コンカレントおよびシーケンシャルエンジニアリング-新製品開発
並行および順次エンジニアリング
同時 およびシーケンシャルエンジニアリング 新製品開発の8つの段階で情報を共有するために、機能チーム間の相互作用を追跡するための2つの主要な製品設計ワークフローアプローチです。
製品開発には時間がかかり、現代の製品を作成するために必要な技術は非常に複雑です。企業は、設計、開発、立ち上げを数人のエンジニアに頼ることができなくなりました。産業革命とそれに続く多くの分野での継続的な技術の進歩により、人々はある分野に特化することを余儀なくされ、企業は専門の従業員を雇うようになりました。現代の新製品開発は学際的なプロセスであり、製品を市場に出すために、工業デザイナー、製品デザイナー(機械、電気、ソフトウェアエンジニア)、製造、マーケティング担当者などの機能チームに依存しています。 NPDが直面している課題は十分にあります。したがって、NPDは成功するよりも頻繁に失敗します。
さまざまな機能チームが(開発のどの段階で)コミュニケーションをとるときに相互作用し、情報を共有することで、製品の成功を追求する上で大きな違いが生まれます。これは、これらの要因が、開発時間、製品コスト、および製品の品質に影響を与えるためです。
シーケンシャルエンジニアリング(SE)とは
従来のシーケンシャルエンジニアリング は、線形の製品開発プロセスを説明するために使用される用語です。このプロセスでは、一度に1つの専門分野に焦点を当てて、設計と開発のステップが次々に実行されます。産業革命の間、製品がより複雑になるため、企業は専門家や部門を雇うことを余儀なくされました。これにより、各チームメンバーまたは部門が自分のタスクのみに集中し、完了した作業を次の作業に渡すという「壁を越えた」精神への道が開かれました(図1)。
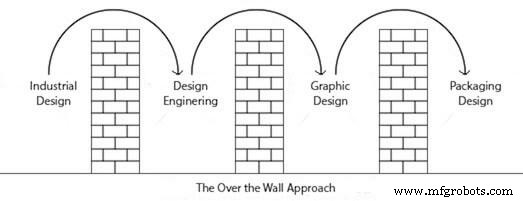
この従来のいわゆる「煙突」ベースの新製品開発プロセスは、下流でのみ相互作用する大きな垂直構造を表しており、次の長所と短所があります。
シーケンシャルエンジニアリングの長所と短所
利点シーケンシャルエンジニアリング
- 進捗状況を簡単に追跡し、プロジェクトとプロセスの要件を理解する
- チームメンバーまたは部門ごとに明確に定義されています
- 理解しやすく、誤解を避ける
- これは、誤解を取り除く、課せられた統制のとれたアプローチです
シーケンシャルエンジニアリングのデメリット
- NPDの後期段階での手直しにより、製品サイクルタイムが増加しました
- 後の段階で他の人からの変更要求は、多くの場合、非常に費用がかかり、管理が困難です
- 段階的なフィードバックと仕様評価ゲートがないと、製品が忍び寄ったり、期待を下回ったりする可能性があります
- 製造および製造コストが難しすぎて高額になる可能性があるため、最終的な単価は経済的に実行可能ではありません。
コンカレントエンジニアリング(CE)とは何ですか?
コンカレントエンジニアリングは、「壁を越えた」方法の問題のいくつかを排除するために1980年代に開発されたアプローチです。コンカレントエンジニアリングには多くの利点があり、新しいエンジニアリング製品を設計および開発しながら、さまざまな部門がエンジニアリング製品開発のさまざまな段階で同時に作業します。いくつかの重要な利点を含む、コンカレントエンジニアリングの新製品開発の詳細。
コンカレントエンジニアリングとシーケンシャルエンジニアリング
企業がとる典型的な新製品開発の旅を見て、コンカレントエンジニアリングとシーケンシャルエンジニアリングの違いを探りましょう。
順次新製品開発
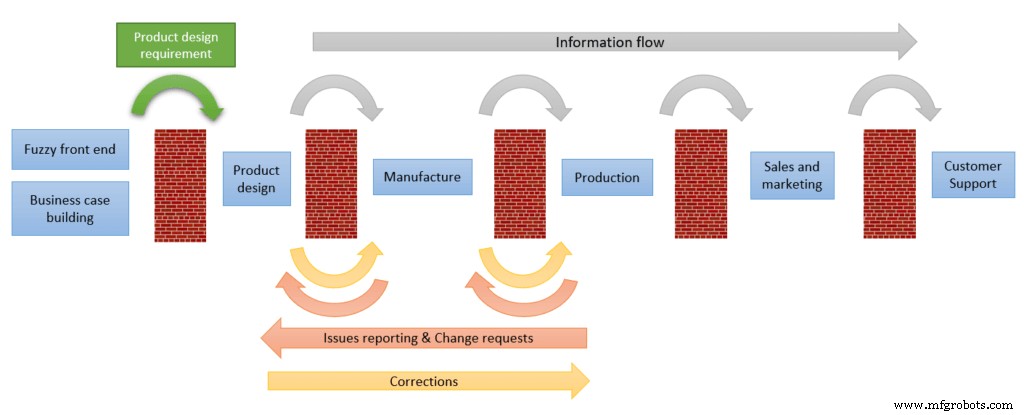
図2は、典型的な製品開発チームと、従来の線形ワークフローにおけるその機能を示しています。
- NPDのファジーフロントエンドで製品開発の機会を特定し、ビジネスケースを分析した後、管理者は製品設計仕様(PDS)を設計および開発部門に渡します。
- PDS中に製品設計チームが何も入力しなかった場合、彼らは白紙で製品開発の旅を開始します。アイデアの生成、評価、顧客評価のデータは渡されません。
- 詳細設計が完了するまで、PDSに従って製品設計が完了します。その後、詳細な図面が製造エンジニアにリリースされます。これは、変更を要求し、サプライヤに問題を報告する製造部門によって多くの問題が報告される段階です。調達段階でサプライヤーから提起された問題は、設計部門にフィードバックされます。
- 要求と変更のフェーズの後、部品は組み立てとテストのために生産部門に配送される準備が整います。そこでは、組み立てでさらに多くの問題が報告されます。
同時新製品開発

同じ製品開発は、追加のリソースをほとんど使用せずに再調整して、同時エンジニアリングワークフローを実現できます。下の図3に示すように、部門はタスクを完了する前に、互いにまたは関連する担当者に相談します。利点を探るプロセスを詳しく見ていきましょう。
- 会社は共同で製品設計仕様(PDS)を定義します。
- 設計の製造可能性を評価するために、製造と製造が相談されます。 DFM、QFD、DFMAなどのツールを評価に使用できます。
- 組立設計(DFA)などのツールを使用して、製造と共同で設計を評価します
- 詳細な設計情報は生産と共有され、ツールと生産ジグを準備できるようになります。
- 最後に、設計チームは最終仕様などの情報を営業チームやマーケティングチームと共有し、データシート、パンフレット、パッケージデザイン、販促イベントなどを準備できるようにします。
CEとSEのコスト比較
シーケンシャルエンジニアリング製品開発では、部門がプロセスに関与するときにアクティビティが順次実行されるため、コストはゆっくりと増加します。ただし、設計-製造段階では、変更要求と変更管理プロセスが前後する反復ループにより、コストが急速に増加します。
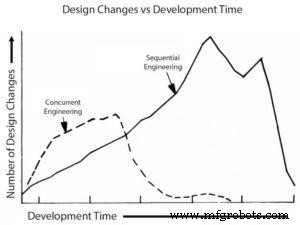
コンカレントエンジニアリング製品開発では、より大きなチームが関与し、集中的な活動を行うため、開発の開始時にコストが急速に増加します。ただし、製品開発が製造と生産に進むにつれて、ソートする問題が少なくなり、反復ループが短くなるため、製品開発が迅速になり、コストが削減されます。
ここで、製品の設計または開発のコストは、製品全体のコストの5〜15%の範囲です。ただし、設計段階で行われた決定は、コストの60〜95%に影響します。これは、製品の全体的なコストを節約するために、設計の初期段階で適切な決定を行うことがいかに重要であるかを示しています。
貯蓄に関して利用できる実際の実用的なデータはたくさんあります。たとえば、
- フォードモーター会社が、一部の車の品質を向上させながら、市場投入までの時間を大幅に短縮した方法。
- トップマネジメントがサポートするDFM、QFD、クロスファンクショナルチームは、HP34401Aマルチメータの成功の鍵でした
概要
製品開発に並行プラクティスを導入することには多くの利点があります。完全に包括的である必要はありません。批判の中には、最初はもっと多くのリソースが必要だというものがあります。しかし、正しく行われると、それを最小限に抑えることができます。すべての部門が最初から、またはすべての主要な段階の会議に参加する必要があるわけではありません。
製品を定期的に開発する企業にとっては、定義された段階でいくつかの製品開発プロセスを導入する価値があります。
製造プロセス