後壁の再起動:ワンストップ、CFRP部分にテープで牽引
炭素繊維複合材料の自動車用途への現在の進歩の始まりで、メーカーのBMW Group(ミュンヘン、ドイツ)は際立っているように見えました。 M の生産のための樹脂トランスファー成形(RTM)を加速するための初期作業 スポーツモデルの屋根は、その i3 に炭素繊維強化プラスチック(CFRP)部品の完全なサプライチェーンを確立することにつながりました。 および i8 車両、そしてその 7シリーズのマルチマテリアルカーボンコアボディインホワイト(BIW)用のまったく新しい製造および組み立てワークセル 。
BMWは i3 にコミットしました 2009年に大ファンファーレになりましたが、その同じ年に、Audi AG(ドイツ、インゴルシュタット)は繊維強化プラスチックを専門とするテクニカルセンターを設立しました。 2011年、アウディはVoith Composites(Garching、Germany)とのパートナーシップを発表し、CFRP部品を大量に開発および製造しました。翌年、レジントランスファーモールディング(RTM)を使用して作られたCFRP強化鋼Bピラーの開発を発表しました。 SOGEFI(フランス、ギュイアンクール)との提携により、複合コイルサスペンションスプリングを商品化しました。 2012年、アウディは、BMW、フォイトコンポジット、SGLグループ(ドイツ、ヴィースバーデン)などを含むMAIカーボン最先端クラスターの創設パートナーも務めました。
最も注目すべきは、アウディ独自のCFRP開発の物語は、その第1世代の R8 から始まります。 2006年に発売されたスポーツカー。コンバーチブルトップ用のコンパートメントカバーと、レジントランスファーモールディング(RTM)製のサイドブレードを搭載。同社は、美的外観と小さな構造から、アウディ R8 e-tron のモジュラースポーツカーシステム(MSS)に発展しました。 。その電気スーパーカーの主な構造は、アルミニウム鋳造物で結合された押し出しアルミニウムビームで構成されていましたが、リアモジュールが金属フレームの5倍のエネルギーを吸収できるようにする波形クラッシュ構造を備えたトランクインサートを含め、すべてのパネルとインフィルはCFRPでした。
MSSのバックボーンは、後壁です。 、2011年の初期コンセプトから、現在非電気用に製造されているモジュールに進化した R8 SGL Technologies(以前のBENTELER-SGL、Ort im Innkreis、オーストリア。「プラントツアー:BENTELERSGL」を参照)。しかし、アウディはすでに次のステップを計画していました。それは、大量生産の A8 で使用するために後壁を反復することです。 フォイトコンポジットを製造パートナーとする高級セダン。
Voith Compositesは、1867年に設立された多国籍Voith GmbH&Co。KGaAの10年前の子会社です。親会社は現在、19,000人の従業員を擁し、年間収益は42億ユーロ(52億米ドル)で、 4つの部門:Voith Digital Solutions、Voith Hydro、Voith Paper、VoithTurbo。フォイトコンポジットは、製紙に使用されるCFRPロールの製造から、自動車および産業用CFRPドライブシャフト/カルダンシャフトおよびフラットラミネートの製造に発展しました。
2011年、Voith Compositesは、 A8 の製造を目的として、高度に自動化されたCFRPプロセスチェーンの開発に着手しました。 後壁。その核となるのはフォイトロービングアプリケーター(VRA)で、これは35KカーボンファイバートウをZoltek(セントルイス、ミズーリ州、米国)からバインダー付き一方向(UD)テープに広げ、次にカットして積み重ねます。テーラードブランクを形成します。 VRAは、2017年にJECイノベーションアワードを受賞しました。また、その後の予備成形および成形作業のための強固な基盤を確立しました。アウディ A8 の製造に使用された完成したVRAベースのデジタル4.0生産ラインについて、JEC World2018でフォイトコンポジットとアウディの自動車部門の最高の栄誉が再び獲得されました。 後壁モジュール。これらのパートナーは、樹脂サプライヤーのDow Automotive(Auburn Hills、MI、US)およびZoltekと協力して、高性能CFRP部品を大量生産するために必要な材料、プロセス、統合インライン検査システムを開発しただけでなく、完全な製品を作成しました。将来の部品を開発するためにすでに適用されている、不可欠なコンピューター支援設計/製造(CAD / CAM)およびシミュレーションツールのスイート。
効率主導の設計の進化
「私たちは早い段階でアウディと協力し始めました」と、フォイトコンポジットの事業開発責任者であるジャロミールウーファー博士は言います。最優先事項は、新しい A8 を開発することでした。 後壁の設計。部品の製造方法を指示します。
「この製品のエンジニアリングを開始したとき、必要なものがすべて揃った既製の[ソフトウェア]製品を見つけることができませんでした」とUfer氏は説明します。 「そこで、ABAQUSのような設計ツールをまとめましたが、独自のマテリアルカードを作成し、独自のシミュレーション方法を開発しました。」アウディは、 R8 の主要な目標として、BIW重量の減少とねじり剛性の増加をすでに特定していました。 後壁のデザイン(「アウディR8シートウォール:生産への前奏曲」を参照)。 A8 の場合 モジュールでは、マルチコンポーネント MSS を削減するために、統合設計が提案されました。 少数の接着およびリベット留めされたアタッチメントを備えた単一の成形CFRPパネルへのアセンブリ。この設計により、局所的な荷重経路を備えた異方性の高いラミネートの開発が促進されました。これにより、完成した部品は、3〜5個の溶接アルミニウム部品のアセンブリと比較して、重量の50%でドライブセルのねじり剛性の33%を提供できます。
「アウディ A8 の複合プリフォーム 後壁パネルは、6層のベースから、局所的な補強が追加された19層までさまざまです。たとえば、カットアウトや、チャイルドキャリア拘束アタッチメントなどの点荷重がある場合です」とUfer氏は説明します(図2)。
フォイトロービングアプリケーター
Uferは、この設計とVRAの開発が並行して進んだと述べています。 「VRAが提供する設計の自由を持っていることによってのみ、新しい A8 のパフォーマンスが実現しました。 後壁が可能です。」また、繊維サプライヤーのZoltekがプログラムに7年間の価格コミットメントを行ったという事実も重要でした。
VRAのプロセスは、ZoltekのPX35カーボンファイバーのクリールから始まります。 50Kトウの複数のボビンが各VRAラインに供給され、広げられて50mm幅のテープが生成されます。次に、エポキシベースのバインダーが適用されます。このバインダーは、後で複合部品の樹脂トランスファー成形(RTM)中にダウVORAFORCEスナップキュアエポキシマトリックス樹脂と反応します。少量の赤外線(IR)熱を加えてバインダーを溶かし、その後の固化、切断、積み重ねのステップ(ステップ1)でテープをまとめます。
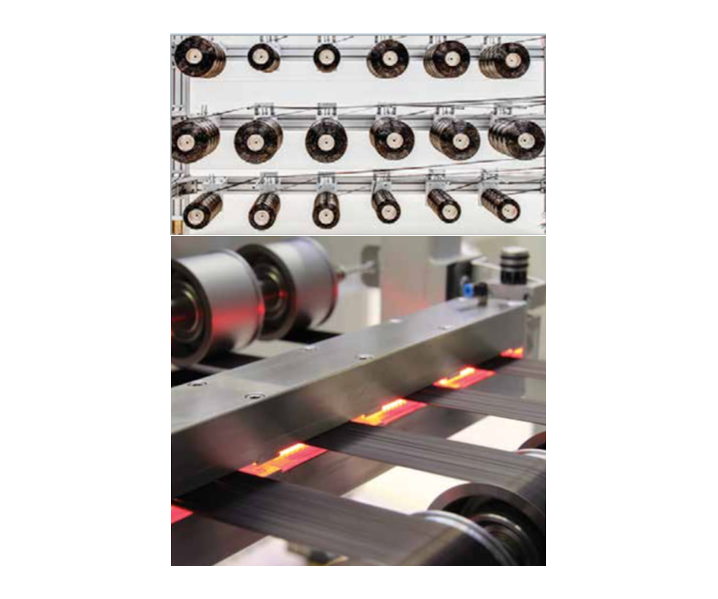
ステップ1:強い> Zoltek50KカーボンファイバートウはVoithRoving Applicator(VRA)に供給され、そこで最初に広げられ、次にエポキシベースのバインダーでコーティングされ、その後IR加熱されてバインダーが部分的に溶融します。
「これは完全に自動化された継続的なプロセスです」とUfer氏は言います。 「何らかの理由で回線を停止する必要がある場合、機器は自動的に反応します。たとえば、テープの過熱による損傷を防ぐために、IRヒーターはすぐにオフになり、引き込まれます。機器にはそのような詳細が何百もあり、このテクノロジーを可能にするデジタル制御があります。」
ステップ2: スプレッドトウテープは、張力がかかった状態で複数のローラーを通過するときに固められます。
バインダーを塗布した後、張力をかけた状態で複数のローラーを通過するときにテープの固化が達成されます(ステップ2)。 Uferは、これも回線のバッファに組み込まれていると説明しています。 「ファイバーの連続的なプルフローを中断するユニットがあり、テープカットアンドプレースメカニズムのパルス形式への移行を提供します。」このガントリーベースのメカニズム テープを調整された長さにカットし、0〜360°の指定された角度で回転台に配置します(ステップ3)。 6〜19層のテープで構成される各調整済みスタックの厚さは、それぞれ1.5〜3.7mmです。
ステップ3: 次に、VRAはテープを切断し、一度に最大4個を回転台に置き、ラミネートスタック内でテープの長さと方向角度の両方を調整します(例:45°/ 90°/ 30°)。
フォイトは4本のVRAラインを設置し(冒頭の写真を参照)、それぞれが一度に最大4本の50 mm幅のテープを適用しますが、Uferは次のように指摘しています。時間。部品のサイズと生産率によって異なります。」
自動化には品質検査が含まれます。テープとプリフォームのスキャンは、拒否アルゴリズムと比較されます。 「VRAがテープを100%スキャンすることで、生産ライン全体に適切な繊維の分配が保証されます」とUfer氏は説明します。 「また、サーモグラフィーとレーザーセンサーを使用して、指定された領域のプリフォームをチェックします。」その後、VRAは検出した問題に対応できます。 「1つのテープが正しくない場合、VRAは不足している長さを切り取り、それを置き換えるために別のテープを作成します」と彼は指摘します。トレーサビリティのために、完成したプリフォームにQRコードが配置されます。 (QRコードは、RFID(Radio Frequency Identification)タグよりも好まれます。これは、樹脂注入プロセスに対する耐性が高いと報告されているためです。)
成形、成形、組み立て
2DスタックはVRAを出て、生産ラインの成形、成形、組み立てセクションにシャトルされます。複合材自動化のスペシャリストであるFILL(オーストリア、グルテン)が提供する最初のプレスは、熱と圧力を使用して2Dテープスタックを3Dプリフォームに成形します(ステップ4)。 Uferは、プリフォームの厚さと形状が異なるため、成形ツールにクランプされたプリフォームの個別の領域をスタンプ成形するときに、プレスが加えられる圧力に適応できると説明しています。 ALPEX Technologies(Mils bei Hall、オーストリア)は、Voith Compositesによって提供された設計に基づいて、マッチドスチールRTM金型を作成しました。 「私たちは事実上、工具とプレスのプロセスを開発しました」とUfer氏は言います。 「実際のテストループは必要ありませんでしたが、 A8 を加工する前に、他の形状や部品のシミュレーションモデルを検証および検証しました。 後壁製造ツール。この成形プロセスのシミュレーションは、実際の生産に直結し、最適化のスピードアップに役立ちました。」
ステップ4 :テープスタックはプレスにシャトルされ、そこで最終的な3Dパーツ形状に成形されます。
プレスを数秒間保持して粉末バインダーを反応させ、形状を設定します。その結果、樹脂注入中の繊維洗浄に耐えることができる安定したプリフォームが得られます。 「バインダー粒子は、繊維を離して保持し、RTM中の樹脂の流れを改善する役割も果たします」とUfer氏は述べています。 「これは、樹脂の流れを助けるためのプリフォームにステッチがないため、これらのバインダー粒子がマイクロフローチャネルとして機能するため便利です。」
成形されたプリフォームは、次にロボットによってEiMa Maschinenbau GmbH(Frickenhausen、Germany)CNCセルに転送され、そこで超音波ナイフが外側の最終輪郭をトリミングします。次に、ENGEL(Schwertberg、オーストリア)が提供するRTMプレス(ステップ5)にロボットで配置されます。ライン内のすべてのロボットは、KUKA Robotics(ドイツ、アウグスブルク)から供給されています。
ステップ5: 成形されたプリフォームは350kNのプレス機に入れられ、ultra-RTMを使用して成形されます。
A8 の成形に使用されるRTMプロセス 後壁は、以前の R8 のためにアウディライトウェイトセンターで開発されたものと同じです。 後壁、ultra-RTMと呼ばれます。高速射出、低圧で大きな部品の成形が可能です。 HP-RTMの典型的な140バールと比較して、アウディのウルトラRTM中のインモールド樹脂射出圧力 A8 後壁は15バール未満で、 R8 よりもさらに小さくなっています。 。その結果、2,500 kNのプレス力の代わりに、350kNしか必要ありません。したがって、より小型で安価な印刷機を使用して、高品質で繊維量の多い部品を製造できます。
VORAFORCE 5300エポキシ樹脂は、離型を含む3成分系で、120°Cで90〜120秒で硬化し、処理粘度は20cpsです。 A8 の場合 後壁では、1.3 kgの樹脂ショットがプリフォームに注入され、120秒の硬化が続きます。
硬化した部品はロボットで型から外され、カットアウトの機械加工のために閉じたCNCフライス盤にロードされます。次に、粉砕された部品を自動洗濯機に入れて、残っているCFRPダストを取り除きます。
洗浄された後壁は、2台のロボットを備えた組立セルに移されます。最初のロボットは、成形部品を自動リベット打ち機に配置します。自動リベット打ち機は、リベットの取り付け中に加えられた力を記録します。これは、プロセス全体に組み込まれている製造インテリジェンスの一部であり、各パーツのデジタル処理レコード(つまり、デジタルスレッド)に追加されます。 次に、パーツがボンディング領域に移動され、2番目のロボットが自動溶剤ワイプを使用してボンディング用の領域を準備します。次に、同じロボットが、3液型エポキシと互換性のある速硬化性の2液型Dow BETAFORCE 9050Mポリウレタン構造用接着剤(ステップ6)を塗布します。次に、部品をオーブンに入れて、短い接着剤硬化サイクルを行います。
ステップ6: BETAFORCEポリウレタン接着剤は、接着されたアタッチメントにロボットで塗布され、短いオーブンサイクルで硬化します。
この生産ラインは、完成した部品のサイクルタイムを5分に維持し、部品の現在の需要は1つまたは2つの8時間シフトで満たすことができます。 3Dレーザースキャンデバイスは、部品の3D形状と測定値をチェックするために定期的に使用されます。完成した部品は、アウディ A8 に出荷するために準備されます。 ドイツのネッカーサルムにある最終組立ライン。道路で約3時間の距離にあります(ステップ7)。
ステップ7: 完成した部品は、アウディA8の最終組立ラインに出荷する準備が整います。
ファイバーの直接配置=将来の柔軟性
すべての投資を行った結果、フォイトコンポジットがこの事業を保証されていなかったことを知って驚くべきことですが、実際に同社は開発を完了し、競争入札プロセスに参加して生産を勝ち取りました。 「アウディが定義した目標部品コストと、品質および部品性能の要件を満たすことができました」とUfer氏は言います。かなりの数の企業がこのプログラムに参加したことを考えると、これは決して小さな偉業ではありませんでした。
Voith Compositesは、そのプロセスの複数の部分について特許を取得しています。 「VRAは、テープの直接ファイバー配置[DFP]を使用した工業化を実証しました。これにより、高度に最適化されたレイアップによって使用されるスクラップや材料が削減されます」とUfer氏は言います。また、最も費用効果の高い材料である未処理のヘビートウファイバーとパウダーバインダーを使用しています。その第2世代のプロセスは、粉末バインダーを樹脂の直接塗布に置き換え、より多くのプロセスステップを排除します。ただし、同社は、Voith LongfiberPreformerやVoithPrepregWindingなどの他のDFPプロセスを開発しました。
「私たちは、大量の自動車の連続生産のための炭素繊維部品の新しい基準を設定しています」と、フォイトコンポジットのマネージングディレクターであるラースハーベック博士は述べています。 「私たちが設立したスマートファクトリーは、CFRPコンポーネントの自動生産を、ほぼすべての形状や個々のロットサイズを含む、新しいレベルの効率と柔軟性にもたらします。」これは確かに、業界が向かっているところです。
樹脂