射出成形における 4 つの最大の設計ミス
多くの企業は、射出成形サービスを利用して、コスト効率の高い方法で大量の同一部品を製造しています。プラスチック射出成形では、加熱されたバレル内で熱可塑性樹脂を溶融してから、加圧ノズルを介して溶融材料を耐久性のある精密な金型に射出します。材料が冷えて固まると、部品が取り出され、プロセスが繰り返されます。企業は、この製造プロセスを使用して、電子機器の筐体からウォーター ボトルまで、あらゆるものを製造しています。
射出成形は複雑なプロセスであり、1 つのミスが外観上の欠陥の原因となり、製品の完全性が損なわれ、費用のかかる再設計につながる可能性があります。幸いなことに、設計のベスト プラクティスに従う限り、これらの問題のほとんどは回避可能です。射出成形用の部品を設計する際に注意する必要がある最も一般的な 4 つの間違いを次に示します。
射出成形でよくある 4 つの間違いとその解決方法
1.アンダーカットのある設計
アンダーカットとは、金型からの部品の突き出しを妨げる凹面、突起、溝、オーバーハング、ねじ山、スナップ フィット、またはその他の機能です。アンダーカットは、製造コスト、部品の複雑さ、および金型のメンテナンス要件の増加につながる可能性があるため、潜在的なアンダーカットを可能な限り排除することをお勧めします。
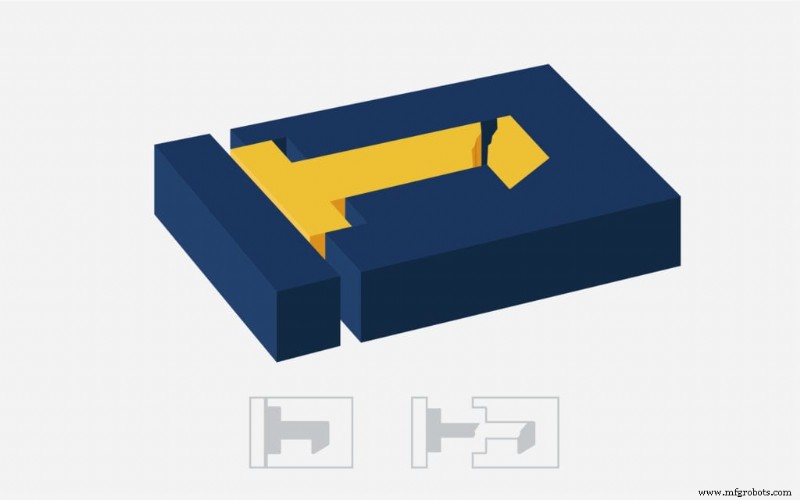
パーツの設計に不可欠なアンダーカットがある場合、パーツの突き出しを改善する方法がいくつかあります。問題のあるフィーチャの向きを変更して、描画ラインと平行になるようにすることは、費用対効果の高いソリューションです。これにより、損傷を受けることなく部品を突き出すことができ、アンダーカットがなくなります。内部アンダーカットまたは抜き勾配のない面を持つパーツがある場合は、リフターを使用して取り出しプロセスを容易にすることもできます。パーツの穴とスロットを巧妙に設計することで、アンダーカット フィーチャを形成できる場合があります。Fast Radius エンジニアがガイドします。
2.不均一な肉厚
肉厚が均一であることにより、溶融プラスチックが金型キャビティを一方向に流れやすくなり、材料がキャビティをより正確に充填できるようになります。ただし、薄い壁は厚い壁よりも速く冷却されるため、壁の厚さの違いにより、ヒケ、反り、ショート ショットなどが発生する可能性があります。
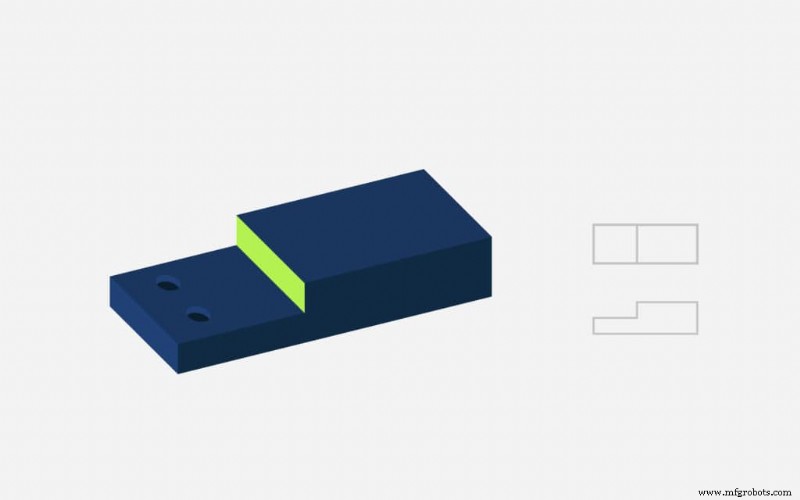
これらの問題を回避し、成形品のすべての領域が同じ速度で冷却されるようにするには、一貫した肉厚を使用します。ほとんどの場合、壁の厚さは 1.2mm ~ 3mm が最適です。さまざまな厚さの壁が必要な場合は、次のことを行う必要があります。
- 薄い部分から厚い部分への移行はできるだけ緩やかに行う — 設計のベスト プラクティスは、肉厚を変更する代わりにコアリングとリブを使用するか、必要に応じて変更を最小限に抑えることです。
- 正しいリブとボスの厚さを使用 — リブとボスは、ベースの半径が壁の厚さの 25 ~ 40% で、ベースの壁の厚さの 40 ~ 80% を超えてはなりません。
- 最も厚い部分からプラスチックを取り除きます — これはコアリングと呼ばれ、壁のセクションを均一に保つのに役立ちます。
3.抜き勾配を忘れる
スムーズな突き出しには、成形品の各垂直面にわずかなテーパーを付けて抜き勾配を付けることが不可欠です。ドラフトなしで設計されたパーツは金型にくっつく可能性があり、抜き勾配がないと、突き出し時にパーツの垂直壁が金型をこすった場合に見苦しい引きずり線が発生する可能性があります。緩やかなテーパーを追加することで、部品を摩擦から保護し、均一な仕上げを確保し、突き出し中の摩耗、裂傷、反りを減らすことができます。
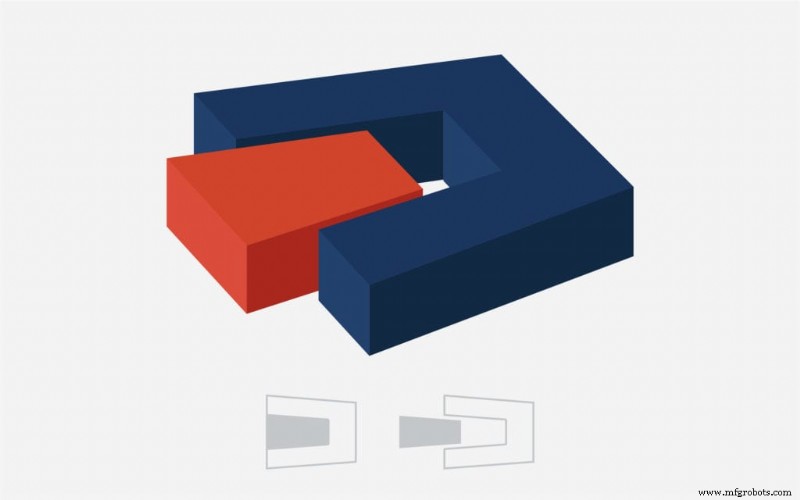
抜き勾配の角度は、壁の厚さから表面の質感まで、いくつかの要因によって異なります。適切なドラフト角度を決定するには、材料の収縮率、部品の最終用途の機能、絞りの深さを考慮する必要があるため、経験豊富な製造パートナーに連絡して正確な評価を得ることが最善です。原則として、少なくとも 1.5 ~ 2 度の抜き勾配を使用し、キャビティの深さ 1 インチごとに 1 度を追加する必要があります。パーツの表面のテクスチャが多い場合は、引きずり線を防ぐために 5 度の抜き勾配が必要になる場合があります。
4.鋭い角を含む
シャープなエッジやコーナーは、充填するのにより多くの圧力を必要とするだけでなく、突き出し中に部品が金型にくっつく原因となることがよくあります。また、角が鋭いとショットが金型を通過しにくくなるため、真空ボイドや気泡が閉じ込められる領域が発生する可能性があります。これらは外観上の損傷を引き起こし、応力集中を増大させ、パーツの故障につながる可能性があるため、可能な限り内側と外側のエッジとコーナーを丸くすることが重要です。
コーナーを設計するときは、壁の厚さが一定になるようにコーナーをモデル化することを忘れないでください。つまり、内側のコーナーは肉厚の 50% にフィレットされ、外側のコーナーは 150% になります。
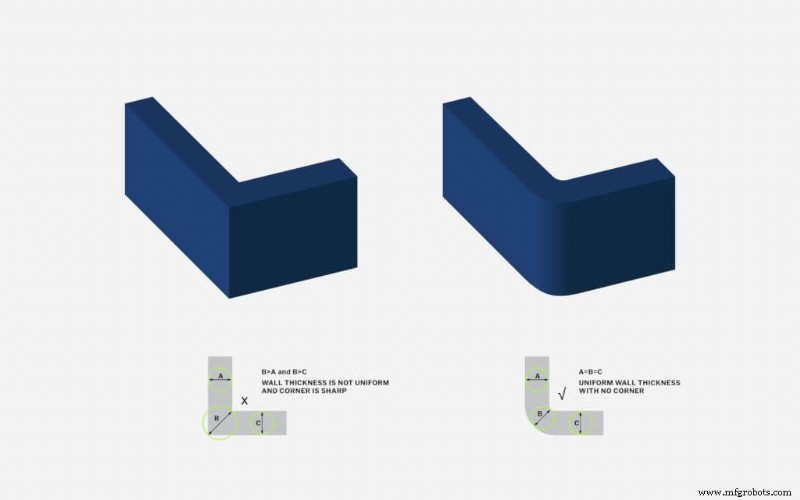
Fast Radius で射出成形部品の欠陥を防止
射出成形の設計ミスにより、生産が数週間遅れたり、コストが増加したり、部品が標準以下になったり、使用できなくなったりする可能性があります。プロジェクトの開始時に時間をかけて慎重に設計を決定することは不可欠であり、長期的には時間とお金を節約できます。ただし、覚えておくべきことがたくさんあるため、Fast Radius のような経験豊富な射出成形パートナーと連携することで、最初から適切な設計を行うことができます。
Fast Radius と提携すると、製造プロセス全体を通じて支援できるエンジニア、アドバイザー、および設計専門家のチームにアクセスできます。ドラフトを設計に微妙に組み込む場合でも、適切な肉厚を決定する場合でも、Fast Radius は可能な限り最良の部品を設計するのに役立ちます。次の射出成形プロジェクトの設計を開始するには、今すぐお問い合わせください。
もっと知りたいですか?リソース センターをチェックして、材料の選択、1 個取り金型と複数個取り金型を使用する場合などについて詳しくお読みください。
Fast Radius でパーツを作成する準備はできましたか?
見積もりを開始する産業技術