アルコアは信頼性の卓越性を追求
暑さに耐えられない場合は、インディアナ州南部のAlcoa PrimaryMetals施設に就職しない方がよいでしょう。
火を噴くポットラインと溶融金属で満たされたるつぼは、生産フロアの周囲温度を3桁近くまで押し上げる可能性があります。熱は目に見えて機械から放射されます。汗の小川が労働者の頬と背中に滴り落ちる。水とゲータレードのための頻繁な休憩は必需品です。
これは物理的に厳しい環境ですが、最初の段落で参照されている実際の熱は、アルミニウム製錬業界におけるこの特定のプラントの位置に関連しています。アルコアの大規模なウォリックオペレーションの一部であるこのサイトは、1950年代後半に建設され、1960年代初頭に缶シート業界向けの生アルミニウムの生産を開始しました。
年齢や技術に敏感な業界の古い植物です。 1980年には33のアメリカの製錬所が稼働していました。現在は13の製錬所があります。今年は世界のアルミニウム生産能力のわずか6%が50年以上前の製錬所で生産されます。時計が刻々と過ぎています。
この状態に、次を追加します:
-
現在、工場の労働力の25%は、年齢または勤続年数を通じて退職する資格があります。
-
工場が支払う賃金は業界で最も高いものの1つです。そして、
-
数年前、この製錬所の生産されたアルミニウム1メートルトンあたりのメンテナンスコストは、世界のアルコアシステムで2番目に高かった。
暑さを感じることができますか?この工場のすべての従業員はそうします。しかし、差し迫ったように思われる終焉を待つ代わりに、保守および運用担当者は前進して行動を起こしました。
「この生活水準を維持し、この植物を生かし続けたいのであれば、それを強化する必要があります」と製錬アルコアビジネスシステムマネージャーのマークケネイプは言います。 「これは新しい現実です。それに対処する必要があります。」
それは鏡を見るところから始まります。
「私たちの課題は、私たちの老後にもかかわらず、コスト競争力があることでした」とケネイプは言います。 「私たちはもはや年齢曲線の最前線にいません。アルコア内で資本を引き付けるには、15年から20年の期間が必要です。 25年から30年ならそれは素晴らしいことです。そのためには、無駄のない、コスト競争力のある、安定した効率的なプラントであることを継続的に証明する必要があります。」
これは弱者のための環境ではありません。しかし、ハードワークと忍耐力を通して、十分な報酬があります。
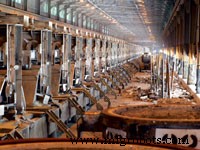
呼び出しタイムアウト
インディアナ州南部の製造コミュニティでAlcoaPrimary Metalsの存在を維持するための取り組みは、企業レベルで始まりました。
1997年、アルコアのCEOであるAlain Beldaは、トヨタ生産方式(TPS)の原則を自社の250のグローバル拠点に導入し始めました。
アルミニウムプラント生産マネージャーのロドニーカニンガム(左)、プロセスコーディネーターのラリーヨークとシニアスタッフのプロセスエンジニアであるブライアンオーディは、アルコアのウォリックオペレーションズの敷地内にある空いているアルミナタンクの中に立っています。このサイトでは、伝統的に、アルミニウム製錬プロセスの重要な成分であるアルミナの保持容器として、このような4つのタンクを使用していました。リーン生産方式と批判的思考により、プラントは2つのタンクに縮小され、会社は多額の費用を節約できました。
TPSは、「ジャストインタイム」生産、廃棄物の排除、および迅速な問題解決に基づいて構築されたリーン生産方式です。ただし、インディアナ州の製錬所は、システムを実装する際に重要な発見をしました。
「不安定で予測不可能な機器がある場合、TPSとフローおよびリーンは機能しません」とKeneipp氏は言います。
効率的で合理化された費用効果の高いプラントのメンテナンスと機械の信頼性を最優先する必要があります。
彼の主張を説明するために、Keneippは「メンテナンス氷山」と呼ばれる図を提供しています。水上には、資材、労働、残業、契約サービス、諸経費および福利厚生に関連する直接保守コストがあります。表面的には、ダウンタイム、セットアップと起動、スケジュールの遅れ、過剰在庫、危機管理、緊急購入、生産への全体的な波及効果に関連する間接費が潜んでいます。
「間接的なコンポーネントは、プラントの不安定な機器とプロセスによって人質にされています」と彼は言います。
この無駄はすべてシステムを圧迫し、運用と保守の両方のコストを押し上げます。
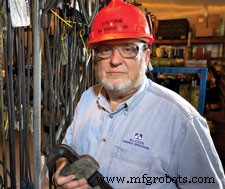
2002年、この製錬所の総維持費は3,500万ドルを超えました。生産されるアルミニウム1メートルトンあたりのメンテナンスコストが137ドルを超える「痛々しいほど高い」比率(年間トン数については「事実」を参照)により、世界中のアルコア製錬所の中で2番目に最後になりました。 2002年の世界平均は1メートルトンあたり90ドルでした。
このアルコア工場とそのリーダーには2つの選択肢がありました。
「プラントマネージャーのロイスホーズは、コストを削減するつもりだと言いました。私たちがいた場所にとどまるという選択肢はありませんでした。それは起こりそうだった」とケネイプは言う。 「私たちはそれを賢い方法か近視眼的な方法のどちらかで行うことができました。あなたが近視眼的に行くとき、それらは恐ろしい日です。メンテナンスを延期するだけで実行する必要のあることを実行するために、プラントに資本を引き付けるのは困難です。誰もそのアプローチに満足していません。それが、人々がより良いものを探す動機です。」
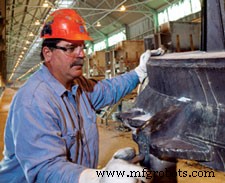
波をキャッチする
今までに推測していなかった場合、アルコア工場はメンテナンスコストを削減するためのスマートなアプローチを選択しました。メンテナンスリーダーは、2003年の初めにライフサイクルエンジニアリング(LCE)およびロンムーアグループのコンサルタントと協力して、3つの「波」で展開された信頼性エクセレンスプロセスと呼ばれるアプローチを作成しました。このプロセスは、正式で明確に定義されたパートナーシップが保守と運用の間に不可欠であるという信念に基づいています。このパートナーシップでは、オペレーションが機器を所有し、信頼性に第一義的な利害関係を持っています。メンテナンスは、タイムリーで効果的な方法、スキル、専門知識、サポートを提供することに専念する対等なパートナーです。
「それは大きな変化です」と信頼性工学の監督者であるジョセフ・モッツは言います。 「以前は、指さしがたくさんあるサイロ環境でした。」
溶融金属はるつぼから注がれます
アルコア工場。
いくつかの例:
オペレーターが潜在的な問題に気づきました。修正は予定も作成もされていません。機械が故障した。誰のせいですか?
または、2時間の予防保守作業のために保守が現れました。マシンにいる間に、追加の問題が見つかり、8時間後にPMジョブが終了したため、出力に影響がありました。誰のせいですか?
これらの場合の答えは、メンテナンスと運用の両方でした。
「私たちは全員が同じチームに所属していることを認識しなければなりませんでした」とMotz氏は言います。 「私たちは皆、アルミニウムを作るためにここにいます。別の方向に進んで一緒に作業しないと、プロセスは機能しません。」
3波アプローチの波1は2003年6月に始まりました。
「ウェーブ1はロン・ムーアでした」とケネイプは言います。 「私たちは彼を連れてきて、主要なプラントリーダーと話をしました。彼は昔からのパラダイムに挑戦しました。 「あなたは資産所有者の哲学をもっと理解する必要があります。」「あなたはお金を無駄にしています。」彼は物事を揺るがし、目を開きます。」
Wave 2は、LCEによる完全なReliabilityExcellence評価とともに8月に到着しました。同社は2週間にわたって、90人の運用および保守担当者(時給および給与)とプラント管理者に長時間のインタビューを実施しました。
情報は次のようになりました:
-
実装コストと比較した信頼性の卓越性へのギャップを埋める際の推定値を詳述する財務分析(投資収益率の計算として表されます)。
- ギャップを埋めるために必要なプロセスと方法論を概説した予備的なマスタープラン。
「私たちは現在の状態を見て、目標の状態を特定したかったのです」とケネイプは言います。 「これら2つの間のギャップは、あなたの苦痛または利益です。ギャップを埋める努力をする価値はありますか?その価値を上級管理職に証明しなければなりませんでした。古い工場にお金を入れることにはメリットがあることを証明しなければなりませんでした。
「すべての事実に直面して、続行するためにできるだけ早くお金を承認することが賢明でした。」
ウェーブ3は9月に始まりました。運用および保守のリーダー:
-
マスタープランを実施
-
機器の信頼性の向上に関連する新しい役割と責任についてすべての従業員を教育しました
-
適切な信頼性向上技術に関するワークショップを実施
-
確立された定義済みのプロセスと効果的な進捗測定
「これは簡単なことではありません。このようなものはどれもそうではありません」と、ポットルームの生産マネージャーであるロドニー・カニンガムは言います。 「しかし、管理責任と保守と運用のパートナーシップがあれば、成功の可能性は高くなります。それらがなければ、成功することはできません。」
バーを上げる
さまざまな分野で定義を確立することは、改善のきっかけとなるのに役立ちました。主な焦点は、「何が可能か」を定義することでした。と「進歩とは何ですか?」
答えは、設備総合効率(OEE)をプラント全体の主要な指標として受け入れることでした。 OEEは、機器の可用性、パフォーマンス、品質などの運用損失の原因を追跡し、最適なパフォーマンスのパーセンテージとして表されます。
「これは基本的に過去の最高のパフォーマンスによって定義されます」と電極製造マネージャーのトム・スボボダは言います。 「あなたはそれが起こるのを見ました。それは架空のものでも架空のものでもありませんでした。その月に機器が異常に稼働していたか、実際にプロセスを上回っていたかにかかわらず、それは起こりました。問題は、その1期間中にそれを行った場合、なぜそれを常に行うことができないのかということです。」
スポーツの例えを使用して、100%OEEの重要性を説明します。走り高跳びが通常、6フィート6インチジャンプするが、7フィートの個人的なベストを確立する場合、これが特にこのピークの100%パフォーマンスにつながりました。彼は別の方法で訓練しましたか?彼は会合の前に食事を変えましたか?彼は別の靴を履いていましたか?彼は文字通り水準を上げた。そのマークを何度も達成するために何を学び、何ができるでしょうか?
メンテナンスと運用が連携して、プラント機能(たとえば、アノードアセンブリ)、プロセス(鉱石の荷降ろし)、結果(スクラップ)、および個々の機器(リング炉)のピークパフォーマンスを定義しました。この情報をまとめた結果、OEEの目標を達成した結果、年間830万ドルのコスト削減が可能であると判断されました。
背景情報を使用して、現在の状態が定義され、ターゲット条件が確立されました。活動–カイゼンや継続的改善などのリーン生産方式を利用した作業プロジェクト–が行われました。進捗状況を測定および分析しました。そして、具体的なメリットが計算されました。
2004年には、240万ドルの改善がOEEの向上につながりました。
深く見て行動を起こすことも、製錬所の維持費の削減につながりました。信頼性イニシアチブを開始してから最初の1年間で、経費はベースラインの3,200万ドルから3,010万ドルに190万ドル減少しました。 2004年には、この数字はさらに70万ドル下落しました。生産されたメートルトンあたりの保守費用の比率も、2004年には109ドルに低下しました。
「計画済み」の計画
メンテナンスの要素をより適切に定義するためにも、大きな努力が払われました。具体的には、このオペレーター主導の信頼性システムでは、「作業はどのように計画されますか?」と「仕事はどのように行われるのですか?」
「振り返ってみると、私たちは自分たちが健康であると思い込んでいました」とメンテナンスマネージャーのダニー・レイエスは言います。 「私たちの古い指標の多くは連絡が取れていませんでした。 「計画およびスケジュールされた作業の割合」は85%であり、「PMの完了率」は90%であると考えました。」
LCEは、間違った定義を使用していることをプラントに通知しました。
「「計画された作業の割合」は、実際には「予定された割合」にすぎませんでした。計画は非常に限られていました」とレイエス氏は言います。 「それはスケジュールの遵守でした。おそらくそれらの仕事の10パーセントが計画されていました。」
職人(140人)と計画者(4人)の35対1の比率が、問題の核心でした。
「それはあまりうまくいきませんでした」とメンテナンスプランナーのラリー・マッカビンズは言います。 「計画する時間はほとんどありませんでした。あなたはスケジューラーになりましたが、それはあまり得意ではありません。」
この設定では、リアクティブな環境が繁栄します。 「私たちは「家のメンテナンスアプローチ」を行っていました」とKeneippは言います。 「それがあなたと私が土曜日の朝にプロジェクトに取り組む方法です。本当に計画外で非効率的です。」
その後、プラントは3つのプランナーを合計7つ追加し、20対1のより管理しやすい比率を提供します。
「これにより、これらの担当者は、セットアップ、作業の整理、計画、生産センターでのスケジュール設定、すべての部品の準備、機器の停止、時間の割り当てが可能になります」と製錬保守責任者は述べています。スコットデオン。
より良い計画のための他の鍵:
-
正式な文書に、計画されたジョブのコンポーネントの概要が示されました(14ページのサイドバーを参照)。 「私たちがすべてをやろうとしていた貧しい4人のプランナーは、同じように物事をやっていませんでした」とデオンは言います。 「この新しいフォーマットにより、作業の実行方法が標準化されました。」
-
正式で安全なエリアは、現在、プランナーがジョブキッティングに使用しています。過去には、必要な部品や材料が少しずつ現場に送られていました。すべてのアイテムが到着するまで、山は数週間座っている可能性があります。待機時間中に、部品や工具が移動したり、紛失したり、別の仕事に使用されたりすることは珍しくありませんでした。
「計画担当者は仕事を計画するときに、すべての材料を注文してここに配達します。 」とマッカビンズは言います。 「仕事のすべてがここにあるとき、私たちはそれを1つか2つのパレットに集めます。その後、工芸品が来て現場に持ち出し、作業を行います。」 -
効果的なコミュニケーション。
「私は、人々が何を望んでいるのかを知っていると思っていました。このプロセスは私がしなかったことを私に教えてくれました」とMcCubbinsは言います。 「彼らが何を望んでいて、何が彼らにとって正しいのかわかりませんでした。以前は、仕事を計画し、質問はしませんでした。」
Deon氏は次のように付け加えます。「制作との責任を共有することで、どの仕事が最初に来るかがわかります。機器の所有者は、最も重要なことを知っている必要があります。以前は、私たちが推測していたとは思いません。しかし、私たちは100パーセントでしたか?おそらくそうではありません。」 -
焦点を絞った効果的な毎週の会議。
「資産所有者が会議の議長を務め、エリアメンテナンスプランナー/スケジューラーがファシリテーターです」とKeneipp氏は言います。 「計画会議の場合は、これをどのように行うかについて話し合います。スケジュール会議の場合は、スケジュールを設定します。」
また、作業の進め方に関しても、プラントは機器の履歴を文書化し、メンテナンスタスクの指示を標準化するための措置を講じました。
「初期には記録を取得できましたが、その後文書化が停止しました」と整流器ステーションの電力エンジニアであるダンデカストラは言います。 「そこで、サーバー上に場所を作成し、文書化を開始しました。このステーションでは、「バッドボーイ」リストを作成しました。私たちは大きな問題を選び出し、そこから始めました。これで、2001年に戻って、エアスイッチ、接点、変圧器、スキッドの履歴を確認できます。」
信頼性エンジニアのジョナサン・フルトンは次のように付け加えています。それは私たちにとって大きな潜在的責任です。そして、外部から質の高い職人を得るのは難しいです。これに対処するために、私たちは作業プロセスを標準化し、機器の履歴を作成しています。これにより、技術的な専門知識を持つ人々を急いでスピードアップさせることができます。」
ベビーベッドノート
最後の改善例は、メンテナンス製品を購入する人と、工具や消耗品タイプの材料にどのようにお金を使うかをプラントがどのように明確に定義したかです。
過去には、製錬所のさまざまな保守要員が、手工具、電動工具、安全製品、クリーナー、マテリアルハンドリング製品、およびその他の100の必要なアイテムを購入していました。購入した製品は、施設周辺の分散型ツールベビーベッドと、多数の非公式の保管場所(ロッカー、チェスト、カビーホール)に保管されていました。
「プラントが拡大し続けるにつれて、エリアが追加されました。彼らには小さなグループがあり、誰かが注文をして、あちこちに物資をプールしていました」と、一般的な整備士のディック・デイは言います。 「私たちはこれらの衛星ベビーベッドに餌をやろうとして多額のお金を費やしていました。彼らは管理されていませんでした。人々は物を購入しましたが、実際にはアクセスできませんでした。」
整備士が特定のツールを必要とする場合、彼はそれを探します。どこかでした。見つからなかった場合は注文します。その購入したツールは、彼に届く前に消えてしまう可能性があります。それは無駄で冗長な支出につながりました。
これに対処するために、集中型のベビーベッドが建設され、すべての衛星ベビーベッドとカビーホールのアイテムがこの安全なゲート付きエリアに持ち込まれました。
入って来たのは無価値です。
「私たちは、時代遅れのものがたくさんあることに気づきました。10年前に取り出した可能性のある機器のためのものです」とKeneipp氏は言います。
そして、貴重なものが入ってきました。
「木工品から出てきたものすべてが素晴らしかったです。誰かが38,000ドル以上のポンプとジャックを備えたキャビネットを持ってきました」と、中央のベビーベッドのメインアテンダントになったデイは言います。 「私たちは持っていたものを使い始めました。一部の資料では、1年間何も注文する必要がありませんでした。」
今日、Dayはこれらのメンテナンス関連製品を購入する責任があります。彼は購入品を受け取り、アイテムを保管し、必要に応じてそれらを分配します。
「私たちは自分たちが持っているものとそれがどこにあるかを知っています」と彼は言います。
Dayはまた、さまざまな製品の最小/最大システムを作成し、電動工具と溶接用品のブランドを標準化する取り組みに着手しました。
「電動工具では、主にDeWaltを標準化しており、コードレス工具に深く取り組んでいます」と彼は言います。 「溶接用品については、ワイヤーフィードガンとそれらのガンの交換部品を標準化しました。」
彼は宿題をし、コストを削減する革新的な方法を見つけました。
いくつかの例は次のとおりです。
手袋 :「以前は、小さなタブが付いた手袋のブランドを1足12ドルで購入していました。それは誰もが「持っていなければならなかった」ものです」と彼は言います。 「少し伸縮性のある同じ手袋をペアあたり2.67ドルで購入できます。人々はそれらが好きでした。」
作動油 :「1ガロンで1ポップ8ドルで購入しました。まとめて購入すると、1ガロンあたり3ドル節約できます。 1個あたり57セントの再利用可能な水差しにオイルを注ぎます。」
アセチレンホース :「以前は、スプールにパッケージ化された状態で購入していました。今、私たちはそれを500フィートのロールで購入し、人が必要とするものを切り取ります。 25%節約できます。」
日はそれがすべて常識だと言います。
「私はそれを自分のお金と見なしています」と彼は言います。 「これが私のビジネスである場合、これは私がそれを実行する方法です。」
汗をかく
ハードワーク、パートナーシップ、所有権、革新的な考え方により、このアルコア製錬所はより安定し、無駄がなく、予測可能で、信頼性が高く、コスト競争力があります。
OEEの費用対効果は、2003年のベースライン値と比較して、2005年の年間年間440万ドルです。
2005年の年間保守費用は年間2,710万ドルで、2003年のベースライン数から490万ドル減少したことを反映しています。
2005年の第2四半期の保守コストは、生産されたメートルトンあたり96ドルであり、近い将来に87ドルを達成するための目標が設定されています。
LCEのフォローアップ評価により、プラントは「予防的条件」カテゴリに分類され、「卓越性」カテゴリに昇格するための作業が進行中です。
楽観主義と勢いがあります。
「私が15年前に雇われたとき、私たちは「私たちは古いテクノロジーです。より近代的な施設のいくつかと競争することはできません」とフルトンは言います。 「私にとっての見返りは、私たちが競争し、効率が上がるのを見ることです。 10年または20年前に建設されたサイトよりも、40年または50年前のテクノロジーを使用した方が生産性が向上しています。」
この植物の熱が完全になくなることは決してありませんが、競争に汗を流すためにできることを行っています。
計画された仕事の特徴は何ですか?
-
監督者がいつタスクを割り当てることができるかについて合理的な期待を抱くように、仕事には正確な時間の見積もりがあります。
-
職人、修理/交換部品、工具、サポート機器などに関して、必要なリソースの正確な見積もりがあります。
-
必要なすべての情報(青写真、許可、安全関連など)が取得されます。
-
作業を遂行するための作業ステップの順序、手順、および指示が確立されています。
-
必要な部品と材料はすべてキット化されています。
-
品質計画された仕事を保証するための組み込みのチェックとして、仕事を完了するために割り当てられた監督者および/または職人と仕事の性質について定期的に話し合ってください。作業範囲を完全に理解し、キット化されたジョブパッケージが完成していることを確認してください。
機器のメンテナンスと修理