運用と保守を調整するための完璧な公式
運用と保守がうまく連携しない場合、コストがかかる可能性があります。そして厄介です。例として、食品メーカーのこの話を取り上げてください。
施設は、生地の巨大なボールを転がすシーターを使用しています。シーターは毎日掃除する必要があります。生産チームは定期的に機械を水で洗浄します。これには1つだけ問題があります。水によって生地が固まり、機械が壊れます。結果として、緊急メンテナンスが標準です。
この状況があなたに馴染みがあると感じたら、あなたは一人ではありません。それは1日に何千回も起こります。運用と保守には、異なる目標、動機、およびプロセスがあります。その結果、混乱、欲求不満、指さしが発生します。これはビジネスや従業員の健康には良くありません。
この記事は、そのサイクルを断ち切り、運用と保守の間の調整を改善する方法を学ぶことについてのすべてです。これには以下が含まれます。
- 共有する指標
- コラボレーションを強化する方法
- 共同プロセスを構築するためのヒント
運用と保守の調整を最優先すべき理由
廃棄物の削減に取り組んでいるメーカーは、パックをリードしているか、フィールドから脱却しようとしています。その証拠として、製造業者が費やすすべてのドルの20%を浪費しているという事実にほかなりません。
これらの恐ろしい統計(automation.comの提供)によって強調されているように、廃棄物は生産中にしばしば現れます:
- 大規模な産業施設では、計画外のダウンタイムにより、年間323時間以上の生産が失われます
- ダウンタイムの平均年間コストは、1時間あたり532,000ドル、またはプラントあたり1億7,200万ドルです
- Fortune 500メーカーのダウンタイムのコストは、年間収益の8%に相当します
莫大な費用は一つのことです。ただし、作業の遅延、事後対応型のメンテナンス、緊急購入には、精神的および肉体的な負担もあります。
運用と保守の関係を改善することは、その発生源でのダウンタイムを削減するために重要です。
「メンテナンスと運用が連携していると、ビジネスは運用内の問題を見つけることができます」と、FiixのシニアソリューションエンジニアであるJasonAfaraは述べています。
「そして、ビジネスリーダーは、適切なリソースを使用してこれらの問題を修正する方法について、情報に基づいた決定を下すことができます。推測ゲームと非難ゲームを統一された取り組みに変えます。」
運用と保守のプロセスを調整する場所
計画されたダウンタイム
効率的なメンテナンスの定義は、可能な限り少ないダウンタイムで機器を稼働させ続けることです。もちろん、これは口で言うほど簡単ではありません。制作チームには、埋める割り当てがあります。そのターゲットを攻撃するのを邪魔するものはすべて脅威です。これにはメンテナンスも含まれます。
「私たちは、マシンのメンテナンスを少し行うためだけにオペレーションと戦います」と、メンテナンスマネージャーとしての時間を思い出しながらジェイソンは言います。
これは非常に一般的で非生産的です。幸いなことに、保守と運用で両方のグループに利益をもたらす予防保守の計画を作成する方法は2つあります。
- データを使用して、メンテナンスの影響と障害の影響を比較します
- スケジュールされたダウンタイムの量を減らす共有プロセスを開発する
最初のステップは、両方のチームがそれぞれの活動が機器のパフォーマンスにどのように影響するかを理解することです。繰り返しになりますが、多くの場合、思ったよりも複雑です。
「これは通常、メンテナンス部門が失敗する場所です」と、33年以上のメンテナンスの経験を持つFiixのシニア実装コンサルタントであるCharlesRogersは言います。
「彼らは彼らの質問をバックアップするためのデータを持っていません。自分のケースを証明し、スケジュールどおりにメンテナンスを行わないと、ある時点で、おそらくより早く、より悪い結果が生じるという証拠を示す必要があります。」
あなたの努力を調整する最良の方法は、1つのチームとして許容できるリスクと失敗の結果を決定することです。一般的な障害モード、それらが発生すると予想される頻度、およびそれぞれの修理時間とコストに関する情報を共有します。これを、定期メンテナンスの頻度、これらのタスクの実行にかかる時間、および関連するコストと比較してください。
違いを定量化することで、メンテナンスのために生産の頻繁な休憩をスケジュールすることが、両方のチームが目標を達成し、時間のかかる大きな故障を回避するためのより良い方法であることが明らかになります。
このFMEAテンプレートを使用して、障害のリスクを計算し、メンテナンスに優先順位を付けます
運用と保守の間で共有プロセスを作成すると、チームはデータを共有してアクションを実行できます。たとえば、オペレーターは小さな障害を検出し、保守技術者はそれらに迅速に対応できます。これらのプロセスの例は次のとおりです。
- 運用および保守リーダー間の定期的な会議で、生産および予防保守のスケジュール、マシンの仕様変更、またはその他の更新について話し合います
- 成功、課題、解決策、根本原因分析について話し合うための2つのチーム間の四半期ごとの会議
- 機械のオペレーターが問題を迅速かつ自信を持って特定し、技術者が最小限の中断で問題に優先順位を付けて対応できるようにする作業要求プロセス
共有作業と明確な責任の作成
運用と保守が連携して機能することに言及すると、必然的に総合的生産管理(TPM)の話につながります。ここでTPMの簡単な入門書を読むことができますが、会社の全員(技術者から会計士まで)が責任を持って保守に関与するという考え方です。
運用を保守プロセスの一部にすることは、TPMプログラムの構築を開始するための最も簡単で効果的な方法の1つです。これがどのように行われるかの例です:
<図>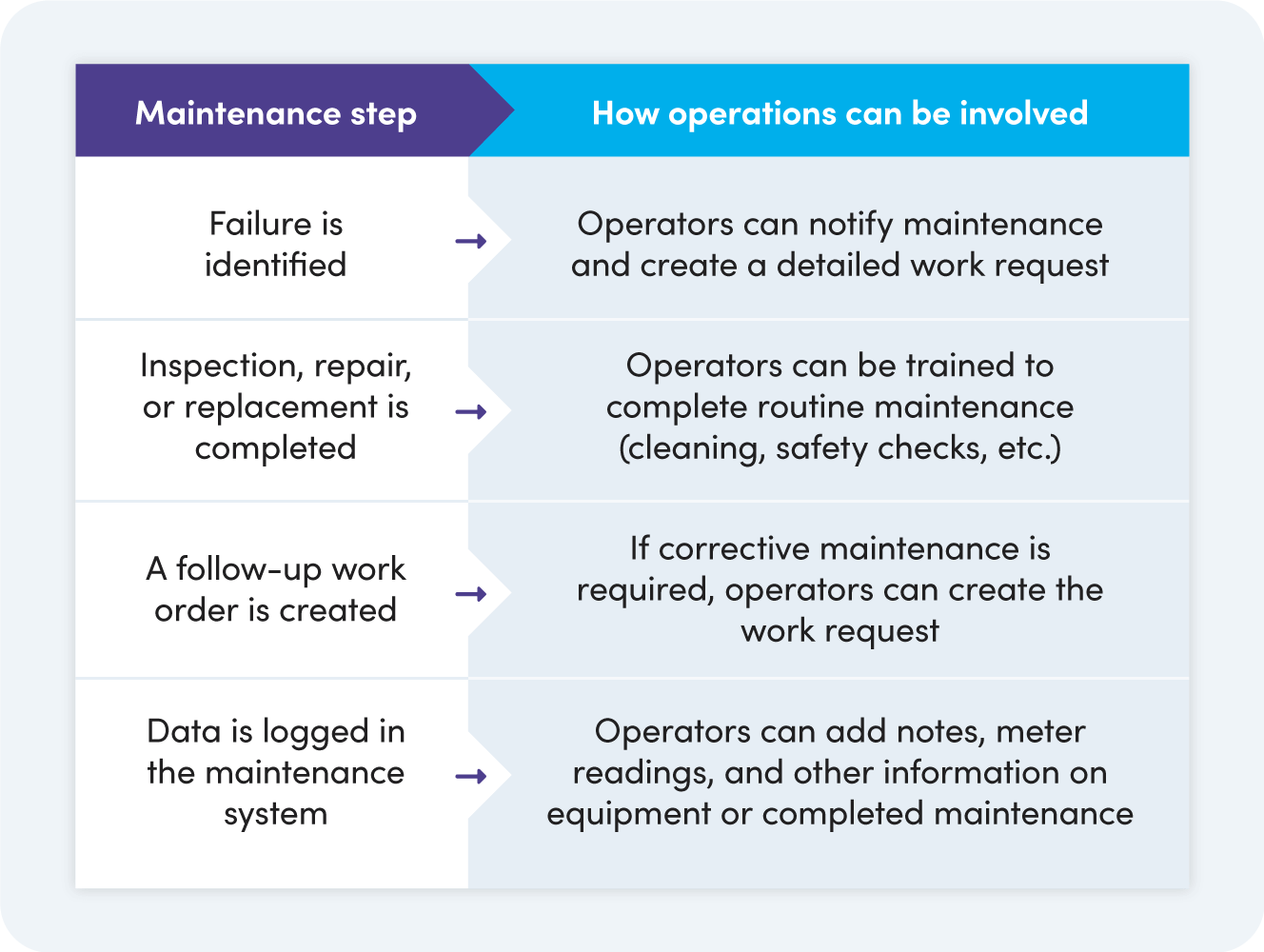
作業指示書を使用してTPMプログラムを開始する12の方法
これらの共有プロセスを成功させるための鍵は、明確な職務責任を作成することです。人々が何をする必要があるかを正確に知っているとき、それはあなたを助けます:
- 適切なトレーニングと資料を適切な人々に提供する
- 正確なスケジュールと予算を作成する
- 新しいプロセスをテストし、最適化し、拡張します
- 不良データを選び出し、その根本的な原因を突き止めます
オペレーターのメンテナンスタイプを作成して、明確な責任の定義を開始します。これにより、運用に費やしている作業量を追跡できます。また、作業範囲が変更された場合に何をすべきか、どこに行くべきかをオペレーターが理解できるように、オペレーターの作業指示書テンプレートを設計するのにも役立ちます。
現実的な作業スケジュールの作成
運用と保守が物事を成し遂げるのにかかる時間を知っている場合、それに応じてスケジュール、予算、および目標を設定する方が簡単です。また、目に見えない遅延を防ぎ、フラストレーションを減らし、2つのチーム間の尊敬を育みます。ただし、メンテナンスのタイムラインが正確でない場合は、それらを共有することは役に立ちません。期待が現実と一致することを確認するためのいくつかの戦略があります:
- 機器のメンテナンスログを確認します。予想よりも頻繁に時間がかかる作業を特定し、それに応じてタイムラインを調整します。
- 作業指示データを分析して、必要なフォローアップ保守の割合が高いPMを見つけます。それを運用チームへのブリーフに織り込みます。
- 実際のレンチ時間外にある作業指示書の部分を説明します。これには、部品の回収、安全手順の完了、および機械でのテストの実行が含まれます。
現実的なタイムラインを提供することは、必ずしもあなたのスケジュールが一致することを意味するわけではありません。しかし、それは運用と保守があなたが持っている時間内に何ができるかについて話し合うのに役立ちます。生産のためにどのメンテナンスを犠牲にすることができるかを決定するとき、ここに尋ねるべきいくつかの質問があります:
<図>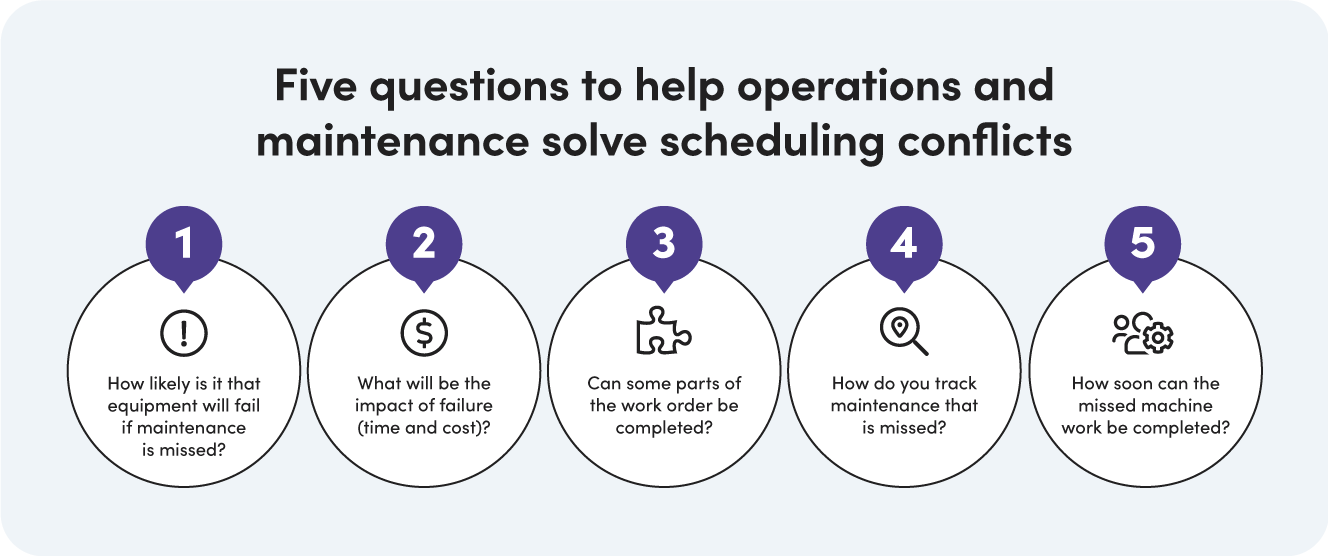
運用と保守の間に強力な関係を構築するための5つの方法
あなたの運用および保守チームは親友かもしれません。あるいは、それらの間にいくらかの緊張があるかもしれません。関係がどのようなものであっても、いくつかの簡単な戦略で関係を改善する機会は常にあります。
2つのチームが通信するための複数の方法を作成します
他のチームとのコミュニケーションは、仕事が忙しくなったときに放棄される最初の活動の1つであることがよくあります。そのため、情報の流れを維持するための正式なプロセスを実施する必要があります。コミュニケーション専用のチャネルの作成には、次のものが含まれます。
- チーム会議:定期的な会議は、全員の声を聞き、課題、計画、更新を可視化するためのスペースを作成します
- 更新を投稿して確認するためのチャネル:これは、ホワイトボードからWhatsAppグループ、またはリクエストのステータスを追跡するためのデジタル作業リクエストポータルまで何でもかまいません
- ピアレビュー:これは、運用チームと保守チームのメンバーが匿名でお互いをレビューして、どのように協力して作業を改善できるかを特定するプロセスです。
これらのチャネルで作業しているときに話し合う重要な情報がいくつかあります。
- マシンの更新:仕様の変更、潜在的な問題、安全上のリスク、または標準的な操作手順の更新を提示します
- スケジュール:今後の作業、リスクまたは対立、成功するために必要なもの、および以前に議論されたものからの変更について話します
- レポート:レポートの目標、進捗状況、問題のある傾向、または主要な成功を確認します
- 障害と解決策:チームが抱える主要な課題や質問について話し合い、それらの障害を取り除く方法について協力します
- 長期計画:予算の管理、長期目標の達成、新しいスキルの開発など、両方のチームが継続的に改善できる方法を理解します。
運用と保守の間のコミュニケーションのフレームワークを持つことで、会話を行動に移すことができます。ここにいくつかの基本的なルールがあります:
- 非難ではなく解決策に焦点を当てる:解決策を見つけることがすべての会話の目標でなければなりません
- 集合体に焦点を当てる:チームのために議論や戦いに勝つことを試みるのではなく、すべての人に役立つ解決策を見つけます
- フィードバックループを作成する:フィードバックを実行し、全員に進捗状況を認識させることで信頼を築きます
- 一貫性を保ちながら柔軟性を維持する:コミュニケーションをとることを約束しますが、緊急事態が発生した場合は、会議をときどき移動する必要があることを理解してください
- すべての会議の議題を作成する:話し合う内容について計画を立てて、全員の時間を最大限に活用できるようにします。
同じ目標を設定する
2つのチームが同じ方法で成功を定義すると、運用と保守の間の摩擦が少なくなります。目標を達成する方法についてはさまざまなアイデアがあるかもしれませんが、両方の部門が同じ方向に進んでいます。
「最悪のシナリオでは、これらの部門は絶えず戦っている兄弟です」とジェイソンは言います。
「しかし、最良のシナリオでは、同じ目標を達成するために協力し、目標を達成したときに一緒に祝い、達成しなかったときに力を合わせて軌道に戻ります。
運用と保守の両方が責任を共有できるいくつかの指標があります:
- メンテナンス後のクリーンなスタートアップとファーストパスの歩留まり/ファーストパスの良好:どちらの数値も、効率と無駄を測定することを目的としています
- 生産単位あたりの総コスト:運用と保守の両方で、品質を向上させながらコストを削減する責任を負うことができます。
- 生産/保守のサポートに費やした時間:各チームが他のチームのサポートに費やした時間を追跡すると、リソースを割り当て、効果的な採用計画を作成するのに役立ちます
- 計画外のダウンタイム(過去90日間):予防保守の影響と、この作業を効率化する共有プロセスを確認してください
- 検出と修復にかかる平均時間:障害が発生する前に、障害を見つけて修正することに誰もが関与し、ビジネスへの影響を最小限に抑えます。
このテンプレートを使用して、運用と保守の間で共有の目標を作成します
生産システムと保守システムを統合する
メンテナンスが故障またはサービスの中断のみにさらされている場合、運用者はメンテナンスについて否定的な見方をするのは簡単です。生産と保守に使用されるシステムを統合することで、各チームの作業を可視化できます。これにより、各部門のプラスの影響を確認し、お互いがさらに多くのことを達成できるようになります。
Ryan Robinsonのメンテナンスチームは、メンテナンスソフトウェアを機器や生産システムと統合することで、驚くべき結果が得られることを示す好例です。卸売樹木生産者の店長であるライアンは、CMMSを使用して複数のマシンのセンサーを接続しました。これにより、メンテナンス間隔を最適化し、生産効率を高めるために必要なデータが得られました。
「私たちは日常的に機器がどのように使用されているかを知っているので、明日、翌日、翌日のメンテナンスに何が期待されるかについてある程度の考えがあります」とライアンは言います。
ライアンは、このデータを使用して、アイドル時間が長い車両を見つけることもできました。彼はこの情報を農場のマネージャーに持ち込みました。農場のマネージャーはその理由を理解し、解決策を見つけました。
ライアンのストーリーを読む
ワールドクラスのメンテナンスチームは運用と連携しています
運用と保守は、多くの資産と大きな生産目標を持つ企業の心臓部です。だからこそ、彼らが健全な関係を築き、協力するための正式なプロセスを構築することが不可欠です。 2つのチームは、目標とするメトリックから使用するシステム、および作業をガイドするスケジュールまで、すべてを共有する必要があります。力を合わせることで、ビジネスが直面する課題とそれらを克服する力をよりよく把握できるようになります。関係者全員にとってメリットがあります。
機器のメンテナンスと修理