金属3D印刷の品質保証:3つの一般的な課題の解決
品質保証(QA)は、間違いなく最も重要ですが、3D印刷で最も困難なステップの1つです。
3D印刷が高性能の産業用アプリケーションでますます使用されるようになるにつれ、このテクノロジーは、要求の厳しいアプリケーションに対応するために必要な特性を備えた高品質の部品を一貫して確実に提供する必要があります。ただし、金属3D印刷に関しては、これはテクノロジーへの投資を検討している多くのメーカーにとって継続的な課題です。
本日の記事では、企業が挑戦する際に直面する主要な課題のいくつかを取り上げます。金属3D印刷部品のQAプロセスを確立し、利用可能なソリューションのいくつかを調査します。
課題1:素材の品質を確保する
3D印刷された部品が非常に要求の厳しいアプリケーションの基準を満たしていることを確認することは、使用される材料の品質に大きく依存します。
ただし、金属粉末を製造または取り扱う企業にとって、材料の認定は継続的な課題です。プロセスを複雑にする1つの要因は、積層造形に使用される金属粉末の純度を維持する必要があることです。
これは、航空機部品や医療機器など、材料が使用される安全性が重要なアプリケーションの場合に特に当てはまります。使用するものは100%汚染されていない必要があります。不純物は最終部品の特性を変える可能性があり、その結果、印刷の失敗につながる可能性があります。
ただし、金属粉が汚染される可能性のある方法はいくつかあります。
たとえば、汚染のリスクは、印刷プロセス自体の間、または保管、輸送、および取り扱い中に発生する可能性があります。最初の例をとると、たとえば、ビルドプレートに別の粉末の残留物が残っている可能性があり、2つの異なる粉末がブレンドされます。したがって、各生産実行後にビルドプレートを徹底的にクリーニングすることは、重要な予防ステップです。
もう1つのリスクは、印刷プロセスで残った粉末を再利用することです。粉末材料を再利用する機能は無駄を減らすのに役立ちますが、この方法で粉末を繰り返し再利用すると、水分、酸素、窒素が吸収されるため、粒子の組成が変わる可能性があることに注意してください。
必然的に、汚染がないことを確認するために、積層造形に適したテスト方法が必要になります。
解決策:CTスキャンを検討してください
金属粉末の汚染を検出する最も正確な方法の1つは、コンピューター断層撮影(CT)スキャンを使用することです。
CTスキャナーは、さまざまな角度から数百枚のX線画像を撮影し、そこから3D画像を作成することで機能します。最新のCTスキャナーは、3ミクロンまでの詳細をキャプチャできますが、一部の高解像度microCTスキャナーは、はるかに小さいマイクロメートルスケールで動作し、0.5ミクロンのボクセルサイズに達します。
現在のmicroCT機器は、アルミニウムやチタンから、ステンレス鋼やインコネルなどのより重い金属合金まで、さまざまな金属を検査できます。
3D印刷用の金属粉末の認定に使用する場合、CTスキャナーは次のことができます。粉末の微細構造に関する詳細なデータをエンジニアに提供します。このデータは、異物粒子の汚染物質を検出するだけでなく、粒子のサイズと形状の分布を測定し、粒子内の多孔性を検出するために使用できます。この情報を入手することは、エンジニアが粉末の製造への適用性を確認する1つの方法です。
積層造形用のCTスキャンサービスを提供する会社の1つは、ExpanseMicrotechnologiesです。
AMFGとのインタビューで、同社の社長兼共同創設者であるJames Hinebaughは、次のように述べています。何がよく広がり、印刷される優れた粉末を作るのかを理解することは、企業にとって重要な関心事です。
「1)理想的な形態があるか、理想的なサイズまたは形態分布がうまく相互作用できるかを理解することが重要です。多種多様なリコーターとプリンターを使用し、2)介在物や粒子内多孔性などの粉末の欠陥をどのように減らすことができるか。研究によると、多くの場合、部品に閉じ込められ、印刷プロセス中に部品から逃げることができません。」
これらは、ExpanseMicrotechnologiesが独自のMicroCTスキャンソリューションで取り組んでいる2つの分野です。
同社は高度な画像処理方法を開発しました。この方法から、材料の多孔性、粒子と細孔の形態、および粒子のサイズと形状の分布に関する詳細なレポートを生成できます。
この情報を入手することで、添加剤製造のユーザーは、原料の問題を特定し、使用する材料と印刷部品の品質レベルとの関連を理解できます。
積層造形用の原料のテストと認定は困難な場合がありますが、積層造形部品の品質を確保するための最も重要なステップの1つです。現在、CTスキャンは、AM原料の検証に使用できる最も堅牢で便利なツールの1つを提供しています。
課題2:プロセス制御の確立
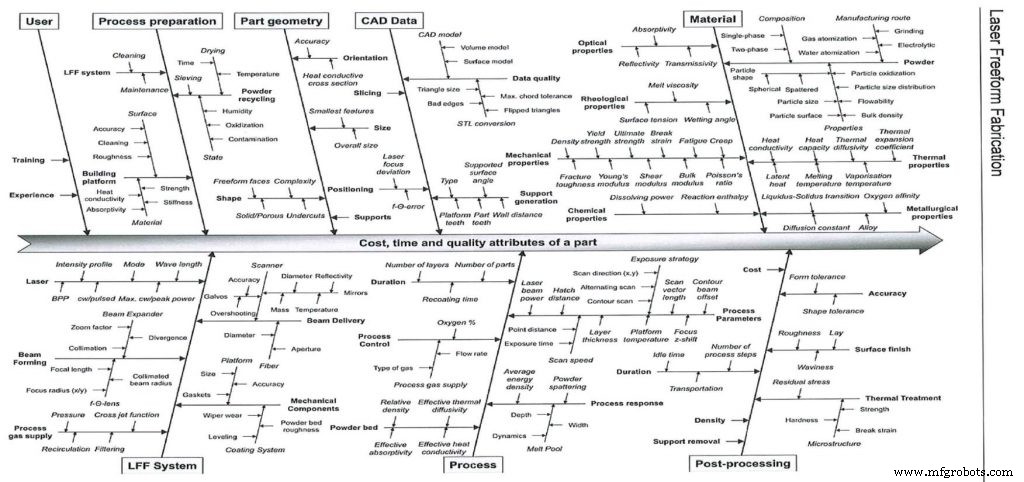
金属3D印刷、特に粉末床溶融技術に関しては、部品の形状と構造に影響を与える可能性のあるさまざまな変数があります。これらの変数は、設計からビルドの準備、後処理まで、AMワークフロー全体に及びます。
例として、印刷プロセスを取り上げましょう。ここでは、プロセスの成功または失敗を決定するパラメータの一部に、レーザーのパスと強度、およびプリンターのリコーターブレードの速度が含まれます。その他の要因には、支持構造の設計や、粉末がリサイクルされた回数などの微妙な点が含まれます。
このリストは網羅的ではありませんが、各要因が結果に影響を与えます。
現在、再現性のあるプロセスを実現するために、さまざまな変数を処理するための最も一般的なアプローチは試行錯誤です。部品。ただし、これには、最終部品の複数回の製造と、部品自体の広範なテストが含まれる場合があります。
もちろん、このアプローチを採用することは非常に費用がかかり非効率的なプロセスであり、技術の主な利点の1つである部品の小さなバッチをコスト効率よく生産できることを打ち消します。
したがって、企業は、プロセス制御と付加的に製造された部品の認定のために、より持続可能で実行可能なアプローチを採用する必要があります。
解決策:閉ループ品質管理システムを開発する
3D印刷された部品のより速く、より信頼性が高く、持続可能な品質保証プロセスを可能にするには、3つの要素を組み合わせる必要があります。これには、ビルド計画、ビルドモニタリング、フィードバック制御が含まれます。
- ビルドの計画
印刷プロセスをよりよく理解する1つの方法は、シミュレーションを使用することです。エンジニアはシミュレーションを使用して、デザインを印刷に送信する前に、仮想のデジタル環境でパーツがどのように動作するかをテストできます。
AMプロセスをシミュレートすることで、エンジニアは印刷プロセス中に発生する複雑なプロセスを分析できます。
金属3D印刷は反りや歪みなどの問題が発生しやすいため、シミュレーションは、たとえば、印刷プロセス中に部品がどのように歪むかについての重要な洞察を提供します。もう1つの例は、シミュレーションを使用して、材料がどのように溶融および固化するかを正確に決定することです。
次に、エンジニアはこのデータを使用してビルドを計画し、最も成功するパーツの方向付けとサポート戦略を選択できます。
そうは言っても、シミュレーションソフトウェアには限界があります。 「今日のすべてのシミュレーションソフトウェアには、提供できる精度を制限するある程度の前提条件が組み込まれています。これがおそらく現時点での最大の欠点です。希望するほど正確ではありません」とANSYSの最高技術責任者であるDaveConoverは、AMFGとの最近のインタビューで述べています。
ただし、シミュレーションテクノロジーは急速に進化しており、ソフトウェアベンダーは引き続き製品を改良しています。最終的には、設計と計画の段階でシミュレーションソフトウェアを統合することで、試行錯誤を排除すると同時に、印刷の失敗の可能性を大幅に減らすことができます。
- ビルドの監視
工程内監視システムは、部品認定プロセスをさらに支援することができます。センサーとカメラを使用して、ビルドの複数の側面をリアルタイムで測定し、ビルドプロセスを文書化し、要件が満たされていることを確認できます。
パウダーベッドAMプロセスを使用すると、カメラは溶融池のサイズと温度をキャプチャできます。これは、微細構造、材料特性、表面仕上げ、および全体的な部品性能に直接影響します。
エンジニア次に、このデータを使用して、反りや亀裂などの欠陥の可能性を予測し、欠陥が発生するかなり前にプロセスに介入できます。このデータは文書化されているため、将来これらの欠陥につながる可能性のあるプロセス条件を回避するのに役立ちます。
現在、AM用に最適化されたインプロセスモニタリングテクノロジーの数は限られています。
Sigma Labsは、インプロセスAM品質保証のソリューションを提供する1つの会社です。アディティブマニュファクチャリング用のPrintRite3D品質保証システムは、PrintRite3DSENSORPAKマルチセンサーとハードウェアをPrintRite3DINSPECTソフトウェアモジュールと組み合わせたものです。
IPQAテクノロジーとして商標登録されているこの多面的な組み合わせにより、センサーデータを使用し、工程内の品質指標を確立して、AMプロセス中に溶融池の状態を最適化できます。プロセスデータの統計分析を使用して、部品の品質に関するレポートを生成し、再現性を検証するために使用できます。
将来、同社はビッグデータ分析の活用に焦点を当てたANALYTICSソフトウェアモジュールを追加する予定です。このモジュールは、印刷プロセス中に収集されたデータから意味のある実用的な情報を抽出して、工程内の品質管理をさらに簡素化することができます。
3Dプリンター自体については、すでにインプロセス監視機能が組み込まれているものもあります。たとえば、3DプリンターメーカーのEOSは、EOSTATEモニタリングスイートを提供しています。ハードウェアとソフトウェアのソリューションは、システムとレーザー、PowderBed、MeltPool、Exposure OT(光トモグラフィー)を含む4つの異なる監視モジュールに基づいており、品質関連のデータをリアルタイムでキャプチャできます。
EOSTATE Exposure OTにより、EOSは、光トモグラフィーを組み込んだ品質保証ツールを顧客に提供する金属粉末ベッドシステムの唯一のメーカーであると主張しています。
この監視システムは、赤外線カメラと同様に、近赤外スペクトルの発光を収集するカメラを使用しています。ジオメトリやサイズに関係なく、ビルドプロセス全体で各パーツをレイヤーごとに完全にマッピングできます。このアプローチにより、エンジニアはAM部品の品質に関連する検出可能な現象の範囲を拡大できます。
MTU Aero Enginesは、AMの連続生産ラインでこの監視ソリューションの使用をすでに開始している企業の1つです。航空エンジン部品。
- ループを閉じる
印刷プロセス中にパラメータを検出して文書化することは非常に重要です。しかし、この情報にリアルタイムで対応する機能(フィードバック制御と呼ばれるプロセス)が、このアプローチをさらに効果的にします。
フィードバック制御は、閉ループシステムとも呼ばれ、印刷プロセス中に偏差を検出し、それらを補正するためにシステムを自動的に調整する機能を指します。ビルドプロセスの制御を維持することで、メーカーは品質を支える一貫した形状、表面仕上げ、および材料特性を実現できます。
フィードバック制御されたAMプロセスを開発した1つの会社は、Velo3Dです。 9200万ドル以上の資金を調達した後、Velo3Dは、エンドツーエンドのメタルAMソリューションである場合、昨年の夏にリリースされました。これは、Velo3D Sapphire 3Dプリンター、Flow印刷準備ソフトウェア、および同社がインテリジェントフュージョンテクノロジーと呼んでいるもので構成されています。
これらの重要な要素が互いに緊密に統合されているため、このテクノロジーにより、熱プロセスシミュレーション、印刷性能予測、および閉ループ制御処理が可能になります。その結果、Sapphireシステムは、サポート構造が実質的にないオーバーハングなどの難しい形状の部品を繰り返し一貫して製造できます。
Velo3DのFlowソフトウェアは、これらのメリットを実現する上で不可欠な役割を果たします。このソフトウェアは、印刷前のシミュレーションと修正を実行し、設計を最適化し、形状と部品の向きを調整します。これにより、ファイルを準備し、変形のバランスを取り、パーツが正しく出力されるようになります。閉ループメルトプール制御を伴う現場プロセス計測は、ソフトウェアと連携して機能し、最終的には前半の成功率を90%以上に高めます。
課題3:ヒューマンエラーの削減
ヒューマンエラーは、3Dプリントされた部品が必要なすべての基準を満たすことを保証する上で、間違いなく最大のリスク要因です。
これは、3D印刷では、サポートの設計と削除から後処理、すべての段階で要件が満たされていることを手動で確認するまで、予想以上に人間の介入が必要なためです。
このレベルの人間の介入は、必然的に最終部分が危険にさらされるリスクを高めます。
例としてポストプロダクションの段階を見てみましょう。
ビルドが完了したら、ビルドを解凍し、そのビルドで印刷されたさまざまなパーツを識別して検査してから、後処理に送る必要があります。
このタスクを実行する制作エンジニアは、通常、印刷されたジョブシートを参照する必要があります。基本的に、2D画像を物理的な対応物と照合し、要件のリストを手動で確認します。
この検査アプローチは時間がかかるだけでなく、ワークフローの可視性を方程式から排除します。
しかし、AMを採用している多くの企業は、マニュアルの変換が難しいと感じています。より速く、より正確な、自動化されたプロセスに関連するタスク。
3D印刷された部品の品質を確保するには、人為的ミスの可能性を減らすことが非常に重要であるため、これを実現する1つの方法は、デジタル手法を使用して可能な限り多くの検査ステップを自動化することです。
解決策:積層造形用のワークフローソフトウェアを実装する
ワークフローソフトウェアは、プロジェクトチームと生産チームがAM生産プロセスを管理するのに役立つデジタルの集中型プラットフォームを提供します。
品質保証のコンテキストでは、ワークフローソフトウェアは、多くの場合、企業がすべての部品の要件を確実に満たすのに役立つ完全なフレームワークを提供できます。
さらに、生産管理者はワークフローソフトウェアを使用して、部品の検査プロセスをペーパーレスで追跡可能にすることができます。手元にあるジョブシートの各パーツを手動で検査する代わりに、物理的なパーツを3Dのデジタル対応パーツと比較できます。
たとえば、AMFGのポストプロダクション管理ツールは、すべての部品データを含む3Dビューアを提供し、ユーザーが部品とそのプロパティをより正確に検査できるようにします。
このツールを使用すると、ユーザーは成功した部品と失敗した部品の比率を追跡できます。故障とマークされた部品は、プラットフォームの内部生産キューに自動的に戻され、複製されます。これの最大の利点は、ユーザーが部品に対して実行された各アクションを追跡できるようにすることです。これにより、品質管理の必要性にトレーサビリティと説明責任が追加されます。
AMに関する業界全体のQA基準はありますか?
これまでのところ、プロセス、材料を認定し、デジタル戦略を実装する方法を理解することが、企業が生産のために3D印刷の恩恵を受けることができるようにするための鍵であることがわかりました。
業界全体の基準は、このプロセス。従来の製造では、標準はすでに一般的であり、企業が製品の品質を確保し、共通点を見つけるのに役立ちます。もちろん、従来の製造では、関連する標準を開発するために、数世紀とは言わないまでも数十年かかりました。
対照的に、3D印刷はまだ比較的新しいプロセスであり、多くの規格と認証がまだ開発中です。今後、業界は、AMの材料、プロセス、および部品を認定するためのコストと時間を削減するために、テスト方法、プロトコル、および参照データを開発する必要があります。
幸い、これは急速に進化している分野です。ちょうど昨年、AMST InternationalはF3303規格を発表しました。これは、レーザーまたは電子ビーム粉末床溶融を使用して部品を製造するために使用される機械とプロセスを認定する方法の概要を示しています。また、部品の認定、品質保証、および粉末床溶融部品の後処理をサポートするための追加の基準がすでに進行中であることにも留意されました。
ASTM Internationalと並んで、米国国立標準技術研究所(NIST)は、AM業界のQA標準開発に取り組んでいます。たとえば、NISTは、「堅牢な後処理測定を作成し、機械的性能を深く理解し、AM部品を認定するために必要な測定、方法、および計測システム」に焦点を当てたAM部品認定プロジェクトを立ち上げました。
品質に注意を払う
3D印刷で一貫して高品質の金属部品を製造するには、材料の品質とプロセス制御を確保することが重要です。
これは最初は複雑に思えるかもしれませんが、業界全体の標準の継続的な開発に支えられた品質保証プロセスをサポートするソリューションが存在するため、メーカーは心を留めることができます。
これらの課題に取り組み、会社に適切なソリューションを戦略的に実装することで、価値が高く要求の厳しいアプリケーション向けの3D印刷のメリットを大いに活用できます。
3Dプリント
- 高融点金属粉末は、3Dプリントの原料となることが期待されています
- 高融点金属粉末VS3D印刷技術
- AMにとって新しい金属印刷技術が何を意味するかを考える
- リアルタイムの品質管理:どのシステムがあなたに適していますか?
- 金属を使用した3D印刷のサポート構造—より簡単なアプローチ
- H.C. StarckのAMPERPRINT:金属3D印刷用の新しいツール
- 2020年に使用できる金属3D印刷粉末は何ですか? [ガイド]
- 金属3D印刷に関する6つの重要な設計上の考慮事項
- Scalmalloy:金属3D印刷用の最新の高性能素材
- ダイレクト メタル レーザー焼結 3D プリントの設計のヒント
- 技術の概要:金属 3D プリントを実際に使用する必要がある場合