リフトゲート設計により、修正されたフィラメント巻線がテストされます
自動車のリフトゲート、またはリアハッチドアは、何十年もの間、金属から複合材料へとゆっくりと移行してきました。金属製のサポート構造を除いた最初のオールプラスチック/コンポジットリフトゲートが商品化されたのは2013年まででしたが、今日のほとんどのリフトゲートは、特に大きくて重いスポーツで、アウタースキンとインナーパネルが取り付けられたこのサポートコンポーネントを備えています-後部ドアが大きいユーティリティビークル(SUV)とクロスオーバーユーティリティビークル(CUV)。
ただし、2019年にトヨタスープラでデビューした複合リフトゲートの次の進化は何でしょうか。 豊田自動車(豊田市)のスポーツカー。フィラメントワインド複合フレームは金属フレームに取って代わり、従来の金属構造よりも軽量で高い剛性と強度を提供し、特に狭い梱包スペースで設計の柔軟性が高いと言われています。伝えられるところによると、フィラメントワインディングプロセスは、関心が高まり、アプリケーションが急増するにつれて、大量生産の速度とコストの目標を達成できるように変更されました。このようにして、デザインとテクノロジーが生まれました。
三国間製造
Magna International Inc.(カナダ、オンタリオ州オーロラ)は、北米ではTier 1インテグレーターですが、ヨーロッパでは、Magna Steyr AG&Co。KG(オーストリア、グラーツ)の子会社も、追加の製造が必要なOEM向けに完全な自動車を設計および組み立てています。容量。
最近、マグナは、2013年から設計と製造プロジェクトに協力して取り組んできた自動車メーカーのトヨタとBMW AG(ドイツ、ミュンヘン)が関与する興味深いプログラムに参加しました。トヨタは、最新の取り組みとして、上記> ネームプレートであり、BMWと提携して、車両と姉妹車であるBMWの2シーター Z4 の設計とチューニングを提供していました。 。 2台の車両はエンジン、サスペンション、ステアリングシステムを共有しています。マグナシュタイアはグラーツで両方の車を組み立てるだけでなく、スープラ シート、ボディパネル、ドアラッチ、リフトゲート付き。両方の車には多くの革新がありますが、スープラに組み込まれたリフトゲート 複合材料の設計革新が最も明白な場所です。
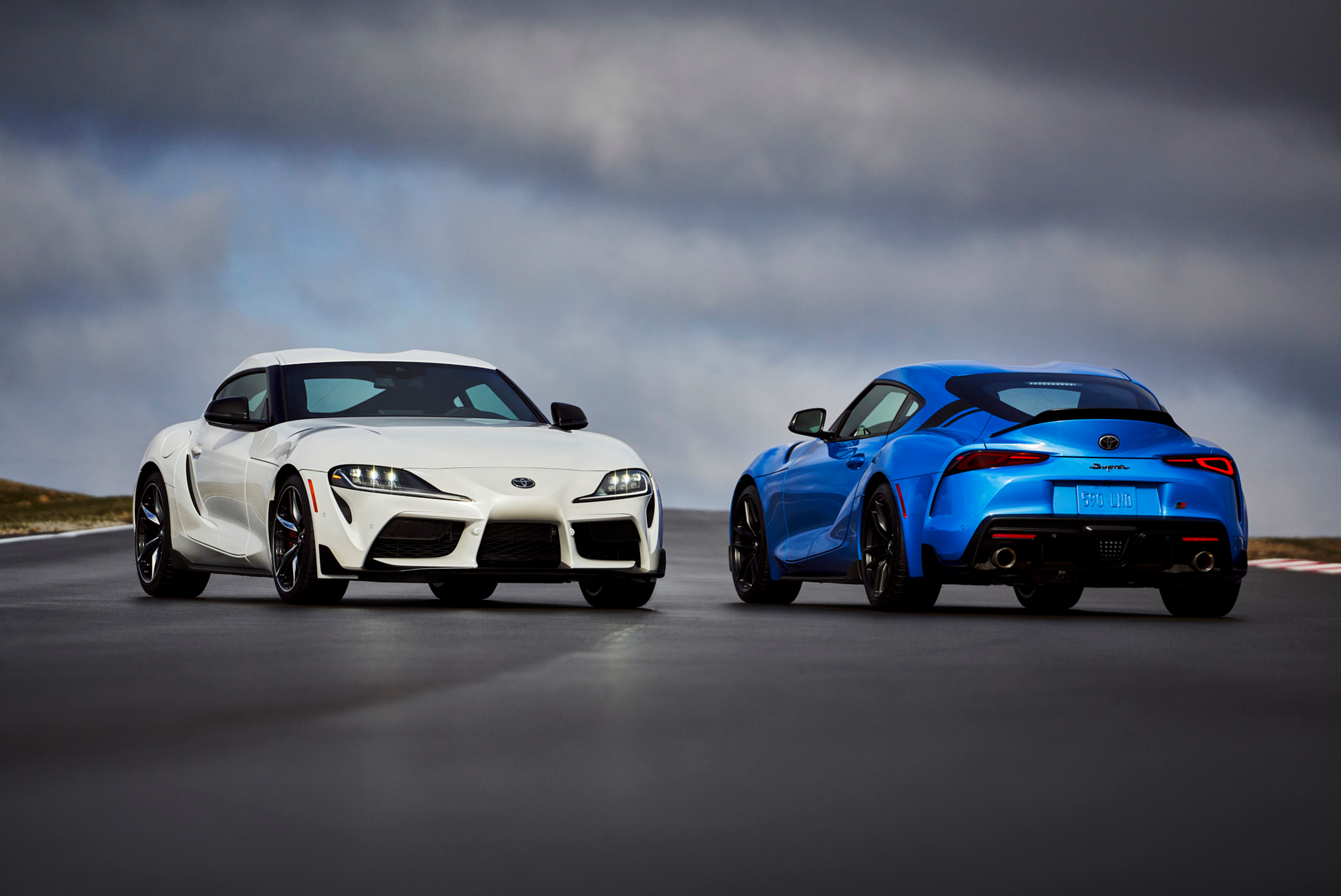
ボヘミアのマンチェスター
マグナが2020年に関与する数年前 モデルイヤースープラ、 チェコ共和国のリベレツでの事業は、多くの潜在的なアプリケーションのための複合スペースフレームの技術を模索してきました。運が良ければ、この地域は主要な織物の中心地としての豊かな伝統があり、かつては「ボヘミアのマンチェスター」として知られていました。リベレツのチームは、高負荷をサポートし、全体の質量を減らし、厳しい寸法公差を維持し、ヨーロッパの自動車メーカーのパフォーマンスと製造の要求を満たすために、高い再現性と再現性(R&R)のプロセスで製造できるテクノロジーアーキテクチャを求めました。
「熱安定性と寸法安定性の高い熱硬化性製品が必要であると結論付けました」と、Magnaのグローバル製品ラインディレクターである複合リフトゲートのRiadChaaya氏は振り返ります。 「また、機械的性能、パッケージスペース、質量、コストを最適化するために必要な、さまざまな形状と厚さの断面を生成できる閉じた形状が必要であることもわかっていました。これは、年間15万個の部品を製造できるプロセスで製造できます。ブロー成形、編組、フィラメントワインディングなど多くの技術を検討しましたが、どれも私たちのニーズを完全には満たしていませんでした。何度も試行を重ねた結果、フィラメントの向きと数を制御して最小の重量で最大の弾性率を引き出すことができたため、フィラメントワインディングを必要なものに最適なものとして選択しました。」
多くの利点にもかかわらず、フィラメントの巻き付けは従来の自動車生産には遅すぎるかもしれないという懸念がありました。さらに、チームは、閉じた形状のフレームを作成するために、巻き取りプロセスを開始および終了する方法を必要としていました。幸い、チームにはフィラメントワインディングの歴史はありませんでしたが、リベレツの繊維製造の遺産は、地元のコミュニティがロービングとフィラメントのワインディングの専門家でいっぱいだったことを意味しました。
「私たちにとって幸運なことに、これらの専門家は、大量の自動車のニーズを満たすために新しい方法でそれを適用するのに役立つ従来のノウハウを復活させることに情熱を持っていました」とDr.-Ingは付け加えます。 JosefPůta、MagnaExteriorsテクノロジーリーダー-チェコ共和国。
「従来のフィラメントワインディングは私たちのニーズには遅すぎたため、私たちとパートナーはそれをより速く実行するための多くの方法を検討しました」と、マグナリベレツの工業化責任者であるLukášStrouhalは回想します。 「私たちは、プロセスの各ステップをスピードアップする方法と、まったく異なる方法で物事を行う方法を検討しました。 どのようにについてはあまり言えませんが そうすることで、速度が大幅に向上し、変更されたプロセスが「自動車にふさわしい」ものになる可能性があると言えます。」
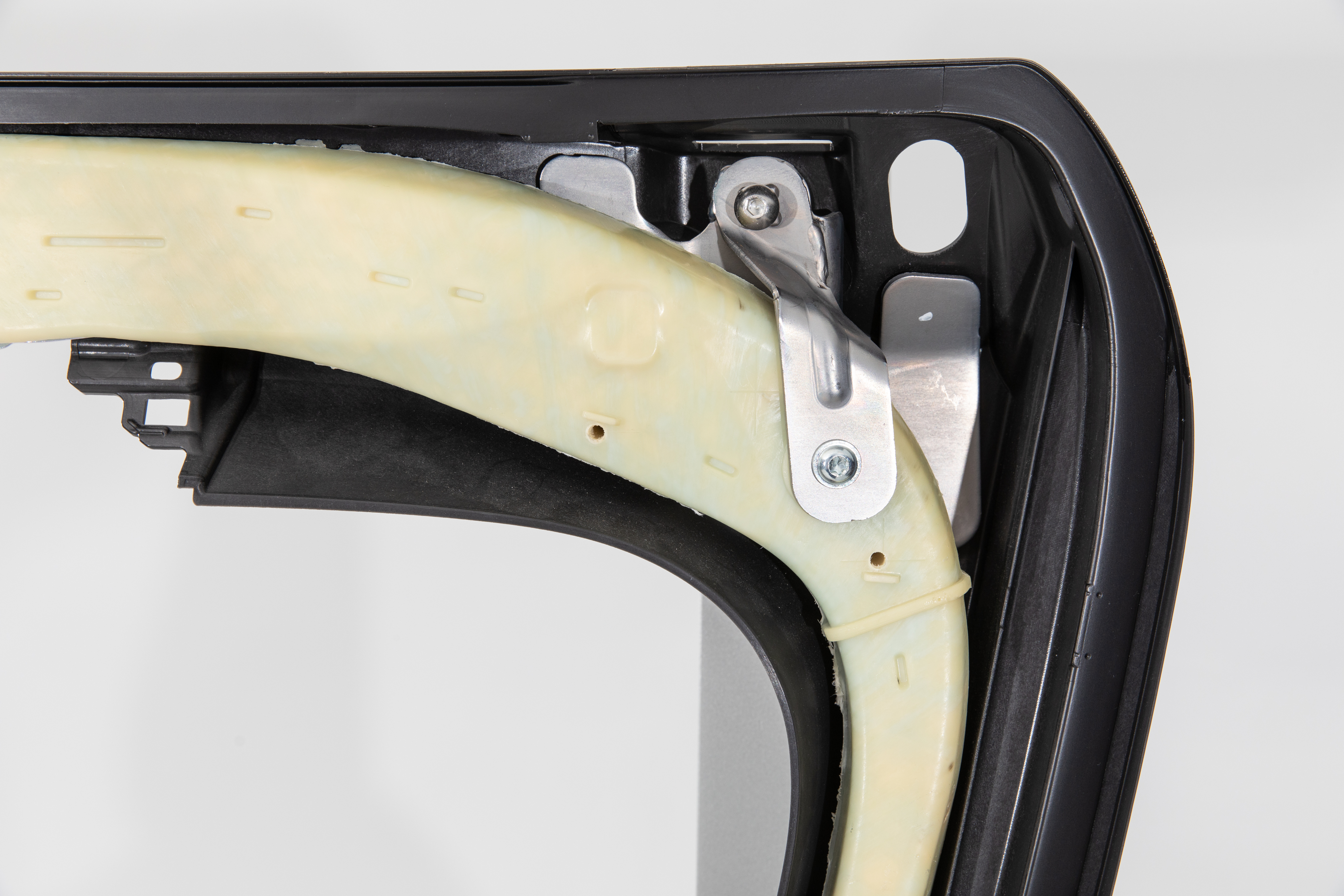
Magnaとそのパートナーは、エポキシ、ポリウレタン(PUR)、PUR /ビニルエステルブレンドに加えて、ガラスからカーボン、玄武岩繊維までのさまざまな補強材を含む多くの樹脂システムを調査しました。最終的なシステムは、PURとガラス繊維を特徴としており、繊維効率、性能、コスト、生産速度の最高のバランスを提供します。
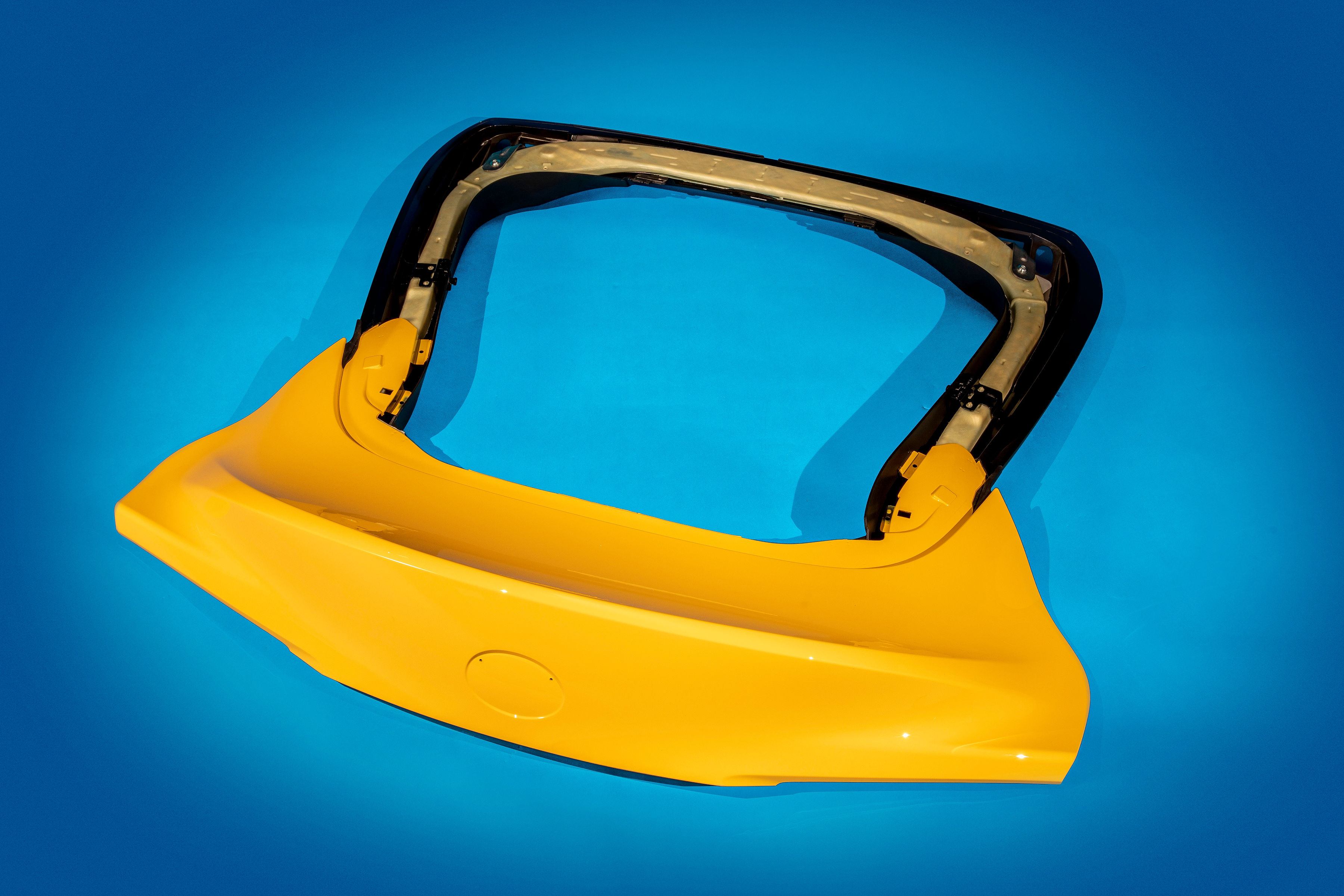
マグナの一般的なフィラメントワインドスペースフレームは3つのステップで製造され、それぞれが速度に合わせて慎重に最適化されています。まず、リジッドなセルラーPURコアが反応射出成形(RIM)によって製造されます。第二に、マンドレルとして機能するそのコアは、ガラス繊維で巻かれています。そして第三に、その創傷構造にPURが注入され、高圧樹脂トランスファー成形(HP-RTM)プロセスで統合されます。注入/圧密中にコアが崩壊しないように注意が払われています。 Půtaは、使用するロービング、サイジング、樹脂の種類を特定し、材料の変更についてサプライヤーと緊密に協力する必要があり、各層の巻線数とフィラメントの方向を決定するために多くの作業が行われたと説明しています。当然のことながら、同社は、設計やコア製造からフィラメントワインディングマシンに至るまで、さらにはそれらが保持する追加の企業秘密に至るまで、すべてをカバーする多数の特許を取得しています。
「私たちは各プロセスステップと製品で複数の革新を行いました」とStrouhalは説明します。 「フレームの1つを引き裂いて、使用されている形状と形状を確認することができますが、それでも、なぜ、どのようにそれを行ったのか疑問に思うでしょう。」
Magna Liberecチームは、特定のアプリケーション向けのスペースフレーム技術を開発していませんでしたが、それを使用する興味深い機会を得ようとしていました。
挑戦的なリフトゲート
マグナは乗用車用リフトゲートを製造してきた長い歴史があります。伝えられるところによると、同社は2013 BMW i3 向けに、北米とヨーロッパで最初のオールオレフィンリフトゲートを製造しました。 電気都市車であり、FCA NA LLC(米国ミシガン州オーバーンヒルズ)の2019ジープチェロキー用の次世代オールオレフィンリフトゲートを設計および製造しました SUV。リフトゲートの生産がスープラの成果物であったことを考えると プログラムでは、マグナはリベレツで行われた作業だけでなく、金属製のリフトゲート構造を複合材やプラスチックに変換してきた長い歴史も利用しました。
「スープラ リフトゲートは多くの差し迫った課題を提示しました」とChaayaは回想します。 「まず、パッケージスペースが非常に限られていました。つまり、許容誤差が非常に厳しく、リフトゲートが自由に開閉できるように線形熱膨張係数の値を注意深く管理する必要があります。第二に、このドアの形状はさらに困難でした。トヨタはより軽いリフトゲートを望んでいただけでなく、車両の後部がどのようにドレープするかについて非常に特定のスタイリング要件を持っていました。第三に、車両の予測されるビルドボリュームでは、金属でその形状を実現するためのツールは非常にコストがかかります。実際、リフトゲートフレームは単一の金属片で製造することはできず、トヨタの設計と性能の要件を満たしていると結論付けました。つまり、スペースフレームは複合材料、より具体的には熱硬化性複合材料で作成する必要がありました。」
外皮は塗装された射出成形されたタルク強化TPOパネルで、攻撃的な形状を処理します。内側のパネルは長ガラスポリプロピレン(PP)です。両方とも、構造用2KPUR接着剤でフレームに接合されます。 Chaayaは、スペースフレームを最適化し、ねじり荷重の要件を満たすためにリフトゲートを完成させるために多くの作業が行われたと付け加えています。初期の課題は、材料特性を正確にシミュレートして、予測結果と測定結果の正確な相関関係を実現する方法を見つけることでした。
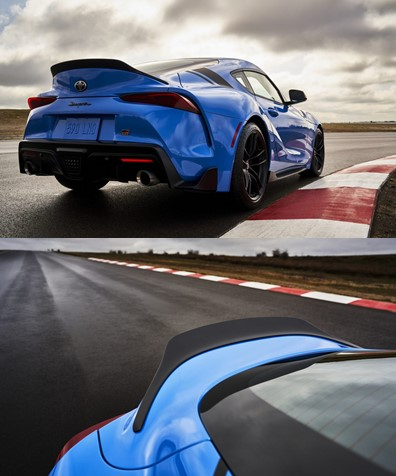
「巻線の各層をシミュレートし、形状、半径、および巻線の要件自体を組み込む必要があったため、材料モデルとの良好な相関関係を得るのは困難な戦いでした」と彼は付け加えます。 「最初は20%オフでしたが、多くの調整と剛性を改善するための最良の方法を決定した後、最終的な予測は非常に近くなりました。このような大きなフレームでは、寸法公差を1mmに抑えることもできました。」
多くのメリット
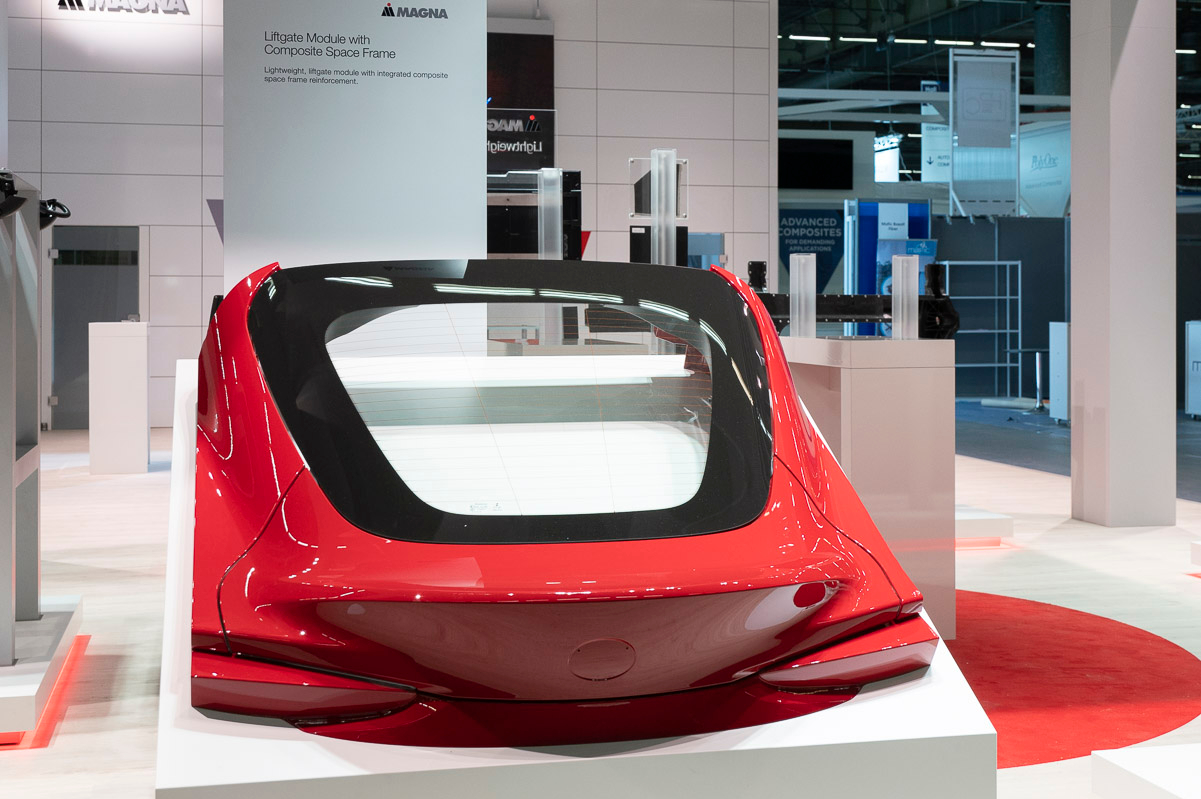
最終的なドーナツ型のフレームは、全体を通してさまざまな直径と壁の厚さを備えていますが、公称直径は50〜60ミリメートルです。隅にある小さなブラケット、ラッチやヒンジなどのハードアタッチメント、および一体型アンテナを接地するためのフォイルを除いて、フレーム全体(104 x 111センチメートル)は完全に複合されています。インナートリムパネルをリフトゲートの下半分に接続するために使用される「イヤー」ブラケットでさえ、複合されており、HP-RTMを介して製造されています。複合フレームは同等の金属フレームよりも10%軽量ですが、質量分解効果により、リフトゲート全体が金属リフトゲートよりも約20〜25%軽量になります。リフトゲートが軽いほど、消費者が開閉する労力が少なくて済み、作業者が車両の組み立て中に設置しやすくなり、車両の使用期間中に燃料を節約し、リフトゲートが閉じたときにストローハルが「驚くべき堅実な音」と表現するものを提供します。複合システムはまた、金属製のリフトゲートに必要なヘミングエッジや溶接ポイント/ジョイントなどの手順を排除しました。
Chaayaは、彼の会社が別の主要なフィラメントワインド自動車プロジェクトを進行中であることをほのめかしています。彼はまた、マグナはリフトゲートを超えた技術の他の用途を見ていると言います。 「ドア、デッキリッド、フード、FEM(フロントエンドモジュール)、さらには自動運転車—ガラスで包まれたフレームで構成されたバスのように — そのようなスペースフレームを使用することができます」と彼は付け加えます。 「そして、それを隠す必要すらありません。カーボンファイバー織りを使用した場合、その美しい表面を露出させたままにし、フレームを内側に隠さないことは名声の表れです。」
樹脂