熱流束センサーによるRTMの高速化
航空機の重量の3〜5%を占める着陸装置は、航空機の効率を向上させるために、長い間軽量化の対象となってきました。これは、エネルギーと排出量を削減する電気推進システムへの差し迫った切り替えにより、さらに重要になっています。
たとえば、Safran Landing Systems(Vélizy、フランス)は、航空機の着陸装置の車輪に統合された電気モーターを介したエンジンオフの電気タキシングを可能にし、NOx、CO 2 を削減します。 、COおよび未燃炭化水素の排出量はそれぞれ51%、61%、73%、62%です。これは、より持続可能な航空にとって大きな勝利ですが、電気モーターには電力が必要であり、その電力を供給するために必要なバッテリーは重いです。
したがって、軽量の着陸装置構造に対する需要は、1つの問題を除いて、複合材料を適用するのに最適であるように思われます。 「着陸装置は単一荷重経路構造であるため、構造コンポーネントの故障は深刻な緊急着陸状態を引き起こす可能性があります」と、GKN Fokker Landing Gear(オランダ、ヘルモント)の技術者であるPeetVergouwenは述べています。 GKN Fokker Landing Gearは、F-35 Lightning II 用の炭素繊維強化ポリマー(CFRP)ドラッグステーブレースの開発など、複合着陸装置構造の技術的実現可能性を実証するために10年以上にわたって取り組んできました。 。 「その重要性のため、着陸装置の構造は民間航空機で最も保守的なものの1つです。」したがって、それらは主に高強度金属から製造されています。
しかし、その流れは変わり始めています。 Clean Sky 2は30%の軽量化を追求していますが、HECOLAG(High Efficiency Composites LAnding Gear)プロジェクトのCFRPコンポーネントを介して、2つのアプリケーションに対応しています。最初のアプリケーションでは、既存のアルミニウム製の上部ドラッグステー用にCFRP代替品が開発されました。 もともとLiebherr-Aerospace(リンデンベルク、ドイツ)によって開発および製造されたA350-1000前脚用。 HECOLAGのパートナーであるRoyalNetherlands Aerospace Center(NLR、Marknesse)とGKN Fokker Landing Gearは、このCFRPドラッグステイをLiebherrの要件に合わせて設計しました。 NLRは、社内で開発された自動プリフォーミングテクノロジーを使用して、CFRPドラッグステイの機能的なプロトタイプを作成しました。これは、GKNフォッカーランディングギアによってテストされました。
HECOLAGによって評価されている2番目のアプリケーションでは、NLRとGKN Fokker LandingGearもCFRP 下側ステーを開発しました。 電化された主脚用のサフラン着陸システムと組み合わせて。 CW 特に2021年後半にHECOLAGプロジェクト全体の結果について報告しますが、ここでは、トピックマネージャーGKN Fokker Landing Gearが指導する、INNOTOOL 4.0サブプロジェクトに焦点を当て、樹脂トランスファー成形(RTM)を使用したCFRP着陸装置構造の高度に自動化された生産を進めます。 。具体的には、INNOTOOL 4.0は、センサー統合ツールを実証することを目的としています。これにより、より少ない質量でより小さなツールを実現し、生産サイクルを短縮し、取り扱いを容易にし、エネルギー消費を削減し、自動化を強化して低コストとコンポジット4.0インテリジェントプロセス制御を実現します。 INNOTOOL 4.0プロジェクトは、GAP No.821261に基づくEUのHorizon研究およびイノベーションプログラムに基づくCleanSky2共同事業によって資金提供されています。
INNOTOOL4.0の目標
HECOLAGのこの2番目の部分(冒頭の画像を参照)のデモンストレーターは、より一般的な部分であるとVergouwenは説明します。 「これは、単通路航空機に必要な性能、生産率、およびコストを提供する部品設計、シミュレーション、および製造方法論を実証するためのものです。」 2017年末までに、HECOLAGコンソーシアムは、最初のCFRPデモンストレーター部品と製造ツールを定義し、ツールの熱的挙動を分析し、性能試験を実施しました。この大きくて複雑な製品は、予備的な設計レビューに合格し、その年の後半に4の技術準備レベル(TRL)に達しました。 「最初のデモンストレーターから学んだ問題と教訓に基づいて、硬化サイクルを最適化および短縮するためのRTMツール技術を開発するパートナーを探していました」とVergouwen氏は述べています。 Clean Sky 2 Call for Partnersは2018年に発行され、機器および自動化のサプライヤーであるTechni-Modul Engineering(TME、フランス、クード)と樹脂注入のスペシャリストであるIsojet Equipements(フランス、コルバ)で構成されるINNOTOOL4.0コンソーシアムに授与されました。彼らは2019年4月に作業を開始し、2021年3月に最初のマイルストーンを完了しました。
「複合部品は、鍛鋼やアルミニウムとコスト競争力がなければなりません」と、GKN Fokker LandingGearのVergouwen氏は述べています。 「これは自動化によってのみ可能であり、現在の航空宇宙グレードのオートクレーブ硬化CFRPよりも非常に少ない労働時間と手頃な価格の材料を可能にします。」
したがって、INNOTOOL 4.0は、樹脂フローフロント検出を含む射出および硬化プロセスを監視および管理するRTMツールにセンサーを統合しようとしました。 「目標は完全に自動化することです。プリフォームをロードし、ボタンを押すと、成形装置が温度、圧力、真空、硬化を管理します」と、TMEのコマーシャルディレクターであるStéphaneBessonは述べています。ただし、GKN Fokker LandingGearとTMEが硬化モニタリングを使用するのはこれが初めてです。 「以前は温度センサーと圧力センサーを使用していましたが、樹脂の流れと重合用のセンサーは使用していませんでした」とBesson氏は言います。
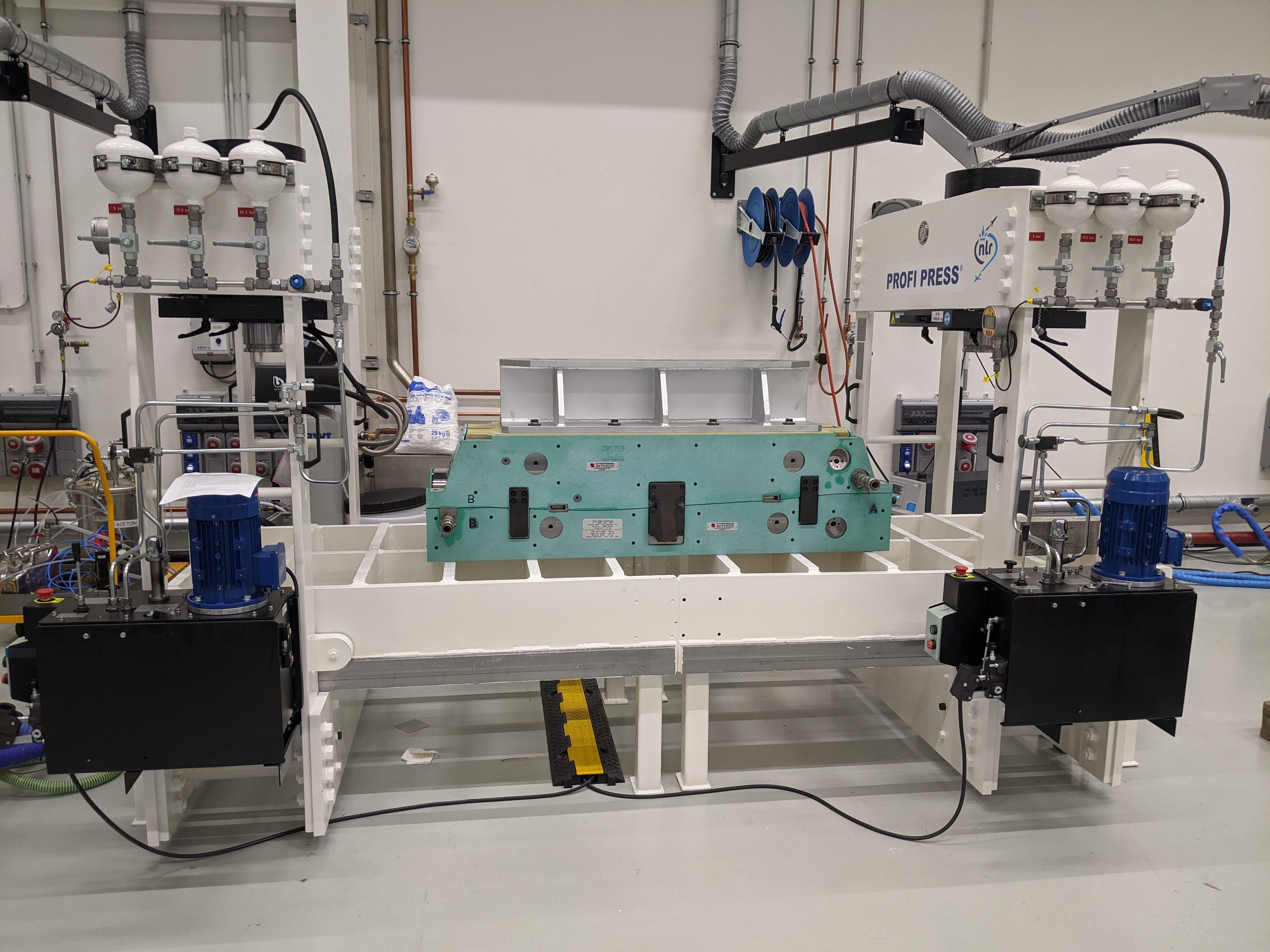
INNOTOOL 4.0プロジェクトの最初のマイルストーンでは、TMEとIsojetが、センサーを備えた成形ツールと射出システムをNLRに提供し、2021年3月と4月にデモンストレーター部品を製造する必要がありました。並行して、TMEは既存のツールを使用してCFRPプレート(サイズ600 x 600ミリメートル、厚さ1〜8ミリメートル)は、施設でのプロセス制御試験用に同じセンサーで変更されています。 「これは、高コストの部品を備えた大きなツールで直接行うのではなく、最初は小規模で行う方がよいことです」とVergouwen氏は言います。したがって、TMEは別のツールを使用しましたが、同じセンサーを使用して機能と深さを示しました。このテストが完了すると、NLRはメインのHECOLAGツールを再利用して、CFRPデモンストレーターの新しいラウンドを作成し、実際の部品のプロセス制御をさらに最適化します。
RTM制作ツールの設計
TMEは、機械的および電気的設計にDassaultSystèmes(Vélizy-Villacoublay、フランス)、熱的および機械的シミュレーションにANSYS(Canonsburg、PA、U.S。)によるCATIAV5ソフトウェアを使用したRTMツール設計の生産を開始しました。このツールは、Isojetのピストンベースの1K-2K(1液型および2液型樹脂用)システムと組み合わせて、Hexcel(米国コネチカット州スタンフォード)、HexFlow 2K RTM 6およびSolvay(米国ジョージア州アルファレッタ)1Kを注入します。 PRISM EP 2400一液型、航空宇宙グレードのエポキシ樹脂、最大20バールの射出圧力。
「この成形ツールの形状は非常に複雑です」とBesson氏は述べています。「3Dドライプリフォームのさまざまな厚さを、閉じた管状の形状と組み合わせています。これにより、複雑な厚さの遷移が発生し、プリフォームアセンブリ、プライエンドの精度、内部温度勾配、樹脂収縮、および内部マンドレルの加熱方法と加熱能力を最適化して短いサイクルタイムを実現する方法に関する問題が発生します。短いサイクルタイムを実現するには、ツールのすべての要素が使いやすく、堅牢で、急速な加熱と冷却が可能でなければなりません。」 INNOTOOL 4.0プロジェクトでは、非金属の金型ソリューションが簡単に要求されましたが、しわを最小限に抑え、成形中の繊維の位置合わせを確実にするために必要な圧力のために、上下の鋼製金型の典型的な一致セットが考案されました。
一致した上下の金型とマンドレルは加熱および冷却されます。 「マッチした金型は、マンドレルが電気的に加熱されている間、統合された水回路を使用します」とBessonは説明します。 「水循環は部品サイクル時間を短縮するための迅速な加熱と冷却を提供し、電気加熱はスペースが限られているマンドレルでも同じことを実現します。」
「もう1つの課題は、マンドレルの部品の数でした」とBesson氏は言います。 「形状が複雑で、成形後にマンドレルを取り外す必要があるため、6つの自己発熱コンポーネントと2つのサポート要素で構成され、センサーが通過してマンドレル部品の内部温度を制御します。使用中、これらの要素は、オペレーターをガイドするベースサポートの助けを借りて手作業で組み立てられます。」解決策としてのインフレータブルマンドレルの使用は、より大きなHECOLAGプロジェクト内で完了しますが、それはINNOTOOL4.0サブプロジェクトには含まれていませんでした。
熱流束センサー
TMEは当初、誘電センサーを使用して樹脂の流れと硬化を監視することを計画していましたが(「複合材料の硬化監視のためのACとDCの誘電測定の組み合わせ」を参照)、TFX(Boncourt、Switzerland)の熱流束センサーに切り替えました。 「開発が進むにつれ、ポリマーや複合材料に直接接触することなく測定できるセンサーを制御できるようにしたかったのです」と、TMEのプロジェクトマネージャーであるホルヘロペストーレスは説明します。 「TFXセンサーは、材料を伝播する熱流束を測定するため、これを可能にしました。」彼は、これは基本的に示差走査熱量測定(DSC)で使用される測定と同じであり、ポリマーまたは複合材料の硬化状態を分析する実験技術であると指摘しています。特に、TFXセンサーとDSCテストはどちらも、重合/硬化中に放出される熱を測定し、温度と時間に対する熱流束の曲線を作成します。
TFXセンサーの場合、温度データは熱流束センサー内の内部温度センサーから取得されます。誘電体センサーにも同様に内部温度センサーが装備されていますが、2つのセンサーは大きく異なります。 「誘電体センサーは、硬化中にポリマーの特性を直接測定します」と、TFXマネージャーのFabienCara博士は説明します。 「熱流束センサーは、特定の瞬間の材料の状態を示しません。ただし、樹脂の流動と重合中に発生する熱を測定することで、プロセスがどのように動作しているか、および製造された各部品の硬化サイクルがどの程度再現可能であるかを把握できます。また、DSCと同様に、硬化プロセスの曲線全体を確認する必要がありますが、硬化を監視する機能は非常に信頼できます。」
数十年の経験
2000年にThermofluxとして設立されたTFXセンサーは、R&Dセンターでの試験や、世界中の100を超える顧客による産業用アプリケーションで使用されています。 「私たちは15年以上前にRTMと協力し始めました」と、Caraは言います。 2006年と2012年に、RTMと3D織りのプリフォームを使用して製造された航空機エンジンのファンブレードの硬化を監視するための2つの大規模なプロジェクトを開始しました。 Safranは、パリ近郊の複合材ラボで開発したデータ取得システムを持っています。最大100個の信号を同時に記録し[(熱流束、温度、圧力])、これらを分析してプロセスサイクルを硬化および監視できます。」 TFXはまた、フランスのレザヴニエールにあるラボでHexcelと協力して、乾燥プリフォームに注入された熱硬化性樹脂の品質と処理サイクルを監視しています。 TFXセンサーは、IRT-M2P(Porcelette、フランス)のプロジェクトでも使用され、Compression RTM(詳細)を実証しました。 「当社のセンサーは、SMCおよびBMC成形コンパウンドを含む圧縮成形などの高速プロセスに非常に効率的です」とCara氏は述べています。 「また、2016年にハンツマンアドバンストマテリアルズ[(スイス、バーゼル)]で、「1分未満でオートクレーブ品質の構造エポキシ部品」というタイトルの開発でJECイノベーション賞を受賞しました。」
TFXには、センサーへの熱伝達方法(伝導(RTM、圧縮および射出成形)、対流(オートクレーブ、オーブン)、および放射(フィラメントワインディング、AFP))に基づいて、あらゆるタイプの複合材料成形プロセス用のセンサーがあります。 INNOTOOL 4.0プロジェクトで使用されたセンサーは導電性であり、金属RTMモールド内に埋め込むために設計されました。 「ツールの表面と複合材料から最大1mmの距離で、非常に再現性の高い信号を提供します」とCara氏は述べています。
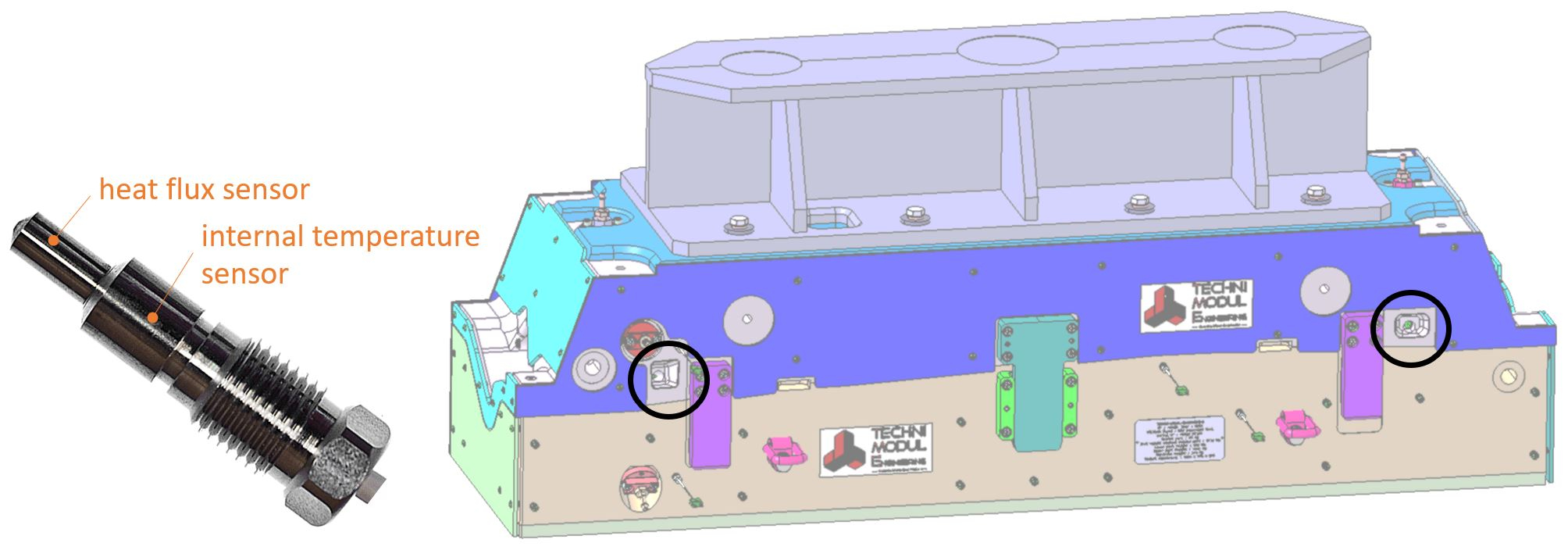
TMEは、2つのTFX-191センサー(1つは樹脂入口に1つ、もう1つは樹脂出口に)を、対応する生産ツールセットの上型に取り付け、NLRに送信しました(図1、2)。 NLRは、この製造ツールを使用して、2021年3月と4月にHECOLAGデモンストレーター部品を製造しました。TFX-191センサーは、厚い金属製のツール用です。
並行して、TMEは、サンプルCFRPプレートの作成に使用されるより小さな社内ツールを採用し、より薄いツール用に、より短い2つのTFX-224センサーで変更しました(図3)。次に、このRTMプレートツールセットを使用して、上記のINNOTOOL4.0の目標に従ってセンサーのデモンストレーショントライアルを実施しました。 「これらのセンサーは、私たちがSafranに使用したものと似ていますが、今でははるかにコンパクトで高感度になるように改善されています」とCara氏は言います。センサーは部品の中央近くと樹脂出口の近くに配置されました。熱流束センサーに加えて、TFXは2つのデータ取得システムを開発して提供しました。1つはIsojetに配信され、もう1つはTMEがCFRPプレートの試験に使用しました。
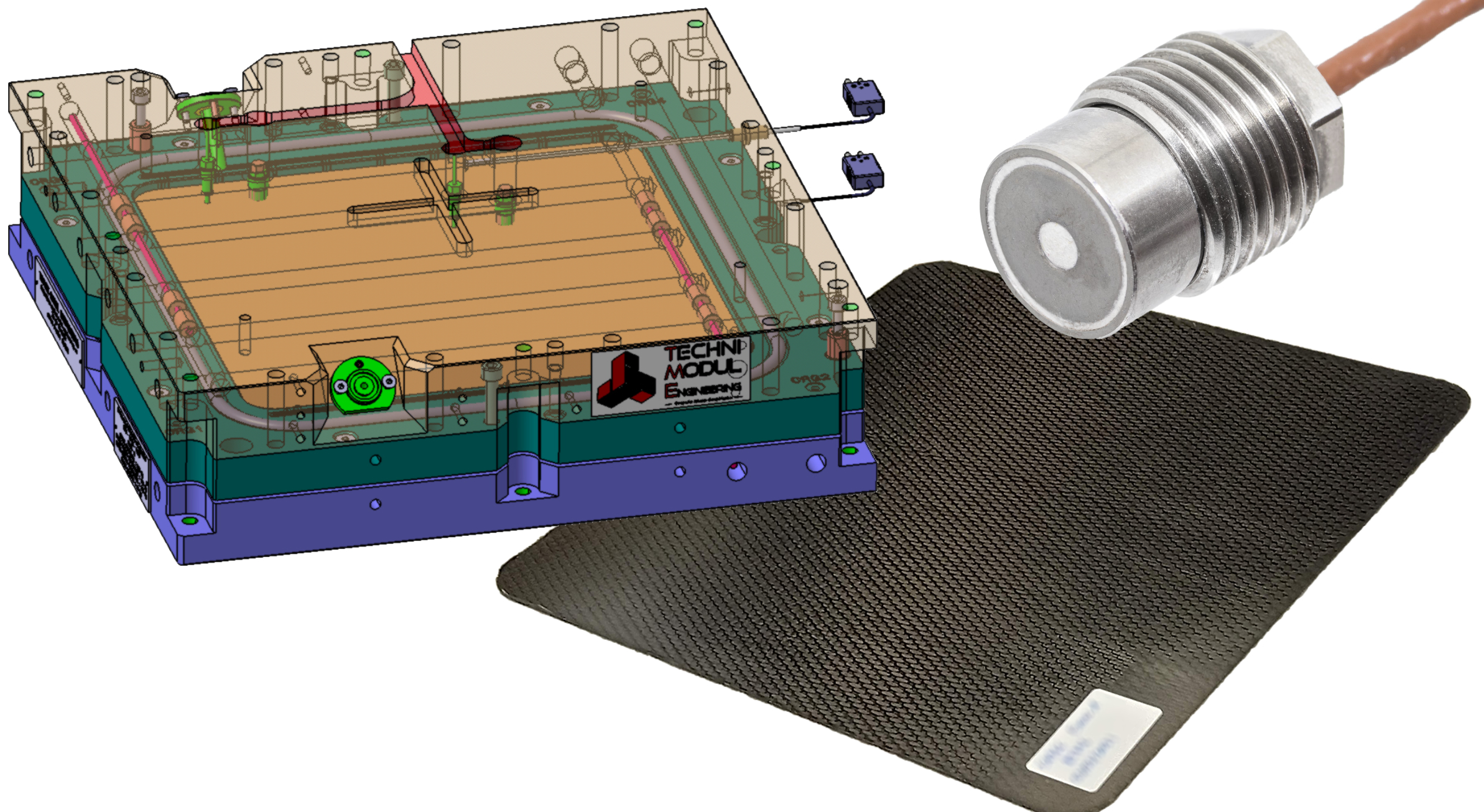
INNOTOOL4.0のテスト結果
TMEがTFXセンサーで修正されたプレートツールを使用して実施した試験では、2つの異なる樹脂(HexFlow RTM6とPRISMEP 2400)、および部品の厚さと全体的な硬化時間の影響をテストしました。 「センサーは、硬化サイクルを監視するための優れた信号を提供しました」とCara氏は言います。 「次に、チームは硬化曲線を分析し、RTM6の硬化時間が処方された2時間の硬化から少なくとも30分短縮できることを示しました。」
これは下の曲線で見ることができます。ここで、t =0時間は注射の開始です。硬化時間は温度が180°Cに達したときに始まり、硬化の終わりは相対硬化レベルの99%に相当することに注意してください(右の縦軸を参照)。硬化の終了は、生の熱流束の安定化とも一致します。
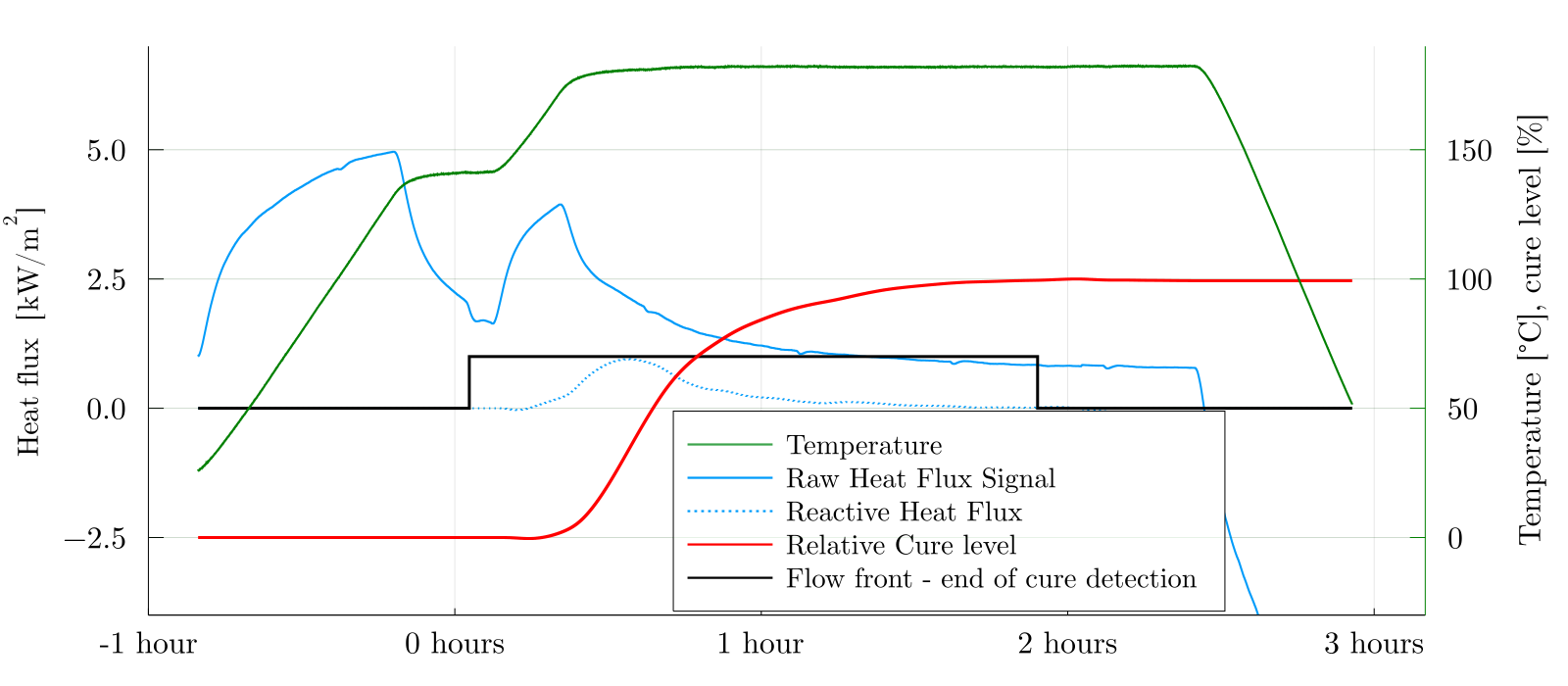
これは、ガラス転移温度(T g )を測定するDSCの代替ラボ手法である動的機械分析(DMA)を使用した離型部品の硬化状態測定によって検証されました。 )コンポジット用。 「DMAの結果により、RTM 6樹脂の場合、T g 180°Cで90分間硬化した後も、変化はありません」と彼は付け加えます。
厚さの影響も調べた。 「TMEがセンサーの実証試験でテストした最初のCFRPプレートは、厚さが2ミリメートル未満でした」とCara氏は述べています。 「これらのプレートは、発熱と熱応力および部品品質の潜在的な問題を防ぐために、繊維量が多く(50〜60%)、硬化サイクルが遅いこともありました。これはすべて航空宇宙部品ではごく普通のことですが、樹脂が非常に少ないため、樹脂反応によって放出される熱流束の量が少なかったことを意味します。そのため、実際には、ツールと部品を加熱する海の中で樹脂が硬化することによる熱流束の針を探していました。」
言い換えると、Caraが説明するように、「ほとんどの航空宇宙RTM硬化サイクルでは、ある温度で樹脂を注入し、次に傾斜して2番目のより高い温度で硬化します。したがって、射出が終了すると、ツールが硬化温度まで加熱され、システム全体に大きな熱流束が発生します。」ただし、DSCテストと同様に、熱流束センサーで硬化を監視するための鍵は、重合/硬化中に放出される熱を測定し、成形システムと時間の熱流束対温度の曲線でそれらの測定値を表示することです。 「そこで、金型の加熱のベースラインとその熱の部品への伝導を差し引くのに役立つ方法を発明しました。これにより、樹脂反応の熱流束を特定できます。」
したがって、最初の薄いプレートのプロセス条件は非常に困難でしたが、Cara氏は次のように述べています。しかし、部品を厚くすることで、部品の厚さによる熱流束レベルの違いを正確に確認することができ、これにより、薄い部品での硬化モニタリングが検証されました。」上記の曲線(冒頭の写真にも示されています)は、3.2mmの厚さのプレートでRTM6樹脂を使用して得られたものであることに注意してください。
ただし、レジンフローフロント検出の結果はより問題がありました。 「出口近くのセンサーでは、流れを非常によく見ることができましたが、樹脂が非常に遅く到着した中央近くのセンサーではそうではありませんでした」とCara氏は言います。 「熱流束センサーを使用したフローフロント検出では、局所的な熱場に変化をもたらすために樹脂の流れが必要です。これは、樹脂がプリフォームと同じ温度でない場合に発生します。」彼は、0.1°Cを超えるΔTで検出に十分であると述べています。 「しかし、薄いCFRPプレートの試験では、金型内の温度は非常に均一で、樹脂の到達は非常に遅くなりました。したがって、熱コントラストは、システム全体の熱雑音に対する樹脂の到着を検出するのに十分ではありませんでした。ただし、出口への樹脂の到着は、ランナー[プリフォームとモールドエッジ間のギャップ、「RAPMの複雑な形状の部品の製造」を参照]により速くなり、検出と監視が容易な、より大きな熱コントラストの作成に役立ちます。 」
Caraは、センサー内に統合された加熱機能を使用するTFXが開発した新しいアクティブセンサーを使用して、この樹脂フローフロントモニタリングを改善できる可能性があることを示唆しています。 「これにより、センサーは、本質的に困難な部品やプロセスに必要な熱コントラストを提供するのに役立ちます」と彼は説明します。
複合プロセス制御機能の拡張
「これまでに完了した作業に満足しています」とTorres氏は言います。「しかし、これは最初のステップにすぎません。目標は、これらの熱流束センサーを使用して、生産環境での複合材料の処理を管理することです。」これは、樹脂の到着に基づいてセンサーシステムから射出装置に信号を自動的に送信し、硬化曲線のゼロ勾配に基づいてプレスに信号を送信することで可能になるとCara氏は言います。トーレス氏は、TMEには、温度と圧力を管理する射出成形機とRTMプレス用のプロセス制御システムがあると付け加えています。 「次のステップは、TFXセンサーをこれらの制御システムに統合し、ラップトップからプロセス全体を管理することです」と彼は言います。 Cara氏は、TFXセンサーとデータ取得は、圧力センサー(Kistler、Winterthur、Switzerlandなど)とも連携して、この全体的なプロセス制御を支援し、彼の会社は熱流束、温度、およびを測定するセンサーを開発していると述べています。 em> 単一の統合デバイス内の圧力。
しかし、このプロセス制御は手頃な価格ですか? Cara氏によると、監視システムへの最初の10〜30,000ドルの投資は、通常、開発フェーズで利益を達成し、プロセスと部品の理解を改善することで試行錯誤を減らします。 「その後、システムは生産中の節約を提供し、サイクルタイムを短縮し、再現性を確保し、ドリフトや不適合の早期検出を提供します。」
GKN Fokkerで、Vergouwenは、サイクルタイムを短縮し、コストを改善する能力が証明されると、「INNOTOOL 4.0およびHECOLAGプロジェクトで実証されたタイプの着陸装置コンポーネントだけでなく、すべてのタイプの複合材を想像することができます。部品。それは私たちのデザインスペースを開き、軽量着陸装置の限界をさらに押し上げることを可能にするでしょう。」 Bessonは、さらに幅広いアプリケーションを検討しています。「このタイプのプロセス制御は、あらゆる種類の金型や複合部品用に開発できます。」
樹脂