このチェックリストを使用して、射出成形設計が生産準備が整っていることを確認してください
射出成形により、同一部品を低価格で大量生産できます。このプロセスでは、溶融した材料を加圧ノズルから耐久性のある金型に注入し、材料が固まったら部品を取り出し、これを繰り返します。水筒、プラスチック製のおもちゃ、電子機器の筐体など、さまざまな日用品が射出成形で作られています。射出成形で使用される最も一般的な材料は熱可塑性樹脂と熱硬化性樹脂ですが、金属も射出成形できます。
射出成形で部品を作成する場合、最終製品の品質と機能に影響を与える多くの変数を考慮する必要があります。フロー ライン、ヒケ、反りなど、射出成形部品が失敗する原因は多数ありますが、いくつかの重要な設計原則に従うことで、ほとんどの問題を回避できます。
Fast Radius では、お客様の射出成形部品に日々取り組んでいます。エンジニアは、効果的に作成する前に調整が必要な優れた部品設計を頻繁に私たちにもたらします。当社の製造設計 (DFM) の専門家は、何千もの部品設計を評価および調整し、最も一般的な問題を特定してまとめました。設計におけるこれらの一般的なエラーを修正することで、コストのかかる間違いを防ぎ、設計の修正にかかる時間を大幅に節約できます。
射出成形する部品の設計を送信する前に、次の設計規則のリストと照らし合わせて確認してください:
適切な抜き勾配を使用する
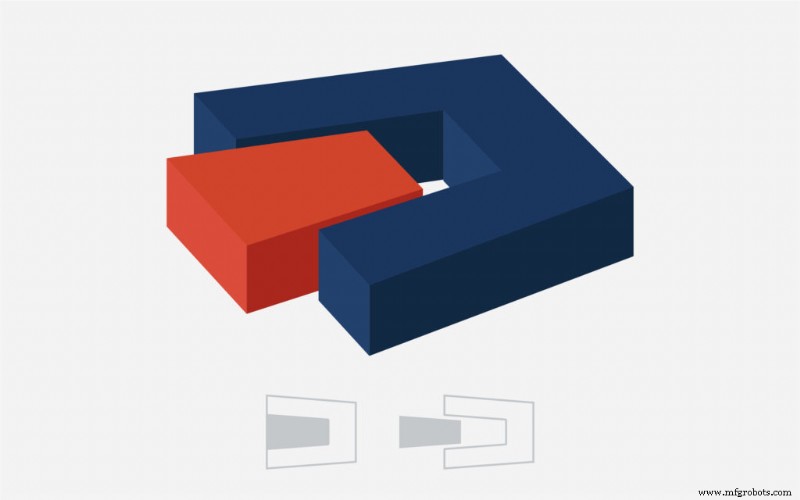
通常、1.5 ~ 2 度のドラフトは、ほとんどのパーツで安全な最小値です。
ドラフト角度とは、射出成形部品の表面に追加された緩やかなテーパーを指し、引っ張る方向に合わせて、摩擦や吸引による損傷を受けることなく金型から部品を取り外すことができるようにします。
パーツに必要な抜き勾配は、肉厚、パーツの材料の収縮率、絞りの深さ、製造後のパーツの表面仕上げやテクスチャリングが必要かどうかなど、いくつかの要因によって異なります。パーツの深さが 1 インチ増えるごとに平均ドラフトが 1 度増加するはずですが、通常、ほとんどのパーツでは 1.5 ~ 2 度のドラフトが安全な最小値です。
可能であれば、壁の厚さを均一に保つ
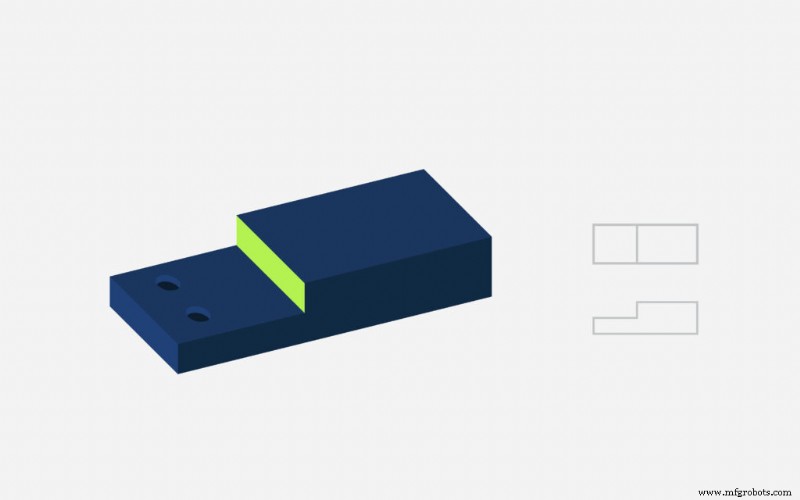
可能であれば、射出成形部品は部品全体で均一な肉厚を持つ必要があります。肉厚が異なると、射出された材料の冷却速度が異なり、ヒケ、ボイド、反りが発生する可能性があります。
一般的に、壁の厚さは 1.2mm から 3mm が理想的です (ただし、材料によって多少の変動が予想されます)。壁が厚いと生産サイクル時間が長くなり、部品の機械的特性に悪影響を及ぼす可能性があるため、壁の厚さはほとんどの場合 5 mm 未満に抑える必要があります。
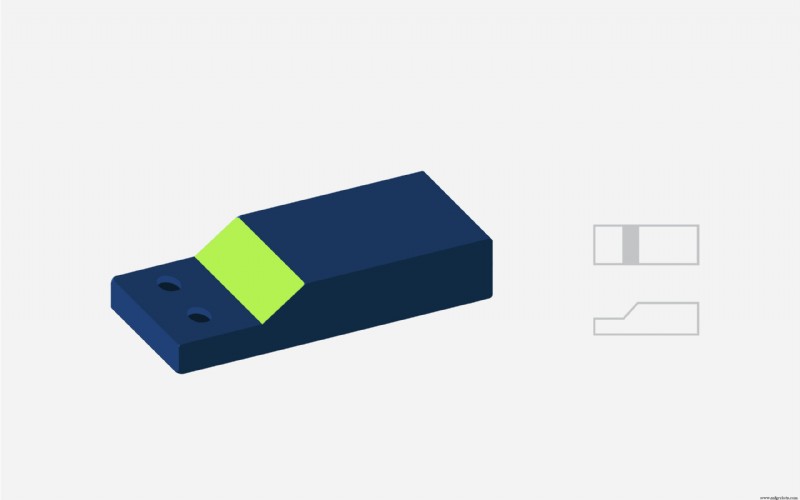
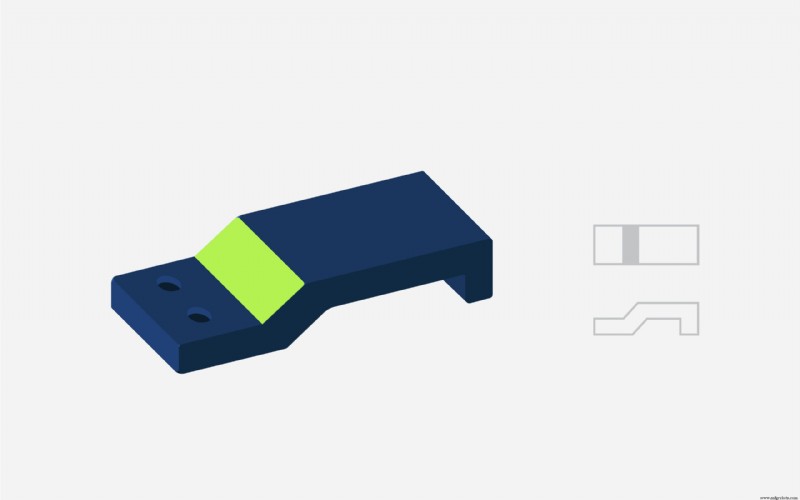
パーツの肉厚を変える必要がある場合は、セクション間の移行をできるだけ緩やかにする必要があります。これを行うには、成形品の設計に面取り (傾斜したコーナーまたはエッジ) またはフィレット (丸みを帯びたコーナーまたはエッジ) を組み込みます。これにより、溶融プラスチックのショットが金型を完全に充填し、完全かつ均一に冷却され、反りや歪みが防止されます。 -均一な収縮。
原則として、壁の厚さが異なるセクション間の移行の長さは、壁の厚さの変化の 3 倍にする必要があります (たとえば、壁の厚さが 1 mm 減少した場合、移行は 3 mm にわたって発生する必要があります)。
アンダーカットを避ける
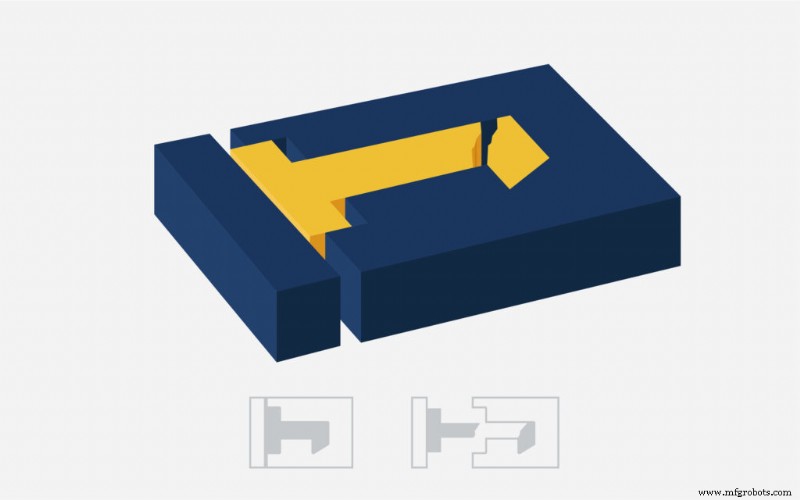
アンダーカットとは、ねじ山、溝、スナップ フィットなどのくぼんだ、または突き出た表面またはフィーチャであり、部品を金型から 1 回、一方向に引っ張っただけでは、損傷することなく突き出すことができなくなります。フィーチャをドロー ラインと平行に配置するか、金型設計にアクションを組み込むことで、アンダーカットを回避することができます。
シャープなエッジと角を丸くする
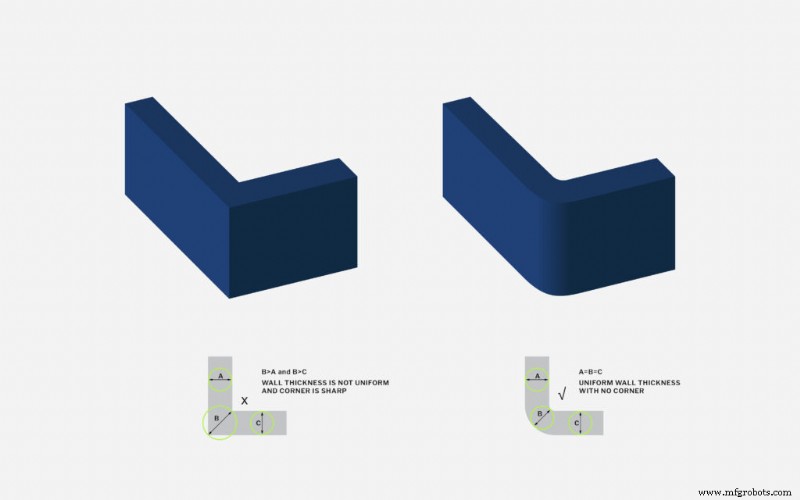
デザイナーやエンジニアは、可能な限り、鋭いエッジや角ではなく、丸い形状を選択する必要があります。エッジは、充填するために追加の圧力を必要とするため、ショットが効率的かつ均一に金型に流れ込むことが難しくなります。また、鋭いエッジは、突き出し時に金型にくっつく傾向があり、部品の損傷や欠陥のリスクを高めます。これらの問題は、内側と外側の角を丸くすることで回避できます。
内部コーナー、または一部の壁が床と接するコーナーは、隣接する壁の厚さの少なくとも 50% の半径を持つ必要があります。プラスチックがより効率的かつ効果的に流れるように、外側の角、または成形品の壁の上部にある角は、隣接する壁の 150% の半径にする必要があります。これは、残留応力と亀裂を最小限に抑えるのにも役立ちます。
パーツ内のすべての垂直フィーチャ (ボス、リブ、スナップ フィットなど) のベースも丸くする必要があります。ボスの半径は隣接する壁の 25%、最小半径は 0.015 インチ (または 0.381 mm) である必要があります。
パーティング ラインを戦略的に配置する
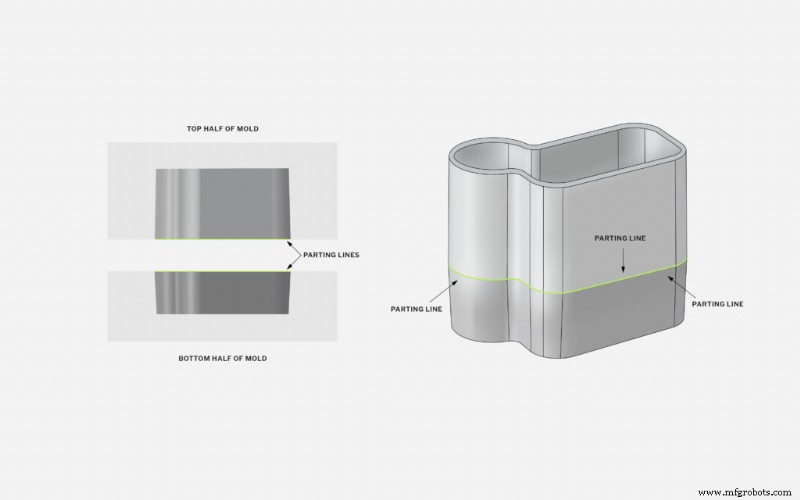
パーティング ラインとして知られる物理的なマークは、金型の 2 つの半分が交わる場所に現れます。多くの場合、パーティング ラインは簡単に見たり感じたりすることができますが、美的な問題以上のものです。パーティング ラインの配置は、金型がどのように開くか (したがって、パーツのフィーチャに抜き勾配を追加する必要がある方向) を決定し、金型ツールのコストと必要な後処理の両方に影響を与える可能性があります。
多くの場合、パーティングを平面ではなくエッジに沿って長く配置することで、パーツの外観と機能を改善できます。これにより、継ぎ目を隠すことができ、バリ (金型が一緒になる場所の周りに過剰な材料) の可能性も減少します。
エジェクタ ピンの配置を考慮する
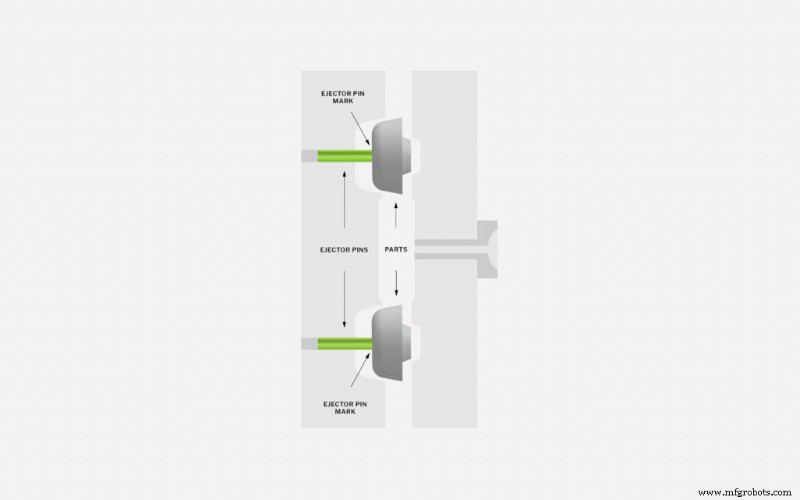
エジェクタ ピンが正しく機能するには、ピンの移動方向に対して垂直に配置された平らな面またはパッドが必要です。ピンの配置と数は、部品の形状、抜き勾配、側壁のテクスチャ、および壁の深さによって通知される必要があります。これらはすべて、部品が金型の壁にどのようにくっつくかに影響します。
材料の選択は、ピンの配置またはサイズにも考慮する必要があります。たとえば、粘着性の高いレジンは、取り出すのにより大きな力を必要とする傾向があります。同様に、より柔らかいプラスチックは、突き出す力を効果的に分散させ、部品の損傷を避けるために、より多くのピンまたは幅の広いピンが必要になる可能性があります。
サポートリブのサイズを最適化
リブは、2 つの部分壁が 90 度の角度で接している場合や、特定の部分の長さが部分の壁の厚さによって弱まっている場合に、部分壁を強化するためによく使用されます。
リブが厚いからといって必ずしもサポートが向上するわけではないことに注意することが重要です。実際、リブが厚すぎるとヒケが発生することがよくあります。支持リブのベースの厚さは、隣接する壁の厚さの最大 3 分の 2 にする必要があります。
金型の肉厚に注意してください
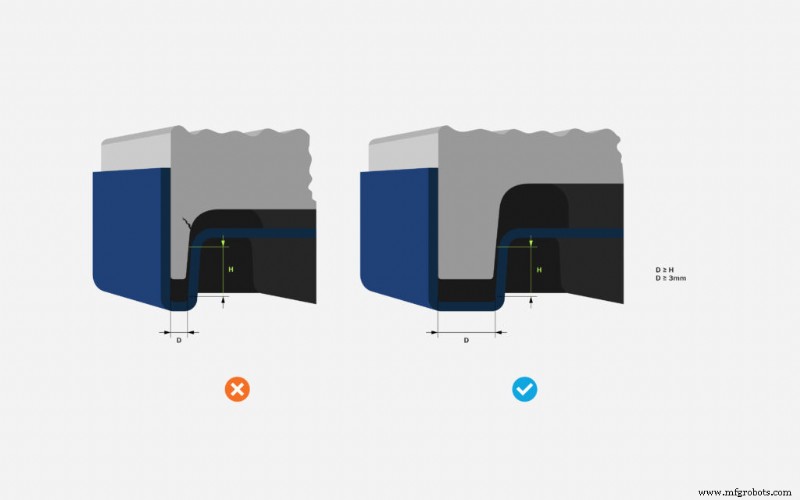
金型の壁の厚さは、もう 1 つの重要な考慮事項です。これは、主に部品フィーチャ間のスペースによって決まります。冷却プロセスが複雑になるため、リブやボスなどの垂直フィーチャが互いに近すぎたり、壁を分割したり、薄い領域に近づきすぎないようにしてください。
金型の肉厚も金型コストに影響を与える可能性があります。大多数の射出成形金型は CNC 機械加工によって作成され、金型内の金属の薄い壁は適切に工具を使用することがより困難になります。肉厚が薄いと、金型のライフ サイクルも短くなります。
金型の肉厚の許容最小値は部品材料の物理的および機械的品質によって決まりますが、一般に、部品フィーチャ間の 3 mm のクリアランスは許容されます。
効率的かつ効果的な射出成形部品の設計
設計ミスは高くつきます。設計エラーを修正するためにツールを作り直すと、製品チームは数週間遅れ、数千ドルの費用がかかる可能性があります。優れた製造パートナーは、DFM によるコストのかかる改訂を回避するのに役立ちますが、そのプロセスはタイムラインにも追加されます。製造パートナーに提出する前に、このガイドの問題について設計をチェックすると、より良い部品をより早く入手するのに役立ちます。
射出成形ではうまくいかないことがたくさんあります。そのため、信頼できるパートナーを見つけて部品を正しく作成する必要があります。ここ Fast Radius では、お客様の作業をより簡単にするためにここにおり、お客様のプロジェクトの成功に投資しています。次の射出成形プロジェクトを開始するには、今すぐお問い合わせください。
材料の選択から、1 個取り金型と複数個取り金型の違い、COVID-19 の蔓延に対抗するフェイス マスクを製造するプロセスをどのように活用したかなど、射出成形の詳細については、Fast Radius ラーニング センターにアクセスしてください。 .
Fast Radius でパーツを作成する準備はできましたか?
見積もりを開始する産業技術