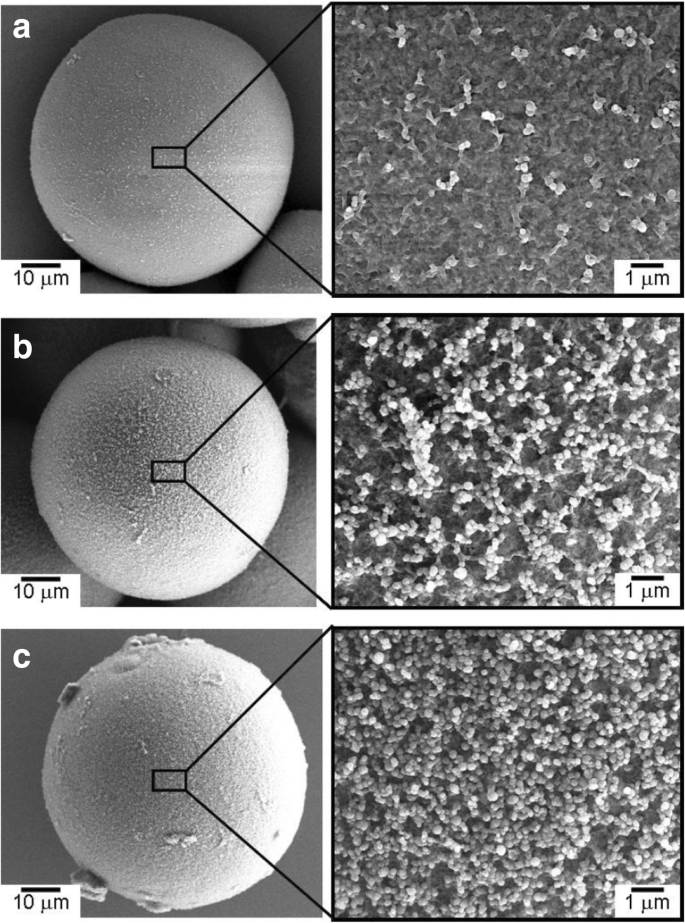
a のSEM画像 0.3 vol%、 b 0.6 vol%、および c Al 2 にコーティングされた1.0vol%CNP O 3 平均直径62μmの造粒粒子
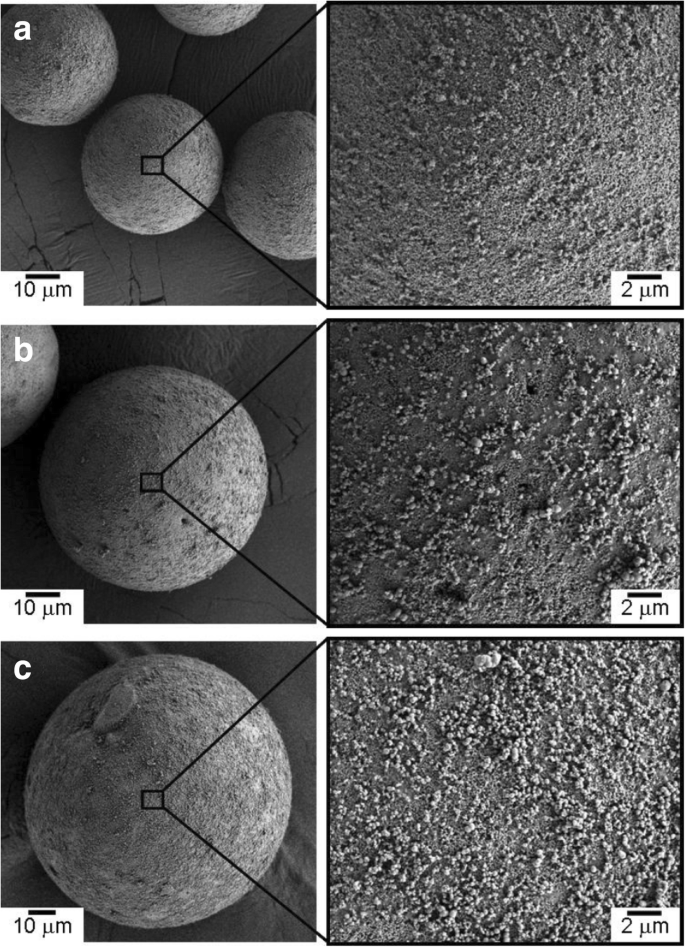
Al 2 にコーティングされた0.6vol%CNPのSEM画像 O 3 平均直径が a の造粒粒子 37、 b 62、および c 98μm
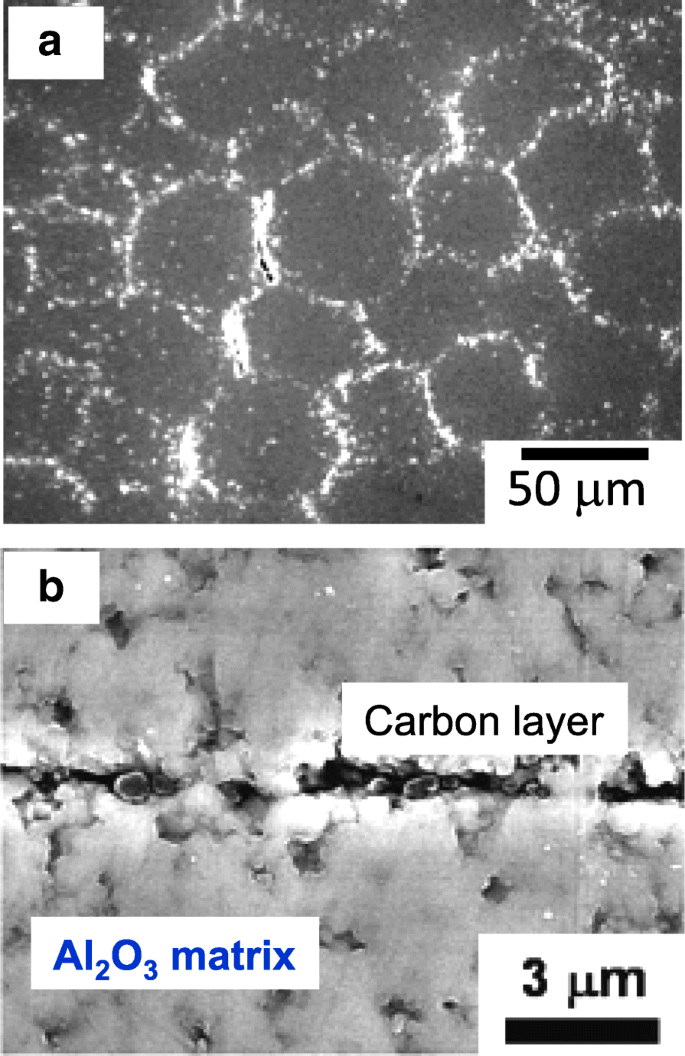
a 0.6 vol%CNP-Al 2 の微細構造 O 3 Al 2 を使用した合成 O 3 平均直径は62μmです。 b CNP-Al 2 の粒界 O 3 複合。 Al 2 間の界面に炭素層が観察された O 3 マトリックス
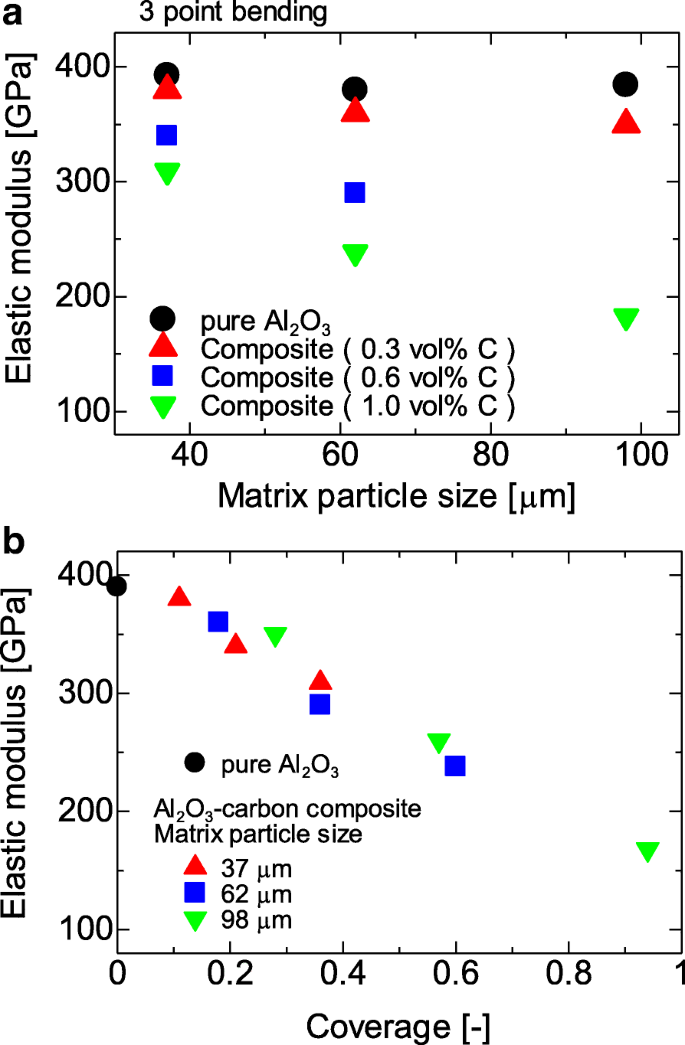
CNP-Al 2 の弾性率 O 3 a の関数としてのコンポジット マトリックスの粒子サイズと b Al 2 のCNPカバレッジ O 3 粒子
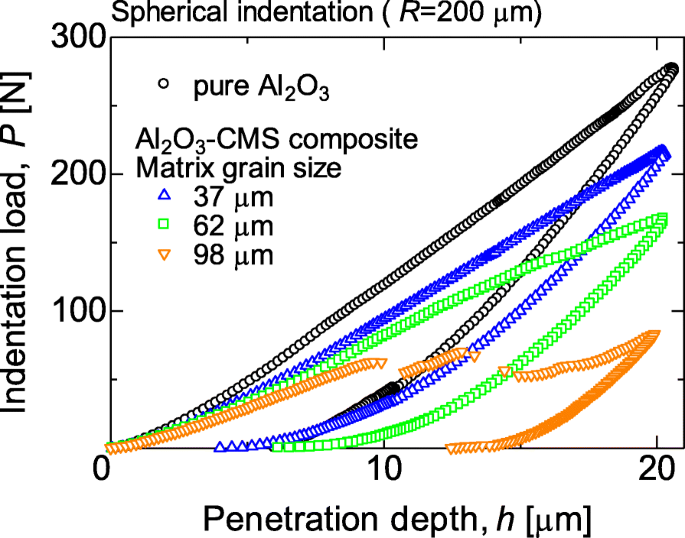
押し込み荷重と侵入深さ1.0vol%CNP-Al 2 のヒステリシス曲線 O 3 コンポジット
インデント荷重から( P )-深さ( h )曲線( P - h 曲線)ロードおよびアンロードサイクル中に、微細構造の変化と表面変形のメカニズムを取得できます[18]。インデント荷重( P )を含む単純な2次方程式 )および侵入深さ( h )式に示されています。 2は、ローディングプロセスの分析に使用できます[18、19、20]。
$$ P \ propto {h} ^ 2 $$(2)モノリシックAl 2 のロード O 3 P との相関関係を示した - h 二次方程式に似た曲線。 2 CNP-Al 2 O 3 Al 2 を使用して製造された複合材料 O 3 サイズが37および62μmの粒子は、モノリシックAl 2 から逸脱した曲線を持つ線形を示しました。 O 3 それぞれ負荷曲線。これは、微細構造内(粒界界面)にCNPが存在し、粒界に沿って局所的な変形が生じたことを示しています。 CNP-Al 2 について O 3 Al 2 を使用して製造された複合材料 O 3 粒子サイズが98μmの場合、粒界での高密度のCNPにより、 P が不連続になりました。 - h ヒステリシス曲線であり、粒界すべりまたは表面マイクロフラクチャーの発生により、最も低い硬度を示しました。
結論
この作業では、CNP-Al 2 の実行可能な制御された形成 O 3 静電吸着法による複合材料を示します。 Al 2 O 3 使用した微粒子は、ナノサイズ(150 nm)のAl 2 の造粒によって得られました。 O 3 より良い圧縮と焼結性を可能にした粒子。複合セラミックの形成において、CNPの量(0.3、0.6、1.0 vol%)および一次粒状Al 2 を含むパラメータ O 3 微粒子サイズ(37、62、92μm)を調査しました。 CNP添加剤とAl 2 の量を制御することにより、 O 3 微粒子サイズ、異なる表面被覆率が得られ、異なる機械的特性を備えた制御された微細構造形成につながる可能性があります。均質なCNP-Al 2 を使用する O 3 複合材料では、Al 2 の粒界に沿って連続的な相互接続炭素層が得られました。 O 3 。高密度でコンパクトなAl 2 O 3 Al 2 の良好な焼結により、マトリックスも観察されました。 O 3 ナノ粒子。 3点曲げおよび押し込み試験の結果から、Al 2 上のCNPの被覆率を調整することにより、機械的特性の制御が実証されました。 O 3。 弾性率の変化は、効果的な焼結の阻害またはAl 2 で生成された炭素層の滑りによるものでした。 O 3 インターフェース。この研究から、CNP-Al 2 を使用した相互接続されたインターフェースを備えたセラミックの微細構造設計の実現可能性を実証しました。 O 3 複合。この微細構造設計の方法は、ボトムアップアセンブリによる材料設計の可能性と可能性を広げ、幅広いアプリケーションに望ましい特性をもたらします。
データと資料の可用性
この調査中に生成または分析されたすべてのデータは、この公開された記事(およびその補足情報ファイル)に含まれています。
変更履歴
略語
- CNP:
-
カーボンナノ粒子
- PDDA:
-
ポリジアリルジメチルアンモニウムクロリド
- PSS:
-
スチレンスルホン酸ポリナトリウム
- SDC:
-
デオキシコール酸ナトリウム
- SEM:
-
走査型電子顕微鏡
ナノマテリアル
- 樹脂と繊維の複合材料の特性とそれらが有益である理由
- フラーレン由来のナノ材料とそれらのポリマー複合材料の常磁性特性:劇的なポンピングアウト効果
- Cu / Ti3SiC2 / Cナノコンポジットの微細構造と機械的性質に及ぼすグラフェンとMWCNTの相乗効果
- 分子線エピタキシー法を用いたGeBi膜の作製と光学的性質
- グラフェン/ Ag3PO4量子ドット複合材料の簡単なワンステップソノケミカル合成と光触媒特性
- 水熱反応によりレモンジュースから製造された蛍光炭素量子ドットの材料と光学特性
- ナノ結晶ストロンチウムフェライトの構造、微細構造、および磁気特性に及ぼすゾル-ゲル修飾のpH調整パラメータの影響
- ナノ粒子と超音波によって制御される水の過冷却
- CdフリーのCuドープZnInS / ZnSコア/シェルナノ結晶:制御された合成と光物理的特性
- Pr2CuO4ナノシートの制御された合成と選択的吸着特性:メカニズムの議論
- エンジニアリング材料の特性:一般的、物理的および機械的