Fraunhofer IPTは、水素貯蔵、エンジンブレードなどの熱可塑性複合材料を開発しています
Fraunhofer IPTの開発には、(左上から時計回りに)熱可塑性複合エアロエンジンファンブレード、レーザー構造化とAFPを使用したハイブリッド複合金属構造、複合材料の構造ヘルスモニタリング(SHM)、およびPrePro2DやPrePro3Dシステムなどの熱可塑性複合テープ処理システムが含まれます。 Conbilityによって商品化されました。写真提供者:Fraunhofer IPT
2020年12月に、Fraunhofer Institute for Production Technology(IPT、アーヘン、ドイツ)が、熱可塑性炭素繊維強化ポリマー(CFRP)エアロエンジンファンブレード用の完全自動テープ敷設および成形をどのように開発しているかについての記事を公開しました。熱可塑性複合テープのその場圧密(ISC)は、Fraunhofer IPTがよく知っているトピックであり、ISCのパイオニアであるAccudyne Systems Inc.(Newark、Del。、US)およびAutomatedとともにこのテクノロジーを最初から推進してきました。 Dynamics、現在はTrelleborg Sealing Solutions Albany(TSS Albany、Niksayuna、NY、US)。 [これらのISCのパイオニアの詳細については、「熱可塑性空気構造の適切な統合、パート1およびパート2」を参照してください。]「IPTは1988年以来、レーザーアシストテープワインディング(LATW)で活躍しており、引き続き主要トピックの1つです。 」と、FraunhoferIPTの繊維強化プラスチックおよびレーザーシステム技術のチーフエンジニア兼部門長であるDr.HenningJanssenは説明します。彼は、LATWテクノロジーは、特に過去10〜15年で大きく変化したと述べています。このブログでは、Fraunhofer IPTによるLATWと熱可塑性複合材料の開発について、また研究所が将来の技術の方向性をどのように見ているかについて詳しく説明しています。
レーザーテープ巻きの進化
「私たちが30年前に始めたとき、レーザー技術は熱可塑性複合材料の高速処理の準備ができていませんでした」とJanssenは言います。 「特にコントロール側では、アナログカメラしか持っていなかったことが想像できます。今、私たちははるかに優れた技術を持っています。たとえば、2008年にコンパクトなレーザー巻線ヘッドを開発してAFPTドイツ(ドイツ、デルト)を設立したとき、フレームレートがわずか8の16ピクセルx16ピクセルのカメラを使用する必要がありました。 1秒あたりのフレーム数。今では、640 x 480ピクセルで、1秒あたり50フレーム以上の処理を簡単に行うことができます。」彼は、これが重要であると説明しています。「私たちが開発したレーザーテープ巻きでは、主な利点の1つは、調べることができることです。 プロセスを処理し、ミリ秒以内に処理能力を変更します。これにより、たとえば、圧力容器のドームなど、巻き取り速度が遅くなり、レーザー加熱パワーを下げる必要がある複雑な形状を移動する場合に、優れた利点が得られます。次に、巻線がタンクシリンダーに沿って速度を取り戻すので、再調整する必要があります。これは15年前には不可能でした。なぜなら、レーザー、制御システム、熱画像技術は準備ができていなかったか、高価すぎて、現在の技術ほど強力ではなかったからです。
Janssen氏は続けます。「つまり、デジタル側で開発されたものはたくさんあります。たとえば、デジタルツインのようなものを提供します。この場合、すべてのセンサー情報を圧力容器にマッピングできるため、製造された部品とデジタル設計を比較して、部品の品質を評価し、パフォーマンスを予測できます。仮想プロセスセンサーとモデルを使用することで、処理履歴によって定義されるラミネート強度を予測することもできます。」熱可塑性テープを使用するLATWは、熱後処理ステップがないため、巻線プロセス自体の間に材料と部品の特性が決定される高速加熱と冷却を使用するため、これは重要です。したがって、迅速なプロセス制御機能を備えていることが重要です。
材料の開発もありました、とヤンセンは言います。 「20年前、現在はソルベイ(米国ジョージア州アルファレッタ)であるCytecのAPC-2など、利用できる熱可塑性複合テープ材料の量は限られていました」と彼は説明します。 「しかし現在、さらに多くの材料が産業用途に適格であり、炭素繊維やガラス繊維で強化されたポリプロピレン(PP)や、たとえばポリアミド6(PA6)などの多くの商品材料もあります。自動車産業でかなり多く使用されています。現在、大量生産に向けたLATWのアプリケーションもあります。たとえば、電気モーターの保持スリーブやその他の部品への動きがあります。これらは単純な熱可塑性複合リングまたはチューブですが、年間10,000〜50,000個のボリュームがあります。」
ambliFIBRE、石油およびガス用パイプ strong>
Janssenが上記で説明したLATWのデジタル制御の一部は、ambliFIBREプロジェクト(2015-2018)で開発されました。 「そのプロジェクトには多くのパートナーがいましたが、そのうちの1つはベイカーヒューズ(イギリスのニューカッスルと米国のテキサス州ヒューストン)で、非金属パイプにはLATW機器を使用しました。」 2018年にambliFIBREが終了した直後、ベイカーヒューズはサウジアラムコ(サウジアラビア、リヤド)との合弁事業を発表し、炭素繊維強化プラスチック(CFRP)の使用を含む非金属パイプの使用を拡大しました。
Baker Hughesは現在、エネルギー分野での非金属材料の導入を加速することを目指しており、Magma(Portsmouth、UK)など、パイプにレーザーベースの技術を使用している他の企業もあります。 (「深海で上昇する熱可塑性パイプ」および「MagmaGlobalが高圧複合ライザーを提供する…」を参照してください。
「熱可塑性複合ライザーとフローラインにもレーザーテープ巻きを使用することも非常に一般的です」とJanssen氏は言います。 「これはまだ他の業界では一般的な知識ではありませんが。」 LATWに最近注目されているのは水素貯蔵タンクであると彼は付け加えていますが、この技術はすでにはるかに幅広い用途を持っています。
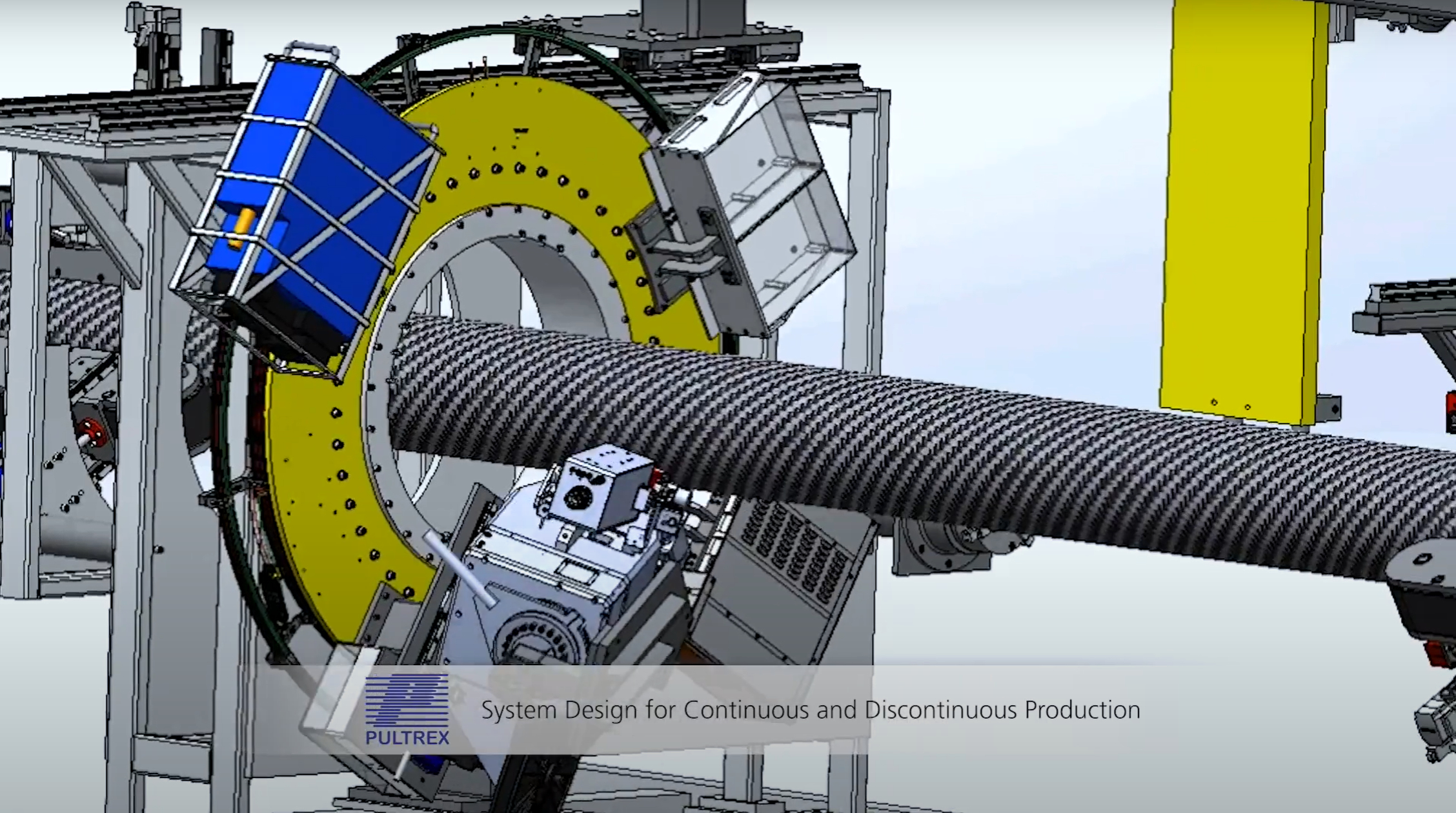
ambliFIBREプロジェクト内で、Fraunhofer IPTは、たとえば数キロメートルの長さのパイプを製造するために、不連続(タンクなど)および連続テープ巻きのデジタルプロセス制御モデルを開発しました。写真提供者:ambliFIBREプロジェクトのFraunhoferIPTビデオ
「そして、Fraunhofer IPTがこれらのアプリケーションに提供するものが重要です」と、ヤンセンは言います。 「明らかに、私たちはここで連続パイプ生産のための本格的な生産ラインを運営していませんが、私たちがお客様に提供しているのは材料試験と製品認定です。たとえば、DNV-GL F114に基づくテストピラミッドがあり、ポリマーと繊維の認定とテストから始まり、複合ラミネートの微細構造またはメソ構造にスケールアップします。そのため、クーポンレベルで多くのテストを行ってから、たとえば、巻き取りによってプレスや自動テープ敷設(ATL)とは異なる特性が得られるため、より小さなパイプや代表的なパイプにスケーリングします。」
また、彼は次のように述べています。「材料にはさまざまな応力があるため、これらの複合材料の多くは、たとえば2〜3インチから数メートルの長さの小さなパイプでテストされます。したがって、このテストを実行してから、プロセスの理解を実際の部品の長さ、たとえば2〜3キロメートルに適用します。その長さでの処理時間は数日かかる可能性があるため、これは非常に興味深いことです。収縮だけでなく、気温の変化など、かなりの影響を与える可能性のある他の要因も考慮する必要があります。」
水素貯蔵タンク内のLATW
Janssen氏は、Fraunhofer IPTは2000年以来、石油およびガス会社と協力してきました。「そして、8年前、これは水素タンクに必要な技術とほぼ同じであることがわかりました」と彼は回想します。 「そして今、私たちはここIPTでの水素製造と、燃料電池の炭素繊維複合材料のための大きなイニシアチブを持っています。燃料電池の自動製造のために8000万ユーロの施設を設置し、長さ7メートル、直径2.5メートルまでの部品を製造できるように新しい非常に大きな巻線施設に投資しています。これも使用します。大型圧力容器用。」
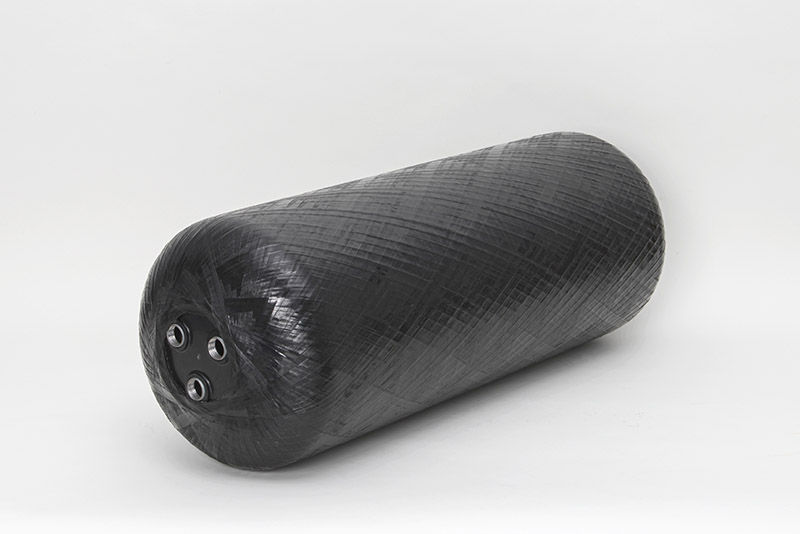
熱可塑性プラスチック複合テープを使用するLATWは、圧力容器製造の最先端ではありません。「熱可塑性プラスチックの化学的性質、処理、耐久性はすべてまだ研究されているためです。しかし、私たちの強い信念は、熱可塑性プラスチックが提供する低い透過性、靭性、およびリサイクル性が重要であるということです。」彼はまた、タイプVの圧力容器に熱可塑性プラスチックが含まれる可能性があると考えています。これは、すべて複合材料ですが、別個の熱可塑性ライナーを使用していません。 「これらは、燃料電池電気トラックなどの一部のモバイル水素貯蔵アプリケーションに将来のソリューションを提供する可能性があります。」
「また、従来の熱硬化性樹脂 フィラメントの巻き付けは、最小巻き取り角度に関して制限されています」とJanssen氏は言います。 「たとえば、ファイバーの角度が10°以上のらせん状の層でドームを一周する必要があります。したがって、従来のフィラメントワインドタンクに0°の補強材を入れることはできません。」ただし、彼は次のように主張しています。「従来のLATWでは、入ってくる熱可塑性プリプレグが基板に直接溶接されているため、任意の方向に進むことができ、設計の自由度が大幅に高まります。現在、自動車業界のパートナーと協力して、安全でエネルギー効率が高く、リサイクルが容易な水素貯蔵用の熱可塑性圧力容器を開発するプロジェクトを実施しています。」
熱可塑性複合ファンブレード
Fraunhofer IPTは、ターボ機械において非常に強力なバックグラウンドを持っているとJanssenは言います。 「ここアーヘンには ターボ機械製造国際センター(ICTM) 競争前の研究開発プロジェクトでエンジンメーカーとそのサプライヤーと共同で製造技術を開発および強化する競争前のコミュニティ。」
彼は、過去20年間、主に圧縮セクションの先進製品やブレード一体型ディスク(ブリスク)などのタービン用のチタンまたはニッケルベースの合金の機械加工に焦点が当てられてきたと述べています。寒冷地では、炭素繊維複合ファンブレードなどの複合材料の部品が1990年代にGEによって開発され、現在はGE90とGEnxで使用されています。 「しかし、現在、セラミックマトリックス複合材料(CMC)は、ジェットエンジンの高温セクション用の次世代材料と見なされています」とヤンセン氏は言います。
「金属と比較して複合材料から部品を製造することは非常に異なります」と彼は続けます。 「金属では、大量の材料から始めて、サブトラクティブ処理、主に機械加工によって部品を導き出すため、設計は製造にそれほど依存しません。これは、常に何らかの生成プロセスを必要とするコンポジットでは正反対です。そこで、製造の観点から新しいファンブレード戦略に取り組むことにしました。」
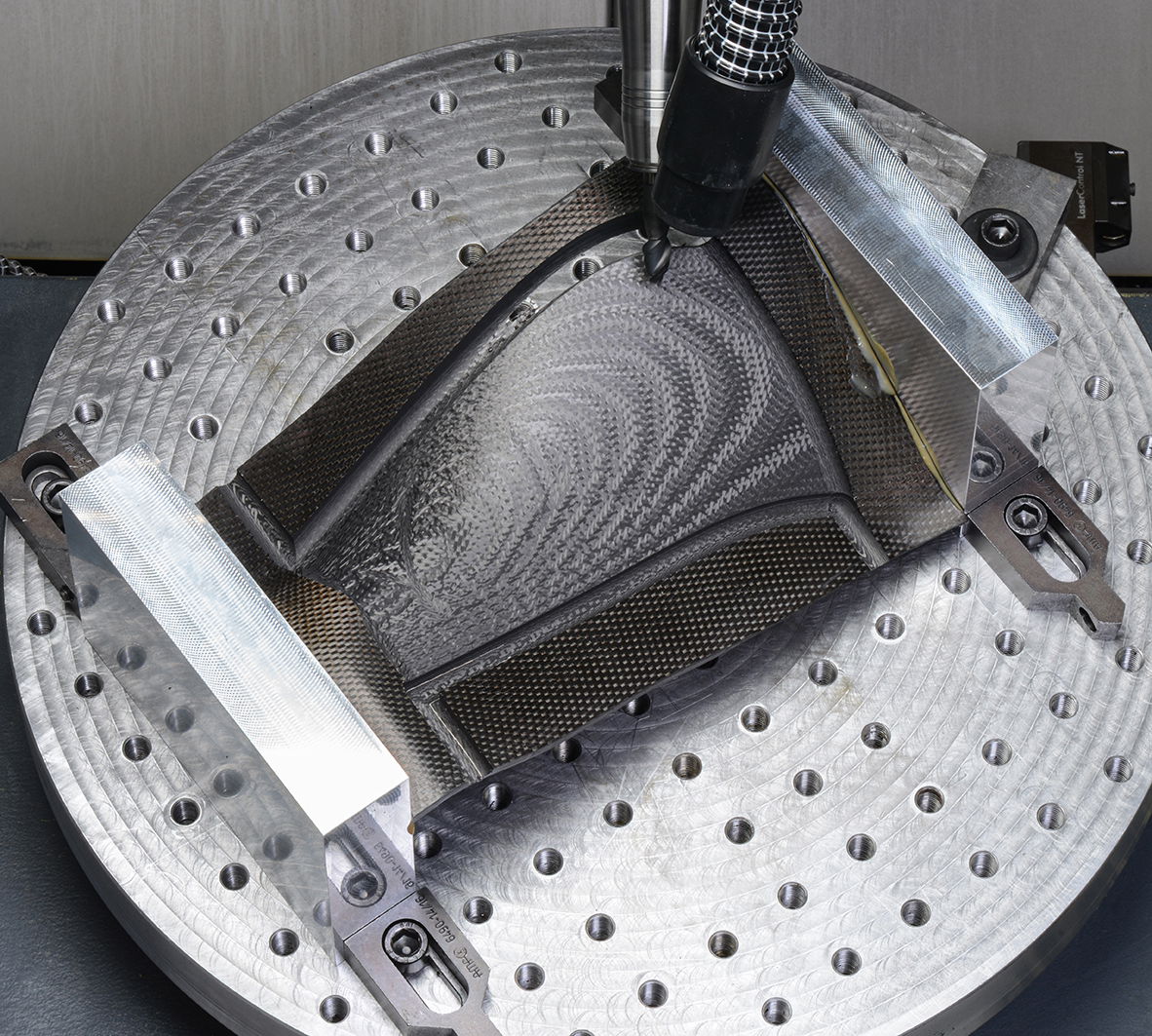
彼はまた、フラウンホーファーがエコデザイン活動を主導しているクリーンスカイ2共同事業にも言及しています。 Fraunhofer IPTは、ライフサイクルアセスメントと環境影響の評価を含むエンジンのエコデザインに焦点を当てています。 「これが、熱可塑性複合材料の検討を開始した理由です」と彼は説明します。 「これまでのところ、TRL [技術準備レベル]は非常に低くなっています。今のところ、開発は、ニアネットシェイプレイアップや少しの熱成形(キャリブレーションステップに似ています)などのさまざまなプロセスルートを製造して試してから、機械加工の観点から仕上げることです。ですから、私たちの前にはまだかなり多くの仕事があります。」
一方、Fraunhofer IPTは、デジタルテクノロジーを使用してすべてのブレードの機械加工パラメータを監視および評価し、金属製の航空エンジンコンポーネントを複合材料に機械加工する専門知識を拡張しています。しかし、複合材料の目標は、このようなサブトラクティブ製造から、より少ない廃棄物でより多くのアディティブ製造に移行することではありませんか? 「はい。ただし、一部のプロセスルートでは、寸法公差を満たすために機械加工が必要です」とJanssen氏は言います。 「私たちが現在取り組んでいるのは、ネットの形に非常に近いものです。」
彼は、現在開発中の設計は、根元が0.75インチの厚さの熱可塑性ラミネートであり、先端がわずか2mmの厚さであると指摘しています。 「そして、さまざまな設計戦略があり、設計エンジニアと一緒に話し合います。また、そのような非常に高負荷の部品用のオートクレーブまたはプレスステップはありますか?このブレードは回転中に少しねじれていることがわかっているため、これは内部応力に関しても役割を果たします。そしてもちろん、バードストライクは重要な問題です。」後者の場合、ヤンセンは熱可塑性プラスチックの靭性の向上をイネーブラーと見なしており、まさにこの理由から、PPS(ポリフェニレンサルファイド)複合材料が翼の前縁に使用されていることを指摘しています。
熱可塑性複合材料の将来の用途
エンジンのナセルに熱可塑性複合材料を使用する可能性について質問しました 、これはおそらく、2021年3月のアビエーションウィークで報告されたように、最近の4つのブレードアウトインシデントの解決策を提供するのに役立つ可能性があります。 記事:
「…ブレードの破片がエンジンのカバーまたはナセルの一部に当たることによって引き起こされた損傷が一連のイベントを引き起こし、エンジンの吸気口やファンカウルの一部を含む大きな構造物が破損しました。あちらへ。" 4つの事故すべてで、航空機の胴体が損傷し、2018年4月のサウスウエスト1380便では、窓の1つが外れ、乗客が死亡しました。
「エンジンコンパートメントに熱可塑性複合材料を使用することへの業界からの関心があります」とヤンセンは言います。「しかし、これは長期的な開発です。」このような開発の1つの問題は、FraunhoferIPTが活動している別の分野である航空当局による認証です。 「現在、新しい製造プロセスが現在および進化している規格に準拠していることをデジタルで証明することにより、認証の労力を削減する方法について認証機関と話し合っています。だから、それは新しい考え方です。 21世紀の製造業では、非常に多くのデータが利用可能です。テストによって1つのプロセスまたは1つの設計を認証するだけでなく、それは凍結されます。」言い換えれば、インダストリー4.0とコンポジット4.0に今日重点が置かれているのは、センサーとAI対応ソフトウェアが継続的にデータを収集し、インテリジェンスを開発して、製造を継続的に最適化し、そのインテリジェンスをデジタルスレッドに送り返して設計を改善することです。これは確かに今日の製造とは大きく異なります。
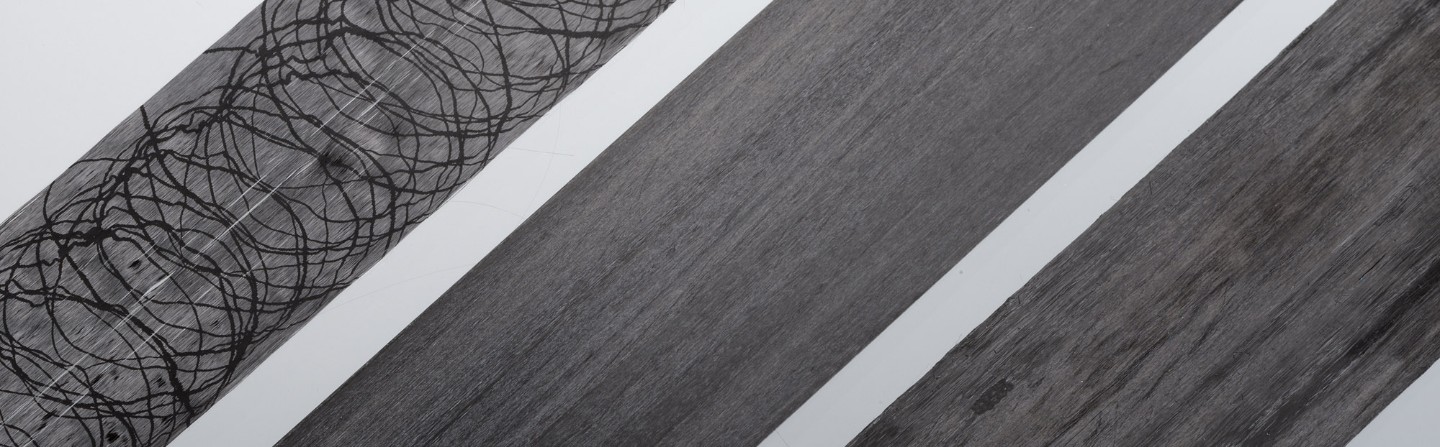
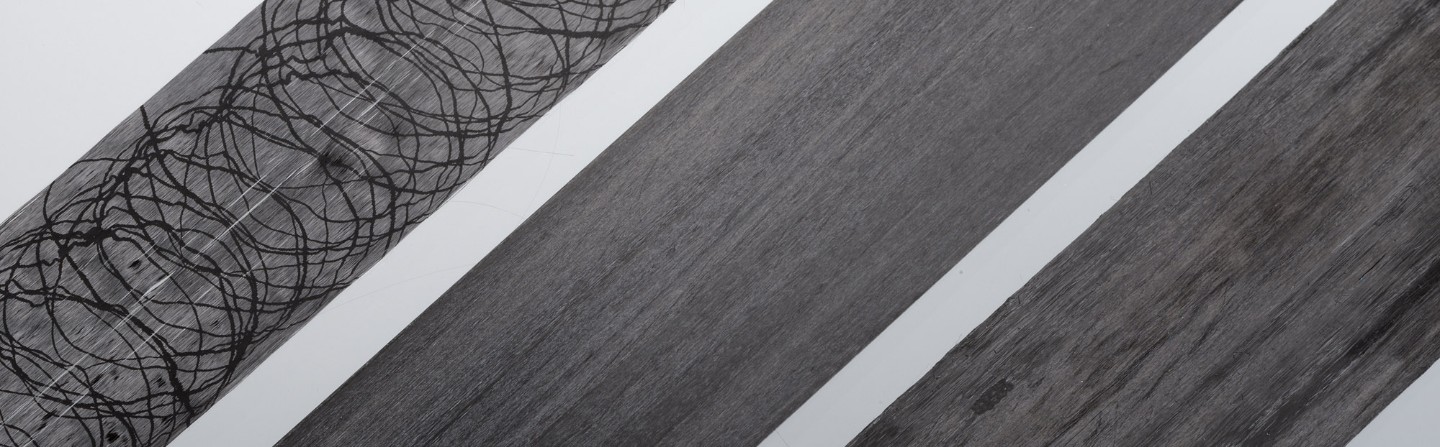
ヤンセン氏は、認証に関するFraunhofer IPTの取り組みは、「エンジン部品用の熱可塑性複合材料などの新しい技術を可能にするのに役立つ可能性があります。つまり、技術、設計、リスク管理を含むすべての側面が考慮されれば」と述べています。彼は、熱可塑性複合材料は、さまざまなの主要な課題を克服するのに役立つ大きな可能性を提供すると主張しています。 Fraunhofer IPTは、熱可塑性複合材料の処理の複雑さを克服するために取り組んでいることを指摘しています。たとえば、新しく利用可能なデジタル製造方法を利用しています。 「さらに、熱可塑性複合材料の可能性を十分に活用するには、再利用やリサイクルを含むライフサイクル全体を検討する必要があります」とヤンセン氏は言います。 「したがって、Fraunhofer IPTは、熱可塑性複合材料の機械的リサイクルにも取り組んでいます。製造時に生成されたデータと複合部品のライフサイクル全体で生成されたデータの両方を考慮することで、高価値のリサイクル材料を実現できると考えています。」
樹脂
- コベストロは熱可塑性複合材料への投資を強化
- 2021ナイフブレードとナイフハンドルに最適なレーザー彫刻機
- RECONTRASプロジェクトは、マイクロ波とレーザー溶接を使用してリサイクル可能な複合材料を取得することを検証します
- OTOMcompositeは、レーザー支援テープの配置と巻き取りを使用して、Composites4.0を作成するためのソフトウェアを開発しています
- 熱可塑性複合材料の熱成形のトラブルシューティング
- 熱可塑性複合材料:構造用バンパーブラケット
- STELIA AerospaceCompositesは水素貯蔵を進歩させます
- TPACとTPRCは、熱可塑性複合材料のリサイクルプロセスを開発しています
- 熱可塑性複合材料の溶接
- 熱可塑性複合材料コンソーシアムは、自動車および航空宇宙向けの大量生産を目指しています
- RTP Companyは、軽くて丈夫な熱可塑性コンパウンドを開発しています