明日のリブの翼:ワンショット、熱可塑性、OOA統合
2015年に開始されたエアバスのWingof Tomorrow(WOT)プログラムは、過去6年間、単通路の民間航空機の翼のための、よりコスト競争力のある、よりスループットの高い材料、製造、および組み立て技術を探求してきました( CW を参照)。 em> の以前のWOTプログラムの報道)
GKN Aerospace Global Technology Center Netherlands(Hoogeveen)のディレクターであるArnt Offringaによると、 GKN Aerospace(英国、ブリストル)は、樹脂トランスファー成形(RTM)と4つのアルミニウム製ウィングリブを介して作成されたウィングスパーデモンストレーターの開発など、WOTプログラムで非常に積極的に活動しています。 GKN Aerospaceが最近提供した別の技術デモンストレーターは、コスト競争力のある熱可塑性複合リブと、それを製造するためのワンショット脱オートクレーブ(OOA)製造用の革新的なモジュラープレスシステムの両方の開発に関与しました。
熱可塑性プラスチックへの飛躍
2018年、GKN Aerospaceは、5人のデモンストレーターを作成するために使用できる材料と製造技術に関する社内ディスカッションを開始しました
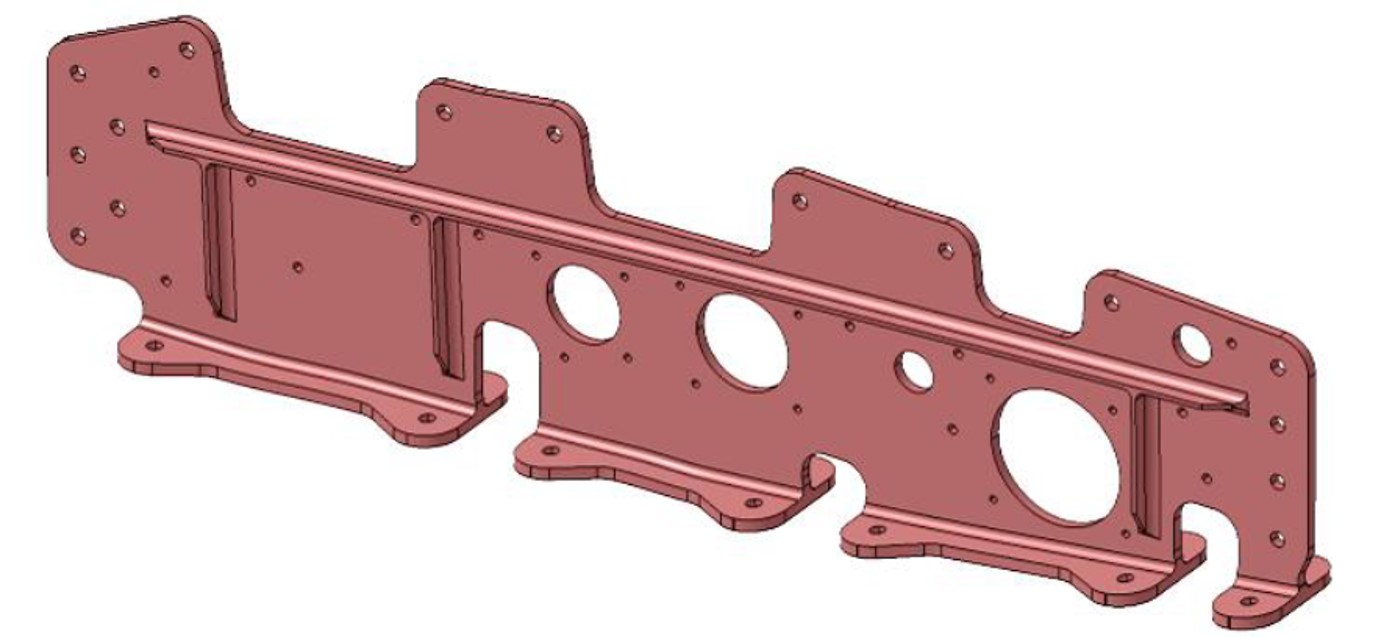
リブの設計。 薄くて軽量な部品を実現するために、リブの設計(上)にはGKNの突合せ継手技術(下)と射出成形された補強材フィラー(中央、緑色で表示)が組み込まれています。
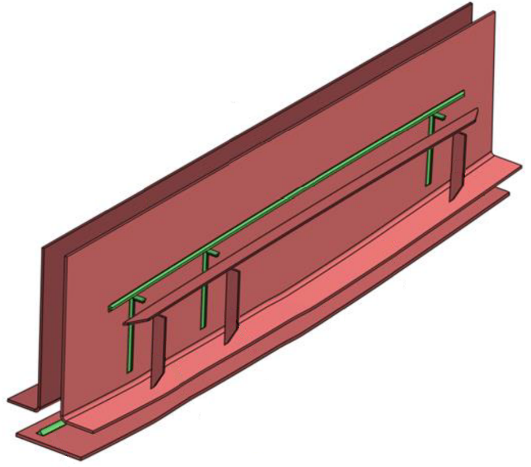
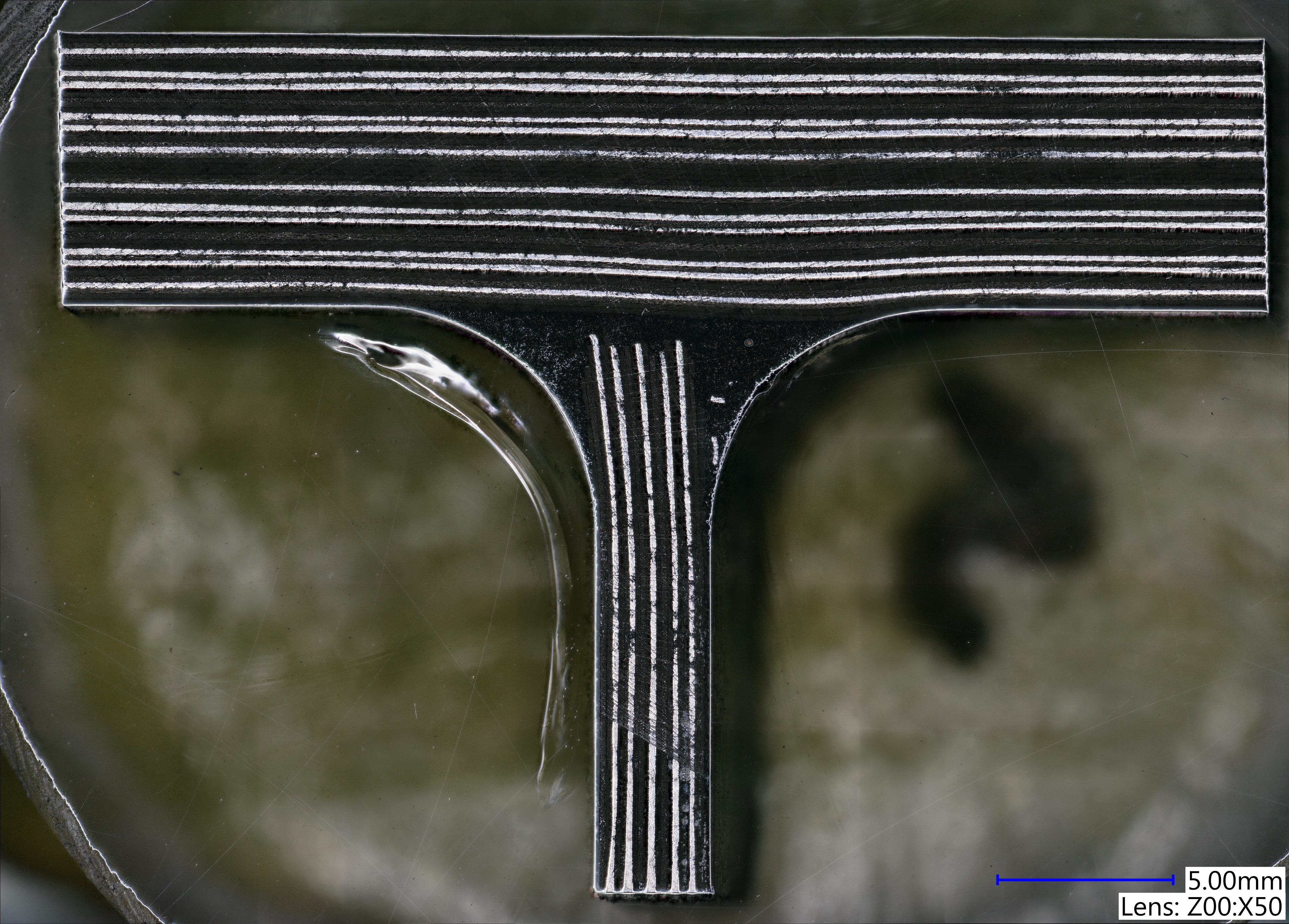
WOTプログラムのリブ。 GKN Aerospaceは、熱硬化性および熱可塑性複合材料を含むいくつかの材料オプションを比較しました。民間航空機のリブの伝統的な材料であるアルミニウムは、4つの大きな船内リブを製造するために選択されましたが、小さな船外リブについては、同社は複合オプションを検討することを決定しました。 Offringaは、WOTデモンストレーターは複合翼になるため、アルミニウムと競合できる複合リブを開発することは論理的なステップであると述べています。
「複合翼の複合リブは、いくつかの理由で有益です」と彼は言います。 「まず、複合材と複合材を使用すると、複合材の翼に金属製のリブがある場合とは異なり、材料間で熱膨張に違いがないことを意味します。その逆も同様です。第二に、腐食に関する問題や懸念はありません。複合材料はまた、軽量化を意味します。最後になりましたが、コンポジットを使用すると検査が簡単になります。」
Offringaは、典型的な金属製のリブは、最終的な翼が組み立てられたら、人間による目視検査が必要であると説明しています。ただし、翼の内側にリブが配置されているため、人間が翼に入って検査できるように、大きな楕円形のハッチを下部の翼の外板に切り込む必要があります。 「複合リブを使用すると、リブの疲労が少なくなり、検査する必要のある潜在的な疲労亀裂が少なくなります。検査がはるかに簡単になり、集中力が低下し、ハッチをウィングスキンに組み込む必要がなくなります。それは連続的な翼の皮になるでしょう」と彼は言います。
熱硬化性または熱可塑性複合材料のいずれかから、軽量化、耐食性、および侵襲性の低い検査の利点を得ることができます。 「私たちは内部調査を行い、重量、コスト、工業化を調べました。さまざまな技術を比較した後、熱可塑性プラスチックを選択しました。これは、コストに関して最も可能性が高く、最良のビジネスケースであったためです」とOffringa氏は言います。 。
WOTデモンストレーターがテストされるエアバスの英国フィルトンウィングテクノロジーセンターに近接していることを考えると、GKNAerospaceの英国ブリストル支店は同社のWOT作業の主要ハブです。ただし、FokkerTechnologiesとしての時代からのGKNAerospace Netherlandsの熱可塑性プラスチックに関する専門知識を考えると、2つのGKNAerospaceチームがリブデモンストレーターのために力を合わせました。 「設計は英国で行われましたが、製造開発はオランダで行われたため、GKNAerospaceのさまざまなチーム間の非常に素晴らしい協力関係でした」とOffringa氏は言います。
エアバスのWOTの責任者であるスーパートリッジは次のように述べています。「パートナーとのコラボレーションは、ウィングオブトゥモロープログラムの重要な側面です。リソースを組み合わせることで、両方の組織の機能を活用してより良い結果をもたらすソリューションを推進できます。」
エアバスに納入されたWOTリブには、GKN Aerospaceがソルベイ(ベルギー、ブリュッセル)のAPC炭素繊維/ポリエーテルケトンケトン(PEKK-FC)テープを使用しました。これは、同社のNovaspire PEKK-FC(FC)速結晶化配合に基づいています。 Offringaは、Toray Advanced Composites(Morgan Hill、CA、U.S。)の低溶融炭素繊維/ポリアリールエーテルケトン(PAEK)材料も、将来のリブ構造のオプションとして評価されていると述べています。
次世代ウィングリブの設計
典型的な単通路航空機の翼には20以上のリブがあります。熱可塑性複合デモンストレーターリブは、デモンストレーターウィングの14番目です。他の人は代替の材料とプロセスを実演します。
熱可塑性複合リブは、多くの場合、小型航空機のスタンプ成形によって製造されます、とOffringaは言います。ただし、GKN Aerospaceは、WOTデモンストレーターのようなナローボディの場合でも、民間航空機の翼が非常に高い圧縮および引張荷重下に置かれているため、WOTリブのオプションとして従来のスタンプ成形を除外しました。
「従来の意味で熱可塑性リブをスタンプ成形する場合は、非常に厚いリブを作成し、それに作用する力に耐えられるように、ウェブを厚くして強度を高める必要があります」とOffringa氏は言います。軽量化の要件を考えると、これは好ましくありません。さらに、スタンプフォーミングでは、パーツが下翼の外板に接続するリブに両面下部フランジコンポーネントを作成できません。追加のコンポーネントを製造し、リブの残りの部分にボルトで固定する必要があります。 GKN Aerospaceは、チームが念頭に置いていた設計の柔軟性を高める製造プロセスを必要としていました。
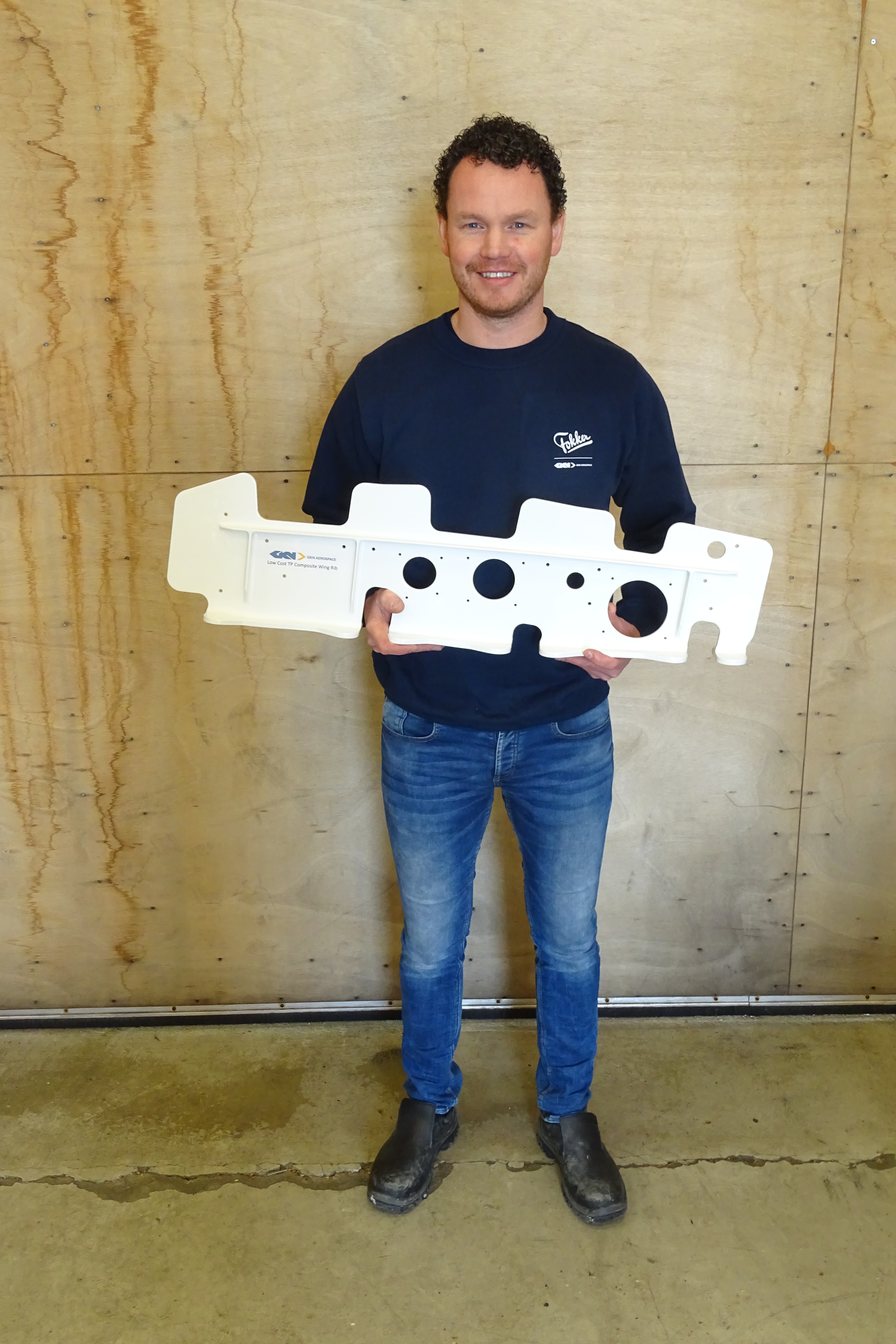
GKN Aerospaceの長さ90センチ、高さ24センチの熱可塑性リブは、垂直ウェブと、リブの下部から伸びる厚さ8ミリメートルの双方向フランジを備えています。重量要件を満たすために、ウェブの厚さはわずか7ミリメートルです。座屈を防ぎ、剛性を高めるために、ウェブはGKN Aerospaceの突合せ継手技術を使用して3ミリメートルの厚さの補強要素で補強されています。この技術では、平らな補強材のプリフォームと射出成形された「フィラー」材料を使用して、強力で連続的な接合部を作成します(「熱可塑性プラスチック」を参照)。主要な航空構造は、ソルベイの炭素繊維/ PEKK-FCテープで製造されたガルフストリーム胴体パネルでのこの技術の使用について学ぶために、さらに一歩前進します。
「この形状を複合材料で作成して堅牢にできれば、私たちが探していた軽量化を備えた非常に軽量な設計になることはわかっていました。しかし、問題は、このような複雑な形状をコスト効率よく高レートでどのように作成するかということでした。そこで私たちはこの新製品の作成に力を注いでいます」とOffringa氏は言います。
ワンステップのOOA製造
このプロセスは、GKN Aerospaceが以前にTAPAS(Thermoplastic Affordable Primary Aircraft Structure)プロジェクトで使用した技術と、同社の突合せ継手技術を使用するGulfstreamの胴体パネル開発に基づいています。 WOTリブについては、GKNAerospaceがOOAのワンステップ統合プロセスを開発しました。 「オートクレーブから初めて出て、前の作業を次のレベルに引き上げました」とOffringa氏は述べています。
まず、一方向(UD)熱可塑性テープを正しい幅にスリットし、ラミネーターを使用してフラット要素を2つのL字型ウェブプリフォームにプリフォームします。ウェブプリフォーム、フランジ用のフラットプリフォーム、およびストリンガーを構成する小さなプリフォームと射出成形フィラー要素はすべて、樹脂トランスファー成形と同様のモジュール式共圧密プレス内に配置されたツールにロードされます。 (RTM)を押します。プレスが閉じ、ブラダーシステムを使用して水平方向と垂直方向の両方から圧力を生成し、オートクレーブ内の圧力をシミュレートします。統合された抵抗加熱システムは、固化のために冷却する前に、複合材料を短時間溶融温度にします。
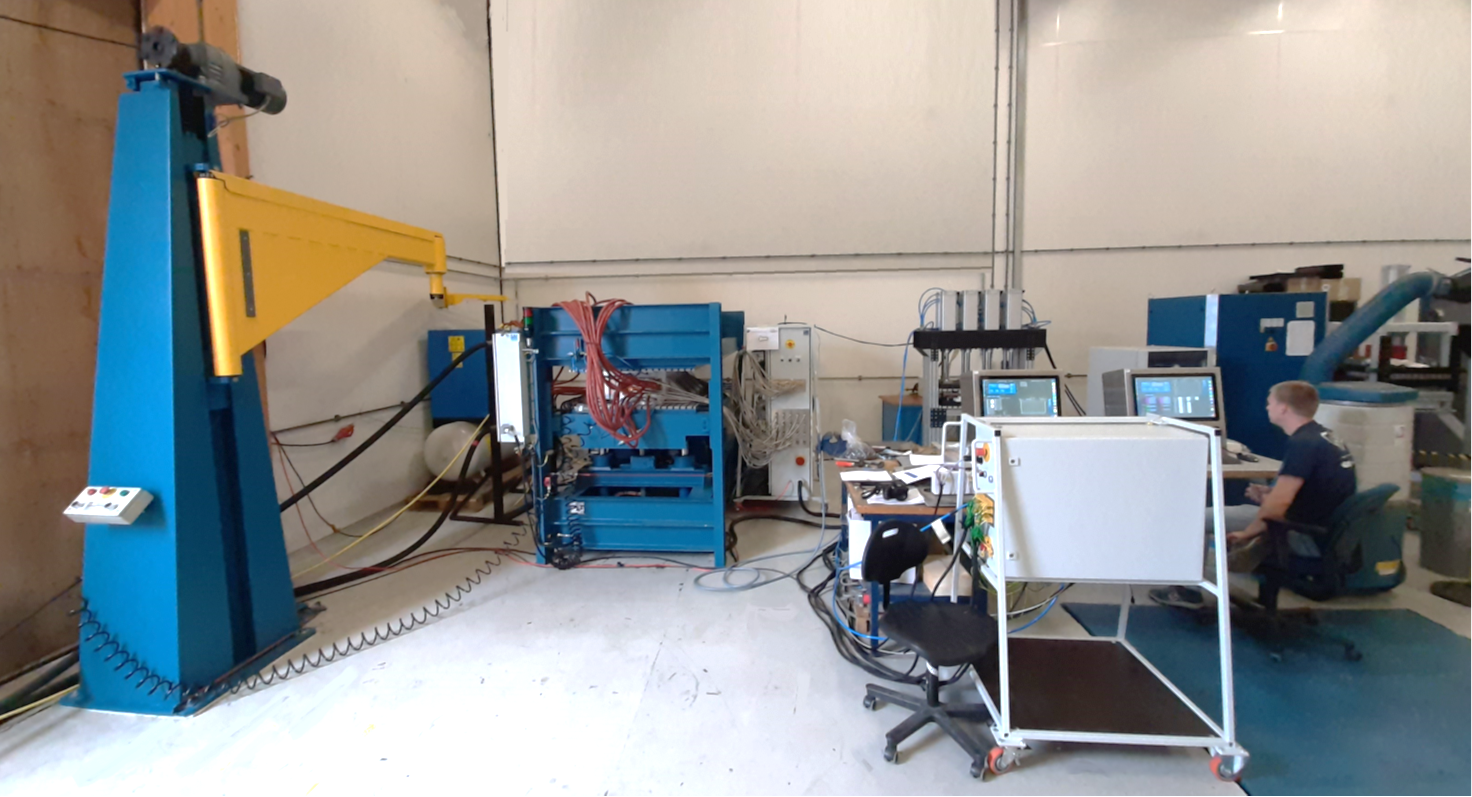
「開発作業のほとんどをツールの調整と最適化に費やしました」とOffringa氏は言います。システムはモジュール式に設計されています。工具は、同じ加熱および冷却システムを維持しながら、さまざまな寸法のリブまたは他のタイプの部品に対応するように交換できます。これらのリブには必要ありませんが、テクノロジーセンターで開発されたプレスGKN Aerospaceは、長さ6メートルまでの部品に対応できます。これには、他のパネルや梁も含まれる可能性があります。
熱可塑性プラスチックを処理する場合、プロセス制御システムが重要です。熱可塑性樹脂は熱硬化性樹脂よりも高温で溶融するため、反りを最小限に抑え、嚢胞性を最大化するために、制御された一貫したプロセスで冷却する必要があります。 「最初から最後まで正確なプロセスを制御することは非常に重要です」とOffringa氏は言います。 「加熱サイクルの熱管理は非常に重要です。」 (熱可塑性プラスチックを使用する場合の問題とプロセス制御の重要性の詳細については、この記事の「熱可塑性(TP)形成の問題」サイドバーを参照してください)。
特別な工具機能を使用して、薄く統合された補強材を工具から簡単に外すことができます。離型した部品はネット形状に近く、トリミングして完成品を形成します。ツールインからツールアウトまで、プロセス全体で約45分かかります。これは、1回のプレスで、8時間のシフトで約15個のウィングリブを製造できることを意味します。
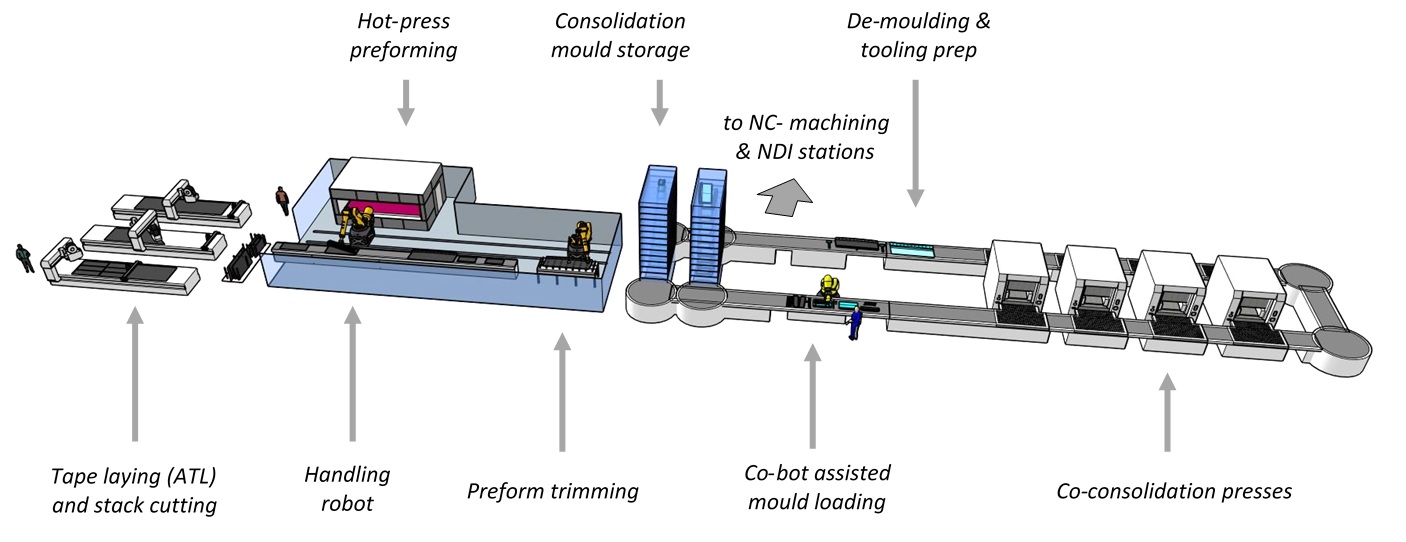
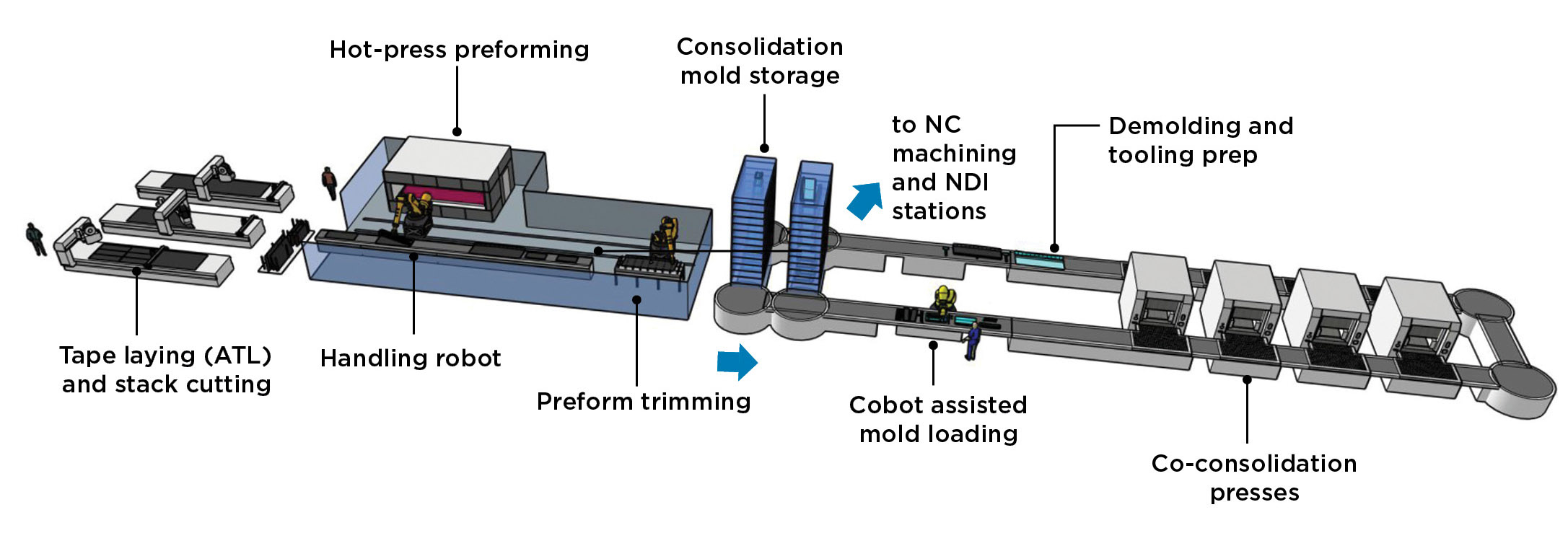
「最終的には単純な製造プロセスになります」とOffringa氏は述べています。 「私たちは一度に多くのことを行っています。さまざまな形状のプリフォームを統合し、リブの下部に双方向フランジを作成すると同時に、突合せ接合技術でウェブを補強しています。ただし、最終的には、材料のすべての要素を取得してツールに配置し、1つの処理ステップで1つの均質なパーツを作成します。」
テスト、配信、およびそれ以降
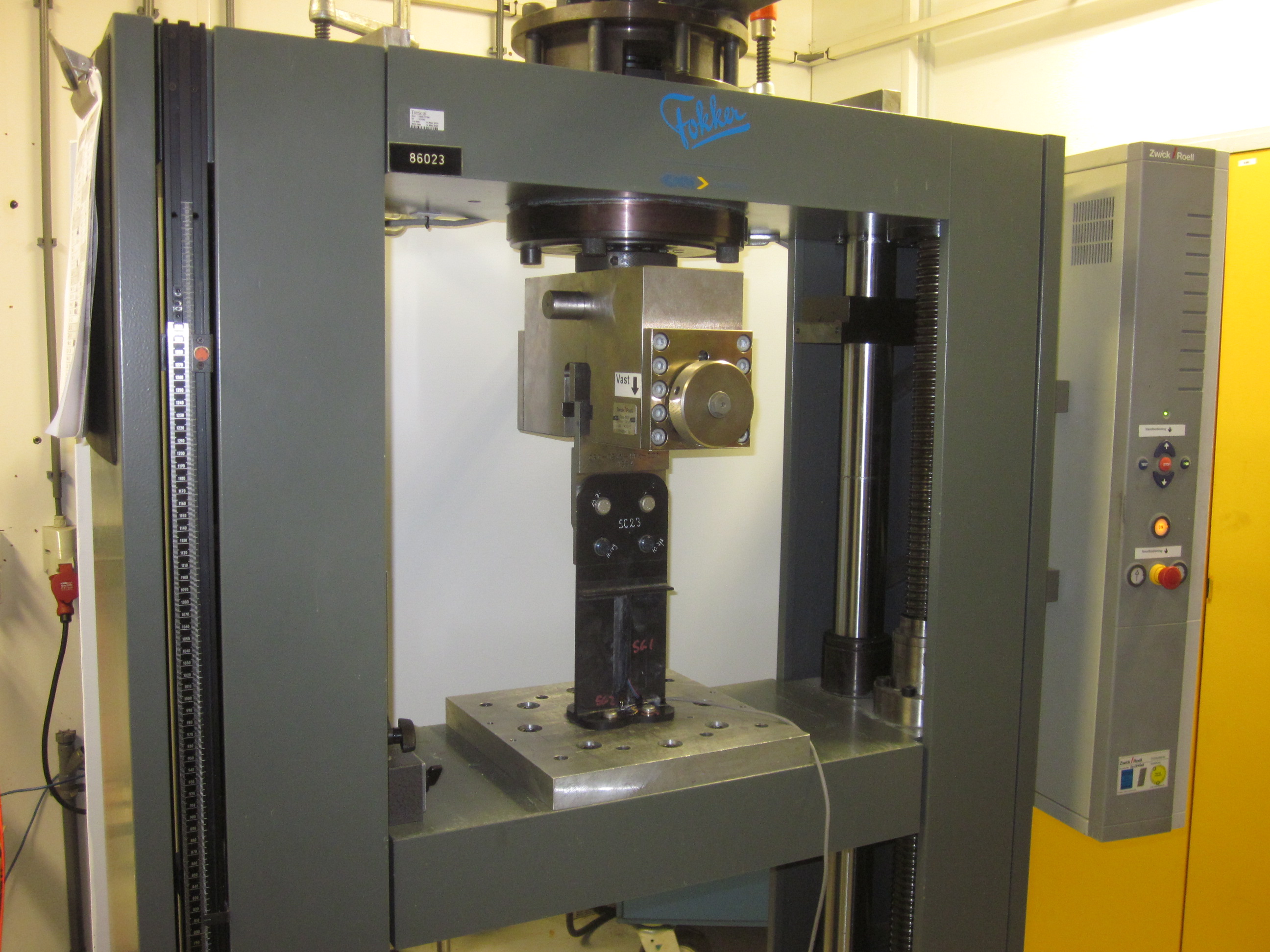
テスト。 サブコンポーネントは、GKNのワイト島とホーヘフェーンの施設で引張および圧縮強度の要件を満たすようにテストされました。
2019年後半に、リブのサブコンポーネントがGKN Aerospaceのワイト島とホーヘフェーンの施設でテストされました。Offringaは、引張荷重と圧縮荷重の要件を「大幅に」合格したと述べています。 「それは強く、タフで、製造が簡単です。これは、私たちが望んでいたとおりに実現したコンセプトです。」アルミニウムバージョンと比較して、Offringaは、熱可塑性複合バージョンは大幅な軽量化を提供し、コスト競争力があると述べています。
同社はエアバスに3つのリブを納入し、そのうちの1つはWOTデモンストレーターで組み立てられテストされます。 GKN Aerospaceは、Wing of Tomorrowとそれ以降の両方で、商用航空宇宙リブのプロセスと材料の最適化に引き続き取り組んでいます。
樹脂
- 完全に天然資源から作られた連続繊維強化熱可塑性複合材料
- ソルベイが熱可塑性複合材料の容量を拡大
- フラウンホーファーは、熱可塑性複合材料の研究開発のために自動化されたエンゲル製造セルを委託しています
- DLR Institute of Structures and Designは、熱可塑性複合材の胴体構造の成熟度を高めます
- Solvayはサウスカロライナの施設の設置を完了し、米国の熱可塑性複合材料の容量を増やします
- 熱可塑性テープは、複合エアロストラクチャーの可能性を示し続けています
- StyLight熱可塑性複合材料の生産拠点を構築するINEOSStyrolution
- XeniaがCF / PP熱可塑性複合コンパウンドを発表
- 深海で上昇中の熱可塑性複合パイプ
- NIARsNCAMP認定TenCate熱可塑性複合材料
- TenCateは、ブラジルでの熱可塑性複合コンソーシアムの組み立てを祝います