セーフティ クリティカル アセンブリの溶接検査
自動車部品を製造するメーカーにとって、そのリスクは高いものです。自動車の運転手と乗客は、設計された条件下で耐えるために溶接品質に依存しています。特に問題の部品がアセンブリにとって「安全上重要」である場合は、製造プロセス中に見逃された 1 つの間違いがビジネスを脆弱または悪化させる可能性があります。
たとえば、自動車のシートは乗客と直接接触します。したがって、シートの溶接は安全上重要であると考えられています。この分類により、製造前の特定のプロトコルが決定されます。 OEM の要件はさまざまですが、業界の慣行と一致している傾向があり、使用されている部品、プラント、および産業用機器に応じてわずかな違いで実装されています。プロトコルの基本要素は次のとおりです:
プリプロダクション プロトコル
- パラメータの設定 - 溶接パラメータを確立し、その許容性を検証します。これは、溶接部分を切断およびエッチングして、溶接の溶け込み (15 ~ 20%) を確認することによって行うことができます。
- リリース プロセス - 上記が確認された後、本番環境をリリースまたは承認する一連のプロセス
- チェンジ マネジメント - 特定の制限を超える重要な変数の変更には、カット アンド エッチング テストによる再検証が必要です。
- 品質保証 - OEM によって指定された頻度でカット アンド エッチング用に生産からランダムなパーツが選択される場合があります。
ロボット溶接は、プログラムされた溶接パラメーターを使用して常に同じ場所に溶接を配置することで、部品の品質を大幅に向上させるのに役立ちました。上記の手順を順守することで、高品質の溶接製品を製造できます。自動車 OEM は、安全上重要な溶接に重点を置いており、その結果、いくつかの重要な要素が見直されました:
生産プロトコル
- セキュリティ - 資格のある担当者が機器にアクセスできること、および品質に悪影響を与えるような変更が加えられていないことを確認する
- アーク監視 - アーク監視システムの実装は、プロセスが制御されていることを確認するのに役立ち、破壊試験の頻度を減らすことができます。アーク監視は、溶接パラメータが設定された制限を満たしていることを確認します。制限外の溶接には、さらなる検査のためにフラグが立てられます。
- トレーサビリティ - 変更と溶接結果を追跡し、部品の変更が発生した日時とシリアル番号を記録する機能を維持する
安川モトマンでは、お客様の製造とトレーサビリティの要件について学ぶことに時間を割いています。長年にわたり、メーカーが信頼性が高く追跡可能な溶接検査を実行できるように、コントローラーのソフトウェアと I/O の機能強化をいくつか開発してきました。
セキュリティ機能
パスワード機能
さまざまなレベルのグローバル パスワードの標準セキュリティ システムは、複数の技術者がプラント内の複数のロボット セルを維持するのに便利です。ただし、グローバル パスワードはプラントの職員間で共有されるリスクがあり、何が誰によって変更されているかを制御できません。
Yaskawa の DX コントローラのパスワード機能は、パスワードとセキュリティ レベルのクリアランスを持つユーザーのデータベースを作成します。ユーザーはロボットを操作するためにログインする必要があります。ログ機能により、ユーザー名と変更内容が記録されます。
DX200 コントローラにソフトウェアが追加され、PLC によるリモート パスワード制御が可能になりました。制御エンジニアは、植物/細胞ベースの制御を使用するロジックを実装して、社内の従業員バッジまたはセキュリティ システムに基づいてユーザーとログインをリモートで管理できます。
セキュリティ レベル
- 作戦レベル - デフォルトでは、この基本レベルでは、誰でもプログラムを移動またはステップ実行できますが、ポイントや溶接設定を変更することはできません。
- 編集レベル - ユーザーがプログラムを作成し、溶接設定を変更できるようにしますが、パラメーターやより高いレベルのデータへのアクセスは許可しません。
- 管理モード - パラメータとメンテナンス機能へのフル アクセスを提供する
- 安全レベル - DX コントローラ (機能安全ユニット – FSU) に実装されている信頼性の高いソフトウェア制限と安全ロジックの設定と管理へのアクセスを許可します。
これらのレベルがユーザーに何を許可し、何にアクセスできるかは、システムによって定義されます。管理者がアクセスを制御するレベルは、工場の場所によって異なります。
ロギング機能
新しいロボット コントローラの多くには、システムに加えられた変更を日付と時刻で追跡する標準のログ機能が付属しています。たとえば、日勤のオペレーターは、夜勤の誰かが変更を行ったかどうかを確認できます。ロボットは最後の一連の変更のローカル ファイルを保持するため、データを定期的に保存することで、ユーザー アクティビティの履歴ログを保持できます。ロボットはパスワード セキュリティを使用することもでき、ユーザーはログインして変更を行う必要があります。変更が行われると、ユーザー名も記録されます。
セーフティリティーチ編集機能
操作レベルでは、ユーザーがプログラム ポイントを変更することはできませんが、一部の企業では、オペレーターまたは第 1 レベルの技術者が部品のバリエーションに対して小さな変更を行うことを許可しています。 Safety Re-Teach により、運用レベルのユーザーは、管理モードで定義された 3D 範囲内でプログラムされたポイントを修正できます。これは通常、数ミリメートルに設定され、管理者はトーチまたは外部軸の角度変化量を制限できます。操作レベルのユーザーは溶接パラメータを変更できないため、重要な溶接変数は変更されません。これにより、反復的な破壊テストを回避できます。 Safety Re-Teach は、任意の DX コントローラの管理モードでパラメータによって有効にすることができます。
アーク監視
Yaskawa Motoman は、溶接システムを統合し、溶接会社とのジョイント ベンチャーの歴史に基づくロボット サプライヤーとして、アーク監視に関する包括的な経験を持っています。電源メーカーが統合した可能性のあるアーク監視機能をサポートする溶接インターフェースを設計しました。
Miller Insight Centerpoint™ と Lincoln Electric Production Monitoring™ の統合機能は、ロボットのティーチ ペンダントからアクセスできます。 Fronius の WeldCube は、電源と直接通信します。 Yaskawa と Fronius は、監視結果が溶接機ステータス ビットで報告されるように取り組んでいます。
「セーフティ クリティカル」指令を満たすという課題には、電源アーク監視からの溶接結果を有用な形式で明確に提示することも伴います。最適な形式は、ロボット セル HMI の部品図で監視結果を強調表示することです。こうすることで、溶接ステーションのオペレーターは、異常を簡単に発見し、迅速に対応することができます。オペレータは、溶接が適合しているか不適合であるかを判断するために、範囲外の監視結果でシステム フラグ付きの溶接を視覚的に検査する必要があります。
ロボット コントローラはアーク モニターのステータスを HMI でローカルに報告できますが、電源メーカーは、パーソナル コンピューターまたはクラウドベースのソフトウェアを介して、アーク モニターの結果をリモートで報告するように設計されたソフトウェアも提供しています。
ミラー インサイト センターポイント
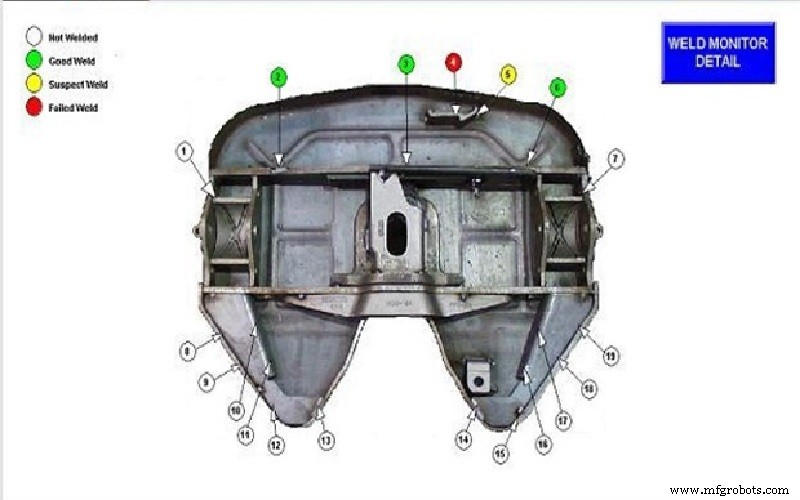
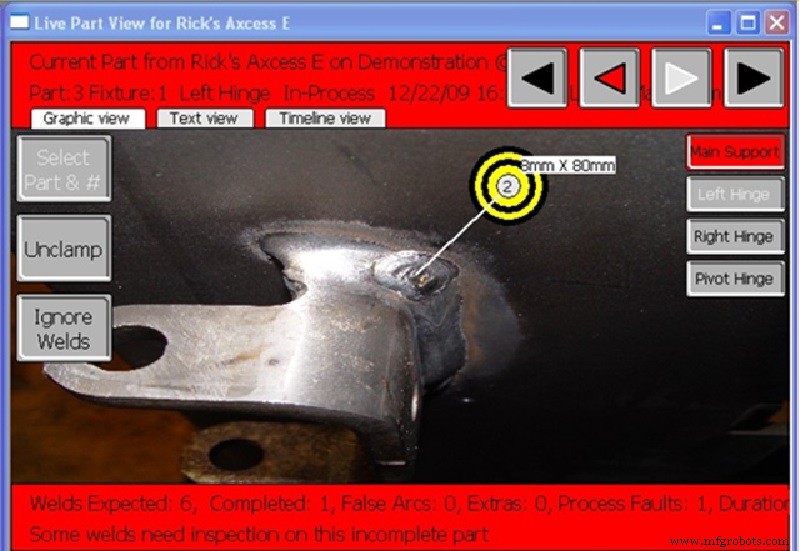
トレーサビリティ
自動車 OEM は、サプライヤーに優れた部品を製造するよう求めているだけでなく、部品の溶接結果をそのシリアル番号と関連付ける「トレーサビリティ」を提供する品質システムを実装するよう求めています。目標は、不適合部品が検出された場合に、部品が適合していることがわかっていた製造時点までさかのぼることができるようにすることです。
メーカーがトレーサビリティを確保できるようにするには、溶接電源とロボット コントローラからのアーク監視データに加えて、リモートでアクセスして最終的に PLC に記録する必要がある部品固有のデータを取得し、部品のシリアル番号に関連付ける必要があります。このデータのマッシュアップをどのように調和させるか (そしてその難しさ) は、メーカーが内部のセキュリティ プロトコルを損なうことなく、何をすぐに統合できるかにかかっています。
文字列変数
トリックの 1 つは、ロボット コントローラーから文字列変数作成関数を使用して、トレース メカニズムとして一意の識別子を作成することです。数値や位置を格納するために使用される変数が混在しており、これらの変数は形式と桁数によって異なります。文字列変数は、最大 32 文字の長さの文字または数字の組み合わせにすることができます。これらは、ペンダントにメッセージを表示するため、または他の用途のために呼び出すことができます。
自動車生産の場合、これらを使用して、生産される特定の部品のシリアル番号情報を含めました。制御エンジニアは、イーサネット通信を使用して PLC またはバーコード リーダーから値を「読み取る」ことができ、それらを他のデバイスに渡すことができます。
同時 I/O
Yaskawa Motoman はコンカレント I/O (CIO) を使用してプログラマブル ロジック制御を実行し、ロボットと電源の間でデータを通信します。溶接設定に使用されますが、電源とロボットの間でアーク監視結果を渡すためにも使用できます。トレーサビリティのために、これを使用して各溶接位置の溶接結果を連結し、それを部品シリアル番号とともにプラント PLC に送信して部品記録を取得しました。また、パーツのシリアル番号を受け取り、溶接モニターを通過したパーツにシリアル番号を刻印するピンスタンパーに送信します。
最近、Lincoln Electric Production Monitor から溶接検査データを取得し、部品のグラフィック表現でオペレータに提示するシステムを提供しました。制限内または制限外に基づいて、各溶接位置でのモニター結果が緑または赤で強調表示されます。 CheckPoint™ モニタリング (外部ソフトウェア) は、クラウドにデータを保存するように設計されています。 CIO は、Production Monitor の結果にすぐにアクセスできるようにして、部品の製造中にオペレーターに提示できるようにしました。
実装
溶接監視データの取り扱いでは、履歴の記録とトレーサビリティの要件とともに、生産管理を考慮する必要があります。途中で取得されたデータは、組織全体で異なる方法で使用されます。これらのニーズは、すべてのステップですべての役割について考慮する必要があります。
溶接監視データを使用すると、現場のオペレーターが部品の品質を簡単に確認できるようになりますが、監督担当者は履歴データを使用して、品質計画を管理し、問題をトラブルシューティングすることができます。セキュリティ機能により、確立されたプロトコルやパラメータから逸脱することはほぼ不可能になり、アーク監視により、さらに検査が必要な溶接部がリアルタイムでグラフィック表示されます。
PLC を最終目的地として使用すると、部品固有の溶接データがログに記録され、保存され、追跡可能になります。データを完全に調和させるには、かなりの事前作業が必要になる場合があります。ただし、その結果、顧客は自信を持ち、品質が向上し、将来の事業の安全を確保するのにも役立ちます。
産業用ロボット