機器の故障の5つの原因(およびそれを防ぐためにできること)
この投稿は元々、CamcodeのNicolePontiusによってゲストブログとして作成されました。 2019年6月にFiixチームによって編集および更新されました。
- 機器の故障の5つの一般的な原因
- 原因#1:不適切な操作
- 原因#2:予防保守を実行できない
- 原因#3:予防保守が多すぎる
- 原因#4:機器を継続的に監視できない
- 原因#5:信頼性の文化が悪い(またはない!)
- 収益
機器の故障が発生します。その影響は、修理コスト、総ダウンタイム、健康と安全への影響、サービスの生産と提供への影響などの要因に応じて、最小限の損失で簡単に修正できるものから壊滅的なものまで、あらゆる範囲に及ぶ可能性があります。
機器が故障する一般的な理由はいくつかあります。機器が故障する理由を理解することが、計画外のダウンタイムの深刻な結果に対する最初の防衛線です。
これらの7つの秘密を使用して、ダウンタイムを削減し、失敗に勝ちます
ビート機器の故障
原因#1:不適切な操作
日常的に機器の中や周囲にいて、全体的な動作状態に大きな影響を与える可能性のある人がたくさんいます。
機器オペレーターはそのようなグループの1つです。彼らは通常、適切な操作手順、基本的なトラブルシューティング、および作業するマシンに関連する安全な機器の使用に関するベストプラクティスに関する詳細なトレーニングを受けます。ただし、オペレーターが適切なトレーニングを受けていないマシンで作業することになった日が来るかもしれません。この状況は、人員不足や予期せぬ欠勤の結果として発生する場合があります。また、最も経験豊富なオペレーターが持っているレベルの専門知識を必ずしも持っていない可能性のある利用可能なスタッフによる迅速な修復を必要とする緊急事態が発生します。
これらの問題の1つの解決策は、スタッフ不足の緊急事態に備えてある程度の柔軟性と緊急時対応計画を可能にするために十分な訓練を受けたオペレーターを確保することです。可能であれば、すべてのオペレーターは、通常は使用しない資産であっても、すべての機器についてトレーニングを受ける必要があります。
最も重要なことは、オペレーターが実行する資格のない機器を使用することを決して許可しないことです。これは運用上のエラーを減らすのに役立つだけでなく、一部の業界では、規制への準拠が不可欠です。労働安全衛生局(OSHA)は、特定の種類の機器および一般的な労働安全に関するオペレータートレーニング要件に関する規制を設定しています。ただし、業界に適用される規制を理解し、適切なコンプライアンス手順を確実に実施するのはあなた次第です。
原因#2:予防保守の実行の失敗
ほとんどの機器は、最適なパフォーマンスを得るために定期的なメンテナンスが必要ですが、多くの場合、人員が不足していて圧倒されている場合は、予防メンテナンスが最初のタスクになります。正常に動作しているように見える場合は、定期的なメンテナンスを簡単に取り除くことができます。多くの企業は、設備が完全に故障する前に、経験豊富な作業員が差し迫った問題を特定することを前提に作業しています。
とはいえ、パフォーマンスの低下や障害の初期段階の微妙な兆候の多くは簡単に検出できず、見過ごされがちです。その他の場合、企業は継続的なメンテナンスを確実に実行するための効率的な計画方法を欠いています。資産タグを使用して機器や機械を追跡することで、トラックのメンテナンススケジュールを維持し、機器を最大の運用効率で運用することができます。
予防保守は、道に迷うことを決して許されるべきではない継続的な機能の1つです。定期的な調整で機器の手入れをすることで、機器の使用可能寿命が延び、最終的には1ドルあたりの費用が増えます。さらに、予防保守は、安価なソリューションの小さな問題を、重大でコストのかかる故障になる前に特定できます。効果的な在庫管理戦略を使用して、最も一般的なメンテナンスタスクと誤動作に適切なスペアパーツを確実に供給できるようにすると、定期的なメンテナンスと修理のダウンタイムが最小限に抑えられます。実際、米国エネルギー省は、予防保守の結果は次のようになると推定しています。
- エネルギーとメンテナンスのコストを最大30%削減
- 故障が35%から45%少ない
- ダウンタイムを最大75%削減
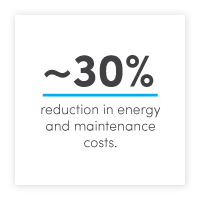
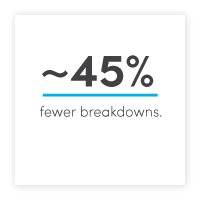
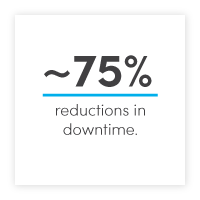
この無料の予防保守スケジュールテンプレートを使用して、終日火災との戦いをやめましょう
原因#3:予防保守が多すぎる
「確かにこれは間違いです」とあなたは考えています。 「予防保守を行わないと、物事が壊れるだろうとあなたは私に言っただけです。」確かに、予防保守に関しては、ゴルディロックスの状況が少し発生しています。上で概説した理由により、十分ではないことが問題になる可能性がありますが、多すぎることも懸念の主な原因です。
これについては以前に詳しく書いたので、メンテナンス後の内訳の概念について詳しく知りたい場合は、このブログをチェックしてください。しかし、ここにコールズのメモがあります。それを維持するために機械に入るたびに、その機器を一連のリスクにさらし、時間の経過とともにそれらのリスクが悪化し、障害につながる可能性があります。
PMが足りない
早期の失敗の兆候が見落とされている
メンテナンススケジュールが苦しむ
機器効率の低下
資産の寿命が短くなる
故障とダウンタイムの増加
コストが急騰
十分なPM
コストは管理されています
ジャストインタイム配信が実現されます
ダウンタイムが削減されます
技術者の効率が向上します
安全性が向上します
重要な資産の生産性が最適化されます
PMが多すぎます
過剰支出の増加
資産の損耗が急増
技術者の時間が無駄になります
不要な在庫が使用されています
不正確な情報が収集されます
このメンテナンスログテンプレートを使用してPMを多すぎないようにしてください
手術の観点から考えてみてください。トリプルバイパスは命を救う手術です。しかし、数年が経過した、または心臓が数百万回鼓動したという理由だけで、定期的に開心術を受けたくはありません。しかし、多くの場合、それがまさに予防保守への取り組み方です。アセットの実際の動作条件を考慮せずに、事前定義されたスケジュール(通常は時間ベースまたは使用量ベース)で実行されます。
これで…
原因#4:機器を継続的に監視できない
では、予防保守の適切なバランスをどのように見つけますか?ここでの治療法は、概念は単純ですが、実行はもう少し複雑です。条件ベースのメンテナンスです。これは、単に「設定して忘れる」スケジュールではなく、機器の動作状態に基づいて行われるメンテナンスです。メーカーの情報機器の履歴から振動解析などのリアルタイムデータまで、多くのことを考慮に入れています。
継続的な監視は、センサーデータに依存して、故障や故障を予測するために使用できる微妙な変化を検出するために、良好な機器の状態がどのように見えるかのベースラインを確立します。これにより、緊急時の計画とダウンタイムのスケジューリングにより多くの時間を確保して、生産の中断を最小限に抑えることができます。このタイプの監視とプロセスで収集されたデータは、企業が機械へのストレスの増加の原因を特定し、ワークロードとスケジュールを調整して、差し迫った障害の早期指標を示す機器の負荷を軽減するのに役立ちます。
<図>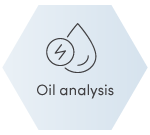
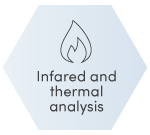
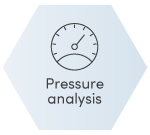
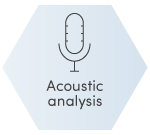
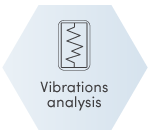
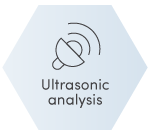
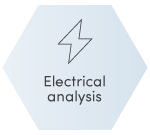
このFMEAテンプレートを使用して、重要なアセットのすべての障害に備えます
ここでの落とし穴は、ペンと紙またはExcelを使用してメンテナンスを管理している場合、これを行うのは実際には非常に難しいということです。これがメンテナンス操作を実行したい場所である場合は、デジタルメンテナンスソリューションへの移行を検討する時期かもしれません。
条件ベースの監視を使用する場合
<図>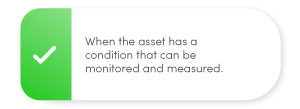
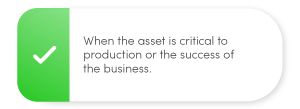
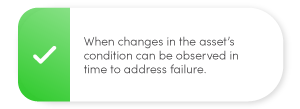
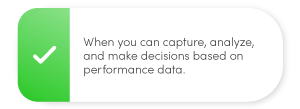
原因#5:信頼性の文化が悪い(またはない!)
誰もがそこにいました。上からの大きなプレッシャーは、制作目標を達成する希望があれば、1秒も余裕がないことを意味します。このような状況では、オペレーターや保守作業員が100%で機能していないことに気づき、バンドエイドソリューションを叩いて、「物事が落ち着いたらこれを理解する」と言うのはとても魅力的(そして簡単)です。下"。問題は、現実的には、その作業を再検討する時間があるほど物事が落ち着かないことです。つまり、バンドエイドソリューションは、機能を停止して本格的な障害になるまで、半永久的なソリューションになります。
これの本当に良い例はボーイングです。おそらく、会社の737 Max航空機に関連する2つの致命的な墜落事故に精通していると思います。これにより、ボーイングが飛行機の生産を急いで行ったために会社が安全上のリスクを冒し、最終的に墜落事故が発生したかどうかについて疑問が生じました。
しかし、より静かな話は別の飛行機モデル、787ドリームライナーに関するものです。サウスカロライナ州チャールストン近郊の当時の新工場で2009年に製造されたドリームライナーについて警告を発するために、数人の内部告発者が前に出てきました。当初から、ずさんな生産は、積極的な生産スケジュールを支持して、常に敷物の下で一掃されていた問題でした。
完全なストーリーが必要な場合は、こちらのNew York Timesの記事全体をチェックしてください(または、オーディオの方が好きな場合は、Dailyの関連ポッドキャストをご覧ください)。しかし、簡単に言えば、ボーイングの問題は、ビジネスの最高レベルでの競争圧力の非常に良い例であり、工場のフロアに至るまで、コマンドのチェーン全体に波及効果があります。最上位の悪い文化は「すぐにそれを成し遂げる」精神を生み出し、壊滅的な見落とし、バンドエイドの解決策、そして間違いをもたらす可能性があります。
では、悪い文化が機器の故障の根本にあるとしたらどうでしょうか?あなたは何ができますか?信頼性に重点を置いた文化の確立を開始する方法について説明しました。信頼性の確固たる基盤を築くために、これらの要素の1つ(またはすべて!)を確認してください。
結論:訓練を受けたオペレーター、堅実なPMスケジュール、信頼性文化への注力は、失敗のない未来へのチケットです(または少なくとも失敗が少なくなります)
機器は予測できない可能性があり、障害が発生します。人々は間違いを犯し、部品は古くなり、時には予防保守は、すでに忙しい日に多すぎることの1つにすぎません。しかし、適切なオペレータートレーニングを確保し、適切なタイミングで予防または状態ベースのメンテナンスを実行し、より良い全体的な文化に向けて取り組むことで、機器を最高の状態に保つためのより良いショットを得ることができます。
機器のメンテナンスと修理