自動エアロコンポジット生産:液体成形または溶接熱可塑性プラスチック?
OEMとサプライヤが次世代の航空機を可能にする材料とプロセスを模索する中で、2つの異なるアプローチが実証されています。 1つ目は、エアバスA320スポイラー用のSpirit AeroSystem(スコットランド、プレストウィック)の高速樹脂トランスファー成形(RTM)ラインや、エアバス主導のWing of Tomorrow(WOT)プログラムで見られる、乾式繊維プリフォームの液体成形です。これは、ノンクリンプファブリック(NCF)の自動配置と液体樹脂の注入を使用し、続いてオーブンでのオートクレーブ(OOA)硬化を使用します(「高速の自動航空宇宙RTMラインが次世代のスポイラーを提供」および「更新:下部翼」を参照)スキン、ウィングオブトゥモロー」それぞれ。)
2つ目は、たとえばClean Sky 2多機能胴体デモンストレーター(MFFD)に搭載されている熱可塑性複合材料(TPC)で、自動ファイバー配置を使用して硬化スキンが作成されます。上半分はその場で統合され、下半分はオートクレーブで統合されます。半分—溶接による組み立てが続きます。これらのプログラムは自動化を使用して、コストを削減しながら生産率と品質を向上させます。しかし、それらはどのように比較されますか?
ドイツ航空宇宙センター(DLR)の構造設計研究所は、アウグスブルクで軽量生産技術センター(ZLP)を運営しています。その多くの複合材料製造プロジェクトの中で、PROTECNSRとFastLane RPBは、それぞれ、ツインアイルエアバスA350用の液体成形熱硬化性後部圧力隔壁(RPB)とシングルアイルエアバス用の熱可塑性RPBを比較するユニークな機会を提供します。 A320。どちらのプロジェクトも、これらの構造のTier1サプライヤーであるPremiumAerotec Group(PAG、ドイツ、アウグスブルク)と協力し、サイクルタイムとコストを評価しながら自動化を実証しました。
液体成形TSバルクヘッド
「私たちは何年も前に、複合材料製造の手動プロセスを分析するためにAZIMUTプロジェクトでPAGを開始しました」と、ZLPアウグスブルクの組立および接合技術の責任者であるラースラーセン博士は述べています。 「私たちの最初の自動化ソリューションはレイアップ用でしたが、その後、より多くの操作を自動化することに取り組みました。」 PROTEC NSRの主な目標は、RPB生産のためのこれらの特殊なソリューションを採用し、それらを単一の自動化されたプロセスにまとめることでした、とDLRのPROTECNSRのプロジェクトマネージャーであるMarcinMalecha博士は説明します。
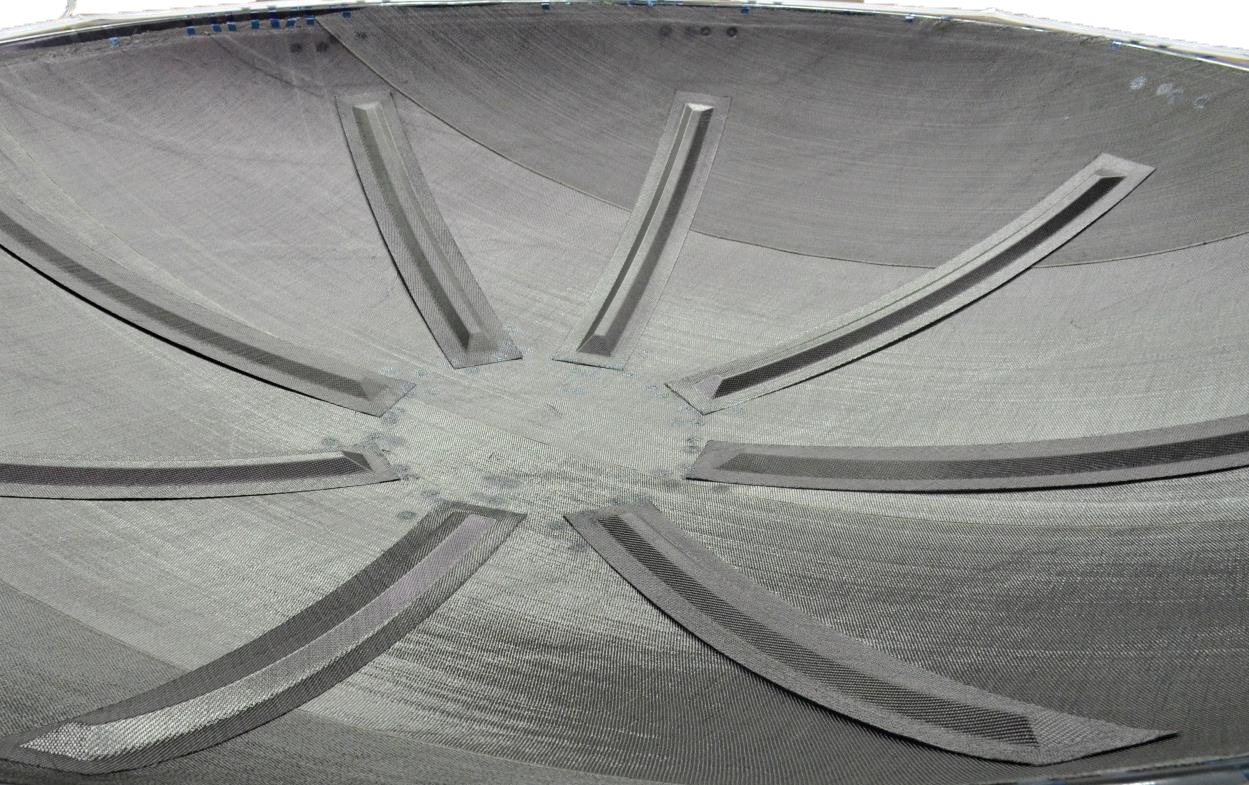
プリフォームとグリッパー。 真空バッグドライプリフォームを作成するためのプロセスステップを下の図1に示します。これには、エアバスが特許を取得した真空アシストプロセス(VAP)を使用してRTM6エポキシ樹脂が注入されました。このプロセスでは、多孔性を低減するために半透膜を採用しています。プリフォームレイアップは、5ハーネスのサテンカーボンファイバーファブリックの幅1.27メートル全体を使用して、長さ5メートルまでの16プライの2セットで構成されていました。これらの2つのセットの間に埋め込まれたのは、最大1.5 x2.5メートルのサイズの25個の複雑な形状の補強部品でした。 8つのストリンガーが上に配置されました。
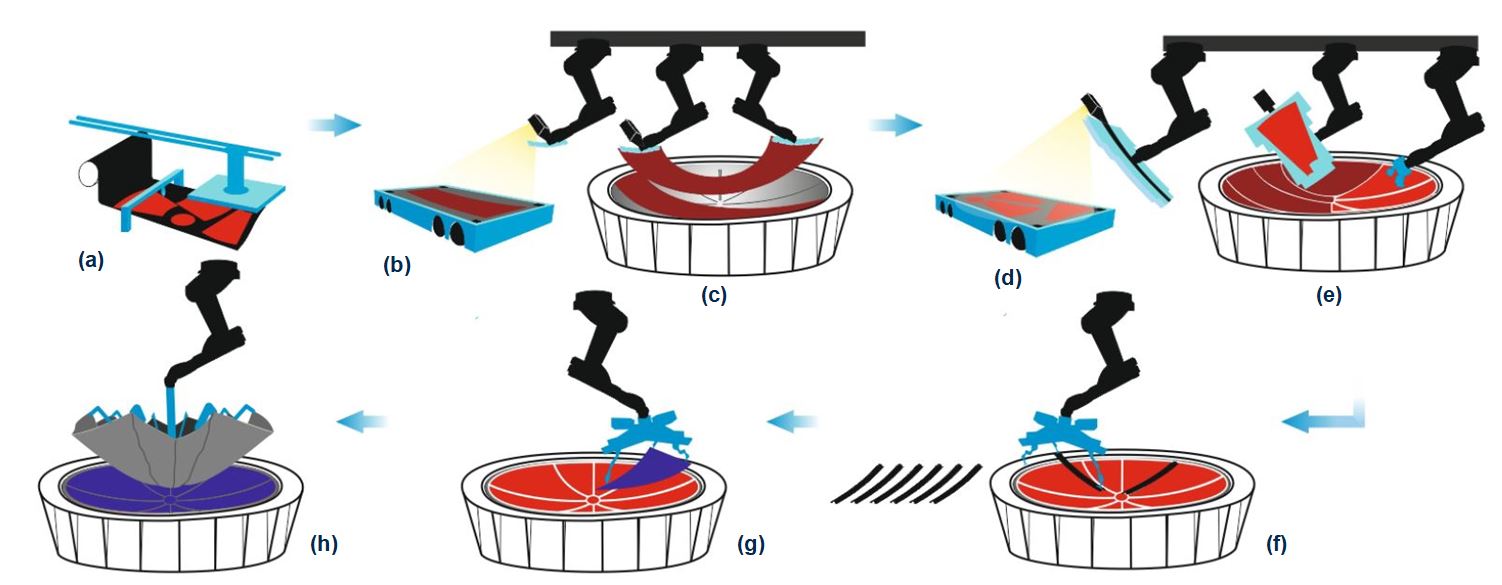
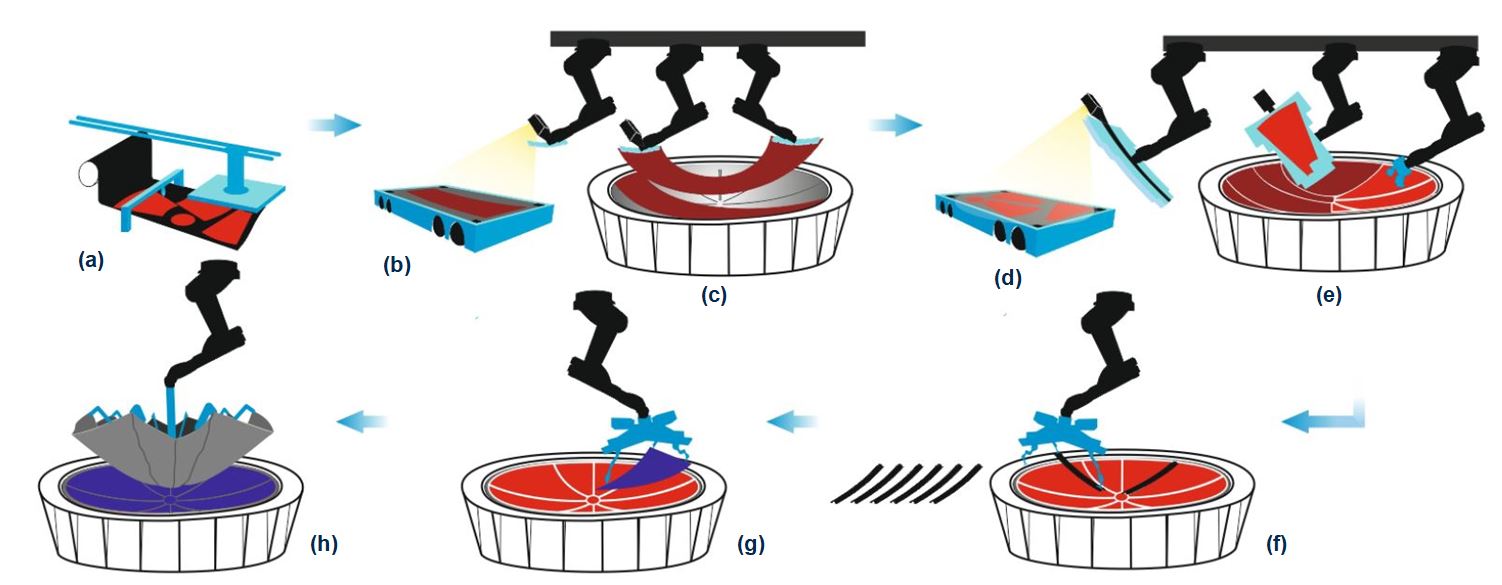
「ドレープとハンドリングに必要な精度を達成できるツールとグリッパーを開発することは、最大の課題の1つでした」とLarsen氏は述べています。これは、3つの異なるドレープメカニズムを必要とするプライの複雑な組み合わせが部分的に原因でした:
- 型の形状に適合しなければならないロールから直接全幅の材料を塗布します。
- ラージカット構造プライのドレーピング 2台のロボットが協力して、ファブリックのエッジごとに1台ずつ、金型のターゲットジオメトリを取得して作成します 配置する前にしわのない適合を確実にするため。
- 1.5 x2.5メートルまでの小さな形状のプライの収容 。
「協調ロボットのために、球形のジョイントで接続された6つのモジュールを含むエンドエフェクターを開発しました」とLarsen氏は説明します。 「これにより、エンドエフェクタは、ヘビのように、金型のターゲットジオメトリに合わせて変形することができます。統合された加熱装置は、輸送および成形中にファブリック内のバインダーを活性化し、配置された後の3D形状と位置を維持します。」
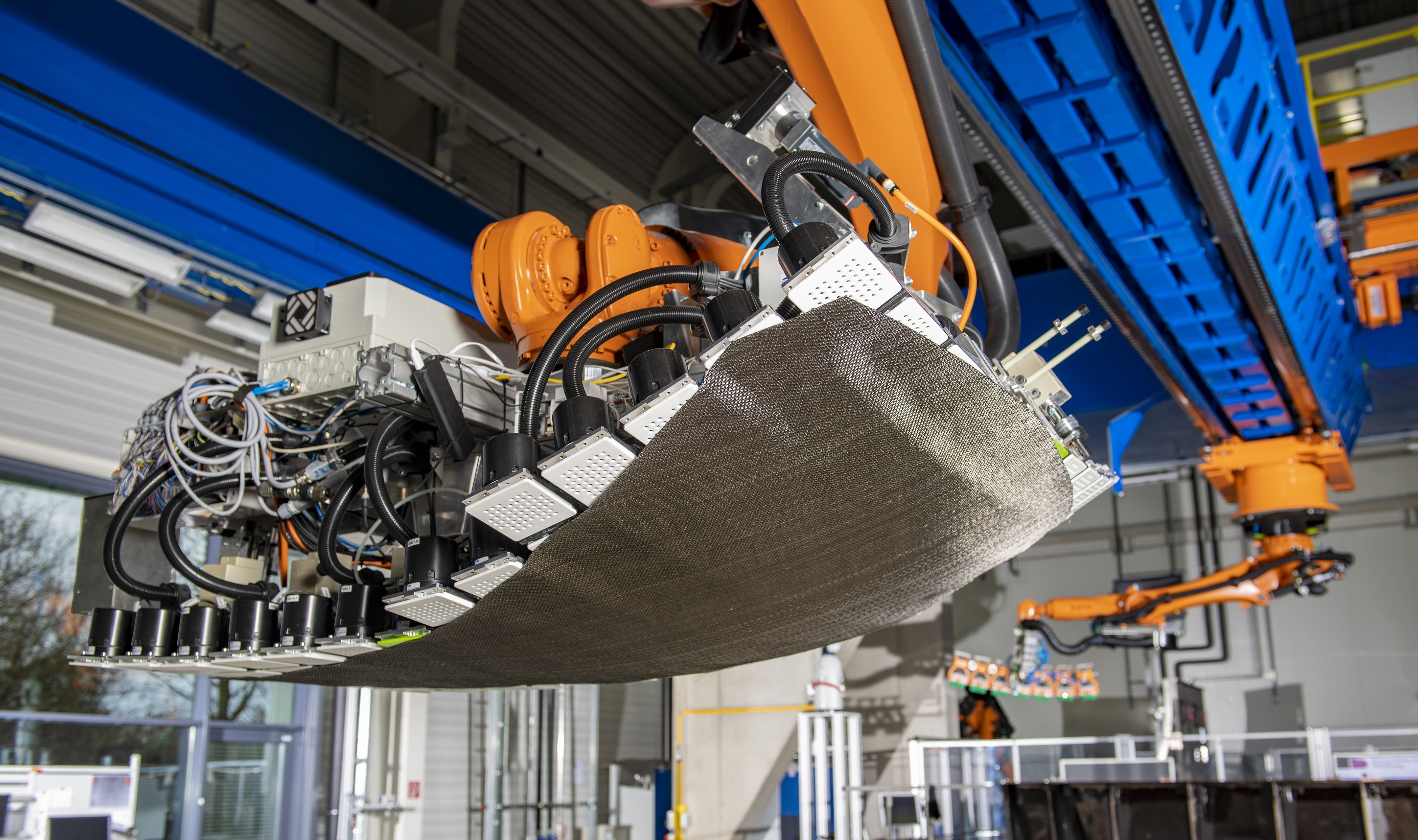
エンドエフェクターは、真空吸引を備えた127個のモジュールを使用して、布のカットプライをピックアップし、3D形状に変換してから、型に入れる前に加熱するグリッパーを備えています。写真提供者:ドイツ航空宇宙センター(DLR)構造設計研究所
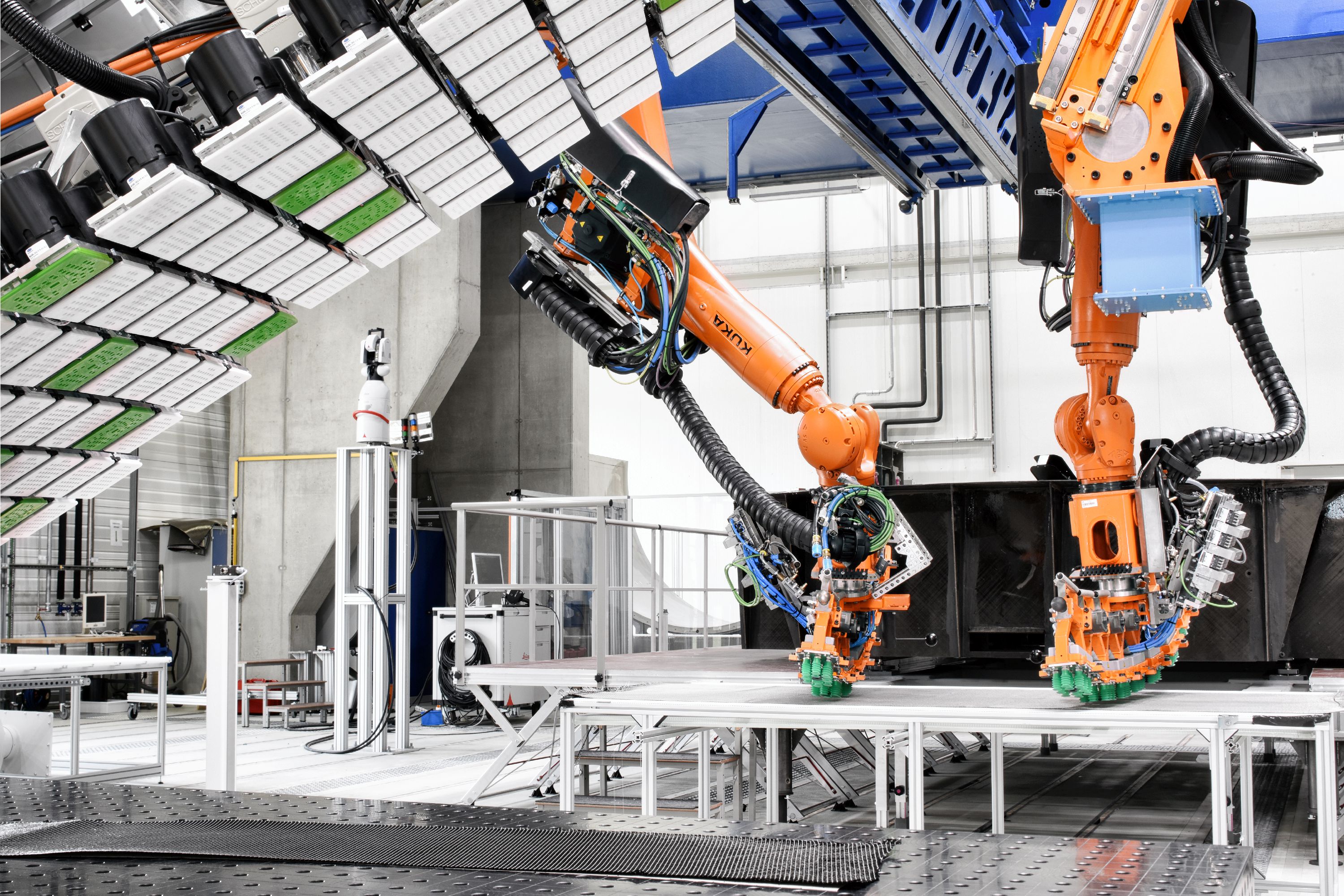
ここでは、127モジュールのグリッパー(左)と共同ロボット(背景)の両方を見ることができます。写真提供者:ドイツ航空宇宙センター(DLR)構造設計研究所
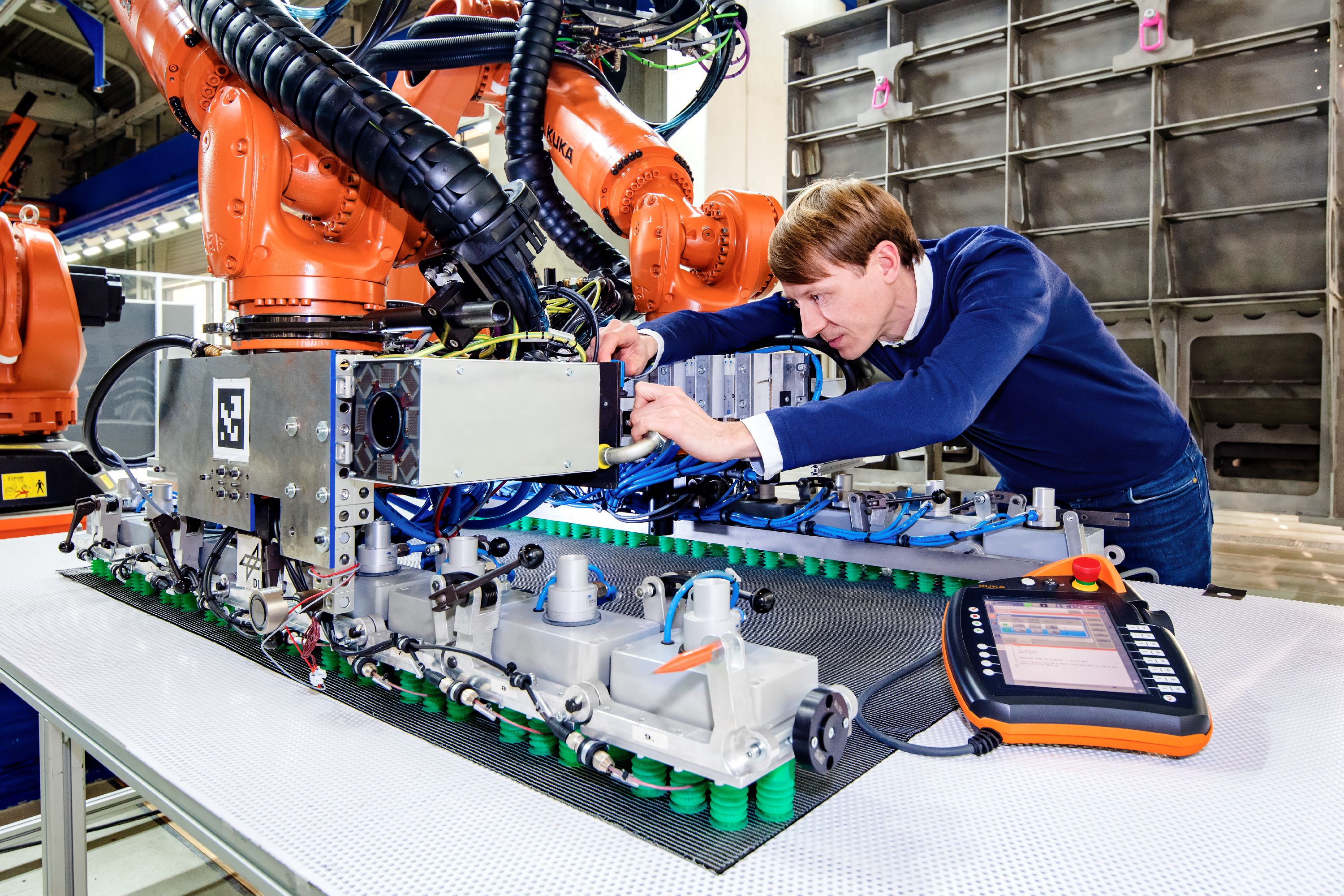
協調ロボットのために、球形のジョイントで接続された6つのモジュールを含むエンドエフェクタが開発されました。写真提供者:ドイツ航空宇宙センター(DLR)構造設計研究所

各ロボットは、大きな布地の層の端を拾います。次に、ファブリックを金型に配置する前に、プライを輸送して必要なターゲットジオメトリを作成するときに、これらが連携して機能します。写真提供者:ドイツ航空宇宙センター(DLR)構造設計研究所
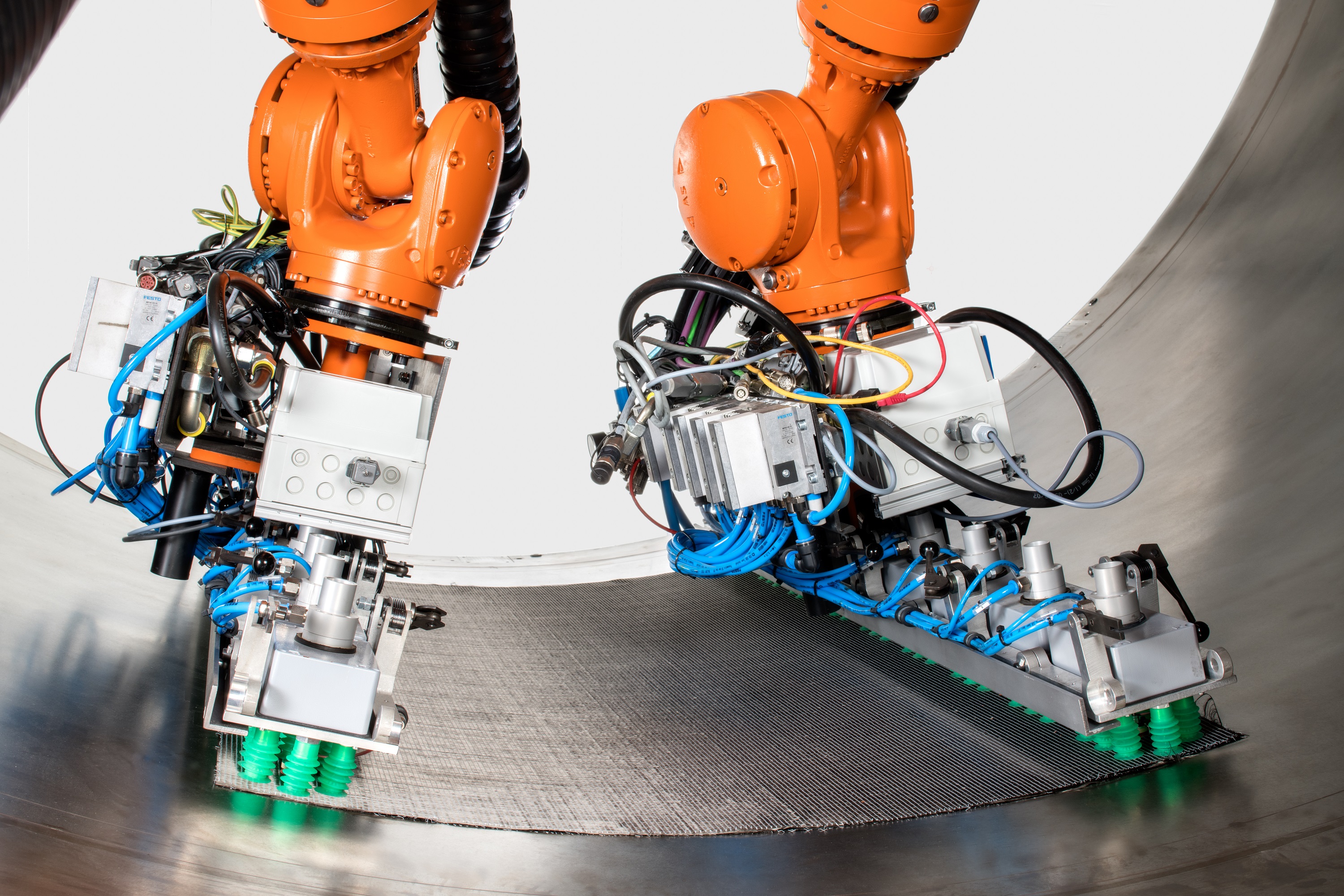
写真提供者:ドイツ航空宇宙センター(DLR)構造設計研究所
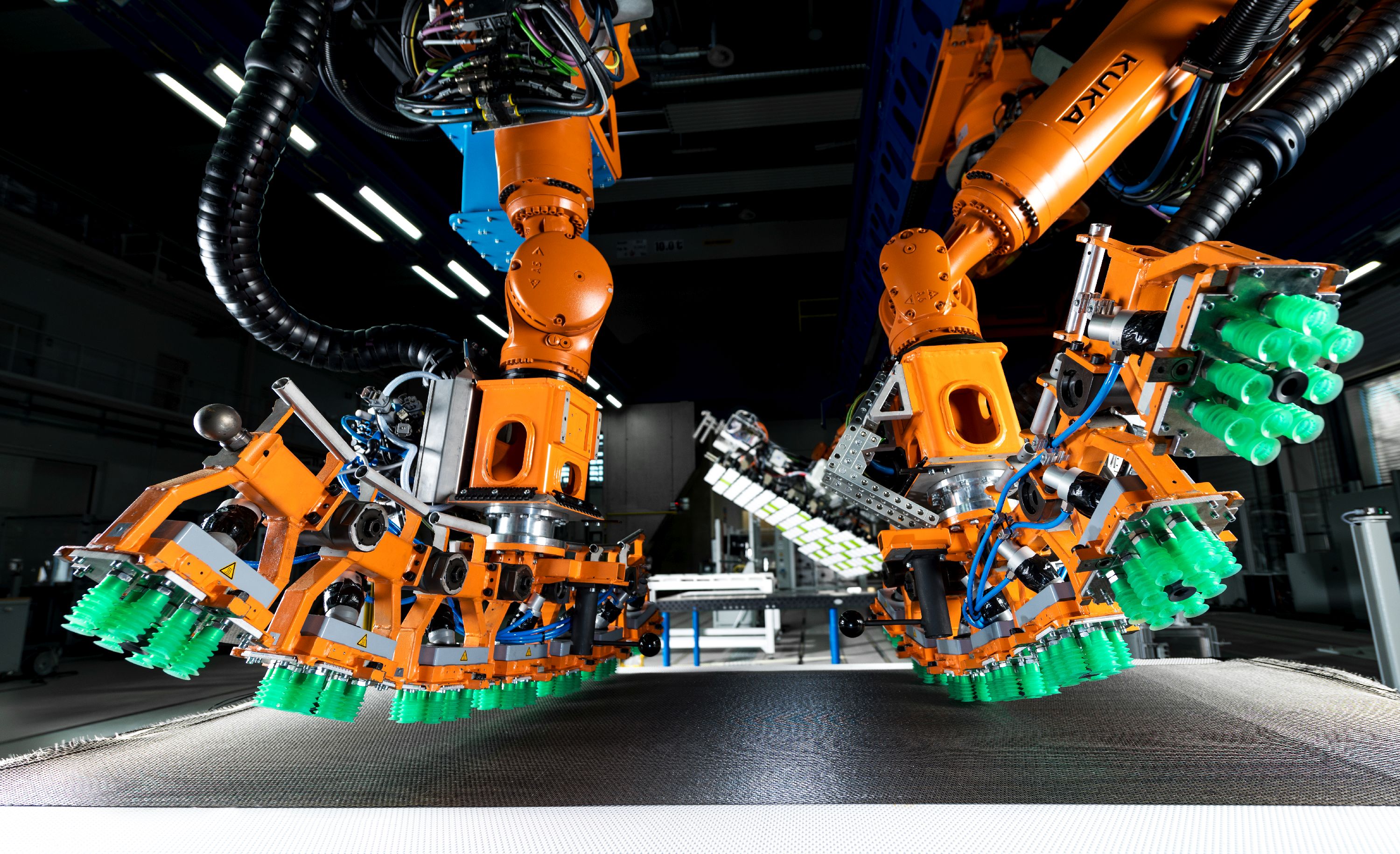
協働ロボットのエンドエフェクタのクローズアップ。写真提供者:ドイツ航空宇宙センター(DLR)構造設計研究所
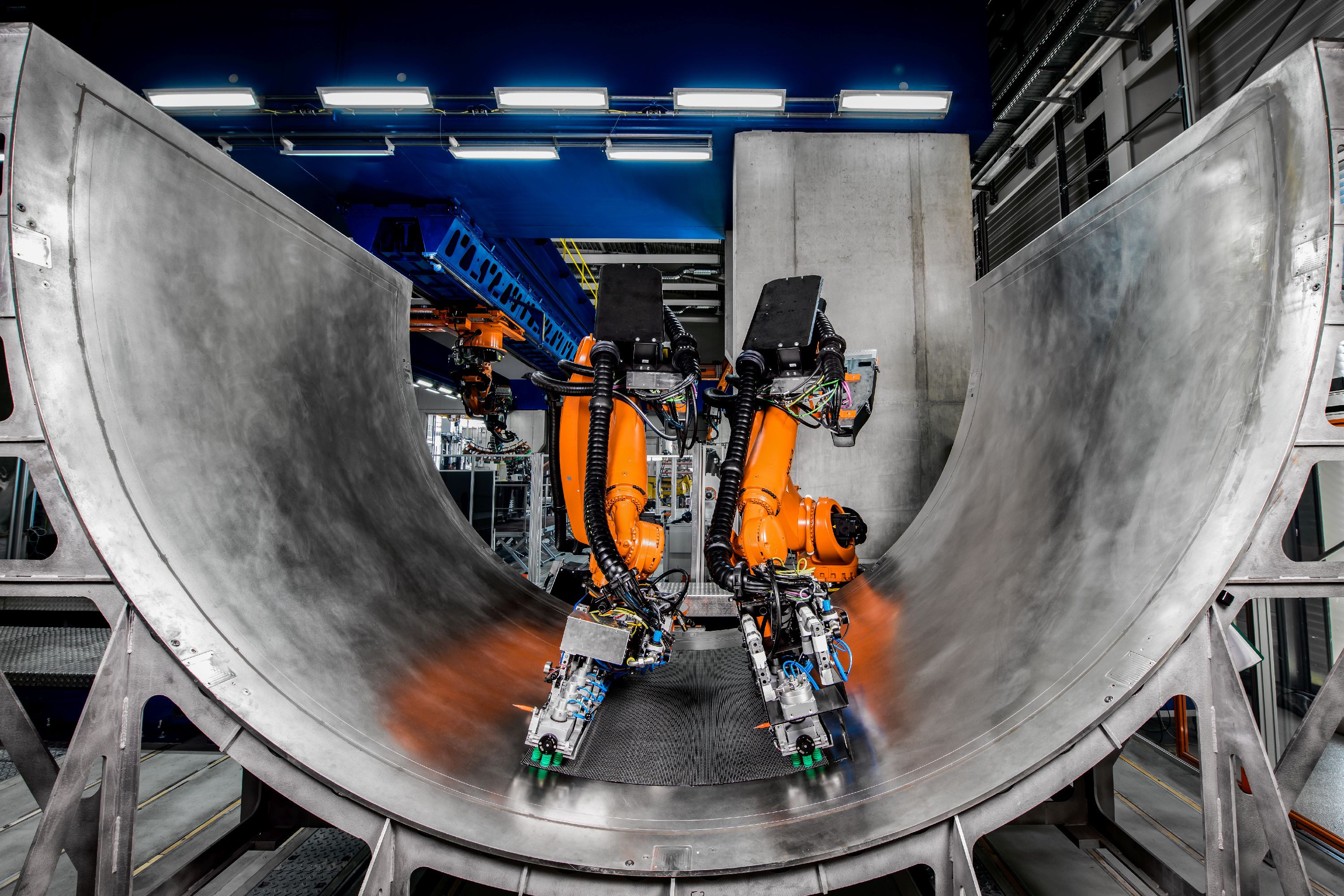
DLRが最初にA320後部圧力隔壁用に開発したこのシステムは、胴体パネルでも実証されており、ロボットを再教育することなく、デジタル設計ファイルに基づいて、さまざまな大型航空構造に柔軟に対応できるように設計されています。写真提供者:ドイツ航空宇宙センター(DLR)構造設計研究所
前へ次へ小さな形のプライの場合 最大1.5x 2.5メートルの、ピックアップ用の真空吸引を備えた127個のモジュールを使用する第2の種類のグリッパーが開発されました。 「このグリッパーは2D状態のマテリアルをピックアップし、それをターゲットジオメトリに曲げます」とMalecha氏は説明します。 「127個のモジュールのどれをしっかりと保持し、どのモジュールをスライドさせて2Dプライを3D形状に変換するかを決定する必要があります。ですから、それは手がドレープをする方法と非常に似ています。私たちは多くの実験を行い、どこで保持し、どこでリリースするかについて経験を積みました。力は、モジュールが材料をつかむ強さによって調整できます。」
インライン検査。 モジュラーグリッパーの光学センサーがドレーププロセスを監視しました。プライを配置した後、ライカT-スキャン(Hexagon Manufacturing、Cobham、UK)とProfactor(Steyr、Austria)によるカメラベースのファイバー角度測定システムを組み合わせたエンドエフェクターが品質を検査します。 「最初にファイバーの角度を測定し、CADファイルと比較しました。次に、各ピースのエッジを測定し、CADファイルとの位置を確認しました。」
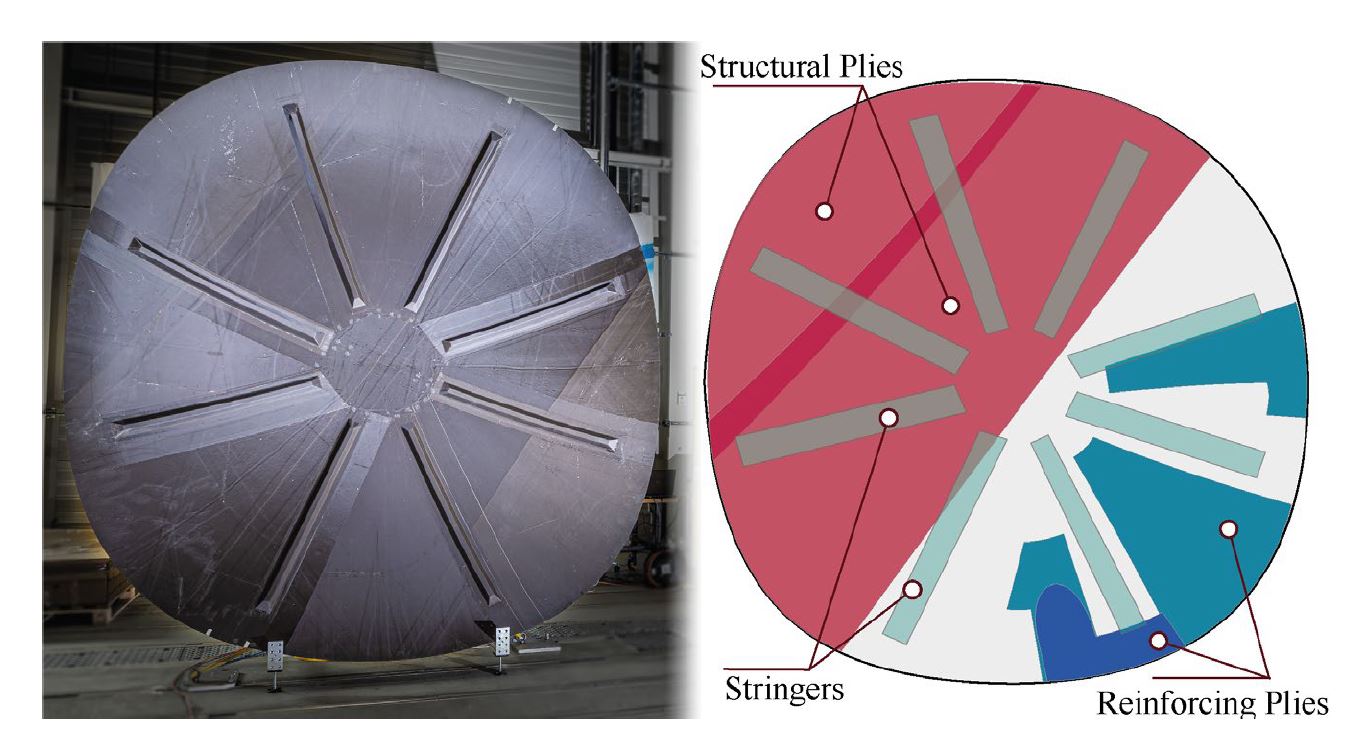
ストリンガーと真空バッグ。 プリフォームが完成した後、8つの補強材(ストリンガー)が上部に取り付けられました。このタスクのために、マルチキネマティックグリッパーが開発され、真空バッグの補助材料を適用するためにも使用されました。このグリッパーは、3つの小型で独立した6自由度(DOF)ロボットと剛性アームで構成され、すべて産業用6-DOFロボットの中央フランジに取り付けられています。真空バッグの補助材料(ピールプライ、穴あきリリースフィルム、樹脂フローメディア(ツール側の補助材料))は、配置場所に合わせて設計され、事前にカットおよび結合されています。 「それらはドレープする必要はなく、配置するだけでした」とマレチャは言います。プレハブの半透膜は、「傘のような」メカニズムを備えたエンドエフェクターを介して半自動で適用され、粘着性のあるテープと外側の真空バッグの配置は手動のままでしたが、自動化することもできました。
サイクルタイムとコスト。 マレチャにとって最大の課題は、プロセスチェーンを監視および制御するためのモジュール式の人工知能(AI)ベースの製造実行システム(MES)を構築することでした。 「まったく異なるプロセスをまとめて、1つのデータ交換ポートを介してMESを介してそれらに命令できるデータ管理システムを構築する必要がありました」と彼は説明します。 「必要に応じてその場で使用できるため、厳格な製造注文に従うよりも柔軟性と幅広い使用が可能になります。」
PROTEC NSRテクノロジーは、2019年1月にフルサイズのデモンストレーターを製造し、2019年半ばまでにTRL5-6の成熟度レベルを達成することによって検証されました。 PAGの現在の最先端技術と比較して、この自動化されたプロセスチェーンは、圧延布の塗布のサイクルタイムを58%短縮し、カットプライのピックアンドプレースを50%短縮します。これらの業務の製造コストは、それぞれ11.5%と31%削減されました。
熱可塑性RPB
「このプロジェクトは2018年にPAGとInstitutfürVerbundwerkstoffe(IVW、カイザースラウテルン、ドイツ)で開始され、大きな部品と一次構造の熱可塑性複合材料で何が可能かを示しています」とFast LaneRPBのプロジェクトマネージャーで専門家のStefanJarka博士は説明します。 ZLPアウグスブルクでの溶接技術。 「RPBは、機械的要件が翼や胴体ほど高くないため、実際には主要ではありませんが、大きく、平らで、わずかに湾曲した構造で何が可能かを示しています。わずか4か月で、既存のアルミニウム構造を熱可塑性複合材料に変換する方法の例として、デモンストレーターA320RPBを開発しました。」
このデモンストレーターは、Cetex炭素繊維(CF)ファブリック/ポリフェニレンサルファイド(PPS)有機シート(Toray Advanced Composites、オランダ、ナイフェルダル)と抵抗溶接を使用しました。溶接される2つの表面間の抵抗素子は熱を発生し、溶接構造に残ります。 GKN Fokker(Hoogeveen、オランダ)は、この技術を何十年にもわたって使用して、航空機の着陸装置のドアと固定された前縁を製造してきました。このA320RPBの場合、ZLPチームは従来のステンレス鋼メッシュの代わりにCF抵抗要素を使用しました。
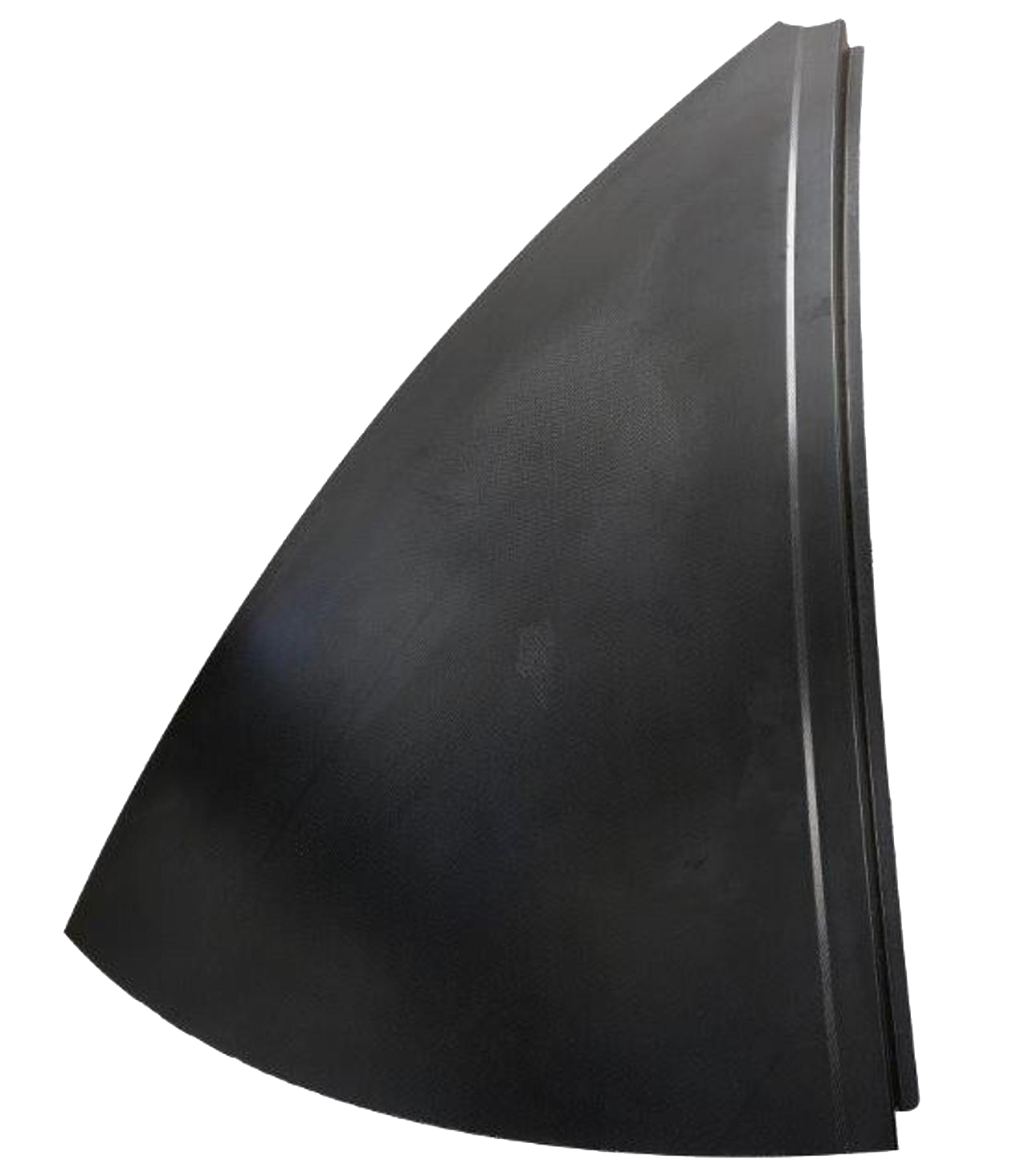
「熱可塑性複合RPBは同じ価格かそれより安いはずでしたが、材料ははるかに高価です」とLarsen氏は述べています。したがって、8つの同一の花びらセクションの使用と同様に、自動化による生産コストの削減が重要でした。 「これらのセクションは、パーツの二重湾曲形状を形成するために必要でした」とJarka氏は説明します。 「単一の部品としての熱成形には、非常に大きなプレスが必要であり、費用がかかりすぎます。したがって、8つの小さなセクションが一致した金属工具を使用してIVWによってプレス成形され、自動溶接を使用してこれらを組み立てました。熱可塑性プレス成形の自動化レベルは、熱硬化性複合材料よりも高くなっています。あなたは主にマッチした金属工具を使用しており、高温であるが一定の温度が主な問題ですが、これにより自動プレスサイクルも非常に速くなります。」
デモンストレーターRPBの全体的なプロセスステップを図2に示します。「使用した溶接プロセスは新しいものではありませんでした」とJarka氏は言います。ワイド]直径3メートルの部分の継ぎ目と品質検査システムを統合します。コンポーネントは最初に位置決めジグを使用して正しい位置に固定され、次に電気エネルギーが適用されて溶接ゾーンでプラスチック溶融物が生成されました。」
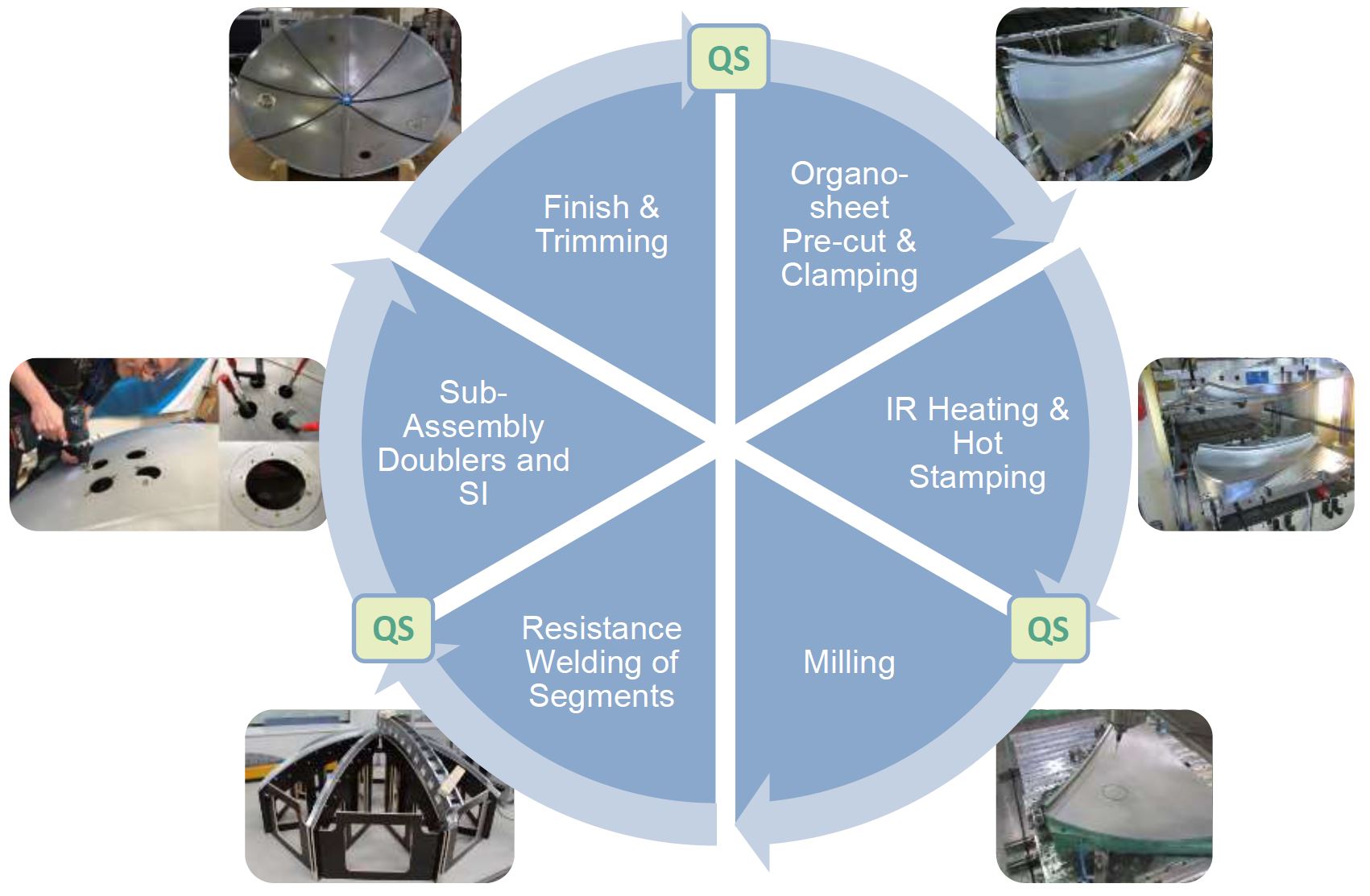
図。 2.熱可塑性RPBプロセスステップ
スタンプ成形されたCF / PPS有機シートの8つのセクション(下)を製造するために使用されるプロセスステップは、抵抗溶接を介して結合され、デモンストレーターA320バルクヘッドを形成しました。写真提供者:ドイツ航空宇宙センター(DLR)構造設計研究所
QAの統合。 「フラッシュランプと超音波の両方で作動するサーモグラフィを試しましたが、これで溶接ゾーンを測定するのはそれほど簡単ではありません」とJarka氏は説明します。 「サーモグラフィは非常に高速ですが、適切に統合されているかどうかは簡単にはわかりません。」代わりに、彼らは標準のテストリグを使用して複数の溶接サンプルを作成し、電流、電圧、温度を測定しました。 「次に、超音波探傷試験(UT)でそれらを検査し、プロセスパラメータと良好な統合の間に相関関係を作成しました」とLarsen氏は言います。 「適切なパラメーターがあれば、適切な部分があります。また、溶接中に取得したデータを、確立した最初のベースラインと比較するためのプロセスシミュレーションを構築しました。」
自動化とサイクルタイム。 「自動車部品の規模では、プロセス全体が非常に高速でした」とJarka氏は言います。 「2019年のレビューでTRL3を達成し、その後TRL4に成熟しました。2021年末までにTRL6を達成する予定です。」パンデミックの前に、PAGは2021年までに熱可塑性RPBを生産することを示していました。将来はまだはっきりしていませんが、熱可塑性RPBは依然として「明日の胴体」を可能にし、重量を41キログラムから35キログラムに減らすと見られています。組み立て時間は75%、全体の部品コストは10%以上です。
TSとTPコンポジットの比較
「熱可塑性プラスチックプロセスは非常に高速であるため、アルミニウムよりも安価で、月に100機の航空機の生産率を達成することもできます」とJarka氏は言います。 「RPBは熱可塑性プラスチック溶接だけでなく自動化にも適しています」とMalecha氏は言います。 「乾式繊維の液体成形RPBは、自動化するのに費用がかかります。」
「しかし、その自動化は興味深いものです。サブプロセスの一部だけを自動化することで実際の利益を達成できるからです」とLarsen氏は言います。 「たとえば、補助装置を自動化することで、手動プロセスの約10倍の速さで、約1時間で真空バッグを完成させることができました。」しかし、彼は、コストがそのような改善を実施するための主要な障害であることを認めています。 「デジタルツール、ロボット、および開発のコストは、RPBなどの単一の部品には高すぎます。しかし、このシステムを多くの部品に使用できるモジュラーアプローチを開発できれば、このコストはより広範囲に分散され、時間と労力を削減して計算すると手頃な価格になります。」 CW で説明されているように、ZLPは実際にこれを達成しています。 の2020年7月の機能:「コンポジット4.0:デジタルトランスフォーメーション、アダプティブプロダクション、新しいパラダイム」
「熱硬化性と熱可塑性の複合構造の比較はまだ多くありません」とMalecha氏は言います。 「しかし、熱硬化性プロセスと熱可塑性プロセスの比較を始めています。」彼は、次の目標は、熱可塑性のウェルドラインが航空機の翼と胴体に必要な特性を備えていることを示すことであると述べています。また、その性能は、たとえば、大型の統合された液体成形翼でも示される必要があります。これはまさにMFFDおよびWOTプログラムが達成しようとしていることです。そして、次のステップを示すために、彼らの結果、および他の多くのClean Sky2およびECプロジェクトからの結果を待っています。
樹脂