バインダー ジェッティングの概要
バインダージェッティングとは? 1993 年、マサチューセッツ工科大学は、さまざまな材料から複雑な部品を印刷するために、この粉末床インクジェット形式の 3D 印刷を開発しました。現在、いくつかの業界でバインダー ジェッティングの用途があり、金属部品から大型の砂型鋳造コア、フルカラー プロトタイプまで、あらゆるものを作成できます。バインダー ジェッティングは高速で費用対効果に優れていますが、多くの製品チームはこの製造プロセスに慣れていません。知っておくべきことは次のとおりです。
バインダージェッティングとは?
他の多くの 3D プリント方法では、1 つのノズルまたはレーザーを使用してパーツをレイヤーごとに作成しますが、バインダー ジェッティングでは、液体バインダーを粉末層にスプレーします。実際、バインダー ジェッティング 3D プリント プロセスは、2D プリンターが紙にインクを追加する方法に似ています。主に金属、砂、セラミックの印刷に使用され、速度、手頃な価格、大型部品の印刷能力で知られています。
バインダー ジェッティング プロセスを開始するには、パーツのデジタル モデルを作成し、スライスして、製造パートナーに送信する必要があります。次に、バインダージェットプリンターに入力します。次に、リコーティング ブレードまたはローラーがビルド プラットフォーム上に粉末の薄い層を広げ、インクジェット ノズルを備えたキャリッジが粉末層の上を通過し、結合剤の滴を堆積させます。フルカラーのパーツを作成している場合、マシンはこのステップでカラー インクも堆積します。
ビルド プラットフォームは、モデルのレイヤーの厚さに応じて下がります。ほとんどのフルカラー モデルの層の高さは 100 ミクロン、ほとんどの金属部品の層の高さは 50 ミクロン、ほとんどの砂型鋳造型材料の層の高さは 200 ~ 400 ミクロンです。次に、ブレードまたはローラーが表面を再コーティングし、パーツが完成するまでこのプロセスが繰り返されます。その後、エンジニアはパーツを硬化させて強度を高め、パウダー ベッドのルース パウダーからパーツをそっと解放し、ブラシまたは加圧空気を使用してクリーニングします。
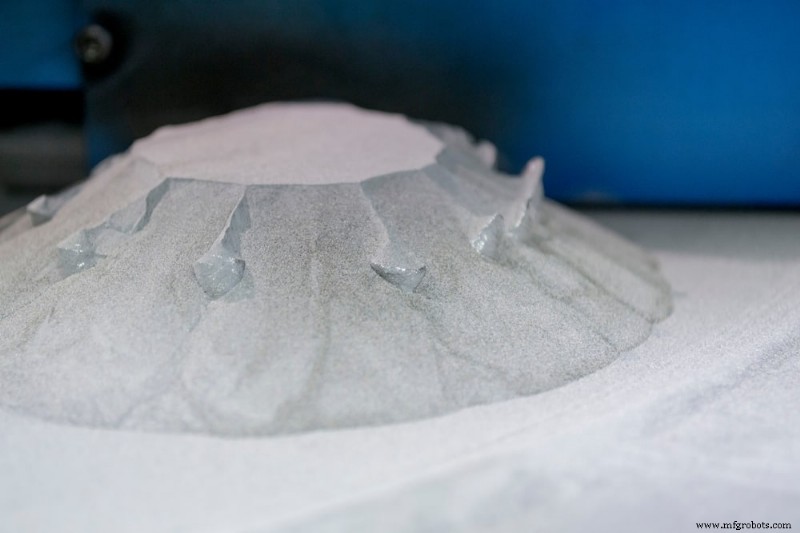
バインダー ジェッティングを使用して作成されたばかりのパーツは、未加工の状態であり、通常、気孔率が高く、機械的特性が劣っています。そのため、エンジニアは造形後にいくつかの後処理ステップを追加する場合がありますが、これはパーツの材料によって異なります。たとえば、金属部品は、青銅のような低融点金属で焼結する必要がある場合があります。フルカラーのパーツがある場合、エンジニアは鮮やかさを向上させるためにアクリルを浸透させることがあります。砂型鋳造の中子または型がある場合は、追加の処理は必要ありません。
一般的な材料バインダー ジェッティング材料
バインダー ジェット材料は、粉末、砂、金属の 3 つのカテゴリに分類されます。
砂岩と PMMA パウダー
バインダー ジェット 3D プリント マシンには、多くの場合、プライマリ プリントヘッドが結合剤を追加するときに色を追加するセカンダリ プリントヘッドがあるため、砂岩またはポリメチル メタクリレート (PMMA) 粉末を使用してフルカラー モデルを簡単に作成できます。ただし、結果として得られるパーツは、処理後でも非常に脆くなるため、地形図や置物などの非機能モデルとして使用するのが最適です。
砂
砂や珪砂は比較的手頃な価格なので、使い捨ての型や中子を作るのに最適です。バインダー ジェッティング サンドを使用すると、従来の方法では作成が困難または不可能な複雑な形状を作成できるだけでなく、± 0.3 mm の寸法精度を達成することもできます。また、次の点にも注意してください:
- 追加の後処理は必要ありません。
- 砂型鋳造の中子と型の層の厚さは、通常 200~400 μm です。
- 造形サイズは 2,200 x 1,200 x 600 mm まで可能です。
メタル
バインダー ジェッティングは、金属の 3D プリントでも一般的な選択肢です。選択的レーザー焼結 (SLS) または選択的レーザー溶融 (SLM) よりも最大 10 倍経済的であり、最大 800 x 500 x 400 mm の比較的大きな造形サイズを提供します。バインダー ジェッティングは、複雑な形状にも対応し、サポート構造を必要とせず、寸法精度は ± 0.2 mm です。
バインダー ジェッティングは、鋼、チタン、クロマイト、銅などと互換性がありますが、使用する金属に関係なく、パーツを後処理して強度を向上させる必要があります。後処理オプションには以下が含まれます:
- 浸透: 溶浸では、硬化した部品を高温の炉に入れます。結合剤が燃え尽きると、パーツの密度は約 60% に低下します。その後、エンジニアは、少なくとも 90% の密度に達するまで、残った空隙を青銅または別の低融点金属で埋めることができます。溶浸パーツは比較的強く、優れた機械的特性を備えていますが、溶浸後は約 2% 小さくなります。
- 焼結: さらに優れた機械的特性が必要な場合は、金属部品を焼結することができます。焼結には、炉内で部品を加熱して結合剤を焼き出し、金属粒子を融合させることが含まれます。焼結部品は高い耐食性と 3% の気孔率を備えていますが、初期サイズから約 20% 収縮することが多いという欠点があります。この収縮は均一ではない可能性があり、デザインがすでに 20% の収縮を占めていたとしても、印刷後に不正確になる可能性があります。
バインダージェッティングの長所と短所
バインダー ジェッティングを選択すると、次のことが可能になります。
- 比較的高い寸法精度を実現: バインダー ジェッティングは室温で行われるため、反りを心配する必要がなく、パーツの寸法精度が高く保たれます。金属をバインダー ジェッティングする場合は、二次的な後処理中に残留応力を緩和することについても心配する必要はありません。ただし、焼結後に収縮する可能性があります。
- 節約: 金属部品のバインダー噴射は、SLM または SLS を使用するよりも 10 倍以上経済的です。手頃な価格であるだけでなく、レーザーの代わりに液体結合剤を使用するため、エネルギーの使用量も少なくて済みます。さらに、バインダー ジェッティング セラミックおよび金属粉末は、通常、SLS および SLM 用の粉末よりも手頃な価格です。同様に、SLS、SLM、またはマテリアル ジェッティングによるフルカラー プロトタイプの作成に通常かかる費用のほんの一部で、バインダー ジェッティングを使用してフルカラー プロトタイプを作成できます。
- サポート構造を忘れる: バインダー ジェッティングでは、結合していない粉末が部品に必要なすべてのサポートを提供するため、サポート構造が不要になり、設計の自由度が高まります。これはまた、他の 3D プリント技術と比較して、後処理時間が短く、材料消費量が少ないことを意味します。
- 無駄を省く: 未使用のパウダーは 100% 将来のプリントに再利用できるため、材料とコストを節約できます。それに比べて、SLS 3D プリンターで使用される粉末の 50% しか再利用できません。
- 大きな部品または複数の小さな部品を同時にすばやく作成: バインダー ジェッティング マシンのビルド ボリュームは最大 2200 x 1200 x 600 mm です。つまり、大きなパーツを作成したり、いくつかの小さなパーツを同時に作成したりできます。
ただし、バインダー ジェッティングを使用する場合に考慮すべきいくつかの欠点があります。次の点に注意してください:
- 金属バインダー ジェッティング パーツは、気孔率が高いため、SLS の対応するパーツよりも機械的特性が低くなります。
- バインダー ジェッティングでは、他の 3D プリント プロセスに比べて材料の選択肢が限られています。
- パーツは緑色の状態では脆いため、大まかな詳細しか印刷できません。
- ほとんどのバインダー ジェット パーツには後処理が必要です。これにより、生産時間が大幅に長くなり、不正確さが生じる可能性があります。
Fast Radius を使用した 3D プリント
バインダー ジェッティングは高速で手頃な価格の技術で、大きなプリントやフルカラーのプロトタイプに最適です。バインダー ジェッティングは、次のプロジェクトに最適なプロセスですか?経験豊富な製造パートナーと協力することで、正しい決定を下すことができます。
Fast Radius の専門家チームは、最新の 3D 印刷技術について長年の経験を持っています。 3D プリント用に設計を最適化し、ニーズに合った材料と 3D プリント方法を選択するなどのお手伝いをします。今すぐお問い合わせください。
産業技術