より民主的な複合材料のための多層熱可塑性テープ、AFPおよび樹脂注入
Novotech(イタリア、ナポリ)は、1992年にLeonardo Lecce教授によって設立された、南イタリアのナポリ大学「Federico II」からのスピンオフとして始まりました。「私たちは一般的な航空会社をサポートし、イタリア全土でR&Dサービスを提供してきました」とLecceは言います。現在NovotechのCEOです。 「航空機部品の構造解析を提供し、航空機の開発も支援しました。」
ボーイング787の複合材胴体セクションを製造するレオナルド工場の近くに位置するNovotechは、2014年に複合材に焦点を当て始めました。CoriolisComposites(Queven、France)から自動繊維配置(AFP)セルを購入し、オートクレーブ( OOA)AFPを使用した現場での統合に関する特別な専門知識を備えた、樹脂注入および熱可塑性複合材料の製造を含む処理。
Novotechは、次のような多くの業界調査プロジェクトに参加しています。
- MESEMA (さらに多くの電気航空機用の磁気弾性エネルギーシステム)
- サリストゥ (スマートインテリジェント航空機構造)
- ASAM (航空機メカニズムの高度なシミュレーション)
- LAMITECH (ハイブリッド複合材料の自動レイヤリングのための革新的なテスト方法)
- PROALATECH (革新的なCFRP尾翼の構造特性評価と修理ソリューション分析)
- 顔 (フレンドリーな航空機キャビン環境)
- エアグリーン2- CLEAN SKY 2(次世代リージョナル航空機向けの革新的な翼の概念と方法論の開発)
- シスターチェック (AFP非破壊検査のための革新的なシステムの調査と統合)
- TRINITI- CLEAN SKY 2(航空機用マルチマテリアル熱可塑性高圧窒素タンク)
- NHYTE- H2020(OOAによって製造された新しいハイブリッド熱可塑性複合材料エアロストラクチャー)
「英国のCytecとも特別な関係があり、新しい複合材料とプロセスを開発しています」とLecce氏は言います。 CytecはSolvayによって買収され、参照されている場所は英国のHeanorにあるSolvay Composite Materialsです。これは、最近RAPMプログラムでテストされた二重ダイアフラム成形プロセスなど、革新の長い歴史を持つサイトです。 「私たちの最後のそのような活動は、PEEK(ポリエーテルエーテルケトン)とPEI(ポリエーテルイミド)を新しい複合材料に組み合わせた新しい革新的なプレスを使用するOOA熱可塑性プロセスの開発でした。」この新しい材料、機器、およびプロセスは、NHYTEプロジェクトによるAFP in-situ統合および溶接を使用して製造された、炭素繊維強化プラスチック(CFRP)航空機ストリンガーで実証されました。
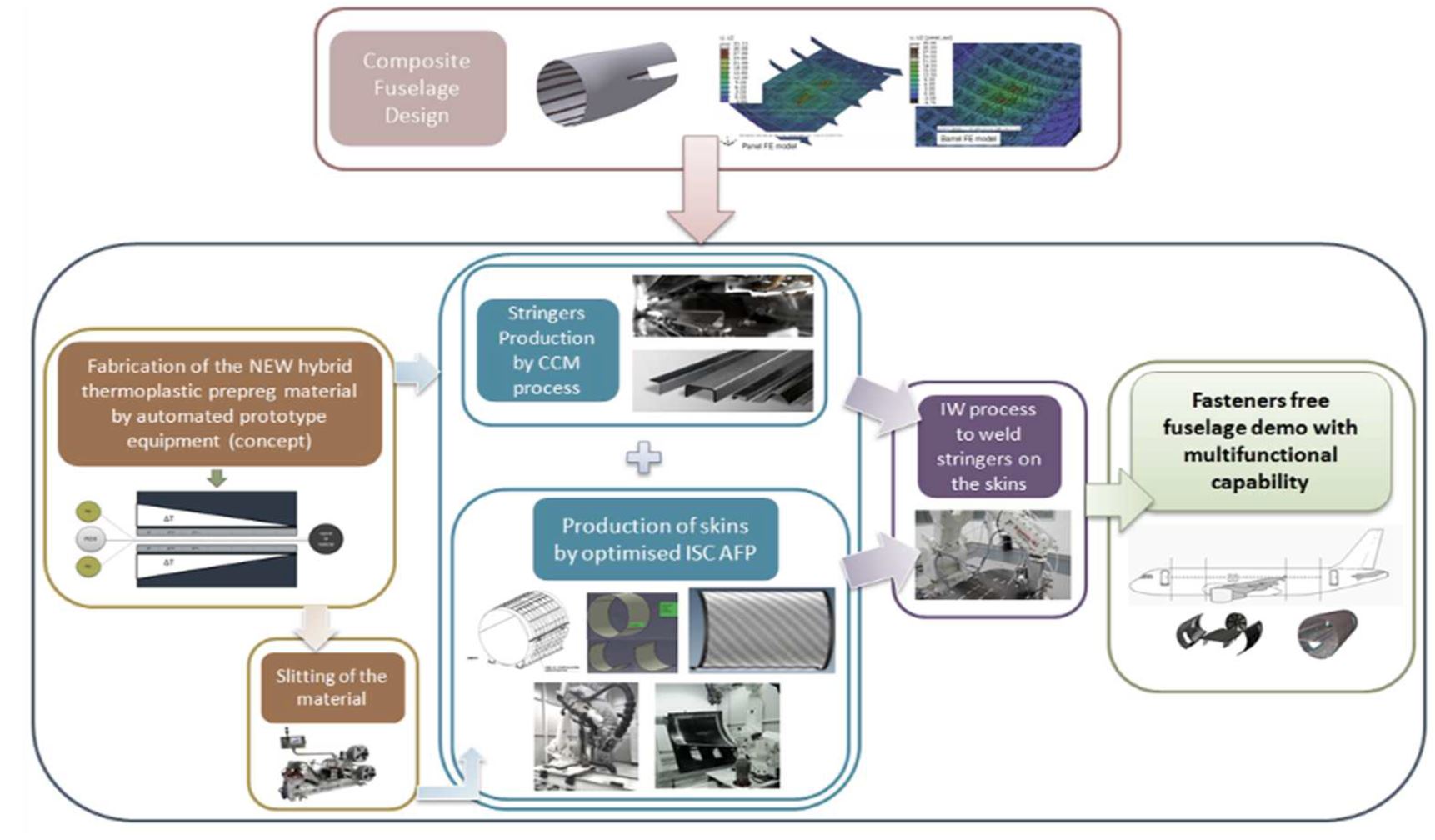
NHYTE
NHYTEは、欧州委員会のHorizon 2020プログラムによって資金提供され、2017年5月から2020年10月まで実施された研究プロジェクトです。ノボテックのCTO。このアモルファスボンディング(下の図を参照)は、別のNHYTEパートナーであるLeonardo(イタリア、ローマ)の航空構造部門が特許を取得したコンセプトであり、南イタリアに複数の生産施設があります。
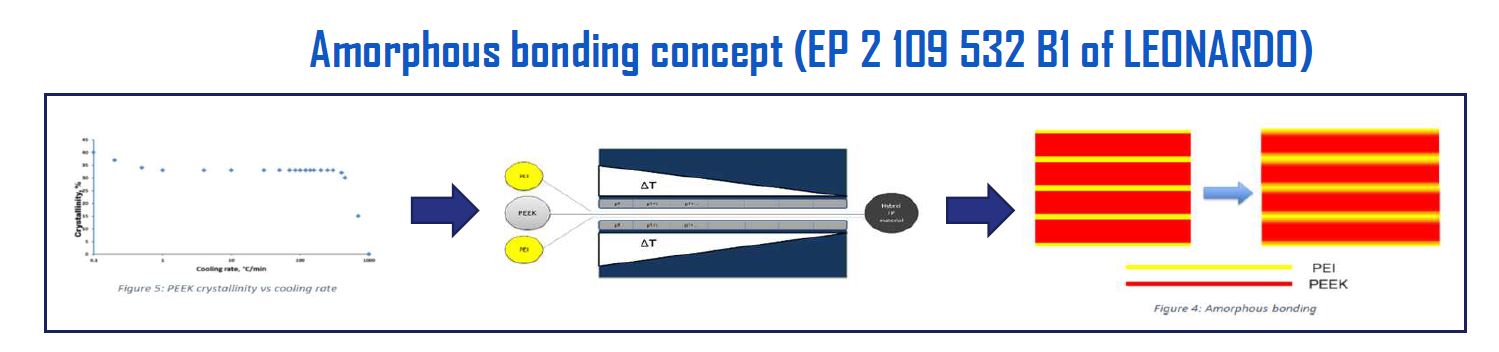
写真提供者:NHYTEプロジェクト
「NHYTEで開発された材料を使用すると、熱可塑性複合材料(TPC)のAFP in-situ統合(ISC)で現在の材料の制限を克服できます。半結晶性PEEKポリマーの場合は400℃未満の温度で処理する代わりに、アモルファスPEI層の場合は215度のガラス転移温度(Tg)のすぐ上で加熱できます。 PEIの溶融と冷却も高速であり、PEEKと比較してそのように制御する必要はありません。」 Barileは、この概念で他のアモルファス熱可塑性プラスチックを使用できると述べています。 PEIが選択されたのは、複数のAFP航空構造デモンストレーターで十分に証明された材料であるPEEKとの結合が良好であるためです。
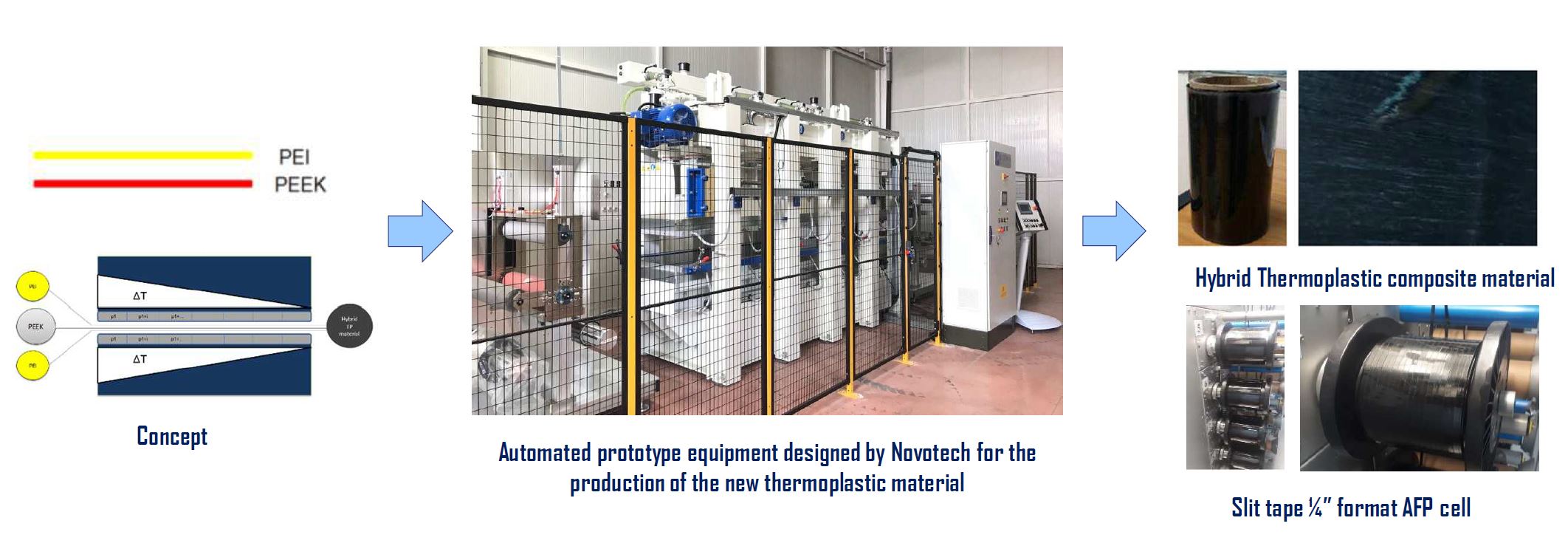
NHYTEで開発されたこの新素材は、NOVOTECHによって設計された連続プレスで製造されました。 Orma Macchine(イタリア、ベルガモ)がプレス本体を供給し、COMEC Innovative(イタリア、キエーティ)が巻き取りおよび巻き戻しモジュールを提供しました。 「このプレスは、AFPマシンで使用するために、スリットテープにスリットを入れた材料の連続ロールを作成できます」とBarile氏は言います。上の画像に見られるように、3つの異なる材料が左からプレスに入ります。 「上部と下部にPEIがあり、中央にPEEKがあります」とBarile氏は説明します。
半結晶性ポリマーとして、PEEKは一次構造に必要な高い機械的特性を提供し、アモルファスPEI層は結合のための高速で簡単な溶融を提供します。 「プレスプレートに沿った材料の圧力と冷却を、プレス開始時の約400℃からプレス終了時の200℃未満まで制御します。その結果、3つの入力レイヤーを組み合わせた1つのマテリアルが作成されます。」
この新しい種類の熱可塑性テープは、製造時にすでに統合されているため、AFP中に加熱するだけで、アモルファス結合用のPEI層を溶融および圧縮できます。その結果、レオナルドの特許に示されているように、完全に統合されたPEEKからPEIへのテープとPEIからPEIへの層を含むラミネートができあがります。このAFPプロセスは、PEEKおよびPEKK(ポリエーテルエーテルケトン)テープを使用する現在のAFPISCよりもハードルが低くなります。その場での圧密に関する2018年の特集のパート2で説明したように、現在のAFP ISCでは、テープと基板を溶融温度まで加熱し、テープを基板上に配置してからローラーで圧密する必要があります。これにより、冷却プロセスが正確に制御され、半結晶性ポリマーは、構造特性に対して十分に高い結晶化度(30〜40%)と低いボイド(<3〜5%)を実現します。
AFP ISCの批評家は、それが遅すぎると主張しています。レイダウン速度は60〜100 mm / sであるのに対し、高速AFPレイアップとそれに続くオーブンまたはオートクレーブでの2次ステップを含む「2ステップ」方式の場合は600〜700 mm / sです。ラミネート内の熱応力を統合/アニーリングします。 「当社の材料を使用すると、通常の現場での圧密ほど遅くないAFPレイダウン速度を達成でき、AFP中に必要な加熱も300℃未満に保つことができます」とBarile氏は言います。 「現在の標準的な材料でパフォーマンスのギャップを埋めることができます。」ここで、Barileは、熱可塑性複合材料のAFP ISCを、ボーイング787およびエアバスA350航空機で使用されている熱硬化性複合材料と比較しています。 「胴体セクションのような大きなコンポーネントでは、オートクレーブ硬化を使用する際の手頃な価格に問題があります。熱可塑性プラスチックは、より手頃な生産プロセスを可能にしますが、現在市場に出回っている航空宇宙グレードの材料では、高温でAFP速度が遅くなります。私たちのアプローチは、これらの問題を解決するのに役立ちます。連続プレスにより、テープの結晶化度は約30%に達します。したがって、パーツにその結晶化度があり、AFP中にのみアモルファス層で動作します。これはまだ実験的な材料であり、改善することができますが、NHYTEプロジェクトの目的は、構造航空宇宙アプリケーションで使用できるワンステップの製造プロセスを持つことです。」
テープとAFPの最適化
「最初の多層テープ材料はここNovotechで作られました」とBarileは言います。これらのテープは、ソルベイのPEIおよびAPC-2 / AS4炭素繊維強化PEEKテープにSabic(Riyadh、Saudi Arabia)Ultem1000アンフィルドスリットフィルムを使用しました。総厚は約0.26ミリメートルで、1または2ミル(.001または.002インチ)の厚さのPEI層で構成されていました。プロジェクトの最初のフェーズでは、ハイブリッド熱可塑性材料の製造プロセスを検証するために、両方のバリエーションの複数のクーポンの層間せん断強度(ILSS)をテストしました。小さなクーポンは、NHYTEパートナーのApplus Laboratories(バルセロナ、スペイン)によって、引張および圧縮強度と弾性率、開穴圧縮(OHC)、充填穴張力、衝撃後の圧縮(CAI)、ほとんど見えないなど、あらゆる機械的特性についてもテストされました。流体調整後の衝撃損傷(BVID)と特性。
「熱可塑性複合テープのサプライヤーと同じ経験はなかったので、材料の品質を向上させることができます。たとえば、繊維の体積は厚さによって低から高に変化し、ILSSを含むテープとラミネートの特性に影響を与えます。しかし、NHYTEは、私たちが行ったコンセプトを実証することを目的としていました。」
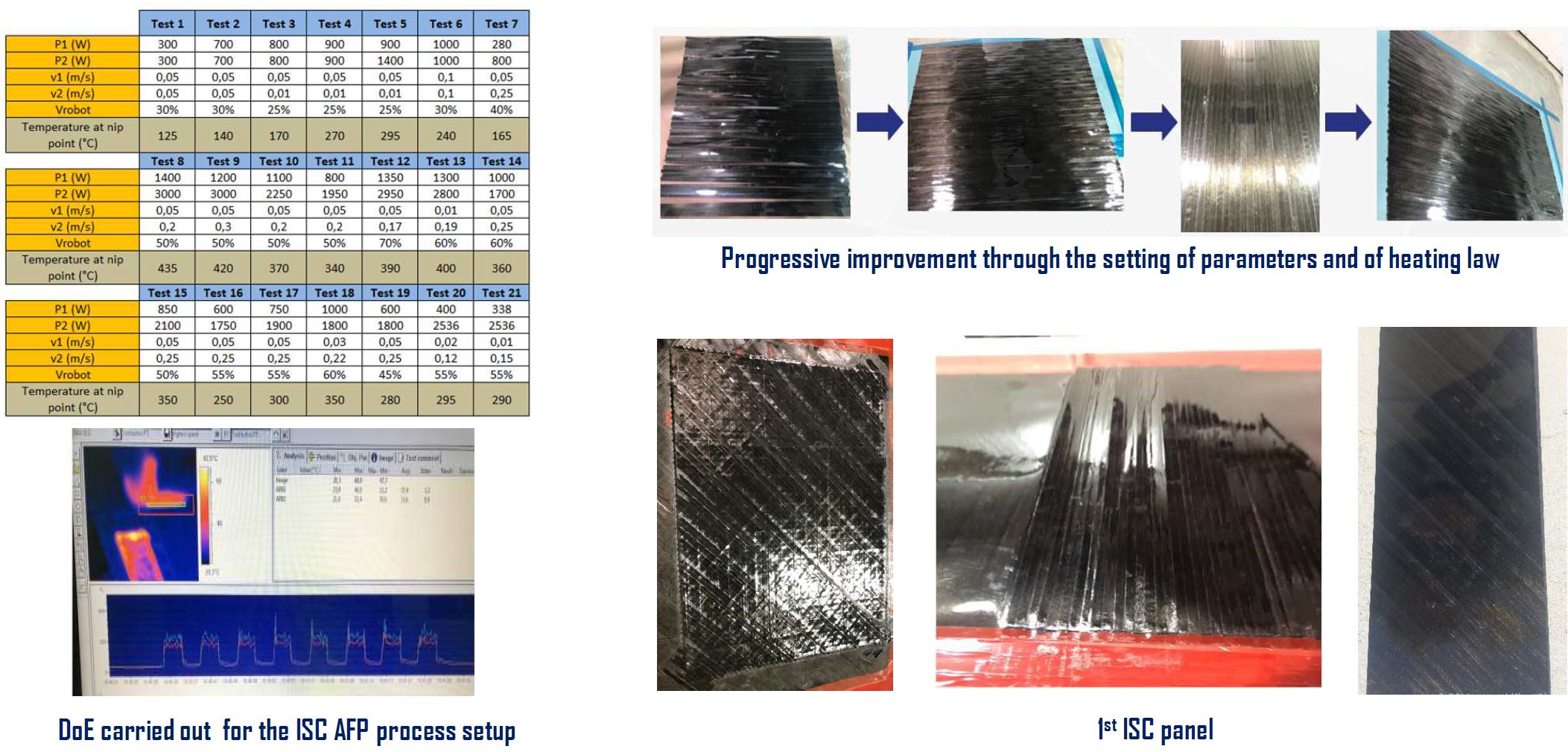
上の画像に見られるように、新しい材料のAFPプロセスを最適化するには、かなりの実験作業が必要でした。 「また、実験計画法(DOE)アプローチを使用してAFPパラメーターを最適化し、NHYTEパートナーのサウスブルターニュ大学(USB、ロリアン、フランス)によってツールが開発され、予測数値シミュレーションによってレーザー加熱負荷が改善されました。」 Barileに注意してください。
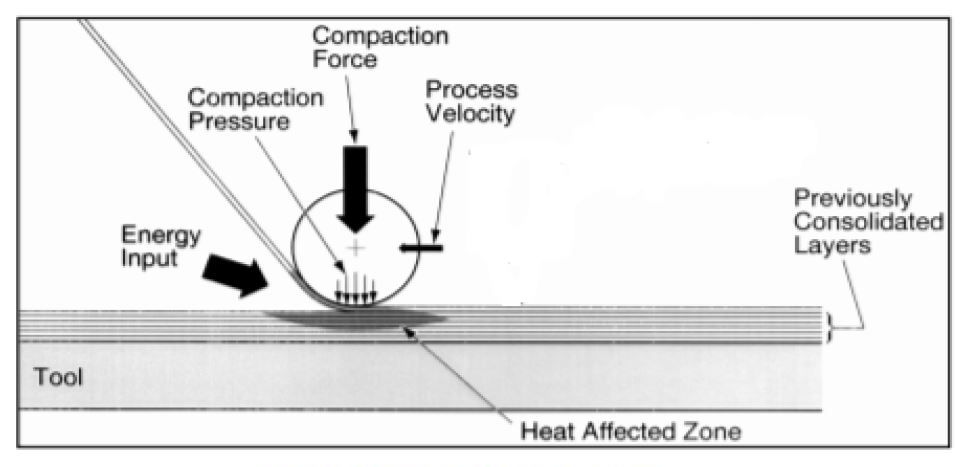
このシミュレーションは、最初にAPC-2テープで予測ツールの品質を検証するために使用され、次に新しい多層材料に適用されました。この研究に関する論文が、ジャーナル Composite Structures に掲載されるように提出されました。 。 「ニップポイントでの熱伝導率をモデル化しています」とBarile氏は言います。 「次に、数値シミュレーションで予測されたものを実験的に検証します。これは、レイダウン速度、ポリマーのメルトフロー、および複合層のエージング[調理]の間の最良の妥協点を決定するために必要です。これは、その場での統合プロセス中のいくつかの変数のバランスです。ツールにすでに配置されているテープへの入ってくるテープの温度の低下を調べます。この温度変化を管理できれば、ラミネートの残留応力を減らすことができます。そこで、レイダウン中の温度変化の評価に取り組みました。パスの形状と薄層の向きに応じて、加熱をカスタマイズする必要があります。
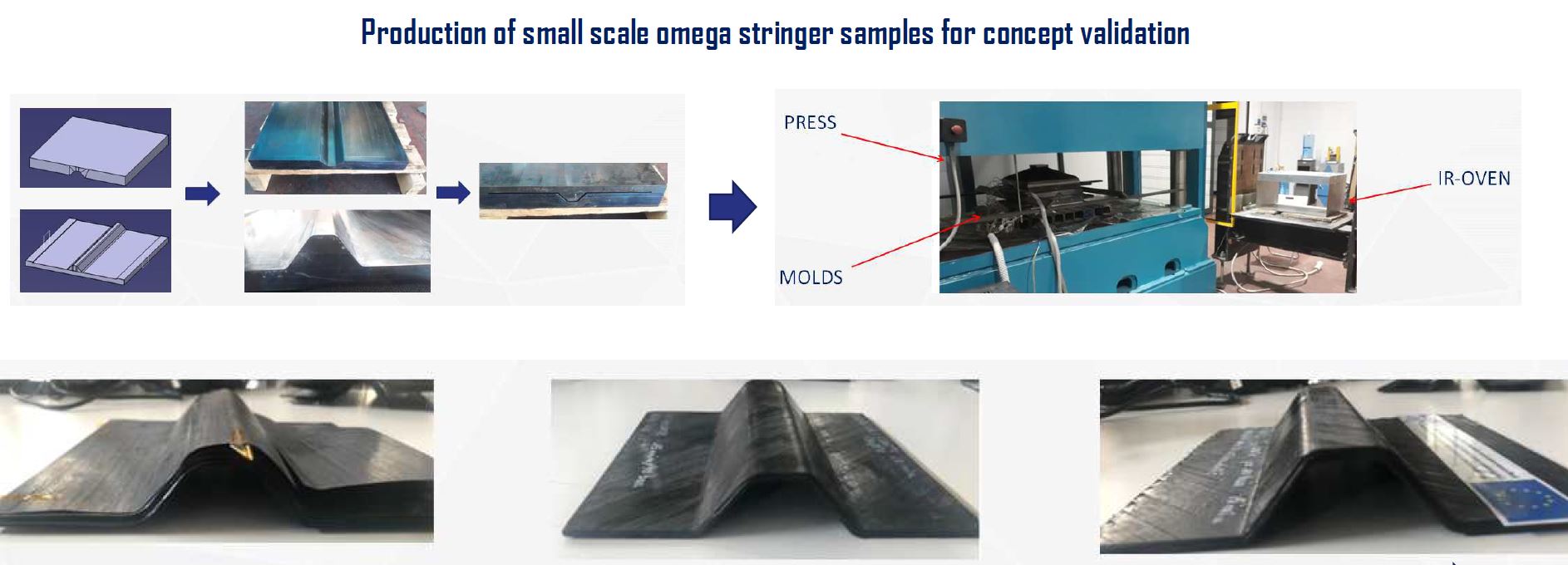
ストリンガーと胴体のデモンストレーター
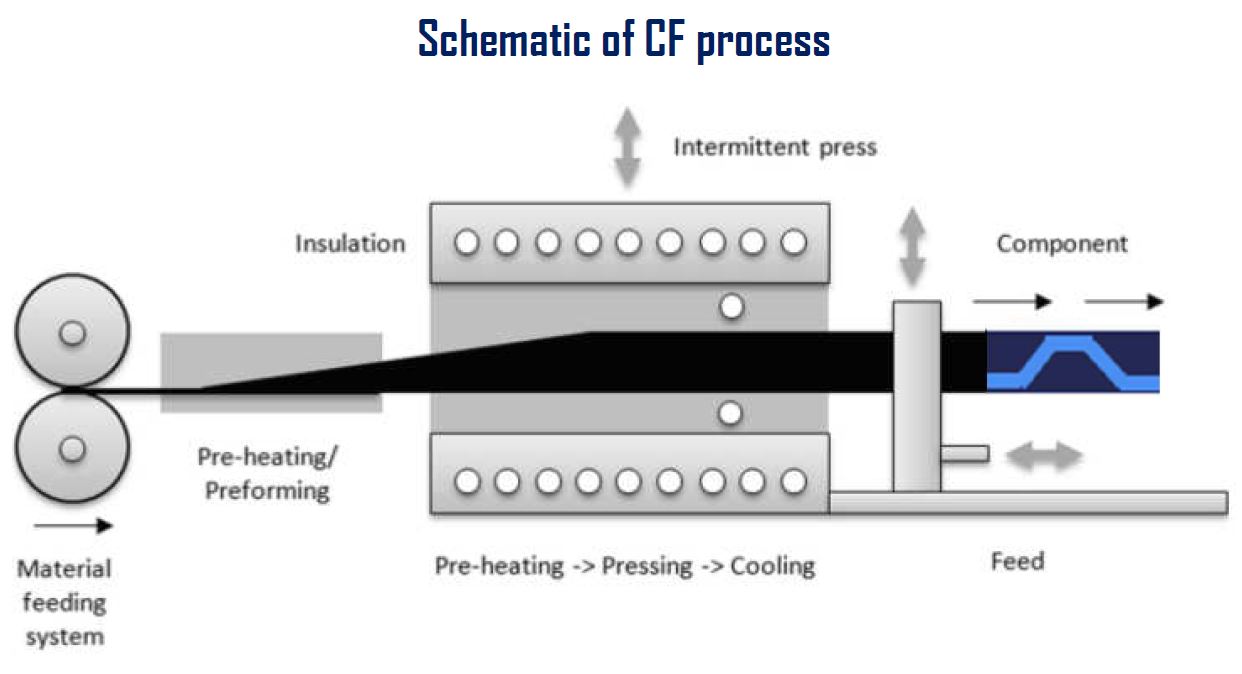
次のステップは、最初に固定プレスで作成された小規模サンプルとして、次に連続ストリンガー成形プロセスのデモンストレーターとしてストリンガーデモンストレーターを製造し、工業部品の製造に何が必要かを検証することでした。次に、これらのストリンガーは、R&D組織CETMA(イタリア、ブリンディジ)によって開発された誘導溶接を使用してAFP胴体スキンパネルデモンストレーターに取り付けられました。
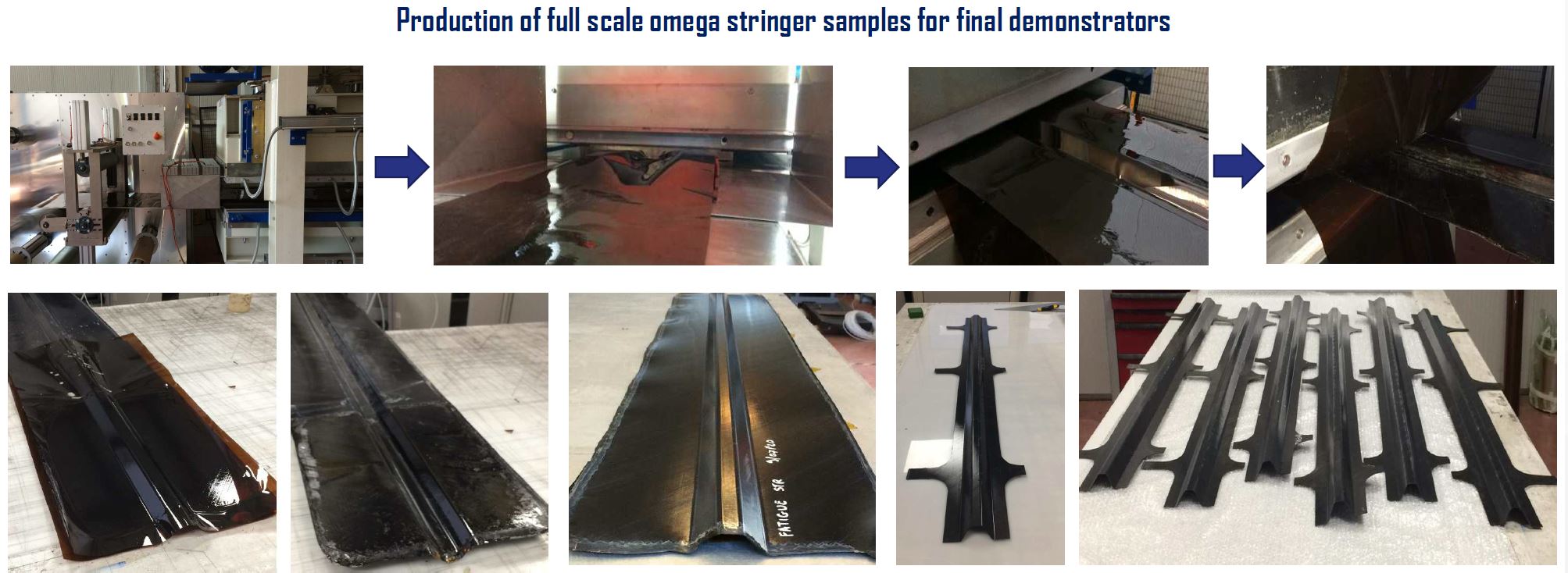
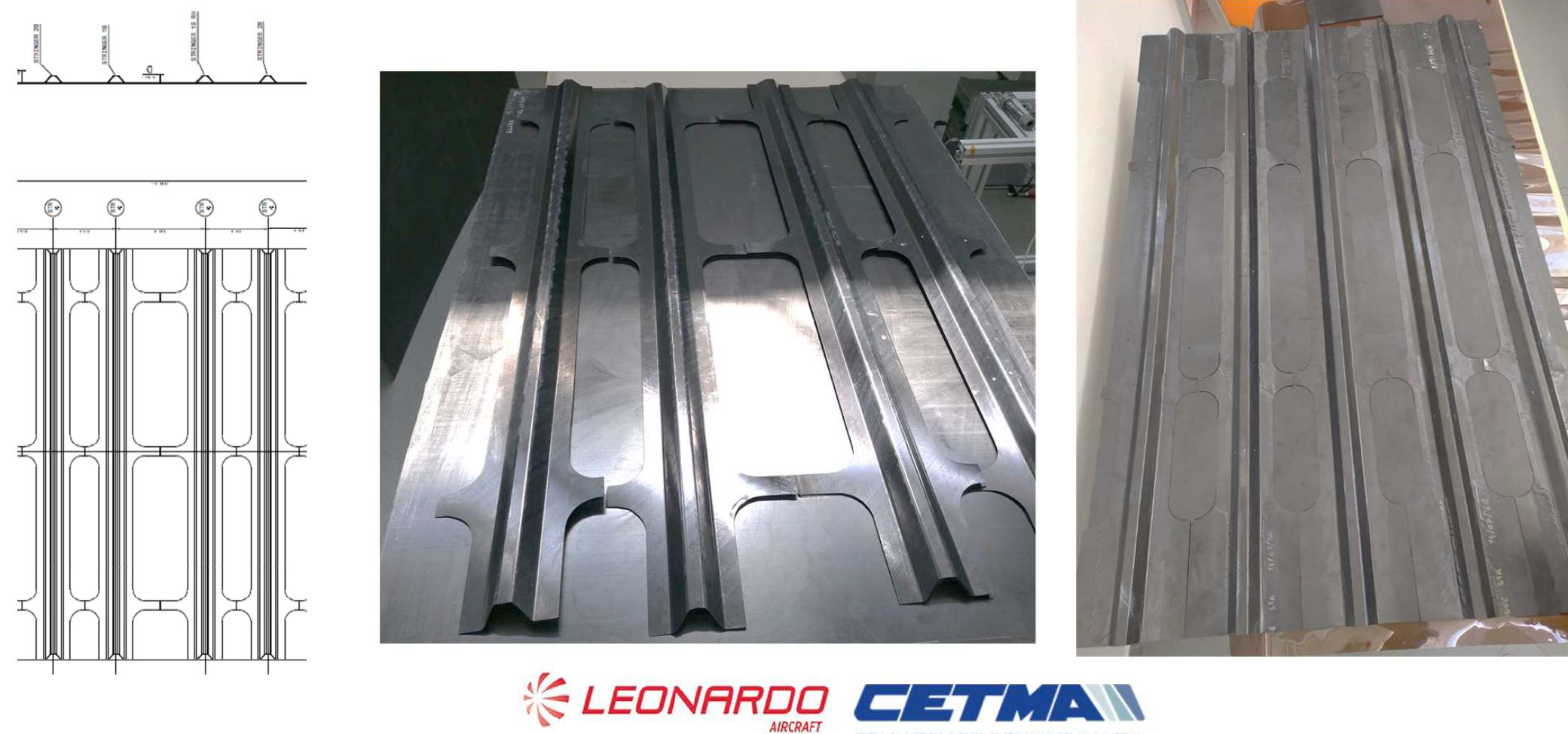
新しい多層材料は、誘導溶接に何らかの利点をもたらしましたか? 「基本的に同じように処理されました」とBarile氏は言います。 「しかし、CETMAが溶接プロセスのパラメーターを定義するのは簡単ではありませんでした。これは、新しい材料の炭素繊維の量が標準のテープよりも少ないためです。」次に、ストリンガーデモンストレーターと最終胴体パネルデモンストレーターがApplusによってテストされました。 NHYTEプロジェクトパートナーであるUniversityof Bath(バース、英国)とLeonardo Aircraftも、NDIを使用してパネルとストリンガーの品質を評価しました。
「私たちはたくさんのクーポンと小さな部品、そして大きなデモンストレーターを作りました」とBarile氏は言います。 「Applusのテスト結果は、現在の標準に比べて製造プロセスのコストが低いことを考えると、非常に優れています。現在入手可能な標準の熱可塑性テープ材料と比較して、強度と剛性の特性が20〜25%低くなっていますが、これを改善するのに役立つプロセスの改善点を特定しました。」
NHYTEは2020年10月30日に終了しました。「私たちのアイデアは、私たちが考えているすべての改善を含む新しいプロジェクトを進めることです」とBarile氏は言います。 「私たちは、AFPの現場圧密、連続成形、および誘導溶接を使用して、材料の製造方法と処理方法を証明しました。今、私たちは工業化のためにさらに最適化する必要があります。」 Novotechは、新しいパートナーで強化された同じコンソーシアムを推進しようとしています。
特に、レオナルドは、迅速に加熱および冷却できる誘導溶接とTPCテープを使用して、AFPの現場統合の改善にも取り組んでいます。さらに、PEI / PEEK多層複合材料に関する有望な結果が、IMDEA Materials Institute(スペイン、マドリッド)とFIDAMC(スペイン、マドリッド)の研究者によって発表されました。後者は、長年にわたってAFPの現場統合のリーダーです。その他の技術論文については、NHYTEの出版物を参照してください。
SWINGプロジェクト
スマートウィングフォーニュージェネラルアビエーション(SWING)は、ピアジオエアロスペース(イタリア、ヴィッラノーヴァダルベンガ)からの承認を得て開始されたプロジェクトであり、イタリア経済開発省(MISE)が共同出資しています。 Novotechに加えて、イタリアのプロジェクトコンソーシアムは、コーディネーターとして技術開発会社Protom(Naples)、Laer Aeronautical Manufacturing(Airola)、A。AbeteAerostructures(Nola)、および航空宇宙設計スペシャリストItalSystem(Avellino)で構成されています。 SWINGの目標の1つは、ピアジオの P.180 Avanti デモンストレーションプラットフォームとしてのフォワードウィング。
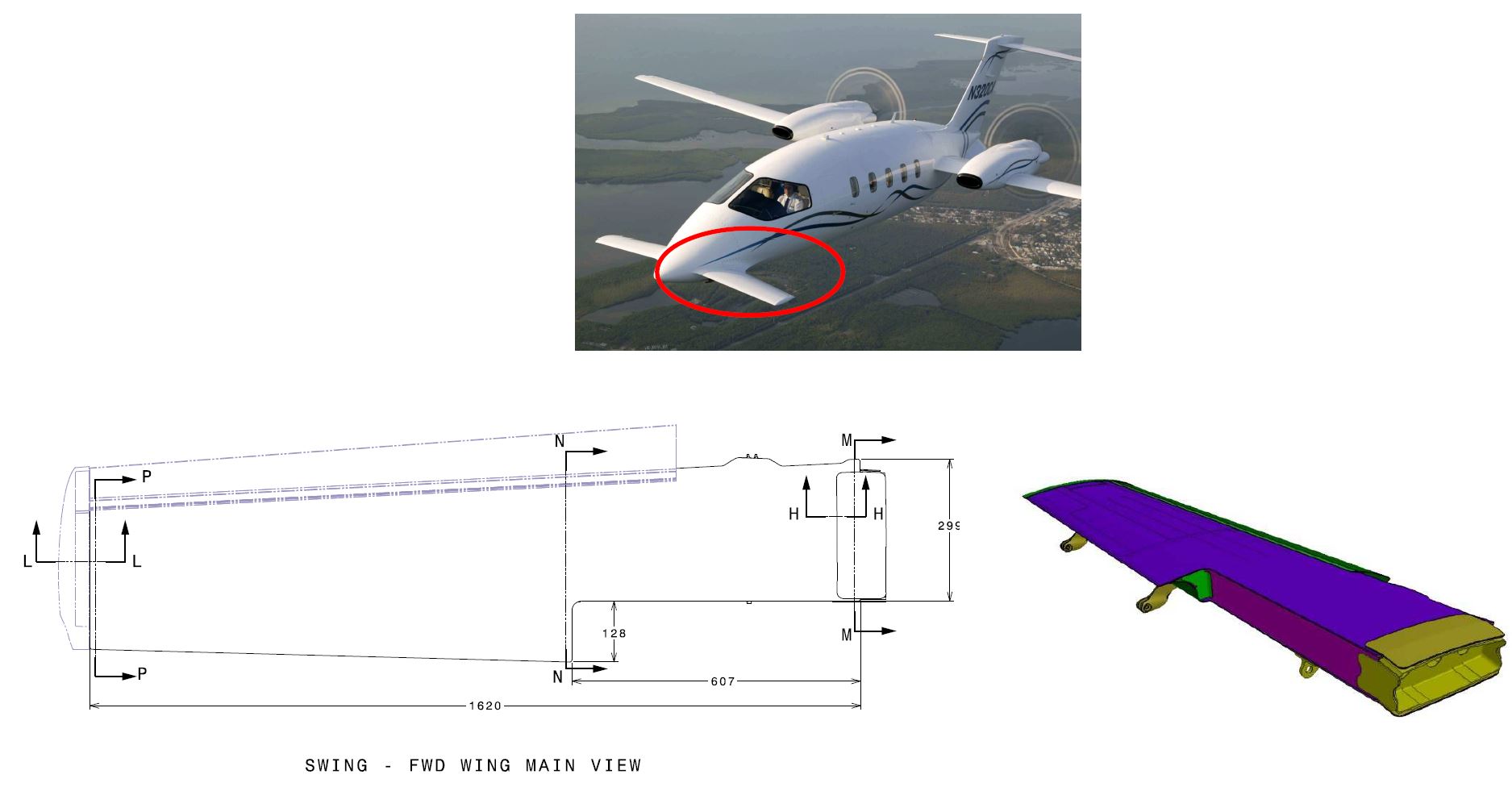
「アイデアは、P.180の前翼を、上部パネルと下部パネルの2つの主要部分で製造することです。どちらも、統合されたストリンガーとスパーで成形されています」とLecce氏は言います。
「私たちにとって、これは英国のソルベイの認定ラボとしての仕事から始まりました。2015年以来、AFP、LRI、熱可塑性複合材料の新しい材料とプロセスに協力してきました。 AFPで使用するソルベイのPRISMTX1100ドライファイバーテープを使用してドライプリフォームを作成していました。次に、これらのプリフォームにソルベイPRISM EP 2400強化エポキシ樹脂を注入し、オーブンで硬化させました。 Clean Sky 2 Green RegionalAircraftプログラムのAIRGREEN2プロジェクトの枠内でこの作業を行った後、SWINGプロジェクトを継続しました。」 PRISMTX1100およびPRISMEP 2400は、ユナイテッドエアクラフトコーポレーションによって、民間航空機用の最初の樹脂注入翼であるAeroCompositによって製造されたIrkutMS-21シングルアイルジェット旅客機の製造に認定されたことに注意してください。
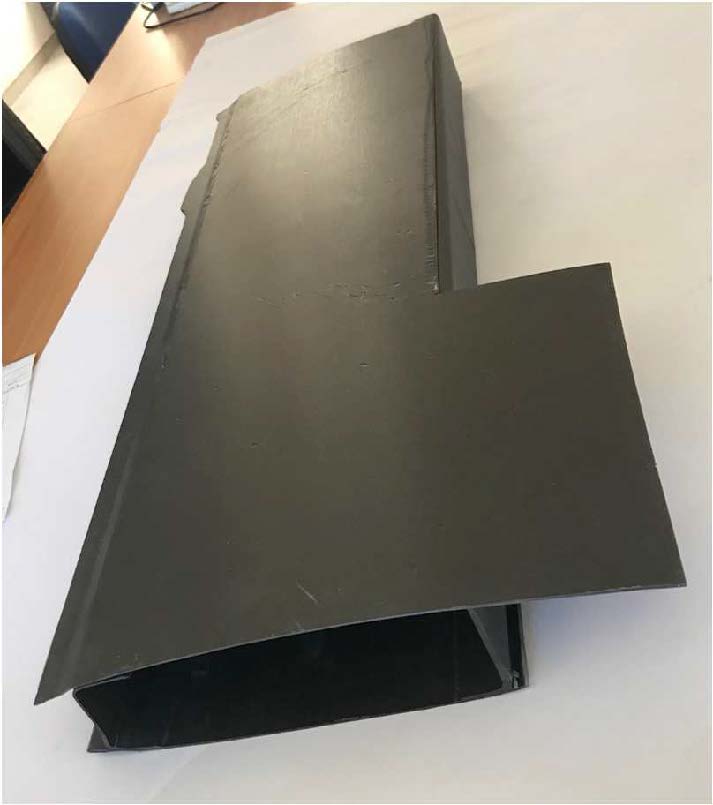
成形された上部パネルと下部パネルは、構造用接着剤を使用して接合され、来年は静的にテストされます。 「並行して、TX1100ドライテープとコベストロ(ドイツ、レバークーゼン)の樹脂ブレンドをベースにした別の複合材料を特徴づけています。これは、特に高い生産率を必要とするセクターで、航空宇宙グレードの樹脂の有効な代替品となります」とBarile氏は付け加えます。 「この樹脂はこれらのシステムほど高性能ではありませんが、注入でうまく機能し、ウィングボックスの要件を満たしています。コストを削減したい場合は、ある程度の妥協が必要です。この開発が一般航空へのAFP技術の導入に貢献することを願っています。自動車分野でも使用できます。」
TRINITI
Novotechは、Clean Sky 2プロジェクトTRINITI(航空機用のマルチマテリアル熱可塑性高圧窒素タンク)にも取り組んでいます。このプロジェクトは、2019年に開始され、2021年に終了します。このプロジェクトへのNovotechの参入は、イタリアの航空宇宙会社との開発から再び発展しました。 「私たちは、ロケット用の極低温燃料タンクの製造において、現在使用されているフィラメントワインディングプロセスと比較して、多層テープを使用してAFPの可能性を検証するために取り組んでいました」とBarile氏は説明します。 「基本的に、TRINITIはNHYTEと同様の多層材料の概念を開発し、AFPの現場圧密を使用してタンクを作成します。」
「FWに関するAFPの利点は、材料を配置する場所を決定できることです」と彼は続けます。部品に連続的に巻かれたフィラメントに拘束されることはありません。フィラメントの巻き取り中に材料を切断できないため、エンドキャップに多くの材料があるタンクを考えてみます。 AFPを使用して、必要な場所でファイバー/テープを切断して再起動することにより、材料は必要な場所でのみ使用されます。したがって、ガスの浸透を防ぐために重要なテープ間のギャップを管理できます。フィラメントワインディングでこれを行うには、AFPではトウプレグではなくスリットテープを使用するため、適用する材料を増やす必要があります。そして、現場での統合により、オートクレーブは必要ありません。 AFPが実現可能な代替手段であり、非常に手頃な価格である可能性があることを実証しました。」
「現在、CETMAは、仕様に対する多層材料の性能を評価するためにガス透過試験を実施しています」とBarile氏は言います。航空機の消火システムで使用される高圧長期貯蔵窒素タンクの要件は、トピックマネージャーのDiehl Aviation(Gilching and Dresden、ドイツ)によって提供されています。これらのタンクは、地上で-55°Cから85°Cの温度、飛行中の操作中は-40°Cから70°C、最大1,000バールの圧力に耐える必要があります。
「目標は、重量と製造ステップを削減することです」と彼は述べています。 「ただし、この方法を使用した製造コストを定義する必要があります。不要な材料を配置しないことで重量を節約できますが、フィラメントワインディングはAFPに比べて高速なプロセスです。」もう1つの要因は、このタイプのタンクには通常、CFRPで覆われた金属またはプラスチックのライナーがあることです。 Barileは、TRINITIがライナーレス(タイプV)タンクを目指していると言います。 「低ボイドのAFPラミネートを使用することで、ガスの浸透を防ぎます。現在、CETMAでさまざまな材料の組み合わせを使用してテストを行っており、ダウンセレクトの準備をしています。次に、プロトタイプタンクを作成しますが、タンクの設計は、選択された材料と最終プロセスによって異なります。ですから、これが私たちが今取り組んでいることです。テスト活動は、CTL Composites(ゴールウェイ、アイルランド)によって実施されます。」
SEAGULL
挑戦的なプロジェクトSEAGULLは3年前に開始されました。 「私たちの目標は、新しい複合材料製造技術、ハイブリッド電気推進力、および私たちが開発して特許を取得した自動折り畳み翼を組み込んだ新世代の小型水上飛行機を開発することです」とレッチェは説明します。 「その意図は、垂直離着陸(VTOL)航空機と競争力があるが、より手頃な価格を提供する短距離離着陸(STOL)航空機でした。これは、あらゆる表面から操作される個人用航空機である可能性があり、将来の航空学および機動性にとって重要な可能性であると信じています。」
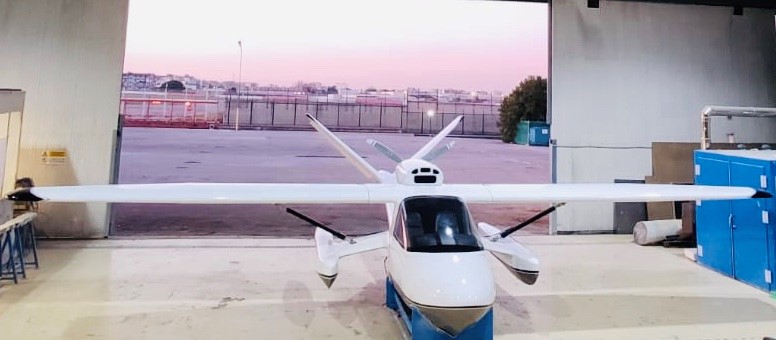
SEAGULLチームは、ハイブリッド推進システムをテストし、最初の水中プロトタイプを作成し、10月に水中テストを開始しました。 「このテストが完了した後、さらに数か月以内に飛行プロトタイプを作成します」とレッチェは言います。 「これは非常に経験豊富なチームであり、一般航空業界で50年以上の経験を持つ重要な企業で構成されています。」
SEAGULL飛行プロトタイプは、複合胴体、尾翼、翼を備えています。 「繰り返しになりますが、AFPと樹脂注入を使用した自動製造の適用を推進します」とBarile氏は言います。 「これらのプロセスを使用する複合材料の主な問題の1つは、材料のコストです。確かに、私たちがやろうとしているのは、コストの面でより民主的な材料とプロセスの組み合わせも見つけることです。」
樹脂
- Fraunhofer IPTは、水素貯蔵、エンジンブレードなどの熱可塑性複合材料を開発しています
- Composites Evolutionは、高性能プリプレグ、新しい熱可塑性UDテープを展示しています
- 少量の航空構造物の自動複合材料製造のための設計
- 熱可塑性テープは、複合エアロストラクチャーの可能性を示し続けています
- 複合材料用の再処理可能、修理可能、リサイクル可能なエポキシ樹脂
- 複合材料の硬化監視のためのACおよびDC誘電測定の組み合わせ
- KarlMayerが熱可塑性UDテープの生産ラインを立ち上げ
- SWMは樹脂注入用のNaltexフローメディアを発売
- 自動車用複合材料の最初の熱可塑性ドア
- 熱可塑性複合材料コンソーシアムは、自動車および航空宇宙向けの大量生産を目指しています
- イスラエルと米国でコンポジットの世界にサービスを提供