CNC 加工におけるドリル加工、リーマ加工、ボーリング加工の違いは?
外面加工と比較してCNC加工の条件 外円の加工よりも穴の加工が難しくなります。これは次の理由によるものです:
- 穴加工に使用する工具のサイズは、加工する穴のサイズによって制限され、剛性が低く、曲げ変形や振動が発生しやすい;
- 固定サイズの工具で穴を加工する場合、穴のサイズは対応する工具のサイズによって直接決定されることが多く、製造誤差と工具の摩耗が穴の加工精度に直接影響します。
- 穴を加工する場合、切削領域が工作物の内部にあり、切りくずの排出と放熱の条件が悪く、加工精度と表面品質の制御が容易ではありません。

1. 掘削
掘削 固体材料に穴を加工する最初のプロセスであり、穴の直径は通常 80 mm 未満です。穴あけには 2 つの方法があります。1 つはドリルの回転です。もう 1 つはワークピースの回転です。上記の 2 つの穴あけ方法によって生成される誤差は異なります。ドリルビットを回転させて穴あけ加工を行う場合、刃先の非対称性やドリルビットの剛性不足によりドリルビットがずれると、加工穴の中心線が傾いたり歪んだりしてしまいます。まっすぐではありませんが、穴の直径は変わりません。逆に、工作物を回転させる穴あけ方法では、穴の中心線は直線のままですが、ドリル ビットのずれによって穴の直径が変化します。
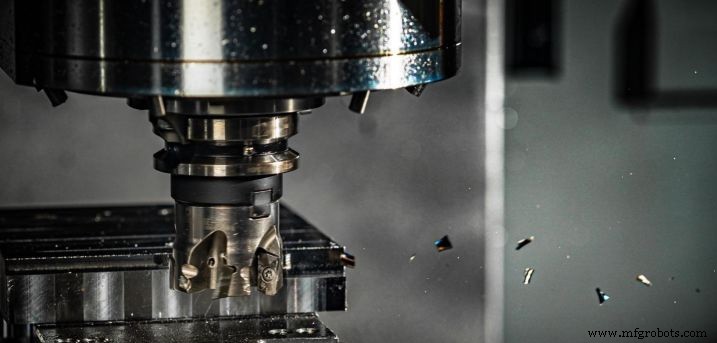
一般的に使用される穴あけ工具には、ツイスト ドリル、センター ドリル、深穴ドリルなどがあります。その中で最も一般的に使用されるのはツイスト ドリルで、その直径の仕様は写真のとおりです。
構造上の制限により、ドリルビットの曲げ剛性とねじり剛性は両方とも低く、センタリングが不十分であるため、穴あけ精度が低く、一般にIT13〜IT11にしか達しません。表面粗さも大きく、一般的に Ra は 50 ~ 12.5μm ですが、穴あけの切りくず排出量が大きく、切削効率が高いです。 穴あけは主に、ボルト穴、ネジ穴、オイル穴など、品質要件の低い穴を加工するために使用されます。 加工精度が高く、表面品質が要求される穴の場合、その後の加工でリーマ加工、リーマ加工、中ぐり加工、または研削加工を行う必要があります。
2.リーミング
リーマ加工は、生産で広く使用されている穴の仕上げ方法の 1 つです。 小さな穴の場合、リーマ加工は、内面研削やファイン ボーリングよりも経済的で実用的な方法です。
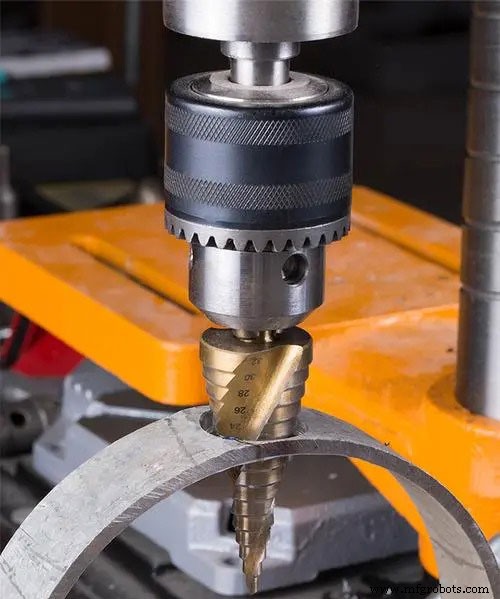
リーマー
リーマーは通常、ハンド リーマーとマシン リーマーの 2 種類に分けられます。 ハンドリーマーのハンドルはまっすぐで、作業部分が長く、ガイド機能が優れています。ハンドリーマは一体型と外径調整式の2つの構造を持っています。マシンリーマには、シャンクタイプとスリーブタイプの2種類があります。リーマーは丸穴だけでなく、テーパー穴もテーパーリーマーで加工できます。
リーマ加工技術とその応用
リーミング代は、リーミングの品質に大きな影響を与えます。余裕が大きすぎると、リーマーの負荷が大きくなり、刃先がすぐに鈍くなり、滑らかな機械加工面を得るのは容易ではなく、寸法公差を保証するのは容易ではありません。取り代が小さすぎると、前工程のツールマークが取れないのでは、当然穴加工の品質は向上しません。通常、蝶番の粗い許容値は 0.35~0.15mm で、細かい蝶番は 01.5~0.05mm です。
構成刃先の形成を避けるために、リーマ加工は通常、低い切削速度で実行されます (鋼および鋳鉄用の高速度鋼リーマの場合、v <8m/min)。フィードの値は、処理するアパーチャに関連しています。口径が大きいほど、フィードの値が大きくなります。ハイス鋼リーマで鋼や鋳鉄を加工する場合、送りは通常0.3~1mm/rです。
穴をリーマ加工するときは、構成刃先を防ぎ、切りくずを時間内に除去するために、穴を冷却し、潤滑し、適切な切削液で洗浄する必要があります。研削やボーリングと比較して、リーマ加工は生産性が高く、穴の精度を確保しやすいです。ただし、リーマ加工では穴軸の位置誤差を補正することはできず、穴の位置精度は前工程で保証する必要があります。段付き穴や止り穴はリーマ加工に適していません。
リーマ穴の寸法精度は概ねIT9~IT7、表面粗さRaは概ね3.2~0.8です。高精度が要求される中サイズの穴 (IT7 レベルの精度の穴など) の場合、生産で一般的に使用される典型的な処理スキームは、穴あけ、拡大、リーミングのプロセスです。
3. 退屈
中ぐり加工とは、既製の穴を切削工具で拡大する加工方法です。中ぐり加工は、中ぐり盤または旋盤で行うことができます。
ボーリング方法
中ぐり加工には 3 つの異なる加工方法があります。
(1) ワークが回転し、ツールが送ります。旋盤でのボーリング加工のほとんどは、このボーリング方法に属します。プロセスの特徴は次のとおりです。加工後の穴の軸線はワークピースの回転軸と一致し、穴の真円度は主に工作機械のスピンドルの回転精度に依存し、穴の軸形状誤差は主に依存しますワークピースの回転軸に対する工具の送り方向。位置精度。この中ぐり工法は、外面との同軸性が要求される穴の加工に適しています。
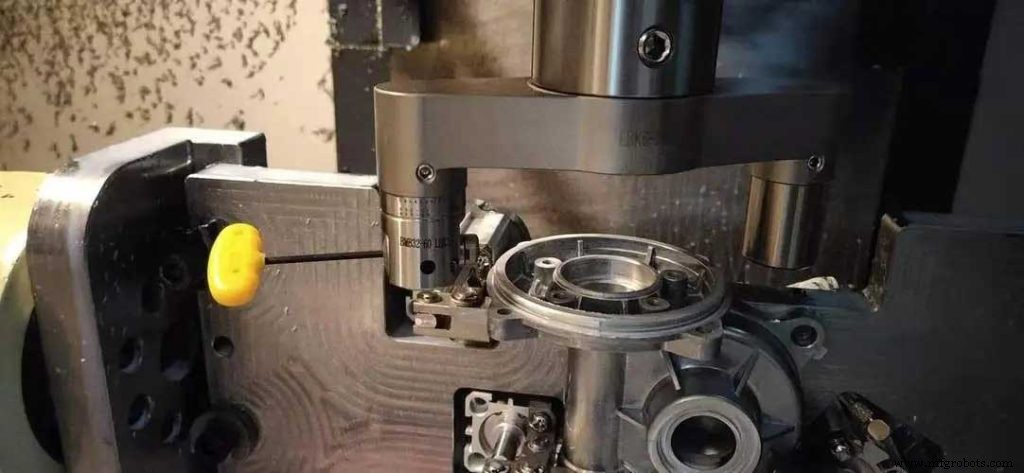
(2) ツールが回転し、ワークが送り動作をします。中ぐり盤のスピンドルが中ぐり工具を回転させ、ワークテーブルが工作物を駆動して送り動作を行います。
(3) 工具が回転して送り運動をするとき、この種の中ぐり方法が中ぐり加工に使用されます。ボーリングバーの突き出し長さが変化し、ボーリングバーの力と変形も変化します。穴径が小さく、テーパー穴を形成。また、ボーリングバーの突出し長さが長くなり、自重による主軸の曲げ変形も大きくなり、加工穴の軸が曲がってしまいます。このボーリング方法は、短い穴にのみ適しています。
ダイヤモンド ボーリング
ダイヤモンドボーリングは、通常のボーリングに比べ、バックカット量が少なく、送り量が少なく、切削速度が速いのが特徴です。高い加工精度(IT7~IT6)と非常に滑らかな表面(Raは0.4~0.05)が得られます。ダイヤモンドボーリングは、もともとダイヤモンドボーリング工具で加工されていましたが、現在では超硬、CBN、人造ダイヤモンド工具で加工されることが一般的です。主に非鉄金属ワークの加工に使用されますが、鋳鉄および鋼の加工にも使用されます。
ダイヤモンド ボーリングの一般的な切削量は次のとおりです。前ボーリングのバック カット量は 0.2 ~ 0.6 mm、最終ボーリングは 0.1 mm です。送り速度は0.01~0.14mm/rです;鋳鉄加工時の切削速度は100~250m/minです。鋼の場合は 150~300m/分、非鉄金属の場合は 300~2000m/分。
ダイヤモンドボーリングで高い加工精度と面品位を実現するためには、使用する工作機械(ダイヤモンドボーリングマシン)の幾何学的精度と剛性が高くなければなりません。工作機械の主軸は、通常、精密アンギュラ玉軸受や静圧滑り軸受、高速回転部品で支えられています。正確にバランスを取る必要があります。さらに、ワークテーブルが安定した低速の送り動作を確実に実行できるように、送り機構の動きは非常に安定している必要があります。
ダイヤモンドボーリングは、加工品質が良く、生産効率が高く、エンジンのシリンダー穴、ピストンピン穴、工作機械のスピンドルボックスのスピンドル穴など、大量生産の精密穴の最終加工に広く使用されています。ただし、鉄系金属製品をダイヤモンドボーリングで加工する場合、ダイヤモンド中の炭素原子は親和性が高いため、超硬合金製とCBN製のボーリング工具しか使用できず、ダイヤモンド製のボーリング工具は使用できないので注意が必要です。鉄族元素入り。 、工具寿命が短いです。
ボーリング工具
ボーリング工具は、片刃ボーリング工具と両刃ボーリング工具に分けられます。
ボーリングの技術的特徴と適用範囲
ドリル-拡張-リーミングプロセスと比較して、穴の直径はツールのサイズによって制限されず、ボーリングには強力なエラー修正能力があります。ボーリング面と位置決め面により、高い位置精度が維持されます。
ボーリング穴の外円と比較すると、工具ホルダーシステムの剛性が低く、変形が大きいため、放熱と切りくず除去の状態が良くなく、工作物と工具の熱変形が比較的大きくなります。中ぐり穴の加工品質と生産効率は、外側の円ほど高くありません。
上記の分析に基づいて、ボーリングは加工範囲が広く、さまざまなサイズと精度レベルの穴を加工できることがわかります。大径で高い寸法精度と位置精度が要求される穴および穴システムの場合、加工はほぼボーリングのみです。方法。ボーリングの加工精度はIT9~IT7、面粗さはRaです。中ぐり盤、旋盤、フライス盤などの工作機械で中ぐり加工ができます。柔軟性の利点があり、生産で広く使用されています。大量生産では、中ぐり効率を向上させるために、中ぐりダイスがよく使用されます。
産業技術