製薬プラントの信頼性のケーススタディ
メンテナンスと信頼性の専門家が違いを生むことができます。ほとんどの製造工場では、これは、より多くの完成品(ソフトドリンク、オートバイ、電球、車、カップケーキ、給湯器など)をドアから出すことができる集中的な作業を意味します。
インディアナポリスにあるイーライリリーの生合成ヒトインスリン(BHI)プラントでは、違いを生み出すことがさらに重要になります。
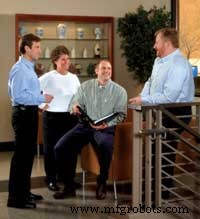
アメリカでは2100万人近く、世界中では2億人が糖尿病を患っています。米国だけでも、毎年100万人近くの新しい症例が診断されています。糖尿病患者の多くは、血糖値(ブドウ糖)を制御するためにインスリンを必要とし、BHI植物はその必要を満たすのに役立ちます。 1992年に生産のために開設されたこのサイトは、世界の薬用インスリンのかなりの割合を生産しています。生産性を向上させるメンテナンスと信頼性の作業により、会社は高品質で生命を維持する薬を必要とする人々の手に届けることができます。
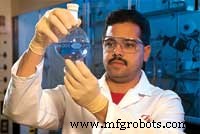
コンピューターチップやポテトチップスを製造している会社で働いているかどうかにかかわらず、利害関係者や経済に付加価値を与えるとき、それは決して軽視することはできません」と、プラントの保守および信頼性チームリーダーであるケンスワンクは言います。 「あなたが何をするかは問題ではありません。それは重要です。ただし、明確な違いが1つあります。私は工業用コーティング会社で働いていました。私たちのコーティングは、ゴルフボールからスペースシャトル、手術器具まで、あらゆるものに使用されました。最終製品を見ると、自分がその一部であることがわかりました。しかし、あなたが製薬会社で働いているとき。 。 。それは個人的なレベルで多くのことを意味します。
私は週末に幼い息子を持つカップルに会いました。話をしましたが、その少年は糖尿病であることがわかりました。私は彼が1型か2型かを尋ねました。父親は、糖尿病についてどうやってそんなに知っているのですか?その少年は彼がタイプ1だと私に言った。私は彼を見て言った、「私が生計を立てるために何をしているのだろうか?インスリンを作ります。私はイーライリリーで働いて、フムリンを作っています。」彼は言った、「ありがとう。私は自分の薬が本当に好きです。気分がとても良くなります。」
「私の部署は、この建物が毎回作るはずの薬を作っていることを確認する責任があります。それに依存し、毎日それに手を伸ばす何百万もの人々がいます。」
会社のインディアナポリスキャンパスには、
製造サイトと企業オフィスがあります。
需要の増加
BHIプラントは大きく、技術的に複雑です。 17,000を超える機器、13,000の入出力ポイント、600のオペレーティングユニットを収容しています。 BHI分子を生成するための処理方法には、いくつかの遠心分離ステップ、少数の反応、多くの精製ステップ、およびさまざまな溶媒交換ステップが含まれます。その結果、オペレーティングユニットの約3分の1が、ハイリスクまたはセーフティクリティカルなオペレーションに分類されます。
数年前、メンテナンスと信頼性のリーダーは、部門の時間、スキル、リソース、およびプラントへの潜在的な影響を最大化するために、大幅な変更を実施する必要があると判断しました。 BHIは当初の設計能力の2倍以上で稼働しており、ビジネス需要は増加し続けました。技術者は過剰にコミットされ、現在のニーズに対応するために修復作業の優先順位が頻繁に変更され、重要なシステムがかなりの割合で注目されていませんでした。
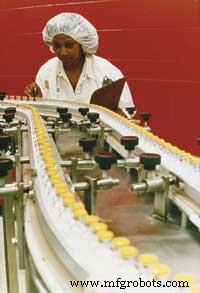
設備が適格な状態で動作することを心配したことはありません」とSwank氏は言います。 「しかし、当時の他の製薬業界と同様に、私たちは、最大限の薬を作るために可能な限り多くの稼働時間を常に望んでいたことを除いて、機器に特別な重点を置いていませんでした。しかし、できるだけ多くのキロを戸外に出すことを検討すると、「施設を追加し続けるのか、それともビジネスの観点からスマートに行い、信頼性に重点を置くのか」という疑問が生じます。」
>これは、1990年代後半にイーライリリーの多くの施設が熟考していたことでした。たとえば、BHIのエンジニアリングマネージャーであるRon Reimerは、会社のClinton(Ind。)Laboratoriesサイトにいる間、プロアクティブな作業と稼働時間を増やし、メンテナンスコストを削減する取り組みを主導しました。そのプロジェクトの一環として、その後体系化され、プロアクティブアセットマネジメントと呼ばれるようになり、彼は会社の最初の信頼性エンジニアを雇いました。
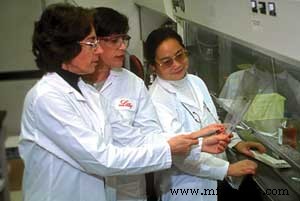
プラントの信頼性におけるすべての主要な利害関係者からの直接の関与
(生産、 HSE、品質管理、財務、エンジニアリング、および
管理)は、信頼性の優先順位付けイニシアチブの成功を確実にするのに役立ちます。
BHIの強化の取り組みは、1999年に信頼性エンジニアが追加され、信頼性中心のメンテナンス(RCM)および根本原因障害分析(RCFA)プロジェクトが導入されたことから始まりました。これらの取り組みは、食品医薬品局や環境保護庁などの規制当局が製薬業界のメンテナンスを綿密に調査し始めたときに増加しました。機関のメッセージは単純でした。メンテナンスはプラントの信頼性に等しい。プラントの信頼性は製品の信頼性と同じです。全体的な信頼性はコンプライアンスに匹敵します。 「信頼できない」企業は、業務の停止などの罰則に直面する可能性があります。
私は彼らが理解するのを助けるためにかなりの量のダンスと歌をしなければなりません。しかし、すべてのアカウントから、賛同は良好でした。」
「その時、信頼性が今日の焦点になり始めたと思います」とスワンク氏は言います。「真に信頼できるプラントになるための私たちの旅のビジョンは、生産が機器は、認定された状態であり、必要なときに利用可能であり、所定のパフォーマンスレベルで実行されます。私たちは明らかにその中で大きな役割を果たします。私たちがまとめたメンテナンス戦略は、その機器を適格な状態。また、保守戦略の深さは、必要な使用率または稼働時間に対応します。施設内には、他よりも実行が多い、他よりも冗長性が低い、または他よりも重要な操作があります。これらには、より注意を払い、より詳細な調査が必要です。 。」
2004年の初めに開始された優先順位付けイニシアチブは、この戦略の中心であり、最も注意を払う必要のあるオペレーティングユニットに稼働時間と信頼性を提供します。
- RCFA、FMEA、RCM分析、リード偏差調査などを介して機器の故障を最小限に抑えます。
-
信頼性の取り組みとリソースを最適化するための指標を開発します。 -
新規および既存の機器の独自の保守計画(レビュー/生成/承認)。 -
フロー全体に影響を与える信頼性に重点を置いたプロジェクトを提供します。 - 機器の可用性を高めるために、メンテナンスと信頼性に焦点を当てたビジネス慣行。
-
メンター信頼性技術者。 - コントロールルームチームと統合して、ビジネスを効果的にサポートします。
- 新しいテクノロジーを探して実装し、機器のパフォーマンスと可用性を向上させます。
-
サイトのイニシアチブをサポートします。 -
CMMSデータ入力フォームに記入して処理します。 - 信頼性エンジニアをRCFA、データマイニング、FMEA、RCM、逸脱、変更管理、現場検証、CMMSデータの改善などで支援します。フォント>
-
特別なプロジェクト–信頼性の取り組みなどをサポートします。
優先する
スワンクは、最終的に信頼性の改善につながるであろう行進命令について語ります。
「当時の上司は、「BHI施設の信頼性を高める方法を考えてください。これを理解する必要があります」とスワンクは言います。 「彼が本当に言いたかったのは、「あなたとあなたのチームは、施設のビジネスニーズを理解し、正しく優先順位が付けられた信頼性のギャップを修正し、それをビジネスに売り、実行し、作成するための道を設定する方法を決定する必要があります。持続可能です。」
簡単そうに聞こえるか、彼は考えました。
「私たちは2月(2004年)に開始し、3月または4月に完了すると想定していました」と彼は言います。 「これは予想よりも複雑で複雑であることにすぐに気づきました。さらに、私たちはそれを正しくやりたかったのです。」
ゲームの計画は、既存のデータを使用して、部門の日常的なサポート作業以外の継続的な改善作業としてシステム修復を優先する分析を開発することです。分析要件は次のとおりです。
- 特定されたシステムを取得し、データに基づいてビジネスへの影響に応じてランク付けします。
- すべての利害関係者が代表されます;
- 分析は1週間(40時間)未満で実行できます。
この課題は、部門の信頼性エンジニアリング部分の肩にかかっていました。このグループには、上級信頼性エンジニアのMark Lafever、Vadim Redchanskiy、Rod Matasovsky(現在は引退)、信頼性エンジニアリング技術者のDavid Doyle、Mary Ann Dust、Matt O’Dellが含まれていました。彼らは分析の内容を戦略化し始めました。
「彼らは賢い人です。私は経営陣からフロアの人たちへの翻訳者でした」とスワンクは言います。 「彼らはデータシステムを理解し、何が理にかなっていて何が理にかなっていないかを理解しました。」
このグループは、このイニシアチブのサポートを得るためには、分析は事実に基づく必要があり、プラントの信頼性、つまり生産におけるすべての主要な利害関係者に直接関与し、意味を持つ必要があることを認めました。健康、安全および環境(HSE);品質管理(QC);ファイナンス;エンジニアリング;と管理。これは信じられないほどのバランスを取る行為になるでしょう。
「誰でも外に出て大量のデータを引き出すことができます」とLafever氏は言います。 「データをどこから取得するか、どのように取得するかを決定し、正しい決定を下すために必要な情報がデータから得られるかどうかを判断する必要がありました。」
表1.5つのシナリオの重みの要約。
表2.最初のシナリオの感度分析の例。
何度か繰り返した後、そして「頭を悩ませた」とLafever氏は言います。チームは、過去12か月の既存のデータを使用して、利害関係者を考慮に入れた分析を完了しました。このデータには次のものが含まれます:
1)生産を満たすための、機器のダウンタイムに相当する緊急作業の時間。これは、各オペレーティングユニットに対して請求されたすべての時間を追跡するプラントのコンピュータ化された保守管理システムから収集されました。緊急作業は「待ちきれない仕事」と定義されました。システムのダウンタイムの従来の測定ではありませんが、これは、システムが適切に機能していなかったときに感じた中断の量と直接相関します。
2)HSEを満たすための、リリーのグローバル統合プロセス安全管理(GIPSM)によるリスク分類。分類システムには4つの可能性があります。セーフティクリティカルな操作、最大のリスク要因。かなりの環境、健康および火災のリスクを伴う高リスク。労働安全衛生局によって定義された機械的完全性。リスクがない、または「上記のいずれでもない」。
3)QCを満たすための機器の故障によって引き起こされたプロセスへの逸脱の数。これは、オペレーターのエラーやその他の機器以外の問題ではなく、機器の信頼性の問題の結果である、対象となる逸脱です。逸脱の数は、製品の品質に対する逸脱の影響を特定するレベル(1、2、または3)とともに考慮されました。
4)財政を満たすための事後対応作業のコスト。これもまた、オペレーティングユニットに対するすべての予算料金を追跡するCMMSから取得されました。このコストには、システムで行われた事後対応作業に関連するすべての部品と労力が含まれています。
5)エンジニアリングを満たすためのプロセスエンジニア入力。各システムを担当するプロセスエンジニアは、システムの使用年数、システム障害によって発生する可能性のあるダウンタイムの時間、規制への影響などのトピックについて調査されました。
6)エンジニアリングを満足させるための、システムの保守計画の状態。これは、次の4つのレベルを含むように作成されました。レベル1、定期的なメンテナンスは行われていません。これは最も厳しいと見なされました。レベル2、予防保守がシステムに存在します。レベル3、定期的な資格評価(PQE)は、システムが常に資格の状態にあり、使用に適していることを確認するように設計されており、実行されます。レベル4では、RCMベースの分析がシステムで使用され、保守計画が生成されました。
このデータは、420のオペレーティングユニットを調べ、生産を停止するか、OSHAまたはEPAの報告可能なインシデントを引き起こす可能性のあるユニットを特定する「重要な機器」の評価を作成しました。
「CMMSで構造を設定する方法、およびインシデントデータベースを制御する方法、オペレーティングユニットが最善の方法でした」とLafever氏は言います。 「場合によっては、オペレーティングユニットは機器の一部です。ほとんどの場合、これは主要な機器であり、さらに多くの機器があります。」
たとえば、Redchanskiyによると、オペレーティングユニットEV1411(蒸発プロセス)には、「バルブ、熱交換器、ポンプなどの50〜60個の機器と計装」が含まれています。
評価により、最初のリストが420オペレーティングユニットから135オペレーティングユニットに70%削減されました。
「この分析を行う前に、生産について話し合ったのは遠心分離機だけでした。フロントエンド」と、イーライリリーメンテナンスおよび信頼性チームリーダーのケンスワンクは述べています。 「分析して、私たちが思いついたものを示した後、遠心分離機は(135のオペレーティングユニットのリストで)63位にランクされていることを指摘しました。彼らはそれについてあまり質問しません。
「これにより、生産設備の定義の外側も見ることができます。分析の前に、人々は廃棄物タンクやエアハンドラーなどを含めるのを忘れていました。彼らは、すべての床排水路が行くコントロールルーム2のタンク1099については考えていませんでした。フラッシュは排水口を通ってタンクに入ります。そのタンクが機能していない場合は、精製ステップをシャットダウンする必要があります。」
重みと測定値
残りの135ユニットの適切な優先順位付けを確実にするために、グループは各データソースに均等化を適用することを決定し、少数の感度分析を実行しました。
「6つの基準が同じように重み付けされているとは感じませんでした」とスワンクは言います。 「安全性と品質は、たとえば緊急時の作業に費やした金額よりも大きな影響があると感じました。」
スコアリングシステム(0から3、0が最小の影響と重大度、3が最大の影響と重大度)が各データセットに対して開発され、各オペレーティングユニットに適用されました。内訳は次のとおりです。
緊急作業時間(HEW) :15時間未満(ゼロのスコア)、15〜25時間未満(1)、25〜40時間未満(2)、および40時間以上(3)。
リスク分類(RC) :HSEリスクなし(ゼロ)、機械的完全性システム(1)、高リスクプロセス(2)、およびセーフティクリティカルオペレーション(3)。
偏差(D) :偏差のレベルと数を考慮して、4つのグループ化が行われました。レベル2の偏差はレベル1の偏差の3倍に等しく、レベル3の偏差はレベル2の偏差の2倍に等しいと判断されました。これにより、レベル1の偏差は1ポイント、レベル2の偏差は3ポイント、レベル3の偏差は6ポイントになります。これはすべての偏差に適用されました。その結果、値は2以下(ゼロ)、2から5まで(1)、5から8より大きく(2)、8より大きく(3)でした。
事後対応作業のコスト(CRW) :5,000ドル未満(ゼロ)、5,000ドルから7,499ドル未満(1つ)、7,500ドルから14,999ドル(2つ)、15,000ドル以上(3つ)。
プロセスエンジニア入力(PEI) :最小影響システム(ゼロ)および最大影響システム(3)にエスカレートします。
システムの保守計画(SSMP)の状態 :システムで実行されたRCM分析(ゼロ)、定期的に実行されたPQE(1)、実行されたPM(2)、定期的なメンテナンスは実行されなかった(3)。
スコアは135のオペレーティングユニットに適用されました。次に、情報がスプレッドシートに読み込まれ、さまざまなデータセットの重要性を強調するためにさまざまな重みが適用されました。感度分析プロジェクトには、単一のデータポイントがシステムの優先順位付けを推進していないことを確認するために、5つの異なる重み付けシナリオが含まれていました。
シナリオは、かなり均等な重み分布(HEW、HSE、D、SSMP、それぞれ20%、CRWとPEI、それぞれ10%)から、2つのカテゴリ(HEW、HSE、D、CRW、それぞれ20%、PEI)の排除までさまざまでした。およびSSMP、ゼロパーセント)。後者のシナリオでは、残りのデータセットは、システムによって実証された信頼性のレベルに応じて変化する「真のデータ」でした。シナリオを表1に示します。
感度分析の各シナリオでは、リスクファクターを取得し、その特定のシナリオの重み付けを掛けました。各カテゴリの製品は、各オペレーティングユニットについて合計されました。表2に、最初のシナリオの例を示します。
5つのシナリオがすべて完了すると、オペレーティングユニットの最終スコアがグラフ化され、信頼性チームによって調査されました。最終的なランキングと修復計画を決定する前に、追加の要因が考慮されました。問題のユニットは最近交換されましたか、それとも資本計画の交換ですか?このユニットの修復計画を他のユニットに適用できますか?この修復にはどのような官能基が必要ですか?それらは利用できますか?過去にどのような修復活動が行われていますか?
「たとえば、遠心分離機の1つがリストの一番上近くに出てきましたが、別のサイトが非常によく似たシステムでRCMを実行していることはわかっていました」とSwank氏は言います。 「努力を繰り返す必要はありませんでした。」
提案された修復アクティビティの最終的なリストは、オペレーティングユニットによって、詳細なRCM分析から、システムをまったく修復しないものまでさまざまでした。
その時点で、チームは包括的な計画があることを知っていました。
「それはグラインドでした」とLafeverは言います。 「私たちは3回計画を立てました-それは30のように感じました-そして私たちは「これは十分ではありません」と言い続けました。「品質管理はこれについてどのように感じますか?」「プロセスエンジニアリングはこれについてどのように感じますか?」非常に当惑しました。すべての側面とすべての潜在的な質問に確実に対処する必要がありました。」
スワンク氏は、次のように付け加えています。大変な作業です。このようなものからあなたを引き離し続ける日常的なものもあります。しかし、私たちはそれに固執してそれを成し遂げるつもりだと自分自身に言い聞かせました。」
書面で
2004年9月21日、Swankは、サイト長とすべての機能マネージャーを含むプラントのリードチームに優先順位付けモデルを正式に提示しました。疲れ果てた7か月の仕事は報われました。
「物々交換や話し合いはありませんでした」と彼は言います。 「彼らは、 『これは素晴らしい。続行します。」
もちろん、頭のうなずきと手の波はここまでしか行きません。そこで、SwankはLafeverに、評価プロセスを要約し、重要な機器分析が毎年どのように実行されるかを詳細に説明したレポートを作成させました。レポートは、将来の評価のテンプレートとして機能します。
「私はリードチームのメンバーに署名するように言いました」とスワンクは言います。 "彼らがやった。私はそれを書面で持っています。ためらうことはありませんでした。これは、私たちが行った分析が非常に強力であったことを示しています。」
2005年2月28日、重要な機器の分析が正式に行われ、リードチームによって承認され、プラントの最も重要なオペレーティングユニットの修復活動がプラントの2005年と2006年の事業計画に含まれました。
テンプレートにより、その後の評価はほぼシームレスになりました。
「昨年、分析を行うのは簡単でした」とLafever氏は言います。
2006年の計画は5月に完了しました。
レメディの結果
このイーライリリー工場の保守および信頼性部門のリーダーは、現在、信頼性優先順位付けイニシアチブの最終的なドルとセントの影響を定量化できないと述べています。
「残念なことに、私たちの仕事の結果が毎年見られるとは限りません」とLafever氏は言います。 「システムの処理に時間がかかるため、1年遅れる可能性があります。」
しかし、それは利益と結果がなかったという意味ではありません。
RedchanskiyとDoyleは、特定の資産のメンテナンスがどのように実行されるかを再評価するだけで、必然的なコスト削減が可能になると述べています。
「分析の結果、事後対応型の作業が行われていないいくつかのシステムにかなりの金額を費やしていることがわかりました」とRedchanskiy氏は言います。 「私たちは予防保守に1トンを費やしました。私たちはPMでそれをやり過ぎました。これらのシステムのメンテナンス方法を変更しました。」
「これからの最大の変化は、一部のシステムでは、障害が発生しても実際には問題ないと言えるようになったということです」とDoyle氏は言います。 「それがその特定のシステムの診断と計画である場合、それは問題ありません。それは私たちにとってまったく異なる哲学です。」
スワンク氏は、プラントの生産性レベルからプラスを引き出すことができると述べています。
「在庫レベルを達成し、ビジネスモデルが生産性の向上に向かっているという事実は、私たちがすでに最初の主要なマイルストーンに到達したことを示しています」と彼は言います。
Lafeverは、修復プロジェクトへの関与が技術的知識の増加と稼働時間の増加につながったと考えています。
「ほとんどの保守および運用担当者がRCM分析から出てきたとき、彼らはそのシステムの専門家として分類される可能性があります」と彼は言います。 「誰もがグループの個々の機能をよりよく理解し、グループがどのように連携して機器の修理や機器に問題があるかを特定する役割を果たしているかを理解しています。その相互作用自体が、発生する緊急作業の量を減らすと思います。」
成功の最良の指標は?
「それは私たちの上級管理職を幸せにします」とドイルは言います。
「そしてそれは私を幸せにします」とスワンクは言います。
これらすべての改善により、BHIが2005年のMaking Medicine Awardを受賞した理由が説明できます。この賞は、「ビジネスのニーズを最もよく満たし、会社での製造業のあり方を具体化した」イーライリリー工場に贈られます。
他のリリー工場は優先順位付けイニシアチブに注目しており、採用の実現可能性を検討しています。これにより、メンテナンスと信頼性について全社的な可視性が向上しました。
「良い点の一部は、メンテナンスが付加する価値に対する企業の理解と認識です」とReimer氏は言います。 「それは私たちが絶対に利用したいものです。」
このチームは、メンテナンスと信頼性の専門家が違いを生むことができること、そして実際に違いを生むことを毎日示しています。
機器のメンテナンスと修理
- ケーススタディ:製紙工場のスリッター巻き取り機のドライブと改造
- ピストンプラントは信頼性とOEEに積極的なアプローチを取ります
- Drew Troyer:ビジネスプロセスが信頼性に与える影響
- プラントの信頼性がリーン実装にどのように影響するか
- ハワイの水力発電所はその効率と信頼性を高めます
- 発電所の信頼性を高めるサウジ電力会社
- ネバダ発電所の信頼性を高める無線システム
- 可用性の向上はメンテナンス以上のものです
- NV Energyは、プラントの信頼性を高めるためにワイヤレスソリューションをインストールします
- ケーススタディ:Machine Down Crisis Solution
- ケーススタディ–プラントからの修理ソリューション:小さなCharmillesパーツは大きな問題を引き起こします