熱可塑性複合構造が、セーフティクリティカルなブレーキペダルの金属に取って代わります
自動車産業は、1990年代にアクセルペダルを金属から射出成形された短ガラス熱可塑性プラスチックに変換しました。ただし、ブレーキペダルは、剛性、強度、ねじり荷重の要件が厳しい、セーフティクリティカルなコンポーネントであるため、変換にはるかに長い時間がかかりました。 Tier1自動車サプライヤーのBogeRubber&Plastics Group(ドイツ、ダンメ)は、熱可塑性複合材料のブレーキペダルの厳しいOEMパフォーマンスとコスト目標を達成した最初のサプライヤーであると述べています。独自のデザイン、3つの異なる素材、特注の製造プロセスにより、同社はより強く、より硬く、より軽量で、より低コストのペダルを製造することができます。
重要なニッチを見つける
Bogeは、自動車産業向けの振動減衰およびパワートレイン/シャーシ取り付け用の製品、ならびに軽量プラスチックモジュールおよびペダルボックス(ブレーキ、クラッチ、およびアクセルペダルの組み合わせを含む)の開発および製造を行っています。 2008年以来、短ガラスオーバーモールディングコンパウンドを使用した連続繊維有機シートで自動車部品を製造しています。2018年に一方向(UD)熱可塑性テープを混合に追加しました。継続的なプロセス革新により、サイクル時間とコストが削減され、ビジネスが増加しました。
「2015年に上司が私のところに来て、「ダニエル、あなたが行ったこれらの変更は素晴らしいですが、本当に重要な生産量のあるより大きな市場を見つけることができればいいのですが」とDr.-Ingは回想します。 。ダニエル・ヘッフェリン、ボージグローバルイノベーションセンターのシニアマネージャー/軽量チームの責任者。 Bogeのエンジニアのチームがこの課題を受け入れ、ファイバーの効率を高めてコストを削減し、より多くのビジネスを獲得する方法についてブレインストーミングを行いました。
「Organosheetは素晴らしい製品ですが、必要な場合にのみ、正しい方法で使用する必要があります」とHäffelin氏は説明します。 「私たちはすでに生産プロセスを非常にスリムにしているので、サイクルタイムをさらに短縮しようとしてもあまり利益は得られません。コストを削減する最善の方法は、そのファイバーをより効率的に使用することで、使用するエンドレスファイバーの量を減らすことであると考えました。」
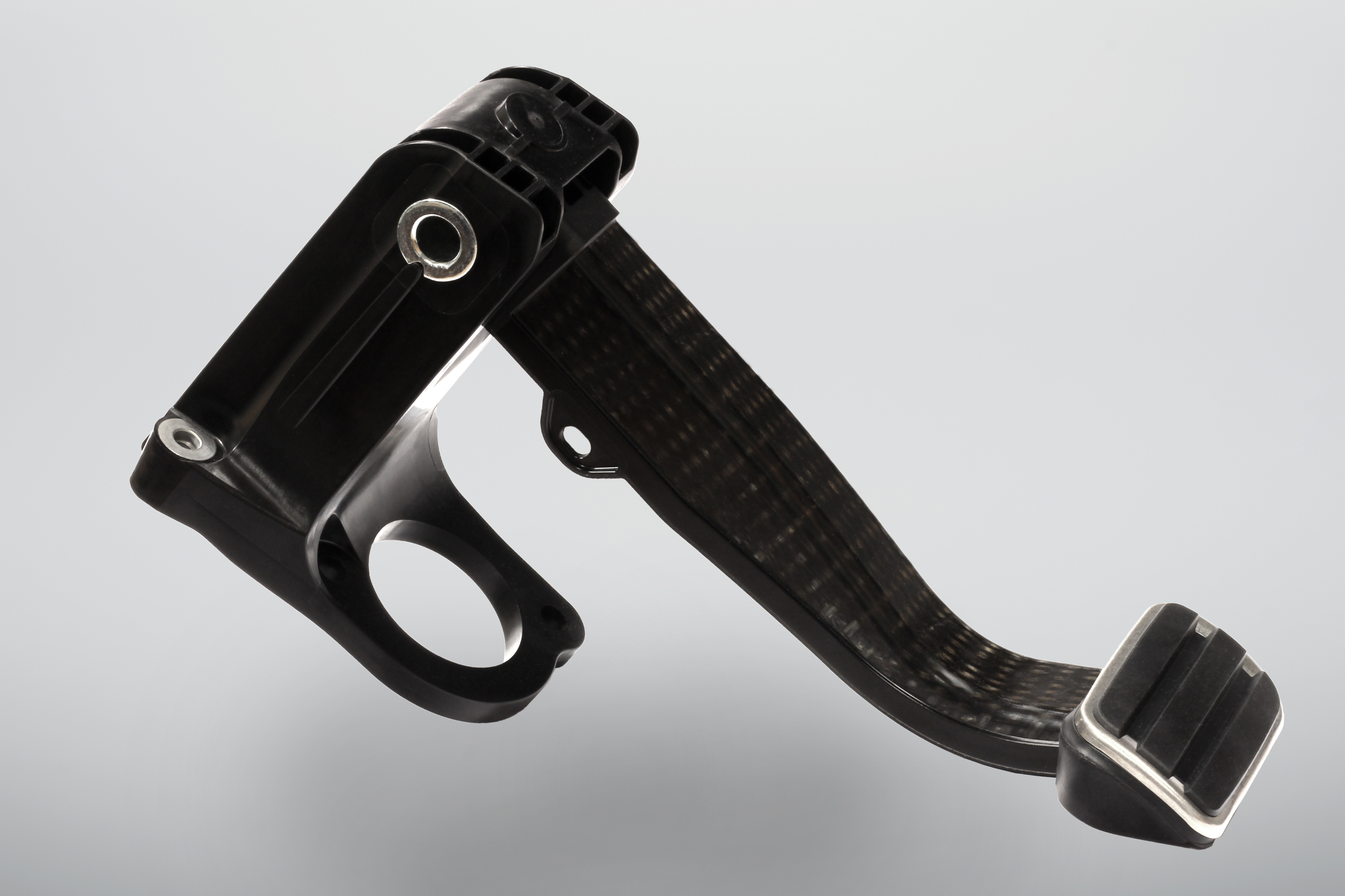
安全性が重要な性質のため、ブレーキペダルのサイズと形状には実際的な制約があるため、ペダルを小さくしたり薄くしたりするだけでは機能しません。最も理にかなっているのは、繊維配向をより適切に制御して、ピーク荷重が最も高い部品の領域の局所特性を最適化し、重要度の低い領域の肉厚を減らす機会を提供する方法を見つけることでした。
「私たちは、剛性と強度を維持するために必要な場所に繊維を配置できるように、繊維を局所的に「操舵」する方法を模索しました」と、Boge Rubber&PlasticsGroupの最高経営責任者であるDr.TorstenBremerは付け加えます。 「私たちは、スポーツ用品や医療で使用されるピックアンドプレースマシンをすでに検討していたため、原則としてこれが可能であることを知っていましたが、それらは高すぎました。そのとき、新しいプロセスが必要だと判断しました。」
「私たちはすでにドイツのOEMと協力して、性能とコストの要件を満たす全複合ブレーキペダルを製造する方法を模索していました」と、Boge Plastics&RubberGroupのエグゼクティブバイスプレジデント兼製品ラインリーダーであるPlasticsのBurkhardTiemannは振り返ります。 「UDテープとオルガノシートを使って新しいプロセスを開発する」とお客様に言いました。「さらに質量とコストを削減できれば、それを実行します。」それが私たちの出発点でした。 2015年には、より安く、より軽く、大量生産が可能なオールコンポジットブレーキペダルを提供できることを大いに約束しました。詳細を検討して最初の製品を納品するのに3年かかりました。」
ファイバーステアリング
複合ブレーキペダルは、既存の鋼またはアルミニウムのペダルと同じ性能仕様を満たす必要があります。これには、3,000ニュートンもの高荷重と最大荷重での鋼のようなたわみを伴う特別な故障モード要件が含まれます。これらの要件と利用可能な限られたパッケージスペースを考えると、最大の負荷を運ぶペダルのメインシェル構造には、継続的な繊維強化が必要です。したがって、チームはペダルバックボーンを形成するためにオルガノシートを使用することにしました。次に、UDテープを使用して、剛性/強度を局所的に高め、成形品の領域でピーク応力が発生したときに内壁を補強します。その後、成形前にUチャネルに曲げられます。また、リブなどの機能的な形状が必要な領域では、チョップドガラスのオーバーモールディングコンパウンドが指定されました。チームは、このハイブリッドアプローチにより、材料の使用量、平均壁厚、およびサイクルタイムを削減しながら、ファイバー効率が向上すると考えました。

チームは、生産中にファイバーの位置を最適化するための集中的なシミュレーション作業を開始しました。 Bogeの研究の基盤は、2011年から2014年にかけて公的資金で運営されたSoWeMa(全自動および閉鎖型軽量製造チェーン向けのソフトウェア、ツール、および機械開発)と呼ばれるドイツの研究プログラムに基づいていました。
「SoWeMaの調査では、1年後に自社のベンチャーについて尋ねる質問の多くが取り上げられました」とHäffelin氏は説明します。 「設計はBogeのコアノウハウの一部であるため、SoWeMaプログラムの基礎から始めて、異方性レイアップ構造用の独自のFE(有限要素)シミュレーション機能を構築しました。」
焦点の1つの領域は、テープレイアップとリブ構造のトポロジー最適化の組み合わせでした。 「テープの配置を最適化し、それに応じてリブ構造を適応させるために反復サイクルを作成しました。これは、両方がパーツの剛性と強度で相互にリンクされているためです」と、CRRCイノベーションセンターのFEAエンジニアであるK.Siebe氏は続けます。 「UDテープ、オルガノシート、短繊維材料の材料の組み合わせは独特であり、それらの用途は湿度と温度の特定のウィンドウにバインドされているため、物理テスト中にこれらの材料がどのように動作するかをより正確に特徴付ける独自の材料カードを作成しました。 」
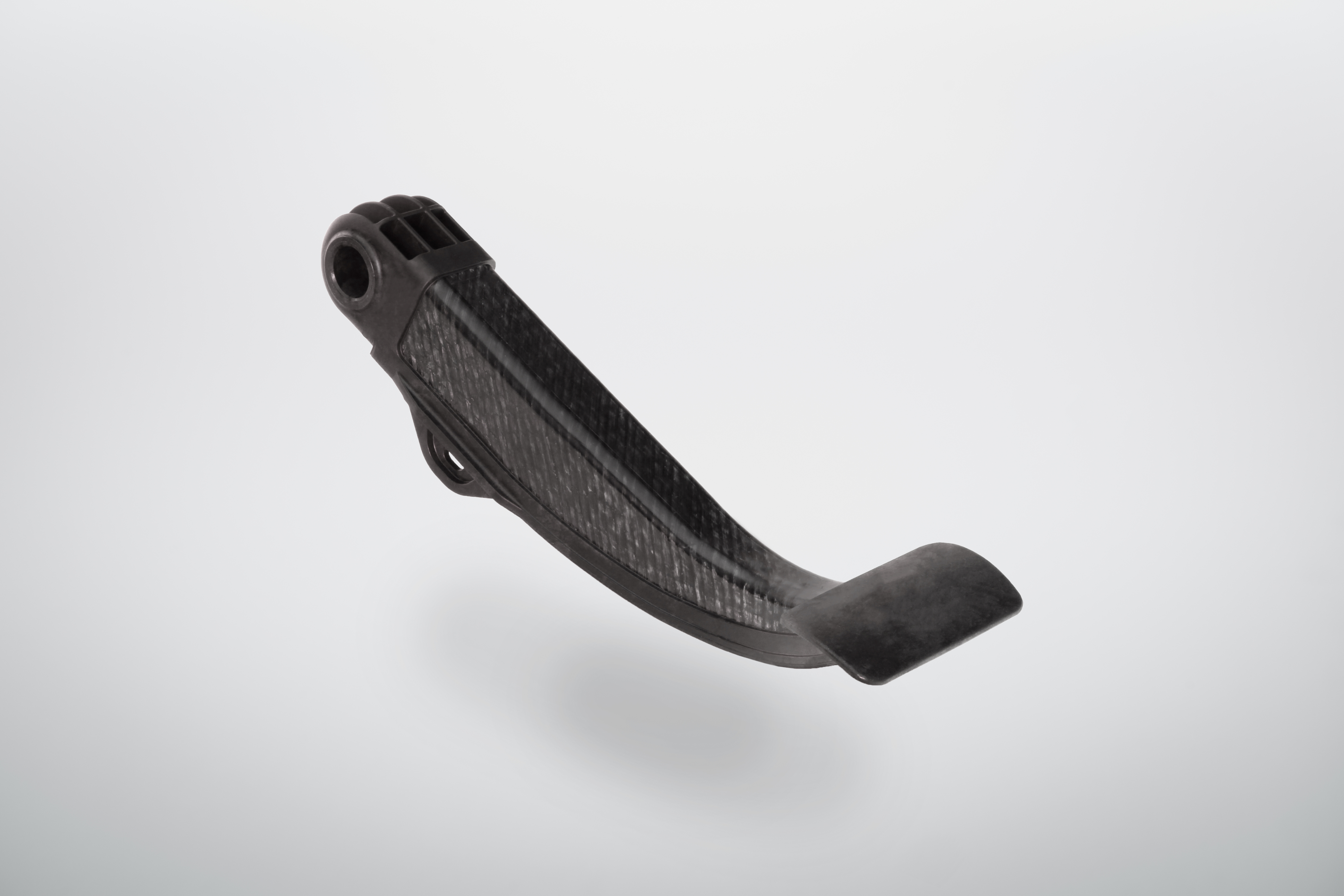
Bogeは、シミュレーション結果と特定のペダル設計に基づいて、各材料の層構造と繊維構造を指定しました。 Lanxess Deutschland GmbH(ケルン、ドイツ)は、45〜50%の繊維体積分率(FVF)で有機シートを供給しています。 FVFが55〜60%のUD熱可塑性テープは、Celanese Corp.(Irving、Texas、U.S。)から提供されました。この用途向けの短ガラス注入コンパウンドは、40〜60%の繊維重量分率(FWF)で、複数の供給元から供給されました。すべての素材は黒で、ポリアミド6または6/6(PA6、PA6 / 6)マトリックスを備えています。顧客の仕様を満たすために、PA6は3つの複合タイプすべてのデフォルトの樹脂です。ただし、製造時の湿度と温度レベル、スペースの制約、ペダルの形状によっては、2つのポリマーが十分に類似しているため、Bogeはオーバーモールド樹脂にPA6 / 6を使用することもできます。
3段階の制作
設計と並行して、チームは3段階の製造プロセスに取り組みました。最初のステップでは、ロードパスに位置合わせされたUDテープのストリップを戦略的にタックしてパーツのシェル構造を強化するための安定したベースとして、事前にカットおよび事前に統合された有機シートを使用して、テーラードファイバーブランクを作成します。 2番目のステップでは、ブランクを移動し、順次加熱、圧密、成形/ドレープします。 3番目のステップでは、短いガラスのコンパウンドでオーバーモールドして、リブ構造を作成します。
速いサイクルタイムを達成するために、このシステムにはロボット処理が与えられました。チームが含めたかった重要なプロセス機能は、任意の長さ、任意の方向、および有機シートシェルの片側の任意の位置にテープを配置し、それらのテープがずれないようにシェルにレーザータックする柔軟性でした。後続のステップで。
チームが下した別の決定は、レイアップの直後ではなく、ドレープ/プリフォームおよびオーバーモールドの直前にテーラードブランクを事前統合することでした。チームは、とにかくドレープ/プリフォーム中に材料を再加熱する必要があり、費用対効果を高めるには、合計サイクル時間を1分近くに保つ必要があると考えました。したがって、Bogeは、ドレープ/プリフォームの直前にブランクを加熱して固め、急速な温度上昇と高圧を組み合わせて、テープと有機シートの間に強力な機械的結合を作成します。まだ高温の圧密ブランクがドレープキャビティに移動すると、加熱が停止し、成形品の温度が下がり始めます。その後、再び移動して、2番目のキャビティのリブやその他の機能機能でオーバーモールドされます。 3つの材料すべての間で、ポリマー鎖の浸透が確認された強力な機械的結合が実現されます。モールド後の仕上げは必要ありません。
これらのセーフティクリティカルな部品の品質要件を満たすために、チームは、製造プロセスの各ステップで材料をチェックするビジョン、力、時間、圧力、および温度センサーを使用する、高速で正確なインダストリー4.0準拠のシステムも開発しました。次に、システムはそのデータを保存し、各ペダルの一意の識別番号に関連付けます。これにより、関連するすべての材料、シフト、およびプロセス設定の100%のトレーサビリティが保証されます。
これまでの成果
Bogeの特注の完全自動化された品質管理プロセスにより、2018年にプロトタイプから大量生産へと移行しました。現在の製造セルは、ほぼ毎分新しいペダルを製造しており、年間最大100万個の部品を製造できます。オールコンポジットペダルは、以前のデザインよりも33%少ない有機シートを使用し、公称壁厚は3ミリメートルから2ミリメートルに減少しました。ペダルも50〜55%軽量ですが、スチールの強度要件を満たすか、それを上回っています。軽いペダルは運転の触覚を改善します 消費者にとって、システム全体は寿命の終わりに100%リサイクル可能です。現在のプロセスでは、複合ペダルはアルミニウムと同等のコストであり、スチールよりもわずかに高いコストです。他の自動車およびスポーツ用の優れたアプリケーションが開発中です。
自動車メーカーが資源をフリート電化にシフトするにつれて、将来はどうなるでしょうか。 「ドライブバイワイヤ[電気機械式作動システム]とパワートレインの電動化が一般的になるにつれて、アクセルペダルはなくなる可能性がありますが、ブレーキペダルは残ります」とHäffelin氏は考えます。 「しかし、ブレーキペダルには、センサーを含む電子機器の統合がさらに進むでしょう。これにより、パーツの複雑さが大幅に増加し、複合材料がさらに 金属よりも競争力があります。」
材料の使用、プロセスステップ、および機器の基準については、 CW で詳しく説明されています。 の2021年1月のフォローアップ記事、「特注プロセスにより、毎分複合ブレーキペダルが製造されます。」
樹脂
- 長繊維強化ナイロン複合材がアルミニウムモーターハウジングに取って代わります
- 完全に天然資源から作られた連続繊維強化熱可塑性複合材料
- ソルベイが熱可塑性複合材料の容量を拡大
- Oribi Composites、オフロードパワースポーツ熱可塑性複合ホイールのパッカードパフォーマンスパートナー
- フラウンホーファーは、熱可塑性複合材料の研究開発のために自動化されたエンゲル製造セルを委託しています
- コンソーシアムは、炭素繊維熱可塑性複合構造のソリューションを対象としています
- StyLight熱可塑性複合材料の生産拠点を構築するINEOSStyrolution
- XeniaがCF / PP熱可塑性複合コンパウンドを発表
- 深海で上昇中の熱可塑性複合パイプ
- NIARsNCAMP認定TenCate熱可塑性複合材料
- TenCateは、ブラジルでの熱可塑性複合コンソーシアムの組み立てを祝います