熱可塑性複合材料:構造用バンパーブラケット
GMの2019年モデル(MY)シボレーシルバラード ピックアップは、隠されているが非常に効果的な場所、つまりスチールバンパーの後ろの左側と右側の前面にある複合材の新しい構造アプリケーションを備えています。ハイブリッド熱可塑性複合材/金属ブラケットは、質量を減らし、限られたパッケージスペースでのモーダル、応力、疲労、およびクラッシュテストで同等以上のパフォーマンスを実現し、腐食と保証のリスクを減らし、大幅な部品の統合を可能にします。すべての写真提供者:General Motors Co.
フルサイズのピックアッププログラムに取り組んでいるOEM設計エンジニアになるのは簡単ではありません。一方では、これらの車両を可能な限り安全で、機能が豊富で、燃料効率の高いものにしたいと考えています。一方、顧客、特に建設業界や農業業界の顧客は、毎日自分の車を強く押して、耐久性のある素材であるかどうかについて特定のアイデアを持っています。彼らは鉄鋼を知っており、信頼しています。コンポジット?多分それほど多くはありません。
ゼネラルモーターズ(GM、ミシガン州デトロイト、米国)のフルサイズピックアップのリードデザインリリースエンジニアであるChris Heoと彼のチームは、最新世代のシボレー Silverado の開発に着手しました。 ピックアップでは、車両の質量を減らすために金属から複合材料に変換できる可能性のあるアプリケーションについて話し合いました。
2019年モデル(MY)では、スタイリングされたバンパーインパクトバー(スタイリングされたA面と仕上げ(クロームメッキまたはボディカラーペイント)を備えたプレス加工されたスチールバンパー)を車両のフロントとリアに維持することがすでに決定されていました。 。スタイリング駆動の形状とスチールシェルの質量により、このようなバンパーは通常、バンパーを車両のフレームに結合し、GMのバンパーの耐久性、車両の損傷性、衝突性能、およびパッケージング要件を満たすために1つ以上のスチール補強ブラケットを必要とします。この場合、バンパーの左右の角にブラケットのペアが巻き付けられています。チームメンバーは、これらの重くて複雑なマルチピースのスタンピングを、パフォーマンスや耐久性を犠牲にすることなく、より軽いものに変換できるかどうか疑問に思いました。
「バンパーの金属スキンを維持しながら、隠れたコンポーネントを軽量の素材に変換する方法について話し合いました」とHeo氏は振り返ります。 「バンパーのような重い部品を保持するには頑丈なブラケットが必要であり、バンパーとブラケットの両方が車両の寿命の間機能しなければならないため、これが課題になることはわかっていました。また、これらのブラケットは、要求の厳しいオフセットバリア衝突試験に対応するための鍵であり、金属の場合でも、合格するのは難しい試験です。」
最初に試す
挑戦に臆することなく、GMチームは仕事に取り掛かり、すぐに車両の指定バンパーサプライヤーであるFlex-N-Gate Corp.(FNG、イリノイ州アーバナ、米国)を持ち込みました。当初、外装車のスタイリングはまだ完成していなかったため、合同チームは1年間、業界のオプションを調査し、有効なアプローチについて話し合いました。 「最終的なスタイリングによっては、使用するデザインやアプローチが変わる可能性があるため、適切な時期を待っていました」とHeo氏は説明します。
「別の会社が、構造的ではない非常に小さなブラケットをトラックのバンパーの1つに合成するように変換したことを知っていたので、開始する場所が与えられました」と、FNGエンジニアリンググループマネージャーのSteve Perucca(R&Dプラスチック)は付け加えます。 / metals。 FNGは、乗用車で構造用金属部品を熱可塑性複合材料に変換した経験が豊富であり、チームは前進する自信を持っていました。
設計上の考慮事項
エクステリアデザインがピックアップで固まったので、結合されたチームは、欲求とニーズのリストでブラケットの独自のデザイン作業を開始しました。ベンチマークブラケットは、高張力/低合金(HSLA)鋼からスタンプされ、炭素鋼よりも機械的特性が高く、耐食性が向上しているために選択されました。ブラケットの公称厚さは3ミリメートルで、それぞれの重量は4.362キログラムでした。まず、複合ブラケットは、バンパーの後ろに制限されていたほぼ同じパッケージスペースに収まる必要がありました。したがって、部品の厚さが大幅に増加しないように、十分な強度のある材料が必要でした。
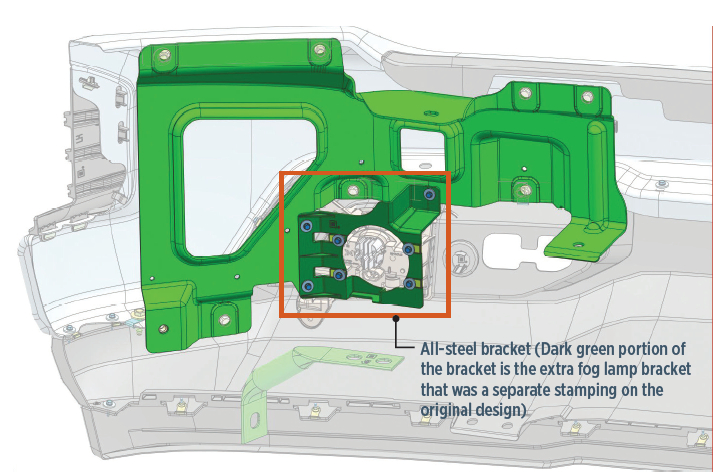
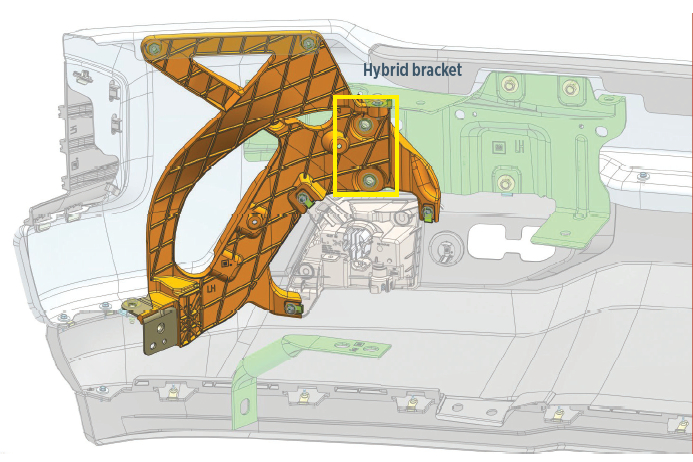
第二に、フロントバンパーは通常、車両のフロントコーナーを包み込み、デザインスタジオが望むスタイリングの手がかりを実現します。ただし、剛性の高いスチールブラケットによってフレームに固定されているため、高速衝突時にバンパーがホイールの内側に押しつぶされ、ホイールの向きに悪影響を及ぼし、ステアリングがロックされる可能性があります。衝撃側のホイールをできるだけ長く保護するために、衝撃時にバンパーブラケットが外れることが望ましいです。 一方、保証の問題を回避するために、バンパーは、車両の寿命の間、通常の使用中に取り付けられたままである必要があります。したがって、チームはこれらの競合するニーズのバランスを取る方法を決定する必要がありました。
チームが対処したかったさらに別の問題は、鋼の成形性の制限のために、ベンチマークブラケットが車両のフォグランプを保持するように成形できず、さらに別の重金属ブラケットのペアを使用する必要があったことでした。可能であれば、チームはフォグランプのサポートを複合ブラケットに統合したいと考えていました。
さらに、ワイヤーハーネスとワイヤーが擦れたり壊れたりするのを防ぐために、ワイヤーハーネスがブラケットを通過するときに、ワイヤーハーネスのピンチポイントを避けることが重要でした。これにより、ヘッドライトやファンなどの重要な機能が短絡する可能性があります。ワイヤーが通ることができる金属ブラケットに穴を設けることによってそれらを回避することは、追加のパンチング操作の使用につながり、設計の自由度の制限のために、より多くの工具費を追加しました。したがって、複合ブラケットでこの問題に対処することを試みることが望ましい。もちろん、複合ブラケットを使用するために車両アセンブリを変更する必要がないようにすることも重要でした。また、自動車用途でよくあることですが、複合ブラケットは理想的には軽量で 金属ベンチマークよりも安価です。最後の懸念は、現在利用可能なCAEモデルが、不連続な繊維強化熱可塑性プラスチックの高サイクル疲労/耐久性を正確に予測できるかどうかでした。
ハイブリッドアプローチ
彼らのウィッシュリストを手にしたので、チームは忙しくなりました。初期の決定は、使用する材料、つまりFNGがすでに経験を積んでおり、GMの承認を得ている材料を選択することでした。彼らは、ロッテケミカル(ソウル、韓国)からSupran PP1340 GMW15890Pと呼ばれる黒色の40%繊維重量分率(FWF)の長いグラスファイバーポリプロピレン(LFT-PP)を選択しました。ブラケットは日光にさらされず、エンジンの熱から十分に離れているため、丈夫なオレフィンポリマーは十分な熱性能を提供します。ハイフローの射出成形可能なグレードのメルトフローインデックス(MFI)は40であり、ゲートを追加することなく複雑な形状を適切に充填できます。余分なゲートは、周囲の材料よりも弱いニットラインを作成するため、構造部品、特に衝突試験に合格する必要がある部品では避ける必要があります。
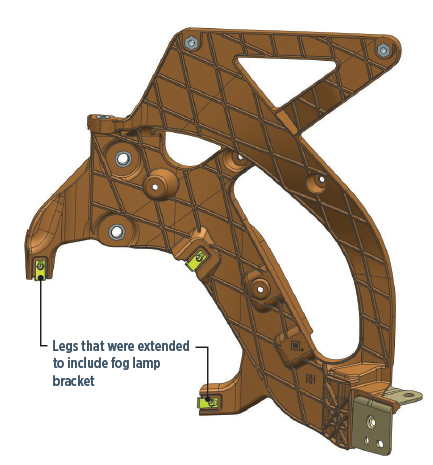
長期的な耐久性と高いクラッシュパフォーマンスという競合するニーズのバランスをとるために、チームはハイブリッドアプローチを採用し、ブラケットを分割しました。バンパーとフレームを接合した部分はHSLA鋼のままですが、外側の部分は複合材に変換されます。このアプローチにより、部品を統合し、質量を減らし、フォグランプを組み込むことができるように設計の自由度が高まりますが、複合部分は、高速サイドクラッシュで壊れて、ホイールの向きが可能な限り縦方向に保たれるように設計されます。ステアリング機能を維持するのに役立ちます。 GMのすべての要件を満たすために、組み立て中に調整できる3つのブッシングとともに、いくつかの金属インサートがブラケットの複合面に追加されました。設計者は、ブラケットの脚(コンポジット/ブラウンCAEデザインで示されている湾曲したエンドピース)をフォグランプを囲むように伸ばすことができ、その場所に別のブラケットが必要ないことを材料に問題がないことを発見しました(図1)。
プロジェクトが進行し、物理的な部品が製造およびテストされたとき、チームはCAEモデルがかなり正確であることを知ってうれしく思いました。 「当初、クラッシュモデリングで耐久性と高G負荷の観点から高サイクル疲労を予測しようとしていたことを考えると、パーツを適切にシミュレートできるかどうか疑問に思いました」とHeo氏は述べています。 「驚いたことに、シェーカーテストの予測結果と測定結果の相関関係は、衝突時でも密接でした。」最終的なブラケットの設計は6か月以内に完了しました。約41x 46センチメートルで、公称壁は3ミリメートルで、より高度な機械用のリブが特徴です。
ツーリングはIntegrityTool&Mold Inc.(カナダ、オンタリオ州オールドキャッスル)によって製造され、2つのキャビティ/プレートと2つのダイレクトドロップ(コールドランナー)を備えた、通気性の良い2 + 2スタックモールドと、4つの部品を生成するシーケンシャルバルブゲーティングを備えていました。 / cycleは Silverado のビルドボリュームが大きいためです プラットホーム。 FNGのVentraEvart部門が成形業者です。ボタン間のサイクルタイムは60秒です。
重要な成果
最初の商用利用では、構造バンパーブラケットに対するGMのハイブリッドアプローチ(図2)は多くの利点をもたらしました。まず、モーダル、応力、疲労、および衝突試験で同等または優れた性能を達成しました(下の表を参照)。
デザイン
10 Gx
20 Gx
1 st モード周波数(Hz)
最大変位(mm)
最大応力(MPa)
最大変位(mm)
最大応力(MPa)
ハイブリッド鋼/複合ブラケット
2.00
213
3.97
381
31.7
オールスチールブラケットのベンチマーク
2.36
259
4.45
480
30.1
金属インサートを備えたハイブリッド複合ブラケットは、質量を減らすだけでなく、その調整された形状により、応力とモーダル性能の両方が向上しました。
第二に、コンポジットの設計の自由度により、比較的小さなパッケージスペースでよりアグレッシブなスタイリングが可能になりました。第三に、ハイブリッドブラケットのペアの質量は、ベンチマークと比較して2.5キログラム/車両減少しました。また、質量分解効果のおかげで、バンパーコーナーが軽量化されたことで、バンパー取り付けブレースやその他のコンポーネントのゲージが削減されたため、フロントバンパーシステムの総質量は、2016年モデルに比べて7.3キログラム削減されました。
さらに、複合ブラケットが錆びないため、腐食のリスクと保証コストが削減されました。質量削減は、燃料経済の改善に貢献したり、法定の道路負荷制限を超えずに重いペイロードを運ぶことができるようにすることで、消費者に利益をもたらします。
ピース価格ベースでは、射出成形金型の追加コストのため、ハイブリッドブラケットは洗浄でした。システムのコストベースでは、追加のコンポーネントをダウンゲージできるため節約できましたが、実際の節約を定量化することは困難です。ブラケットは3年以上問題なく製造されています。
次世代のシルバラードのために 、Heoのチームは、フロントバンパーでハイブリッドブラケットを引き続き使用することを計画していますが、彼はすでにチームメンバーに、リアバンパーブラケットでハイブリッドアプローチを採用する方法について考え始めるように求めています。これは、リアバンパーのコーナーにステップアシスト機能があり、人々がピックアップボックスに簡単かつ安全に乗り降りできるようにするという事実によって複雑になっています。さらに、より多くのコンポーネント(バックアップ警告センサーなど)がスチールスキンの後ろにパッケージ化され、パッケージスペースが削減されます。
「私たちは、問題を調べ、製品がどのように使用されているか、そしてそれらの機能要件が何であるかを理解し、それから限界を押し上げるというスマートエンジニアリングアプローチを使い続けます」とHeoは結論付けています。
樹脂
- コベストロは熱可塑性複合材料への投資を強化
- Oribi Compositesの熱可塑性複合材料:CWトレンド、エピソード4
- 熱可塑性複合材料の熱成形のトラブルシューティング
- Toray Advanced Compositesは、熱可塑性複合材料の機能を拡張します
- Teledyne CML Compositesは、熱可塑性プラスチック加工機能に投資しています
- Cato Compositesは、熱可塑性複合材料の生産能力を拡大します
- 熱可塑性複合材料のレーザー支援テープ巻線の課題
- ACMAが熱可塑性複合材料会議2020プログラムをリリース
- 自動車用複合材料の最初の熱可塑性ドア
- 熱可塑性複合材料:風光明媚なビュー
- 熱可塑性複合材料の溶接