最新の CNC は難しい作業を簡単にこなす
CNC はますます高速化、スマート化され、使いやすくなっています
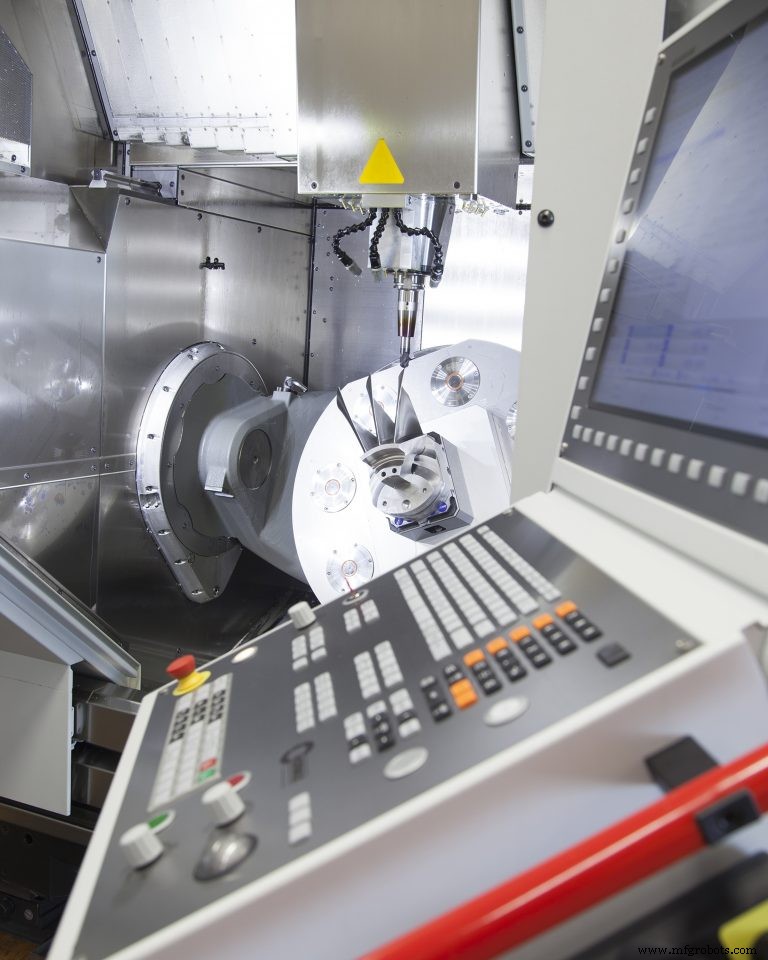
それは決して言葉にすることのない工作機械の頭字語です:CNC。そして多くの場合、「コンピュータの数値制御」を魔法を行うブラック ボックスと見なしても問題ありません。しかし、高速加工に苦労している場合、より良い表面仕上げまたはより高い精度が必要な場合、トレーニングと保持の問題がある場合、または生産効率を改善したい場合、答えはこれら 3 つの小さな文字の最新の反復である可能性があります。
スピードが必要なのは誰?
すべてのコンピューター関連と同様に、CNC は常に高速化しています。目のくらむような仕様の配列からいくつかの例を挙げると、Heidenhain は 0.5 ミリ秒以内にプロセス データ ブロックを制御し、Siemens SINUMERIK 840D sl は最大 31 の軸と 10 の加工チャネルを単一のプロセッサで制御でき、パルスファナックの最新のドライブとモーターでは、1 回転あたり最大 3,200 万回のカウントが可能です。誰がこの種の力を必要としていますか?
まず、複数の軸を同時に動かそうとする人、特に素早く動かす必要がある場合。 Fagor Automation-USA (イリノイ州エルク グローブ ヴィレッジ) のシニア アプリケーション エンジニアである Tom Maxwell 氏は、「より高速な高速 5 軸ルーターは一般に、より多くの処理能力を必要とする航空宇宙での複合材料の使用の増加を特に指摘しました。また、高性能マシニング センターでの 5 軸によるアルミニウムの高速加工の必要性も認識しています。」
または、ハイデンハインの TNC ビジネス開発マネージャーである Gisbert Ledvon 氏は次のように述べています。ツールではなく、チップに熱を伝達する必要があります。しかし、制御が遅すぎて CAD/CAM システムまたはポストプロセッサからのデータを管理できない場合、一定のチップ負荷を保証できず、ツールがすぐに燃え尽きてしまいます。また、同じ表面仕上げや精度も得られません。スピンドルを 80 ~ 100,000 rpm の高回転数で稼働させるには、チップ負荷を一定に維持するために、より高速な制御も必要です。 CNC は、これらの分野で成功するための大きな要素です。」
ミルターン マシンやフライスと研削の両方を行うマシンなど、加工方法を組み合わせたマシンも、超高速プロセッサの必要性を高めています。 「たとえば、部品がフライス盤のテーブルの中心に置かれておらず、旋盤加工を行う場合、回転軸だけでなく、すべての軸で動きがあります」と Ledvon 氏は言います。
Siemens Industry Inc., Digital Factory Division, Machine Tool Business (イリノイ州エルク グローブ ヴィレッジ) のビジネス デベロッパーである Steve Holmes 氏は、別の例を追加しました。 SINUMERIK 840D コントロールには、「Run My Robot」と呼ばれる機能があり、別のロボット用の別のコントロールまたは PLC が不要になります。コントロールは単に別のチャネルをそのタスク専用にします。
一方で、コントロールから得られると思われる速度が別のコンポーネントによって妨げられないように注意してください。 FANUC America Corp. (イリノイ州ホフマン エステーツ) の全国セールス マネージャーである Jody Michaels 氏は次のように説明しています。それは問題ありませんが、CPU の処理速度とドライブとモーターが迅速に応答しなければ、どれだけ先を見据えていても意味がありません。 John Deere 社のトラクターに 1000 馬力のモーターを搭載することはできますが、それは時速 150 マイルで走行できるという意味ではありません。システム全体が必要です。」
速度の話題を離れる前に、最新のほとんどの CNC には、一般に「適応送り制御」と呼ばれる機能が含まれていることに注意してください。これは、測定されたスピンドル負荷を使用して切削速度を調整します。たとえば、「空気」を切断している場合、コントロールは自動的に設定した最大速度まで送り速度を上げます。工具が切り込みに埋もれている場合、コントロールは送りを遅くして一定の安全なトルクを維持します。すべてオンザフライ。 Ledvon 氏が見ているように、この機能は「無人加工とトロコイドミリング」に特に適しています。予測される材料除去量に基づいて加工速度を調整する CAD/CAM パッケージをさらに最適化します。」
より高い精度、より良い仕上がり
すでに提案したように、高度な制御は、運動学的な複雑さと複数のプロセスを処理する機能、またはより高速に機械加工する機能以上のものを提供します。おそらく最も重要なことは、金型や金型、およびこれらの要素が重要なその他のアプリケーションで、より高い機械加工精度と改善された表面仕上げを提供することです。 Fagor に代表される一般的なアプローチの 1 つは、デジタル モーターのエンコーダーと別のアブソリュート リニア エンコーダーの両方を使用して制御に通知するデュアル フィードバックです。 Maxwell 氏は、これにより「より高い精度を実現しながら、滑らかな動きを維持できる」と述べています。
機械メーカー Hurco (インディアナポリス) のパス プランニング、フロントエンド設計、R&D 担当マネージャー、Paul J. Gray 氏は、同社の WinMax コントロールには、特許取得済みの UltiMotion 公差ベースの制御アルゴリズムをサポートするためにより多くの処理能力が必要であると述べました。 4 軸および 5 軸加工のサイクル タイムを短縮します。しかしそれ以上に、Hurco の新しい 5 軸マシンは、UltiMotion の高い動的応答を最大限に活用してより滑らかな表面仕上げを実現するダイレクト ドライブの回転軸トルク モーターを備えています。
「アルゴリズム」について言及すると、現代の CNC はブラック ボックスであるという一般的な認識に戻ります。実際、加工プログラムで定義された動作を単に実行するだけでなく、高度なプログラムがバックグラウンドで実行されていることがよくあります。
主な例は、CAD/CAM ポスト プロセッサから出力されるスプライン カーブの再解釈です。レドボンが説明したように、このような等高線は通常、特定の曲線の半径のすぐ外側にある点を持ちます。
「このような輪郭に沿って機械を強制的に点から点へ移動させると、加工物に振動やゲージング マークが発生する可能性があります。ハイデンハインの制御では、数ミクロンの帯域幅を確立し、機械がプログラムされた輪郭の周りのこの許容範囲内でスムーズに動くようにすることができます。制御は、精度を維持しながら、輪郭の形状に応じて速度と送りも最適化します。」 Heidenhain はこの機能を Advance Dynamic Prediction (ADP) と呼び、高度な制御では一般的です。たとえば、FANUC はそのバージョンを Smooth Tolerance Control と呼んでいます。
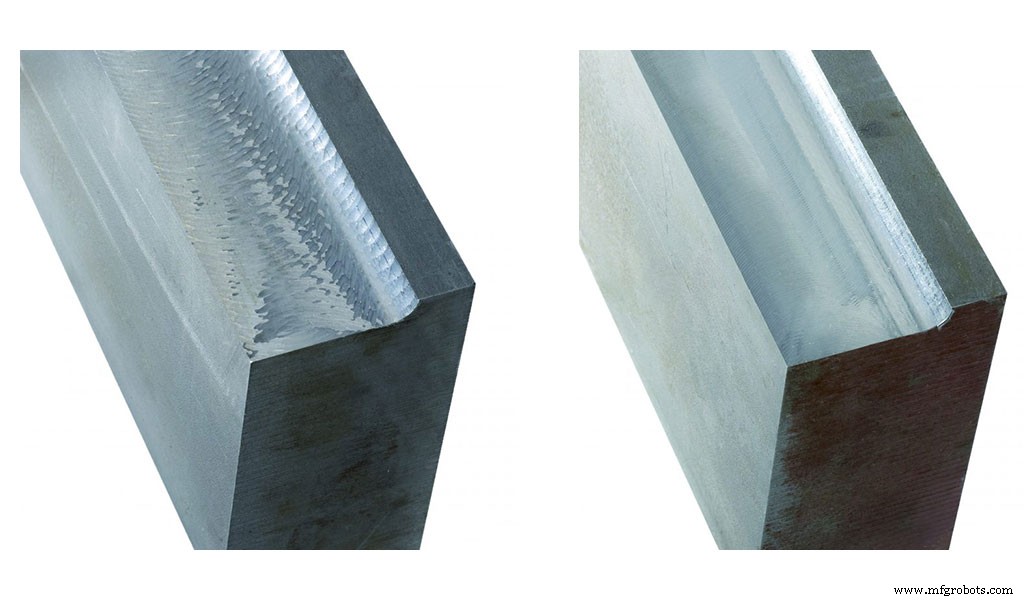
Heidenhain の Adaptive Chatter Control (ACC) のように、固有の機械エラーを修正する機能も多数あります。 「私たちは工作機械メーカーと協力して、機械で振動がどのように発生するかを判断します。これは機械によって異なるためです」と Ledvon 氏は述べています。 「そして、そのような高調波が発生したときに制御がどのようなアクションをとるべきかを決定しますが、これもマシンごとに異なります。工作機械メーカーはこのデータを PLC に入力し、PLC が制御にフィードバックすると、自動的に実行されます。」
ハイデンハイン、ファナックなどにも、工具先端点での加速度による位置誤差を補正する機能があります。たとえば、Ledvon 氏によると、質量と慣性により、制動中および加速中にピッチング動作が発生し、位置エンコーダーによって認識されない位置エラーが発生する可能性があります。
エラーは、ガイドウェイの剛性、送り力の作用点と質量の中心との間の距離、および質量の中心とツールの中心点との間の距離に部分的に依存します。そのため、ハイデンハインは機械メーカーと協力して機械の仕組みを理解し、その理解に基づいて計算を行い、これらの加速度エラーを修正します。 Ledvon 氏は、このような調整は数ミクロンにすぎないため、用途によっては必ずしも必要ではない可能性があると付け加えました.
ファナックの用語は、工作機械メーカー、つまりユーザーが利用できるようになった魔法のように見える追加機能のいくつかをよく理解しています:スマート スピンドル加速/減速、スマート送り速度加速/減速、スマート バックラッシュ補正、スマート サーマル コントロール。
Michaels 氏は、Smart Spindle Acc/Dec はエネルギー コストの節約にも役立つと指摘しました。これは、CAD/CAM プログラムがスピンドル速度の大きな変化を出力することが多く、そうでなければ必要以上に多くの電力を消費するからです。しかし、これらの機能のほとんどの主なメリットは、より優れたパーツを製造することです。または、彼が要約したように、「今日の公差制御と当社のモーターとドライブの高応答により、バックグラウンドで多くのことが行われているため、機械加工された部品は洗練された仕上げのように見えます。」
HMI の進歩
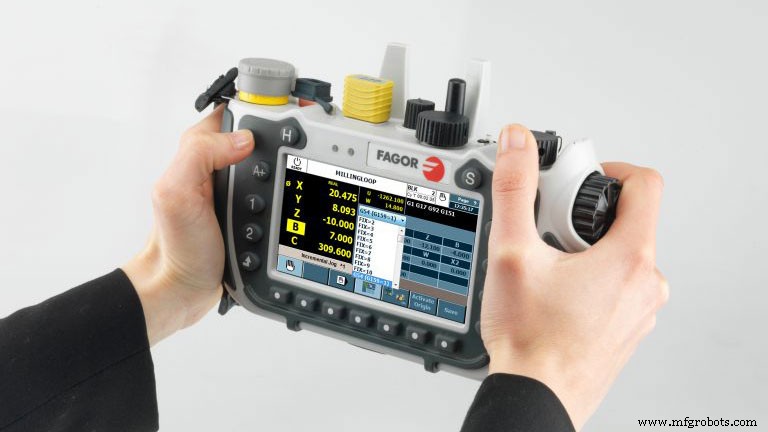
ご想像のとおり、ヒューマン/マシン インターフェイス (HMI) の最近の進歩には、アイコン駆動型のデザインと、スマートフォンで普及した種類の指先コントロール (画像を縮小するためのピッチ、拡大してズームするなど) が含まれます。ユビキタスな HMI を 25 年間あまり変更していなかった FANUC でさえ、Michaels 氏が「非常に異なるインターフェイス」と表現したものを提供しています。ツールデータ、プログラムの編集、メンテナンスなどのさまざまなアイコンが並んだ、ファナックの画面とはまったく異なるホーム画面。別のベンダーのプログラミングアプリを追加するなど、カスタマイズすることもできます。最も重要なことは、これにより私たちのコントロールの実行がミレニアル世代により受け入れられるようになることです。」
しかし、この変化はミレニアル世代だけにとどまらない。 CNC ベンダーは、オフラインの CAD/CAM から独立したプログラミング機能をマシン オペレーターに提供するだけでなく、比較的簡単にできるようにしました。
グレイ氏によると、Hurco の新しいグラフィカル会話型プログラミング システムにより、オペレーターは「ソリッド モデルの CAD ファイルをインポートし、切断したいパーツ フィーチャをクリックするだけでパーツ プログラムを生成できます。 5 軸加工機を自動的に方向付けて、3+2 軸フィーチャを切断します。プログラミングの単純さは、オペレーターの生産性を向上させるだけでなく、生産シーケンスにおける人的エラーの原因をさらに排除します。」
Siemens、Heidenhain なども同様の機能を提供しており、Holmes 氏は、あらゆる傾斜面で標準の 3 軸固定サイクルを使用できるため、5 面パーツ用の高価な CAM システムが不要になると付け加えました。
Holmes 氏はまた、「今日の高度な HMI は、基本的な視覚的検証を超えています。プログラミング、ツールとスピンドルのセットアップ、パーツのプロービング、ツールパス効率の 3D グラフィック検証を提供し、視覚的検証によって実現可能な衝突回避などのさまざまな新機能をサポートします。さらに、3 軸から 3+2、さらには完全な 5 軸加工まで、同じ視覚的検証エクスペリエンスを工場全体で利用できます。」
グレイ氏は、オンコントロール グラフィックスとマシン シミュレーション システムはもはや特別なものではなく、「特に 5 軸加工の場合、ほとんどのコントロールが行き詰まるのはプログラミング側です」と反論しました。これに対処するために、Hurco は「パート プログラムに変更を加える必要なく、その構成に関係なく、Hurco 5 軸マシンで同じパーツを切削する会話型プログラミングと NC プログラミングの両方に対応するユニバーサル プログラム タイプを開発しました」と彼は言いました。 「これにより、5 軸オペレーターのトレーニングが簡素化され、お客様にかなりの生産の柔軟性がもたらされます。」
あるマシン用に作成されたプログラムが別のマシンで実行できる程度 (キネマティック独立プログラミング) は、シーメンスのもう 1 つの焦点です。
「このアプローチにより、工作機械ごとに個別のポストプロセッサを必要とせずに、異なるキネマティクスを持つ複数の 5 軸マシンで同じプログラムを実行できます」と Holmes 氏は述べています。 「キネマティックに依存しないプログラミングにより、生成される CNC プログラムは機械にも依存しないため、5 軸加工の柔軟性が向上します。したがって、関節ヘッドを備えた機械用に作成された部品を、関節ヘッドなしでトラニオン テーブルを備えた VMC に移動します。コントロールは、このマシンでパーツを実行するようにプログラムの方向を自動的に変更します。」また、シーメンス独自の CAD/CAM パッケージである NX を使用して部品をプログラムする必要はありません。どんな標準パッケージでも構いません。
同時に、完全な CNC システムと CAD/CAM ソフトウェア パッケージの両方を提供する点で、Siemens はおそらくユニークです。この 2 つは非常に統合されているため、一方への変更は、後処理なしですぐに他方に反映されます。 Siemens と FANUC は、より広い範囲で、フライス加工から旋盤、研削盤まで同様に見える「ユニバーサル HMI」も提供し、トレーニングを容易にします。
Maxwell 氏によると、Fagor は、「ユーザーが材料とツールを選択し、プログラミングしている特定の部品の基本的な速度と送りを取得できるようにする新しい機能を提供します。 Fagor はまた、速度と精度をオンザフライでオペレーターが調整できるようにしました。これにより、荒加工では速度を上げ、仕上げでは精度を上げています。」
ホームズ氏によると、シーメンスの制御には「オペレータが荒削り、中仕上げ、または仕上げの機械加工プロセスを簡単に調整できる高速機械加工サイクルが含まれており、すべてサイクル内の値を 1 つまたは 2 つ変更するだけです。」
その他の設定補助
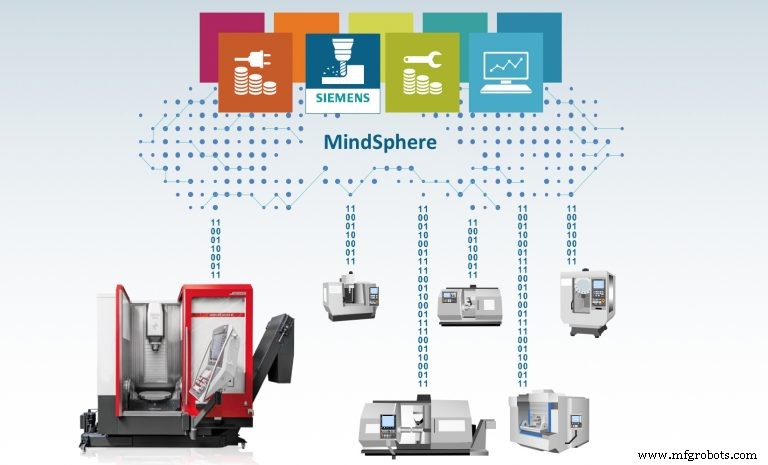
直感的なインターフェースに加えて、今日の CNC は各機能のガイダンスによってオペレータを支援します。 Siemens には、Animated Elements と呼ばれる 100 以上の短いビデオ クリップが含まれており、定型サイクルまたはセットアップ操作のほぼすべてのフィールドを説明しています。
Heidenhain には、VSC (Visual Setup Control) と呼ばれる新しいシステムがあり、ワークホールディング内のパーツの向きやボルトの締め付けなどを最適化した後、セットアップの写真を撮ります。次に、制御はその画像を同じ生産工程での後続のセットアップと比較し、部品にレンチが残っている、穴がないなどの異常をオペレーターに警告し、続行するか、次のパレットに切り替えるか、または次のパレットに切り替えるか、または是正措置のために停止します。 VSC は非常に敏感であるため、カメラはトルクがかかりすぎて完全に平らでないボルトの頭を認識することさえあります。
KinematicsOpt は、ハイデンハインのもう 1 つの興味深い機能です。 「キャリブレーション球をテーブルに置いてください」とレドボンは言いました。 「プローブはさまざまな角度で球の円周に接触し、機械を中心のピボット ポイントに正確に調整します。これは 5 軸アプリケーションにとって重要です。これは非常に強力な機能で、特に日中に店内の温度差がある場合に役立ちます。シフト中にキャリブレーション ボールをパレットにロードすると、次のバッチのパーツを切断する前に機械が自動的に再キャリブレーションを行うことができます。」
また、Hurco と Siemens は、あらゆるキネマティック構成の回転軸を備えた機械にこの機能を提供し、生産中の自動測定のためにパート プログラムにセンターライン プロービング サイクルを含める追加機能を提供しています。
最後に、すべての制御は、予想されるワーク保持、部品サイズなどに基づいて工場で調整されますが、現場での変更 (意図的またはその他) によって調整が必要になる場合があります。そのため、ファナックなどは、マイケルズ氏が「自分でできる一定量の自動調整」と呼んでいるものを可能にしています。
Maxwell 氏は次のように述べています。このソフトウェアは、ボード線図を使用して CNC とドライブのパラメータを調整し、高速切削機能を最適化します。 Fagor らは、CNC に組み込みのオシロスコープも提供して、さらに高度な調整を行っています。」
それは一体誰の支配ですか?
HMI の話題を離れる前に、オペレーターに実際に提示されるインターフェースは、CNC ベンダーではなく、工作機械メーカーの作成によるものであることが多いことに注意してください。同様に、多くの場合、同じビルダーから複数のコントロール オプションがあるため、そこにあるものについて自分自身を教育することは有益です.
たとえば、DMG Mori の CELOS フロント エンドの背後には、FANUC、Siemens、Mitsubishi、または Heidenhain のいずれかのコントロールがありますが、最後の例ではバックグラウンドでは実行されず、同じ画面上に並んでいます.
マイケルズ氏は、「マキノは主にファナックを使用していますが、あなたはそれを知らないでしょう.彼らは私たちが Panel i と呼んでいるものを使用し、バックグラウンドでコントロールをコンピューターに接続し、ユーザーにビデオ画面を表示します。標準の立形および横形マシニング センターおよび旋盤では、多くの場合、標準の FANUC HMI が使用されます。研削などのより専門的なアプリケーションには、通常、OEM 独自の HMI があります。」グリーソン歯車加工機は、ファナックの制御を専用の HMI で埋めます。もう 1 つの例には、HMI を使用して Siemens 制御を実行する Weiler 旋盤が含まれます。HMI は、「ビルダーによって非常にカスタマイズされているため、気付かないでしょう」と Holmes 氏は述べています。
データの力を活用
「インダストリー 4.0 とインダストリアル IoT は、今日の業界で最も重要な推進力であることは間違いありません」とグレイ氏は述べています。 「情報は、より賢明な意思決定を行うための鍵であり、今日の CNC マシンは、生産性と生産に関連する情報を公開し、他のインテリジェント デバイスとネットワーク化してセットアップ時間とコストを削減することが期待されています。」
この取り組みの一環として、Hurco は GitHub 上のコントロールにオープンソース インターフェイスを自由に提供し、多数のロボット工学および生産性監視企業と提携して、コントロールの相互接続機能を拡大しています。
ハイデンハインのコントロールは事実上すべての事象を詳細に伝えることができますが、Ledvon 氏によると、同社の StateMonitor システムにより、スピンドルのオン、オフ、および「非常に明確で決定的な情報」を提供するエラー コードなどの比較的制約のあるデータ セットを簡単に取得できます。手間をかけずに分析できます。」また、オペレーターは、機械が稼働していなかった理由を入力することもできます。これは、完全に自動化されたシステムでは捕捉できない重要なデータ ポイントである可能性があります。
インダストリー 4.0 に対する先進的な考え方は、シーメンスの MindSphere です。これは、さまざまなメーカーのマシンがデータを安全にアップロードして、世界中のどこからでも保存、分析、監視できるオープン アーキテクチャのクラウドベースのプラットフォームです。振動、消費電流、温度、その他の要因を監視するインテリジェント センサーを搭載したマシンは、ステータス レポートを MindSphere にアップロードします。
たとえば、センサーが特定のタイプの工作機械の Y 軸から発生する異常な振動を検出した場合、センサーは (他のユーザーから収集された大量のスマート データから得られたアルゴリズムに基づいて) 振動が原因であると判断できます。 Y軸ボールねじのベアリングの摩耗。その部品は、顧客が問題に気付く前に注文して出荷することができます。これは、予防保守を超えて予測保守にまで及びます。大きな前進です。
自動制御システム