計測ソフトウェアがスマート マニュファクチャリングにプラグイン
Scott Lowen が学校に通ってからしばらく経ちましたが、彼はまだ「科学プロジェクト」を行っています。これは Lowen が冗談めかして概念実証プロジェクトと呼んだもので、部品を測定し、結果のデータから修正を決定し、それをターニング センター、ミル、またはその他の工作機械に自動的に送ります。
Lowen 氏がミシガン州ウィクソムの Zeiss Industrial Quality Solutions でソフトウェアとアクセサリのプロダクト マネージャーを務めている現在進行中の科学プロジェクトは、計測データが完全に自動化された機械加工補正を簡単に生成できるという仮説を完全には支持していない可能性がありますが、Zeiss は自動化に引き続き取り組んでいます。ソリューション。 Capture 3D Inc. (Zeiss 会社)、Renishaw Inc.、Verisurf Software Inc. などの他の企業は、計測データを使用して工作機械でさまざまな程度の自動修正を行うソリューションを提供しています。
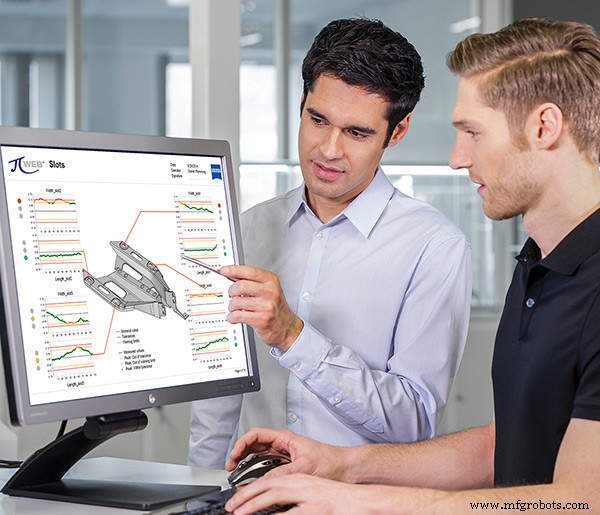
それまでの間、進行中の科学プロジェクトは Lowen の仕事の一部です。
「自動フィードバック [システム] でこの種の接続を作成するために費やされた時間は、この種の自動フィードバックを工作機械に提供するための見返りをはるかに上回ります」と彼は言いました。 「適切なデータを見て、適切なフィードバックや工作機械への修正を作成するために、適切な場所にエンジニアがいることを今でも信じています。」
これは、製造エンジニアの雇用確保にとっては朗報かもしれませんが、次のような疑問が生じます。測定プロセスは、スマート マニュファクチャリングに完全に組み込むことができるでしょうか?それとも、計測は、接続され、データ駆動型で、自動化された新しいモノづくりの世界の前に製造業者が使用していたプロセスに大部分が追いやられているのでしょうか?
自動是正措置
イリノイ州ウェスト ダンディーのレニショーには、ソフト ローンチ モードの製品があります。レニショー セントラルは、工作機械のプローブやツールセッター、Equator ゲージング システム、CMM からのマシン ステータス、アラート、測定結果などの情報のための製造データ プラットフォームです。

このプラットフォームには、ユーザーが情報を調べて、エンタープライズ リソース プランニングやカスタマイズされたダッシュボードなどの他のソフトウェア システムにフィードできるアプリケーション プログラミング インターフェイスがあります。
「私たちが目にしている [お客様が行っている] 大きな機能強化は、その測定データを取得して、事前に構成された自動補正アクションを生成することだと思います。それがツール オフセットであろうとワーク オフセットであろうと、」と Brandon Golab 氏は述べています。レニショーの工作機械ソフトウェアマネージャー。 「私たちのシステムのユーザーは、測定値にどのように反応するか、どのマシンに是正措置を伝えたいかを構成します。」
これを可能にするのは、インテリジェント プロセス コントロールと呼ばれる製品の機能強化です。これは、顧客が測定シナリオをどのように処理したいかを指示できる一連の通信プロトコルです。これにより、必要に応じて製造プロセスや工作機械にオフセットやインテリジェントな調整を加えることができます。
Renishaw Central には、マシンのステータスと測定結果を表示する標準ダッシュボードを提供する視覚化機能もあります。また、履歴データの分析にも使用できます。
ソフトローンチ中、プラットフォームは測定デバイスごとに 1 台の工作機械用にセットアップされますが、Golab 氏は、Renishaw Central とやり取りできるマシンの数に制限はないと考えていると述べています。
「Renishaw Central に加えて、マシン [ツール] 自体がデータを収集するだけでなく、単一のマシン アーキテクチャ内でクローズド ループの製造フィードバックを実行できるようにする製品もいくつか用意しています。」
初心者または経験の浅いオペレーター向けに設計されたのは、オンマシンで使用されるプログラム ビルダーによる設定と検査、およびオフライン ソリューションである Productivity+ です。 Set and Inspect は、部品のセットアップ、部品の検証、固定具の負荷の検証、切断-測定-切断 (オペレータが半仕上げパスを実行し、結果を測定し、測定データに基づいて仕上げパスを実行する場合) などのジョブを実行するために使用されます。 . 「これらのソフトウェアですべてをセットアップできます」と Golab 氏は述べています。 Set and Inspect は、レニショーのレポーター ソフトウェアと併用して、データをレニショー セントラルにフィードバックすることもできます。
「Productivity+ は CAD モデルを使用して、[Renishaw の] Inspection+ と同様のプログラムを生成しますが、CAD 駆動であるため、プログラマーにとってより簡単です」と Golab 氏は述べています。 「しかし、個々のマシン レベルでのデータの処理に関しては、Inspection+ と非常によく似ています。」 Inspection+ は、CNC コントローラ レベルで実行される G コードを記述できる経験豊富なユーザー向けのレニショーのマクロベース計測ソフトウェアです。
レニショーの測定技術は、故障の予測にも使用できます。これを行うために、Productivity+ からのデータは、部品の表面状態を評価するために毎秒数千点を測定する同社の Sprint センサーと組み合わせられます。
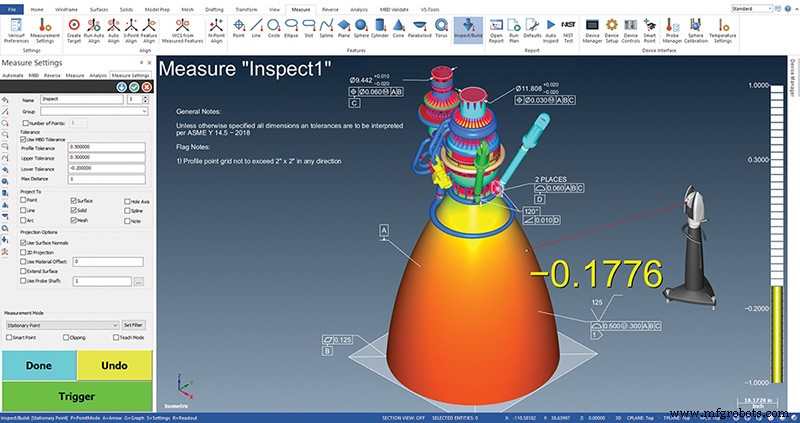
「ツールが磨耗すると、[パーツの表面に] 通常、うねりが見られます」と Golab 氏は言います。 「これは工具の性能を直接測定するものであるため、スピンドル負荷などの間接的な方法よりも、工具の摩耗を示す優れた指標となる可能性があります。」
決定権をデザイナーに委ねる
クローズド ループ製造は、Capture 3D (カリフォルニア州サンタ アナ) のゼネラル マネージャーである Rick White にもよく知られていますが、より具体的には、アダプティブ マシニングと呼ばれるクローズド ループ技術を使用しています。 「スキャン データの結果に基づいて、CNC マシニング センターでクローズド ループを作成します」と彼は言います。 「[アダプティブ マシニング ソフトウェア] は、CAD モデルに到達するために何をすべきかを判断し、修正が必要なものを修正するための機械用の新しいパスを自動的に作成します。これは、人間の介入なしにリアルタイムで行われます。」
White は、2021 年 10 月に同社が Zeiss に買収されるまで、GOM 3D 非接触測定ソリューションの主要な米国パートナーである Capture 3D の CEO でした。
アダプティブ マシニングでの使用に加えて、Capture 3D のフルフィールド ATOS 3D スキャン テクノロジーからのデータは、GOM ソフトウェアを使用したデジタル アセンブリ解析にも使用できます。 「当社の航空宇宙および自動車の顧客は、当社のテクノロジーを使用して世界中から部品をデジタルで組み立て、実際に出荷する前に適合性、位置合わせ、および仕様を確認することで大きな成功を収めています」とホワイト氏は述べています。 「これにより、企業は問題を修正したり、変更に迅速に対応したりできるようになり、コストを削減して製品の発売を早めることができます。」
たとえば、自動車の OEM は、どこにいても、工場、ベンダー、ティア サプライヤーからハングオン パーツの計測データを受け取った後、協力的なデジタル プロセスで、コンポーネントがアセンブリに適合するかどうかを次の方法で判断できます。ホワイトボディのデジタルモデル。さらに、フィールド全体のデータは、デジタル ツインに数百万の正確なデータ ポイントを提供します。 「そして素晴らしいのは、それが実際に機能し、非常に成功していることです」と White 氏は言います。
一部のメーカーが使用するデータの流れを利用するもう 1 つの手法は、モデルベースの定義 (MBD) です。 「[MBD] が意味することは、コールアウトとプロセスと差異の測定と GD&T [幾何学的寸法と公差] が最初から CAD モデルの一部であり、PMI [製品製造情報] と共に GOM ソフトウェアにインポートされることです。」ホワイトは言った。 「設計者はパーツを設計する際に、パーツの公差に関する情報も入力します。そして、計測システムがその情報を持っています。何を検査すべきか、どのコンポーネントが許容範囲外かを判断する方法を知っています。」
これにより、何を測定するかに関する決定が、プロセスの下流にいる検査官から設計者に移ります。デザイナーの視点は本質的によりグローバルであるため、デザイナーは他の誰よりもその情報をよく知ることができると考えられています。彼らは一緒に機能する部品を設計しており、同じ部品であっても公差は普遍的ではありません.
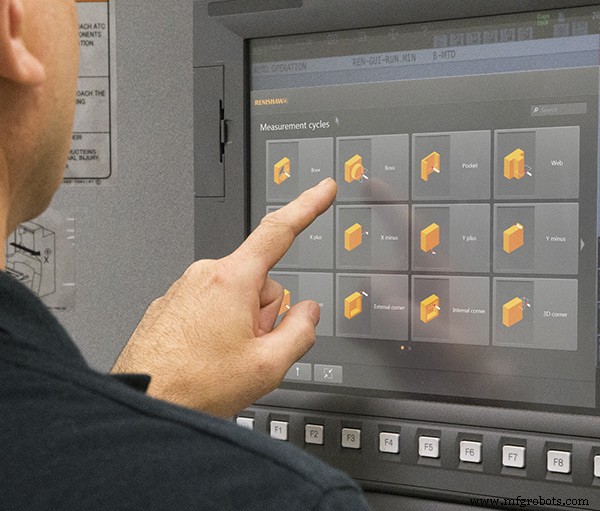
「MBD では、計測ソフトウェア内で適切に読み取られる普遍的な標準化が必要です」と White 氏は述べています。 「願わくは、[QIF [フォーマット] がその架け橋になることを願っています」と彼は述べ、品質情報をデジタルで共有するための統一された XML フレームワーク標準である Quality Information Framework に言及しました。彼は続けて次のように述べています。ただし、全体的に上昇傾向が見られ、これが将来の展望です。」
Digital Metrology Standards Consortium (DMSC) は、寸法計測の進歩を支援するデジタル計測標準の重要なニーズに対応するために QIF を作成しました、と White は説明しました。コンソーシアムのウェブサイトによると、DMSC は、2020 年 8 月に QIF 3.0 計測規格が新しい ISO 規格 ISO 23952:2020 として ISO によって収集、承認、公開されたことを発表しました。
「私たちは、誰にとっても意味のあるフォーマットの標準化に取り組んでいます」と White 氏は述べています。 「主要な CAD ソフトウェア メーカーに代わって回答することはできませんが、それが標準になった場合、彼らはそれを使用する必要があるでしょう。」
スキャンされたメッシュへの MBD の追加
「ボーイングには[MBD]が必要です。カリフォルニア州アナハイムにある Verisurf の社長兼 CEO である Ernie Husted 氏は、MBD は時間とお金の節約になると述べています。 「ティア企業の多くは、それを処理することに慣れていません。彼らは図面に慣れています。
「すべての主要な CAD 企業が標準機能として実装したのは、ここ数年のことです。そのため、適切な GD&T 公差でモデルを公差して、そのファイルをベンダーに送信できるようになりました。図面はもう必要ありません。」
CAD モデルに MBD 情報が含まれている場合、Verisurf ソフトウェアは埋め込まれたデータを使用して、CMM、アーム、トラッカー、またはスキャナーを使用した検査計画を自動化できると Husted 氏は述べています。 「工作機械のプロービングを行う場合、ツールのオフセットを調整できるプロセスがあります」と Husted 氏は言います。 「工作機械では、カッター補正と工具摩耗補正があり、工具が摩耗した場合、オフセットを調整して、内部フィーチャか外部フィーチャかに応じてフィーチャを大きくまたは小さく加工できます。そのため、ツールの摩耗を自動的に調整できますが、ツールが故障したら、ツールを交換する必要があります。」
ユーザーは、Verisurf のソフトウェア開発キットを使用して特別なアプリケーションを作成し、意思決定を支援することもできます。たとえば、パーツが許容範囲外である場合、工作機械のカルーセルに余分なツールがある場合、アプリはツールの変更を実装するのに役立ちます。工程内検査やその他の自動化されたプロセスのために、ロボットを制御するルーチンを作成することもできます。
Verisurf ソフトウェアのユーザーは、CAD モデルがない場合、スキャンしたメッシュに MBD を追加することもできます。 「そのため、パーツをスキャンすると、実際にメッシュの表面をクリックして、厚みを引き出すことができます」と彼は言いました。 2021 年 11 月、レニショーと Verisurf は、北米の企業がレニショーの Verisurf CMM ソフトウェアにアクセスできるようにする契約を結びました。
製造エンジニアが一番知っている
Zeiss の Lowen 氏は、自動化は確かに急速に進んでいますが、製造業者はその過程で貴重な人間のインプットを必要としていると警告しています。
「[私たちの]経験では、自動化を非常に困難にする現実のエンジニアリング変数が多すぎます」と Lowen 氏は言います。 「人間の頭脳を持った製造技術者が、『OK、この 1 つの形状が許容範囲外である理由は次のとおりです。実際に何が間違っていたのか、それを修正するために私たちがしなければならないことは次のとおりです』と言う必要があると判断しました。」
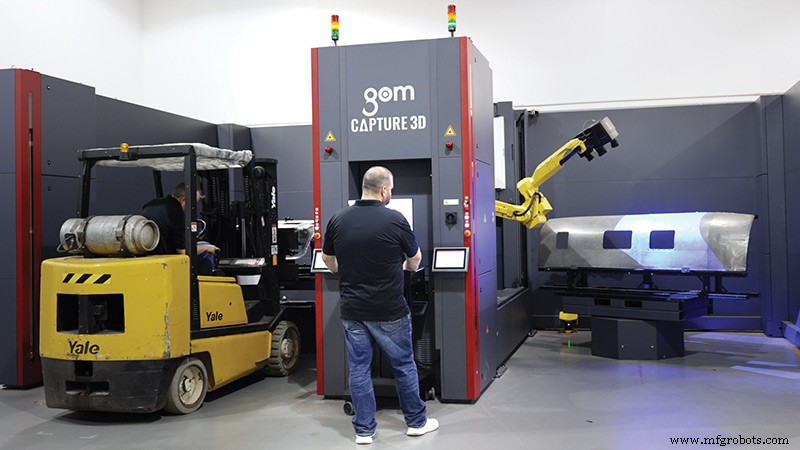
ツールの摩耗は理解するのが簡単な理由の 1 つですが、寸法が許容範囲外になる理由はめったにありません、と彼は言いました。寸法が許容範囲外になる唯一の理由が工具の摩耗である場合、Lowen 氏はそれを自動化できることに同意します。しかし現実には、部品が仕様に適合しない理由は他にもたくさんあると彼は言いました.
「保持治具が部品を歪ませているか、十分に締め付けていない可能性があります。おそらく、1 つの軸での切削中に工具が一貫して偏向していないか、ストック材料が許容範囲外である可能性があります」と彼は言いました。 「それが何であれ、それがエンジニアが学校に行く目的です:… より良い部品を作る方法.」
自動化されたソリューションを設計するための利益をさらに妨げるのは、製造業者がより多様な部品を使用して短期間で実行するという現在の傾向です.
「自動車サプライヤーにアプローチして、『今後 7 年間、この 1 つの部品を製造するので、これを設計しましょう』と言うことができるかもしれません」と彼は言いました。 「『この 1 つの形状から 10 億個のパーツを作ることになるので、時間を投資しましょう。』しかし、多くのお客様は小ロットで作っています。」
Zeiss は、Lowen 氏が自動車サプライヤーの仮想例で使用したようなエンジニアリング ソリューションを提供しています。しかし、より多様な部品を短期間で製造する企業などのために、同社は PiWeb を提供しています。これは、製造技術者がどの部品が許容範囲外であるかを分析して判断するだけでなく、その理由を判断するためのツールを提供するのに役立つエンジニアリング ツールです。
「部品が許容範囲外である場合、製造エンジニアは通常、部品が許容範囲外である理由を仮説を立て始める最も教育を受けた人であり、必要なのは仮説を裏付ける証拠です」と Lowen 氏は述べています。 「PiWeb を使用すると、部品データベースを検索して、特定のマシン ツール、日付と時刻、またはバッチ番号のいずれかを調べてフィルタリングし、統計的傾向を調べることができます。そして、PiWeb は、データだけでなく、工作機械のどの軸を修正する必要があるかを知らせるための寸法と座標を示す部品自体の優れた視覚的ツールを彼らに提供します。」 PiWeb は、Zeiss の計測ソフトウェアである Calypso から直接データを取得します。ただし、データが別の計測ソフトウェアからのものである場合、PiWeb は QDAS、DMO、QIF などの一般的なファイル形式を読み取ることができると Lowen 氏は述べています。
Lowen は、業界が測定データと自動化された工作機械補正を使用して、より自動化されたソリューションに移行する必要があることを理解しています。これらは、実装がより簡単かつ迅速になるにつれて、より広く受け入れられるようになると彼は言いました。そのために、Lowen と彼の同僚は、より多くの「科学プロジェクト」を確実に実施するでしょう。
自動制御システム