「マシンの血液をテストする」ことでダウンタイム ゼロのパフォーマンスを実現
2000 年代半ば、ケンタッキー州ジョージタウンにある北米トヨタ工場の圧縮空気システムは、平均して年に 1 回以上クラッシュしました。そのため、機械学習と AI を活用することで、異常の検出、障害の特定、そして最も重要なこととして、差し迫った障害を発生前に予測することで、この問題に対処できるのではないかと疑問に思う人もいました。
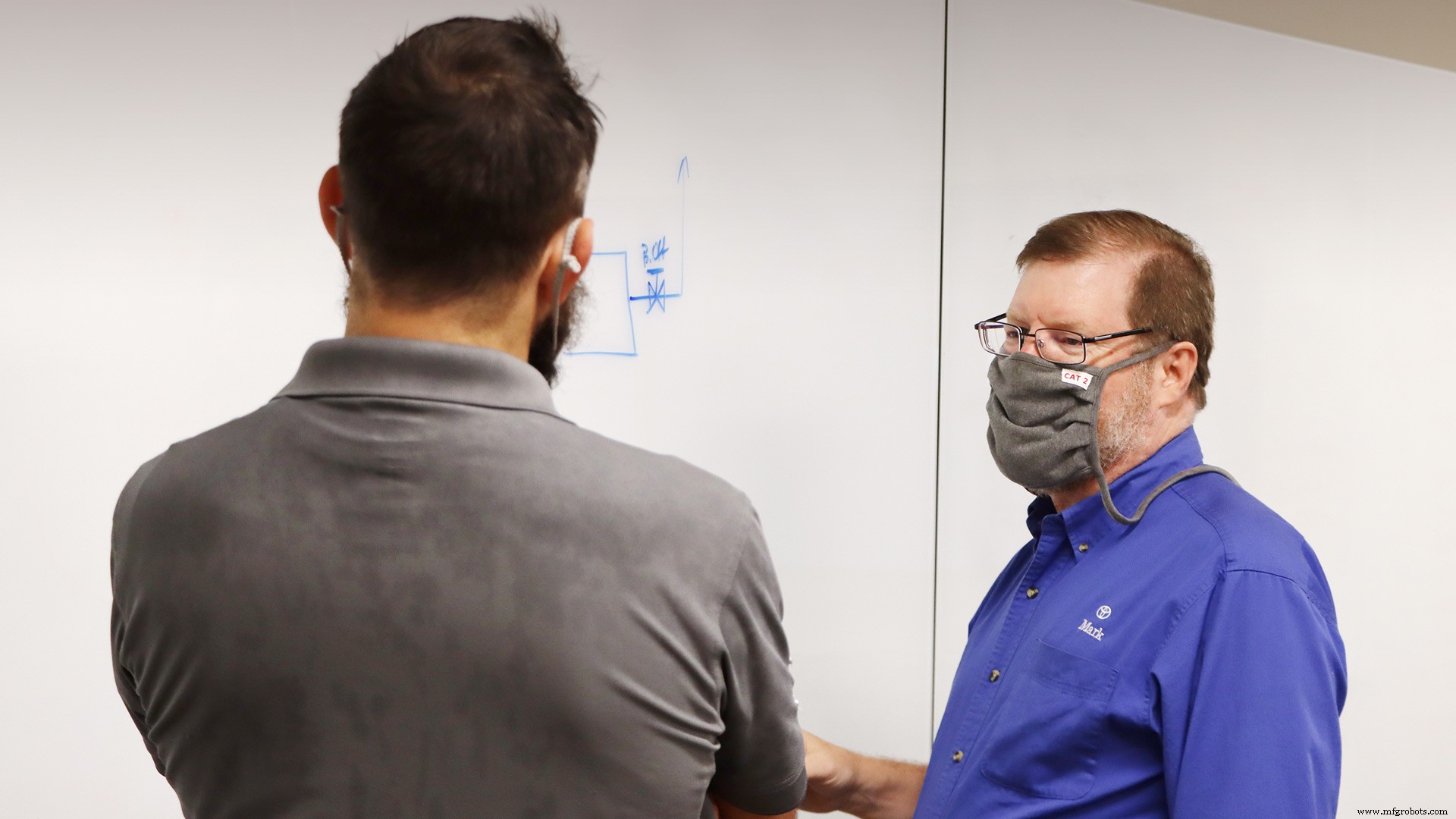
もちろん、圧縮空気システムの予期せぬダウンタイムは、工場全体に問題が発生したことを意味していました。塗装工場は、圧縮空気を使用して新車の塗装をスプレーしました。このシステムはエアツールに命を吹き込み、サンディングやその他の残留物を吹き飛ばすための圧縮空気に匹敵するものはありません.
工場の 3 つのラインのうちの 1 つを完成車が 2 交代制で 25 秒ごとに走行しているため、圧縮空気ユーティリティに障害が発生した場合、重大な結果が生じました。
「ラインがダウンした場合の費用は莫大です」と、工場のプロジェクト マネージャーであり、電気分野の専門家である Mark Rucker 氏は述べています。 「ですから、優れた、信頼できる、安定したユーティリティを手に入れる良いインセンティブがあります。」
数百万ドルの圧縮空気システムは、1ダースの Ingersoll Rand 遠心空気圧縮機で構成されており、それぞれが小さなセミトラックのサイズです。各圧縮機の最終段のブレードは、ハウジングからわずか 1 インチのところを 20,000 rpm で回転します。ブレードが仕様を少しでも超えて動作し、ハウジングに触れた場合、それは失敗です。マシン全体を約 100,000 ドルで再構築する必要があります。
ただし、ブレードのぐらつきはクラッシュの原因ではありません。それが結果です。
クラッシュ—別名サージまたは逆流 — 何かがコンプレッサーからパイプへの通常の空気の流れを引き起こし、逆流を試み、パイプ内の空気が押し戻されたときに発生します。
クラッシュの頻度、コスト、および結果により、トヨタはインテリジェント メンテナンス システムの創設ディレクターであるジェイ リーに助けを求めるようになりました。
Jay Lee はインダストリー 4.0 の時代を先取りしていた
新しいミレニアムの始まり、トヨタからの電話に先立って、リーはシンシナティ大学の工学教授であり、工場内のすべての機械が接続され、インテリジェントなメンテナンスのためのデータを提供することを思い描いていました。しかし、当時、リーのビジョンを実現するために必要な技術の多くはまだ存在していませんでした.
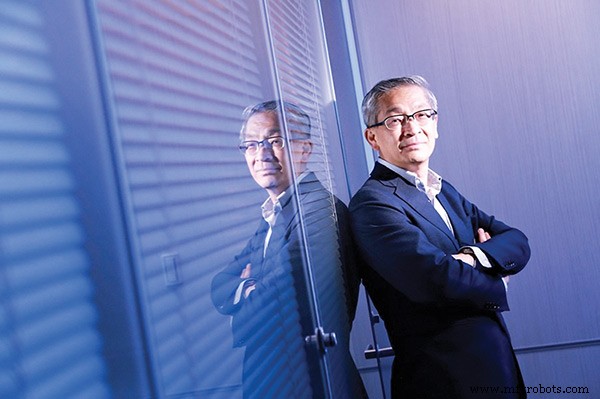
「20 年前、それが可能だと信じていた人はほとんどいませんでした」と、現在は教職を離れており、ウィスコンシン州の Foxconn Technology Group の副会長兼取締役である Lee 氏は述べています。
彼の産業ビジョンでは、機械は患者のようなものであり、機械を監視するセンサーから収集されたデータは、患者の健康に関する情報を提供します。専門家は、収集および分析したデータを解釈して予測を導き出します。
「私は言いました。『機械の血液を検査してみませんか?』そして、機械の血液は何ですか?」リーは言った。 "データ。問題は、「どのようなデータを取得したいのか?」ということです。それは、何を分析したいかによって異なります。文脈と内容を理解し、目に見えない未知の間の関係モデルをさらに策定する必要があります。」
データに隠されているのは、マシンまたはプロセスの逸脱した動作に関する意味です。その意味を明らかにすることで、品質を予測し、機械やプロセスの安定性を判断し、潜在的な障害を防ぐことができます。 「それがまさに今日のインダストリー 4.0 です」とリーは言いました。
もちろん、「インダストリー 4.0」という用語は、2013 年にドイツ政府がイニシアチブを開始するまで普及しませんでした。
2006 年以降、クラッシュは発生していません
トヨタに入社すると、リーと彼のデータ アナリスト チームは、圧縮空気システムの問題に取り組むために、ラッカーと熟練した保守作業員とプラント エンジニアのグループと合流しました。
彼らの質問の単純さは、目の前のタスクの複雑さとは裏腹でした.
「クラッシュを引き起こす前に、逆流の問題を予測できますか?」ラッカーは言った。 「それについて何かをするのに間に合うように何かが発展するのを見ることができますか?」
チームは 2005 年に数か月に及ぶ試行錯誤を繰り返しながら、圧縮機の 1 つから忠実度の高いデータを収集して分析し、異常を探しました。時々、チームはサージまたはサージへのアプローチ条件を作成して、マシンに逸脱した動作を強制的に開始させ、それがデータセットでどのように見えるかを確認できるようにしました.
最終的に、チームの仕事は報われました。そのメンバーは、第 2 段階 (通常の圧力から 120 ポンド/平方インチ (PSI) の圧力まで圧縮機が実行する 4 つの段階のうち) で発生する初期サージ状態の最良の予測因子を確認しました。
「その背後にある物理学は何ですか。なぜこれが予測因子なのですか?」ラッカーは言った。 「わからない、気にしないで。これにより、将来の急増が確実に予測され、数秒の警告で予測されることがわかりました。」
次のステップは、各コンプレッサーに差動センサーを配置し、中央制御ユニット用の機械学習アルゴリズムを作成することでした。テストでは、ステージ 2 が「ぐらつき」始めるとすぐに、コンプレッサーが後退し始めることが確認されました。
「テストするたびに、問題を回避できました」と彼は言いました。 「2006 年以来、クラッシュは発生していません。」
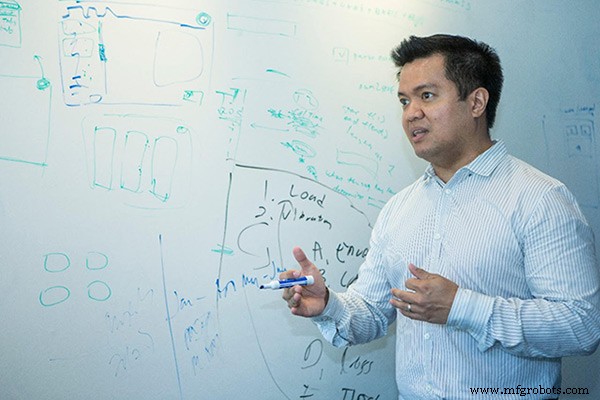
コンプレッサ サージ プロジェクトは成功しましたが、圧縮空気の巨獣のベアリングの寿命を予測することに焦点を当てた別のプロジェクトは失敗しました。チームは信頼できるメンテナンス データを十分に見つけられず、それを機械の運用データと組み合わせて有用な相関関係を引き出すことができなかった、と Rucker 氏は述べています。
「それはおそらく研究開発の適切な組み合わせについてです」と彼は言いました。 「何かを試してみても、うまくいくかどうかはわかりません。そして半分の確率でお金が戻ってきたら、それは勝利です。そして、サージ制御など、他のすべての費用を支払うものを見つけることがよくあります。」
柔軟性が鍵
リーはその後、トヨタ プロジェクトに関する論文を発表し、2013 年には、インテリジェント メンテナンス システムの従業員であるパトリック ブラウンと、2 人の大学生であるデビッド シーゲルとエドゼル ラピラと共に Predictronics の共同設立を支援しました。茶色。 Lapira と Siegel は Predictronics C スイートを構成します。
Toyota の Rucker が Lee に AI の支援を求めたように、企業はゼロ ダウンタイムの目標を達成するために Predictronics に支援を求めています。
CEO の Lapira 氏は、次のように述べています。 「すでにデータ収集構造を整えている顧客が何人かいます。彼らはデータ レイクを持っていますが、データをどう処理すればよいかわかりません。ゼロから始めなければならない顧客もいます。」
50 年または 60 年前の資産をお持ちのお客様は、さらに早い段階から開始する必要があります。
Predictronics は、レガシー マシンを使用する顧客からのアプローチがますます増えています。 Lapira と彼の同僚は、加速度計やトランスデューサーなどのコンポーネントを購入するために彼らを送ります。
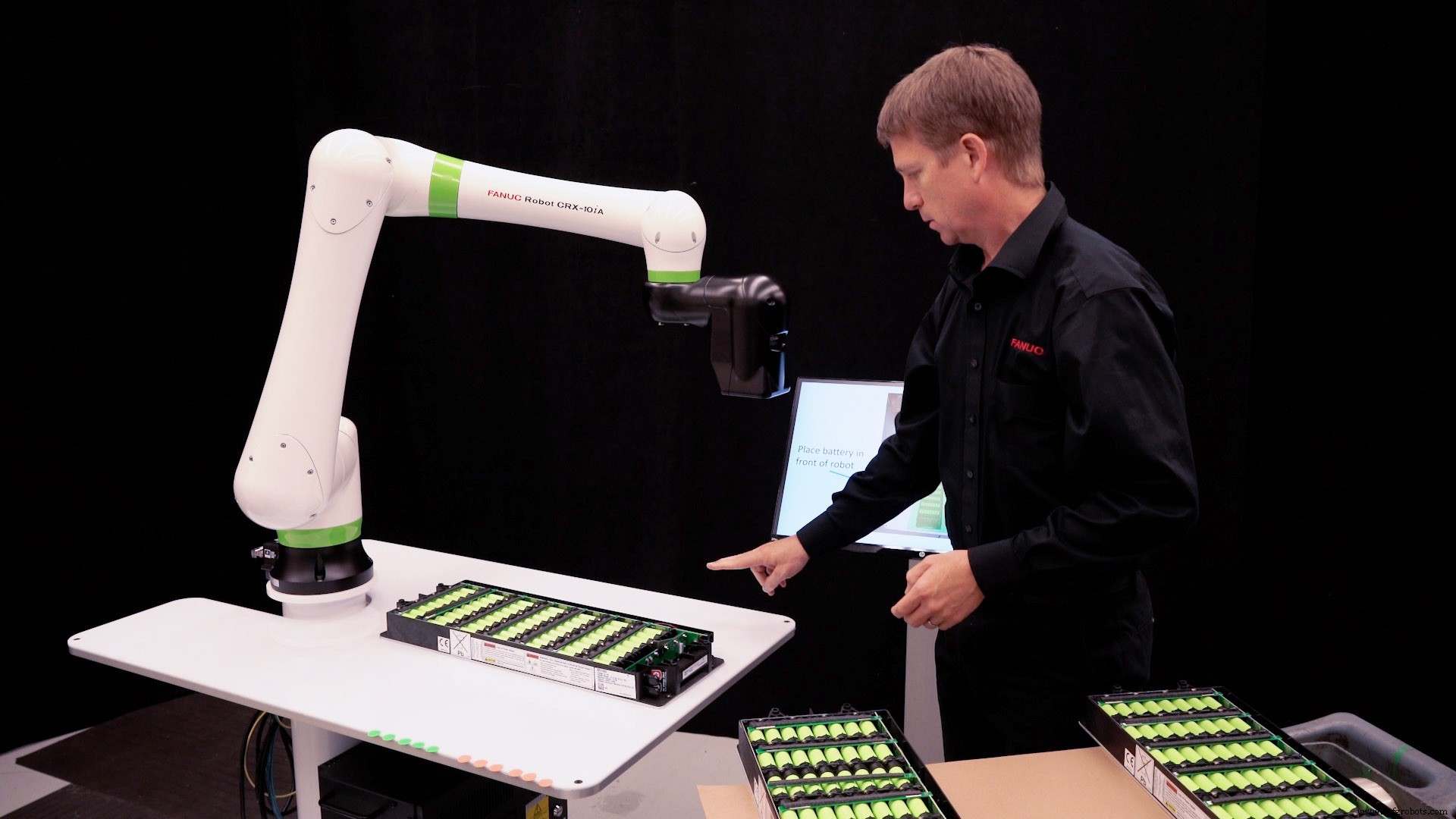
「これらは、データを取り出すために必要なさまざまなアナログ - デジタル コンバーターです」と彼は言いました。
2013 年の創業以来、Predictronics は 70 以上の工場を AI ソリューションで支援してきました。その多くはフォーチュン 500 企業です。
Predictronics は、ある顧客である半導体メーカーと協力して、センサーと測定変数の関係を学習できる仮想計測予測ソリューションを確立しました。
このプロジェクトは、半導体機器から放出される何百もの信号が測定されたため、困難なものでした。
しかし、可能性の数を絞り込むためのよく知られた統計的手法があります、と Siegel は言いました。
「これらの方法に加えて、ここ数年、組み込みの変数選択部分を持つ分類回帰アルゴリズムを組み込んだ方法を開発したのは、機械学習コミュニティの多くでした」と彼は言いました。 「それで、上位 10、20、または 30 の変数に絞り込まれます。次に、顧客と協力するか、自分の知識を使用して、ソフトウェアと分析モデルに含めるのが最も理にかなっているものを決定します。」
Predictronics が、コストを抑えるのに役立つテンプレートベースのアプローチで以前の経験から得た知識を適用するか、会社の一部で作成されたソリューションを社内で拡張できるかどうかに関係なく、「最も重要な問題に直接対処するソリューションを見つける」問題だけでなく、他の問題に適用できるほど柔軟であることが重要です」と Brown 氏は述べています。
デュー デリジェンス AI
トヨタが圧縮空気の問題で行ったように、AI ソリューション プロバイダーを探し回っている工場は、適切な適合を見つけるために十分な注意を払う必要があります。
Predictronics の専門家は次のように述べています。
あなたのサービスは以前にどこで利用されましたか?
あなたのソリューションは、ダウンタイムの短縮や品質の向上という点で、事業運営の明確な改善を示しましたか?
あなたのソリューションは私の業界で使用されていますか?
あなたのチームは産業分野の知識を持っていますか?
あなたのソリューションはレガシー機器で動作しますか?
あなたのソリューションはさまざまなセンサーで動作しますか?
あなたのソリューションは機械学習を使用していますか?
モデルのトレーニングに必要なデータ量は?
正常なマシンからのデータだけが必要なのか、それとも劣化または故障したマシンからのデータから学習する必要があるのか?
ロボットも AI を欲しがる
工場の工作機械は AI の影響下でパフォーマンスが向上していますが、ロボットが同じことを実行できない理由はありません。
Fanuc America は最近、部品検査に機械学習 (ML) を使用するロボット コントローラーとロボットのビジョン機能 iRVision に「AI Error Proofing」を追加しました。
エラー防止機能により、オペレーターは画像を使用して ML をトレーニングし、2 つの異なる状況 (たとえば、溶接されたナットが存在するかどうか) をチェックし、部品を受け入れるか拒否するかを調べます。
iRVision は最大 27 台のカメラをサポートできるため、エラー防止機能は製造プロセスの多くのポイントで機能します。
ファナックのマシン ビジョン グループのスタッフ エンジニアである Josh Person 氏は、次のように述べています。
「多くの場合、ある段階でエラーが発生し、次の段階でそれが隠されます」と彼は付け加えました。
セットアップ中に、オペレータはワークピースの複数の例を提示し、それらを 2 つのカテゴリ (良し悪し) に分類できます。例がどちらのクラスにも当てはまらない場合、「undetermined」と出力されます。その後、学習したモデルを改善するために、未決定の例を追加できます。
自動制御システム