費用効果の高いCFRPエアロストラクチャーの連続生産のためのHP-RTM
樹脂トランスファー成形(RTM)が約10年前に高圧RTM(HP-RTM)に移行し始めたとき、それは主に自動車用途で賞賛され、複合部品のサイクル時間を数時間から2分未満に短縮しました。この技術を航空宇宙部品に適用することについてはあまり言われていません。航空機業界には、従来のRTMで長い歴史があり、数千の炭素繊維強化プラスチック(CFRP)ファンブレードや民間航空機エンジン用の格納ケースを製造するために使用されています。エアバスは、RTMを使用してエアバスA320用に長さ7メートルのワンピース複合マルチスパーフラップのプロトタイプを作成しました。しかし、何時間にもわたるプロセスでのこの経験を、数分で複合航空機部品の完全に自動化された成形に移行することは可能ですか?何人かの主要なプレーヤーはそれが可能であると言います。
ここでは明確にするためにLP-RTMと呼ばれる従来のRTMは、通常10〜20バールの射出圧力を使用します。一方、HP-RTMは、30〜120バールの射出圧力を使用します。
「私たちは、胴体フレームを製造するためのEU資金によるプロジェクトを通じて、10年前に航空宇宙RTM処理の作業を開始しました」と、シリアルコンポジット用の革新的なツーリングシステムのサプライヤーであるAlpex Technologies(Mils、オーストリア)の研究開発責任者であるBernhardRittenschoberは述べています。部品生産。 「当時、[エアバス] A350の多くの部品がRTMで作られると予測されていましたが、これは実現しませんでした。」しかし、Alpexはこの技術に取り組み続け、自動車産業と航空宇宙産業の両方へのサプライヤーとして、これら2つの産業で使用されるプロセスをどのように統合できるかを検討し始めました。 「アイデアは、航空宇宙で認定された[Hexcel] RTM6エポキシ樹脂を使用することでしたが、自動車工具のベストプラクティスと、サイクルタイムを短縮するための自動噴射システムを備えています」とRittenschober氏は説明します。
その結果、オーストリア政府が資金提供した2013年から2015年にかけて、AlpexがパートナーのAirbus Helicopters(ドイツのドナウワース施設)、機器サプライヤーのKraussMaffei(ドイツのミュンヘン)、テストスペシャリストのAerospace and AdvancedCompositesとともに参加したTAKEOFFという研究プログラムが行われました。 (AAC、Wiener Neustadt、オーストリア)および樹脂サプライヤーHexcel(スタンフォード、コネチカット、米国)。このプログラムは、HP-RTMがA350ドアフレームのコストを30%削減し、2成分(2K)樹脂システムの使用、インモールドセンサーによるインテリジェントな射出および硬化監視などの重要な技術開発をもたらしたことを実証しました。部品サイクル時間をさらに短縮する機能。 Alpexは開発を続けており、このHP-RTMテクノロジーが現在のCFRP生産の問題を克服するのに役立つ可能性があると考えています。
この見解を支持するために、Airbus OperationsGmbHの子会社であるCompositesTechnology Center(CTC)も、最初はLP-RTMで、次に約5年前にHP-RTMに移行して10年間自動RTMを開発してきました。 ( CompositesWorld CTCのKraussMaffeiHP-RTMマシンとその施設の2016年ツアー中の開発作業に注目しました。)「HP-RTMは、反応性の高い樹脂を使用できる高速混合により、注入と硬化のボトルネックを解決します」とJanSchiller氏は説明します。実動システムのCTCプロジェクトリーダーおよびRTMテクノロジーのリードコンタクト。 「私たちは、20分のサイクルタイムで航空宇宙の要件(たとえば、繊維の体積が60%、ボイドが2%未満)を満たす、1〜2メートルのサイズのやや複雑な形状の部品を製造するプロセスを開発しました。」彼は、昨年エアバスのサプライヤーを訪問して話し合った後、HP-RTMに移行するための多くの部品が特定され、A320航空機のより高い生産率を可能にしたと付け加えました。 「現在、これらの特定の処理を開発しており、今年はそれらを連続生産するために取り組んでいます。」
HP-RTMA350ドアフレーム
Alpexの開発は、SPARTAと呼ばれるプロジェクトを介したオーストリアのTAKEOFFプログラムを通じて完了しました。 「エアバスヘリコプターがその部分を選びました」とRittenschoberは回想します。 「このドアフレームは、ドアを開けた状態でA350に足を踏み入れたときに見えるものです。高さ約2メートル、幅200〜250ミリメートル、厚さ8〜10ミリメートルで、一次構造である組み立てられたドアのさまざまな要件を満たす複雑な形状と設計機能を備えています。」 A350ドアは、ドイツのドナウワースにあるエアバスヘリコプターがLP-RTMを使用して製造した14個の部品で構成されています。 SPARTAに選択されたフレームは、ドアのより難しい部品の1つです。 「HP-RTMを標準の航空宇宙LP-RTMと直接比較できるので、これは優れたデモンストレーション部分です」とRittenschober氏は付け加えます。
Alpexは、エアバスヘリコプターでのA350ドアフレームの製造に現在使用されているLP-RTMツールを設計および製造しました。 HP-RTMツールの設計と構築については、 それはより自動車的な考え方を適用するでしょう。 「私たちの目標は、航空宇宙複合部品の生産において自動車タイプの自動化を可能にすることでした」とRittenschober氏は言います。 「これは、エアバスがより多くの複合部品を使用し、月に60〜100機の割合で将来のA320を製造する場合に必要です。」
彼は続けます。「エアバスが以前の航空宇宙の複雑さから来ていたのに対し、私たちは部品とプロセスを簡素化してサイクルタイムを短縮しようと積極的に試みていたBMW用の金型を製造していました。たとえば、私たちが始めたとき、エアバスヘリコプターズは、この金型にいくつの部品があるかを尋ねました。」現在のLP-RTMドアの生産には、複雑なマルチピースツールが含まれていることに注意してください。 「HP-RTMツールには上部と下部の金型が1つしかないことを説明しました」と、Rittenschober氏は言います。
したがって、Alpexは単純な金型設計から始めて、処理をより堅牢で柔軟にする機能を追加しました。たとえば、大量の自動車生産に使用されるシーリングシステムなどです。 「さらに、すべてのセンサーが金型に統合されています」と彼は述べています。
プリフォームとプロセス
現在A350ドアフレームに使用されているプリフォームは織物を使用しており、複数の減量ステップが必要であるため、3日間の生産サイクルが発生します。 「代わりにノンクリンプファブリック(NCF)を使用することにしました」とRittenschober氏は言います。 「これにより、価格とサイクルタイムが大幅に低下します。また、Hexcel認定の織物プリフォームを使用して一部の部品をデモンストレーションしましたが、航空宇宙以外の複合材業界では、SGLなどが織物からテープや、NCFなどの低コストのフォームに開発するようになりました。」
射出位置とファイバー洗浄の問題について尋ねられたとき、Rittenschoberは、HP-RTMツールには射出ポイントが1つしかないが、プリフォームが型に固定されて非常に安定しているため、ファイバー洗浄がないことを説明します。
もう1つの重要なポイントは、Alpexが、エアバスヘリコプターで現在使用されている1コンポーネントのRTM6ではなく、2コンポーネント(2K)の樹脂システムを使用することを選択したことです。 Rittenschoberは、2Kシステムはより反応性が高く、HP-RTMに適していると主張し、事前に混合されておらず、危険物の輸送を必要としないため、コストを節約できる可能性があります。ただし、180°Cの高温が必要です。 「これは私たちにとって最も困難な部分でした。120°Cでの処理に慣れていたためです」とRittenschober氏は言います。
KraussMaffeiは、ドイツのミュンヘンにある軽量技術センターに、自動化された高圧(最大80 bar / 1,100 psi)の混合、メーター、および注入を備えたRimStar CompactHP-RTMシステムに完成した工具を設置しました。次に、20個のデモンストレーターパーツを作成しました。 Rittenschoberは、ベースラインプロセスについて説明しています。80°Cで注入し、120°Cまで上昇させ、1時間保持し、180°まで上昇させ、90分間硬化させ、下降させ(2°C /分)、離型します。 「射出には20秒しかかかりませんが、成形サイクルの合計は約4時間です。」
サイクルタイムとコスト
SPARTAドアフレームのまだ長い硬化サイクルは、エアバス認定のHexcelRTM6樹脂の配合と処理によって推進されます。 「熱応力を取り除き、機械的特性を確保するために、その後真空下で追加の後硬化を行うことで、180°Cで30分の硬化サイクルを達成することができました」とRittenschober氏は述べ、特性は非常に良好で、LPに匹敵すると付け加えました。 -RTMパーツ。
「このプロセスを使用して、より多くの部品量の生産を自動化できることを示しました」とRittenschober氏は言います。 「金型に射出して硬化させてから、プレスから後硬化させることができます。」彼は、これには追加のツールセットが必要であると認めていますが、プレスと射出ユニットは1つだけです。 「このシステムを使用すると、部品コストを700ユーロ削減できます。これにより、500〜1,000部品/年の生産率で機器の支払いが簡単になり、それほど大量ではありません。」
CTCプロセスの開発とデモンストレーター
工具とプロセスはさておき、HP-RTMドアプロジェクトには、ファイバーフォーマットの革新的な使用も含まれていました。 「私たちはすでにエアバスによって認定された織物から始め、非常に成功しました」とシラーは回想します。 「その後、NCFとより革新的なテキスタイルを継続しました。」後者には、靭性を高めるための乾燥繊維の配置とトウ層を広げたインターリーフが含まれていましたが、後者は繊維と層の密な充填に問題があり、透過性が低く、樹脂の浸透が妨げられていました。 「透過性を改善するための特殊繊維を使用したNCFなど、これに対処するための開発もあります」と彼は付け加えます。
HP-RTMの圧力に関して、Schillerは、プロセスを使用するという決定は、高いプロセス圧力よりもポリウレタン業界の技術を混合することによって推進されたことを強調しています。 「私たちは、反応性の高い樹脂を適切に混合するためだけにHP-RTMを使用しています」と彼は説明します。 「金型内の圧力がいくらか高くなる可能性がありますが、これは高速射出による二次的な影響です。サイクルタイムが2分の自動車部品の場合、ドライプリフォームに樹脂をはるかに速く浸透させる必要があります。 15分の硬化時間により、樹脂の浸透により多くの時間をかけることができ、金型内の圧力も低下します。」
一方、プレストン数は部品サイズによって異なります。 「最大2メートルのサイズの部品(約1,500トン)を作ることはうまくいきますが、4〜6メートルのサイズの部品は、プレス投資が非常に高くなるため、ビジネスケースを計算する必要があります」とシラーは言います。 CTCは、2018年のJEC Worldで、航空宇宙の一次構造の可能性を表す1.5メートル×0.5メートルのCFRPリブを展示しました。また、2019年末には、より高いトン数のプレスを受け取ります。
2KレジンとセンサーベースのQA
シラーは、以前のすべてのRTM航空機構造は、サプライヤーによって混合された1Kシステムのみを使用していたことを観察し、サプライヤーは混合物を認証し、樹脂が認定要件を満たしていることを確認する責任を負います。 「現在、2Kシステムを検討していますが、課題は混合品質を確保することです」と彼は説明します。プレミックス1Kシステムでは、部品が処理されるまで反応を防ぐために、冷蔵輸送と保管が必要です。したがって、2Kシステムの利点には、この費用の排除と、より高速な処理のためのより高い反応性が含まれます。ただし、1つの問題は、品質保証(QA)が樹脂サプライヤーから部品メーカーに移行することです。 「このQAでは、混合比の検出が必要です 混合樹脂の品質。両方とも、エアバスによる新素材の認定に必要です。つまり、これは、混合直前の2つの成分と、混合後の樹脂の測定を意味します。現在、ミックスヘッドの前にセンサーがあり、ミックスに計量されている樹脂と硬化剤の量を示しています。資格を得るにはこれだけでは不十分です。」
一方、Alpexは、エアバスが必要とする100%適切に混合された樹脂の検証を提供するインライン品質システムの開発に取り組んでいます。 「この開発の当初から、Netzschのインモールドセンサーを使用してきました」とRittenschober氏は述べています。 「NetzschがKistler(スイス、ヴィンタートゥール)と提携したことで、新しいテクノロジーが利用可能になりました。金型に含まれる単一のセンサーから、樹脂の温度、圧力、硬化を監視できます。」
「Alpexはインモールドセンサーを使用するように言っており、混合/射出装置のサプライヤーはセンサーを彼らのに置くべきだと言っています。 システム」とシラーは言います。 「どちらも正しい。」しかし、彼は後者にも改善の必要があると述べています。 「自動車用HP-RTMでは、樹脂の混合比はプロセス全体で測定されるため、平均値です」とSchiller氏は説明します。 「しかし、プロセス中のすべての個別のポイントでこの測定が必要です。これにより、注入中の最後の0.5秒間でも、混合比が常に正しいことがわかります。測定システムには、より優れた時間分解能が必要です。」シラーは、センサーはおそらくミックスヘッドの前、ミックスヘッドの内側に必要になるだろうと示唆しています 型の中で。 「私たちは、航空宇宙アプリケーションでの2K樹脂の評価と並行して、このQA開発に取り組んでおり、機械サプライヤーと協力して、十分な解像度を約束するセンサーシステムを特定しました。今年中に検証されます。」
Alpexは、Aerospace&Advanced Composites(AAC、Wiener Neustadt、オーストリア)によって開発された新しいハイブリッド多機能圧電センサーも試しています。 に配置 RTM金型では、金型内の樹脂フローフロントを監視する圧力センサーとして機能します。プリフォームに樹脂が含浸されて硬化が始まると、インピーダンススペクトルの変化がセンサーによって使用され、硬化の程度が決定されます。硬化が完了すると、圧電センサーが部品の表面で共硬化され、アコースティックエミッションセンサーとしてのパッシブモードまたはガイド付き超音波を使用したアクティブモードのいずれかで構造ヘルスモニタリングに使用されます。それらは、完成部品への衝撃と損傷を監視するために実証されています。
このプロセスデータは、インダストリー4.0インテリジェント生産システムで分析して、品質と効率をさらに向上させるためのルートを特定できることに注意してください。このプロセスデータは、各部品のデジタルツインについても記録できます。
将来の可能性
Rittenschober氏は、HP-RTMテクノロジーの唯一の本当のハードルは認証であると述べています。「このプロセスが機能することをエアバスヘリコプターで実証していますが、誰かがそれを認証する必要があります。」シラー氏は、誰が最初になるかを見つけるのは常にハードルであることに同意しますが、昨年は多くの部品のビジネスケースも計算しました。 「年間200パーツの場合、それは意味がありません。ただし、たとえばA320の部品の場合、魅力的になります。毎月、A320プログラムの目標率が高くなっています。これらの部品の多くは1980年代に設計され、手動で製造されているため、HP-RTMを使用すると簡単にはるかに効率的にすることができます。」
HP-RTMは、CTCで実証された部品サイクル時間が20分であるため、エアタクシーメーカーによって年間5,000機の生産量が上限として提案されている、電気垂直離着陸(eVTOL)航空機市場にとっても魅力的である可能性があります。 UBER。
Alpexは、さまざまなRTMの進歩を開発し続けると、Rittenschober氏は述べています。 「HP-RTMは、CFRPエアロストラクチャーのより費用効果の高い工業化された生産でいくつかの問題を解決するのに役立つ本当の可能性を秘めていると信じています。」シラーは、対象となるA320アプリケーションの多くについて、シップセットごとに多数のCFRP部品があることに注意して同意します。 「したがって、より効率的なプロセスのメリットが蓄積され始めます。本番環境で最初のアプリケーションを入手できれば、他のアプリケーションもあります。」
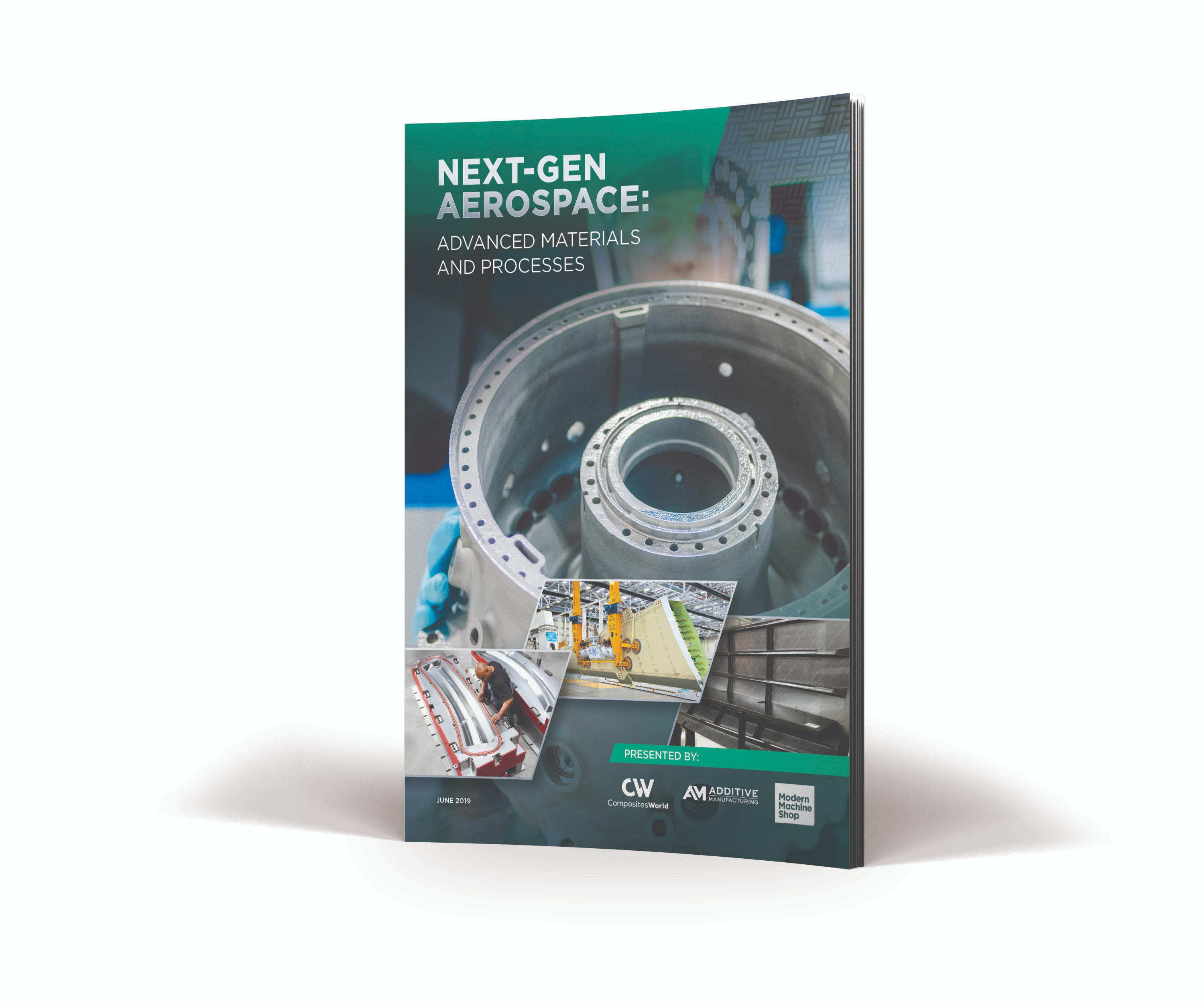
次世代の
航空宇宙製造
商用航空業界は今後20年間で倍増すると予測されており、旅客機と貨物機の需要を満たすには、新しい技術と前例のない製造率が必要になります。
CompositesWorld、Modern Machine Shop のストーリーのコレクションで、次世代航空機を形作る材料とプロセスの詳細をご覧ください。 およびアディティブマニュファクチャリング 、無料で読んだりダウンロードしたりすることができます 。ここで入手してください。
樹脂
- 添加剤:ワイヤーおよびケーブル用途向けの費用効果の高い着色剤
- 薄肉ポリオレフィン包装製造用のパージ化合物
- フラウンホーファーは、熱可塑性複合材料の研究開発のために自動化されたエンゲル製造セルを委託しています
- 少量の航空構造物の自動複合材料製造のための設計
- 熱可塑性テープは、複合エアロストラクチャーの可能性を示し続けています
- AFPと3D印刷を組み合わせて、柔軟な部品生産を実現
- KarlMayerが熱可塑性UDテープの生産ラインを立ち上げ
- CFRP / CMC加工の効率のためのウォータージェットとレーザーの融合
- Broetje-Automationは、連続複合材生産のためのAFPポートフォリオを拡大します
- StyLight熱可塑性複合材料の生産拠点を構築するINEOSStyrolution
- キャスティング プロダクションのトレーサビリティ プラクティス